
- •4.5.3. Температурные компенсаторы
- •5.1. СПОСОБЫ НАГРЕВАНИЯ И ОХЛАЖДЕНИЯ ГОРЮЧИХ ВЕЩЕСТВ И МАТЕРИАЛОВ
- •5.2. СУЩНОСТЬ ПРОЦЕССОВ НАГРЕВАНИЯ И ОХЛАЖДЕНИЯ
- •5.2.1. Тепловой баланс теплообменного аппарата
- •5.2.2. Передача тепла в теплообменном аппарате
- •5.2.3. Температурный напор
- •5.3. ХАРАКТЕРИСТИКА ТЕПЛО- И ХЛАДОНОСИТЕЛЕЙ
- •5.7. ОБОРУДОВАНИЕ ДЛЯ НАГРЕВАНИЯ ГОРЮЧИХ ВЕЩЕСТВ ПЛАМЕНЕМ И ТОПОЧНЫМИ ГАЗАМИ
- •5.8. НАГРЕВАНИЕ ГОРЮЧИХ ВЕЩЕСТВ ЭЛЕКТРОЭНЕРГИЕЙ
- •6.1. ОБЩИЕ СВЕДЕНИЯ О ДИФФУЗИОННЫХ ПРОЦЕССАХ
- •6.1.1. Виды массообменных процессов
- •6.1.2. Способы выражения состава фаз двухкомпонентных систем
- •6.1.3. Материальный баланс процессов массообмена
- •6.1.4. Уравнение массопередачи
- •6.2. АППАРАТЫ ДЛЯ ПРОВЕДЕНИЯ СОРБЦИОННЫХ ПРОЦЕССОВ
- •6.2.1. Виды сорбционных процессов
- •6.2.2. Аппараты для проведения процессов адсорбции
- •Сущность процесса адсорбции
- •Адсорбенты и их характеристика
- •Понятие об изотерме адсорбции, динамической и статической активности адсорбента
- •Влияние технологических параметров на протекание процессов адсорбции и десорбции
- •Основные типы адсорберов
- •6.2.3. Аппараты для проведения процессов абсорбции
- •6.3.1. Сущность процессов перегонки и ректификации
- •6.3.2. Простая перегонка растворов
- •6.3.3. Перегонка с дефлегмацией пара
- •6.3.4. Простая ректификация
- •6.3.5. Основные типы ректификационных колонн
- •6.3.6. Тарелки ректификационных колонн
- •6.4. АППАРАТЫ ДЛЯ ПОВЕДЕНИЯ ПРОЦЕССОВ СУШКИ
- •6.4.1. Виды влаги в материале и способы ее удаления
- •6.4.2. Понятие о влажности материала и влагосодержании
- •6.4.3. Тепловая сушка горючих веществ и материалов
- •6.4.4. Кинетика процесса сушки
- •6.4.5. Основные типы сушилок
- •Глава 7. АППАРАТЫ ДЛЯ ПРОВЕДЕНИЯ ХИМИЧЕСКИХ ПРОЦЕССОВ ПОЖАРОВЗРЫВООПАСНЫХ ПРОИЗВОДСТВ
- •7.1. КЛАССИФИКАЦИЯ ХИМИЧЕСКИХ РЕАКТОРОВ
- •7.2. ТЕХНОЛОГИЧЕСКИЕ ПЕЧИ ДЛЯ ПРОВЕДЕНИЯ ВЫСОКОТЕМПЕРАТУРНЫХ ХИМИЧЕСКИХ ПРОЦЕССОВ
- •7.3. ОСНОВНЫЕ ТИПЫ ХИМИЧЕСКИХ РЕАКТОРОВ
- •7.3.2. Реакторы для проведения процессов в гомогенной жидкой среде
- •7.3.4. Реакторы для проведения процессов в системе газ–жидкость
- •7.3.7. Реакторы для проведения процессов в системе газ–жидкость–твердый катализатор
- •Глава 8. МЕТОДЫ ИЗУЧЕНИЯ ТЕХНОЛОГИИ ПОЖАРОВЗРЫВООПАСНЫХ ПРОИЗВОДСТВ
- •8.1. ИСТОЧНИКИ ИНФОРМАЦИИ О ПРОИЗВОДСТВЕННОМ ПРОЦЕССЕ
- •8.1.1. Технологическая часть проекта
- •8.1.2. Технологический (производственный) регламент
- •8.2. РАЗРАБОТКА ПРИНЦИПИАЛЬНОЙ СХЕМЫ ТЕХНОЛОГИЧЕСКОГО ПРОЦЕССА
- •8.3. РАЗМЕЩЕНИЕ ТЕХНОЛОГИЧЕСКОГО ОБОРУДОВАНИЯ
- •8.4. ИЗУЧЕНИЕ ТЕХНОЛОГИИ СЛОЖНОГО ПРОИЗВОДСТВА ПО ТИПОВЫМ ТЕХНОЛОГИЧЕСКИМ ПРОЦЕССАМ
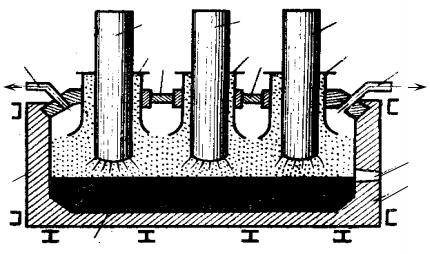
4FeS + 11O2 → 2Fe2O3 +8SO2 + Q .
