
Детали машин и основы конструктирования
.pdf
191
корпусе, либо в отделенное перегородкой пространство;
•по объему заливаемой смазки. Способ заключается в том, что сначала полностью сливают имеющуюся в машине смазку, а затем заливают необходимый объем новой смазки (количество заливаемой смазки указывается в документации по эксплуатации). Способ применяют при невозможности контроля уровня никакими другими способами.
Помимо контроля уровня может возникать потреб-
ность в контроле давления, температуры и других пара- Рис.8.91 – Пробка-отдушина метров смазки.
Необходимость контроля давления связана с тем, что при работе машина нагревается, и давление внутри нее повышается, и тем сильнее, чем ниже КПД и теплоотдача. Это, в лучшем случае, ведет к выдавливанию смазки через щели стыков и уплотнений, а при последующем охлаждении машины (узла) – засасывает ее, но уже загрязненную, назад. Во избежание такого явления внутренний объем корпуса делают сообщающимся с внешней средой, например, выполняя отверстие в корпусе, либо устанавливая отдушину. Отдушина представляет собой пробку со сквозным отверстием (рис. 8.91). Форму канала отверстия выбирают такой, чтобы избежать попадания внутрь пыли, грязи и других нежелательных объектов. При большом размере отверстия внутри канала могут устанавливать сетку фильтра. Отдушину, представленную на рис.89, также используют в качестве ручки для удержания смотровой крышки.
8.8 Уплотнения
Уплотнения предназначаются для герметизации внутренних объемов технических систем (машин и их узлов, аппаратов, приборов) с целью:
•их защиты от неблагоприятных внешних воздействий (влага, пыль, грязь и т.п.);
•защиты внешней среды от вредных воздействий со стороны технической системы (утечки или испарения экологически опасных веществ);
•экономии расхода рабочих материалов (снижение утечек смазки и потерь хранимых жидкостей и газов, предотвращение изменения рабочих параметров, например, стравливание давления и т.п.).
Взависимости от условий работы уплотняемого узла различают уплотнения подвижных и неподвижных стыков (рис. 8.92).

192
8.8.1 Уплотнения неподвижных стыков
Уплотнения неподвижных стыков подразумевают герметизацию узла по стыкам деталей, неподвижных относительно друг друга. На степень герметичности существенно влияют качество обработки контактирующих поверхностей: шероховатость и отклонения форм (такие как, например, плоскостность, цилиндричность, перпендикулярность). Для облегчения обработки этих поверхностей им стараются придать простую геометрическую форму – плоскую или кольцеобразную.
В зависимости от требований к точности взаимного положения стыкуемых деталей уплотнения подразделяют на мягкие и жесткие.
Мягкие уплотнения конструктивно и технологически просты. Их применяют, когда нет необходимости точно выдерживать взаимное осевое положение соединяемых деталей: расстояние между поверхностями стыка зависит от степени обжатия расположенной между ними прокладки. Герметичность достигается тем, что при обжатии материал прокладки упруго или пластически деформируется и заполняет собой щели и микронеровности поверхностей стыка. Поперечная (радиальная) центровка соединяемых деталей посредством прокладки недопустима, и при необходимости осуществляется штифтами, центрирующими выступами, сопрягаемыми с канавками, или другими средствами.
