
nano_1_97_4_lec
.pdf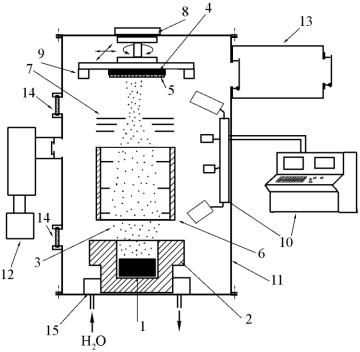
Лекція 13
Технології, основані на фізичних процесах: осадження з парової фази, термічне випаровування, катодне і магнітронне, високочастотне розпилення, іоннопроменеві і лазерні методи.
Осадження з парової фази (PVD — Physical Vapour Deposition).
Методи об'єднані спільною схемою нанесення покриття і використанням вакууму. Спочатку матеріал для покриття переводять з конденсованого стану у парову фазу, потім проводять його транспортування до підкладки (матеріалу на який наносять покриття), де відбувається осадження матеріалу покриття з парової фази і формування покриття (рис. 40). Використання вакууму полегшує переведення матеріалу в парову фазу.
Рисунок 40. — Типова схема установки для нанесення покриття PVD-методом: 1 – матеріал покриття, 2 – система переводу матеріалу в парову фазу, 3 – потік випаруваної речовини, 4 – підкладка, 5 – сформоване покриття; 6 – система транспортування матеріалу покриття в паровій фазі до підкладки, 7 – система фокусування (та/чи сканування) потоку речовини, що осаджується на підкладку, 8 – система закріплення підкладки та її контрольованого переміщення, 9 – система регулювання температури нагріву підкладки, 10 – система керування і контролю технологічними параметрами (температура підкладки, швидкість переводу матеріалу в парову фазу, тиск в камері, швидкість осадження покриття, товщина покриття тощо), 11 – вакуумна камера, 12 – система створення і підтримування високого вакууму (система вакуумних засувок, форвакуумних і високовакуумних насосів, азотна пастка тощо), 13 – шлюзова камера і система подачі та зміни підкладок, 14 – оглядові контрольні вікна, 15 – система охолодження
91
Широко розповсюдження PVD-методів обумовлено такими причинами:
можливість отримання дуже рівномірних поверхневих шарів завтовшки від 1 нм до 200 мкм з дуже добрим відтворенням властивостей;
розмір поверхні, яку покривають, може бути обмеженим, а може у ряді випадку (магнетронне напилення) складати смуги практично необмеже-
ної довжини;
можливість селективного нанесення на вибрані ділянки;
майже необмежений вибір матеріалів підкладки (теоретично матеріал пі-
дкладки може бути будь-яким);
достатня гнучкість стосовно температури підкладки;
широкий вибір матеріалів для поверхневих шарів (метали, сплави, хімічні сполуки);
можливість отримання багатошарових покриттів з шарами різної товщи-
ни та з різних матеріалів;
зміна складу, структури і властивостей шарів змінами технологічними параметрами нанесення;
можливість забезпечення високої чистоти матеріалу покриття;
мінімальне забруднення оточуючого середовища.
До недоліків цієї групи методів відносять:
складність і велику вартість технологічного і контрольного обладнання;
необхідність дуже високої кваліфікації обслуговуючого персоналу;
порівняно низьку продуктивність;
складність розробки технологічного режиму для конкретного випадку нанесення покриття, особливо у випадку покриттів точного хімічного складу;
необхідність спеціальної попередньої підготовки поверхонь.
Класифікація методу всередині групи визначається використовуваним
поєднанням способів випаровування, транспортування та осадження.
92

Термічне випаровування Вперше цей метод був використаний для осадження тонких шарів металів
ще в кінці ХІХ сторіччя. Проте тільки з появою достатньо досконалого вакуум-
ного обладнання у другій половині ХХ сторіччя він знайшов широке застосу-
вання для отримання, наприклад, просвітлених покриттів для оптики, дзеркал,
інтерференційних фільтрів, затемнювальних оптичних покриттів, декоративних покриттів на пластиках і тканинах, плівок напівпровідників та електронно-
оптичних матеріалів. Іноді цей метод називають також газофазовим осаджен-
ням, вакуумним або термічним напиленням.
Процес термічного випаровування проводять у вакуумі тиску порядку
10–3–10–5 Па . За такого тиску довжина вільного перебігу атомів або молекул становить декілька метрів. Отримана унаслідок нагріву парова фаза напилюва-
ної речовини вільно осаджується на підкладку, яка має температуру набагато нижчу, ніж температура парової фази.
