

Рис. 20.17. Уплотнения сильфонного и манжетного типов
тельного гидростатического давления. Герметизирующие элементы должны быть гибкими и прочными при циклической нагрузке, а устройство для герметизации в целом простым и надежным.
Сначала в шарнирах использовали простейшие резиновые уплотнения, в дальнейшем стали применять уплотнения сильфонного и манжетного типов (рис. 20.17).
Гибкие валы. Существенный шаг, оказавший влияние на подходы к конструированию ВЗД в целом, был сделан в середине 1970-х годов, когда ВНИИБТ выполнил комплекс научно-исследовательских работ и впервые в практике проектирования ВЗД предложил конструкцию гибкого вала, защищенную патентами СССР и других стран.
Êначалу 1990-х годов в большинстве типоразмеров ВЗД, выпускаемых
âРоссии, для соединения ротора и выходного вала стали применяться гиб-
кие валы. В двигателях с наружным диаметром 88 мм и более гибкий вал размещают в расточке ротора, а в малогабаритных двигателях – ниже ротора.
В большинстве случаев гибкий вал ВЗД представляет собой металличе- ский стержень круглого сечения с утолщенными концами, на которых выполнены присоединительные элементы: гладкий конус или коническая резьба. Иногда гибкий вал изготовляют полым – со сквозным цилиндриче- ским каналом для подвода рабочей жидкости высокого давления непосредственно к долоту. Для повышения циклической прочности в месте перехода от заделки к рабочей части вала имеется конус с углом 5–15° или галтель с отношением радиуса галтели к диаметру вала в пределах 0,1–0,2 (рис. 20.18).
Преимущества использования гибких валов заключаются в простоте конструкции и высокой технологичности, большом сроке службы, соизмеримым с ресурсом корпусных деталей двигателя, а также в возможности реализации различных компоновок двигателей.
Рис. 20.18. Конструкции гибкого вала
744
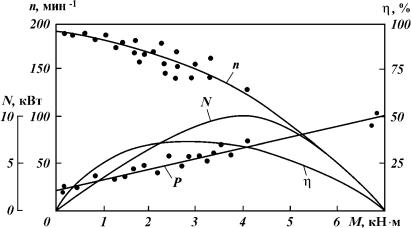
Опыт эксплуатации двигателей в наклонно направленном и горизонтальном бурении выявил недостаточную стойкость гибких валов при углах перекоса секций более 1°30′. В связи с этим в последних конструкциях двигатели типа ДГ стали оснащать шарнирно-торсионными соединениями.
ХАРАКТЕРИСТИКИ ВЗД
Характеристики необходимы для выбора оптимальных параметров режима бурения и поддержания их в процессе долбления, а также для определения путей дальнейшего совершенствования конструкций ВЗД и технологии бурения с их использованием.
В последнее время внимание к характеристикам ВЗД все более повышается. Это связано с внедрением регулируемых приводов буровых насосов, для эффективного использования которых знание характеристик гидромашины становится непременным условием; распространением новых технологий (наклонно направленное и горизонтальное бурение, бурение с использованием непрерывных труб), особенно чувствительных к изменению режимов работы ВЗД.
В общем случае различают статические и динамические характеристики ВЗД.
Статические характеристики отражают зависимости между переменными гидродвигателя в установившихся режимах. Эти характеристики можно условно классифицировать как стендовые и нагрузочные. Стендовые характеристики (как функции от крутящего момента) определяют в лаборатории (рис. 20.19).
Динамические характеристики определяют соответствующие зависимости в неустановившихся режимах и обусловливаются инерционностью происходящих процессов. К динамическим относят и пусковые характеристики гидродвигателя.
Рис. 20.19. Типичная стендовая характеристика ВЗД (ДГ-155)
745
ВЛИЯНИЕ РАСХОДАЖИДКОСТИ НАХАРАКТЕРИСТИКИ ВЗД
Расход жидкости Q является одним из параметров режима бурения. Чаще всего возможный диапазон изменения Q определяется технологией бурения скважины, и его задают конструктору ВЗД вместе с другими исходными данными.