Уплотнения |
|
|
|
|
|
|
|
|
|
|
|
|
|
|
|
||
|
|
|
|
|
|
|
|
|
|
|
|
|
|
|
|
|
|
|
|
|
|
|
|
|
|
|
|
|
|
|
|
|
|
|
|
|
Уплотнение |
|
|
Жесткие |
|
|
– прокладками |
|
|
||||||||
|
относительно |
|
|
|
|
|
|
|
|
– посадкой де- |
|
|
|||||
|
|
|
|
|
|
|
|||||||||||
|
неподвижных |
|
|
|
|
|
|
|
|
талей |
|
|
|
||||
|
стыков |
|
|
|
|
|
|
|
|
– шипами |
|
|
|
||||
|
|
|
|
|
|
|
|
|
|
|
|
|
– другие |
|
|
|
|
|
|
|
|
|
|
|
|
|
|
|
|
|
|
||||
|
|
|
|
|
|
|
|
|
|
|
|
|
|
|
|
|
|
|
|
|
|
|
|
|
|
Мягкие |
|
|
– герметиками |
|
|
||||
|
|
|
|
|
|
|
|
|
|
|
|
|
– утопленными |
|
|
||
|
|
|
|
|
|
|
|
|
|
|
|||||||
|
|
|
|
|
|
|
|
|
|
|
|
|
прокладками |
|
|
||
|
|
|
|
|
|
|
|
|
|
|
|
|
– шипами |
|
|
|
|
|
|
|
|
|
|
|
|
|
|
|
|
|
– другие |
|
|
|
|
|
|
|
|
|
|
|
|
|
|
|
|
|
|
|
|||
|
Уплотнение |
|
|
Контактные |
|
|
Радиаль- |
|
– манжетные |
||||||||
|
относительно |
|
|
|
|
|
|
|
|
ные |
|
– сальники |
|||||
|
|
|
|
|
|
|
|
|
|||||||||
|
подвижных |
|
|
|
|
|
|
|
|
|
|
– кольцевые |
|||||
|
|
|
|
|
|
|
|
|
|
|
|||||||
|
стыков |
|
|
|
|
|
|
|
|
Торцевые |
|
– другие |
|||||
|
|
|
|
|
|
|
|
|
|
|
|
|
|
|
|
|
|
|
|
|
|
|
|
|
|
|
|
|
|
|
|
|
|
|
|
|
|
|
|
|
|
|
Бесконтакт- |
|
|
– щелевые |
|
|
|
||||
|
|
|
|
|
|
|
|
|
ные |
|
|
– лабиринтные |
|
||||
|
|
|
|
|
|
|
|
|
|
|
|
|
– центробежные |
|
|||
|
|
|
|
|
|
|
|
|
|
|
|
|
– другие |
|
|
|
|
|
|
|
|
|
|
|
|
|
|
|
|
|
|
|
|
|
|
|
|
|
|
|
|
|
|
|
|
|
|
|
|
|
|
||
|
|
|
|
|
|
|
Специали- |
|
|
– суфлерные |
|
|
|
||||
|
|
|
|
|
|
|
зированные |
|
|
– гидрозатворы |
|
||||||
|
|
|
|
|
|
|
|
|
|
|
|
|
– герметичные |
|
|||
|
|
|
|
|
|
|
|
|
|
|
|
|
|||||
|
|
|
|
|
|
|
|
|
|
|
|
|
– другие |
|
|
|
|
|
|
|
|
|
|
|
|
|
|
|
|||||||
|
|
|
|
|
|
|
|
|
|||||||||
|
|
Устройство |
|
|
Одинарные |
|
|
|
|
||||||||
|
|
|
|
|
|
|
|
|
|
|
|
|
|
|
|||
|
|
|
|
|
|
|
|
|
|
|
|
|
|
||||
|
|
|
|
|
|
|
|
|
|
Комбинированные |
|
|
|
|
|||
|
|
|
|
|
|
|
|
|
|
|
|
|
|
|
|
|
|
|
|
|
|
|
|
|
|
|
|
|
|
|
|
|
|
|
|
|
Стояночные |
|
|
|
|
|
|
|
|
|
|
|
|
|
|
||
|
|
|
|
|
|
|
|
|
|
|
|
|
|
|
|
|
|
Рис. 8.92 – Классификация уплотнений

193
а) б)
в) г)
Рис. 8.93 – Формы поперечного сечения прокладок
Пластически деформируемые прокладки лучше герметизируют стыки, но плохо работают в часто разбираемых узлах и в податливых стыках при действии пульсирующих внешних нагрузок (прокладки не восстанавливают свою форму). В таких случаях применяют упругие прокладки. Их податливость выбирается тем выше, чем больше возможное циклическое расхождение стыков.
Степень герметичности, т.е. просачиваемость и диффузия среды сквозь прокладку, зависит от плотности прилегания прокладки к поверхностям стыка и ее ширины. Во избежание диффузии прокладка широкой. С другой стороны, для обеспечения плотного прижатия прокладки приемлемым по величине усилием (усилием обжатия) поверхность контакта должна быть небольшой.
Прокладки выполняют следующих форм поперечного сечения (на примере кольцевых прокладок):
•плоские прямоугольного сечения (рис. 8.93а). Они просты в изготовлении, но требуют приложения большого усилия обжатия;
•зубчатые прокладки (рис. 8.93б). Для их обжатия достаточно небольшого усилия, поскольку начальная поверхность контакта мала;
•круглого или овального сечения (рис. 8.93в). Они компактны, но нуждаются в дополнительной осевой фиксации, так как легко выдавливаются из стыка;
•V-образные (рис. 8.93г). Хорошо работают в податливых стыках, но сложны в изготовлении. Выполняются из материа-
|
лов с высокой жесткостью. |
|
|
|
Возможна герметизация стыков без |
|
|
применения прокладок: |
|
||
• |
посадкой соединяемых поверхностей с |
Рис.8.94 – Беспрокладочное уплотнение |
|
• |
натягом; |
(шипами) |
|
посадкой по конической поверхности, в |
|||
|
том числе – сбегом резьбы;
• посредством внедрения острого выступа (шипа) одной детали в торец другой детали (рис. 8.94).
