
Проектирование ЦП маг Л4
.pdf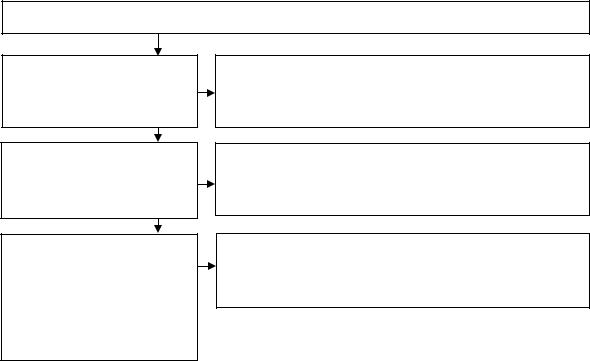
Тема 4. Задачи проектирования на микроуровне
Задачи проектирования в логистике на микроуровне
- определение емкости и конфигурации рабочего пространства
-оптимальное размещения технологического оборудования
-маршрутизация движения материального потока внутри рабочего пространства между точками размещения оборудова-
ния и складами
Проектирование складов, портов, контейнерных терминалов, производств (расчет площадей рабочих зон, определение расположения зон) и т.д.
Проектирование конвейера (поточной линии), оптимальная расстановка оборудования в цехах; slotting
Транспортная задача, задача коммивояжѐра для внутрискладского или внутрипроизводственного транспорта
Рис.4.1. Задачи проектирования в логистике
4.1. Общие принципы организации материальных потоков в микрологистических системах.
1.Прямоточность – необходимо стремиться к максимальному выпрямлению технологических маршрутов движения элементов материального потока по стадиям технологического процесса как в горизонтальном, так и в вертикальном направлениях таким образом, чтобы обеспечить кратчайший в пространстве и во времени путь, без возвратных и встречных перемещений, без пересечений материальных потоков.
Реализация на практике данного принципа при проектировании микрологистических систем позволяет сократить объем внутрипроизводственных перевозок, снизить время транспортировки, уменьшить потребность в транспортных средствах и технологическом оборудовании.
2.Пропорциональность (сбалансированность, согласованность) – взаи-
мосвязанные технологические процессы и их элементы должны соответствовать друг другу по производительности, пропускной способности, скорости.
Реализация на практике данного принципа подразумевает не только обеспечение равной пропускной способности разных рабочих мест одного процесса, но также и пропорциональное обеспечение рабочих мест информацией и материальными ресурсами и т.д.
Нарушение этого принципа может привести к возникновению «узких мест» в работе и серьезным сбоям.
1
3.Ритмичность – предполагает организацию во времени и пространстве отдельных технологических процессов в единый непрерывный производственный процесс, обеспечивающий своевременный выпуск каждой конкретной продукции в установленных объемах с минимальными затратами производственных ресурсов.
4.Поточность (непрерывность) – предполагает сокращение перерывов между обработкой элементов материального потока на взаимосвязанных этапах технологического процесса, а также отсутствие разрывов в пространственной цепи взаимосвязанных рабочих центров. Выполнение каждой предыдущей операции должно одновременно являться подготовкой к следующей; размещение рабочих мест (зон), оборудования, инструментов должно производиться в соответствии с последовательностью технологического процесса, направлением и скоростью перемещения материального потока.
Реализация принципа поточности на практике способствует сокращению длительности цикла рабочего процесса, улучшению использования оборудования, площадей, персонала; снижению уровня запасов и связывания в них оборотных средств. Удельная трудоемкость поточной организации технологического процесса в 3-4 раза ниже соответствующего показателя при традиционных формах организации. Поточность на практике осуществляется в частности за счет применения конвейерных систем.
5.Параллельность – предполагает совмещение во времени (одновременность) выполнения различных рабочих процессов, операций. При этом экономится рабочее время, сокращается длительность производственного цикла.
6.Надежность – обеспечение достаточной гибкости и маневренности в реализации цели при возникновении различных отклонений от плана. Достигается за счет точных прогнозов, эффективного управления запасами, использование высокопроизводительного оборудования и системы резервирования оборудования.
