
Детали машин и основы конструктирования
.pdf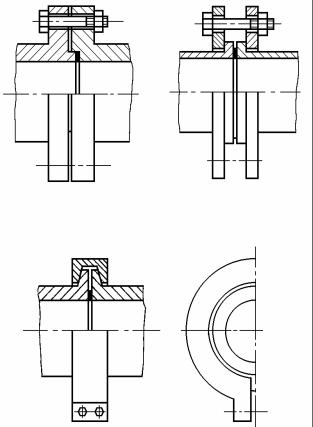
181
ски повторяющихся перегрузках целесообразны муфты с автоматическим восстановлением соединения, т.е. по окончании действия перегрузки муфта сама снова замыкает кинематическую цепь. Муфты этого типа сложнее в устройстве, но проще в эксплуатации.
Основным представителем муфт с неавтоматическим восстановлением является муфта с разрушаемым элементом. В качестве такого элемента часто применяют штифты (рис. 8.78), соединяющие две полумуфты. При перегрузке штифт, параметры которого рассчитываются на передачу определенной величины крутящего момента, срезается (ломается), и вращение с ведущего вала на ведомый не передается. Для восстановления кинематической цепочки привод останавливается, и разрушенный штифт заменяется на новый. Обычно штифт располагают в осевом направлении, как показано на рисунке. Число штифтов может быть больше одного, но тогда из-за статической неопределенности точность срабатывания муфты снижается.
В качестве предохранительных муфт с автоматическим восстановлением можно использовать сцепные муфты, но с постоянно действующим усилием поджатия полумуфт. Величина усилия должна быть настроена на предельную величину передаваемого момента. Поджатие удобно осуществлять посредством пружины: возможна простая регулировка усилия прижатия полумуфт и слабая зависимость его величины от степени износа (и следовательно, сближения) рабочих поверхностей.
Помимо перечисленных функций муфты также способны:
•передавать вращение только в одном направлении (обгонные муфты);
•автоматически соединять и разъединять валы при достижении заданной частоты вращения (центробежные муфты) и др.
8.5.10 Прочно-плотные соединения (соединения трубопроводов)
Соединения трубопроводов, шлангов, крышек и т.п. предназначаются не только для скрепления деталей, но также обеспечения герметичности узла, удобства его монтажа. Наиболее распространены следующие виды соединений:
• фланцевое соединение. Здесь, например, |
|
|
трубы стягиваются фланцами посредством |
|
|
резьбовых деталей. Фланцы могут выпол- |
|
|
няться заодно с трубами (рис. 8.79а), либо в |
|
|
виде самостоятельных колец (накладные, |
|
|
рис. 8.79б). Соединение центрируется по- |
а) |
б) |
средством буртика (рис. 8.79а), либо уста- |
||
новкой болтов без зазора. В неответствен- |
|
|
ных соединениях центровка может отсутст- |
|
|
вовать (например, как на рис. 8.79б). Для |
|
|
хорошей герметичности контактирующие |
|
|
поверхности должны быть параллельны; |
|
|
• бугельное соединение (рис. 8.79в). Конст- |
|
|
рукция включает косые фланцы, охвачен- |
|
|
ные хомутом. Стягивая концы хомута, на- |
|
|
пример, болтами, сдавливают фланцы (в |
|
|
радиальном направлении) и заставляют их |
|
|
плотно прижиматься друг к другу (в осевом |
|
в) |
направлении). Соединение удобно при час- |
|
|
той сборке-разборке, но хомуты испыты- |
Рис.8.79 Фланцевое (а,б) и бугельное |
|
вают значительные напряжения; |
||
|
(в) соединения |

182
•штуцерные соединения. Применяют для соединения трубопроводов небольших диаметров. Штуцер – слово немецкого происхождения. Наряду с ним используют термин "нипель" аналогичного значения, но английского происхождения. Существует много разновидностей штуцерных соединений, пример одного из которых показан на рис. 8.80. Здесь на конце одной трубы нарезается резьба, а у другой имеется выступ. При заворачивании гайка за выступ притягивает торец одной трубы (на рисунке – правой) к торцу трубы с резьбой.
