
DM_1 / Деталі машин КЛ [Стадник В. А
.].pdf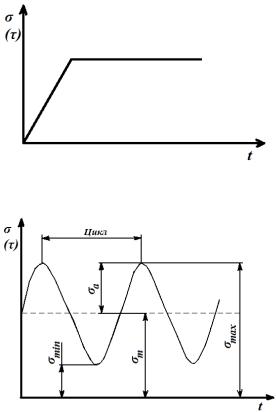
Тема 4. Вплив характеру навантаження елементів машин на вибір допустимих напружень і довговічність деталей
4.1. Характеристики навантажень
Під навантаженням розуміють всі сили і моменти, прикладені до деталі, як діючі, так і сили опору (корисного і шкідливого) в тому числі
опорні реакції. |
|
|
|
|
|
Навантаження, |
що |
сприймається |
деталлю, |
повинно |
бути |
зрівноваженим, тобто |
∑Fi = 0 ; |
∑ Mi = 0 . |
|
|
При незбігу у часі сил діючих і сил опору виникають коливання.
На практиці всі напруження, які виникають від навантаження деталей можна розділити на дві групи, як показано на рис. 4.1.
а)
б)
Рис. 4.1. Характеристики напружень: а) постійні в часі напруження; б) змінні в часі напруження.
50
Під час дії на деталь постійного за модулем та напрямом навантаження в ній виникають постійні в часі напруження. Якщо модуль або напрям навантаження щодо деталі змінюється в часі, то і напруження в деталі будуть змінюватись у часі.
Змінні напруження, що виникають у деталях машин, у більшості випадків змінюються в часі періодично.
Сукупність всіх напружень за один період зміни їх називається
циклом напружень. Цикл напружень характеризується максимальним σ max
і мінімальним напруженнями, а також амплітудою напружень σa та коефіцієнтом асиметрії R , а також середнім напруженням σ m циклу.
Згідно з рис. 4.1,б середнє напруження циклу визначається за формулою
σm |
= σmax +σmin . |
(4.1) |
|
2 |
|
Амплітуда напружень σa циклу за формулою |
|
|
σm |
= σmax −σmin . |
(4.2) |
|
2 |
|
Відношення мінімального напруження циклу до максимального, взяте з відповідним знаком, називається коефіцієнтом асиметрії
R = σmin , |
(4.3) |
σmax
На рис. 4.2 показані різні цикли напружень, які можуть бути на практиці. ∑
51

Рис. 4.2. Можливі цикли напружень.
Практичне застосування в розрахунках деталей машин знаходять:
постійне напруження (σm = σ ; σa = 0 ; R = 1), симетричний (σm = 0 ;
σa = σmax ; R = −1), і пульсуючий (σm = 0 ,5σmax ; σa = 0 ,5σmax ;
R = 0 ) цикли напружень. Усі інші цикли напружень можуть бути зведені до певної сукупності названих трьох циклів.
Відомо, що змінні напруження спричинюють явища втоми матеріалу деталей. Характеристикою міцності матеріалу в цьому випадку виступає границя витривалості σ R (відповідно σ−1 , τ−1 для симетричного і σ0 , τ0
для пульсуючого циклів).
4.2. Визначення граничних напружень
Вихідною характеристикою для визначення граничних напружень σ lim (τ lim ) є одна з нормативних технічних характеристик матеріалу:
а) для постійно діючих у часі напружень – границя плинності (рос.
граница текучести) σ n (τn );
б) для змінних у часі діючих напружень – границя витривалості
σ lR (τ R ) .
52

