
Konspekt_lekcii автом.пр.проц.в. маш.(Норко)
.pdf111
СД- серводвигатель перемещения каретки вдоль оси Z; ПР- преобразователь сигналов)
При отклонении щупа по оси Z от исходного положения всего на 1мкм внутри головки срабатывают электрические контакты и электрический сигнал через преобразователь (ИР) поступает в УЧПУ. Подача каретки с головкой на инструмент .мгновенно прекращается, а координата положения каретки по оси Z, отсчитываемая при программном перемещении датчиком обратной СВЯЗИ (ДОС), запоминается в регистре. Поскольку положение шпинделя известно
(размер Аст), то автоматически вычисляется размер Ари .
Использование контактной головки на многоцелевом станке для автоматического измерения вылета инструмента позволяет не только отказаться от настройки многих инструментов вне станка и повысить тем самым степень автоматизации, но, кроме того, позволяет компенсировать погрешности установки инструмента в шпиндель станка, размерный износ, тепловые деформации технологической системы. Использование описанного метода регулирования требует получение дополнительной информации, которая обеспечивается контактной головкой, и дополнительными затратами времени на осуществление измерений.
Размеры получаемые между поверхностями, обработанными за одну установку.
Размер Г, получаемый между двумя поверхностями, обработанными на многоцелевом станке за одну установку заготовки, зависит от двух размеров Г1и Г2, полученных от каждой обработанной поверхности до одной и той же технологической базы заготовки как размер третьего вида Е (рис, 4.7). Этот случай показан на рис. 4.10. Как видно из этого рисунка: Г =Г2-Г1 и для рассеивания этих размеров: ω∆=ω1+ω2.
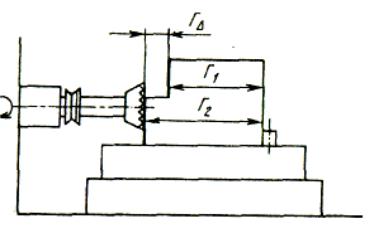
112
Рис. 4.10. Схема получения размера между поверхностями, обработанными за однуустановку заготовки и режущего инструмента.
В соответствии с выражением для полей рассеяния размер Г получается менее точным, чем каждый из размеров Г1 а Г2. Это происходит потому, что и в данном случае погрешность настройки и установки режущего инструмента при обработке обоих поверхностей заготовки одинаковы по величине и направлению. Однако на размер Г∆ эти приращения влияния не окажут, т.к. одинаковые погрешности взаимно компенсируются на размере Г , что следует из следующей закономерности:
Г11=Г1+∆3+∆РИ Г21=Г2+∆3+∆ри
Г∆= Г11-Г21=Г1+ ∆3+∆РИ –( Г2+∆3+∆ри )= Г1-Г2=ГД.=Г∆ Отсюда следует, что увеличение или уменьшение обоих размеров Г1 и Г2
на одну и те же величину не изменяет размера между поверхностями, обработанными за одну установку.
4.4Межоперационные размерные связи.
Межоперационными размерными связями называют технологические размерные связи, проявляющиеся во взаимодействии размеров детали и размеров заготовки на различных стадиях изготовлении детали. Простейшей

113
межоперационной размерной связью является связь размеров заготовки, детали и припуска на обработку, показанная на рис. 4.11. В результате обработки заготовки, имевшей размер Иь в размер детали й2 удаляется припуск Z, который в данном случае является функцией двух размеров И1 и И2. Связь определяется уравнением:
Z=И1-И2=И∆ .
Рис. 4.11. Связь размеров заготовки И1, изделияИ2 и припуска Z .
Рассмотрим более сложный случай межоперационных размерных связей. Пусть необходимо изготовить двухступенчатый валик (рис. 4.12) Валик обрабатывается на токарном станке за два установа, как показано на эскизах наладок. Все торцовые поверхности заготовки пронумерованы по порядку. Припуски показаны с двойной индексацией. Припуск Z32 означает, что он снимается с поверхности № 2 на операции № 3. Каждый из припусков в описанной схеме является замыкающим звеном соответствующей технологической размерной цепи:
Z11 = Б0 — Б\; Z32 = Бг — А2 — Б2.
Для того чтобы составить уравнения, можно схему технологических размерных связей составить по методике проф. В.В. Матвеева (рис. 4.13).
