
- •Учебник подготовлен в рамках Инновационной образовательной программы
- •ISBN 978-5-7262-0821-3
- •ISBN 978-5-7262-0978-4 (т. 4)
- •15.1. Мольный термодинамический потенциал Гиббса
- •15.2. Система уравнений равновесия двух фаз
- •15.4. Различные трактовки системы уравнений равновесия
- •15.6. Термодинамическая теория фазовых переходов 1-го рода
- •15.7. Феноменологический метод описания фазовых переходов
- •15.8. Методы расчета параметров стабильности чистых
- •15.10. Инвариантность решений системы уравнений фазового
- •15.12.1. Обобщение правила равенства площадей Максвелла
- •15.12.2. Обобщение правила равенства площадей Максвелла
- •15.14. У-алгоритм расчета равновесия двух неизоморфных
- •15.18. Одно/двухфазные α/α+β или β/α+β фазовые границы
- •15.21. Анализ трехфазных равновесий в двухкомпонентных
- •системах. Расчет энтальпии трехфазной реакции T–p–x
- •Глава 11. ФИЗИКА ПРОЧНОСТИ МАТЕРИАЛОВ
- •11.1.1. Основные понятия
- •11.1.2. Напряжения и деформации
- •11.1.3. Диаграмма растяжения: характерные точки
- •11.2. Упругость
- •11.2.1. Закон Гука для случая одноосной деформации
- •11.2.3. Закон Гука в обобщенном виде
- •11.2.4. Модули и коэффициенты упругости
- •11.3. Процессы пластической деформации
- •11.3.1. Кристаллографическое скольжение
- •11.3.2. Фактор Шмида
- •11.3.4. Начало пластической деформации
- •11.3.6. Взаимосвязь величин сдвиговой деформации
- •11.3.7. Стадии деформационного упрочнения
- •11.3.8. Теории дислокационного упрочнения
- •11.3.9. Текстуры деформации и текстурное упрочнение
- •11.3.10. Двойникование как механизм деформации
- •11.3.15. Возникновение зуба текучести
- •11.4. Ползучесть
- •11.4.1. Неупругая обратимая ползучесть
- •11.4.2. Логарифмическая ползучесть
- •11.4.3. Высокотемпературная ползучесть
- •11.4.4. Диффузионная ползучесть
- •11.4.5. Характеристики ползучести
- •11.5. Разрушение
- •11.5.1. Основные виды разрушения
- •11.5.2. Зарождение трещины
- •11.5.7. Схема Иоффе перехода из хрупкого
- •11.5.8. Особенности охрупчивания ОЦК металлов
- •11. 6. Усталость материалов
- •11.6.1. Общие характеристики явления
- •11.6.2. Особенности протекания пластической деформации при циклическом нагружении
- •11.6.4. Влияние различных факторов на усталость
- •Контрольные вопросы
- •Список использованной литературы
- •Введение
- •Контрольные вопросы
- •Глава 13. РАДИАЦИОННАЯ ФИЗИКА ТВЕРДОГО ТЕЛА
- •Введение
- •13.5.2. Низкотемпературное радиационное охрупчивание
- •Влияние облучения на стали. Наиболее важным требованием к конструкционным материалам в процессе длительного облучения является стабильность их физических и механических свойств. Поэтому пригодность той или иной стали для изготовления узлов и деталей активной зоны атомного реактора может быть обоснована только после определения ее свойств в нейтронном поле.
- •На рис. 13.46 показаны начальные участки кривых растяжения нескольких монокристаллических образцов урана близкой ориентировки, облученных различными флюенсами (номера кривых соответствуют номерам на стереографической проекции выхода оси растяжения).
- •13.6.2. Механизмы радиационной ползучести
- •Контрольные вопросы
- •Глава 14. ОСНОВЫ КОМПЬЮТЕРНОГО МОДЕЛИРОВАНИЯ В КОНДЕНСИРОВАННЫХ СРЕДАХ
- •14.1. Задачи компьютерного моделирования
трации здесь напряжений. Дальнейшее развитие получают только те трещины, которые достигают достаточно большой длины и имеют острую вершину. Окончательное разрушение происходит в результате ослабления сечения образца какой-то одной самой острой и глубокой трещиной.
