
Детали машин и основы конструктирования
.pdf
91
Дополнительно могут устанавливаться требования к виду и последовательности обработки, к шероховатости отдельных участков поверхности.
Обозначение шероховатости на чертеже показано на рис. 7.27. Параметры шероховатости приводятся в микрометрах. Целесообразно пользоваться следующими предпочтительными значениями параметров Ra и Rz:
50 – 25 – 12,5 – 6,3 – 3,2 – 1,6 – 0,8 – 0,4 – 0,2 – 0,1 – 0,05 – 0,025 – 0,012 .
Если шероховатость задана параметрами Ra или Rz, а базовая длина определяется требованиями стандарта, то знак шероховатости дается без полки. При этом значение параметра Ra приводится без его символа, например, 2,5.
Различают три вида требований к обработке поверхностей:
•знак по рис. 7.28а применяют, если вид обработки конструктором на чертеже не устанавливается. Он соответствует обычным условиям нормирования поверхности;
•знак по рис. 7.28б применяют для обозначения шероховатости, которая должна быть получена с обязательным удалением слоя материала, например, точением, сверлением, травлением и т.п., причем конкретный вид обработки может и не указываться;
•знак по рис. 7.28в применяют для обозначения шероховатости поверхности в состоянии поставки или с обработкой без удаления слоя материала, например, литьем, ковкой, прокаткой и т.п., причем конкретный вид обработки может не указываться.
Вид обработки поверхности приводят в обозначении шероховатости только в случаях, ко-
гда он является единственным, применимым для получения требуемого качества поверхности. На рис. 7.29 показано обозначение на рабочих чертежах шероховатости тех поверхностей
детали, к которым не проставлен знак шероховатости.
Величина шероховатости устанавливается исходя из функционального назначения поверхности. С другой стороны, параметр шероховатости влияет на точность характеризующего эту поверхность размера. Данное условие задает предельно-наибольшее значение параметра Ra, приблизительно равное
Ra ≤ 0,08 IT,
где IT – допуск координирующего размера на соответствующую поверхность. Если данная поверхность также характеризуется допусками формы и расположения (т.е. к ней предъявляются повышенные требования), то значение параметра уменьшают в 1,5...6 раз.
Следует помнить, что обеспечение заданных параметров шероховатости зависит и от свойств материала детали. Так, чистую поверхность стальных деталей проще получить, если
Вид обработки поверхности и/или другие дополнительные указания
Полка Параметры знака шероховатости
|
|
|
|
|
Базовая |
высотные Ra, Rz, Rmax |
|
|
|
|
длина (l) |
шаговые Sm, S |
|
|
|
|
Условное |
|
|
|
|
||
опорные tp |
|
|
|
|
|
|
|
|
|
||
|
|
|
|
||
|
|
|
|
|
обозначение |
|
|
|
|
|
направления |
|
|
|
|
|
неровностей |
|
|
|
|
|
(=, , X, M, C, R) |
|
|
|
Знак |
Рис. 7.27 – Обозначение шероховатости поверхности на чертежах. Знак проставляется снаружи поверхности детали
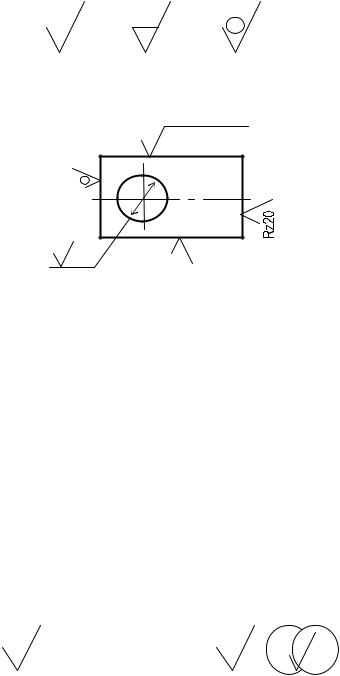
92
а) |
б) |
в) |
Rmax2,5 |
|
|
0,32 |
|
|
Sm0,08 |
|
полировать |
t5070 |
|
0.5 |
|
|
М
г)
2,5
1,6
2,5
Рис.7.28 – Знаки шероховатости поверхности с нерегламентированной обработкой (а), с удалением (б) и в состоянии поставки или без удаления поверхностного слоя (в) и примеры их нанесения на чертеж детали (г)
поверхность имеет высокую твердость (HRC не ниже 30).