Наряду с затяжкой по плоским торцам применяют затяжку по конической поверхности. Соединение компактно и удобно в монтаже. Соединения трубопроводов рассчитывают на прочность, жесткость и герметичность.
Рис.8.80 – Штуцерное соединение
8.6 Пружины
Пружины – это элементы, функционирование которых основано на явлении упругой податливости. Общая классификация пружин представлена на рис. 8.81. В основном пружины используются в качестве элемента, обеспечивающего силовое замыкание звеньев, аккумулятора механической энергии, динамического и измерительного элементов.
Пружины как элемент, обеспечивающий силовое замыкание звеньев. Благодаря своей по-
датливости пружины способны оказывать заданное силовое воздействие на детали, не смотря на их заметные относительное смещение или деформацию (изменение размеров), разброс действительных размеров или неточность взаимного положения. При силовом замыкании на выбор пружины влияет не только потребная величина усилия замыкания, но и допустимые пределы его изменения при удлинении пружины в процессе работы устройства. Так, при силовом замыкании подвижных деталей, допускающих значительные относительные смещения, пружины выбирают более податливыми.
Пружины как источник механической энергии, механический аккумулятор. Энергия запа-
сается и впоследствии высвобождается благодаря упругой деформации пружины. Величина энергии пропорциональна степени деформации и величине жесткости пружины. КПД механического аккумулятора тем выше, чем меньше гистерезис у материала, из которого изготовлена пружина.
Пружины как динамический элемент. Введение такого элемента изменяет упругодинамическую характеристику всей системы с одной из следующих целей:
•пружины как амортизаторы (буферы). Установка пружины между соударяющимися объектами (деталями, системами и т.п.) снижает динамические нагрузки (реакции в опорах или инерционные силы торможения). Степень смягчения нагрузок возрастает с ростом податливости пружины. При этом энергия динамического воздействия накапливается в пружине в виде обратимой энергии ее деформации;
•пружины как виброгасители, защищающие конструкцию от нежелательных резонансных колебаний. Это достигается, например, введением в конструкцию пружин с нелинейной характеристикой, что позволяет изменять жесткость системы с ростом амплитуды ее колебаний, и следовательно, – уходить от резонансной частоты;
•пружины как демпферы (бамперы), поглащающие механическую энергию соударения твердых тел (деталей, систем и т.п.) и предотвращающие последующее возникновение колебаний. В механических демпферах, в отличие от амортизаторов, кинетическая энергия поглащается необратимо, например, преобразуется сначала в энергию деформации элемен-

183
та демпфера, потом – в тепловую, и затем отводится и рассеивается в окружающем пространстве. Преобразование поглащаемой энергии в тепловую происходит благодаря внешнему (связанному с износом), либо внутреннему трению. В последнем случае выбирается упругий материал с большим гистерезисом. Возможны конструкции разовых демпферов, в которых энергия поглащается пластически деформируемым элементом.
