
Сб. тезисов докладов Инновационные материалы и технологии в дизайне. 19-20 марта 2015
.pdf
УДК 667.621.6 |
А. С. Дринберг |
|
Холдинговая компания «ПИГМЕНТ», Санкт-Петербург |
ПЕРСПЕКТИВНЫЕ НАНОТЕХНОЛОГИИ ДЛЯ МОДИФИКАЦИИ ПОЛИМЕРОВ И ПОКРЫТИЙ
Аннотация. Рассмотрены и изучены различные методы модификации полимеров и покрытий специальными наноматериалами. Разработана технология получения нанодисперсий на стандартном оборудовании.
Ключевыеслова:фуллерены, детационный углерод, нанотрубки, дислокационнно-диф- фузионная диффузия, нанодисперсия, метаматериалы.
В настоящее время интенсивно исследуются методы получения и свойства наноматериалов – систем, состоящих из структурных единиц размерами десятки или единицы нанометров. По своим размерам эта величина примерно соответствует молекулам белков, или менее, но все же более величин размеров и масс, характерных для простых органических молекул. В этой области размеров уже в значительной мере перестают действовать закономерности, действительные для твердого тела и описываемые моделью зонной структуры, но еще не вполне применимы закономерности и явления, характерные для молекул. Кроме того, наноматериалы имеют вследствие своих размеров относительно высокую долю поверхностных атомов, также обладающих специальными свойствами, не совпадающими со свойствами твердого тела. Это дает возможность получать покрытия, одновременно сочетающие такие свойства, как эластичность и высокая твердость; получать материалы, стойкие к большинству агрессивных сред, с высокой гидрофобностью покрытий.
Особый интерес представляют наноматериалы на основе углерода, которые получены в последние десятилетия – фуллерены, состоящие в основном из 60 (С60), а также из 70, 84, 96 атомов углерода. В отличие от других форм углерода фуллерены растворимы в органических растворителях, образуя истинные растворы. На основе фуллеренов возможно создание покрытий с высокими физическими свойствами (вместо наполнителей с размером частиц 50–100 мкм), снижающих массу покрытий в 10 раз и более.
Детонационный углерод – продукт, получаемый методом взрывного синтеза (МВС). Это вещество состоит из мелких частиц алмаза с рентгеновским размером 4–5 нм и сферических частиц графита такого же размера. Обычно детонационный углерод содержит от 30 до 80 % частиц алмаза. В детонационном углероде алмазная и графитная части некоторым образом связаны друг с другом, так что разделить их чисто физическими методами даже при интенсивных воздействиях ультразвуком или гравитационным полем не удается. Детонационный углерод уже используется в промышленности в смазочно-восстанови- тельных композициях для двигателей внутреннего сгорания, демонстрируя достаточно необычные свойства в узлах трения. Возможны и другие области применения.
Детонационный наноалмаз – продукт, получаемый из детонационного углерода МВС путем избирательного окисления графитной части. Сейчас известно, что вследствие большого числа поверхностных атомов детонационный наноалмаз интенсивно взаимодействует с окружающей средой, проявляя разноообразные и не вполне понятные свойства, в том
© А. С. Дринберг, 2015.
61

числе и в биологических системах. Детонационный наноалмаз используется как добавка
вупрочненных гальванических покрытиях и в полировальных составах, полупроводниковых и оптических материалах, грунтовочных покрытиях.
Нанотрубки – материал, состоящий из совокупности углеродных трубок диаметром в несколько атомных диаметров как многослойных, так и однослойных, и длиной до единиц миллиметров. По свойствам к нанотрубкам приближаются нановолокна, для которых характерна некоторая неоднородность по длине и диаметру. Нанотрубки и нановолокна находят применение в электрохимии и производстве углеродных композиционных материалов [1].