На выбор параметров шероховатости также сказываются условия работы и дополнительные требования к детали. Так, для повышения усталостной прочности деталей необходимо обеспечить высокие требования к чистоте поверхностей. Параметры шероховатости также уменьшают при повышенных требованиях к контактной жесткости, коррозионной стойкости, отражательной способности, безопасности, эстетическому восприятию и т.д. Но во всех случаях значения параметров не могут быть грубее их предельно-наибольших величин.
|
|
|
|
|
|
|
3,2 |
|
3,2 |
|
|
|
|
|
|
|
|
|||
|
|
|
|
|
|
|
|
|
|
|
|
|
|
|
|
|
|
|
|
|
Указание одинаковых требований к |
Указание одинаковых требований к |
шероховатости всех поверхностей |
шероховатости поверхности, к кото- |
рым |
|
детали |
не проставлен знак шероховатости |
Рис.7.29 – Обозначение шероховатости поверхности на чертежах

93
8. Типовая элементная база механических устройств
Технические системы представляют собой единое, целостное устройство, предназначенное для выполнения определенных функций. Но эти системы, в свою очередь, обычно состоят из отдельных элементов (частей), которые также характеризуются выполняемой функцией, принципом действия, структурой и параметрами.
Элементы, родственные по выполняемой функции (хотя они и могут принадлежать различным системам), объединяют в группы, которые образуют элементную базу предметной области – машиностроения, аппаратостроения, приборостроения и т.д. Знание этих групп и составляющих их элементов облегчает анализ сложных и создание новых систем.
Наиболее распространены типовые механические элементы. Типовые – поскольку такие элементы составляют основу устройства не только машин (от простейших передач до сложных механизмов), но и основу конструкции разнообразных аппаратов и приборов. Состав элементной базы механических устройств (машин, аппаратов, приборов) показан на рис. 8.1.
8.1 Передаточные устройства
Передаточные устройства – главная функциональная часть машин или механизмов иных технических систем. Они подразделяются (рис. 8.2):
•на передачи, предназначенные для согласования (преобразования) вида и параметров движения, которое поступает от двигателя к исполнительному устройству; Если в процессе работы устройства передаточное отношение постоянно, то его обычно
называют передаточным числом и обозначают буквой u. Под словом “передача” понимают именно такие устройства. С другой стороны, некоторые устройства могут допускать периодическое изменение (перенастройку) величины передаточного числа. Если изменение происходит ступенчато (пошагово), то устройства относят к коробкам скоростей. Устройства, позволяющие изменять передаточное число беступенчато (непрерывно в пределах заданного диапазона), относят к вариаторам.
Рассмотрим подробнее виды и характеристики передач с постоянным передаточным отношением (передаточным числом).