Выбор формы и материала прокладок также существенно зависит от перепада давлений в разделяемых пространствах, агрессивности среды и ее температуры.
Жесткие уплотнения применяют, когда точность взаимного положения соединяемых деталей должна быть высокой. В этом случае стыкуемые поверхности деталей входят в непосредственный контакт и являются базирующими, а герметизация достигается следующими способами:
•нанесением на поверхности стыка герметизирующих составов (герметиков) в виде пасты или лака. При обжатии соединения их избыток выдавливается (до посадки одной поверхности на другую), и в стыке остается очень тонкая пленка, не нарушающая точность взаимного расположения деталей (например, частей корпуса при радиальной сборке). Разборка таких соединений из-за слипания поверхностей бывает затруднена, поэтому в конструкции
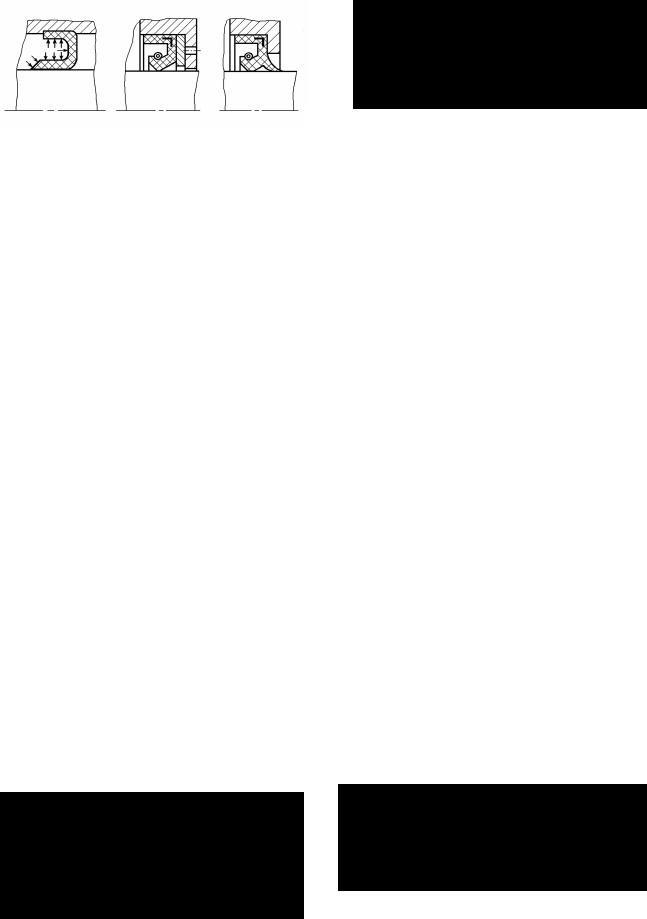
194
должны быть предусмотрены съемные устройства (например, отжимные винты). Герметизируемые поверхности обрабатываются с высокой точностью;
•использованием утопленных прокладок. Первоначально, при установке, прокладка выступает над плоскостью стыка (рис. 8.95а). После обжатия соеди-
нения прокладка осаживается пока поверхности стыка |
а) |
б) |
не лягут друг на друга (рис. 8.95б). Такой способ |
Рис. 8.95 – Уплотнение утопленными про- |
|
применяется, например, при уплотнении корпусных |
||
деталей при осевом способе сборки. При деформации |
кладками |
|
|
|
прокладки в стесненных условиях паза (условиях всестороннего сжатия) ее жесткость значительно возрастает. Поэтому паз должен быть шире начального сечения прокладки, чтобы не препятствовать свободе ее деформации, но не настолько, чтобы плотность прилегания прокладки была недостаточной.
Основные отказы уплотнений неподвижных стыков связаны с нарушением прочности и плотности соединений.
8.8.2 Уплотнения подвижных стыков
Уплотнения подвижных стыков конструктивно и технологически сложнее. Различают три способа уплотнения: контактное, бесконтактное и специализированное.
Вконтактном уплотнении герметичность достигается благодаря плотному соприкосновению участков поверхностей подвижной и неподвижной деталей. В зависимости от расположения соприкасающихся участков уплотнения подразделяют на радиальные (контакт по цилиндрической поверхности) и торцевые (контакт по торцам деталей).
