
nano_1_97_4_lec
.pdf(від 100 до 1200 МПа). Застосовують для виготовлення формовок складної фо-
рми.
Газостатичне пресування Проводять, застосовуючи металеві оболонки (капсули) з алюмінію або
пластичних сталей. Форма оболонок — проста, максимально наближена до конфігурації виробів. Часто газостатичне пресування застосовують до вже ра-
ніше виготовленої іншими методами заготовки. Металеву капсулу розміщують у газостаті, в робочій камері якого створюють тиск до 200–300 МПа.
Квазігідростатичне пресування Спрощений варіант гідростатичного пресування. Порошок розміщують в
еластичних оболонках, пресування яких проводять за одностороннього або дво-
стороннього прикладання тиску в звичайному пресовому устаткуванні. Матері-
ал оболонки (гумова маса, епоксидні смоли тощо) під тиском має поводити себе подібно до рідини, мати достатню пружність і не склеюватися з порошком.
81
Лекція 11
Спікання напівфабрикатів: під тиском, за одновісного прикладання тиску, гаря-
че ізостатичне пресування, швидке не спрямоване компактування, високотем-
пературна газова екструзія, ежекційне лиття. Методи аморфізації.
Спікання формовок з нанопорошку обмежено неможливістю застосуван-
ня високих температур. Підвищення температури спікання призводить до зме-
ншення пористості, але з іншого боку призводить до росту зерна. Цю проблему розв'язують методами активації, які дозволяють отримувати малу пористість виробів за низьких температур спікання:
застосування високошвидкісного мікрохвильового нагріву (за збільшення швидкості нагріву від 10 до 300 град/хв необхідна для спікання нанопо-
рошку TiО2 температура знижується від 1050 до 975 °С;
ступінчасте контрольоване спікання;
плазмоактивоване спікання;
проведення спікання в вакуумі або відновних середовищах (для метале-
вих порошків).
Спікання під тиском Суміщення процесів формування і спікання або проведення спікання під
тиском дозволяє досягати великої густини, у тому числі й близької до теорети-
чної за використання нижчих температур нагріву.
Спікання за одновісного прикладання тиску Найбільш простий спосіб спікання. За літературними даними проведення
спікання нанопорошку заліза під тиском пресування до 400 МПа температура спікання, за якої відсутня пористість, знизилася від 700 до 350 °С, а розмір зер-
на у виробах зменшився від 1,2 мкм до 80 нм. Схема установки для спікання нанопорошків під тиском приведена на рис. 37. У випадку металевих нанопо-
рошків процес проводять у вакуумі або у відновній атмосфері з метою його ак-
тивації,
82

Рисунок 37. — Схема установки для спікання нанопорошків під тиском: 1 —
подача інертного або реакційного газу, 2 – формовка, 3 – ковадло, 4 – нагрівний елемент, 5 – вивід газу, 6 – робоча камера, 7 – термопара, 8 – пуансон, 9 – силь-
фон, 10 – герметизувальна прокладка
Гаряче ізостатичне пресування (ГІП)
Прогресивний методом суміщення процесів формовки і спікання. Метод
(ГІП) універсальний і широко використовуваний на практиці порошкової мета-
лургії. В сучасних установках можуть бути досягнуті тиски до 300 МПа і тем-
ператури до 2000 °С. Металічні зварні капсули для порошків виготовляють в цьому з вуглецевої або корозійно стійкої сталі. Для простих виробів використо-
вують тільки сталеві капсули, а для виробів достатньо складної форми — виго-
товлювані за спеціальною технологією металокерамічні форми. На якість виро-
бів впливають не тільки технологічні параметри ГІП, але й якість виготовлення капсул і процес їх заповнення порошком. Часто під час заповнення порошком застосовують віброущільнення порошку, проводять дегазацію і ретельну герме-
тизацію капсул. У випадку нанопорошків через їх велику питому поверхню і схильність до насичення газами застосування дегазації стає особливо важли-
вим.
83
Швидке неспрямоване компактування Спосіб замінює ГІП. У цьому процесі використовують нагріту циліндри-
чну прес-форму з товстою стінкою, яку після заповнення порошком піддають одноосному стиску під високим тиском (до 900 МПа). У такому разі зовнішні стінки прес-форми щільно прилягають до металевого циліндра відповідних ро-
змірів, який перешкоджає деформації прес-форми. В результаті заповнений по-
рошком внутрішній об'єм, який має форму майбутньої деталі, перебуває під квазіізостатичним тиском. Метод дозволяє спресувати металевий порошок майже до 100 % щільності всього за декілька хвилин.