Механические
устройства
Типовая |
|
|
|
Передачи |
|
|
|
|
|
|
|
|
элементная база |
|
|
|
|
|
|
|
|
|
|
|
|
|
|
|
|
|
|
|
|
|
||||
(детали и узлы) |
|
|
|
Валы, оси, штоки |
|
Передаточные |
|
|
|
|
||
|
|
|
|
|
|
|
устройства |
|
|
|
|
|
|
|
|
|
|
|
|
|
|||||
|
|
|
|
|
|
|
|
|||||
|
|
|
|
Опоры подвижных |
|
|
|
|
|
|
|
|
|
|
|
|
|
|
|
|
|
|
|
|
|
|
|
|
|
деталей и узлов |
|
|
|
|
|
|
|
|
|
|
|
|
|
|
Передачи |
|
u = const |
|
Передачи |
||
|
|
|
|
|
|
|
|
|
|
|
|
(рис.3) |
|
|
|
|
Корпусные детали |
|
|
|
|
|
|
|
|
|
|
|
|
|
|
|
|
|
|
|
|
|
|
|
|
|
|
|
|
|
|
|
u = var |
|
Коробки |
|
|
|
|
|
|
|
|
|
|
|||
|
|
|
|
Соединения и |
|
|
|
|
|
|
|
скоростей |
|
|
|
|
|
|
|
|
|
|
|
||
|
|
|
|
муфты |
|
|
|
|
|
|
|
|
|
|
|
|
|
|
|
|
|
|
|
(ступенча- |
|
|
|
|
|
|
|
|
|
|
|
|
|
тое изме- |
|
|
|
|
Уплотнения |
|
|
|
|
|
|
||
|
|
|
|
|
|
|
|
|
|
|
нение u) |
|
|
|
|
|
|
|
|
|
|
|
|
|
|
|
|
|
|
|
|
|
|
|
|
|
||
|
|
|
|
|
|
|
|
|
|
|
|
|
|
|
|
|
Смазочные |
|
|
|
|
|
|
|
Вариаторы, |
|
|
|
|
устройства |
|
|
|
|
|
|
|
(непрерыв- |
|
|
|
|
|
|
|
|
|
|
|
|
ное изме- |
|
|
|
|
Пружины |
|
|
|
|
|
|
|
нение u) |
|
|
|
|
|
|
|
|
|||||
|
|
|
|
|
|
|
|
|
|
|
|
|
Специальная |
|
|
|
Трансмиссии |
|
|
|
|||||
элементная база |
|
|
|
|
|
|
|
|
|
|||
|
|
|
|
|
|
|
|
|
Рис.8.2 – Виды передаточных устройств
Рис. 8.1– Состав типовой элементной базы механических устройств
94
8.1.1. Виды механических передач
Известно большое число видов передач. Однако все они в зависимости от назначения и условий применения могут быть подразделены на группы, как показано на рис. 8.3.
Функциональный признак. Наиболее важный. Он характеризует допустимость применения передачи по своему непосредственному назначению, т.е. для согласования видов и параметров движений на входе и выходе. Возможен ряд случаев:
1. Согласуются (изменяются) только параметры вращательного движения. Передаточное
число u = ωвх /ωвых ,
где ωвх , ωвых – угловая скорость вращения входного (ведущего) и выходного (ведомого) звеньев (валов) передачи.
Передачи относят к редукторам, если движение замедляется и, следовательно, передаточное число по абсолютной величине больше единицы, u >1, либо к мультипликаторам, если движение ускоряется, u <1. Если параметры движения не изменяются, т.е. u =1, то такие передачи уже относят или к трансмиссиям (основная функция – передавать), или к муфтам (функция – соединять, но при этом звенья передачи относительно неподвижны). Передаточное число может иметь знак, указывающий на совпадение или нет направлений вращений входного и выходного валов.
В группу передач вращательного движения входят цилиндрическая, коническая, планетарная, волновая, червячная, ременная, цепная и винтовая передачи и другие. При этом ременная и цепная передачи часто используются и как трансмиссии: они содержат гибкие звенья (ремни и цепи), которые называются гибкой связью и обеспечивают выполнение обеих функций (передавать, соединять).
2. Преобразуется вид передаваемого движения и согласуются его параметры. Передаточное число
u = ωвх / vвых , или u = vвх /ωвых ,
где ω , v – угловая и линейная скорости передаваемого движения. В этом случае передаточное число имеет размерность. К такому типу относятся, например, реечная и канатная (с гибкой связью – канатом) передачи, передача винт-гайка.
3. Согласуются только параметры передаваемого поступательного движения. Передаточ-
ное число u = vвх / vвых .
Класс таких передач сравнительно мал. Это, прежде всего, – клиновая и рычажная передачи.
На практике, работа некоторых передач в режиме мультипликации ( u <1) или по преобразованию поступательного движения во вращательное иногда становится невозможной, т.е. независимо от величины приложенной на входе нагрузки привести в движение звенья передачи не удается. Такое явление называется самоторможением. Оно вызывается тормозящим действием сил трения в звеньях передачи, которые при определенных условиях всегда уравновешивают внешнюю (на входе) нагрузку. В большинстве, самотормозящимися являются передачи, принцип действия которых основан на эффекте клина. Это – клиновая и червячная передачи, передача винт-гайка и другие.