Вгруппу контактных уплотнений, прежде всего, входят манжетные уплотнения, сальники
иуплотнения кольцами.
Манжетные уплотнения. Герметичность обеспечивается установкой специальной кольцевой детали – манжеты, выполняемой из мягкого упругого материала, с различной формой поперечного сечения (рис. 8.96). Обычно манжету закрепляют в неподвижной детали. Под действием давления в уплотняемом пространстве она плотно прижимается к подвижной детали (рис. 8.96а). При обратном расположении манжеты давление среды будет отжимать ее от подвижной детали. При необходимости двустороннего уплотнения устанавливают две противоположно направленные манжеты.
Манжеты – стандартизированные, взаимозаменяемые, покупные детали. Для компенсации износа и хорошего поджатия в манжете имеется пружинное кольцо, а для повышения ее жесткости – армированное металлическое кольцо (рис. 8.96б, в). Манжету подбирают по величине диаметра вала, а их число – по необходимой степени уплотнения. Для работы в сильно загрязненной среде применяют манжеты с пыльником (рис. 8.96в).
В конструкции узла с манжетным уплотнением необходимо предусматривать ее защиту от возможного выворачивания при действии высокого давления (например, опиранием манжеты о торцевую поверхность) и возможность удаления при замене, учитывая то, что манжета часто крепко схватывается с неподвижной деталью (удалять, например, выдавливанием манжеты посредством шайбы через отверстие, как показано на рис. 8.96б).
а) б) в) а) б)
Рис. 8.96 – Уплотнение манжетами |
Рис. 8.97 – Сальники |
|

195
Сальники. Они представляют собой полость, набитую уплотняющим материалом, например, фторопластом или пропитанным маслом войлоком. Уплотнения конструктивно просты, но не взаимозаменяемы. На рис. 8.97а показано наиболее распространенное сальниковое уплотнение с трапецеидальной канавкой. Такая форма канавки благодаря действию сил упругости обеспечивает плотное поджатие уплотнения к подвижной детали (валу). Для компенсации износа применяют регулируемое уплотнение (рис. 8.97б), в котором уплотняющий материал поджимается втулкой (например, посредством затяжки гаек на шпильках). Длина участка набивки и плотность поджатия зависят от перепада давления в уплотняемых объемах и требования к степени их герметизации.
Уплотнения кольцами. Способ обычно применяют при возвратно-поступательном движении деталей. Кольца могут быть разрезными, если изготавливаются из твердых материалов, либо цельными, если допускают упругое растяжение (рис. 8.98а).
Наряду с перечисленными спосо- |
|
|
||
|
|
|||
бами в торцевом уплотнении широко |
|
|
||
применяется |
уплотнение |
упругими |
|
|
стальными шайбами (рис. 8.98б). Оно |
|
|
||
обладает способностью самоприраба- |
|
|
||
тываться и компенсировать износ тру- |
а) |
б) |
||
щихся поверхностей. |
|
|||
Контактные уплотнения |
хорошо |
Рис.8.98 – Уплотнения кольцами (а) |
||
герметизируют |
при разных |
условиях |
и шайбой (б) |
эксплуатации (горизонтальное и вертикальное расположение валов, высокое давление и т.п.) за исключением высоких скоростей относительного перемещения деталей. Эффективность герметизации зависит от силы прижатия уплотнения, что, с другой стороны, ведет к заметному износу и снижению КПД машины. Установка нескольких уплотнений еще в большей степени снижает КПД. Для повышения срока службы уплотняемого узла поверхность подвижной детали должна обрабатываться до высокой твердости (чем выше, тем лучше, обычно не менее HRC45) и шероховатости (не грубее Ra0,3...0,63). Для предохранения более дорогой детали (вала) от износа, на нее могут надевать сменную втулку, по наружной поверхности которой и будет контактировать уплотнение.
Бесконтактные уплотнения.
В бесконтактном уплотнении подвижные детали не касаются друг друга. Это обеспечивает им практически неограниченный срок службы, отсутствие износа и незначительные потери на трение (высокий КПД), отсутствие ограничений по скоростям. Однако уплотнительные свойства здесь ухудшаются при снижении вязкости среды (особенно для газообразных сред) или при остановке машины, а уплотнительный узел требует высокой точности изготовления и монтажа.
Герметизация основана на применении различных физических эффектов, по видам которых и подразделяют уплотнения.