Стендовые испытания ВЗД разных типоразмеров показывают, что с увеличением расхода повышаются как тормозной момент и перепад давления, так и мощность, крутящий момент, частота вращения и перепад давления в экстремальном режиме. КПД гидродвигателя при увеличении Q в допустимом диапазоне изменяется незначительно.
Нижний предел расхода жидкости ограничивается нагрузочной способностью или устойчивостью работы двигателя. Верхний предел допустимого расхода жидкости определяют три фактора:
высокие инерционные нагрузки при увеличении частоты вращения; КПД двигателя η: при заданном натяге после достижения определен-
ного значения расхода жидкости происходит снижение объемного η. Это объясняется тем, что с увеличением частоты вращения и перепада давления по линии контакта образуется односторонний зазор, приводящий к разгерметизации РО и росту утечек. Кроме того, с увеличением расхода растут и гидравлические потери в двигателе;
износ РО вследствие повышенных контактных напряжений и скоростей скольжения в рабочей паре, а также скорости жидкости в каналах РО.
Если ограничения по расходу не удовлетворяют требованиям гидравлической программы бурения, используют способ разделения потока жидкости через полый ротор двигателя с помощью регулятора расхода.
20.4. ТУРБОВИНТОВЫЕ ЗАБОЙНЫЕ ДВИГАТЕЛИ
В последние годы отечественный парк забойных гидравличе- ских двигателей пополнился новым представителем – турбовинтовым двигателем (ТВД).
Впервые схема турбовинтового агрегата была предложена в 1970 г. авторским коллективом ВНИИБТ в составе М.Т. Гусмана, Д.Ф. Балденко, А.М. Кочнева и С.С. Никомарова.
ТВД органично сочетают высокую стойкость, свойственную турбобурам, и оптимальную энергетическую характеристику (высокий уровень отношения M/n при незначительном падении частоты вращения при нагрузке двигателя), характерную для ВЗД.
Турбовинтовой двигатель можно отнести к редукторным турбобурам, в котором винтовая пара выполняет функции не только редуктора, но и стабилизирующего элемента при перегрузках долота.
Несмотря на большую металлоемкость и сложность конструкции, эти двигатели в ряде случаев успешно конкурируют с ВЗД, прежде всего вследствие их существенно большего ресурса, что особенно привлекательно при использовании современных высокопроизводительных долот.
Двигательные секции ТВД конструктивно выполняют в двух вариантах: с винтовой парой, монтируемой над турбинной секцией или между
746
турбинной и шпиндельной секциями. В первом варианте упрощается конструкция двигателя – проектируют лишь один узел соединения планетарного ротора. Второй вариант менее предпочтителен, так как требует двух узлов соединения ротора.
20.5. ЭЛЕКТРОБУРЫ
Наряду с гидравлическими в бурении используют и электриче- ские машины – электробуры.
Электробур – это электрическая забойная машина, своеобразный электродвигатель, смонтированный в трубном корпусе малого диаметра и предназначенный для привода долота на забое скважины.
Современный электробур представляет собой, как правило, асинхронный маслонаполненный двигатель с короткозамкнутым ротором.
Конструкция промышленного электробура была разработана в СССР в 1937–1940 гг. группой инженеров (А.П. Островский, Н.В. Александров, Ф.Н. Фоменко, А.Л. Ильский, Н.Г. Григорян и др.). Последующие опытноконструкторские работы позволили значительно модернизировать электробур по сравнению с первыми образцами: была создана безредукторная машина, мощность на валу электробура была увеличена в 2–3 раза (от 70 до 120–230 кВт) и наряду с этим уменьшен наружный диаметр. Серийное производство электробуров в СССР было налажено с 1956 г.
В настоящее время в ряде районов страны этим способом ежегодно бурят 200–250 тыс. м пород. Хотя указанный объем многократно уступает объему турбинного бурения в нашей стране, принципиальная схема подачи электрической энергии к забою скважины и использование погружного электрического двигателя для привода долота имеют неоспоримые преимущества. Однако конструктивные трудности, невысокие эксплуатацион- но-технические показатели и большая стоимость машины на данном этапе пока сдерживают применение этого вида техники в бурении.