Концентрация сернистого ангидрида (SО2) в газе доходит до 14 %, а отсутствие в нем пыли упрощает последующую схему переработки газов обжига на серную кислоту.
В электродуговых печах нагрев материала осуществляется за счет тепла дуги, которая образуется между электродом и нагреваемым материалом (прямой нагрев) или между двумя электродами (косвенный нагрев).
На рис. 7.4 представлена схема э л е к т р о д у г о в о й п е ч и прямого нагрева для производства карбида кальция. Печь состоит из стального корпуса 1 и свода 5, выложенных огнеупорным кирпичом 7. В своде печи имеются
патрубки |
4, |
через |
|
3 |
3 |
3 |
|
|
которые |
|
проходят |
|
4 5 |
4 5 |
4 |
|
|
угольные электроды |
2 |
2 |
||||||
3 меньшего диамет- |
|
|
|
|
|
|||
ра. Под печи выло- |
|
|
|
|
|
|||
жен |
угольными |
|
|
|
|
|
||
блоками |
8 |
и имеет |
|
|
|
|
6 |
|
уклон |
в |
сторону |
1 |
|
|
|
||
|
|
|
7 |
|||||
летки 6. Из негаше- |
|
|
|
|
||||
ной извести и кокса |
|
|
|
|
|
|||
готовится |
|
шихта, |
|
8 |
|
|
|
|
которая непрерывно |
|
|
|
|
||||
|
Рис. 7.4. Схема электродуговой печи прямого нагрева: |
|
||||||
загружается |
в печь |
|
|
|||||
через кольцевые от- |
1–стальной корпус; 2–газоотводящие патрубки; 3–электро- |
|||||||
верстия |
|
|
между |
ды; 4–отверстия для подачи шихты; 5–свод печи; 6–летка; |
||||
|
|
|
7–футеровка; 8–угольные блоки |
|
|
|||
электродами |
и |
|
|
|
||||
|
|
|
|
|
внутренними стенками патрубков. Реакционные газы отводятся через патрубки 2. Расплав карбида кальция периодически отводится через летку 6.
Карбид кальция образуется при взаимодействии извести с коксом при 1800–2000 оС по уравнению
СаО + 3С →← СаС2 + СО + 475 кДж .
7.3. ОСНОВНЫЕ ТИПЫ ХИМИЧЕСКИХ РЕАКТОРОВ
Во многих современных производствах преимущественно используются реакторы непрерывного действия (проточного типа), а периодически действующие реакторы находят ограниченное применение в малотоннаж-
255
ных, опытных и вспомогательных производствах. Для большинства химических технологических процессов проектируются нестандартные реакторы, зачастую изготавливаемые в единственном экземпляре. На производственных установках применяются не только одиночные, самостоятельно работающие реакторы, но и их комбинации. Реакторы могут соединятся параллельно и последовательно. В первом случае достигается только количественный эффект увеличения производительности. Во втором случае достигается качественный эффект, связанный с обеспечением большей степени превращения сырья и высокой селективности, а также с повышением устойчивости и безопасности технологического режима при проведении экзотермических процессов.