Исследования, связанные с разработкой новых типов покрытий на основе композиционных наноуглеродных материалов, интенсивно ведутся во всем мире. Как предполагается, такие покрытия имеют низкую поверхностную энергию и обладают гидрофобностью . Установлено, что они имеют повышенные прочностные характеристики в случае введения
вих состав углеродных нанотруб, поскольку модуль Юнга по оси нанотрубки превышает соответствующий модуль монокристаллического алмаза. Известно также, что гальванические покрытия, использующие совместное осаждение металлов и наноалмазных частиц,
внесколько раз превышают по своим прочностным характеристикам традиционные гальванические покрытия.
Высокими физико-механическими свойствами обладают и нанопорошки в качестве наполнителей ЛКМ.
ВХК «Пигмент» совместно с ФТИ им. А. Ф. Иоффе разработан метод получения нанопорошков с применением явления дислокационно-динамической диффузии при разломе твердых тел [2]. Такие наполнители можно использовать в сочетании с акриловыми, полиуретановыми, эпоксидными и другими пленкообразователями в виде органических растворов или водных дисперсий. При этом необходимо учитывать сложность введения тонкодисперсных частиц, связанных с эффектом флокуляции и образования крупных коагуляционных агрегатов размером 6–12 мкм, что можно избежать путем подбора специальных добавок.
Вкачестве примеров нанотехнологий, которые могут использоваться в лакокрасочной промышленности, следует отнести методы молекулярного наслаивания со структурой ядро-оболочка. Формирование тонких покрытий на поверхности твердого тела или ядра происходит в вакууме плазмохимической полимеризацией, полимеризацией мономера, нанесением покрытий из газовой фазы и т.д. Известно изготовление по этому способу керновых пигментов, например перламутровых, а также материалов с различными свойствами, когда в качестве ядра используются дешевые наполнители, а на поверхность осаждаются вещества, обладающие необходимыми свойствами. На основе дисперсий фторполимеров по типу ядро-оболочка предлагается изготовление порошковых красок.
Одним из перспективных направлений является золь-гель технология, основанная на методе синтеза из растворов органических и неорганических веществ. Сущность метода заключается в превращении золя в гель, например, при изготовлении растворов силикатов щелочных металлов по следующей схеме: истинный раствор– полимеризация (коллоидные частицы – золь) – агрегация (сетка частиц – гель) – конденсация (ксерогель). При этом образуется трехмерная жесткая сетка, содержащая связанные между собой поры, заполненные жидкостью. В зависимости от сушки геля раличают ксерогель, аэрогель. Золь-гель технология позволяет приготовлять нанокомпозиты, в которых поры заполняются необходимой фазой.
Интересным направлением применения нанотехнологий в ЛКМ является использо-
вание нано TiO2. Прежде всего, нано TiO2 это эффективнейший УФ-адсорбер. Поэтому данный материал можно применять в качестве добавок в покрытиях для ж/д и обще-
62

ственного транспорта, автоэмалях, в промышленных покрытиях (металлоконструкции, мосты, эстакады, фасадные краски и нефтегазохранилища ) и т. п. Также нано TiO2 можно создавать ПК с эффектом грязеотталкивания (металлоконструкции, мосты, эстакады, фасадные краски, покрытия для памятников, дорожных знаков, антивандальные ПК и т. п.).
Наноглины представляют собой модифицированный монтмориллонит, он применяется в нефтегазовой промышленности при очистке и крекинге нефти, синтезе полимеров, пищевой промышленности в качестве адсорбента примесей, фармакологической и фармацевтической промышленности, а также для изготовления различных строительных материалов.
Разработана уникальная технология получения нанодисперсий винилированных алкидных олигомеров через стадию инверсии. Показано, что синтез и эмульгирование ВАО с получением нанодисперсий можно вести на стандартном оборудовании для производства лаков на конденсационных смолах с применением двух видов поверхностно-актив- ных веществ: ионогенного и неионогенного. Установлено, что процесс эмульгирования ВАО идет эффективно только через стадию инверсии [3].
Ведутся исследования по разработке специальных метаматериалов. Метаматериалы представляют собой искусственно сформированные и особым образом структурированные среды, обладающие электромагнитными или акустическими свойствами, сложно достижимыми обычными технологиями.
Список литературы
1.Калинская Т.В., Дринберг А.С., Ицко Э.Ф. Нанотехнологии. Применение в лакокрасочной промышленности. М.: ЛКМ-пресс, 2011.