Размерный ряд электробуров предусматривает их выпуск с наружными диаметрами корпуса 164, 170, 185, 215, 240, 250 и 290 мм. Более распространен электробур диаметром 170 мм. В обозначении электробура первое число – его наружный диаметр, второе – число полюсов обмотки статора (например, Э215-10). Могут добавляться буквы «М», обозначающая модернизированную модель, и «Р» – для редукторных электробуров. Обозначе- ние электродвигателя содержит сведения о наружном диаметре корпуса, общей длине магнитопровода с длиной немагнитопроводных пакетов и о числе полюсов. Например, маркировка МАП1-17-658/6 расшифровывается следующим образом: МАП – мотор асинхронный погружной; 1 – для электробура; 17 – наружный диаметр корпуса в см; 658 – общая длина магнитопровода и немагнитных пакетов статора в см; 6 – число полюсов.
Выпускаемый промышленностью электробур включает трехфазный асинхронный маслонаполненный двигатель À и маслонаполненный шпиндель Á на подшипниках качения (рис. 20.20).
В трубном корпусе электробура размещены пакеты магнитопроводной стали статора 6; они разделены пакетами немагнитопроводной стали в местах расположения радиальных шариковых опор ротора. Пакеты ротора 7 с алюминиевой обмоткой насажены на полом валу 5 двигателя. Ротор расположен в статоре с зазором 0,5–0,6 мм на сторону. Полость двигателя за-
747
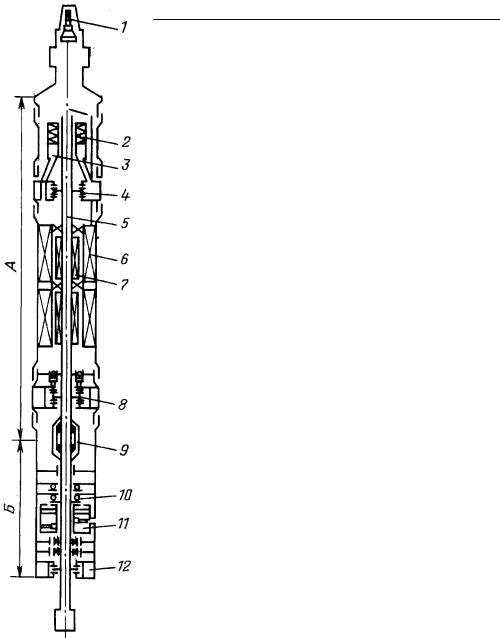
Рис. 20.20. Принципиальная схема электробура
полнена сухим изоляционным маслом. От внешней среды полость двигателя изолирована верхним 4 и нижним 8 сальниками. В сальники подается машинное масло. Для компенсации утечек масла через сальники и поддержания некоторого избыточного давления внутри двигателя, препятствующего попаданию промывочной жидкости внутрь, в верхней части электробура в лубрикаторной головке размещены лубрикаторы сальника 2 и двигателя 3. Внутри верхнего переводника проходит кабельный ввод от контактного стержня 1 до обмотки статора. Для восприятия веса вала в нижней его части над нижним сальником установлен упорный шариковый подшипник.
Снизу к двигателю присоединен шпиндель. В шпинделе находится многорядная осевая опора на шариковых подшипниках 10. Полый вал центрируется в корпусе с помощью роликовых и шариковых подшипников. Вал шпинделя соединен с валом двигателя посредством соединительной зубчатой муфты 9; в месте соединения валов находится шарнирное уплотнение для изоляции внутреннего пространства от промывочной жидкости, поступающей к забою по внутреннему каналу в валу двигателя и шпинделя. Осевые нагрузки на породоразрушающий инструмент полностью воспринимаются осевой опорой шпинделя и на вал двигателя не передаются. В нижней части шпинделя помещено сальниковое уплотнение 12. Шпиндель заполнен густым машинным маслом и оснащен лубрикатором 11, который создает избыточное давление за счет усилия сжатой пружины, давящей на поршень. Под поршнем находится резерв масла, восполняющий его потери из шпинделя.
На рис. 20.21 приведена типичная конструкция электробура.
