
Konspekt_lekcii автом.пр.проц.в. маш.(Норко)
.pdf51
2.10 Захватные устройства промышленных роботов
Захватное устройство (захват) промышленного робота предназначено для захватывания предмета обработки и удержания его в процессе перемещения. Вид захвата определяется формой, размером, массой и свойствами захватываемого предмета обработки, а также специфическими требованиями технологическою процесса.
В зависимости от принципа действия захваты делят на:
-механические (работают по принципу зажима с удержанием детали с помощью сил трения и запирающего действия рабочих элементов, а также ио принципу использования выступающих частей рабочих элементов устройств в качестве опоры для детали);
-вакуумные (работают в результате сил, возникающих при разности давлений);
-магнитные (работают с помощью сил магнитногопритяжения).
По числу рабочих позиций захваты всех типов разделяют на:
-однопозициониые (имеют одну рабочую позицию);
-многопозиционные(имеют несколько рабочих позиций).
Захватные устройства изготовляют несменными и сменными (требуют малого времени для смены, могут заменяться автоматически),
Для загрузки металлообрабатывающих станков, как правило, используют механические зажимные устройства. Кроме закрепления заготовки эти устройства выполняют функции ориентации, центрирования предмета обработки.
Узкодиапазонные захватные устройства при переналадке обеспечивают возможность закрепления детали за поверхность с размерами, включающими соседние меньшие значенияряда: 1; 4; 12; 32; 63; 100; 125; 160; 200; 250; 320;
400; 500 мм. Эти захваты обычно выполняют на базе клиновых и рычажных механизмов.
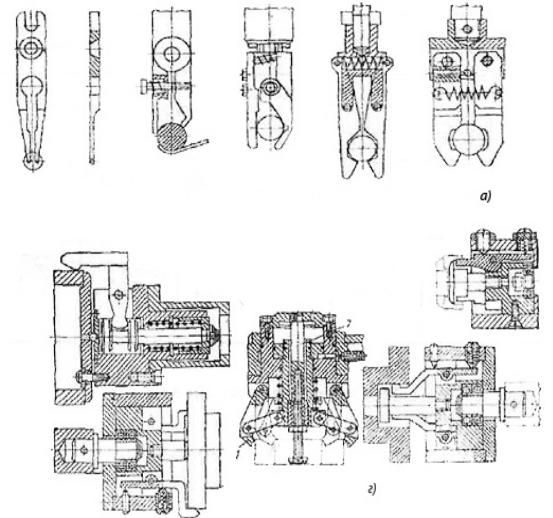
52
Широкодиапазонные захваты обладают возможностью закрепления без переналадки деталей с размерами, включающими соседние меньшие значения указанного выше ряда. Эти захваты выполняют обычно с использованием реечных и зубчатых передаточных механизмов. Они имеют более широкие технологические возможности, чем узкозахватные. Механические захваты (рис.2.16) используются для загрузки станков деталями типа тел вращения или коробчатой формы.
Рис.2.16. Захваты промышленных роботов
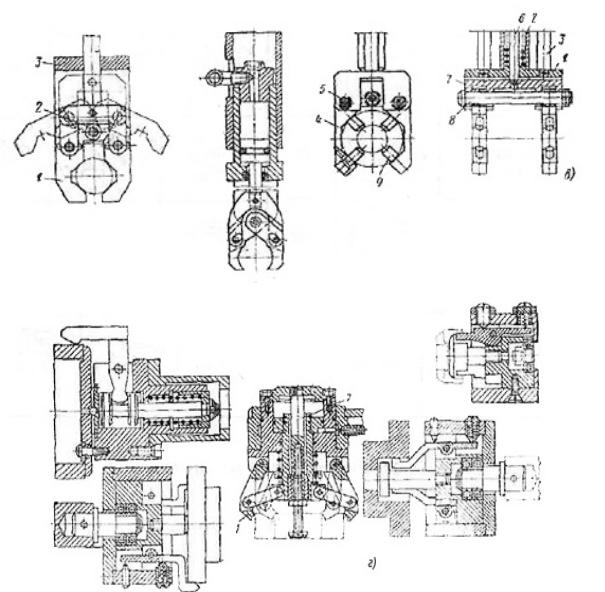
53
Продолжение рис. 2.16
Рис.2.16. Захваты промышленных роботов: а) неуправляемые типа пинцета или клещей для валов; б)неуправляемые для втулок в)клещевые управляемые для валов; г) патронные для захвата за наружную поверхность; д) оправочные.
