
DM_1 / Деталі машин КЛ [Стадник В. А
.].pdf
спряженої поверхні) називають інтенсивністю зношування і позначають літерою I h
I h = |
h |
. |
(3.10) |
|
|||
|
L |
|
Рис. 3.2. Зміна інтенсивності зношування та зносу в часі На рис. 3.2. представлений графік, що характеризує інтенсивність
зношування I h і зносу h протягом строку служби машини. В процесі роботи інтенсивність зношування робочих поверхонь (зубчастої пари, підшипника, шарніра, гвинтової пари і т.д.) може суттєво змінюватися. В початковий період роботи через неминучі похибки виготовлення і деформації можливі значні нерівномірності розподілу навантажень в зоні дотику. На ділянці I
відповідному періоду припрацювання, інтенсивність Ih = Iпр значна і величина h швидко росте. Потім інтенсивність I h знижується і наступає так званий період усталеного зношування (період II), причому I уст << Iпр .
Якщо між спряженими поверхнями забезпечується безперервний мастильний шар, то зношування може бути відсутнім (див. штрихові лінії на рис. 3.2).
40
Зміна форми і розмірів при терті деталей в період усталеного зношування може стати причиною збільшення зазорів, порушення умов мащення і приводить до III періоду інтенсивного зношування на кінцевому етапі експлуатації машини (рис. 3.2).
Теплостійкість. Під теплостійкістю розуміють здатність деталей зберігати нормальну працездатність у припустимих (заданих) межах температурного режиму, викликаного робочим процесом машин і тертям у їхніх механізмах. Тепловиділення, яке пов’язане з робочим процесом, має місце в теплових двигунах, електричних машинах, ливарних машинах і в машинах для гарячої обробки матеріалів. Нагрівання деталей машин може викликати такі шкідливі наслідки: зниження міцності матеріалу і появу залишкових деформацій (так зване явище повзучості, яке спостерігається в машинах з дуже напруженим тепловим режимом, наприклад, у лопатках газових турбін); зниження захисної здатності мастильних плівок, а отже, збільшення зносу тертьових деталей; зміну зазорів у спряжених деталях; у деяких випадках зниження точності роботи машини; у деталях, що працюють в умовах багаторазової циклічної зміни температури, можуть виникнути і розвинутись мікротріщини, що призводять в окремих випадках до руйнування деталей.
Для забезпечення нормального теплового режиму роботи деталей і вузлів машин у ряді випадків виконують спеціальні розрахунки, наприклад, тепловий розрахунок черв’ячних редукторів.
Вібростійкість. Під вібростійкістю розуміють здатність деталей і вузлів працювати в потрібному режимі без недопустимих коливань (вібрацій). Вібрації викликають додаткові змінні напруження і можуть призвести до втомного руйнування деталей. Особливо небезпечними є резонансні коливання. У зв’язку з підвищенням швидкостей руху машин небезпека вібрації зростає, тому розрахунки параметрів вимушених коливань набувають усе більшого значення.
41

3.2. Види руйнування деталей під дією навантаження та формули
для визначення напружень
Для виконання розрахунків, що відповідають основному критерію працездатності за допустимими напруженнями, використовують формули опору матеріалів, які залежать від деформації, як схематично показано на рис. 3.3. а, б, в, г, д, є, ж, з:
а) розтяг, а потім розрив,
σ р = F , де A – площа
A
перерізу, мм2 ( для круга
A = πd 2 );
4
б) стиск, а потім зминання,
σ |
|
= |
A |
, де A – площа |
|
с |
F |
||||
|
|
|
|||
|
|
|
|
перерізу, мм2 ( для круга
A = πd 2 );
4
в) скручування, а потім зсув або
зріз, τ = |
T |
, де W p - |
|
||
W p |
|
полярний момент опору, мм3(для круглого перерізу
W p = πd 3 ≈ 0 ,2d 3 );
16
г) зріз заклепки по площині
стику листів, τ = F , де
A
42

A = πd 2 ;
4
д) згин, потім деформація і
злам, σ зг = М , де W x -
W x
осьовий момент опору, мм3 (для круглого перерізу
W x = πd 3 ≈ 0 ,1d 3 );
32
є) втрата стійкості і руйнування конструкції. Розрахунок за формулою Ф.С. Ясінського (див. довідкову літературу з опору матеріалів).