Пружины
Функциональное назначение:
задается
Вид создаваемой нагрузки:
выявляется
Силовое замыкание
Источник механической энергии
амортизатор
Динамический виброгаситель элемент
демпфер
Измерительный элемент
Пружины сжатия
Пружины растяжения
Пружины кручения
Особенности |
|
Вид |
|
|
– линейная |
характеристики |
|
|
|
– нелинейная |
|
|
|
|
|||
|
|
|
|
||
пружины |
|
|
|
|
|
|
|
|
|
|
|
выбирается |
|
Жесткость |
|
|
– обычная |
|
|
|
|
|
– повышенная |
|
|
|
|
|
|
|
|
|
|
|
|
|
|
Внутреннее |
|
|
– малое |
|
|
трение |
|
|
– большое |
|
|
|
|
|
|
Форма пружины |
|
Спиральные |
|
|
Плоские |
выбирается |
|
|
|
|
|
|
|
|
|
|
|
|
|
|
|
|
Пространственные: |
|
|
|
|
|
– цилиндрические |
|
|
|
|
|
– фасонные |
|
|
|
|
|
|
|
|
|
|
|
|
|
|
Тарельчатые |
|
|
|
|
|
|
|
|
|
|
|
|
|
||
|
|
Кольцевые |
|
|
|
|
|
|
|
|
|
|
|
|
|
|
|
|
|
Пластинчатые |
|
|
|
|
|
|
|
|
|
|
|
|
|
|
|
|
|
Сплошные |
|
|
|
|
|
|
|
|
|
|
|
|
|
||
Конструкция |
|
Простые |
|
|
|
пружины |
|
|
|
|
|
|
|
|
|
|
|
выбирается |
|
Сложные |
|
|
– составные |
|
|
|
|
|
– многожильные |
|
|
|
|
|
|
|
|
|
|
|
|
Рис. 8.81 – Классификация пружин
Пружина как измерительный элемент, позволяющий определять величину усилия по степени деформации (удлинению или закручиванию). Для данных целей предпочтительны пружины, удобные для тарирования (градуировки). Прежде всего, это – пружины с линейной характеристикой.

184
В зависимости от направления и вида воспринимаемых нагрузок (деформаций) выделяют пружины растяжения, сжатия и кручения. Вид пружины влияет на способ ее соединения с взаимодействующей деталью (законцовку пружин).
Важным свойством пружин является их характеристика, т.е. зависимость развиваемого усилия от степени деформации (удлинения, сжатия или закручивания). График характеристики может иметь различный вид (например, как показано на рис. 8.82), в зависимости от которого различают:
пружины с линейной (линия 1) и нелинейной (линии 2,3) характеристиками (рис. 8.82а);
•пружины с обычной и повышенной жесткостью. Понятие “повышенная жесткость” – относительное и говорит о более крутом подъеме линии характеристики относительно рассматриваемой или базовой;
•пружины с относительно малым и большим внутренним трением (гистерезисом). На графике (рис. 8.82б) величине гистерезиса, как потерям энергии при циклической работе, соответствует площадь, ограниченная кривыми нагружения (3) и разгружения (2). Показанная на рисунке кривая 1 соответствует начальному нагружению. В идеальной пружине, у которой отсутствует внутреннее трение, кривая начального нагружения и кривые последующего цикла нагружение-разгружение совпадают.
Конструкции пружин могут иметь различную форму. Наиболее распространены, как технологичные, спиральные пружины. Они навиваются из проволоки круглого (рис. 8.83а) или прямоугольного (рис. 8.83б) сечения (прямоугольное сечение позволяет лучше использовать рабочее пространство пружины). Если все витки лежат в одной плоскости, то такая пружина относится к плоским: ее витки плотно упакованы и обеспечивают пружине компактность. При
а) б)
Рис.8.82 – Вид характеристики пружин
пространственном расположении витки могут лежать на цилиндрической или иной, фасонной поверхности. Цилиндрические пружины технологичны, а фасонные, например, конические, бочкообразные и т.п., – позволяют получить желаемую нелинейную характеристику или лучше вписаться в рабочее пространство узла.
Цилиндрические спиральные пружины стандартизированы и характеризуются следующими параметрами (рис. 8.83а):
•d – диаметр круглой проволоки (либо ширина b и высота h поперечного сечения проволоки прямоугольного сечения);
•D – средний диаметр пружины;
•h – шаг витков в ненагруженном (исходный параметр) и нагруженном состоянии;
•H – длина рабочей части пружины в ненагруженном и нагруженном состоянии;
•направление навивки – правое (типовое) или левое (как показано на рисунке). Вспомогательными параметрами служат:
•D+d – наружный диаметр пружины. Его величина незначительно изменяется при деформации пружины;
•c=D/d – индекс пружины (для проволоки прямоугольного сечения c=D/b). С ростом величины индекса податливость пружины возрастает. Индекс стандартных пружин выражается целым числом от 4 до 12;
•i=H/h – число рабочих витков пружины.