По числу рабочих позиций захваты всех типов разделяют на однопозициониые (имеют одну рабочую позицию) и многопозиционные (имеют несколько рабочих позиций).
Захватные устройства изготовляют несменными и сменными (требуют малого времени для смены, могут заменяться автоматически),
54
Для нагрузки металлообрабатывающих станков, как правило, используют механические зажимные устройства. Кроме закрепления заготовки эти устройства выполняют функции ориентации, центрирования предмета обработки.
Широкое применение находят многонозиционные (многоместные) захватные устройства. При наличии на руке робота двух захватов цикл загрузки-разгрузки оборудований сокращается. Во время обработки предыдущей заготовки робот захватывает заготовку для обработки и смешается на максимально близкое расстояние к рабочей зоне. После окончания обработки ПР свободным захватным устройством захватывает обработанную заготовку и после поворота устанавливает очередную заготовку, в приспособление станка. Во время обработки новой заготовки робот укладывает обработанную заготовку в тару или на тактовый стол, В результате совмещения вспомогательных переходов с работой станка время загрузки может сократиться в 2 — 3 раза. Современные захватные устройства помимо захватов для удержания заготовок имеют захваты для смены инструментальных головок или блоков.
Промышленные роботы обычно комплектуют набором типовых захватных устройств, Часто при переходе на обработку другой детали меняют не сам захват, а его сменные рабочие элементы (призмы, губки и т. д.).
К захватным устройствам предъявляют следующие требования: надежность захватывания и удержания объекта во время разгона и торможения подвижных элементов ПР, точность базирования заготовки в захвате, недопустимость повреждения или разрушения предмета обработки, прочность при малых габаритных размерах и массе. Особое внимание должно быть обращено на проверку допустимых для данного захватного устройства сил, моментов, нагрузок на местакрепления.
При частой смене заготовок или при обслуживании одним ПР нескольких станков захватные устройства должны обеспечивать возможность работы с заготовками с размерами, формой и массой в широком диапазоне. В
55
этом случае наиболее приемлемыми являются широкодиапазониые захватные устройства. В некоторых случаях возникает необходимость применения захватных устройств с автоматической сменой их. Требование быстрой смены захватного устройства и его элементов часто является важным, так как восполняет недостаток подвижности самого ПР и позволяет более полно использовать робот в роботизированном процессе.
Расчет механических захватных устройств включает проверку на прочность деталей захвата. Кроме того, необходимо определить силу привода захватного устройства, силу в местах контакта заготовки и губок, проверить отсутствие повреждений поверхности заготовки или детали при захватывании, возможность удержания захватом заготовки (детали) при манипулировании, особенно в моменты резкихостановок.
Соотношение между силой Р привода, силами F на губках или моментом М на губках захватного устройства определяют из условий статического равновесия. Так, для захвата с рычажным механизмом, показанным на рис. 2.17, из условия ∑ Р = 0 в точке С имеем
2 F23 sin γ – P =0 ,
откуда
F23 = P /(2 sin γ ) /
Из условия ∑М==0 относительно точки А следует
P = ( F / η ) (2 h1 sin γ ) / h2 ,
где η - КПД механизма.
При известном моменте М сила привода
P η = (∑j=1…n Mj sin γ)/ b ,
где Мj- — момент сил на губке; b — плечо рычага; п — число губок (обычно п =2).

56
Рис.2.17. Расчетная схема захватногого устройства с рычажиым механизмом
Данный захват обладает эффектом самоблокировки, так как рычаг проходит через «мертвое» центральное положение.
Для захватного устройства с клиновым механизмом сила привода
(рис.2.18)
Рис.2.18. Расчетная схема захватного устройства с клиновым механизмом
57
P η = (∑j=1…n Mj tg (β + ρ))/ b ,
|где р — приведенный угол трения, учитывающий сопротивление осей рычагов (при осях на подшипниках качения р — 1○10'; на подшипниках скольжения р = 3°); п — число губок захвата (обычно п = 2); т\ = 0,95 — КПД шарниров; р = 4°- 8° — угол клина.