4.2. Оптимальное размещение продукции на складах - slotting
Функционирование склада сопровождается затратами трудовых и технических ресурсов. По оценкам американских специалистов, большинство современных складов (распределительных центров) тратят ежегодно на 1030% больше потому, что в них неправильно организованы места хранения товаров. Снизить эти затраты можно путем разделения всего ассортимента на группы, требующие различной частоты манипуляций и рациональным размещением этих групп товаров на имеющемся складском пространстве.
2
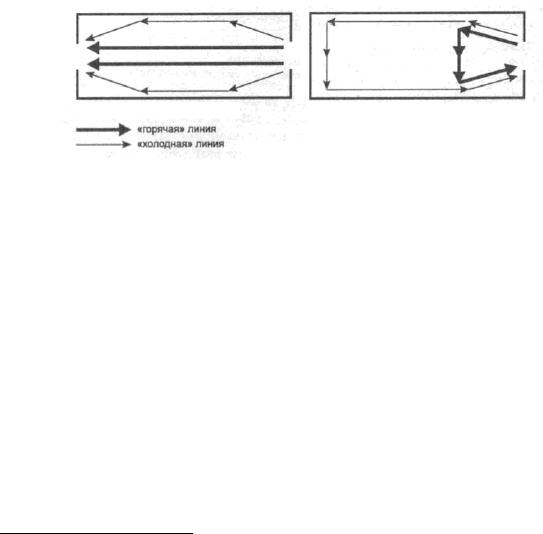
Общие принципы и рекомендации по размещению продукции на складах1:
-совместное размещение товаров, близких по своим физикохимическим свойствам и требованиям к режиму хранения;
-расположение по соседству товаров, отпускаемых вместе, в общей
партии;
-закрепление мест хранения не за отдельным товаром, а за товарной группой;
-размещение товаров одного вида в стеллажах по обе стороны одного прохода и на одном уровне;
-использование унифицированной тары (товароносителей);
-товары, пользующиеся наибольшим спросом (а также крупногабаритные товары и товары, хранящиеся без тары), рекомендуется размещать
в«золотой зоне» вдоль «горячих линий», а также ближе к зонам отгрузки; товары, требующиеся реже, отодвигают на «второй план» и размещают вдоль «холодных» линий, на верхних полках.
«Золотая зона» – это места хранения, расположенные на уровне между поясом и плечами комплектовщика.
Расположение «горячей» и «холодной» зон или линий склада зависят от конструктивных особенностей складов (рис. 4.2)
Рис. 4.2 «горячие» и «холодные» линии размещения продукции на складах [Гаджинский, Современный склад]
Slotting – это методика размещения единиц хранения (SKU, stockkeeping units) в зоне хранения на складе, то есть определяется сколько единиц (SKU) и какого товара где разместить.
Критерии размещения продукции на складе:
1. число запросов на отгрузку SKU данного товара, которое влияет на объем работы комплектовщика (наиболее распространенный критерий);
2. оборот по позиции, то есть общие количество SKU данного товара, которое было отгружено со склада за определенный период времени;
3. объем – оборот по позиции, помноженный на объем одной единицы хранения в метрах кубических;
4. плотность комплектации - отношение среднего числа запросов на отгрузку данного товара к среднему объему его хранения на складе;
1 Гаджинский. Современный склад.
3
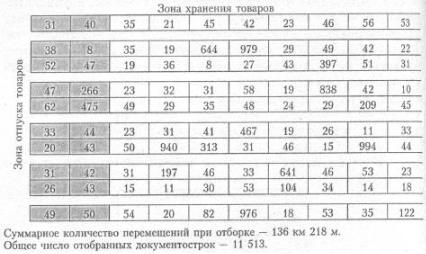
5. cube-per-order-index (COI) – отношение среднего объема, занимаемого товаром на складе в течение определенного периода к обороту по позиции.
Далее товары ранжируются по критериям 1-3 от максимума к минимуму, а по критериям 4 и 5 – от минимума к максимуму. Товары, которые после ранжирования оказались на первых строчках ранжированного перечня располагают в наиболее удобных местах склада, которые называют «горячей» или «золотой» зонами склада.