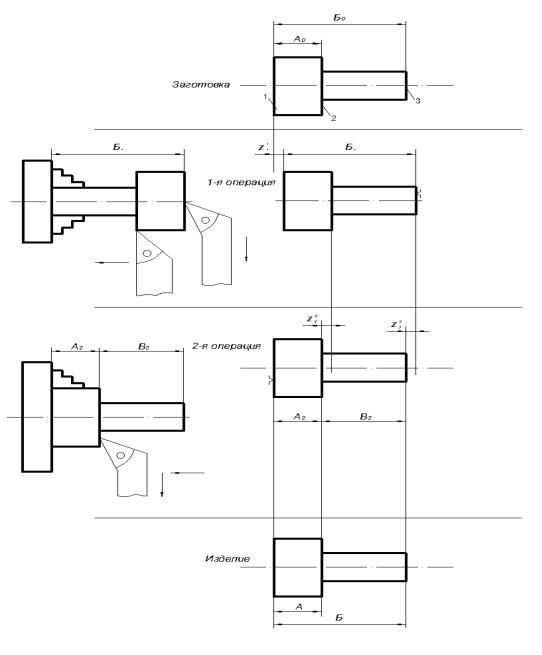
114
На этой схеме наверху вычерчивается заготовка, внизу изделие. Поверхности заготовки нумеруют слева направо цифрами 1, 2, 3 и т.д. и далее к номеру поверхности добавляют нули. Поверхности заготовки 10, 20, 30 обозначают точками, от них проводят вертикали. В зоне с надписью "Заготовка" наносят размеры заготовки A0 и Б0, которые, как и поверхности, имеют нулевые индексы, что указывает на принадлежность к размерам заготовки.
Рис. 4.12. Схема преобразования размеров заготовки в процессе изготовления детали
115
Число размеров должно быть на один меньше, чем число вертикальных линий. На данной схеме три поверхности и два размера между ними. Ниже зоны с размерами заготовки следуют зоны операций, на которых происходит изменение продольных размеров заготовки. В данном примере операций две.На первой операции обрабатывают поверхность 10 заготовки, в результате чего поверхность 10 исчезает, а на ее месте появляется справа новая поверхность 11. Исчезновение поверхности 10 показывают крестиком, а появление новой поверхности 11 справа показывают жирной точкой. Разрыв вертикальной линии в данном случае показывает припуск, который обозначен Z11 – припуск с первой поверхности на первой операции ставят рядом. Далее проставляют размер от вновь полученной поверхности 11 до технологической базы, которой является на первой операции торец 30 заготовки. Поэтому ставится между поверхностями 11 и 30 размер Б1 .
Аналогично на второй операции снимают припуски Z22 и Z32 с поверхностей 20 и 30 заготовки. При этом образуются соответственно новые поверхности 21 и 31 слева от соответствующих поверхностей заготовки, поэтому крестики ставят на линиях справа, а точки — на новых поверхностях на линиях слева. На второй операции образуются размеры А2 до базы и В2 между поверхностями, обработанными за один установ. На этом получение продольных размеров заготовки заканчивается, поэтому ниже последней второй операции идет поле с надписью "изделие", где на продолжениях вертикалей ставятся размеры изделия в соответствии с чертежом.
После построения схемы продольных размеров составляют уравнения технологических размерных цепей для каждого замыкающего звена. Замыкающими звеньями являются, как правило, припуски и те размеры детали, которые не получаются непосредственно ни на одной из операций технологического процесса.

116
Рис,4.13. Схема размерного анализа технологического процесса изготовления валика.
Чтобы выявить замыкающие звенья, которые являются размерами детали, если такие есть, необходимо последовательно проверить получение каждого размера детали. В данном случае, размер А совпадает с размером А2, полученным на второй операции. Поэтому размер А не является замыкающим звеном, этот размер непосредственно получается на второй операции. Проверяем следующий размер Б. Размер Б непосредственно не получается ни на первой, ни на второй операции. Считать, что размер Б1\ является размером Б, нельзя, так как между ними есть разрыв линии — припуск Z32 . Поэтому размер Б является замыкающим звеном и
117
определяется из уравнения
Б = А2 + В2.
Теперь составим уравнения для каждого из припусков. В нашем примере таких припусков три, следовательно, и уравнений три. При составлении уравнений пользуются следующим правилом: двигаясь от одной линии, ограничивающей замыкающее звено по горизонтальным размерам схемы и вертикалям стремятся придти к другой линии, ограничивающей то же самое замыкающее звено. Все размеры через которые проходят при этом движении включаются в размерную цепь. При выявлении контура размерной цепи, проходить через разрывы вертикальных линий нельзя. Нельзя также двигаться по размерам детали.
Пользуясь этим правилом получим следующие уравнения для припусков:
Z11=Б0-Б1 Z22=Б0-Б1-А0+А2 Z32=Б1-А2-Б2
Таким образом, для приведенного примера получили все четыре уравнения размерных цепей по количеству замыкающих звеньев.