При рассмотрении различных типов химических реакторов в первую очередь необходимо учитывать фазовый состав веществ, находящихся в реакционной зоне, включая реагенты, катализаторы и растворители (твердые теплоносители и инертные насадки не учитываются). Рассмотрим некоторые типы реакторов, предназначенных для проведения реакций в гомогенных средах (только газовая или только жидкая фаза) и в гетерогенных средах: газ–твердый катализатор; жидкость–твердый катализатор; жидкость–жидкость (не смешивающаяся с первой); газ–жидкость–твердый катализатор.
7.3.1.Реакторы для проведения процессов
вгомогенной газовой среде
Реакторы смешения. Перемешивание газов в таких реакторах осуществляется за счет конвекции в реакционном объеме или путем принудительной циркуляции с помощью встроенных вентиляторов.
На рис. 7.5 в качестве примера показан адиабатический реактор с конвекционным перемешиванием для проведения реакций в гомогенной газовой фазе, используемый в технологическом процессе термического хлорирования метана. При пуске реактора в работу перед подачей сырья реакционная камера разогревается за счет сжигания метана в горелках 7. Смесь реагентов (метан и хлор) поступает в реактор нагретой до требуемой температуры, обеспечивающей их химическое взаимодействие. Процесс протекает без наружного теплообмена. Внутренняя насадка 5, аккумулирующая теплоту, служит для увеличения динамической устойчивости технологического режима.
Указанный тип реакторов, применяемых для проведения газовых реакций при высоких температурах и в агрессивных средах, имеет следующие достоинства: отсутствие теплообмена через стенку; надежное обеспечение тепловой и коррозионной защиты корпуса; высокую динамическую
256
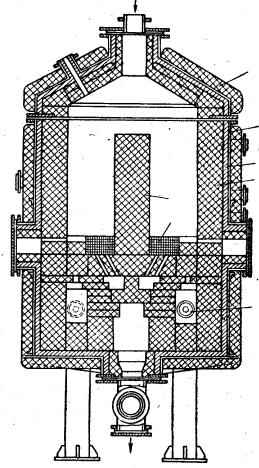
устойчивость |
технологического |
|
|
Реакционная смесь |
||||||||||||
процесса. Недостатки: низкая селек- |
|
|
||||||||||||||
|
|
|
|
|
|
|
|
|
|
|
||||||
тивность (протекание нежелатель- |
|
|
|
|
|
|
|
|
|
|
|
|||||
ных реакций); недостаточно высо- |
|
|
|
|
|
|
|
|
|
|
|
|||||
кая скорость превращения исходно- |
|
|
|
|
|
|
|
|
|
|
|
|||||
|
1 |
|
||||||||||||||
го сырья; ограниченная возмож- |
|
|
||||||||||||||
|
|
|
|
|
|
|
|
|
|
|
||||||
ность регулирования процесса, свя- |
|
|
|
|
|
|
|
|
|
|
|
|||||
занная с постоянством состава ис- |
|
|
|
|
|
|
|
|
|
|
2 |
|||||
|
|
|
|
|
|
|
|
|
|
|||||||
ходной сырьевой смеси; неравно- |
|
|
|
|
|
|
|
|
|
|
3 |
|||||
|
|
|
|
|
|
|
|
|
|
|||||||
мерность |
температурного |
поля |
в |
|
|
|
|
|
|
|
|
|
|
|||
объеме реактора. Последние два не- |
|
5 |
|
|
|
4 |
||||||||||
|
|
|
|
|
||||||||||||
достатка |
ликвидируются |
при |
ис- |
|
|
|
|
|
||||||||
|
6 |
|
|
|
|
|||||||||||
пользовании систем принудитель- |
|
|
|
|
|
|||||||||||
|
|
|
|
|
|
|
|
|
|
|
||||||
ной циркуляции газовой смеси, но |
|
|
|
|
|
|
|
|
|
|
|
|||||
при этом возникают трудности с те- |
|
|
|
|
|
|
|
|
|
|
|
|||||
пловой и коррозионной защитой. |
|
|
7 |
|||||||||||||
Реакторы вытеснения. При- |
|
|||||||||||||||
|
|
|
|
|
|
|
|
|
|
|
||||||
мерами |
таких |
реакторов |
служат |
|
|
|
|
|
|
|
|
|
|
|
||
трубчатые реакторы для пиролиза и |
|
|
|
|
|
|
|
|
|
|
|
|||||
термического крекинга змеевиково- |