2.Клявин О.В., Дринберг А.С., Чернов Ю.М., Шпейзман В.В. Диспергирование кристалличе-
ских порошковых материалов в газовых средах различного химического состава // Физика твердого тела. 2012. Т. 54. Вып. 5. С. 1019–1023.
3.Дринберг А.С. Винилированные алкидные олигомеры М.: ЛКМ-пресс, 2014.
УДК 778.38 О. Э. Бабкин, В. В. Ильина, В. Н. Михайлов
Санкт-Петербургский государственный институт кино и телевидения, Санкт-Петербург
ЗАВИСИМОСТЬ ГЛУБИНЫ РЕЛЬЕФА ЗАПИСИ ДИФРАКЦИОННОЙ РЕШЕТКИ ОТ СПОСОБА СУШКИ ФОТОСТРУКТУРИРУЕМОГО МАТЕРИАЛА
ПРИ ПОСТЭКСПОЗИЦИОННОЙ ОБРАБОТКЕ
Аннотация. Основной целью работы было изучение влияния стадии сушки материала после экспозиционной обработки, а также обоснование возможности использования желатиновых светочувствительных композиций для записи голографических дифракционных решеток пропускающего и отражательного типа.
Ключевые слова: фотоструктурируемые материалы, голография.
© О. Э. Бабкин, В. В. Ильина, В. Н. Михайлов, 2015.
63

Дифракционные решетки – самый распространенный вид голографических оптических элементов. Они широко применяются в интегральной оптике (в качестве элементов связи), в лазерной технике, оптоэлектронике, волноводной оптике, в массовом тиражировании голографических защитных элементов, в полиграфии. Из двух известных способов изготовления дифракционных решеток голографический способ менее трудоемок, а сами оптические элементы характеризуются лучшими оптическими характеристиками (уменьшенным светорассеянием, высоким разрешением, отсутствием ложных линий в спектре), к тому же голографический способ позволяет изготавливать решетки больших размеров [1].
Материалы для голографического способа записи дифракционных решеток должны обладать высокой прозрачностью, большой дифракционной эффективностью, устойчивостью к воздействию внешней среды. Из используемых материалов наибольшее распростране-
ние получили фотополимерные материалы, фоторезисы, а также светочувствительные слои на основе желатина: слои бихромированного желатина (БХЖ) и галогенсеребряные фотографические материалы высокого разрешения [2].
Вработе в качестве материала использовались фотографические пластинки типа ВРП.
Воснову способа записи дифракционной решетки положена способность желатиновых слоев к фотодеструкции под воздействием коротковолнового (УФ) излучения: образование рельефа на поверхности материала вызвано изменением толщины желатинового слоя под воздействием УФ-излучения и постэкспозиционной обработки. Количество энергии УФ-излучения, поглощенной различными участками материла, определяется оптической плотностью серебряного изображения, образуемого после проявления и фиксировании, т.е. местами УФ-излучение экранизируется серебряным изображением, и информация записывается на материале в виде поверхностного рельефа. Данным методом получаются высокоэффективные, рельефно-фазовые голограммы (с максимальной дифракционной эффективностью, близкой к теоретическому пределу ~34 % для тонких фазовых голограмм).
Материал экспонировался твердотельным лазером с диодной накачкой на длине волны 532 нм в течение 1/250; 1/125; 1/60; 1/30; 1/15 секунд. Соотношение пучков 1:1, мощность опорного пучка составляла 0,034 Вт/см2; запись осуществлялась в попутных пучках (рис. 1).
Постэкспозиционная химико-фотографическая обработка проводилась в проявляющем растворе SM-6 с использованием стадии отбелки в растворе PBU, приготовленной по принятой рецептуре. Время УФ-засветки варьировалось в диапазоне 5–40 мин. Для равномерной сушки использовали ступенчатые режимы обработки в спиртах различной концентрации, для сравнения использовали естественную сушку материала после полного цикла обработки. Измерение глубины рельефа проводили на микроскопе МИИ-4.