Асинхронные двигатели для электробуров имеют жесткую характеристику, т.е. диапазон изменения их частоты вращения довольно ограничен. Ее изменение зависит от скольжения ротора относительно поля статора:
n = nï(1 – S),
ãäå n – частота вращения ротора двигателя; nï = 60 f/p – частота вращения магнитного поля статора (f – частота тока; p = 6, 8, 10 – число пар полюсов); S – скольжение (при нормальной нагрузке скольжение S = 8÷ ÷12 %).
Вращающий момент (Н м) асинхронного двигателя электробура может быть подсчитан по формуле
748
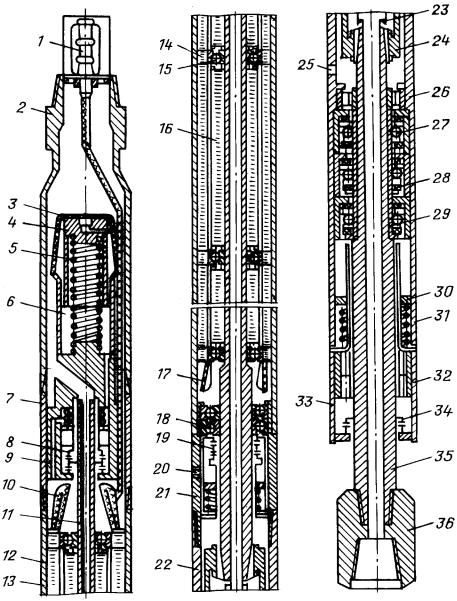
Рис. 20.21. Конструкция электробура:
1 – контактный стержень; 2 – переводник; 3 – резиновая диафрагма компенсатора двигателя; 4, 30 – поршень компенсатора двигателя и шпинделя соответственно; 5, 31 – пружина; 6 – цилиндр компенсатора; 7 – соединительный корпус двигателя; 8, 19 – верхний и нижний сальники двигателя; 9 – верхний клапан двигателя; 10, 17 – верхняя и нижняя части обмотки статора; 11 – вал двигателя; 12 – пакет магнитопроводной стали статора; 13 – корпус статора; 14 – промежуточный пакет статора из немагнитного материала; 15, 18 – промежуточный и нижний подшипники двигателя; 16 – секция ротора двигателя; 20 – клапан; 21 – нижний соединительный корпус; 22 – корпус шпинделя; 23 – втулка; 24 – зубчатая муфта; 25 – клапан; 26, 32 – верхний и нижний радиальные подшипники; 27 – упорный подшипник; 28, 29 – наружная и внутренняя обоймы распределителя осевой нагрузки; 33 – пробка; 34 – сальник шпинделя; 35 – вал шпинделя; 36 – переводник на долото
749
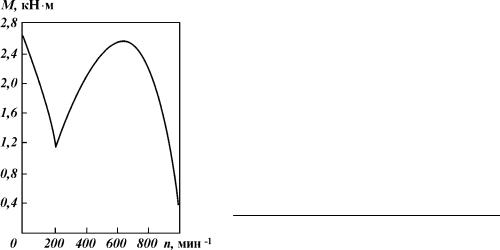
M = |
|
|
m pU 2 |
R′ |
/S |
|
|
|
|||
|
|
1 |
|
1 |
2 |
|
|
|
|
, |
|
|
πf[(R |
+ c R |
|
/S) + |
(x |
|
|
2 |
|||
2 |
2 |
1 |
+ c x′ ) ] |
||||||||
|
|
1 |
1 |
|
|
|
1 |
2 |
|
ãäå m1 – число фаз обмотки статора; U1 – напряжение на зажимах двигателя, В; R′2 – приведенное омическое сопротивление ротора, Ом; R1 – омическое сопротивление фазы обмотки статора, Ом; x1 – индуктивное сопротивление обмотки статора, Ом; x′2 – приведенное индуктивное сопротивление ротора, Ом; ñ1 – коэффициент, зависящий от напряжения на клеммах двигателя.
Как следует из формулы, вращающий момент двигателя прямо пропорционален квадрату напряжения на его входе. Снижение напряжения приводит к заметному падению вращающего момента. В связи с этим необходимо учитывать потери напряжения в токоподводе от поверхности к двигателю, а падение напряжения при кратковременных перегрузках двигателя рекомендуется компенсировать некоторым повышением напряжения на входе двигателя на 5–10 % номинального значения. Номинальное напряжение на клеммах электробуров составляет 1000–1200 В в зависимости от типа двигателя.
