
Подлесных В. И.ТО
.pdfСпециализация участков. При технологической форме участки специализируются на выполнении однородных технологических операций. Например, в механообрабатывающем цехе могут функционировать участки, созданные на базе однородного оборудования: токарный, фрезерный, шлифовальный и т. п. Такая форма специализации участков усложняет внутрицеховое кооперирование, ограничивает ответственность руководителей участков за выполнение плана по общему объему работ и функциональному набору деталеопераций. Она не соответствует требованиям современного развития техники, технологии и организации серийного производства и оправдана лишь в экспериментально-опытныхцехах.
При предметной форме участки специализируются на изготовлении отдельных или нескольких групп конструктивно-однотипных сборочных единиц одного или разных изделий. На таких участках в максимально возможной степени обеспечивается технологически замкнутый цикл производства. Предметные (агрегатные) участки строятся как механосборочные, на которых концентрируются механообработка деталей и сборка из них отдельных узлов, блоков или изделий (например, участок фотозатворов ит.д.).Предметнаяформахарактернадлямассовогоикрупносерийногопроизводства.
На подетально-специализированных участках сосредотачивается обработка одной или нескольких групп конструктивно и технологически однородных деталей по номенклатуре изделий цеха или предприятия. Эти участки строятся по максимально замкнутому технологическому циклу работ данной стадии (рис. 5.1). Помимо крупно- и среднесерийного производства данная форма специализации участков в настоящее время получает широкое распространение в условиях механообрабатывающих цехов с мелкосерийным и единичным типами производства. Прогрессивность подетальной формы объясняется ее полным соответствием таким принципам современной теории орга- низации, как единство целей пространственной и временной организации и приобретение системой качественно новых свойств. В условиях подетальной организации участков коллективы несут ответственность за выдачу законченных частей (деталей) целого (изделия), устанавливаются прямая и обратная связи по видимым конечным результатам работы, жесткая связь между элементами производственного процесса;
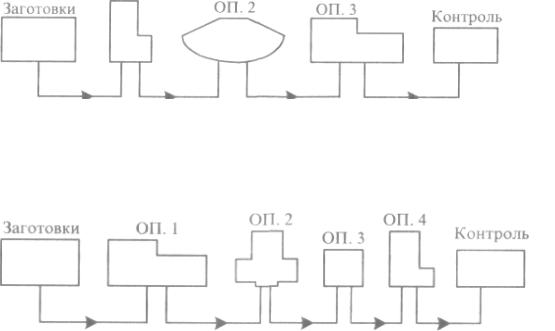
появляется возможность саморегулирования и самоорганизации по большинству возникающих возмущающих отклонений. Специальными исследованиями технологической, предметной и подетальной форм организации участков установлено, что по структурным свойствам они ранжируются в относительных баллах как 1: 3,8 : 4,2
[61].
Технико-организационные преимущества предметной и подетальной форм состоят
вследующем:
•повышается уровень специализации рабочих мест за счет сокращения номенклатурыдеталей (в3-5 раз);
Деталь
1
Рис. 5.1.
Схема движения деталей и размещения оборудования на подетально-специализированных участках
Деталь 2
•резко сокращается межучастковая кооперация (в 10-30 раз);
• повышается прямоточность, и сокращаются пути движения де талей (в 5-10 раз
• уменьшаются потери времени на переналадку оборудования (в 1,5- 2 раза) и на межоперационные перерывы в производстве (на 30-40%);
•улучшается качество планирования производства;
• расширяется сфера внедрения групповых и поточных методов производства;
•обеспечивается возможность решения задач комплексной автоматизации производства.
Не менее важны и их социальные преимущества:
• |
повышается |
ответственность |
коллективов |
участков |
за |
полное |
|
|
изготовление определенной номенклатурной части производственной |
||||||
|
программы цеха; |
|
|
|
|
|
|
• |
открываются |
возможности |
для |
широкого |
внедрения |
|
бригадной |
формы организации и оплаты труда.
