
Konspekt_lekcii автом.пр.проц.в. маш.(Норко)
.pdf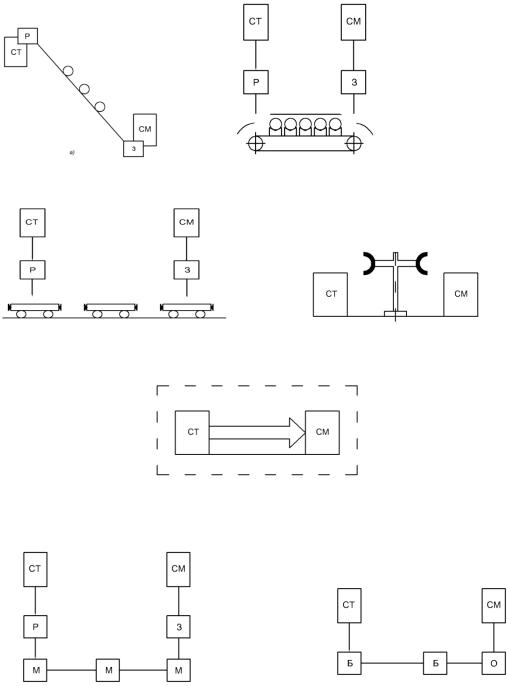
31
а) б)
в) |
г) |
д)
е) |
ж) |
Рис.2.7. Схема автоматического транспортирования: Б- бункер; О- ориентирующее устройство; М- магазин.
Характерной особенностью кассеты ( рис.2.8) для автоматизированного производства является: наличие постоянных основных баз (Б) для точной установки кассеты около станка или сборочной машины; наличие определённого нормированного расстояния между комплектами вспомогательных баз для ориентации деталей; наличие определённого
32
нормированного расстояния между комплектами вспомогательных баз для ориентации деталей; наличие определённых размеров Ах, Бу с допусками, определяющих положение вспомогательных баз относительно основных баз кассет. Это необходимо для автоматической загрузки и разгрузки тары манипулятором или роботом. Робот может брать детали, находящиеся в определённом положении в заранее известных координатах пространства, задаваемых управляющей программой в заданном порядке. Из кассеты заготовки в заданном программой порядке из ячеек кассет роботом устанавливаются в патрон станка для обработки и обработанную заготовку снова ставить на свободное место кассеты и так до тех пор, пока все заготовки не будут обработаны. Причём если известны постоянные шаги (х и lyрасположения гнёзд, то роботу нет необходимости задавать в программе координаты каждого гнезда. В этом случае достаточно задавать положение первого гнезда (шаги tx, ty); aтакже количество рядов и ячеек в одном ряду и порядок выемки. Координаты каждого гнезда устройство числового программного управления робота вычислить автоматически. Если кассеты или детали будут другими или по другому расположены, то достаточно поменять программу и схват робота и он сможет работать в новых условиях. Смена программы и схвата на многих современных роботах может осуществляться автоматически без вмешательства человека.

33
Рис. 2.8. Транспортная тара, сохраняющая ориентированное положение транспортируемых заготовок и деталей при сборке: а) детали (заготовки); б) установочные элементы; в) корпус; г) транспортная тара в сборе
2.6 Устройства подачи ориентированных деталей
Для подачи ориентированных деталей из магазинов, кассет, лент к сборочным, обрабатывающим или другим технологическим позициям используются разнообразные устройства, отличающиеся, прежде всего
34
степенью универсальности и гибкости. Промышленные роботы являются наиболее универсальными и гибкими устройствами. Однако стоимость загрузочного робота с системой управления на базе ЭВМ (CNC) значительно больше многих других устройств, не имеющих такой гибкости и универсальности. Абсолютное большинство современных роботов может брать деталь или заготовку только в предварительно ориентированном виде и в заданной области пространства, что требует применения кассет, магазинов или бункеров с ориентирующими устройствами. Манипуляторы отличаются от роботов постоянной или цикловой программой работы, которая не может так быстро меняться как у роботов. Манипулятор в отличие от роботов может брать детали или заготовки только в одном определённом месте, на которое он настроен. Поэтому, для того чтобы манипулятор мог работать с деталями в ячейках кассеты необходимо дополнительное устройство - тактовый стол, который должен перемещать кассету с деталями так, чтобы они оказывались по очереди в зоне схвата манипулятора.