Високотемпературна газова екструзія Спосіб полягає у формуванні гідростатичним методом за кімнатної тем-
ператури, подальшої термічної обробки в середовищі водню за відносно низь-
кої температури і виконання наступної екструзії за підвищеної температури.
Цей метод дозволяє проводити компактування порошків за короткочасної тем-
пературної дії і досить високих температурах. Наприклад, компактні заготовки,
отримані цим методом з нікелевого нанопорошку, вирізняються високими по-
казниками міцності за одночасних дуже добрих характеристиках пластичності.
Ежекційне лиття Метод оснований на додаванні у порошок спеціальної зв'язки (наприклад,
термопластичні полімери типу поліпропілену, поліетилену або полістеролу),
яка забезпечує малу в'язкість порошкової суміші. Порошкову суміш застосову-
ють потім для лиття під тиском (аналогічно литтю під тиском металів і пласт-
мас). Після отримання відливки проводять випалювання термопластичних ре-
човин, а потім вже спікання. Недоліки методу пов'язані зі складністю процесу вилучення компонентів зв'язки під час вигоряння (зміна форми деталі, процеси взаємодії продуктів розкладання термопластичних речовин з матеріалом поро-
шку, забезпечення вільного вилучення суміші, що утворюється під час випалю-
вання). Тому цей метод обмежено використовують для отримання невеликих спеціальних деталей складної форми з товщиною стінок менше 10 мм. Варіан-
том методу є використання водяної суспензії порошку. Суспензію виливають у
84
форму, а потім заморожують. Просушку заготовки здійснюють у замороженому виді, а потім проводять спікання.
Методи аморфізації
Аморфні металеві сплави є новим перспективним класом матеріалі. Амо-
рфний стан сплаву характеризується відсутністю дальнього порядку у розташу-
ванні атомів. Такий стан створюють завдяки надшвидкому охолодженню мате-
ріалу з газоподібного, рідкого або іонізованого стану. Існують такі методи отримання аморфних сплавів:
високошвидкісне іонно-плазмове і термічне напилення матеріалу на охо-
лоджувану рідким азотом підкладку (отримують шари завтовшки до 5
мм);
хімічне або електролітичне осадження іонів металу на підкладку;
оплавлення тонких поверхневих шарів деталей лазерним променем;
лазерна обробка суміші порошків за умови швидкого відводу тепла від розплаву;
гартування з рідкого стану.
Останній метод у теперішній час найдокладніше опрацьований і є основ-
ним методом отримання аморфних сплавів. Виробництво стрічок, фольг і дро-
тів (завтовшки до 100 мкм і завширшки до 200 мм) проводять за схемою подачі струменю рідкого металу на охолоджуваний водою барабан (як правило мід-
ний) з гладкою поверхнею, який обертається (рис. 38). Іноді використовують також схему видобування рідкого металу з ванни розплаву диском, зануреним вертикально торцем у розплав, який також охолоджують водою і швидко обер-
тають. Ще один спосіб полягає в плавленні сплаву струмами високої частоти,
витягуванні і швидкому охолодженні аморфної нитки завтовшки до 200 мкм. У
випадку нанесення на нитку перед охолодженням склоподібного покриття спо-
сіб використовують для отримання склометалевих аморфних композиційних матеріалів.
85
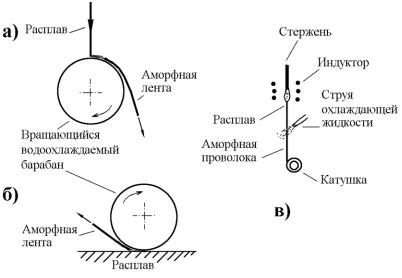
Рисунок 38. — Принципові схеми отримання аморфних стрічок і дротів мето-
дом швидкого охолодження: а) гартування на обертовому охолоджуваному во-
дою барабані, що обертається; б) екстракція розплаву барабаном, що обертаєть-
ся; в) охолодження тонкого струменю розплаву рідиною
За першого варіанту для отримання аморфної структури до складу спла-
вів вводять спеціальні легувальні елементи — аморфізатори в кількості до
30 %. Як аморфізатори зазвичай використовують Бор, Карбон, Силіцій, Нітро-
ґен та інші. Другий підхід пов'язаний з вибором сплавів, в яких утворюється пе-
вна базова евтектика, яка утворюється за взаємодії декотрих фаз-аморфізаторів.