По указанным технико-экономическим показателям и социальным факторам участки с технологической, предметной и подетальной структурой ранжируются как
1 : 2,5 : 3,2.
Рассмотренные структурные, технико-организационные и социальные преимущества способствуют и существенному улучшению экономических показателей производства при предметной и подетальной формах организации участков в сравнении с технологическими. Производительность труда повышается на 20-40%. Трудоемкость обработки снижается на 15-30%, себестоимость — на 8-10%, длительность производственного цикла сокращается на 60-70%, объем незавершенного производства—на 50-60%. Относительная оценка сравниваемых форм организации производственных участков по значениям экономических показателей выражается соотношением 1 :1,5 :1,9.
Интегральная оценка структурных, технико-организационных, социальных и экономических характеристик производства при технологической, предметной и подетальнойформахорганизацииможетбытьпредставлена отношением 1:4:7.
Проведенные выше интегральные оценки являются убедительным аргументом современной науки и передовой практики в пользу предметной и подетальной форм специализации, внедрение которых должно стать важным направлением совершенствования производственной структуры механообрабатывающих цехов при реконструкции действующих, а также при проектировании новых предприятий.
Групповое производство. Работы по совершенствованию производственных структур предприятий и цехов должны строиться на органическом воссоединении прогрессивных организационных и технологических форм построения производственных процессов. Реализуется данное направление созданием систем группового производства.
Групповое производство основывается на целевой (подетальной, предметной) специализации подразделений (цехов, участков, поточных линий) и
унифицированной групповой форме организации технологических процессов,
предусматривающей совместное полное или частичное изготовление или ремонт групп изделий различной конфигурации на специализированных рабочих местах.
Цель организации группового производства — локализация дискретности процессов на рабочих местах серийного, мелкосерийного и единичного типов производства за счет применения методов и средств, свойственных крупносерийному и массовому производствам.
Критерии достижения цели—повышение основных технико-экономических показателей производственной деятельности цехов и предприятий.
В зависимости от полноты реализации принципов групповой организации производственных процессов на практике встречаются следующие основные формы группового производства:
•при подетальной специализации и единичной или типовой структуре технологических процессов — подетальные цехи и участки и мно- гономенклатурные групповые потоки с переналадкой станков;
•при подетальной специализации и групповой структуре технологических процессов — подетально-групповые цехи и участки и многономенклатурные групповые потоки с элементарной подналадкой станков.
Создание систем группового производства способствует повышению уровня специализации рабочих мест. Происходит это за счет следующих факторов:
•резкого возрастания конструктивно-технологической однородности изделий,
|
закрепляемых за цехами, участками и линиями; |
|
|
|
|
|||
• |
применения |
группового |
оснащения, |
обеспечивавшего |
|
без |
его |
|
|
полной переналадки непрерывную занятость рабочего места в течение |
|||||||
|
экономически целесообразного периода и, следовательно, более высокую |
|||||||
|
стабильность производственных условий; |
|
|
|
|
|||
• |
общего |
упорядочения |
пространственно-маршрутного |
и |
сложной |
совокупности сроков календарного движения изделий и их частей.
5.1.3. Макропроектирование ПС
Как было указано, при проектировании систем группового производства необходимо обеспечивать органическую увязку прогрессивных принципов организации с внедрением передовых методов технологии. Решению этой задачи в наиболее полной мере отвечает метод групповой обработки, который обеспечивает применение передовой технологии, внедрение высокопроизводительной быстропереналаживаемой технологической оснастки, создание предпосылок для модернизации и автоматизации оборудования, внедрения станков с ЧПУ и обрабатывающих центров.