185
Цилиндрические пружины делятся на три класса, в свою очередь, подразделяемые на разряды:
1 – для больших циклов нагружения;
2 – для средних циклов нагружений;
3 – для малых циклов нагружений. Установлены три группы точности пружин:
•первая группа – отклонения по силам и упругим перемещениям до ±5%;
•вторая группа – до ±10%;
•третья группа – до ±20%.
Тарельчатые пружины соответствуют шайбам конической, сферической, гофрированной, многолепесковой и иных форм. В большинстве случаев эти пружины обладают нелинейной характеристикой и повышенной жесткостью.
Тарельчатые пружины конической формы (рис. 8.84а) стандартизированы и выпускаются в виде готовых изделий. Они выполняются с наружным диаметром D от 28 до 300 мм и высотой конуса hо от 0,6 до 9 мм для рабочих нагрузок (усилий сжатия) до 520кН. Угол подъема конуса составляет 2...6о. Пружины подразделяются на следующие:
а) |
б) |
в) |
Рис.8.83 – Вид и параметры цилиндрической пружины
•нормальной (Н) и повышенной (П) точности;
•статического (С), динамического (Д) и многократного действия нагрузки;
•большой и малой (но все равно больше, чем у спиральных пружин) жесткости.
Для повышения податливости или получения требуемой величины осадки тарельчатые пружины могут устанавливаться в виде комплекта (рис. 8.84б). Расположение тарелок пакетами, как показано на рис. 8.84в, вследствие трения по конической поверхности позволяет использовать их в качестве демпферов.
а)
б) в)
Рис. 8.84 – Тарельчатые пружины

186
Кольцевые пружины (например, типа представленной на рис. 8.85) состоят из набора чередующихся колец с наружными и внутренними коническими поверхностями. При приложении осевой силы кольца деформируются в радиальном направлении (внутренние – сжимаются, наружные – растягиваются), а вследствие малости угла конуса эти небольшие деформации преобразуются в значительную суммарную осевую осадку. Благодаря большому внешнему трению кольцевые пружины обладают высокой демпфирующей способностью – до 60% энергии, воспринимаемой за цикл нагружения, необратимо рассеивается. Кольцевые пружины требуют высокой точности изготовления размеров.
Пластинчатые пружины имеют форму защемлен-
ных с одного края полосок или пластин, отдельных лепестков и т.п. Они обычно предназначаются для создания прижимающих усилий и работают на изгиб (например, в контактах электроприборов, рессорах машин).
Сплошные пружины представляют собой объемное тело и работают вследствие объемной деформации: рас- тяжения-сжатия, сдвига и кручения. В качестве материала таких пружин широко применяется резина.
В зависимости от места в узле, отведенного пружине, потребной характеристики и осадки возможны кон-
струкции одинарной и сложной пружин. В свою очередь, Рис.8.85 – Кольцевая пружина различают следующие конструкции сложных пружин:
•многожильные пружины. Обычно, это спиральные цилиндрические пружины, изготовленные из тросов, т.е. свитых вместе тонких проволок (рис. 8.83в). Пружины обладают кусоч- но-линейной характеристикой, повышенной податливостью и демпфирующей способностью. С другой стороны, пружина сложна в изготовлении, интенсивен износ проволочек;
•составные пружины, которые получают набором из отдельных пружин в пакет последовательно (например, как на рис. 8.84б), либо параллельно (например, одна пружина вставляется в другую). Первый случай используют для повышения податливости и осадки пружины, второй – для повышения ее жесткости и более полного использования объема, отведенного под пружину.
8.6 Смазывание машин
Смазывание выполняет вспомогательные функции и служит для повышения эффективности и качества работы машины. Его роль настолько велика, что во многих случаях не только отсутствие смазки, но и неправильное смазывание приводят к отказу машины. Общее представление о смазывании дано на рис. 8.86.
Под смазыванием подразумевается использование смазки и выполнение определенных операций.