Пример [Гаджинский, Современный склад]:
Рассмотрим в качестве примера модель склада, планировка которого соответствует форме, представленной на рис. 4.3 ниже. Ассортимент склада включает 100 позиций, размещенных в случайном порядке в разных секциях стеллажей (ячейки таблицы). Предположим, что груз хранится в стеллажах на поддонах в пакетированном виде, отпускается целыми грузовыми пакетами, и все операции с ним полностью механизированы. Всего за предшествующий период (например, за прошлый месяц) в нашей модели было отпущено 11513 грузовых пакетов.
На рис. 4.3 А. показан вариант случайного размещения запаса на складе, т. е. без учета скорости оборота разных позиций. Числа в ячейках таблицы указывают на количество заказов по данной позиции за период. Для данного варианта суммарный пробег техники при укладке на хранение и отборке составляет за период более 136 км (при длине ячейки стеллажа - 1400 мм).Суммарное количество перемещений при отборке - 136 км 218 м. Общее число отобранных документострок - 11513.
В этом примере на 20 позиций ассортимента пришлось 82% заказов. Очевидно, что размещение запасов по этим позициям следует тщательно контролировать. Моделирование, выполненное на компьютере, показало, что при размещении «ударных» позиций на «горячих» линиях склада суммарный пробег сократится до 56 км, т. е. более чем в два раза (см. рис. 4.3 Б).
Рис.4.3 А. Случайное размещение товаров на складе (в ячейках таблицы указана количество обращений к лежащему в них товару)
4
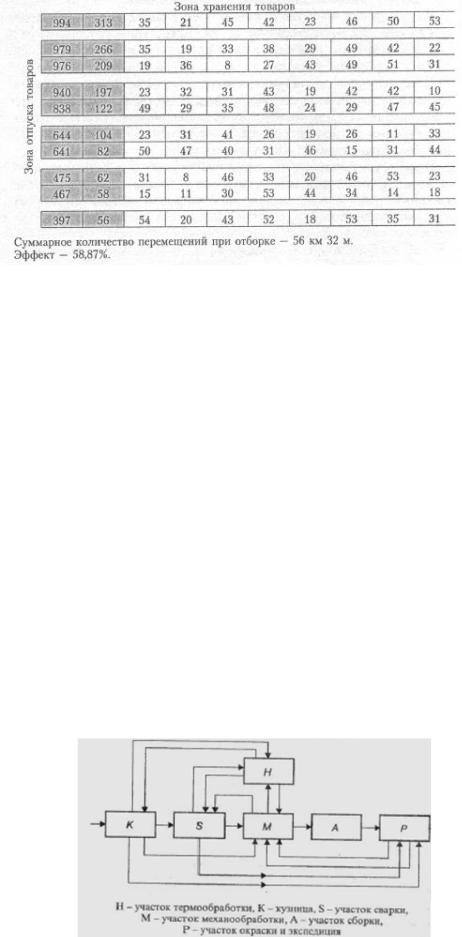
Рис.4.3 Б. Оптимизированное по критерию «частота обращений» размещение товаров на складе
4.3. Задача оптимального размещения производственных мощностей на предприятии
Существует четыре основных способа размещения оборудования и организации рабочих мест на промышленных предприятиях:
1.размещение по технологическому принципу (технологическая специализация);
2.размещение по предметному принципу (объектная специализация);
3.размещение по принципу групповой технологии;
4.размещение оборудования по принципу обслуживания неподвижного объекта
Размещение оборудования по технологическому принципу (техно-
логическая специализация) - это такой способ размещения, при котором одинаковое оборудование или однородные технологические операции группируются вместе. Например, все токарные станки располагают в одном месте, а все штамповочные прессы - в другом. Обрабатываемая деталь перемещается в соответствии с последовательностью операций с одного места на другое, где для каждой операции расположено соответствующее оборудование.