Щелевые уплотнения. Уплотняющий эффект связан с наличием сопротивления истечению жидкости в узкой длинной щели между относительно подвижными поверхностями деталей. Для повышения степени уплотнения на поверхности одной из деталей делают канавки (рис. 8.99а и у мазеудерживающего кольца на рис. 8.87а), часто заполняемые густой смазкой. Чем уже щель, тем выше герметичность, но и выше требования к точности изготовления и жесткости деталей (во избежание последствий от разброса размеров и перекосов).
При нереверсивной работе машины канавки выполняют винтовыми. Их направление согласуют с направлением вращения вала так, чтобы витки отгоняли уплотняемую среду назад.

196
Лабиринтное уплотнение. Уплотняю-
щий эффект основан на торможении вязкой |
|
|
|
|
|
|
среды в узкой извилистой щели, часто до- |
|
|
|
|
|
|
полнительно заполняемой густой смазкой |
|
|
|
|
|
|
(рис. 8.99б). Эффективность этого уплотне- |
|
|
|
|
|
|
ния выше, чем щелевого, но выше и требова- |
|
|
|
|
|
|
ния к точности изготовления и жесткости |
|
|
|
|
|
|
деталей, а также к точности осевого монта- |
|
|
а) |
б) |
||
жа. Известно множество форм лабиринтов. |
|
|
||||
Центробежное уплотнение. Уплотняю- |
|
|
|
|
|
|
щий эффект основан на отбрасывании смаз- |
|
|
|
|
|
|
ки с выступа вращающейся детали центро- |
|
|
|
|
|
|
бежной силой и возвращении ее назад через |
|
|
|
|
|
|
дренажное отверстие (рис. 8.99в). В качестве |
|
|
|
в) |
||
выступа может использоваться кольцо или |
|
|
|
|||
|
|
|
|
|
||
диск, установленные на валу. Требования к |
|
|
|
|
|
|
точности изготовления и сборки здесь пони- |
|
|
|
|
|
|
женные. Уплотнение применяется при доста- |
|
|
|
|
|
|
точно высоких окружных скоростях. Для по- |
|
|
|
|
|
|
вышения степени герметизации могут после- |
Рис. 8.99 – Бесконтактные уплотнения |
|||||
довательно устанавливать несколько уплот- |
|
|
|
|
|
|
нений одного или разных видов (комбинированные уп- |
|
|
|
|
||
лотнения). |
|
|
|
|
|
|
Для удовлетворения особо высоких требований к |
|
|
|
|
||
герметичности применяют специализированные |
виды |
|
|
|
|
|
уплотнений, обычно, более сложные и дорогие. Из них |
|
|
|
|
||
наиболее распространены следующие: |
|
|
|
|
|
|
• суфлерные уплотнения (уплотнения передавливани- |
|
|
|
|
||
ем). Действие уплотнения основано на подаче под |
|
|
|
|
||
давлением в рабочую камеру (в герметизируемый |
|
|
|
|
||
объем) специальной жидкости или воздуха. Благода- |
|
|
|
|
||
Рис. 8.100 – Сильфонное уплотнение |
||||||
ря их постоянному вытеканию наружу через неплот- |
ности и зазоры, исключается проникновение во внутрь каких-либо веществ. Возможна подача специальной среды, обычно воздуха, в про-
межуточную камеру, расположенную между герметизируемыми полостями машины. В этом случае среда будет перетекать в оба соседних объема и исключит утечки из одной полости в другую;
•гидравлическое уплотнение. Действие основано на заполнении зазоров жидкостью, которая создает гидравлическую пробку. Жидкость в зазоре удерживается, например, центробежными силами;
•уплотнение с полной герметизацией гибкими элементами. Такие элементы служат гибкой стенкой, соединяющей относительно подвижные детали, либо движение передается сквозь гибкий элемент. Например, герметизация сильфоном при возвратно-поступательном движении деталей (рис. 8.100). Сильфон представляет собой гофрированную тонкостенную трубку, которая одним концом плотно закрепляется в неподвижной детали (на рисунке – защемляется шайбой, закрепленной к корпусу), а другим концом – в относительно подвижной детали (на рисунке – приварена к штоку). Податливость сильфона позволяет штоку свободно смещаться в осевом направлении, а непрерывность стенки гарантирует отсутствие утечек. При передаче вращательного движения применяются специальные виды герметичных муфт и передач, например, герметичная волновая передача (рис. 8.19в).
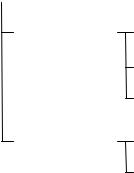
197
К промежуточному типу относятся стояночные уплотнения: при работе машины, в узле с подвижными деталями уплотнение работает как бесконтактное, а при их остановке уплотнение захлопывается, т.е. детали по поверхности стыка плотно прижимаются. Зазор в рабочем состоянии может создаваться вследствие действия центробежных сил, клиновым механизмом и иными способами.