Результатом стали данные, что толщина материала после засветки (на границе УФ – Стекло) составила 2,0 ± 0,2 мкм; толщина без УФ-засветки – 11,0 ± 0,2 мкм. Расчетная глубина рельефа (на границе Маска – УФ) составляет 9,0 ± 0,2 мкм. При естественной сушке глубина рельефа составила 1,8 ± 0,1 мкм. Следовательно, для достижения максимальной глубины дифракционной решетки, записываемой на галогенсеребряных материалах типа ВРП, рационально использовать многоэтапную спиртовую сушку материала, что приводит к увеличению глубины рельефа, определяющей характеристики качества рельефно-фазовых голограмм.
64
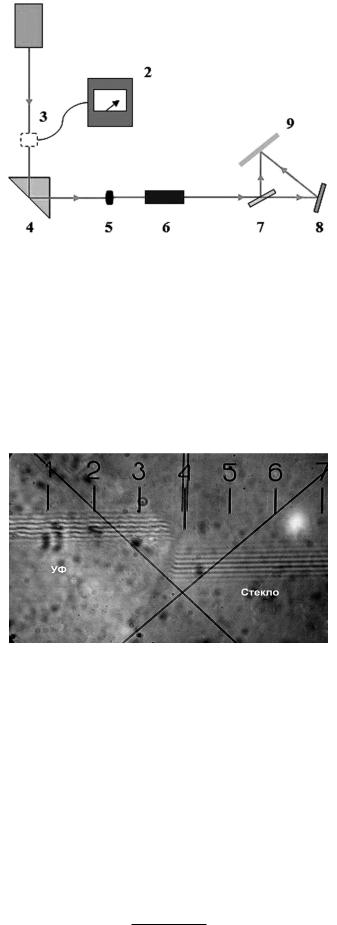
Рисунок 1 – Схема записи дифракционной решетки в попутных пучках:
1 – твердотельный лазер с диодной накачкой;
2 – измеритель мощности лазерного излучения Spectra-Physics 404 PM; 3 – измерительная головка прибора 2; 4 – призма;
5 – затвор; 6 – телескоп; 7 – полупрозрачное светоделительное зеркало; 8 – зеркало; 9 – фотопластинка ВРП
На рис. 2 приведена фотография интерференционных картин, наблюдаемых на материале, высушенном обезвоживанием материала изопропанолом (трехступенчатая сушка).
Рисунок 2 – Фотография интерференционной картины на материале ВРП
Публикация подготовлена по материалам исследований, выполняемых в рамках до-
говора НИР № 10-15/ГП от 13.01.2015 г.
Список литературы
1.Иванов В. П., Лукин А. В., Любимов А. И., Саттаров Ф. А., Скочилов А. Ф. Голограммные дифракционные решетки рельефно-фазового типа в ГИПО // Сб. тр. Всероссийского семинара «Юрий Николаевич Денисюк – основоположник отечественной голографии». СПб.: СПбГУ ИТМО, 2007.
2.Ильина В.В., Абрамова О.О. Фотоматериалы для голографии: Учеб. пособие. СПб.: СПбГУКиТ. 2004.
65

УДК 667.6 Е. Д. Войнолович, О. Э. Бабкин
Санкт-Петербургский государственный институт кино и телевидения, Санкт-Петербург
ВСПУЧИВАЮЩИЕСЯ ПОЛИМЕРНЫЕ ПОКРЫТИЯ, ПОЛУЧЕННЫЕ ПО ТЕХНОЛОГИИ УФ-ОТВЕРЖДЕНИЯ
Аннотация. Рассмотрена возможность применения технологии УФ-отверждения для создания огнезащитных композиций, создания толстослойных покрытий; изучено влияние природы и функциональности мономеров на огнезащитные свойства композиции.
Ключевые слова: огнезащитные полимерные покрытия, УФ-отверждение.
Сегодня огнезащитные материалы представлены, в основном, так называемыми вспучивающимися полимерными композициями, которые под воздействием огня или жара образуют изолирующую пену на поверхности защищаемого материала, предотвращая тем самым возгорание последнего, снижая нагрев и дымообразование. В состав таких композиций входят пентаэритрит, меламин и фосфаты аммония – чаще всего высокомолекулярный полифосфат [1].