Такі сплави легують з метою зниження температури плавлення і пригнічення процесу утворення зародків кристалів під час затвердіння сплаву. Цей підхід дозволяє отримувати окрім мікрозаготовок (стрічок, фольг, дротів) також і об'ємні заготовки завтовшки до 5–10 мм.
Можливість створення аморфного стану визначається хімічним складом та швидкістю охолодження. Остання зазвичай становить 105–1010 К/с. Хімічний склад обирають згідно з двома підходами.
Аморфний стан сплавів є метастабільним, тому після аморфізації часто проводять відпал, якого структура сплаву частково переходить до більш стабі-
льного стану. Проте певний ступінь метастабільності залишається, а за нагрі-
вання до (0,4–0,65) Тпл матеріал набуває повністю кристалічну структуру.
86
Останнім часом поряд з аморфним велику зацікавленість почали виявляти й до нанокристалічного стану сплавів, що аморфізуються.
В окремих випадках для отримання аморфного стану проводять поперед-
ню обробку (наприклад високошвидкісне гартування) заготовок; такі заготовки часто називають «прекурсорами».
Для ряду здатних до об'ємної аморфізації сплавів, наприклад для сплавів на основі заліза, можливо отримання нанокристалічної або аморфно-
нанокристалічної структури безпосередньо під час гартування розплаву з шви-
дкістю охолодження дещо нижчою від критичної швидкості утворення аморф-
ного стану. Проте у більшості сплавів за такого підходу отримують неоднорід-
ну, нестабільну структуру. Тому для отримання наноструктури використовують контрольовану кристалізацію сплавів з аморфного стану під час термообробки.
Як перспективну розглядають технологію отримання нанокристалічної струк-
тури шляхом ініціації процесів кристалізації в процесі деформування аморфно-
го матеріалу.
87
Лекція 12
Технології обробки поверхні. Хімічні технології: осадження з парової фази,
осадження з використанням плазми тліючого розряду, реактивне розпилення.
Методи можна умовно поділяють на дві великі групи — технології, осно-
вані на фізичних та хімічних процесах. Серед усіх наноорієнтованих технологій обробки поверхні на сьогоднішній день найбільш перспективними є іонно-
вакуумні технології нанесення покриттів (так звані CVD та PVD технології).
Нанесені такими способами шари вирізняються високою адгезією, а температу-
рна дії на матеріал основи як правило мінімальна. За літературними даними ро-
змір кристалітів у плівках, отриманих за технологіями вакуумного нанесення,
може сягати 1–3 нм.
Хімічні технології
Осадження з парової фази (CVD — Chemical Vapour Deposition)
Група методів основана на осадженні на поверхню нагрітих деталей плі-
вок з сполук металів, які перебувають у газоподібному стані. Осадження, як правило, проводять в спеціальній камері за пониженого тиску шляхом викорис-
тання хімічних реакцій відновлення, піролізу, диспропорціонування. У ряді ви-
падків можуть використовуватися реакції взаємодії основного газоподібного реагенту з додатковим. Найчастіше як такі сполуки використовують карбоніли,
галогени, металоорганічні сполуки. Наприклад, галогеніди металів відновлю-
ються воднем до металу з утворенням сполуки галогенів з воднем, а карбоніли за допомогою реакції піролізу розкладаються на метал і оксид Карбону. Най-
більш сприятливі умови для перебігу хімічних реакцій складаються за темпера-
тур 500–1500 °С. Тому оброблювані деталі нагрівають саме до таких темпера-
тур, що забезпечує локалізацію хімічної реакції поблизу від поверхні деталей, а
також створює умови для оптимального перебігу процесу, досягнення належ-
них властивостей покриття, зокрема доброї адгезії.