8.9 Двигатели
Двигатель – неотъемлемая часть любой машины: как источник механической энергии обеспечивает ее функционирование. За исключением особых условий, в проектируемых устройствах целесообразно применение двигателя как готового покупного изделия, выпускаемого промышленностью. Это экономит время и средства на его разработку и изготовление, повышает надежность всей системы, обеспечивает взаимозаменяемость и т.д. В таких случаях двигатель подбирается по каталогам предприятий-производителей, что позволяет также оценить и его доступность. Ниже приводятся основные сведения и характеристики типовых двигателей, необходимые для их подбора.
На рис. 8.101 представлена классификация двигателей по виду создаваемого движения. Двигатели вращательного движения наиболее распространены. Они подразделяются на
следующие:
•двигатели, обеспечивающие длительное (в пределах ресурса) вращение своего вала, т.е. позволяющие вращать вал в пределах - ∞ < ϕ < ∞ (при реверсивной работе). Такие двигатели также называют моторами;
•поворотные двигатели. Угол поворота их вала изменяется только в ограниченных пределах
– 0 < ϕ < ϕ o (величина интервала обычно не превышает 270о). В пределах этого интервала обеспечивается точное позиционирование вала (его поворот на требуемый угол);
•шаговые двигатели. Обеспечивают поворот своего вала на величину, кратную некоторому
шагу ∆ϕ , т.е. ϕ = ϕ 0 ± k ∆ϕ , где k=1,2,... ∞, а ϕ 0 – начальное значение угла. Величина шага может быть различной. Шаговые двигатели предназначены для точного (в пределах шага)
позиционирования вала.
|
Двигатели |
|
|
|
|
|
|
|
|
|
|
|
|
|
|
Вращательного |
|
Длительного |
|
|
движения |
|
вращения:−–∞ < ϕ < ∞ |
|
|
|
|
|
|
|
|
|
|
|
|
|
|
|
Поворотные: 0 < ϕ < ϕ o |
|
|
|
|
|
|
|
|
|
Шаговые: ϕ = ϕ 0 ± k ∆ϕ , |
|
|
|
|
k=1,2,... ∞ |
|
|
|
|
|
|
Поступательного |
|
Линейные: 0 < s< s o |
|
|
движения |
|
|
|
|
|
|
||
|
|
|
|
Шаговые: s = s 0 ± k ∆ s , |
|
|
|
|
|
|
|
|
|
k=1,2,... k max |
Рис. 8.101 – Классификация двигателей по виду создаваемого движения
Двигатели поступательного движения не позволяют получить большие линейные перемещения (за исключением, может быть, транспортных двигателей, перемещающих повозки по длинным магистралям). Они подразделяются только на два вида:
•линейные двигатели. Обеспечивают перемещение своего штока в пределах 0 < s < s o (шток может ходить в пределах от миллиметра до нескольких метров);
•линейные шаговые двигатели. Обеспечивают перемещение штока в пределах определенно-
го интервала с заданным шагом, т.е. s = s 0 ± k ∆ s , где k=1,2,... kmax . Величина шага может быть различной. Шаговые двигатели, по сравнению с линейными, имеют более сложную конструкцию, но и точнее позиционируют шток.

198
На рис. 8.102 представлена классификация двигателей по принципу действия.