Планирование организации или технико-экономическое проектирование систем группового производства призвано рационально использовать комплекс задач
пространственного построения группового производственного процесса. В задачи этого комплекса входят:
•создание цехов и участков подетальной и подетально-групповой специализации;
•организация многономенклатурных групповых поточных линий;
формирование группового оснащения для отдельных рабочих мест. Системное описание производственных подразделений позволяет
выделить две стадии в их проектировании:
•макропроектирование, то есть функционально-структурное строение системы;
•инженерное проектирование отдельных компонентов системы. Макропроектирование подетальных участков (цехов) при реконструкции
действующих или проектировании новых цехов (предприятий) должно осуществляться в четыре этапа.
1-й этап. Анализ конструктивно-технологической общности состава продукции
выполняют с помощью классификации деталей по всей номенклатуре. Цель классификации — получение неделимых наборов однородных по конструкции и технологическим процессам обработки деталей.
Применительно к задачам макропроектирования систем группового производства классификация деталей должна осуществляться по основным конструктивно- технологическим признакам, определяющим в конечном итоге пооперационный маршрут обработки и конструктивный тип деталей. Состав этих признаков, их внутренняя градация устанавливаются с учетом конструктивно-технологических особенностей изготовляемых данным предприятием (цехом) изделий.
К числу таких основных признаков относят: вид заготовки (Р'{), габариты деталей (Р2), основной пооперационный технологический маршрут (Р3) и конструктивный тип деталей (Р4).
Первый признак предопределяет общий характер обработки и выбор вида оборудования. В результате классификации по этому признаку всю совокупность
деталей разбивают на классы, например, классы деталей, изготавливаемых из поковок, литья, катаного круглого или полосового материала.
Второй признак обуславливает габаритные размеры и мощность потребного для обработки оборудования.
Третий признак учитывает пооперационный технологический процесс обработки деталей. По этому признаку детали распределяются по рабочим местам, оснащенным технологическим оборудованием, в соответствии с технологическим процессом.
Четвертый признак устанавливает в конечном счете состав групп деталей.
Кроме того, конструктивный тип деталей определяет и выбор видов и моделей технологического оборудования.
Результатами первого этапа являются:
•во-первых, разбивка всей номенклатуры деталей на минимально
необходимое число конструктивно однородных групп;
• во-вторых, возможность правильного отбора и закрепления де талей за участками и формирование профиля их специализации.
2-й этап. Анализ определяющих планово-организационных характеристик деталей. К
числу основных планово-организационных показателей следует отнести трудоемкость производства детали (t) и объем выпуска N.
От этих факторов в значительной степени зависит стабильность производственных условий на рабочих местах и характер движения деталей в производстве, то есть временная структура производственной системы.
Для группирования деталей по трудоемкости их изготовления и объемам их выпуска, отражающим степень стабильности производственных условий на рабочих местах, используется показатель относительной трудоемкости деталей Kg.. Он определяет расчетное суммарное количество единиц обезличенного оборудования, необходимого для обработки i-u детали при заданных объемах выпуска, технологии и режиме сменностиработы. Процедура расчета представлена в табл. 5.1.
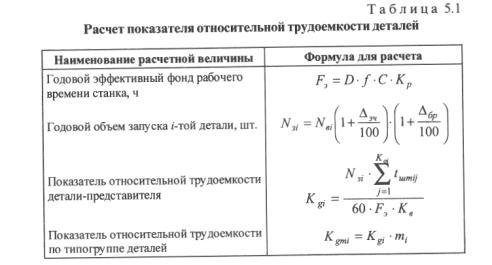
3-й этап. Расчет меры близости между двумя группами деталей. Одним из условий высокоэффективной работы предприятия является проектирование его цехов и участков по принципу предметной, а еще лучше — по подетальной форме их специализации. Выполнение этого условия достигается методом дальнейшей детализации и анализа сформированных на втором этапе однородных по конструктивно-технологическим и организационно-плановым признакам групп деталей. Решение этой задачи строится на положении теории распознавания образов с помощью потенциальной функции, которая устанавливает меру близости между группами деталей.