11.6.4. Влияние различных факторов на усталость
Усталостная прочность металлических материалов реагирует на изменение условий испытания или эксплуатации значительно резче, чем многие другие механические свойства. К этим условиям относятся температура и скорость (частота) приложения нагрузки, характер напряженного состояния, свойства окружающей среды, а также характеристики самих объектов испытания – их размеры, форма и состояние поверхности. При прочих равных условиях усталостные свойства, естественно, определяются составом и структурой материала, зависящей от технологии его обработки.
Температура испытания значительно влияет на выносливость металлов. Для большинства металлов при любых температурах может быть получено разрушение, обладающее признаками усталостного. Если изменение температуры не вызывает фазовых или структурных превращений в материале, то выносливость этого материала непрерывно повышается с уменьшением температуры вплоть до абсолютного нуля. Отношение пределов выносливости многих используемых в технике сплавов при температуре жидкого азота (–196 оС) и комнатной (σR-196/σR+20) составляет 1,5–2,5.
С повышением температуры усталостного испытания в пределах низких и средних температур кривая напряжение–число циклов сдвигается в сторону меньших напряжений, но форма ее не изменяется (рис. 11.53).
Монотонная зависимость сопротивления усталости от температуры может нарушаться в результате структурных изменений, вызванных одновременным воздействием циклической деформации и повышенной температуры. Так, углеродистые стали имеют отчетливый максимум предела выносливости при 350оС – при повышении температуры от комнатной до 350оС предел выносливости не
133
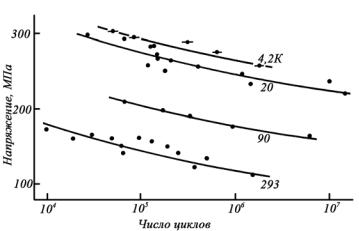
уменьшается, а вырастает на 50% вследствие протекания деформационного старения и сопутствующего упрочнения.
Рис. 11.53. S – N-кривые меди в области температур 4,2 – 293 К
При высоких температурах статическая составляющая цикла вызывает ползучесть материала, что приводит к снижению сопротивления усталости. Начиная с определенной температуры, эффекты ползучести проявляются даже при симметричном цикле. В результате изменяется и форма кривых усталости – исчезает горизонтальный участок, соответствующий пределу выносливости, и разрушающее напряжение непрерывно снижается с увеличением базы испытаний.
Вусловиях высокотемпературной усталости, как и при ползучести, формируется субзеренная структура, характер распространения трещин вместо внутризеренного становится межзеренным. Трещины зарождаются в стыках между зернами в результате межкристаллитных смещений или на пограничных порах, возникающих в местах встречи поверхности границы с полосами скольжения.
Вреальных условиях высокотемпературной службы материалов усталостные процессы и ползучесть протекают параллельно. Большое значение имеет усталость в условиях циклического изменения температуры, например, в материалах камеры сгорания двигателей, поверхности прокатных валков, тормозных элементов колес и т.д.
134
Если температура изменяется при постоянном напряжении, то имеет место так называемая термическая усталость. Способность материала сопротивляться разрушению в условиях проявления термической усталости называют термостойкостью. Разрушение здесь происходит как при циклическом нагружении под действием термических напряжений, так и при ползучести, идущей особенно активно вблизи максимальной температуры цикла. Чаще всего условия термоциклирования отвечают малоцикловому нагружению, при котором сжатию способствует максимальная температура термического цикла, а растяжению – минимальная. Принципиальным отличием термической усталости от механической является то, что при термоциклировании уровень возникающих напряжений определяется упруго-пластическими свойствами материала, а не прикладываемой внешней нагрузкой.
Частота циклического нагружения в реальных условиях экс-
плуатации изделий может изменяться от нескольких циклов в месяц до нескольких тысяч циклов в секунду, т.е. на 10 порядков. Однако большинство деталей машин работает в диапазоне частот от 500 до 10 000 циклов в минуту. В этом диапазоне влияние увеличения частоты нагружения на предел выносливости является довольно слабым – с ростом частоты предел выносливости увеличивается на 5 – 10%. Но с увеличением максимальных напряжений цикла влияние частоты нагружения усиливается.
