
Проектирование ЦП маг Л4
.pdf
Одной из основных логистических задач применимо к поточным про-
изводственным линиям является задача балансирования поточной линии.
В наиболее общем случае поточная линия представляет собой движущийся конвейер, предметы труда на котором проходят через ряд рабочих мест (станций) через одинаковые временные интервалы, которые называют тактом поточной линии (промежуток времени между изготовлением на поточной линии двух соседних единиц продукции). На каждом рабочем месте выполняется определенная технологическая операция.
Операция, выполняемая на каждом рабочем месте, состоит из множества отдельных элементов, действий и движений, объединяемых в рабочие блоки. Обычно рабочие блоки сгруппированы из элементов и движений таким образом, что их трудно подразделить на более мелкие группы действий.
Задача балансирования поточной линии сводится к проблеме установления продолжительностей всех операций таким образом, чтобы каждый рабочий выполнял столько элементов (рабочих блоков), составляющих операцию, сколько их можно выполнить за такт поточной линии, и чтобы свободное время, не предназначенное для выполнения операций (простой), было минимальным на всех рабочих местах. Задача может усложняться наличием взаимосвязей между операциями, обусловленными конструкцией изделия и технологическим процессом. Эти взаимосвязи определяют порядок выполнения элементов операций во время сборки.
Алгоритм балансирования поточной линии:
1.Строится граф последовательности выполнения элементов. Граф состоит из кружков и стрелок. Кружками обозначены элементы операций, а стрелками — очередность их выполнения.
2.Рассчитывается такт поточной линии - С:
С |
дневноерабочее время |
(4.1) |
необходимый объем дневног о выпуска продукции |
3. Определяется расчетное минимальное количество рабочих мест N, , необходимое для обеспечения заданного такта (результат необходимо округлить до наибольшего целого числа):
N |
суммарное время выполнения всех операций |
(4.2) |
|
такт поточной линии |
|||
|
|
4. Формулируется первое правило (а), в соответствии с которым следует определять последовательность выполнения элементов на рабочих местах, и второе правило (b) для формирования операций:
Правило (a): При определении состава операций из всей группы элементов вначале последовательно извлекаются элементы с наибольшим количеством последующих элементов, и производится их ранжирование по мере убывания количества последующих элементов;
Правило (b): В цепочках с заданной последовательностью выполнения элементов среди ближайших последующих элементов выбирают самые продолжительные элементы.
11
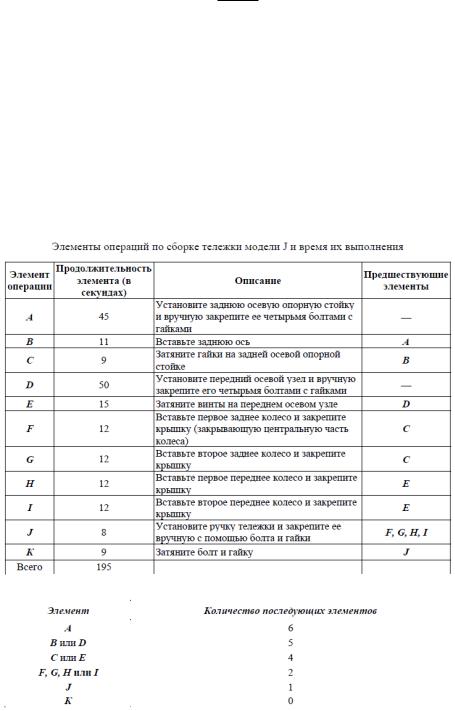
5. Определяется состав и продолжительность операций для первого рабочего места поточной линии путем последовательного добавления элементов рабочего процесса, начиная с первого, по одному до тех пор, пока суммарное время выполнения операции не станет равно такту поточной линии (С) или пока станет невозможно добавить какие-либо элементы из-за ограничения по времени или последовательности выполнения элементов.
Данная процедура повторяется для рабочих мест № 2, 3 и т.д., пока не определится продолжительность всех операций, число которых - Na.
5. Осуществляется оценка эффективности балансировки:
Э |
T |
, |
(4.3) |
N A C |
где Т – суммарное время выполнения всех операций.
7. Если эффективность недостаточна, осуществляется повторное балансирование, используя другие правила формирования операций.
Пример балансирования поточной линии:
Пусть на конвейере собирается модель тележки J. В день необходимо изготовить 500 штук тележек. Суммарное время выполнения операций — 420 минут, элементы сборочных операций и их продолжительности приведены на рис. 4.12. Необходимо сбалансировать линию так, чтобы число рабочих мест было минимальным и соответствовало такту конвейера.
Рис. 4.12. Исходные данные для решения задачи
12
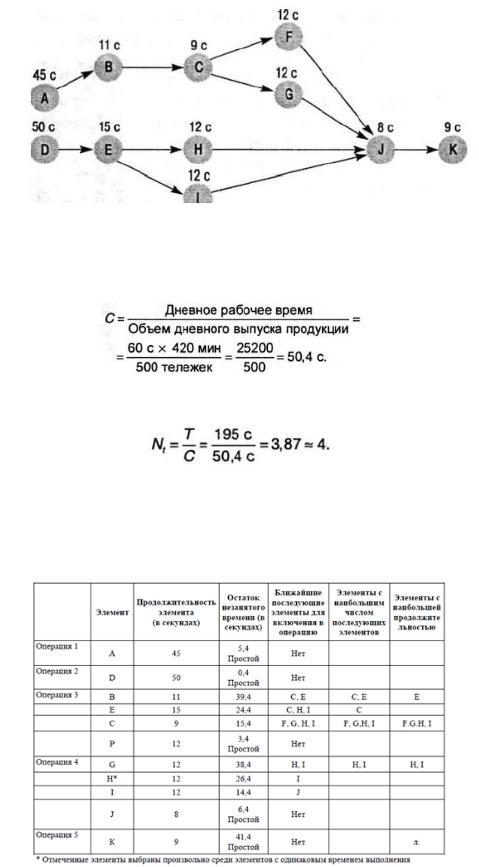
Решение:
1. Строим граф последовательности выполнения элементов сборки тележки (рис. 4.13).