Рис. 4.4. Технологическая специализация
5

Размещение оборудования по предметному принципу (объектная специализация) - означает создание производственных ячеек под конкретные изделия (или их семейства), которые будут в них изготавливаться. На машиностроительном предприятии это могут быть цеха: механообработки, шестерен, сборки двигателей и т.п. Вследствие такого решения в одной ячейке концентрируются машины различных типов.
Рис. 4.5. Объектная специализация
Размещение оборудования по принципу групповой технологии
предполагает группировку различного оборудования в рабочие центры, или технологические ячейки, для обработки изделий, имеющих одинаковые или сходные способы и требования к обработке. Размещение оборудования по принципу групповой технологии, с одной стороны, аналогично размещению оборудования по технологическому принципу, в соответствии с которым создаются ячейки для выполнения определенного набора технологических операций, а с другой - напоминает размещение по предметному принципу, поскольку рабочие центры специализируются на выпуске ограниченного ассортимента изделий.
Размещение оборудования по принципу обслуживания неподвиж-
ного объекта реализуется в случае, если изделие (из-за больших габаритов или массы) в течение всего технологического процесса остается на одном месте. Производственное оборудование подвозится к изделию, а не наоборот. По такому принципу организованы судостроительные верфи, строительные площадки и т.п.
Многие производственные объекты в целом представляют собой комбинацию различных видов размещения оборудования и организации процесса. Например, работу одного цеха можно организовать на основе технологического принципа, а другого – на основе предметного.
Обычно работа всего предприятия организуется по предметному принципу (изготовление основных узлов, промежуточная сборка, линия окончательной сборки), но каждая производственная стадия реализуется по технологическому принципу или по предметному, например, в сборочном цехе.
Организация производственных участков и размещение технологического оборудования обусловлены следующими факторами:
6
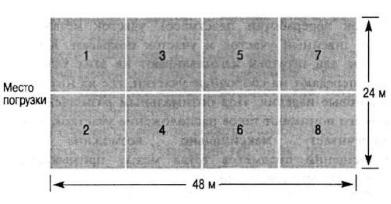
особенности производственного пространства (архитектурные особенности здания, размер и взаимное расположение производственных площадей);
-особенности технологического процесса;
-характер и направление материального и сопутствующих потоков;
-принцип однонаправленности движения материального потока;
-минимизация времени продвижения материального потока в системе
исокращение транспортных издержек.
4.3.1.Размещение оборудования по технологическому принципу
Предположим, что на фабрике игрушек для минимизации затрат на пе-
ремещение нужно сформировать восемь участков. Для упрощения примем, что все участки равны по площади (скажем, 12 на 12 метров) и что ширина здания - 24 метра, а длина – 48 (см. рис. 4.6).
Рис.4.6. Размеры здания и расположение участков на примере фабрики игрушек [Чейз и др.]
Во-первых, следует выяснить структуру потока между участками и способ транспортирования материалов. Допустим, что такая информация у нас есть. Будем считать, что все материалы транспортируются в стандартных тарных решетчатых ящиках с помощью автопогрузчика с вилковым захватом.
Перемещение одного ящика (тарного места) требует одного автопогрузчика, что составляет один лоуд ("лоуд" - мера загрузки).
Теперь предположим, что транспортные расходы составляют 1 доллар при перемещении одного лоуда между соседними участками и 1 доллар дополнительно при каждом пересечении границ между несмежными участками. Ожидаемый объем транспортируемого груза в лоудах между участками за единицу времени представлен в виде таблицы (см. рис. 4.7); допускаются диагональные перемещения, поэтому участки 2 и 3, 3 и 6 считаются смежными.
7

Рис.4.7. Материальный поток между участками фабрики игрушек [Чейз и др.]
Далее графически изобразим материальный поток между участками, например, в виде графа, показанного на рис. 4.8. Этот граф будет исходным для поиска схемы наилучшего размещения участков.
Рис.4.8. Базовый граф материального потока
Определим транспортные затраты при исходном размещении производственных участков. Для этого стоимость транспортировки одного лоуда умножают на количество лоудов, перемещаемых между каждой парой участков – см. рис 4.9.