Выбор вида смазки зависит от конкретных условий и режима эксплуатации, материалов контактирующих деталей и состояния их поверхностей. Существующие смазки подразделяются на следующие типы:
•твердая (графит, двусернистый молибден и т.д.). Эффективна в экстремальных условиях (вакуум, очень высокие и низкие температуры, высокие требования к чистоте окружающей среды и т.п.) и при редких перемещениях;
•пластичная (солидолы, консталины и т.д.). Удерживается на вертикальных и открытых поверхностях, хорошо герметизирует и консервирует детали и узлы, упрощает обслуживание (и конструкцию), особенно, труднодоступных узлов;
•жидкая (легкие, средние и тяжелые индустриальные масла, турбинные, моторные и трансмиссионные масла, вода и т.п.). Позволяет значительно уменьшить коэффициент трения, эффективно отводит тепло, защищает от коррозии;
187
•воздушная (газообразная). Позволяет максимально снизить величину коэффициента трения, особенно в опорах, имеет неограниченный ресурс, экологически чистая.
Смазывание осуществляется, прежде всего, в следующих целях:
•уменьшение потерь на трение. Для этого используются смазки с антифрикционными свойствами. По возможности смазка должна разделять трущиеся поверхности и заменять сухое трение на трение между слоями смазки;
•снижение или предотвращение износа и схватывания рабочих поверхностей. Для этого используются противоизносные и противозадирные смазки;
•отвод тепла, выделяющегося вследствие трения, от рабочих поверхностей деталей. Для осуществления интенсивного теплоотвода предпочтительны жидкие смазки с высокой теплоемкостью и малой вязкостью;
•предохранение от коррозии. Для этого предпочтительны пластичные и твердые смазки с антикоррозионными свойствами и пониженной агрессивностью;
•герметизация узлов. Для этого предпочтительны пластичные смазки с высокими вязкостью
иадгезионными свойствами;
•поглощение шумов, возникающих при работе машин и их узлов. Для этого применяются смазки, снижающие трение, как основной источник шума, а также смазки в жидком или пластичном состоянии, которые хорошо поглощают звук, амортизируют ударные нагрузки
идемпфируют колебания.
Вмашинах возможна индивидуальная или общая системы смазывания. Индивидуальное смазывание учитывает особенности каждого узла, но сложнее, так как нуждается в независимых смазывающих устройствах. Его применяют при удаленности друг от друга смазываемых узлов, либо когда для каждого узла требуется различная по виду или состоянию смазка.
По способу подачи смазки к рабочим поверхностям различают картерную и циркуляционную системы смазывания.
При картерной системе рабочие поверхности постоянно погружены или периодически окунаются в жидкую смазку. Смазка находится в специальной ванне (в корпусах – в картере), форма и расположение которой выбирается с учетом следующих условий:
•разбрызгиваемая при работе смазка должна иметь возможность свободно стекать и полностью собираться в этой ванне;
•при сливе смазки ванна должна свободно и полностью опорожняться, а смазка – не скапливаться и не застаиваться в возможных углублениях, пазах и т.п.;
•объем масляной ванны должен обеспечивать свободное погружение рабочих поверхностей на требуемую глубину, длительное сохранение свойств смазки (чем больше объем, тем дольше сохраняются ее свойства) и поддержание теплового баланса узла. С ростом глубины погружения смазывание становится эффективнее, но и возрастают потери энергии на непроизводительное перемешивание, существенно зависящие от вязкости смазки и скорости вхождения детали в ванну.
При картерной системе рабочие поверхности постоянно погружены или периодически окунаются в жидкую смазку. Смазка находится в специальной ванне (в корпусах – в картере), форма и расположение которой выбирается с учетом следующих условий:
•разбрызгиваемая при работе смазка должна иметь возможность свободно стекать и полностью собираться в этой ванне;
•при сливе смазки ванна должна свободно и полностью опорожняться, а смазка – не скапливаться и не застаиваться в возможных углублениях, пазах и т.п.;
•объем масляной ванны должен обеспечивать свободное погружение рабочих поверхностей на требуемую глубину, длительное сохранение свойств смазки (чем больше объем, тем дольше сохраняются ее свойства) и поддержание теплового баланса узла. С ростом глубины погружения смазывание становится эффективнее, но и возрастают потери энергии на непроизводительное перемешивание, существенно зависящие от вязкости смазки и скорости вхождения детали в ванну.