Традиционная рецептура ЛКМ УФ-отверждения включает низкомолекулярный олигомер, реактивный разбавитель, фотоинициатор, синергетик, добавки, наполнители и пигменты. К пленкообразователям, способным отверждаться под действием УФ-излучения, относятся эпоксиакрилаты, эпоксиэфиракрилаты, полиэфиракрилаты, ненасыщенные полиэфиры, уретанакрилаты [2].
В работе изучали влияние природы и функциональности химических веществ с двойными связями С=С на огнезащитные свойства композиции. В качестве таких веществ были взяты четыре монофункциональных мономера (полиэтиленгликоль(6) акрилат, изоборнилакрилат, гидроксиэтил-метакрилат, циклогексилметакрилат) и один бифункциональный мономер (пропоксилированный диакрилат неопентилгликоля). На их основе приготовили наполненные композиции «пленкообразователь : наполнитель» в соотношении 1:1 и провели ряд исследований.
Наибольшее значение адгезионной прочности к металлической подложке показала композициянаосновеизоборнилакрилата,наименьшее–наосновегидроксиэтилметакрилата. Поверхностная энергия наиболее высокая у композиции на основе гидроксиэтилметакрилата, наименьшая – у композиции на основе изоборнилакрилата. Самый высокий показатель коэффициента вспучивания был получен у композиций на основе пропоксилированного диакрилата неопентилгликоля и на основе полиэтиленгликоль(6)акрилата; наименьший – у композиций на основе гидроксиэтилметакрилата и циклогексилметакрилата.
По итогам проведенных исследований можно утверждать, что технологии УФотверждения могут быть использованы для создания огнезащитных полимерных покрытий. Приемлемые огнезащитные свойства показали как композиция на основе бифункционального мономера, так и монофункционального. Изменение исходного состава полимерного покрытия УФ-отверждения позволяет регулировать его огнезащитные характеристики.
© Е. Д. Войнолович, О. Э. Бабкин, 2015.
66

Список литературы
1.Олейников К.В., Троценко П.А., Мацицкая А.В. и др. Основные компоненты огнезащитных вспучивающихся материалов и их роль в образовании защитных пенококсовых слоев // Химическая промышленность. 2008. Т. 85. № 1. С. 49–52.
2.Бабкин О.Э., Бабкина Л.А., Ильина В.В. УФ-отверждаемые антикоррозионные покрытия // Лакокрасочные материалы и покрытия. 2014. № 2. С. 42–45.
УДК 614.841.1 А. А. Триполицын
Военный институт (инженерно-технический) Военной академии материально-технического обеспечения им. генерала армии А. В. Хрулева, Санкт-Петербург
О. Э. Бабкин
Санкт-Петербургский государственный институт кино и телевидения, Санкт-Петербург
РАЗРАБОТКА ОГНЕЗАЩИТНОГО СОСТАВА ДЛЯ СОЗДАНИЯ ПОЛИМЕРНОГО ПОКРЫТИЯ ДРЕВЕСНЫХ МАТЕРИАЛОВ
Аннотация. В работе рассмотрено создание полимерного огнезащитного покрытия на поверхности древесины с использованием амидофосфатов.
Ключевые слова: огнезащита, амидофосфаты вспучивающего действия, огнезащитное полимерное покрытие для древесины.
Создание защитного покрытия древесины является естественным стремлением сохранить полезные свойства природного полимера. Известно множество способов защиты в виде нанесения защитного слоя (краски, лаки, обмазки), но приводящих к ухудшению эстетического вида материала. Применение пропиток (антипиренов) позволяет сохранить природную красоту и свойства древесины.
Проникая в пористую структуру древесины [1], антипирены закрепляются физически и химически. При воздействии повышенных температур происходит карбонизация верхних слоев древесины, что приводит к уменьшению их теплопроводности и уменьшению температуры воздействия на внутренние слои, что сказывается на реакции термического разложения природного полимера.