Рис.4.9. Матрица затрат при базовом варианте размещения участков
8
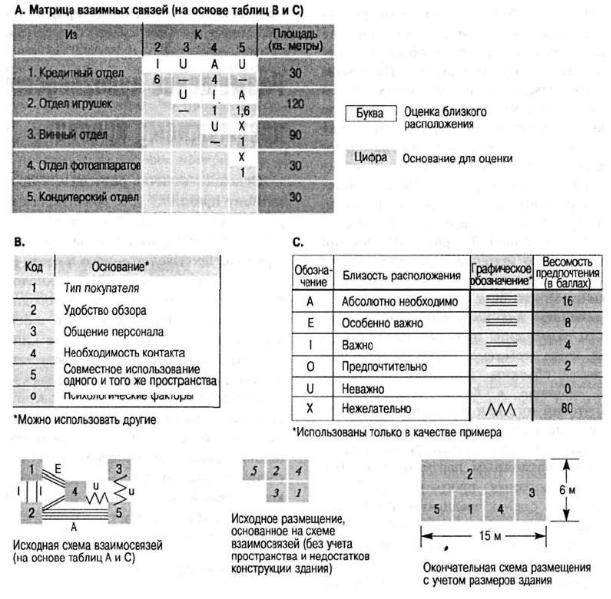
Для поиска оптимального решения на практике используют компьютерное моделирование в сочетании с оптимизационными моделями математического программирования и эвристическими алгоритмами.
Когда невозможно получить количественное описание материального потока, используется метод системной планировки размещения оборудо-
вания (Systematic Layout Planning — SLP). Данный метод включает разра-
ботку матрицы взаимных связей, отражающую степень предпочтения каждого производственного объекта по отношению ко всем остальным в отдельности. На основе этой матрицы разрабатывают схему взаимных связей (отношений) между отдельными объектами, аналогичную графу материальных потоков. Устанавливаются числовые значения в баллах для степеней (весомости) предпочтений того или иного отдела, а затем опробываются различные варианты размещения. Вариант размещения выбирается по наибольшей сумме баллов, подсчитанной по всем возможным парам отделов – см. рис. 4.10.
Рис.10. Решение задачи о размещении пяти отделов в магазине методом системной планировки [Чейз и др.]
9
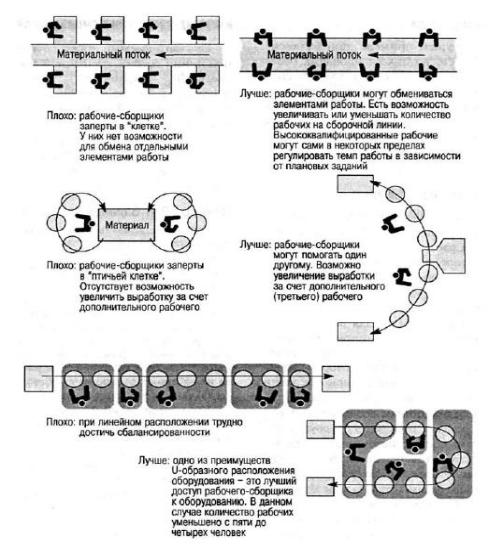
4.3.2. Размещение производственного оборудования по объектному принципу
При организации производственного процесса по объектному принципу оборудование или участки предназначаются для производства совершенно определенных видов продукции, для бесперебойной работы используют резервное оборудование и в целом достигается прямолинейное движение материального потока. Размещение оборудования по предметному принципу имеет смысл, когда объемы партий конкретных изделий или деталей велики, а ассортимент производимых изделий или деталей ограничен несколькими наименованиями. Примером организации производственного процесса, ориентированного на изделие являются поточные линии.
Поточная линия предполагает многократно повторяющийся процесс, отдельные звенья которого связаны между собой устройством для транспортирования материалов. Поточные линии, как правило, работают с определенным темпом и нормы времени каждой технологической операции одинаковы. Возможные конфигурации поточных линий представлены на рис.4.11.
Рис.4.11. Возможные конфигурации поточных линий [Чейз и др.]
10