|
|
|
|
|
|
|
|
|
|
|
|||||
го типа, аналогичные трубчатым на- |
|
|
|
|
|
|
|
|
|
|
|
|||||
гревательным печам (см. рис. 5.16). |
|
|
|
|
|
|
|
|
|
|
|
|||||
Реактор парофазного пиролиза неф- |
|
|
|
Продукты |
||||||||||||
тепродуктов представляет собой пу- |
|
|
|
|||||||||||||
|
|
|
|
|
|
|
|
|
|
|
||||||
чок длинных труб (длиной 10–12 м) |
Рис. 7.5. Реактор термического хлориро- |
|||||||||||||||
небольшого диаметра (80–120 мм), |
|
|
вания метана: |
|||||||||||||
обогреваемых |
снаружи топочными |
1 и 2–наружная теплоизоляция; 3–сталь- |
||||||||||||||
ной корпус; 4–внутренняя футеровка; |
||||||||||||||||
газами. Современные пиролиз- |
|
|||||||||||||||
|
5–теплоаккумулирующая насадка; 6–ке- |
|||||||||||||||
ные печи имеют в одном корпу- |
|
|||||||||||||||
|
|
рамические кольца; 7–горелки |
се 4–5 топочных камер, в которых заложено до 16 параллельно работающих змеевиков. Трубы змеевика в за-
висимости от места расположения в печи делятся на 4 зоны: предварительного нагрева и испарения сырья, перегрева пара, высокотемпературную конвекционную и радиантную зону. Температура реакционной смеси по
мере ее продвижения по трубам постепенно повышается с 200 оС до 800– 850 оС.
К достоинствам трубчатых реакторов для проведения газофазных реакций относятся: интенсивный регулируемый теплообмен через стенку трубы; оптимальный температурный режим; высокая селективность процесса при отсутствии продольного перемешивания потока. Недостатки: ограниченность температуры процесса жаропрочностью материала труб;
257
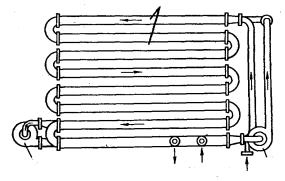
большое гидравлическое сопротивление реактора; образование отложений кокса на внутренней поверхности труб, что приводит к ухудшению теплообмена, увеличению гидравлического сопротивления, т. е. создаются условия для прогара труб.
7.3.2. Реакторы для проведения процессов в гомогенной жидкой среде
Реакторы смешения. К таким реакторам относятся аппараты с механическими перемешивающими устройствами (мешалками), в которых достигается однородность концентрации компонентов и высокие коэффициенты теплоотдачи (см. рис. 2.3). Для обеспечения подвода или отвода тепла из зоны реакции применяются встроенные теплообменники.
Реакторы вытеснения. Наибольшее распространение в промышленности получили трубчатые реакторы, аналогичные по конструкции с теп-
|
1 |
|
|
лообменниками типа |
«труба-в- |
|
|
|
трубе». На рис. 7.6 показана схема |
||
|
|
|
|
||
|
|
|
|
р е а к т о р а т р у б ч а т о г о т и- |
|
|
|
|
|
п а с посекционной циркуляцией |
|
|
|
|
|
реагирующей смеси (альдолиза- |
|
|
|
|
|
тор). Реактор состоит из несколь- |
|
|
|
|
|
ких последовательно соединенных |
|
|
|
|
|
секций 1 с интенсивной много- |
|
2 |
Альдоль- |
Ацеталь- |
2 |
кратной циркуляцией |
жидкости в |
|
|
каждой секции, создаваемой насо- |
|||
|
сырец |
дегид |
|
||
Рис. 7.6. Схема альдолизатора: |
|
сами 2. Такой аппарат работает по- |
|||
|
добно каскаду реакторов идеально- |
||||
1–секции реактора; 2–циркуляционные |
|||||
|
насосы |
|
|
го вытеснения (труба) и смешения |
|
|
|
|
|
(центробежный насос), |
вследствие |
чего его эффективность приближается к эффективности реактора идеального вытеснения.