Для захватов с симметричным расположением губок при М 1=М2 = М сила привода
P η =( 2 M tg (β + ρ))/ b .
Для захватных устройств, показанных на рис.2.19, соотношения между силами Р и F- следующие:
P =( F/η) (2 l)/ (a sin ɵ) |
(рис.10а) |
P =( F/η) (b / (b + c) |
(рис.10б) |
P =( F/η) (b sin ɵ sin (2 Ф))/( l sin Ф sin (ɵ + Ф)) (рис.10в)
P =( F/η) (a c) / ( b ( c – d)) |
(рис.10г) |
P =( F/η) (2 b/ c) tg ɵ |
( рис.10д) |
P =( F/η) (2 b/ a) |
(рис.10е) |
P =( F/η) (2 b c) / ( l ( c + d)) |
(рис.10ж) |
P =( F/η) (a d) / ( b ( c – d)) |
(рис.10з) |
P =( F/η) (2 b/ a) cos2 ɵ |
(рис.10и) |

58
Рис. 2.19. Схемы захватных устройств ПР.
Если захватное устройство имеет несколько губок, то сила захвата на каждой губке
R1=(l-c)Q/l и R2=cQ/l –для схемы, приведенной на рис2.20а; R1=(l+c)Q/l и R2=cQ/l –для схемы, приведенной на рис.2.20б.

59
Рис2.20. Схемы для определения сил, действующих, |
на губки от |
силы тяжести |
|
Силы захватывания, которые требуются для удержания заготовки в процессе ее перемещения,
F = К1К2К3 mg,
где т - масса заготовки; g — ускорение свободного падения; К1 - коэффициент безопасности, значение которого зависят от условия применения ПР и расположения других элементов РТК; К1 = 1,2— 2,0; К2 — коэффициент, зависящий от максимального ускорения А, с которым робот перемещает заготовку, закрепленную в его захвате; К2=1+А/g; К3- коэффициент передачи, зависящий от конструкции захвата и расположения в нем заготовки.
Например, для двухшарнирного захвата (рис, 2.21)
Р dх = 2Fb dɵ;
здесь dх — малое перемещение привода; dɵ - соответствующее малое перемещение губки (угловое).
Так как R2 = R1 + mg, в предельном случае при Р = Р min имеем R1=0; R2= тg, причем
Рmin dх = R1h dɵ + R2b dɵ= mg b dɵ,
где R1 и R2 — силы, действующие на губки.
Тогда
F/ ( mg) = K3 =1/2.
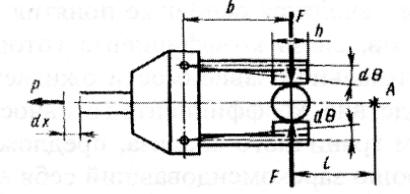
60
Таким образом, для данной конструкции захвата К3 = 1/2. В табл. 10 приведены значения К3 для различных относительных расположений захвата и заготовки.
Рис.2.21. Двухшариирное захватное устройство; точка А центр тяжести консольно-закрепленной заготовки
Сила захватывания для схемы, приведенной на рис. 2.22 а,
N1 |
=( Rn sin α2)/ ( sin (α1 |
+ α2) |
|
N2 |
=( Rn sin α1)/ ( sin (α1 |
+ α2) |
|
|
Где Rп - реакция от расчетной нагрузки на п-й захват; α 1 , α 2 — углы |
||
контакта |
заготовки с губкой. |
||
Сила захватывания для схемы, приведенной на рис, 2.22 6, |
|||
|
N1 |
= Rn / ( 2Cosα1 ); |
F1 = μ N1 , |
|
где |
Ni — нормальная сила для 1-й точки контакта; Fi — сила трения в i-й |
точке контакта; Кn — реакция на n-и захват от расчетной нагрузки;αi — угол контакта поворотной центрирующей или призматической губки с заготовкой для 1-й точки контакта; μ - коэффициент трения губки захвата о деталь; для незакаленных губок без насечки (стали 45, 50)μ = 0,12 - 0.15; для закаленных губок в виде гребенки с острой насечкой (стали 651. 60С2. У8А, У10А) при твердости HRС > 55μ = 0,3 - 0,35.
Таблица 10. Зиачеяия коэффициента К3