В условиях массового и крупносерийного производств для подачи ориентированных деталей заготовок как правило создаются специальные устройства, приспособленные только для конкретной детали или близких по форме деталей. Примером может служить приведённое на рис.2.9 устройство для подачи дисков или других плоских деталей. Подающее устройство содержит поворотный стол 2 с отверстиями 3, диаметр которых больше диаметров транспортируемых дисков 1. Диски 1 уложены стопкой в магазине 4, Нижний диск опирается на поверхность поворотного стола 2. Стол 2 может вращаться непрерывно или поворачиваться дискретно на определённый фиксированный угол. Как только отверстие 3 при вращении стола займёт положение под магазином 4, стопа дисков / опустится вниз, т.к. нижний диск падает в отверстие стола. Стол при повороте перемещает диск по неподвижной плите 5, имеющей вырез 6. Под вырезом б установлен склиз 7. Когда при повороте стола 2 его отверстие 3 с диском 1 окажется над вырезом б, диск 1 упадёт на склиз 7 и перемещаясь по наклонной плоскости

35
склиза 7 попадёт в рабочую зону сборочного автомата или обрабатывающего оборудования. При непрерывном вращении стола разность между диаметрами отверстия и диска определяется из следующего предположения: время свободного падения диска на высоту (толщину) h стола должно равняться времени прохождения пути, равному разности диаметров, при повороте стола с частотой вращения ω стола, т.е.
Dотв.-dдиска = ωR (2h/g)(1/2)
где: Don,- диаметр отверстия стола; dдиска-диаметр диска; ω- частота вращения стола; R - расстояние от центра отверстия до оси вращения стола.
Рис. 2.9. Устройство для подачи дисков.
Схема специального устройства для подачи валов в центры станка показана на рис.2.10. В бункере помещены заготовки валов с центровыми отверстиями 2. Отсекатель 3 периодически отсекает поток заготовок на выходе бункера. Рычаг 4, расположенный на оси 5, может поворачиваться, занимая три различных положения левым плечом 4. В верхнем положении левого плеча 4 происходит загрузка заготовки в центры станка, расположенные по оси 0. В положении I правое плечо 6 рычага опущено и очередная заготовка скатывается по плечам 6 и 4 рычага в положение, при котором ось заготовки располагается по оси центров станка. Далее осуществляется подвод заднего центра и заготовка вдвигается в патрон

36
станка. Плечо рычага 4 опускается в положение II. В этом положении рычага осуществляется обработка заготовки. После окончания обработки задний центр станка отходит, обработанная заготовка падает на плечо 4 рычага. Рычаг опускается в нижнее положение III, при котором обработанная заготовка скатывается по направляющим 7 в приёмный бункер 8. В этом положении рычага отсекатель 3 поднимается и пропускает очередную заготовку из бункера 1 к торцу плеча 6 рычага. Далее плечо 4 рычага идёт вверх и цикл повторяется. -
Рис.2.10. Схема устройства в центры станка
2.7Проектирование лотков
Лотки - наиболее простые устройства, предназначенные для передачи ориентированных деталей самотёком. Лотки могут иметь различный поперечный профиль (прямоугольный, круглый.,V-образный и др.), различное расположение в пространстве: прямые наклонные и вертикальные, спиральные и т.д. Детали по лоткам перемещаются по
наклонным поверхностям под действием |
собственного веса. |
Лотки |
могут быть открытыми и закрытыми, |
как показано на рис.2.11. В |
|
открытых лотках (рис.2.11а) можно в любом месте вынуть или |
вставить |
деталь. В закрытых лотках (рис.2.11б) выпадение детали не может произойти. Лотки используются в основном в комплекте с другими
|
|
37 |
устройствами |
в массовом |
и крупносерийном производстве. При |
расчёте лотков |
необходимо |
выбрать зазор ∆l между изделием и |
направляющими стенками лотка, такой, чтобы детали не заклинивались при скольжении или качении по лотку. Для круглых деталей с плоскими терцами минимальное значение зазора ∆l вычисляется согласно расчётной схеме, приведённой на рис.2.11 в. Как следует из этого рисунка:
L= l + ∆l = ( d2 + l2 ) ½ Cos α .
. Но с другой стороны мы можем записать:
Cos2a + Sin2а = 1 или Cos2а (1 + tg2a) = 1.
Отсюда получим Cos а = 1/ (1 + tg2a )1/2 и окончательно l + ∆l =( ( d2 + l2 ) / (1 +tg2 α )) ½
или
∆l =( ( d2 + l2 ) / (1 +tg2 α )) ½ -l .
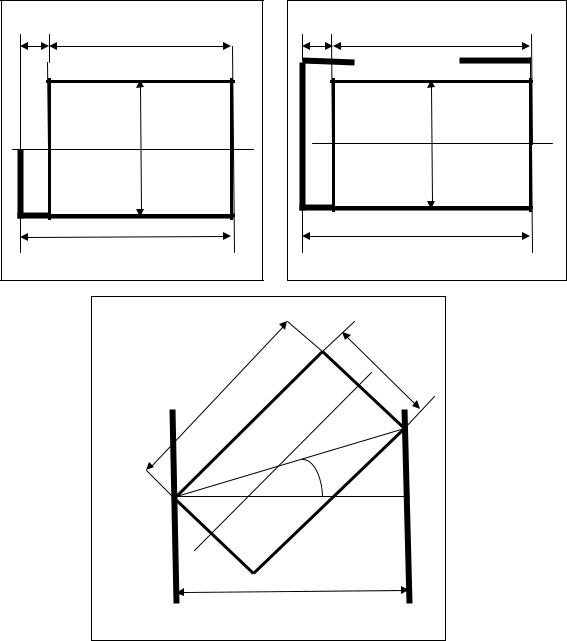
|
|
38 |
|
a |
l |
б |
l |
|
dd |
|
|
|
L |
|
L |
|
в |
|
|
|
l |
|
d |
|
|
α |
|
|
|
L |
|
Рис.2.11. Лотки: а)- открытый; б)- закрытый; в)- расчетная схема.