Потребность в передаче выявляется из назначения проектируемой системы или из необходимости обеспечения совместной работы ее частей, т.е.:

95
•согласования вида и параметров движений двигателя и исполнительного устройства. Например, согласовать частоту вращения вала имеющегося двигателя с заданной частотой вращения колеса автомобиля;
•получения заданного, часто – увеличенного, усилия: вращающего момента T или силы F. Например, создать большое выходное усилие при незначительном усилии на входе (домкрат, пресс и т.п.). Изменение нагрузки основывается на законе сохранения энергии: мощность на выходе Nвых с учетом потерь должна равняться мощности на входе Nвх , т.е.
Nвых = Nвх η ,
где η – КПД передачи, а входная и выходная мощность в зависимости от вида движения равна N=F v или N=Tω . И, следовательно, замедление или ускорение передаваемого движения ведет соответственно к увеличению или снижению величины выходной нагрузки;
•обеспечения самоторможения, т.е. передачу движения только в одном направлении;
•передачи движения на значительное или изменяемое расстояние.
Геометрический признак. Выявляется из анализа размещения частей проектируемой системы в пространстве: задается либо внешними условиями, либо возможным или желаемым взаимным расположением входного и выходного звеньев. В соответствии с этим признаком передачи подразделяют на следующие:
Передачи |
|
|
|
|
|
|
|
|
|
|
|
|
|
|
|
|
|
|
|
|
|
|
|
|
|
|
|
|
|
|
|
|
|
|
|
|
|
|
|
|
|
|
||
Функциональный |
|
|
вращательное- |
|
|
|
|
|
|
|||||
признак |
|
|
вращательное |
|
|
|
|
|
|
|||||
(задается вид |
|
|
|
|
|
|
|
|
|
|
|
|
|
|
движения на |
|
|
вращательное- |
|
|
передачи |
||||||||
|
|
|
|
|
|
|
|
|||||||
входе и выходе) |
|
|
поступательное |
|
|
|
|
|
|
|||||
|
|
|
|
|
|
|
|
|||||||
|
|
|
|
передачи– |
||||||||||
|
|
|
|
(и наоборот) |
|
|
|
|||||||
|
|
|
|
|
|
|
трансмиссии |
|||||||
|
|
|
|
|
|
|
|
|
|
|
||||
|
|
|
|
|
|
|
|
|
|
|
|
|||
|
|
|
|
поступательное- |
|
|
|
|
|
|||||
|
|
|
|
|
|
|
|
|
||||||
|
|
|
|
поступательное |
|
|
|
|
|
|
||||
|
|
|
|
|
|
|
|
|
|
|
||||
|
|
|
|
|
|
|
|
|
||||||
Геометрический |
|
|
соосная |
|
|
|||||||||
признак |
|
|
|
|
|
|
|
|
|
|
|
|
|
|
|
|
|
|
|
|
|
|
|
|
|
||||
(определяется |
|
|
с параллельными осями |
|
|
|||||||||
условиями |
|
|
|
|
|
|
|
|
|
|
|
|
|
|
|
|
|
|
|
|
|
|
|
|
|
|
|||
эксплуатации) |
|
|
с пересекающимися осями |
|
|
|||||||||
|
|
|
|
|
|
|
|
|
|
|
||||
|
|
|
|
|
|
|
|
|
|
|
|
|
|
|
|
|
|
|
|
|
|
|
|
|
|||||
|
|
|
|
со скрещивающимися осями |
|
|
||||||||
|
|
|
|
|
|
|
|
|
|
|||||
|
|
|
|
|
|
|
|
|||||||
Устройство |
|
простые |
|
|
|
одноступенчатые |
|
|||||||
(выбирается |
|
|
|
|
|
|
|
|
|
|
|
|
||
|
|
|
|
|
|
|
|
|
|
|
|
|||
конструктивный |
|
|
|
|
|
|
однопоточные |
|
||||||
|
|
|
|
|
|
|
||||||||
признак) |
|
|
|
|
|
|
|
|
|
|
|
|
||
|
|
|
|
|
|
|
|
|
|
|
|
|||
|
|
|
|
сложные |
|
|
многоступенчатые |
|
||||||
|
|
|
|
|||||||||||
|
|
|
|
|
|
|
|
|
|
|
||||
|
|
|
|
|
|
|
|
|
|
|
|
|
|
|
|
|
|
|
|
|
|
|
многопоточные |
|
|||||
|
|
|
|
|
|
|
|
|
|
|
|
|
||
|
|
|
|
|
|
|
|
|
|
|
|
|||
|
|
|
|
|
|
|
|
|
|
рядовые |
|
|||
|
|
|
|
|
|
|
|
|
|
|
||||
|
|
|
|
|
|
|
|
|
|
|||||
|
|
|
|
|
|
|
|
другие |
|
|
|
|||
|
|
|
|
|
|
|
|
|||||||
|
|
|
|
|
|
|
||||||||
Характер взаи- |
|
силовое |
|
|
|
|
фрикционные |
|
||||||
модействия |
|
|
|
|
|
|
|
|
|
|
|
|
||
|
|
|
|
|
|
|
|
|
|
|
|
|||
звеньев |
|
геометри- |
|
|
|
|
|
резьбовые |
|
|||||
(выбирается |