Для быстро протекающих процессов при большой линейной скорости реагентов используются реакторы кожухотрубного или колонного типов с внутренними теплообменными устройствами.
К достоинствам указанных типов реакторов относятся возможность обеспечения заданной температуры процесса и противоточного режима движения теплоносителя (хладоносителя). Основные недостатки: низкая эффективность теплообмена с теплоносителем (хладоносителем); необходимость устройства каскада реакторов для обеспечения высоких степеней превращения и селективности и, как следствие, высокая удельная металлоемкость; сложность конструкции реакторов.
258
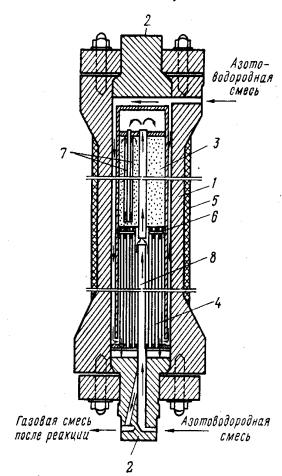
7.3.3.Реакторы для проведения процессов
вгетерогенной системе газ–твердый катализатор
Для этих видов процессов существует большое число разнообразных реакторов, преимущественно относящихся к классу реакторов вытеснения в связи с тем, что как в аппаратах с неподвижным слоем катализатора, так и в аппаратах с псевдоожиженным слоем катализатора практически не удается достигнуть эффекта полного перемешивания веществ.
Реакторы вытеснения. К этой группе аппаратов относятся колонные реакторы со сплошной загрузкой катализатора, трубчатые реакторы, а также адиабатические колонные полочные реакторы.
|
На рис. 7.7 показан |
р е а к т о р |
к о л о н н о г о т и п а для синтеза |
||||||
аммиака под средним |
давлением |
|
|
|
|
|
|||
(до 30 МПа). В корпусе 1 такого |
|
|
|
|
|
||||
|
|
|
|
|
|||||
реактора, изготовленного из высо- |
|
|
|
|
|
||||
колегированной |
хромоникелевой |
|
|
|
|
|
|||
стали с толщиной стенок 175 мм, |
|
|
|
|
|
||||
диаметром 1,0–1,4 м и высотой 13 |
|
|
|
|
|
||||
м, |
расположена |
катализаторная |
|
|
|
|
|
||
коробка 3 и теплообменник 4, |
|
|
|
|
|
||||
обеспечивающий автотермичность |
|
|
|
|
|
||||
процесса. |
|
|
|
|
|
|
|
|
|
|
|
|
|
|
|
|
|
||
|
Трубчатые реакторы исполь- |
|
|
|
|
|
|||
зуются для проведения сильно эк- |
|
|
|
|
|
||||
зотермических процессов (напри- |
|
|
|
|
|
||||
мер, окислительных, гидрогениза- |
|
|
|
|
|
||||
ционных, |
синтеза углеводородов |
|
|
|
|
|
|||
из СО и Н2) или эндотермических |
|
|
|
|
|
||||
процессов (например, дегидриро- |
|
|
|
|
|
||||
вания этилбензола, паровой кон- |
|
|
|
|
|
||||
версии метана). По конструкции |
|
|
|
|
|
||||
такие реакторы напоминают труб- |
|
|
|
|
|
||||
чатые нагревательные печи с вер- |
|
|
|
|
|
||||
тикальным |
расположением труб |
|
|
|
|
|
|||
или |
кожухотрубные теплообмен- |
|
|
|
|
|
|||
ники с трубами, заполненными ка- |
|
|
|
|
|
||||
|
Рис. 7.7. Колонна синтеза аммиака под |
||||||||
тализатором. |
|
|
|
||||||
|
К достоинствам таких реакто- |
|
средним давлением: |
||||||
|
1–корпус; 2–крышка; 3–катализаторная ко- |
||||||||
ров относятся: глубокое превра- |
робка; 4–теплообменник; 5–теплоизоляция; |
||||||||
щение сырья и высокая селектив- |
6–опорная решетка; 7–трубы Фильда; |
||||||||
ность процесса, т.к. режим движе- |
|
8–центральная труба |
259
ния потока близок к полному вытеснению; развитая поверхность теплообмена и высокие значения коэффициентов теплопередачи; эффективная работа катализатора во всех трубах, достигаемая в результате калибровки гидравлического сопротивления каждой трубы; возможность использования в отдельных случаях стандартных теплообменников.