188
|
|
Смазывание |
|
|
|
|
|
|
|
|
|
|
|
|
|
|
|
|
|
|
|
|
|
|
|
|
|
|
|
|
|
|
|
|
|
|
|
|
|
|
|
|
Функциональное |
|
|
|
|
Уменьшение потерь на трение |
|||||||
|
|
назначение: |
|
|
|
|
|
|
|
|
|
|
|
|
|
|
|
|
|
|
|
|
|
|
|||
|
|
задается |
|
|
|
|
Снижение износа |
||||||
|
|
|
|
|
|
|
|
|
|
|
|
|
|
|
|
|
|
|
|
|
|
|
|
|
|
|
|
|
|
|
|
|
|
|
|
|
|
|
|
||
|
|
|
|
|
|
|
|
Теплоотвод |
|||||
|
|
|
|
|
|
|
|
|
|
|
|
||
|
|
|
|
|
|
|
|
|
|
|
|
||
|
|
|
|
|
|
|
|
Предохранение от коррозии |
|||||
|
|
|
|
|
|
|
|
||||||
|
|
|
|
|
|
|
|
|
|
|
|
||
|
|
|
|
|
|
|
|
|
|
|
|
||
|
|
|
|
|
|
|
|
Герметизация |
|||||
|
|
|
|
|
|
|
|
|
|
|
|
|
|
|
|
|
|
|
|
|
|
|
|
|
|
|
|
|
|
|
|
|
|
|
|
Снижение шума |
|||||
|
|
|
|
|
|
|
|
|
|
|
|
|
|
|
|
|
|
|
|
|
|
|
|
|
|
|
|
|
|
|
|
|
|
|
|
и др. |
|
|
|
|
|
|
|
|
|
|
|
|
|
|
|
|
|
||
|
|
|
|
|
|
|
|
|
|
|
|
|
|
|
|
|
|
|
|
|
|
|
|
|
|
|
|
|
Обеспечение |
|
|
|
|
Система |
|
|
|
|
Общая |
||
|
|
смазывания |
|
|
|
смазывания |
|
|
|
|
|
||
|
|
|
|
|
|
|
|
|
|||||
|
|
выбирается |
|
|
|
|
|
|
|
|
|
|
|
|
|
|
|
|
|
|
|
|
Индивидуальная |
||||
|
|
|
|
|
|
|
|
|
|
|
|
||
|
|
|
|
|
|
|
|
|
|
|
|
|
|
|
|
|
|
|
|
|
|
|
|
|
|
|
|
|
|
|
|
|
|
|
|
Картерная |
|
|
Окунанием |
||
|
|
|
|
|
|
|
|
|
|
|
|
|
|
|
|
|
|
|
|
|
|
|
|
|
|
|
|
|
|
|
|
|
|
|
|
|
|
|
|
|
Центробеж- |
|
|
|
|
|
|
|
|
|
|
|
|
|
ными силами |
|
|
|
|
|
|
|
|
|
|
|
|
|
|
|
|
|
|
|
|
|
|
|
|
|
|
|
Разбрызги- |
|
|
|
|
|
|
|
|
|
|
|
|
|
ванием |
|
|
|
|
|
|
|
|
|
|
|
|
|
|
|
|
|
|
|
|
|
|
Циркуляци- |
|
|
Струйная |
||
|
|
|
|
|
|
|
|
онная |
|
|
|
||
|
|
|
|
|
|
|
|
|
|
|
|||
|
|
|
|
|
|
|
|
|
|
|
|
|
Капельная |
|
|
|
|
|
|
|
|
|
|
|
|||
|
|
|
|
|
|
|
|
|
|
|
|
|
|
|
|
|
|
|
|
|
|
|
|
|
|
|
|
|
|
|
|
|
|
|
|
|
|
|
|
|
Масляным |
|
|
|
|
|
|
|
|
|
|
|
|
|
туманом |
|
|
|
|
|
|
||||||||
|
|
Подача и отвод смазки |
|
|
|
|
|
||||||
|
|
|
|
|
|
|
|
|
|
|
|
||
|
|
|
|
|
|
|
|
|
|
|
|
|
|
|
|
Контроль |
|
|
|
|
уровня |
|
|
– фонарные |
|||
|
|
параметров |
|
|
|
|
|
|
|
|
|
– трубчатые |
|
|
|
|
|
|
|
|
|
|
|
|
|||
|
|
|
|
|
|
|
|
|
|
|
|
|
– жезловые |
|
|
|
|
|
|
|
|
давления |
|
|
|||
|
|
|
|
|
|
|
|
|
|
– крановые |
|||
|
|
|
|
|
|
|
|
|
|
|
|
|
|
|
|
|
|
|
|
|
|
|
|
|
|
|
– другие |
|
|
|
|
|
|
|
|
|
|
|
|
|
|
|
|
|
|
|
|
|
температуры |
|
|
||||
|
|
|
|
|
|
|
|
|
|
||||
|
|
|
|
|
|
|
|
|
|
||||
|
|
|
|
|
|
|
|
|
|
|
|
|
|
и др.
и др.
Рис. 8.86 – Назначение и обеспечение смазывания