Нормативні механічні характеристики визначають в лабораторних умовах за стандартними методиками на стандартних зразках. Оскільки реальні деталі відрізняються від зразків розмірами, формою, станом поверхні деталі і поверхневого зміцнення, то всі ці фактори потрібно врахувати у розрахунках за допомогою коефіцієнтів, які приводяться у довідковій літературі. У свою чергу, ці коефіцієнти теж визначаються за допомогою спеціальних лабораторних випробувань реальних деталей.
4.3. Визначення допустимих напружень і коефіцієнтів запасу
міцності
Допустимі напруження [σ ] і [τ ] та розрахункові коефіцієнти запасу міцності визначають за формулами опору матеріалів:
|
[σ ]= [S ]; |
[τ ]= [S ] |
|
(4.4) |
|||||
|
|
|
|
σlim |
|
τlim |
|
|
|
|
|
|
|
σ |
|
|
τ |
|
|
S |
= |
|
σlim |
³ [S ]; |
S |
= |
τlim |
³ [S ], |
(4.5) |
|
|
||||||||
|
|
|
|||||||
σ |
|
|
σ |
σ |
τ |
|
τ |
τ |
|
|
|
|
|
|
|
|
|
||
де σlim і τlim |
- граничні напруження; |
σ |
і τ - розрахункові максимальні |
напруження; [Sσ ] і [Sτ ] - допустимі коефіцієнти запасу міцності деталі за нормальними та дотичними напруженнями.
У загальному випадку при дії нормальних і дотичних напружень в небезпечному перерізі умова міцності на втому записується у вигляді:
S = |
|
|
|
Sσ |
Sτ |
|
|
³ [S ]; |
(4.6) |
||
|
|
|
|
|
|
|
|
||||
|
|
Sσ |
2 + Sτ |
2 |
|||||||
|
|
|
|
|
|
|
|||||
Sσ |
= |
|
|
|
|
|
σ −1 |
; |
|||
|
|
K |
|
|
|
|
|
|
|||
|
|
|
|
σ |
|
σa +ψσ ×σ m |
(4.7) |
||||
|
|
|
β × ε |
σ |
|
||||||
|
|
|
|
|
|
|
|
53
|
Sτ |
= |
|
|
|
|
τ −1 |
. |
|
|
|
|
|
|
|
K |
τ |
|
+ψτ ×τ m |
|
|
|
(4.8) |
||||
|
|
|
|
|
|
|
|
|
|||||
|
|
|
|
|
|
|
|
|
|
|
|||
|
|
|
|
|
|
|
|
|
|
|
|
||
|
|
|
|
β × ετ |
|
|
|
|
|
|
|||
У наведених |
формулах |
|
для |
визначення Sσ |
і Sτ : |
σ −1 |
- |
границя |
|||||
витривалості при |
симетричному |
циклі напружень |
згину; |
τ −1 |
- |
границя |
витривалості при симетричному числі циклі напружень кручення; σ а і τ а -
амплітуда номінальних напружень відповідно при згині і крученні; σ m і τ m
- середні значення напружень відповідно при згині і крученні; Kσ і Kτ -
ефективні коефіцієнти концентрації напружень; β |
- коефіцієнт впливу |
|||||
поверхневого зміцнення; εσ і ετ |
- коефіцієнти впливу абсолютних розмірів |
|||||
деталі (масштабний фактор); ψσ |
і ψτ - коефіцієнти чутливості матеріалів до |
|||||
асиметрії циклу напружень відповідно при згині і крученні: |
||||||
ψσ = |
2σ −1 − σ 0 |
; |
ψτ = |
2τ −1 −τ 0 |
, |
(4.9) |
|
|
|||||
|
σ 0 |
|
τ 0 |
|
де σ0 і τ 0 - границі витривалості при пульсуючих від нуля напруженнях.
На перший погляд студент розгублюється від такої кількості коефіцієнтів. Але в дійсності такі розрахунки не відрізняються особливою складністю, оскільки ці коефіцієнти відомі і зводяться в окремі таблиці, що приводяться у довідковій літературі, яка використовується на практичних заняттях.
Для визначення допустимого коефіцієнта запасу міцності [S ] користуються двома методами – табличним і диференційним.
Табличний метод застосовують для деталей та конструкцій, руйнування яких особливо небезпечні для життя людей (наприклад, для вантажопідйомних машин).
54

Диференціальний метод полягає у визначенні допустимого коефіцієнта запасу міцності як добутку коефіцієнтів запасу міцності, які враховують окремі фактори , що впливають на міцність і довговічність деталі. Тобто
[S ]= S1 × S 2 × S 3 , |
(4.10) |
де S1 – коефіцієнт, що враховує властивості |
матеріалу (неоднорідність |
структури, відхилення механічних характеристик матеріалів від прийнятих
нормативів |
у |
залежності від |
технології виготовлення деталі та ін.), |
S1 =1,2÷2,5; |
S2 |
– коефіцієнт, |
що враховує точність розрахункових схем, |
S2 =1÷1,5; |
S3 – |
коефіцієнт, що враховує специфічні вимоги безпеки (ступінь |
відповідальності деталі), S3 =1÷1,5.
4.4.Урахування довговічності в розрахунках на міцність
Здатність опору матеріалів втомному руйнуванню встановлюється за допомогою спеціальних експериментально одержаних графіків, які називають кривими втоми (або кривими Веллера) і показують залежність числа циклів N ц до руйнування від напруження σ . Крива втоми для однорідних сталей має вигляд, показаний на рис. 4.3, а.
а) |
б) |
Рис. 4.3. Криві втоми матеріалів:
а– в системі координат N ц - σmax ;
б– в системі координат lg N ц - σmax .
55
Крива втоми має дві ділянки: криволінійну, що лежить ліворуч від точки N0 і близьку до горизонтальної – праворуч від цієї точки.
Крива втоми показує,що при зменшенні напруження (наприклад, від σ N ) на криволінійній ділянці число циклів до руйнування безперервно збільшується до N0 , що відповідає переходу кривої втоми в горизонтальну ділянку. Це чіткіше видно на графіку, побудованому в системі координат
(рис. 4.3, б).
Число циклів напружень N0 , що відповідає переходу кривої втоми в горизонтальну ділянку, називається базою випробувань або базовим числом циклів випробувань, а відповідне йому напруження σ R - довгочасною або
необмеженою границею витривалості матеріалу.
Найбільше напруження циклу, яке із заданою ймовірністю неруйнування може витримати матеріал при числі циклів N N < N 0 ,
називається обмеженою границею витривалості, яку будемо позначати σ N (рис. 4.3.).
Для ряду матеріалів і умов навантаження криві втоми не мають горизонтальної ділянки. В таких випадках можна говорити лише про обмежену границю витривалості матеріалів.
Експериментально доведено, що криволінійна ділянка кривої втоми
може бути апроксимована рівнянням |
|
N ц ×σ i m = const , |
(4.11) |
де показник степеня т характеризує нахил кривої і залежить від матеріалу та способу навантаження (згин, кручення, розтяг).
Скориставшись апроксимованим рівнянням кривої Веллера, можна встановити залежність між необмеженою σ R і обмеженою σ N границями витривалості
56