ж) скручування зі згином, еквівалентне напруження
σ екв = σ 2 + ατ 2 ,α = 3...4
з) втомне викришування контактуючих поверхонь. Розрахунок на міцність контактуючих поверхонь, підданих циклічним навантаженням, виконують за контактними напруженнями σ н . Для контакту двох циліндрів за формулою Герца
43
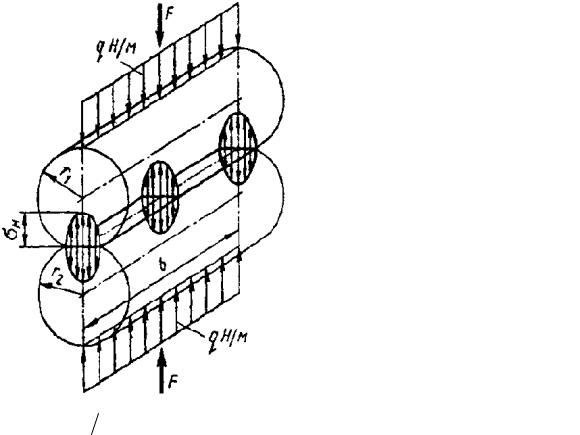
σ н |
= |
q |
|
Enp |
|
|
, де |
|
ρзв 2π (1 − |
μ 2 ) |
|||||||
|
|
|
q = F - навантаження на b
одиницю довжини контактної
лінії; |
1 |
ρзв |
= |
1 |
± |
1 |
, де знак |
|
r |
r |
|||||||
|
|
|
|
|
||||
|
|
|
1 |
2 |
|
+ для зовнішнього контакту, знак – для внутрішнього, ρзв - зведений радіус кривини контактуючих поверхонь, r1 і r2 - радіуси кривини в точках контакту;
Епр = 2 Е1 Е2 (Е1 + Е2 ) - |
Рис. 3.3. Види руйнування деталей |
зведений модуль пружності, E1 і E2 – модулі пружності матеріалів циліндрів; μ - коефіцієнт Пуассона. Формула Герца є вихідною у розрахунках фрикційних, зубчастих і черв’ячних передач на контактну міцність.
Проектні і перевірні розрахунки
Проектний розрахунок полягає у визначенні параметрів перерізів деталей у небезпечних перерізах за допустимими напруженнями. Розрахунок набуває в більшості випадків форми попереднього для прийнятої або намічуваної конструкції.
Використовуючи, наприклад, формулу для визначення напружень розтягу (рис. 3.3. а), виведемо формулу проектного розрахунку для стрижня круглого перерізу з невідомим діаметром d .
44

Умова міцності стрижня має вигляд
σ = |
F |
|
|
£ [σ ]p |
, |
|
|||
|
|
|
(3.11) |
||||||
πd 2 |
4 |
||||||||
|
|
|
|
|
|||||
звідки діаметр небезпечного перерізу: |
|
||||||||
|
|
|
|
|
|
||||
d ³ |
|
4F |
|
|
|
||||
|
|
, |
|
(3.12) |
|||||
|
|
||||||||
|
|
π[σ ]p |
|
||||||
|
|
|
|
де F - поздовжня сила в небезпечному перерізі стрижня.
Перевірний розрахунок відрізняється від проектного тим, що за відомими розмірами деталі, наприклад, діаметра стрижня d , конструктор перевіряє виконання основної умови міцності (формула 3.11).
Кінцевим результатом виконання розрахунків, що відповідають основним критеріям працездатності за допустимими напруженнями, жорсткістю, теплостійкістю та вібростійкістю є надійність виробу.
Надійність – це властивість виробу зберігати в часі в установлених границях всі параметри, що забезпечують виконання потрібних функцій у заданих умовах експлуатації.
Надійність оцінюється ймовірністю збереження працездатності протягом заданого строку служби.
Якщо надійність φ(t )= 0 ,99 , при t = 10000 годин, то це значить, що із 100 виробів 1 виріб втратить працездатність раніше 10000 годин.
Втрату працездатності називають відказом. Відкази поділяють на відкази функціонування, при яких виконання своїх функцій виробом припиняється (наприклад, поломка зубців шестерні, заклинювання, прокол, тощо) і відкази параметричні, при яких деякі параметри виробу змінюються у недопустимих границях (наприклад, втрата точності верстата, падіння компресії у двигуні, тощо.
Причини відказів діляться на випадкові і систематичні.
45
Випадкові причини – це непередбачені перевантаження, дефекти матеріалу і похибки при виготовленні, невиявлені контролем, помилки обслуговуючого персоналу або перебої системи управління.