|
Двигатели |
|
|
|
|
|
|
|
|
|
|
|
|
|
|
|
|
|
|
|
|
|
|
|
|
|
|
|
|
|
Механические |
|
Механические |
|
|
– деформационные |
|||
|
|
|
|
двигатели |
|
|
– гравитационные |
||
|
|
|
|
|
|
|
|
– инерционные |
|
|
|
|
|
|
|
|
|
||
|
|
|
|
|
|
|
|
||
|
|
|
|
|
|
|
|
– другие |
|
|
|
|
|
|
|
|
|
|
|
|
|
|
|
|
|
|
|
|
|
|
|
|
|
Гидро- и |
|
|
– поршневые |
||
|
|
|
|
пневмодвига-тели |
|
|
– шиберные |
||
|
|
|
|
|
|
|
|
– шестеренчатые |
|
|
|
|
|
|
|
|
|
– винтовые |
|
|
|
|
|
|
|
|
|
||
|
|
|
|
|
|
|
|
– турбинные |
|
|
|
|
|
|
|
|
|
– другие |
|
|
|
|
|
|
|
|
|
||
|
|
|
|
|
|
|
|||
|
Тепловые |
|
Турбодвигатели |
|
|
– газовые |
|||
|
|
|
|
|
|
|
|
– паровые |
|
|
|
|
|
|
|
|
|
|
|
|
|
|
|
|
|
|
|
|
|
|
|
|
|
|
|
|
|
|
|
|
|
|
|
Поршневые |
|
|
– паровая машина |
||
|
|
|
|
двигатели |
|
|
– внутреннего сгора- |
||
|
|
|
|
|
|
|
|
ния |
|
|
|
|
|
|
|
|
|
– другие |
|
|
|
|
|
|
|
|
|
||
|
|
|
|
|
|
|
|
|
|
|
|
|
|
другие |
|
|
|
||
|
|
|
|
|
|
|
|||
|
|
|
|
|
|
|
|
|
|
|
Электричес-кие |
|
Постоянного тока |
|
|
||||
|
|
|
|
|
|
|
|
||
|
|
|
|
|
|
|
|
||
|
|
|
|
Переменного тока |
|
|
|||
|
|
|
|
|
|
||||
|
|
|
|
|
|
|
|||
|
|
|
|
|
|
||||
|
Биологичес-кие |
|
– гужевые |
|
|
||||
|
|
|
|
– человеческие |
|
|
|||
|
|
|
|
– другие |
|
|
|||
|
|
|
|
|
|
|
|
|
|
другие
Рис. 8.102 – Классификация двигателей по принципу действия
Работа двигателя нуждается в подпитке внешней энергией. По способу ее подведения двигатели подразделяются на непрерывно подпитывающиеся (обычные виды двигатели) и периодически подпитывающиеся (двигатели аккумуляторного типа, периодически запасающие энергию и затем постепенно ее расходующие). По виду подводимой энергии двигатели подразделяются на механические, тепловые, электрические и биологические. Возможны и другие, но реже встречаемые виды, например, химические двигатели.
При подборе двигателя важное значение имеет его механическая характеристика, т.е. зависимость угловой скорости ω (или частоты вращения n) вращения вала двигателя от величины приложенного к нему момента T. Эта характеристика позволяет определить соответствие двигателя условиям эксплуатации.
8.9.1Механические двигатели
Взависимости от состояния вещества рабочего тела механические двигатели они подразделяются на твердотельные, гидравлические и пневматические.
Твердотельные или, как чаще они называются,– механические двигатели. По принципу действия они подразделяются на следующие:
199
•деформационные, которые в процессе работы постепенно расходуют ранее накопленную энергию деформации упругого твердого тела (например, пружины);
•гравитационные, которые в процессе работы преобразуют потенциальную энергию в кинетическую (например, маятниковые и гиревые двигатели);
•инерционные, которые в процессе работы расходуют ранее накопленную кинетическую энергию (например, маховики);
•и другие.
Механические двигатели конструктивно просты, но относятся к аккумуляторному типу, и поэтому нуждаются в периодической подзарядки (подзаводе). Их механическая характеристика – падающая, т.е. с ростом внешней (полезной) нагрузки частота вращения вала или скорость перемещения штока уменьшается. Механические двигатели проектируются и изготавливаются специально для каждого конкретного устройства.
Гидравлические и пневматические двигатели. Семейство этих двигателей достаточно ве-
лико и разнообразно: их выпускают для специального и общего назначения, мощностью от нескольких ватт до нескольких мегаватт (но мощность пневмодвигателей обычно невелика). Двигатели компактны, имеют высокий КПД и надежность, пожаробезопасны, позволяют беступенчато регулировать скорость (например, плавно изменять частоту вращения вала двигателя от 1 до 1500 оборотов в минуту). Существенным их недостатком является потребность в источнике жидкости или газа определенного давления и расхода, которым часто служит насосная станция. В состав станции входит двигатель и насос, и в итоге, для всего комплекса, такие характеристики, как КПД, габариты и надежность оказываются ниже. По этой причине гидро- и пневмодвигатели преимущественно применяют при необходимости получения специальных характеристик или в особых условиях, например, когда единственным источником энергии необходимой мощности является жидкость (допустим, течение реки).
Гидро- и пневмодвигатели, обеспечивающие неограниченное вращение вала, называют моторами. Двигатели, являющиеся источником поступательного движения, называют гидроили пневмоцилиндрами.