|
ческое |
|
|
|
|
|
|
|
|
|
|
||
|
|
|
|
|
|
|
|
|
|
|
|
|||
конструктивный |
|
|
|
|
|
|
зацеплением: |
|||||||
признак) |
|
|
|
|
- зубчатые эволь- |
|||||||||
|
|
|
|
|
|
|
|
вентные |
||||||
|
|
|
|
|
|
|
- зубчатые с зацеп- |
|||||||
|
|
|
|
|
|
|
|
лением Новикова |
||||||
|
|
|
|
|
|
|
- цевочные |
|||||||
|
|
|
|
|
|
|
- другие |
Рис.8.3 – Классификация механических передач

96
соосные (рис. 8.4а). Они характеризуются совпадением осей вращения входного и выходного валов (например, планетарная и волновая передачи) или совпадением оси вращения и траектории движения входного и выходного звеньев (например, передача винт-гайка). Соосные передачи хорошо компонуются (встраиваются в конструкцию системы) и имеют уменьшенные габариты;
•с параллельным расположением осей вращения или траекторий движения входного и выходного звеньев (рис. 8.4б). К таким передачам относятся цилиндрическая, ременная и цепная;
•с пересекающимися осями или траекториями движения входного и выходного звеньев (рис. 8.4г). Это – коническая и клиновая передачи;
•со скрещивающимися осями или траекториями движения входного и выходного звеньев (рис. 8.4в). Это – червячная, винтовая, реечная и канатная передачи, а также ременная передача с угловым расположением шкивов.
Иногда требуется только передать движение между валами или штоками, расположение которых уже задано. В таком случае передачи подбирают по геометрическому признаку и используют как трансмиссии, с передаточным числом равным единице, т.е. u =1. Часто, это – коническая, ременная и цепная передачи.
Устройство передачи. Характеризует ее конструктивные особенности. Прежде всего,
это:
1. Простота конструкции. Достигается применением одноступенчатых и однопоточных передач. Под ступенью понимается элементарная передача, не допускающая расчленения на более простые передачи и не имеющая внутри себя промежуточных валов или штоков. На рис. 8.4д представлена схема многоступенчатой передачи, в которой ступени последовательно из-
Вход Пере- Выход дача
а) б)
|
|
|
в) |
|
|
|
|
г) |
||
|
|
|
|
|
|
|
||||
|
|
|
|
|
|
|
||||
|
|
|
|
|
|
|
|
|
|
|
|
|
|
|
|
|
|
|
|
|
|
|
|
Ступень |
|
Ступень |
|
|
Ступень |
|
||
|
|
|
I |
|
II |
|
|
|
k |
|
Многоступенчатая передача
д)
е) ж)
Рис.8.4 – Блок-схемы основных видов передач (прямоугольники
– передачи, линии и стрелки – входные и выходные звенья): а - соосная, б – с параллельным расположением осей входного и выходного звеньев, в – с пересекающимися осями (в данном случае - межосевой угол равен 90° ), г – со скрещивающимися осями, д – многоступенчатая, е – многопоточная, ж – с раздвоенным выходом(входом)
97
меняют характеристики движения. На рис. 8.4е показана блок-схема многопоточной передачи. Здесь движение (мощность) от входного звена к выходному передается несколькими потоками (на входе разветвляется на ряд потоков, которые потом к выходу снова сливаются в один);
2. Удобство компоновки передачи. Часто достигается применением многоступенчатых, т.е. последовательно сочлененных элементарных передач. Использование передач с различной пространственной ориентацией входных и выходных звеньев (рис. 8.4 а, б, в, г) или/и изменение взаимного пространственного расположения отдельных ступеней позволяет достичь необходимой геометрической конфигурации (компоновки) всей передачи в целом. С другой стороны, общее передаточное число такой сложной передачи равно произведению передаточных чисел отдельных ступеней, т.е.