Залежно від джерела нагріву отримали розповсюдження такі варіанти ме-
тоду: електротермічний нагрів (пряме пропускання електричного струму або нагрів у тиглі); нагрів в індукторі; випаровування за дії електродугового розря-
ду; нагрів електронним або лазерним променем (рис. 41).
Рисунок 41. — Декотрі варіанти методу термічного випаровування: а) випаро-
вування з металевого листа із захисним покриттям, б) металевий випаровувач в формі човника, в) керамічний тигель з зовнішнім нагрівним елементом, г) ви-
паровування лазерним або електронним променем.
Більшість методів основано на випаровуванні металевих матеріалів. На-
грів у тиглі й використання лазерного випромінювання дозволяють випарову-
93
вати широку гаму матеріалів. Зокрема перший метод можна використовувати для випаровування матеріалів з відносно невисокою температурою випарову-
вання, яку призначають залежно від температури плавлення, а також темпера-
тури і хімічної стійкості матеріалу тигля (табл. 4). Так тиглі з графіту забезпе-
чують температуру процесу до 1400 °С, з Al2O3 — до 1600 °C, з BN+TiB2 — до
1750 °C, з фольги Мо і Та із захисним покриттям — до 1850 °С, з ThO2 та ZrO2
— до 2100 °С. Важливою умовою вибору матеріалу тигля є відсутність хімічної взаємодії між ним і випаровуваною речовиною за високих температур. Для за-
безпечення кращих умов випаровування і подолання ряду інших недоліків тиг-
льового методу нагрівання використовують електронно-променеве випарову-
вання. У цьому випадку електропровідний випаровуваний матеріал поміщують у охолоджуваний водою тигель і нагрівають електронним променем за напруги прискорення променя 2–10 кВ і струму порядку 0,1 А. Пляма фокусування еле-
ктронного променя на поверхні випаровуваного матеріалу може становити до 1
мм, тому зона плавлення буде менше всього об'єму матеріалу і, отже, не буде контактувати з тиглем. Недоліком електронно-променевого методу, як і випа-
ровування з тиглів, є складність випаровування матеріалу, який складається з компонентів з різною пружністю парів за однієї й тої самої температури, що викликає складність в отриманні покриття з бажаним хімічним складом.
Застосування лазерного випромінювання (імпульсного або неперервного)
дозволяє позбутися більшості температурних і хімічних обмежень і усуває пот-
ребу в тиглях. Практично миттєве випаровування речовини уможливлює збе-
реження співвідношення хімічних компонентів в осаджуваній плівці таким са-
мим як і у випаровуваного матеріалу. До недавнього часу застосування лазерного випромінювання у такого типу процесах стримувалося через високу вартість потужних імпульсних і неперервних лазерів та складністю юстування оптичних систем для транспортування, фокусування і наведення лазерних про-
менів.
94
Таблиця 4. — Температури нагрівання декотрих речовин за методом термічного випаровування у вакуумі
Речовина |
Температура |
Використовувані температури |
плавлення, оС |
випаровування, оС |
|
алюміній |
650 |
1250…1400 |
|
|
|
миш'як |
820 |
> 300 |
|
|
|
барій |
710 |
> 610 |
|
|
|
берилій |
1283 |
>1250 |
|
|
|
вісмут |
271 |
650…1000 |
|
|
|
вуглець |
3700 |
> 2600 |
|
|
|
хром |
1900 |
> 1400 |
|
|
|
залізо |
1536 |
> 1480 |
|
|
|
мідь |
1084 |
> 1300 |
|
|
|
золото |
1063 |
> 1400 |
|
|
|
срібло |
961 |
> 1150 |
|
|
|
платина |
1770 |
> 2100 |
|
|
|
тантал |
3000 |
> 3100 |
|
|
|
вольфрам |
3380 |
> 3250 |
|
|
|
цинк |
420 |
350–1000 |
|
|
|
CdTe |
1100 |
750–850 |
|
|
|
BeO |
2530 |
2100–2700 |
|
|
|
Al2O3 |
2030 |
> 1850 |
|
|
|
Використання вакууму призводить до того, що у ряді випадків темпера-
тура, за якої досягають інтенсивну швидкість випаровування для уможливлення бажаною продуктивності процесу, виявляється нижчою за температуру плав-
лення випаровуваної речовини. Для оцінки робочих температур нагріву зазви-
чай використовують температуру, яка забезпечує значення усталеного тиску парів випаровуваного матеріалу не нижче 1 Па. Для більшості матеріалів робочі
95
температури випаровування змінюються в межах від 1100 до 2600 °С (див.
табл. 4). Швидкість осадження покриттів може становити від декількох ангст-
рем до декількох мікрометрів за секунду (наприклад, для W — до 5 мкм/с, для
Al — до 40 мкм/с). Для покращення адгезії або створення заданої структури осаджуваного покриття у ряді випадків застосовують підігрів підкладки.