Характер зависимости вращающего момента двигателя МАП1Д-25- 617/10 от частоты вращения вала двигателя приведен на рис. 20.22. На графике вращающего момента правая ветвь от точки максимума является областью устойчивой работы (рабочая область), левая – областью неустойчи- вой работы. При пуске двигателя заметно снижается вращающий момент (зона провала) в процессе выхода на режим. В зоне провала вращающий момент может снизиться до 60 % номинального. Но так как двигатель пускают с малой нагрузкой, а маховой момент вращающихся деталей и инструмента мал, то даже при уменьшенном моменте двигатель быстро увели- чивает частоту вращения вала.
КПД двигателя при номинальной нагрузке составляет 66–68 %. Поскольку механические потери в шпинделе на опорах качения сравнительно невелики, характеристику электробура можно принимать по характеристике двигателя.
К забойному двигателю электроэнергия подводится по секционированному кабелю, помещенному внутри бурильной колонны. Токоподвод может осуществляться по трехили двухжильному кабелю. В последнем случае в ка- честве третьего провода используют бурильную колонну. Эта система питания носит название «два провода – земля» (сокращенно ДПЗ).
Система ДПЗ позволяет увеличить площадь сечения проходного канала в бурильной колонне и таким образом способствует снижению потерь напора при циркуляции промывочной жидкости по бурильной колонне.
Каждую кабельную секцию разме-
Рис. 20.22. Характеристика двигателя МАП1Д-25- 617/10
750
щают в отдельной бурильной трубе, и ее концы закрепляют в трубе на опорах с втулками, обеспечивающими некоторое свободное проворачивание кабеля при соединении труб. Секции соединяются в единую цепочку с помощью контактных элементов – контактного стержня на верхнем конце и контактной муфты на нижнем. Контактный стержень защищен от механических повреждений защитным стаканом. Соединение контактных элементов происходит автоматически при свинчивании бурильных труб, при этом контактный стержень входит в муфту с натягом, обеспечивающим герметичность соединения от проникновения бурового раствора.
Для монтирования секций электрокабеля используют специальные бурильные трубы типа ЭБШ с гладкопроходным сечением. Их выпускают диаметрами 140 и 114 мм с высаженными наружу концами. Трубы изготовляют из стали групп прочности Д и Е.
Кабельный подвод электробура – одно из наиболее слабых звеньев системы. Вследствие загрязнения и недостаточной герметичности соединений секций омическое сопротивление изоляции снижается. Если при спуске инструмента наблюдается резкое падение сопротивления (начальное сопротивление собственно электробура 50 МОм), то спуск инструмента прекращают и выбраковывают трубы с низким сопротивлением в изоляции кабеля. В процессе работы в соединениях с недостаточной герметичностью происходят пробои. Пробои и разрывы электрической цепи могут происходить также вследствие поломки медных контактов в муфте и излома кабеля в местах его сращивания с контактными соединениями.
Для бурения с электробуром буровую установку оснащают дополнительным электрооборудованием: распределительным устройством высокого напряжения, трансформатором, станцией управления электробуром. На пульте бурильщика устанавливают дополнительные электрические контрольные приборы (вольтметр, амперметр) для контроля нагрузки электробура, кнопки управления контактной системой, подающей напряжение на электробур, органы управления режимом работы автоматического регулятора. Автоматический регулятор управляет подачей инструмента в зависимости от загрузки двигателя и буримости горных пород.