Систематичні причини – це закономірні явища, які зумовлюють поступове накопичення пошкоджень: вплив середовища, часу, температури, опромінення – корозія, старіння і робота тертя – втома, повзучість, зношування, функціональні впливи – засмічення, залипання, витікання.
За причинами виникнення відкази можна також розділити на конструкційні, викликані недоліками конструкції, технологічні, викликані недоліком або порушенням технології, і експлуатаційні, викликані неправильною експлуатацією.
Таким чином надійність машини залежить від трьох періодів:
−проектування;
−виробництва;
−експлуатації.
При проектуванні надійність закладається конструктором.
При виробництві надійність деталі забезпечується технологом і контролером, так як відхилення від вимог конструкторської документації порушує надійність.
При експлуатації надійність гарантується дотримуванням правил і норм експлуатації. Випадкові відхилення від розрахункових режимів експлуатації знижують надійність. Надійність складної системи (наприклад, автомобіля), нижча надійності самого ненадійного елемента системи. Чим більше елементів має система, тим нижча її надійність. Багато систем включають десятки і сотні тисяч елементів (літаки, ракети, автоматичні лінії та ін.). Низька надійність елементів (деталей, вузлів) робить такі системи непрацездатними.
Основні шляхи підвищення надійності на стадії проектування:
46
1.Потрібно проектувати прості вироби з найменшою кількістю деталей. Надійність деталей повинна бути одного порядку.
2.Зменшення напруженості деталей за рахунок використання високоміцних матеріалів і зміцнюючої технології. Так термообробка
зубчастих коліс збільшує |
|
навантажувальну здатність у 2…4 рази. |
|
Дробоструменевий наклеп |
зубчастих |
коліс, пружин, ресор підвищує |
|
строк служби на втому в 2…3 |
рази і т. |
д. |
3.Хороша система мащення, правильний вибір мастила, захист від попадання пилу та бруду.
4.Статично визначені системи більш надійні, так як у них дефекти виробництва у меншій мірі впливають на характер розподілу навантаження.
5.Необхідно застосовувати стандартні вузли та деталі, які виготовляються на спеціалізованих заводах у серійних і масових кількостях.
6.Запобіжні пристрої виключають випадкові перевантаження, відключаючи вузол або систему в цілому.
7.Іноді застосовують не послідовне, а паралельне з'єднання вузлів і резервування. Літак з чотирма двигунами більш надійний.
8.Ремонтопридатність конструкції машини – це відношення часу простою в ремонті до робочого часу – підвищує надійність машини. Отже, по надійності виробу можна судити про якість проектно-
конструкторських робіт, технічного рівня виробництва і експлуатації машин.
9.Для попередження шкідливих наслідків впливу перегріву на роботу машини виконують теплові розрахунки, а при необхідності передбачають штучне охолодження.
10.Забезпечення вібростійкості виробу.
Вібрації при роботі машини виникають з різних причин:
47
1.Нерівномірність навантаження приводить до коливання швидкості ведучої ланки.
2.Неврівноваженість деталей, що обертаються, тобто недостатнє балансування (статичне і динамічне) цих деталей.
3.Неврівноваженість механізму машини.
4.Низька жорсткість окремих деталей.
5.Збільшені зазори в кінематичних парах.
Випадкові (неперіодичні) коливання, спричинені раптовою зміною корисних і шкідливих опорів, викликають додаткові напруження в деталях і приводять до їх втомного руйнування. У деяких випадках вібрації знижують якість роботи, виконуваної машиною (наприклад, у металорізальних верстатах).
Особливу небезпеку представляють резонансні коливання. При підвищених швидкостях роботи машини у деяких випадках зростає вібрація. Рекомендується вибирати режими роботи таким чином, щоб вони знаходились у дорезонансній або зарезонансній областях. Для багатьох машин, що серійно випускаються промисловими підприємствами, передбачено нормування шумових характеристик.
Контрольні запитання
1.Що таке працездатність машини і які критерії її характеризують?
2.Охарактеризуйте розрахунки, які виконуються під час проектування і конструювання.
3.Запишіть умови міцності для простих деформацій і наведіть приклади деформацій деталей машин.
4.Охарактеризуйте параметри, від яких залежать контактні напруження.
5.Поняття жорсткості і податливості деталей машин.
6.Назвіть та дайте визначення основних термінів надійності.
7.Назвіть шляхи підвищення надійності машин.
48
8.Які шкідливі явища виникають в машинах при роботі їх в умовах підвищення температур?
9.Що таке вібростійкість та які шкідливі дії вібрацій?
49