Таблица 5.1 Расчет показателя относительной трудоемкости деталей
Условные обозначения к табл. 5.1: D — количество рабочих дней в году (D - 261);/— продолжительность смены, ч (f= 8,2 ч); С — число смен в сутки; К __ средний коэффициент сокращения фонда времени на плановый капитальный ремонт (0,95< Кр <0,98); Na_годовой объем планового выпуска /-Й детали, шт. (см. информационную карту); DK — процент деталей, идущих на запасные части; Д6р — процент потерь

производства от брака; /шт. — штучное время обработки г'-й детали по у'-й операции в нормо-мин; К — число операций по основному технологическому процессу /-и детали; Кв — средний коэффициент выполнения норм времени (1,0< Кв < 1,2); т.— количество деталей (номенклатурных позиций), входящих в данную ти-погруппу.
Значение коэффициента пропорциональности Я выбирается для всей совокупности деталей группы, исходя из следующего алгоритма:
0,1,еслиR^ = 1+9
Л.=0,01,еслиR2 = 1+99 0,001, если R2 = 1+999и т.д.
В свою очередь R2(xix.) есть квадрат меры расстояния между базовой деталью- представителем (х.) и всеми другими деталями (х.), которая рассчитывается по значениям кодов, в следующей зависимости
где (хп—х1}); (x2.—x2j); (x4.—x4j); (х5.—х5.) — разность кодов между базовой деталью- представителем х.и деталями-представителями х.по признакам Р{;Р2;Ру Р-,Р5.
Мера расстояния (Rxix) между деталями, входящими в сформированные на первом этапе группы, осуществляется через систему кодирования параметров или особенностей каждогопринятогопризнака.
Код признака — численное значение, присваиваемое каждому параметру, выбранному дляхарактеристики выделенных признаков.
Например, по признаку габаритные размеры (Р2) могут быть выделены в отдельные группы деталей с границами предельных размеров. Размеры010-^-50мм— 1-ягруппа,0 >50-ь100мм—2-ягруппаит.д.Иливидзаготовки(Pt) — 1 -ягруппа— изпруткаипроката,— 2-ягруппа— листовойматериал.
При кодировании необходимо выполнять следующие правила:
•код для различных деталей, входящих в одну группу, должен быть одним числомврамкаходногопризнака;
•величина кодов для разных групп в составе одного признака должна отличаться друготдруганеменее чемна15%;
•величина кодов в составе разных признаков может иметь одинаковоезначение. При расчете меры расстояниявкаждой группе деталей выбираетсядеталь-представитель,
скоторой и сравниваются все детали, входящие в этугруппу.
Как правило, в качестве детали-представителя берется самая трудоемкая деталь группы с наибольшим количеством технологических операцийпроизводственногопроцесса.
Все действия и результаты расчетов заносятся в табл. 5.2.
В качестве примера рассмотрим фрагмент кодирования и расчета меры близости междудеталямисформированнойгруппы.
По результатам анализа конструктивно-технологической общности деталей сформированы однотипные группы—валы, шестерни, корпуса и т. д.
Пусть в группе валов имеется наиболее трудоемкая деталь А (деталь-представитель) соследующимипараметрамипопризнакам:
•вид заготовки (Р}) — стальной прокат;
•габаритные размеры (/*,) — 085 мм;
• пооперационный |
технологический |
маршрут |
(Р3)—токарная |
(Т) |
— фрезерная (Фр) |
— сверлильная (Св) |
— закалка |
(3) — шлифовальная |
(Шл) — слесарная (Сл);
•конструктивный тип (Р^—ступенчатый вал.
Вэту группу входит деталь Б с параметрами: Р{, — поковка; Р2— 0 45 мм; Р} — токарная — фрезерная—сверлильная — шлифовальная; /*4— простойвал.
Затем проводятся расчеты меры близости детали-представителя (А) со всеми деталями, входящими в эту группу.
Результаты расчетов служат базой для проведения следующего этапа работ по закреплению деталей за цехами и участками.