Обладая всеми достоинствами, присущими забойным двигателям (облегчение условий работы бурильной колонны, существенное снижение износа бурильных труб в скважине, исключение затрат мощности на их холостое вращение и т.п.), электробур имеет преимущества по сравнению с гидравлическими забойными машинами:
режим работы электробура не зависит от расхода промывочной жидкости, который в данном случае можно выбирать только по условию полной и своевременной очистки забоя от шлама;
режим работы электробура практически не зависит от свойств циркулирующего бурового раствора, что позволяет применять его при использовании утяжеленных растворов, газообразных агентов и при продувке;
токоподвод с поверхности к электробуру является каналом связи, позволяющим использовать забойные системы контроля режима работы породоразрушающего инструмента и непрерывно следить за направлением ствола скважины;
при работе с электробуром открывается возможность автоматизировать процесс бурения по данным забойных датчиков для оптимального использования мощности двигателя;
поскольку электробур представляет собой маслонаполненный двига-
751
Ò à á ë è ö à 20.14
Основные характеристики электробуров
|
|
|
|
Ñèëà òîêà, À |
|
Вращающий |
|
|
|
||
|
|
|
|
|
момент, Н м |
|
|
|
|||
|
|
|
|
|
|
|
|
|
|
||
|
|
Íîìè- |
|
|
|
|
|
|
|
|
|
|
|
Íîìè- |
|
õîëî- |
Частота |
|
|
|
|
|
|
Òèï ýëåê- |
Длина, |
íàëü- |
нальное |
|
стого |
враще- |
|
|
|
cos ϕ |
|
íàÿ |
напря- |
|
õîäà |
íèÿ |
íîìè- |
макси- |
ÊÏÄ, |
Масса, |
|||
тробура |
ì |
ìîù- |
жение, |
рабоче- |
ïðè |
âàëà, |
íàëü- |
ìàëü- |
% |
|
ò |
|
|
ность, |
 |
ãî õîäà |
íîìè- |
ìèí–1 |
íûé |
íûé |
|
|
|
|
|
êÂò |
|
|
нальном |
|
|
|
|
|
|
|
|
|
|
|
напря- |
|
|
|
|
|
|
|
|
|
|
|
жении |
|
|
|
|
|
|
|
|
|
|
|
|
|
|
|
|
|
|
Ý290-12 |
14,02 |
240 |
1750 |
165 |
121 |
455 |
510 |
1100 |
72,0 |
0,67 |
5,1 |
Ý250-8 |
13,0 |
230 |
1650 |
160 |
107 |
675 |
332 |
750 |
72,0 |
0,7 |
3,6 |
Ý240-8 |
13,4 |
210 |
1700 |
144 |
107 |
690 |
297 |
760 |
75,0 |
0,66 |
3,5 |
Ý215-8Ì |
13,93 |
175 |
1550 |
131 |
95,5 |
680 |
250 |
550 |
72,0 |
0,69 |
2,9 |
Ý185-8 |
12,5 |
125 |
1250 |
130 |
93 |
676 |
180 |
360 |
67,5 |
0,66 |
2,05 |
Ý170-8Ì |
12,145 |
75 |
1300 |
83,6 |
78,6 |
695 |
110 |
240 |
63,5 |
0,63 |
1,8 |
Ý164-8Ì |
12,305 |
75 |
1300 |
87,5 |
80,0 |
685 |
110 |
240 |
61,0 |
0,625 |
1,65 |
|
|
|
|
|
|
|
|
|
|
|
|
Ò à á ë è ö à 20.15
Технические данные электробуров с редукторами-вставками
|
|
Íîìè- |
|
Ñèëà |
|
Вращающий мо- |
|
Переда- |
|
|
|
Íîìè- |
íîìè- |
Частота |
ìåíò, Í ì |
|
точное |
||
Òèï ýëåê- |
|
нальная |
Масса, |
||||||
Длина, м |
ìîù- |
нальное |
нального |
враще- |
|
|
число |
||
|
|
||||||||
тробура |
|
ность, |
напря- |
рабочего |
íèÿ âàëà, |
íîìè- |
макси- |
ò |
редук- |
|
|
жение, В |
òîêà, À |
ìèí–1 |
|
òîðà- |
|||
|
|
êÂò |
|
|
|
нальный |
мальный |
|
вставки |
|
|
|
|
|
|
|
|
|
|
|
|
|
|
|
|
|
|
|
|
Ý290-12Ð |
15,92 |
240 |
1750 |
165 |
145 |
1600 |
2600 |
5,7 |
3,15 |
Ý240-8Ð |
14,78 |
145 |
1400 |
112 |
230 |
615 |
1200 |
3,9 |
|
Ý215-8ÌÐ |
15,545 |
110 |
1350 |
102 |
230 |
465 |
1050 |
3,2 |
3,0 |
Ý215-8Ð |
14,445 |
150 |
1250 |
144 |
220 |
666 |
1020 |
3,0 |
|
Ý185-8Ð |
14,4 |
70 |
1100 |
90 |
240 |
300 |
700 |
2,3 |
2,92 |
Ý170-8Ð |
12,925 |
|
930 |
63 |
|
|
|
1,8 |
|
Ý170-8ÌÐ |
13,93 |
45 |
1000 |
59 |
220 |
200 |
400 |
2,00 |
3,13 |
Ý164-8Ð |
13,186 |
|
930 |
65 |
|
|
|
1,8 |
|
Ý164-8ÌÐ |
14,09 |
|
1000 |
61,5 |
|
|
|
1,9 |
|
|
|
|
|
|
|
|
|
|
|
тель, все детали которого работают в среде, изолированной от бурового раствора, он меньше подвержен абразивному изнашиванию и его рабочая характеристика остается практически неизменной в течение всего срока работы.