u = uI uII ... uk ,
где k – количество ступеней (рис. 8.4д). Представление передачи в виде многоступенчатой (особенно при больших значениях передаточного числа u) ведет к уменьшению габаритов передачи. Целесообразность выбора числа и вида ступеней, последовательности их расположения устанавливается на основе экспериментальных и теоретических исследований.
Например, конструкция механических часов. Потребное передаточное число механизма, обеспечивающее согласование частоты вращения маятника и, допустим, часовой стрелки, составляет около 40 000. Габариты одноступенчатой, например, цилиндрической передачи с таким передаточным числом составили бы десятки метров, что вряд ли позволило разместить ее не только на руке, но и в комнате. Многоступенчатая же передача свободно размещается в небольшом корпусе;
3.Повышение нагрузочной способности. Достигается многопоточностью, т.е. передачей механической энергии одновременно несколькими звеньями (потоками). При этом многопоточность может использоваться не только для передачи движения с входного звена к выходному (рис. 8.4е), но и для организации нескольких входов или выходов (рис. 8.4ж). Многопоточность позволяет повысить надежность всей передачи, так как параллельные потоки взаимно подстраховывают друг друга. Но следует помнить, что многопоточные передачи – статически неопределимые системы и, как следствие, заключают в себе некоторую неопределенность количественного распределения мощности по отдельным направлениям;
4.Передача движения на заданное расстояние или изменение его направления при сохранении значения передаточного числа. Достигается применением рядовых передач (особенность их конструкции будет рассмотрена позже, на примере цилиндрических передач).
Характер взаимодействия звеньев. Представляет собой физический принцип передачи нагрузки с одного звена на другое. Взаимодействие возможно:
•посредством надавливания одних деталей на другие. Это – так называемое геометрическое замыкание деталей (звеньев). Здесь важное значение имеет форма контактирующих поверхностей – ее конкретный вид определяет эффективность функционирования, прочность, жесткость и другие факторы;
•благодаря действию сил трения, тяжести, инерции, магнетизма и т.п. Это – силовое взаимодействие (замыкание) звеньев. Оно часто является косвенным результатом действия других нагрузок, таких как, например, сила давления, приводящая к появлению силы трения. К передачам с силовым замыканием, прежде всего, относятся фрикционные передачи, в которых движение передается посредством сил трения. Эти передачи характеризуются простотой форм рабочих звеньев, технологичностью, но требуют специальных нажимных устройств, обладают проскальзыванием и повышенным износом рабочих поверхностей. Усилие поджатия звеньев может в несколько раз превышать рабочую нагрузку, что дополнительно и существенно нагружает элементы передачи, снижает их прочность и, следовательно, требует увеличенных габаритов.
Рассмотрим подробнее основные формы контактирующих поверхностей в передачах с
геометрическим замыканием звеньев. Подавляющее их большинство составляют передачи с резьбовым соединением (винт-гайка) и зубчатым зацеплением.
98
Резьбовое соединение. Резьба характеризуется формой профиля (основные профили резьб показаны на рис. 8.5) и следующими параметрами:
•число заходов z, т.е. число винтовых линий (ниток), которые образуют резьбу. Различают однозаходные и многозаходные резьбы;
•направление навивки винтовой линии: правая (линия закручивается, удаляясь, по часовой стрелке и соответствует естественному заворачивающему движению правой руки человека) и левая;
•наружный диаметр резьбы d, который является и ее номинальным размером;
•внутренний диаметр резьбы d1, т.е. диаметр отверстия в гайке “на просвет”;
•средний диаметр резьбы d2. На этом диаметре толщина витков равна ширине впадин;
•шаг резьбы Р. Для многозаходных резьб также используют понятие хода винта, который равен произведению шага на заходность (P·z) и соответствует осевому смещению винта за один оборот;
•рабочая высота профиля h, по которой происходит контакт витков винта и гайки.