Влияние частоты связано в основном с действием временного фактора: при равном числе циклов увеличение частоты означает уменьшение времени и повышение скорости нагружения. Это ограничивает развитие процессов пластической деформации и приводит к уменьшению результирующего усталостного повреждения. Однако при изучении влияния частоты могут действовать сопутствующие факторы, существенно влияющие на результаты испытания. Так, при низких частотах усиливается влияние окружающей среды, поскольку значительно возрастает длительность испытания, а при высоких частотах в результате тепловыделения может существенно повышаться температура образца, особенно для материалов с низкой теплопроводностью. Поэтому при очень низких и очень высоких частотах возможны отклонения от общей закономерности, вызываемые косвенными причинами.
135
В том случае, когда повреждения усталостного нагружения складываются с повреждениями от ползучести, говорят о сопротивлении усталости в условиях ползучести (creep fatigue resistance) – это со-
противление совместному действию усталости и ползучести. При наличии трения и износа в условиях циклирования напряжений го-
ворят о сопротивлении фреттинг-усталости (fretting fatigue resistance), т.е. сопротивлении усталости, вызванной или усиленной небольшим колебательным проскальзыванием (трением) по контактной поверхности твердых тел, прижимаемых друг к другу поперечной (нормальной) нагрузкой.
Окружающая среда чрезвычайно сильно влияет на сопротивление усталости большинства материалов. Даже обычная атмосфера воздуха является важным фактором снижения усталостной прочности. Например, долговечность образцов меди при испытании в вакууме 10-5 мм рт. ст. более чем в 10 раз превышает долговечность при атмосферном давлении. Увлажнение воздуха дополнительно уменьшает сопротивление усталости, а переход к жидким средам вызывает снижение предела выносливости на сотни процентов. Усталостные процессы в условиях одновременного воздействия коррозионной среды настолько своеобразны, что повреждение и разрушение материалов в этих условиях характеризуют специальным термином – коррозионная усталость. Сопротивле-
ние коррозионной усталости (corrosion fatigue resistance) – это со-
противление усталости, которая усилена действием коррозии, т.е. в условиях химического или электрохимического взаимодействия материала со средой.
Сопротивление коррозионной усталости металла обычно тесно связано с его сопротивлением коррозии в данной среде, поэтому повысить коррозионно-усталостную прочность удается только теми методами, которые повышают коррозионную стойкость. В условиях одновременного воздействия коррозионной среды особое значение приобретают характеристики циклического нагружения: частота (опасны низкие частоты), асимметрия цикла (опасны растягивающие напряжения, способствующие раскрытию поверхностных трещин).
Размер испытываемых образцов оказывает очень большое влияние на усталостную прочность. Предел выносливости значи-
136
тельно снижается при переходе от образцов диаметром 5 – 10 мм к образцам диаметром 50 – 200 мм. Этот «масштабный эффект» имеет затухающий характер: снижение выносливости продолжается с ростом размеров образца до определенного предела (30–50 мм) и при дальнейшем увеличении размеров прекращается.
Существует несколько вариантов объяснения этого эффекта:
1)при увеличении размеров образца неизбежно возрастает неоднородность состава и структуры, имеющая технологическое происхождение;
2)при испытании крупных образцов может повышаться скорость роста трещины из-за большего запаса упругой энергии;
3)вероятность присутствия опасного дефекта в материале возрастает с увеличением его объема.
Состояние поверхности играет особую роль при циклическом нагружении, так как усталостное разрушение начинается обычно на поверхности детали даже при однородном напряженном состоянии. На практике однородное напряженное состояние реализуется очень редко, почти всегда присутствуют изгибающие моменты и роль состояния поверхности дополнительно возрастает, поскольку напряжения здесь выше, чем в глубинных слоях. Кроме того, взаимодействие материала детали с окружающей средой всегда осуществляется через ее поверхность.
Наличие на поверхности дефектов снижает усталостную прочность на десятки процентов. Это обусловлено концентрацией напряжений около дефектов. К числу дефектов, способствующих зарождению трещин на поверхности, относятся локальная коррозия (например, питтинг), дефекты микроструктуры, границы зерен, остаточные напряжения, участки концентрации напряжений, пластическая деформация и технологические дефекты (например, царапины), вызванные механической доводкой поверхности материала. Известно, что около 90% случаев выхода из стоя деталей машин и инструмента при эксплуатации вызвано повреждением поверхности материалов в результате изнашивания, коррозии и усталости. В этой связи одной из важных задач является устранение дефектов поверхности, способных облегчать зарождение трещин, т.е. устранение резких нарушений сплошности (например, покрытий), царапин, коррозионных ямок и продуктов коррозии, растягивающих остаточных напряжений и других дефектов.
137