Для создания защитного полимерного покрытия [2] разработана технология получения амидофосфата. В качестве базового компонента использовался карбамидоформальдегидный концентрат марки КФК-85.
Высокоинформативные методы исследования, такие как ЯМР спектроскопия, позволили уточнить состав базового компонента и амидофосфата, получившего авторское название «ОСА-1» [3]. Уточнение составов помогло повлиять на стадии синтеза амидофосфата на изменение свойств итогового антипирена в необходимую сторону.
© А. А. Триполицын, О. Э. Бабкин, 2015.
67

а |
б |
Рисунок 1 – Дериватограммы образцов древесины: а – без обработки; б – обработанной составом «ОСА-1»
Исследования с использованием метода термического анализа (рис. 1) подтвердили снижение температур начала химических реакций, уменьшения их интенсивности и уменьшения экзоэффектов [4].
Стандартные методы [5] испытания на огнезащитную эффективность подтвердили перевод древесины в группу трудногорючих материалов.
Таким образом, разработана технология получения амидофосфата с заданным комплексом свойств. Рассмотрено создание полимерного огнезащитного покрытия на поверхности древесины. Подтверждена высокая огнезащитная эффективность.
Список литературы
1.Таубкин С.И. Основы огнезащиты целлюлозных материалов. М.: Изд-во МКХ РСФСР, 1960.
2.Пат. 2270752 Российская Федерация, МПК В27 К 3/52., С 09 К 21/12. Способ получения антипирена / В.Н. Махлай, С.В. Афанасьев, М.П. Михайлин, Р.В. Коротков. Заявитель и патентообладатель ОАО «ТольяттиАзот». Заявл.12.10.04. Опубл. 27.02.06. Бюл. № 6.
3.Афанасьев С.В., Триполицын А.А., Кузьмин И.В. О фракционном составе КФ концентра-
та // Древесные плиты: теория и практика: Материалы X Междунар. науч.-практ. конф. 21–22 марта 2007. СПб.: СПбГЛТА, 2007. С. 23–28.
4.ТриполицынА.А.Поведение огнезащищенной древесины в условиях воздействия повышенной температуры // Строительные материалы. 2009. № 8. С. 64.
5.ГОСТ 16363–98. Средства защитные для древесины. Метод определения огнезащитных свойств.
68

УДК 735.29.(32) Н. С. Лукичева, М. Я. Татаренко, А. А. Лысенко
Санкт-Петербургский государственный университет технологии и дизайна, Санкт-Петербург
ПОГЛОЩЕНИЕ МАСЛА ПОРИСТЫМИ УГЛЕРОДНЫМИ МАТЕРИАЛАМИ
Аннотация. В работе изучена поглотительная способность различных пористых материалов по отношению к трансмиссионному маслу; изучена поглотительная способность нетканых материалов; изучена возможность регулирования сорбционных свойств нетканых материалов.
Ключевые слова: пористые материалы, нетканые материалы, сорбционная активность.
Проблема сбора масло- и нефтепродуктов из разливов на почве и воде по-прежнему остается актуальной, несмотря на то, что к настоящему времени разработано множество методов сбора таких загрязнений и поглотителей нефтепродуктов.
Одним из наиболее эффективных поглотителей является терморасширенный графит (ТРГ). Вместе с тем ТРГ обладает такими существенными недостатками, как высокая дисперсность и низкая насыпная плотность, что затрудняет его использование. В этой связи перспективными являются разработки новых пористых материалов, в том числе и с регулируемой пористостью [1]. Нами проведен сравнительный анализ поглотительной способности различных пористых материалов (таблица) и показано, что наибольшей сорбционной активностью (СА) по отношению к маслу трансмиссионному обладает ТРГ.