Для того, чтобы не произошло зак линивание угол α |
должен |
|
быть больше или равен углу трения, т.е. |
tga>f, где f-коэффициент |
|
трения. Поэтому, максимальному значению |
зазора будет соответствовать |
|
случай когда tga =f, т.е. |
|
|
∆l =( ( d2 + l2 ) / (1 +f 2)) ½ -l . |
|
|
На практике зазор ∆l определяют по формуле∆l max ≥ ∆l =T1+TL+ |
min |

39
где: Тl - допуск на длину перемещаемой детали; ТL- допуск на ширину лотка; min наименьший гарантированный зазор.
Гарантированный минимальный зазор min при отсутствии загрязнения лотка и заготовок принимают равным допуску на длину заготовки или детали по 10-11 квалитету точности, если заготовки загрязнённые, то по 1214 квалитету точности.
Угол наклона γ лотков-скатов и лотков-склизов назначают в зависимости от шероховатости поверхностей заготовок и лотков, твёрдости и степени загрязнения заготовки;, наличия на их поверхности смазки и рассчитывают по формулам, приведённым в табл.2. 4.
Таблица 2.4. Формулы для расчета угла наклона лотка
Лотки |
|
|
|
|
|
|
|
Формулы |
|||||
|
|
|
|
|
|
|
|
|
|
|
|
|
|
Коробчатые прямолинейные |
|
|
|
|
|
|
|
|
|
|
|
|
|
|
|
|
2H |
á |
|
|
|
|
|
||||
лотки-скаты |
sin ≥ Kf |
f |
|
|
|
|
|
+tg (α0 −β′) |
|||||
|
|
r |
|
|
|||||||||
|
|
|
|
|
|
|
|
|
|
|
|
|
|
|
|
|
|
|
|
|
|
|
|
|
|||
Коробчатые прямолинейные |
tgγ = |
|
2ghf ′ |
|
|
|
|
|
|
|
|||
лотки-склизы |
|
|
|
|
|||||||||
2gh +U02 −U 2 |
|
|
|
||||||||||
|
оптимальный угол наклона γ = 20 −25 |
||||||||||||
|
|
|
|
|
|
|
|
||||||
Роликовые прямолинейные лотки |
|
|
|
mp |
d0 fö |
|
2K′ |
||||||
|
tgγ ≥ |
1+ z |
|
|
|
|
|
|
|
|
= |
|
|
|
m |
|
Dð |
Dð |
|||||||||
|
|
|
|
|
|
|
|||||||
|
|
|
|
|
|
|
|
|
|
|
|
|
|
Обозначения для таблицы: f- коэффициент трения |
качения; |
а 0- |
угол между диагональю и образующей заготовки; β '- |
угол перекоса; |
К- |
коэффициент, зависящий от шероховатости поверхности и чистоты лотка |
|
К=1,2 … 1,5 для обычных и К= 2,5 … 3 для загрязнённых, лотков; Нб - высота борта лотка; U0 и U соответственно скорость движения заготовки начальная и конечная; /'- приведённый коэффициент трения; h- высота наклонной поверхности (высота скольжения); fц–коэффициент
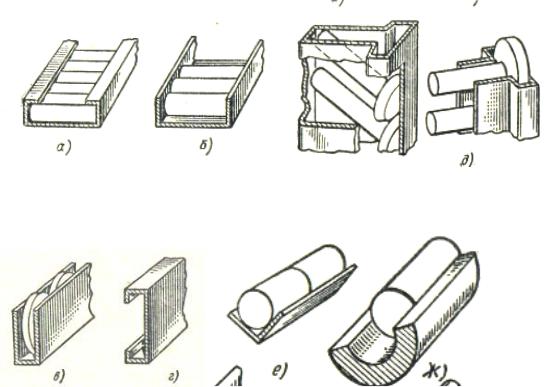
40
трения в цапфах роликов; Dp- диаметр роликов; К'- коэффициент трения качения заготовок по роликам; z - число роликов; тр- масса ролика; т - масса заготовки; d0- диаметр оси ролика; r=d/2- радиус заготовки.
Поперечные сечения лотков приведены на рис.2.12, а формулы для расчета зазора ∆l в лотке для заготовок с различными торцами в табл. 2.5.
Рис.2.12. Поперечные сечения лотков