Треугольный профиль (рис. 8.5а). Наиболее распространен, поскольку технологичен и стандартизован (самый первый в мире стандарт – на дюймовые резьбы, был разработан в Англии Витвортом в 1840 году). Ему свойственно повышенное трение между витками и, как следствие, – склонность к самоторможению.
Различают два основных вида треугольных резьб – метрическая и дюймовая. Метрическая резьба. Характеризуется углом профиля α =60°, наружным диаметром и ша-
гом. В обозначении резьбы указывается ее вид – М (метрическая), и номинальный диаметр (для резьб с крупным шагом, т.е. с наибольшим из приведенных в стандарте для данной величины диаметра. Например, М20), а для резьб с мелким шагом – еще и величина шага (например, М20х2). Для левозаходной резьбы в конце обозначения ставят буквы LH (например, М20х2LH). В обозначении многозаходной резьбы вместо шага приводят величину хода и, рядом в скобках, – букву Р и значение шага (например, М20х6(Р2), что соответствует трехзаходной резьбе с шагом 2мм).
Стандартные посадки резьбовых деталей образуются на основе четырех полей допусков для винтов (h, g, e, d) и двух – для гаек (H, G) и с 3-ей по 9-ую степеней точности. Допуск резьбы указывается после обозначения размера через тире, например, М20х2 –7h6h для винта и М20х2 –5H6H для гайки. Он состоит из допуска на средний диаметр, помещаемого на первом месте (в приведенных примерах 7h и 5H), и допуска на наружный диаметр винта (6h) или внутренний диаметр гайки (6H). Если обозначения полей допусков на оба диаметра совпадают, то оно приводится только один раз (например, М12–6g. Здесь допуски среднего и наружного диаметров винта совпадают и равны 6g). Посадки резьбовых деталей обозначаются дро-
бью, например, М12–6H/6g, М20х2LH–5H6H/6e.
Степени точности 4 и 5 обычно относят к точным, 6 – к средней, 7, 8 – к грубым. Если длина свинчивания мала (менее эмпирического значения 2,24*Р*d0,2), то рекомендуют степень точности понижать на единицу. Для больших длин свинчивания (более 6,7*Р*d0,2) степень точности рекомендуют повышать на единицу. При отсутствии особых условий основным видом сопряжений являются посадки с гарантированным зазором – 6H/6g, 7H/8g.
Дюймовая резьба. Характеризуется углом профиля α =55° и числом витков резьбы на один дюйм. Используется в деталях из стран, в которых действует дюймовая система мер, либо в деталях старых машин, и в трубной резьбе. В связи с действием в нашей стране метрической системы (SI), изготовление дюймовых резьб осложняется возможным отсутствием необходимого оборудования и инструмента.
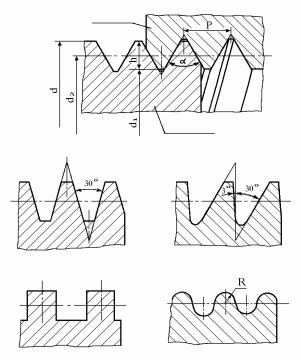
99
Трапецеидальный профиль (рис. 8.5б). Стандартизован, технологичен, обладает улучшенными кинематическими и прочностными характеристиками. Принципы обозначения трапецеидальной и метрической резьб подобны, только вид резьбы обозначается буквами Tr (международное обозначение) или Трап, например, Tr 40х6–7H/7e или Трап 40х6–7H/7e.
Упорный профиль (рис. 8.5в). Стандартизован, но по сравнению с трапецеидальным профилем несколько сложнее в изготовлении. Позволяет сочетать повышенную прочность витков и невысокие потери на трение, но при одностороннем действии нагрузки – при контакте витков по рабочей стороне, имеющей угол наклона 3°. Резьба обозначается буквами Уп, диаметром и шагом, например, Уп 40х6.