Следующим этапом является решение уравнений. Для этого, прежде всего, следует разобраться, что нам известно о всех размерах, вошедших в уравнения. Для этого все размеры удобно разделить на четыре группы и рассмотреть их по порядку.
1)Размеры детали. В нашем примере размеры А и Б. Эти размеры полностью известны из чертежа детали, где указаны номинальные значения размеров и допустимые предельные отклонения.
2)Размеры заготовки. В нашем примере размеры А0 и БоНа эти размеры в начале расчеты известны лишь допуски, т.к. метод получения заготовки выбран. Номинальные значения размеров должны быть установлены в ходе расчетов.
118
3)Размеры, получаемые на операции. В данном случае это размеры А2, Б1,
Б2- Размер А2 = А известен полностью из чертежа детали. О размерах Б1 и Б2 известно только их поле рассеяния, которое может быть получено при проведении операции на данном станке. Эти данные для конкретного производства могут быть установлены экспериментально, могут быть рассчитаны при рассмотрении операционных размерных цепей или приближенно могут быть взяты из справочных таблиц. Итак, в начале расчета известны допуски указанных размеров. Номинальные значения и отклонения получают в результате расчета.
4)Припуски на обработку. В нашем примере Z11, Z22, Z32. Для припусков к началу расчета размерных цепей известны лишь их номинальные величины (Z11min, Z22min, Z3 2min), которые рассчитываются по формуле
Zimin=Riz+Дi
где:Riz- высота шероховатости заготовки; Дi- глубина дефектного слоя заготовки.
Значения шероховатости заготовки после каждого вида обработки могут быть взяты из справочных таблиц. Максимальные значения припусков рассчитываются в результате решения уравнений размерных цепей.
Аналогичным образом строятся размерные схемы по другим направлениям образования размеров (в данном примере нужна еще схема диаметральных размеров), а также схема отклонений положений поверхностей (параллельности, перпендикулярности).
В результате расчета размерных цепей определяют припуски, межпереходные размеры и размеры заготовки. Целью расчета является проверка возможности получения требуемых размеров детали в результате выбранного технологического процесса. В результате расчета устанавливаются запасы на допуски, или выявляется невозможность обеспечения того или иного размера детали. В последнем случае
119
проектируемый технологический процесс нуждается в изменении. Такими изменениями могут быть: введение дополнительных проходов, введение дополнительных операций, изменение технологических баз на операциях, выбор другого метода получения заготовки и ряд других мероприятий.
В результате расчета межоперационных размерных цепей могут быть два случая;
1.Все размеры детали обеспечиваются и ряд операционных размеров имеют запасы до допускам. В этом случае, в зависимости от типа операционного размера и величины запаса по допуску, можно расширить допуски на некоторые наиболее критичные составляющие звенья. Например, можно увеличить допуск на настройку некоторых инструментов вне станка.
2.Некоторые размеры в детали не обеспечиваются в заданных допусках. В этом случае необходимо внести изменения в проектируемый технологический процесс, и следовательно, в его размерные связи. Такими изменениями могут быть:
I) повышение точности операционных размеров за счет: повышения точности составляющих звеньев соответствующих операционных размерных цепей, например, повышение точности подстройки инструментов вне станка, увеличением частоты очистки базовых поверхностей и т.д.; компенсации погрешностей настройки, установки и размерного износа режущих инструментов, например использование контактных головок или повышением частоты измерений; применения адаптивного управления для сокращения погрешности размера динамической настройки или его компенсации при получении операционного размера.
2)изменение типа операционного, размера, например, замена чистового точения отверстия развертыванием или использование активного контроля размеров.
3)введение дополнительного прохода или дополнительной операции.
4)изменение схемы базирования заготовки.
120
5)повышение точности размеров заготовки.
Таким образом, размерный анализ позволяет обосновать требования к средствам автоматизации, позволяющих обеспечить требуемые размеры детали с требуемой достоверностью.
ЛИТЕРАТУРА 1.Ковальчук Е.Р. , Митрофанов В.Г. ,Султан-заде Н.М. и др. Основы
автоматизации машиностроительного производств. Учебник. М.; «Высшая школа», 2001г. , 312 с.
2. Султан-заде Н.М, Клепиков В.В., Солдатов В.Ф.“Основы автоматизации производственных процессов». Конспект лекций для студентов машиностроительного направления ( компьютерный вариант). Москва ,МГИУ, 2012 г.
Дополнительная литература 1.Дашенко А.И., Белоусов А.П. Проектирование автоматических линий. М.: Высшая школа, 1983. 327 с.
2.Гибкие производственные системы сборки / П.Н. Алексеев, А.Г. Герасимов, Э.П. Давыденко и др. М.: Машиностроение, 1989. 348 с