Для створення покриття зі сплавів або сполук, як правило, проводять ви-
паровування кожного їх компонента від незалежних джерел. Це пов'язано з тим,
що під час випаровування складної речовини її компоненти можуть мати силь-
но відмінні значення тисків парів. У цьому випадку склад парової фази, а отже,
і склад покриття буде відрізнятися від складу випаровуваної речовини. Окрім того, випаровування сполук (хімічних чи інтерметалевих) часто супроводжу-
ється процесами дисоціації та/або асоціації, що також перешкоджає отриманню заданого складу покриття.
До переваг методу термічного випаровування належать відносна простота обладнання і контролю процесу, а до недоліків — слабка адгезія покриття вна-
слідок малої енергії осаджуваних на підкладку атомів чи молекул і висока чут-
ливість до наявності на поверхні підкладки сторонніх плівок і забруднень.
Вплив цих недоліків дещо послаблюють завдяки застосуванню спеціальних ме-
тодів підготовки поверхні (ультразвукове очищення поверхні, хімічне, електро-
хімічне очищення, хімічне або іонне травлення).
Метод термічного випаровування достатньо широко використовують у виробництві жорстких магнітних дисків для комп'ютерів. Підкладкою слугує алюмінієвий диск з висотою мікрошорсткістю поверхні менше за 20 нм з нане-
сеним на нього аморфним нікель-фосфорним підшаром завтовшки приблизно
20 мкм (для покращення адгезії та компенсації різниці у величині коефіцієнтів термічного розширення підкладки та покриття). Спочатку напилюють проміж-
ний металевий шар, наприклад Ni–Fe завтовшки 500–1000 нм, а вже потім — основний шар з магнітного матеріалу, наприклад сплаву на основу Co або Co– Cr, завтовшки 100–500 нм. Поверх всього покриття наносять зносостійкий за-
хисний вуглецевий шар завтовшки 30–50 нм. Також термічне напилення вико-
96

ристовують також у виробництві CD–дисків. На диск з пластмаси наносять алюмінієве основне покриття завтовшки у нанометровий діапазон. В обох ви-
падках для забезпечення високої чистоти матеріалів тиск у вакуумній камері підтримують менше з 10–5 Па.
Такі матеріали для електронно-оптичної техніки і для створення регуляр-
них наноструктур, у тому числі двомірних фотонних кристалів, як фулеренові й композитні фулереноосновні плівки також отримують розглядуваним методом.
Наприклад, плівки С60–CdTe (рис. 42) завтовшки 200–600 нм на підкладках
GaAs вирощують шляхом випаровування міксту заданого складу у вакуумі тис-
ку 10–4 Па і температурі підігріву підкладки приблизно 160 °С.
Рисунок 42. — Зображення то-
пографічної структури поверхні плівки С60 – 40 % CdTе, отри-
мане за допомогою растрового електронного мікроскопу
Останнім часом активно проводять прикладні дослідження стосовно отримання тонких покриттів і шаруватих композитів на їх основі використан-
ням для випаровування матеріалів випромінювання імпульсного лазера з дуже коротким часом імпульсу (аж до фемтосекундного діапазону). Такий метод у літературі часто позначають як PLD (Pulsed Laser Deposition). Наприкладl, так отримують плівки Y2O3–ZrO2 на кремнію для електроніки; шаруваті композити,
які складаються з покриття Sm–Fe завтовшки 20 нм, підшару Та завтовшки100
нм і кремнієвої підкладки; магнітні плівки Ni з середнім розміром кристалітів
40 нм.
Катодне і магнітронне розпилення Найпростіший варіант цього методу — двохелектродний (рис. 43, а). Він
оснований на використанні плазми тліючого розряду у вакуумі за тиску 1–0,1
Па. Перед початком процесу для вилучення газів у вакуумній камері зазвичай створюють вакуум до10–2–10–3 Па, потім подають у камеру інертний газ і до-
97

водять тиск до робочих значень. Частіше за все використовують аргон. Між ка-
тодом (мішенню з розпилюваного матеріалу) і анодом (як правило, тримачем підкладки, на яку наносять покриття) прикладають постійну напругу 1–5 кВ.
Така величина напруги перевищує потенціал іонізації і напругу пробою, тому з катоду емітується достатня кількість вторинних електронів, які, рухаючись від катоду до аноду, стикаються з атомами газу й іонізують їх.