N 0 ×σ R m = N N ×σ N m ,
звідки |
|
|
|
|
|
|
|
|
|
|
|
|
|
|
|
|
|
|
|
|
|
|
|
|
|
|
|
|
|
|
|||
σ N = σ R m |
|
|
N 0 |
|
|
= σ R × K L , |
(4.12) |
|||||||||
|
|
N N |
|
|
||||||||||||
|
|
|
|
|
|
|
|
|
|
|
|
|
||||
де K L – коефіцієнт довговічності, що визначається за формулою |
|
|||||||||||||||
|
|
|
|
|
|
|
|
|
|
|
||||||
|
K L |
= m |
|
N 0 |
. |
|
(4.13) |
|||||||||
|
|
N N |
||||||||||||||
|
|
|
|
|
|
|
|
|
|
|
|
|
||||
Очевидно, що |
|
|
|
|
|
|
|
|
|
|
|
|
|
|
|
|
σ |
N |
m |
|
|
|
N |
0 |
|
|
|||||||
|
|
|
= |
|
|
|
|
|||||||||
|
σ R |
|
|
|
|
|
|
|
|
|
. |
|
||||
|
|
|
|
|
|
|
|
N N |
|
Розв'язавши це рівняння відносно показника степеня, знаходимо, що m = ctgα , де α – кут нахилу лівої ділянки прямої графіка (рис. 4.3. б) в
координатах lg N ц − σ max .
Дійсно:
m(lg σ N − lg σ R ) = lg N 0 − lg N ,
звідки
m = |
lg N 0 − lg N n |
= |
ac |
= ctgα . |
(4.14) |
|
|
||||
|
lg σ N - lg σ R aв |
|
Одержану властивість використовують для експериментального визначення т .
Відомо, що:
т=9 – згин (сталі, чавуни);
т=6 – контактне навантаження (сталь, чавун, бронза);
т=5÷8 – згин, розтяг (матеріали пасів);
т=3 – всі види деформацій зварних і клепаних конструкцій.
57

Більш детально про розрахунок числа циклів N N , вибір базового числа циклів навантаження N 0 та показника степеня m буде розглянуто в курсі по мірі вивчення конкретних розділів курсу.
4.5. Врахування зміни навантажень у розрахунках деталей машин
Розрахунок деталей машин, які знаходяться під дією постійних за величиною навантажень, здійснюється за величиною цих навантажень. У кожному конкретному випадку приходиться враховувати можливі перевантаження, корозійне чи абразивне спрацювання та ін.
Більшість деталей машин працює в умовах циклічно змінних навантажень, величина і строк дії яких по різному впливають на строк служби машини. Кожний, різний за величиною і частотою цикл напружень по різному викликає в матеріалі деталі накопичення фізичних змін, які спричиняють виникнення мікроскопічних тріщин, розвиток яких призводить до поломок втомного характеру. І було б неправильно виконувати розрахунки деталей за величиною найбільших діючих навантажень, оскільки час дії цих навантажень значно менший строку служби деталі. Такий розрахунок призвів би до неоправданого збільшення розмірів і маси деталі.
Рис. 4.4. Робочі цикли зміни навантаження
58
На рис. 4.4. показаний у формі приклада закон зміни навантаження F і частоти обертання n (хв-1) розраховуваної деталі (вала, осі, зубчастого колеса і т. д.) за деякий повторюваний період часу tc = t з перервами між змінами tПЗ . Число таких періодів (блоків) за повний строк служби ∑ tc
позначимо μc .
Закон зміни навантаження і частоти обертання може бути однаковим або різним в залежності від характеру виконуваної роботи. Навантаженням може бути сила F , момент згину М або крутний момент Т і т. д. Плавну зміну F і n звичайно замінюють ступінчастою (гістограмою) шляхом
вписування прямокутників зі сторонами F1t1 ; F2 t2 … Fk tk і n1t1 , n2 t2
… nk tk . Максимальне навантаження і відповідну йому частоту обертання відмічають індексом 1, а наступні навантаження у порядку зменшення позначають 2, 3 і т. д.
Розгляданий закон зміни навантаження можна представити у виді, показаному на рис. 4.5 а, на якому по горизонтальній осі відкладені значення чисел циклів зміни напружень N ∑ , а по вертикальній – значення
навантажень у порядку зменшення. На рис. 4.5,а показані три навантаження, але розгляданий метод відноситься до будь-якого числа навантажень.
59