При смазывании пластичными смазками их наносят на рабочие поверхности или заполняют часть свободного пространства узла. Такой способ можно отнести к картерной системе. Если соседние узлы смазываются различной по консистенции смазкой, то во избежание вымывания пластичной смазки пространство, где она находится, должно быть изолировано от пространства с жидкой смазкой, например, мазеудерживающими кольцами (рис. 8.87а). Пластичная смазка может закладываться в узлы при сборке или во время профилактических осмотров, либо периодически подаваться под давлением посредством масленок. На рис. 8.87а показана стандартная пресс-масленка, позволяющая подавать масло под давлением при помощи шприца.
Картерная система проста и удобна, но смазка здесь не очищается и со временем засоряется неизбежными продуктами коррозии и износа. При больших скоростях движения частей машины (например, при входе в ванну сателлитов планетарной передачи) смазка чрезмерно разбрызгивается и быстро окисляется, плохо удерживается и сбрасывается центробежной силой.

189
В случае, когда несколько узлов смазываются из одной масляной ванны, но недопустимы попадание вместе со смазкой продуктов износа из одного узла в другой (например, продуктов износа зубчатых колес в подшипниковый узел) либо чрезмерное затопление узла потоком смазки, создаваемого при работе другого узла (например, при работе червяка), соседние пространства разделяют маслоотражательными кольцами (рис. 8.87б).
Поскольку уровень смазки ограничен, то для смазывания высоко расположенных узлов применяют комбинированный способ, сочетающий картерную и циркуляционную системы. В зависимости от взаимного расположения узла и ванны, скорости движения деталей и подаваемого количества смазки возможны следующие его способы:
•смазывание окунанием в ванну специально введенных деталей, которые затем подают смазку к рабочим поверхностям основных деталей. Например, смазывание посредством вспомогательных колес (в зубчатых передачах – смазочные шестерни, рис. 8.88), дисков с лопатками, навесными кольцами и т.д. Возможно применение скребков, которые снимают слой смазки с боковых сторон колес и по желобам и каналам самотеком подают ее к смазываемым узлам;
•смазывание благодаря действию центробежных или иных сил, обеспечивающих подачу смазки из ванны к узлу;
•смазывание разбрызгиванием. Здесь смазка захватывается из ванны и разбрызгивается быстро вращающейся деталью, например, быстроходным колесом передачи или специальными брызговиками (дисками с лопатками, рис. 8.89). Брызги в виде капель и тумана могут непосредственно попадать на рабочие поверхности деталей, либо оседать на стенках корпуса или специальных лотках, затем стекать по каналам в нужные узлы и, омывая их, возвращаться в ванну.