Рисунок 43. — Основні принципіальні схеми катодного розпилення: а) двох-
електродний метод, б) чотирьохелектродний метод, 1 – вакуумна камера, 2 —
тримач підкладки (за двохелектродного методу також є анодом), 3 – підкладка,
4 – зона плазми тліючого розряду, 5 – мішень (розпилюваний матеріал), 6 – ос-
новний катод, 7 – тепловий катод, 8 – стабілізувальний електрод, 9 – анод
В результаті такої взаємодії виникає тліючий розряд. Іони інертного газу бомбардують мішень-катод і вибивають з неї атоми покриття. Останні осаджу-
ються на розміщену поблизу підкладку. Підкладка разом з тримачем замкнена на масу, але у ряді випадків функції анода і тримача підкладки можуть бути су-
міщені. Для того, щоб забезпечити достатню імовірність досягнення мішені іо-
нами з високими значеннями енергії (і відповідно забезпечити достатню проду-
ктивність процесу розпилення) анод і катод не повинні бути розташовані досить близько. Зазвичай віддаль обирають у такий спосіб, щоб анод не попа-
дав у ділянку від'ємного свічення. З іншого боку, якщо присунути анод до краю темного простору, то віддаль між катодом і анодом буде менше величини віль-
98
ного перебігу електронів, й іонізації газу не буде відбуватися. Швидкість оса-
дження за такого варіанту методу достатньо низька (порядку 0,1 мкм/хв).
Високочастотне розпилення Спосіб є різновидом катодного. Загальна схема аналогічна схемі на рис.
43 а, тільки замість постійного електричного струму використовують змінний високочастотний напругою 0,3–2 кВ, частотою 13–14 МГц. До того ж у ряді ви-
падків на анод подають додатковий потенціал зміщення –(0,1–0,5) кВ, що до-
зволяє зменшити ступінь забруднення нанесеного на підкладку матеріалу газо-
вими домішками.
Для збільшення продуктивності процесу застосовують більш складні схеми, у тому числі чотирьохелектродний метод і метод магнетронного розпи-
лення.
За чотирьохелектродною схемою (рис. 43, б) напруга розряду може бути більш низькою, а розрядний струм і напругу на мішені регулюють незалежно один від другого. Розряд виникає унаслідок різниці потенціалів між тепловим катодом і анодом, а розпилення відбувається за зіткнення іонів газу з катодом-
мішенню, на який подають від'ємний потенціал. Додавання теплового катоду,
який нагрівається до температури, що забезпечує теплову емісію електронів,
дозволяє суттєво полегшити утворення плазми і проводити процес за більш ви-
сокого вакууму (0,1 Па), а отже забезпечувати вищу чистоту напилюваного ма-
теріалу. Швидкість осадження становить приблизно 1 мкм/хв. Недоліком цього варіанту є значний нагрів підкладки, який у ряді випадків досягає 300–500 °С.
Катодне розпилення застосовують переважно для нанесення шарів з ме-
талевих матеріалів.
Магнетронне розпилення (рис. 44) — на ділянку розряду для збільшення продуктивності процесу накладають магнітне поле, яке концентрує плазму на мішені-катоді. Силові лінії магнітного поля спрямовані від одного полюса пос-
тійного магніту до другого. Траєкторія руху електронів розташовуються між місцями входу й виходу силових ліній магнітного поля. У цих місцях і локалі-
зується інтенсивне утворення плазми і перебіг процесів розпилення. Унаслідок
99

такої локалізації з'являється можливість розпилення не тільки металевих, але й діелектричних і напівпровідникових матеріалів. Метод магнетронного розпи-
лення дозволяє зменшити нагрівання підкладки до 100-250 °С і забезпечити швидкість осадження до 1–2 мкм/хв. На рис. 45 показано приклад структури алюмінієвого наноструктурного покриття, нанесеного на мартенсито-старіючу сталь 06Н16К4М4Т2Ю за методом магнетронного розпилення. Покриття нано-
сили за дистанції підкладки від розпилюваного матеріалу ~ 70 мм за таким тех-
нологічним режимом: струм розряду 5 А, напруга розряду 480–500 В, тиск ар-
гону 0,4–0,5 Па, напруга зміщення, яку подавали на підкладку –50 В.
Рисунок 44. — Схема магнетронного розпилення: 1 – вакуумна камера, 2 – три-
мач підкладки (за двохелектродного методу також є анодом), 3 – підкладка,
4 – зона концентрації плазми тліючого розряду, 5 – розпилюваний матеріал,
6 – катод, 7 – анод кільцевої або рамочної форми, 8 – магніт, 9 – напрямки си-
лових ліній магнітного поля
Рисунок 45. — Магнітронне покриття з алюмінію на мартенсито-старіючій сталі 06Н16К4М4Т2Ю
Іонно-променеві методи Ця група методів отримала розвиток відносно нещодавно. Основою мето-
дів є використання концентрованих потоків іонів. Іонно-променева технологія
100