К недостаткам электробура относятся: высокая стоимость забойного двигателя, опасность потери дорогостоящей машины в результате прихвата в скважине, ограниченный срок межремонтной работы вследствие недостаточной износостойкости уплотнительных сальников электробура и недостаточной надежности системы токоподвода.
Перспективы развития буровых работ с применением электробуров связаны с существенным повышением ресурса до 200 ч и более.
В табл. 20.14 и 20.15 приведены характеристики электробуров.
752
21 |
УСТЬЕВОЕ ОБОРУДОВАНИЕ |
ГЛАВА |
БУРЯЩИХСЯ СКВАЖИН |
Устьевое оборудование – это комплекс оборудования, предназначенного для обвязки обсадных колонн, герметизации устья скважины при возникновении проявлений в процессе бурения, капитального ремонта, герметизации устья и регулирования режима работы скважины в процессе ее эксплуатации. Условно все устьевое оборудование делят на оборудование, применяемое при бурении скважины и при ее эксплуатации. В состав устьевого оборудования, участвующего в обвязке устья в процессе бурения скважины, входят колонная головка и противовыбросовое оборудование, состоящее из следующих основных узлов: крестовины, превенторов, надпревенторной катушки, разъемного желоба, манифольда, гидроуправления превенторами и задвижками, ручных приводов.
Колонная головка, с помощью которой обвязываются обсадные колонны в процессе бурения, служит также основанием для установки фонтанной арматуры; она остается на скважине на весь период эксплуатации. В состав эксплуатационного устьевого оборудования также входят: фонтанная арматура; манифольд фонтанной арматуры; приспособление для замены задвижек под давлением; лубрикатор, применяемый при исследованиях скважин; комплект задвижек, переводников и других деталей, необходимых для монтажа и обвязки устьевого оборудования.
21.1. КОЛОННЫЕ ГОЛОВКИ
Колонные головки предназначены для обвязки обсадных колонн газовых и нефтяных скважин. Они обеспечивают подвеску колонн, герметизацию межколонных пространств и контроль давления в них, проведение таких технологических операций, как снижение давления в межколонном пространстве, закачка цемента или других тампонажных материалов в межколонное пространство и т.п.
Конструкция колонной головки должна обеспечивать: 1) надежную герметизацию межколонных пространств; 2) контроль за давлением в межколонном пространстве; 3) быстрое и надежное закрепление обсадных колонн; 4) универсальность, т.е. возможность крепления к одной колонной головке обсадных колонн разных диаметров; 5) предохранение устьевой части обсадных колонн от повышенного изнашивания при работе бурильным инструментом; 6) возможность вертикального перемещения обсадных колонн при высоких температурах в скважине; 7) высокую надежность работы подвесок и узлов уплотнений во время бурения и длительной эксплуатации скважины; 8) минимально возможную высоту; 9) достаточную прочность с учетом действия различных нагрузок.
Кроме того, для осложненных условий бурения отдельные детали колонной головки должны быть коррозионно-стойкими, если в продукции скважины предполагаются корродирующие вещества; при бурении на Севере головка должна быть приспособлена для работы в условиях, где возможно понижение температуры до –60 °С; при морском бурении должна
753