Прямоугольный профиль (рис. 8.5г). Нестандартизован, сложен в изготовлении, форма профиля по высоте не является равнопрочной, но способен обеспечить наивысший из всех профилей КПД резьбовой передачи и хорошее взаимное центрирование винта и гайки.
Круглый профиль (рис. 8.5д). Нестандартизован, сложен в изготовлении, но позволяет существенно снизить концентрацию напряжений в резьбе и резьбовых деталях.
Зубчатое зацепление. Движение передается благодаря контактному взаимодействию профилированных выступающих элементов деталей – зубьев. Форма рабочих (т.е. контактирующих) поверхностей определяется условиями изготовления и эксплуатации передачи и может быть различной. Наиболее распространено зацепление зубьев с эвольвентным профилем рабочих поверхностей, менее – зацепление Новикова и цевочное зацепление.
Эвольвентное зацепление (теоретически предложено и разработано Л.Эйлером в конце 18 века для замены использовавшихся тогда в колесах зубьев с треугольным профилем, удобных в изготовлении, но быстро изнашивавшихся, с низким КПД и вызывавших неравномерность передаваемого движения). Профиль боковых поверхностей зубьев соответствует правой (одна сторона) и левой (другая сторона) эвольвенте (рис. 8.6а). Эвольвента является разновидностью спирали, которая вычерчивается любой точкой прямой линии при перекатывании ее без проскальзывания по окружности, называемой основной (эвольвента также вычерчивается
гайка
винт а) треугольный профиль резьбы
б) трапецеидальный профиль |
в) упорный профиль |
г) прямоугольный профиль |
д) круглый профиль |
Рис.8.5 – Основные виды профилей резьб

100
концом натянутой нити при разматывании ее с цилиндра, называемого основным). Эвольвентное зацепление характеризуется:
•постоянством мгновенного передаточного числа (в любой промежуток времени при равномерном движении ведущего звена ведомое также будет двигаться равномерно). Профили взаимодействующих зубьев, удовлетворяющие этому условию, называют сопряженными;
•высокой технологичностью (простота изготовления как эвольвентных колес, так и необходимого для их нарезания инструмента);
•высоким КПД и малым трением (зуб одного звена-колеса при передаче движения катится относительно зуба другого колеса, и, следовательно, между взаимодействующими звенья-
ми реализуется трение качения).
Эти достоинства обеспечили эвольвентному зацеплению наибольшее распространение в машиностроительных зубчатых передачах (более 90% от общего числа зубчатых колес).
Технологичность зацепления базируется на том, что в частном случае, когда радиус колеса бесконечно возрастает и колесо становится зубчатым стержнем-рейкой, криволинейная эвольвентная боковая сторона зуба вырождается в прямую линию (рис. 8.6в). Форма такой рейки служит основой для производящего исходного контура инструмента для нарезания эвольвентного зацепления. Параметры исходного контура стандартизованы (хотя допускаются и отклонения). Это, прежде всего:
•профильный угол α – угол наклона боковой стороны зуба к его оси. Его наиболее распространенное значение равно αo =20° (еще допустимо значение в 30°);
•модуль m. Его величина пропорциональна шагу р, замеряемому вдоль средней прямой, с коэффициентом пропорциональности π, т.е.
m= p / π .
Средняя прямая – линия, вдоль которой толщина зуба равняется ширине впадины. Она также условно по высоте делит зуб на две равные части: головку и ножку. Понятие модуля было введено исторически для упрощения расчетов (исключения из расчетов иррационального числа π ) и теперь используется вместо шага как основная характеристика эвольвентных передач. Величины модуля устанавливаются ГОСТ 9563.
При нарезании зубчатых колес стандартным инструментом их геометрическими параметрами будут (рис.6а):
р – шаг по делительной окружности. Делительной является окружность, пересекающая профиль зуба в точке, в которой профильный угол равен стандартному значению αo ;
m – модуль зацепления;
х – коэффициент смещения. Он измеряется в долях модуля и характеризует величину смещения инструмента относительно его номинального положения:
а) б)
в)
Рис.8.6 – Эвольвентное зубчатое колесо (а – вид спереди, б – вид сбоку) и профиль производящей рейки (в)