88
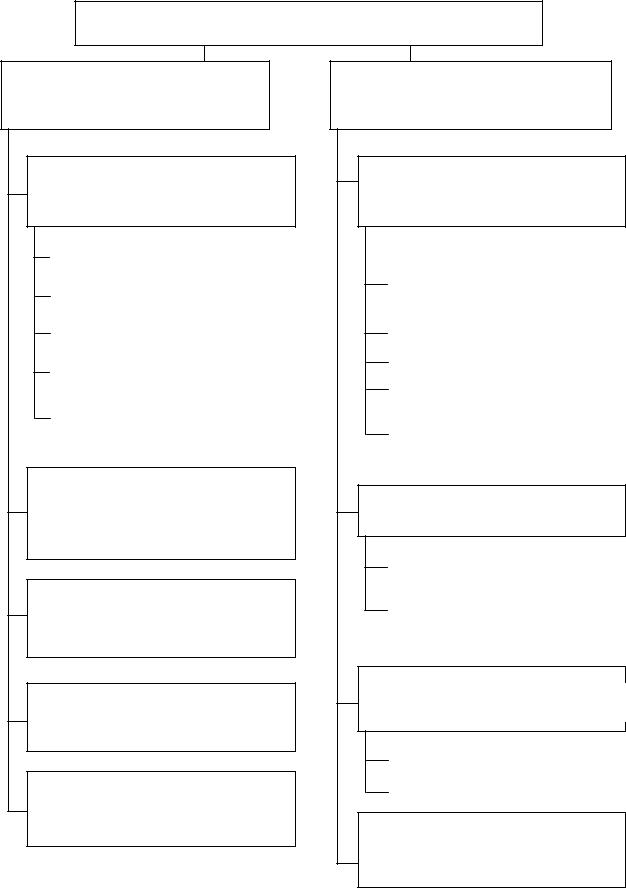
Нанорієнтовані технології обробки поверхні
Технології, основані на хімічних процесах
Хімічне осадження з парової фази (CVD–технології)
відновлення
2MeG + H2 → 2Me + 2HG;
виробництво карбонілів
Mex(CO)y → xMe + yCO;
диспропорціонування
→ Al + AlCl6;
взаємодія з проміжними компонентами; осадження за розкладання металоорганічних сполук (MOCVD–технології)
Осадження з використанням
плазми тліючого розряду
Ti+ + N+ → TiN
Світлова та електронна літографія
Осадження з розчинів металоорганічних сполук
Хімічне та електрохімічне окиснення, наприклад анодування
Технології, основані на фізичних процесах
Фізичне осадження з парової фази (PVD–технології)
термічне випаровування (індукційне, електродугове, електронно-променеве, лазерне нагрівання тощо); катодне і магнетронне розпилення;
іонне осадження (енергія до 1 кеВ); іонне плакування або перемішування; іонна імплантація
низькоенергетична 2–5 кеВ
високоенергетична 5–30 кеВ
Газотермічне напилення
високошвидкісне газополум'яневе напилення (HVOF);
плазмове напилення на повітрі (APS) та у контрольованій атмосфері (VPS)
Лазерні методи
лазерне легування або імплантація; лазерна аморфізація поверхні
Інтенсивна пластична деформація поверхневого шару; ультразвукова дія
Рисунок 39 — Класифікаційна схема наноорієнтованих технологій
обробки поверхні
89
Утворення покриття проходить шляхом послідовного нашаровування осаджуваного матеріалу. Високі температури процесу можуть також активізу-
вати процеси твердофазної або газофазної дифузії елементів між покриттям і підкладкою. Метод забезпечує отримання покриттів завтовшки 1–20 мкм з швидкістю 0,01…0,1 мкм/хв. Метод можна застосовувати для нанесення пок-
риття на внутрішні поверхні трубок і отворів. Можна отримувати плівки бори-
дів, карбідів, нітридів, оксидів, силіцидів. Основним недоліком CVD-методу є необхідність нагріву деталей до високих температур. З одного боку це негатив-
но впливає на структуру і механічні властивості підкладки, а з другої викликає труднощі в забезпеченні наноструктурного стану самого покриття.
Осадження з використанням плазми тліючого розряду Як правило проводять за пониженого тиску у камері за схемою розгляну-
тих методів катодного і магнетронного розпилення або іонного плакування. Іс-
нують два різновиди розглядуваного методу.
Реактивне розпилення — матеріал мішені у вигляді іонів взаємодіє в пла-
змі тліючого розряду з іонами активного газового середовища. На поверхню об-
роблюваних деталей покриття осаджується у виді сполуки. Типовим прикладом може слугувати отримання покриття з нітриду титану, коли в плазмі тліючого розряду взаємодіють іони титану і азоту.
Другий різновид часто називають «іонноактивоване хімічне осадження з парової фази». У цьому випадку застосовують аналогічні CVD-методу хімічні реакції, але унаслідок активації плазмою тліючого розряду необхідні для їх пе-
ребігу температури знижують до 200–300 °С. Такий підхід дозволяє подолати основний недолік CVD-методу — потребу створення високих температур. Про-
те у такому разі практично неможливо отримати покриття з необхідно високою чистотою хімічного складу, тому що через недостатню десорбцію за низької температури підкладки в утворюване покриття можуть проникати реакційні га-
зи.
90