Недостатки трубчатых реакторов, ограничивающие область их применения: невысокая доля общего объема реактора, заполненного катализатором; большой расход металла на трубы; сложность загрузки и выгрузки катализатора из реакционных труб; сложность обеспечения оптимального температурного режима по всей длине труб.
В связи с этим в последнее время нашли широкое применение адиабатические реакторы со сплошным неподвижным и с подвижным слоем катализатора. Адиабатические реакторы со сплошным слоем катализатора используются в процессах протекающих в кинетической и переходной областях (например, гидрокрекинга, риформинга, изомеризации парафинов, прямой гидратации этилена, дегидрирования этилбензола в стирол и других), а также в процессах, протекающих в диффузионной области (например, окисления спиртов в альдегиды и кетоны). Для проведения процессов первого вида используются адиабатические реакторы шахтного типа с достаточно высоким слоем катализатора.
На рис. 7.8 показан а д и а б а т и ч е с к и й ш а х т н ы й р е а к- т о р дегидрирования алкилбензолов со сплошной засыпкой катализатора. Катализатор в виде цилиндров диаметром 10–20 мм или колец Рашига укладывается на слой инертной насадки 4, препятствующей просыпанию его через опорную решетку 2. Важное значение имеет смеситель 9, предназначенный не только для получения однородной реакционной смеси, но и для равномерного распределения газового потока по сечению реактора.
К достоинствам таких реакторов относятся: полнота использования объема реактора, простота конструкции, небольшая металлоемкость.
Недостатки: ограниченная область применения (они применяются только для процессов, в которых адиабатический перепад температур не слишком высок, т. е. когда нет опасности перехода в области слишком высоких или низких температур); невозможность обеспечения оптимального профиля температур по высоте слоя катализатора; трудность равномерного распределения подачи реакционной смеси на слой катализатора.
Процессы с большим адиабатическим изменением температуры реакционной смеси проводят в р е а к т о р а х п о л о ч н о г о (секционированного) т и п а (рис. 7.9). Число секций в таких реакторах (обычно не более 10) и распределение катализатора между ними определяют, исходя из величин адиабатического перепада температур и оптимальной степени превращения в каждом слое. Охлаждение (нагревание) реакционной смеси
260
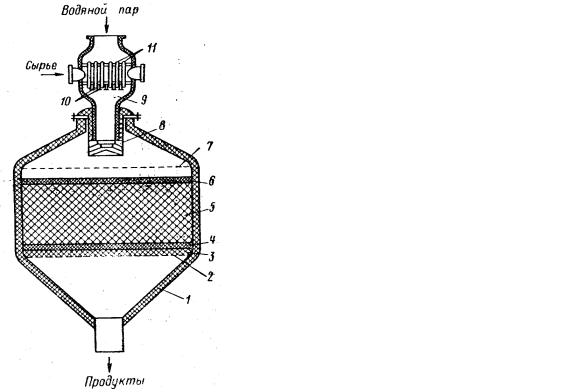
между полками производится, как правило, непосредственным смешением реакционной смеси с холодным (горячим) теплоносителем или впрыскиванием испаряющейся жидкости. В то же время между секциями реактора могут использоваться встроенные 3 или выносные теплообменники.