Сорбционная активность различных материалов
|
|
|
Тип сорбента |
|
|
|
|
|
|
|
|
|
Сорбент-1 |
Сорбент-2 |
Сорбент-3 |
Сорбент-4 |
ТРГ |
|
|
|
|
|
|
СА, г/г |
10,0 ± 2,0 |
13,0 ± 2,0 |
10,0 ± 2,0 |
19,0 ± 2,0 |
22,0 ± 2,0 |
|
|
|
|
|
|
Примечание:
—сорбент-1 – нетканый материал из графитированных углеродных волокон (ГУВ);
—сорбент-2 – гидрофобизированный неканый материал из ГУВ;
—сорбент-3 – углеродная губка на основе ПВС;
—сорбент-4 – углеродный сорбент, полученный по тамплетной технологии.
Близкой СА обладает пористый углеродный композит, полученный с использованием тамплетной технологии, которая позволяет регулировать объем и размеры пор. Сорбционная активность нетканых материалов в два раза ниже. Установлено, что гидрофобизация нетканого материала повышает их СА на 25–30%.
Список литературы
1.Лукичева Н.С., Кузнецов А.Ю., Житенева Д.А., Нижельская Л.В., Лысенко А.А. Сорбци-
онно-активные материалы для очистки водной поверхности от нефтепродуктов // Дизайн. Материалы. Технология. 2014. № 35. С. 120–122.
© Н. С. Лукичева, М. Я. Татаренко, А. А. Лысенко, 2015.
69

УДК 621.039:620.92 |
Р. О. Цицер, С. В. Лавриненко |
|
Национальный исследовательский Томский |
|
политехнический университет, г. Томск |
БЕЗОПАСНОСТЬ АТОМНЫХ СТАНЦИЙ. ЗАЩИТА ОТ РАДИОАКТИВНОГО ВОЗДЕЙСТВИЯ
Аннотация. Целью исследования является освещение проблем, связанных с эксплуатацией АЭС, в частности проблемы экологической безопасности станции.
Ключевые слова: атомные электростанции, радиоактивные вещества, ядерное топливо, безопасность АЭС.
Актуальность проблемы заключается в том, что основными факторами вредного воздействия на персонал объектов атомной промышленности и энергетики являются загрязнение поверхностей оборудования, помещений и воздуха радиоактивными веществами. Также не стоит забывать о возможности аварий на АЭС, которые могут привести к катастрофическим последствиям. Несмотря на значительные финансовые вложения в отрасль и современный уровень развития технологий, проблема безопасности при эксплуатации АЭС до сих пор не решена, о чем свидетельствуют аварии на объектах атомной промышленности.
Атомная электростанция является сложным комплексом, состоящим из большого числа сооружений, технологически связанных между собой. Прямое назначение АЭС – выработка электроэнергии. Следует осуществить много различных технологических операций, чтобы обеспечить безотказную и безопасную работу сложного оборудования.
Безопасность атомной станции – это свойство обеспечивать защищенность персонала, населения и окружающей среды от радиационного воздействия АЭС во всех режимах ее эксплуатации и при любых аварийных ситуациях, ограничивая это воздействие допустимыми пределами [1].
Системам безопасности на АЭС уделяется исключительно большое внимание, ведь именно эти системы в любой нештатной ситуации обеспечивают защиту персонала и населения от загрязнения радиоактивными веществами.
Большую угрозу для здоровья и жизни человека представляют аварии на заводах ядерной промышленности, атомных энергетических установках, в хранилищах ядерных материалов и отходов. 11 марта 2011 года в результате стихийного бедствия произошла авария на АЭС Фукусима-1, что привело к радиационному загрязнению окружающей среды, и, по прогнозам экспертов, на восстановление экологического состояния потребуется до 40 лет [2]. Вероятность таких аварий крайне мала, но присутствует.
Каждая АЭС при нормальной эксплуатации лишь понемногу накапливает небольшие дозы облучения. Не стоит утаивать то, что радионуклиды способны откладываться в водоемах, почве, органах, тканях и т. д. Несомненно, что их концентрация может возрасти в тысячи раз. Данное явление уже давно изучено и носит название «буаккумуляция радиоактивности» [3]. Поэтому основным источником опасности для экологической обстановки является ядерное топливо и продукты его использования, которые нужно изолировать от окружающей среды. Современный уровень развития
© Р. О. Цицер, С. В. Лавриненко, 2015.
70