Наиболее распространены следующие виды моторов:
•шестеренчатые моторы. Они включают пару зацепляющихся цилиндрических зубчатых колес, с минимальным зазором расположенных в корпусе. Колеса приводятся в движение прокачиванием рабочего тела (жидкости или газа) из объема, расположенного по одну сторону от плоскости, в которой лежат оси валов, в объем, расположенный по другую сторону. Моторы технологичны и конструктивно просты, компактны, удобны в обслуживании, очень распространены. Типовые моторы выпускаются на мощности до 10 кВт и частоты вращения от 150 до 3000 об/мин, их КПД составляет 70...80%. Моторы нуждаются в больших пусковых моментах;
•пластинчатые моторы (другое название – шиберные). Они содержат эксцентрично расположенный ротор, на котором находятся радиально подвижные пластины. Моторы обладают высокой компактностью, равномерностью вращения вала и малой инерционностью, дешевы. Их выпускают на мощности до 10 кВт и частоты вращения от 100 до 3000 об/мин. КПД моторов невелик и составляет 50...75%;
•поршневые моторы. Здесь вначале создается поступательное движение поршня, которое потом преобразуется во вращательное. По способу преобразования движения моторы подразделяются на аксиально-поршневые, радиально-поршневые, кривошипные и другие. Типовые моторы выпускают на широкий диапазон мощностей и частот вращения (20...20000 об/мин), часто применяют в качестве шаговых двигателей. КПД моторов составляет около 90%;
•винтовые моторы. Здесь вал связан с винтом (шнеком), приводимым во вращение движущимся рабочим телом. Типовые моторы выпускают мощностью до 100 кВт и с частотами вращения до 1000 об/мин. Их КПД составляет около 80%. Моторы имеют средние габариты, надежность и удобство обслуживания, но обеспечивают высокую равномерность вращения;
•турбомоторы. Здесь вращение создается при обтекании лопастей турбины. Моторы выпус-

200
кают практически на любые (технически реализуемые) мощности, но на низкие частоты вращения (порядка 100 об/мин), имеют сравнительно большие габариты. Их КПД составляет около 80%. В отличие от других моторов, нуждающихся в специальных рабочих жидкостях и газах (очищенных, специального состава), подаваемых под давлением, турбины могут работать в любой среде и при любом, даже очень малом, перепаде давления.
Механическая характеристика гидро- и пневмодвигателей – постоянная или линейно падающая и зависит от системы подачи жидкости или газа (рис. 8.103).
Рис. 8.103 – Механические характеристики гидро- и пневмодвигателей
8.9.2Тепловые двигатели
Втепловых двигателях источником энергии является внутренняя энергия нагретого вещества. Механические характеристики двигателей подобны характеристикам гидро- и пневмодвигателей и также зависят от системы подачи топлива. По принципу работы двигатели подразделяются на следующие:
•турбодвигатели газовые и паровые. Газотурбинные двигатели выпускаются по заказу, мощностью от 0,1 кВт до 100 мВт и развивают частоту вращения от 1000 до 100 000 об/мин. Двигатели очень компактны, но имеют невысокий КПД (20...40%, но это КПД всей установки, что приблизительно соответствует КПД гидродвигателя с насосной станцией). Паротурбинные двигатели также выпускаются по заказу, мощностью от 10 кВт до 1000 мВт
иразвивают частоту вращения от 1000 до 10 000 об/мин. Их КПД составляет 30...50%. Эти двигатели достаточно громоздки, и им необходим источник пара или устройство для его получения;
•поршневые двигатели (паровая машина, двигатели внутреннего сгорания и другие). Паровая машина работает на паре, имеет низкий КПД и большие габариты. В настоящее время выпускается редко, для специальных условий. Двигатель внутреннего сгорания (бензиновый, дизельный, спиртовой и другие по виду топлива и системы зажигания) выпускается для специального и общего назначения, мощностью от 0,1 до 1000 кВт и частотой вращения от 100 до нескольких тысяч оборотов в минуту (чем больше мощность, тем обычно меньше частота вращения). Их КПД и габариты занимают промежуточное положение между газотурбинными и паротурбинными двигателями, но при меньшем сроке службы (ресурс ниже).
8.9.3Электрические двигатели
Доступность и удобство передачи электрической энергии обусловили широкое применение электрических двигателей, выпускаемых как для общего, так и специального назначения. Двигатели доступны, сравнительно дешевые и простые в эксплуатации, имеют высокий КПД. Классификация двигателей по виду подводимого электрического тока и принципу действия показана на рис. 8.104.
Наибольшее распространение получили двигатели постоянного тока независимого (ДПТ НВ) и последовательного (ДПТ ПВ) возбуждения, асинхронные с короткозамкнутым (АС КР) и фазным (АС ФР) ротором, синхронные с постоянными магнитами (СД). Их механические характеристики показаны на рис. 8.105.