|
|
|
|
|
|
|
|
|
|
|
|
|
|
|
|
|
|
|
|
|
|
|
|
|
|
|
|
|
|
|
|
|
|
|
|
|
|
|
|
|
|
|
|
|
|
|
|
|
|
|
|
|
|
|
|
|
|
|
|
|
|
|
|
|
|
|
|
|
|
|
|
|
|
|
|
|
|
|
|
|
|
|
|
|
|
|
|
|
|
|
|
|
|
|
|
|
|
|
|
|
|
|
|
|
|
|
|
|
|
|
|
|
|
|
|
|
|
|
|
|
|
|
|
|
|
|
|
|
|
|
|
|
|
|
|
|
|
|
|
|
|
|
|
|
|
|
|
|
|
|
|
|
|
|
|
|
|
|
|
|
|
|
|
|
|
|
|
|
|
|
|
|
|
|
|
Рис. 7.8. Схема адиабатического |
|
- |
Рис. 7.9. Схема адиабатического |
|
|
||||||||||
шахт |
|
|
|||||||||||||
|
ного реактора: |
|
|
полочного реактора: |
|
|
|||||||||
1–корпус; 2, 7–опорные решетки; 3, 4, |
1–опорные решетки (полки); 2–ка- |
|
|
||||||||||||
6–насадка; 5–катализатор; 8–распреде- |
тализатор люки; 3–теплообменник; |
|
|
||||||||||||
лительное устройство; 9–смеситель; |
|
|
4–перегородка |
|
|
||||||||||
|
10–сопла; 11–трубы |
|
|
|
|
|
|
|
|
|
Достоинства секционированных реакторов: возможность поддержания оптимального температурного режима; простота конструкции (без встроенных или выносных теплообменников) и удобство эксплуатации; небольшая металлоемкость. Недостатки: необходимость использования больших количеств катализатора; необходимость последующего отделения продуктов реакции от теплоносителя; громоздкость и сложность конструкции реакторов со встроенными и выносными теплообменниками.
Для проведения процессов, протекающих в диффузионной области, используются адиабатические реакторы с катализаторами в виде сеток.
На рис. 7.10 представлен к о н т а к т н ы й а п п а р а т для окислительного аммонолиза метана. Аналогичные по конструкции аппараты (с устройством в нижней части закалочной камеры) используются для полу-
261
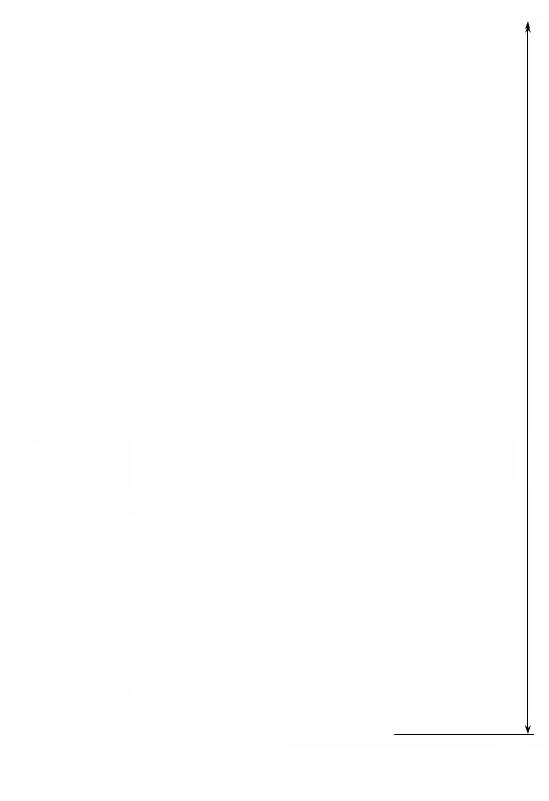
чения формалина из метилового спирта и в других окислительных процессах (например, для окисления аммиака в нитрозные газы в технологическом процессе производства азотной кислоты). Реактор прост по конструкции, но регулирование процесса в нем затрудненно и обеспечивается, в какой-то мере, только изменением состава исходной реакционной смеси.
Рассмотренные выше реакторы с неподвижным слоем катализатора непригодны для проведения процессов, требующих регенерации катализатора. В этом случае более пригодны аппараты с подвижным катализатором: с медленно движущимся
Рис. 7.10. Схема адиабатического реактора вытеснения с катализатором в виде сеток:
1–корпус; 2–катализаторные сетки;
3–теплоизоляция
55200
Рис. 7.11. Схема реактора с псевдоожиженным катализатором:
1–корпус; 2–циклоны; 3–стояки; 4–распре- делительная решетка; 5–форсунка; 6–десор- бер; 7–стояк; 8–штуцер ПК; I–ввод сырья; II и IV–подвод и отвод катализатора; III–отвод продуктов реакции; V–подвод водяного пара
262