При циркуляционной системе смазывания смазка на рабочие поверхности деталей принудительно подается насосом или иным внешним устройством: из картера или специального бака смазка прогоняется сквозь фильтр и охладитель, затем подается на смазываемые поверхности, стекает и снова собирается в емкости. Масляные насосы могут приводиться в движение от независимого двигателя либо от одного из валов машины. Циркуляционная система сложна, ведет к увеличению габаритов машины, но обеспечивает хорошие условия смазывания, и следовательно, высокую эффективность работы машины. Ее применяют в ответственных и высоко скоростных устройствах.
Возможны следующие способы циркуляционной системы смазывания:
•струйное смазывание. Здесь смазка по трубопроводам непрерывным потоком прокачивается сквозь рабочий узел;
а)
б)
Рис. 8.89 – Смазывание разбрызгиванием диском с лопатками
Рис. 8.87 – Смазывание |
Рис.8.88 – Смазывание |
окунанием паразитного |
|
смежных узлов машины |
зубчатого колеса |

190
а) |
б) |
в) |
|
|
|
|
|
|
Рис. 8.90 – Маслоуказатели
•капельное смазывание. Применяется при необходимости непрерывной подачи смазки малыми дозами (каплями). Для этих целей часто используются фитильные или капельные масленки. В фитильной масленке по фитилю из бачка непрерывно, даже в остановленной машине, подается смазка. В капельной масленке имеется игла, регулирующая или запирающая канал в трубке, по которому из бачка поступает смазка;
•смазывание масляным туманом, т.е. распыленными в воздухе мелкими частицами смазки, которые вместе с воздухом продуваются сквозь опору. Применяется для особо быстроходных узлов. На выходе из машины (узла) воздух осушается, а смазка отфильтровывается.
При картерной системе смазывания смазка заливается через отверстия, закрываемые пробками, либо через смотровые люки. Слив смазки производится через отверстия, располагаемые в самой низкой точке масляной ванны, так чтобы все масло могло стечь.
При циркуляционной системе смазывания смазка подводится и отводится по трубопроводам, но предусматриваются и дренажные отверстия, закрываемые пробками. Залив масла в ванну производится также как и при картерной системе смазывания.
Контроль прокачиваемого объема смазки при циркуляционной системе смазывания регулируется настройкой системы. При катерной системе смазывания контроль уровня (объема) жидкой смазки производят следующими способами:
•фонарным маслоуказателем (глазком) круглой (рис. 8.90а) или, при большом перепаде уровня, удлиненно-овальной формы. Они конструктивно просты, но их применяют, если наблюдение за уровнем не вызывает неудобства, т.е. уровень глаз человека может легко располагаться на уровне маслоуказателя;
•трубчатым маслоуказателем. Он использует принцип сообщающихся сосудов. Возможны конструкции замкнутых и открытых (сообщающихся с внешней средой, как, например, на рис. 8.90б) указателей. Трубчатые, как и фонарные, указатели требуют внимательного обращения, особенно при транспортировке и монтаже, так как легко бьются. Они позволяют легко вести непрерывный контроль;
•крановым маслоуказателем. Он представляет собой краны или пробки, закрывающие отверстия в корпусе, расположенные на уровне смазки. Уровень контролируется по вытеканию смазки при их открытии. Предпочтительно краны устанавливать попарно, с целью контроля нижнего и верхнего предельных уровней;
•жезловым маслоуказателем (рис. 8.90в). Уровень контролируют по следу смазки на жезле (щупе) после того, как его вынули из гнезда, имеющего доступ к ванне с маслом. Предельные значения уровня указываются на щупе посредством рисок. Указатель применяют для контроля в труднодоступных местах машины. Обычно контроль ведется при остановленной машине, и предварительно щуп вынимают и протирают. При неизбежности контроля уровня во время работы, в условиях волнения и брызг, щуп помещают в трубку, закрепленную в