Рис. 4.13. Граф последовательности выполнения элементов сборки тележки модели J
2.Рассчитываем такт в секундах:
3.Рассчитываем теоретически необходимое минимальное количество рабочих мест (фактическое количество рабочих мест может быть больше):
4.Определяем состав операции на каждом рабочем месте по правилам «а» или «в». Эти манипуляции для нашего примера представлены в табл. на рис. 4.14 и на графе, рис. 4.15. Числу сформированных операций (в нашем примере их 5, см. табл. на рис. 14) соответствует количество необходимых рабочих мест, т.е. Nа = 5.
Рис. 4.14. Результат балансировки в табличной форме
13
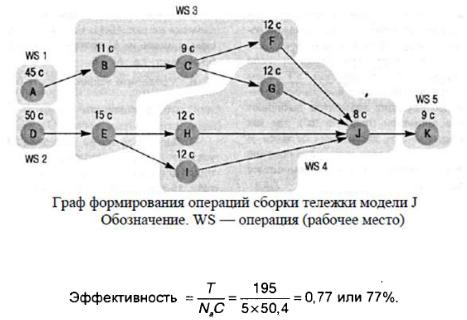
Рис. 4.15. Результат балансировки в графической форме 5. Определяем эффективность балансирования по формуле:
Значение эффективности, равное 77%, указывает на существование простоев, продолжительность которых для всей поточной линии составляет 23% (1,0 - 0,77). Из табл. на рис. 4.14 можно найти, что общее время простоев составляет 57 с, причем пятая операция имеет максимальный простой, рав-
ный 41,4 с.
Лучшей балансировки можно достичь опять таки с использованием специального программного обеспечения, например, - программный пакет
Siemens FactoryFLOW (www.plm.automation.siemens.com).
4.3.3.Размещение оборудования по принципу групповой технологии
При размещении оборудования по принципу групповой технологии
различное оборудование группируют в ячейки для выполнения операций с несколькими изделиями, однородными по конструктивнотехнологическим признакам. В настоящее время этот принцип широко используется при металлообработке, производстве чипов для компьютеров и на сборочных работах. Наибольшие преимущества и выгоды от размещения оборудования по принципу формирования технологических ячеек получает производство, работающее по заказам, и мелкосерийное производство. К этим преимуществам относятся следующие:
1.Улучшение человеческих взаимоотношений. В состав ячейки входят несколько рабочих, которые образуют небольшую рабочую бригаду, выполняющую законченный блок работ.
2.Быстрое приобретение и накопление производственного опыта. Рабочие имеют дело с ограниченным числом разнотипных деталей. Поэтому благодаря частому повторению работ с одними и теми же деталями, рабочие быстро обучаются.
3.Уменьшение незавершенного производства и затрат на транспортирование материалов. Ячейка объединяет несколько производственных опера-
14
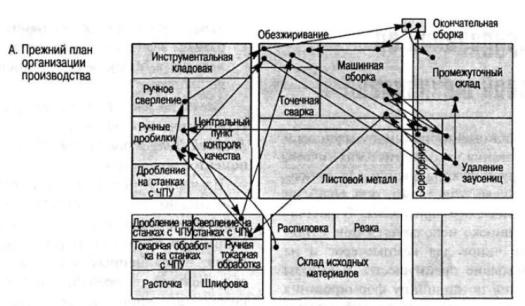
ций, поэтому детали в ней меньше задерживаются на обработке и не требуется их большого запаса.
4. Быстрая переналадка производства. Ограниченное количество видов выполняемых работ требует относительно небольшого комплекта необходимых инструментов, который можно быстро заменить при переходе на выпуск другой продукции.
Алгоритм формирования производственных ячеек:
1.Группировка компонентов изделия в семейства, имеющие общие этапы обработки. Эта стадия требует разработки компьютеризированной системы классификации и кодирования деталей. Часто эта стадия самая дорогая, несмотря на то, что многие компании разработали короткие процедуры для идентификации и формирования семейств деталей.
2.Определение структуры доминирующих потоков семейств компонентов, на основе которых размещаются или переразмещаются технологические процессы.
3.Физическая группировка оборудования и технологических процессов
вячейки. На этом этапе иногда некоторые компоненты невозможно включить в какое-либо семейство, а специализированное оборудование нельзя разместить в одной из ячеек из-за того, что оно часто используется для выполнения работ, относящихся к разным ячейкам. Такие негруппируемые компоненты изделия и оборудование размещают в отдельной ячейке "остатков".
Схема на рис. 4.16 иллюстрирует процесс разработки технологических ячеек, который применяют в компании.
Рис. 4.16. Схема формирования производственных ячеек
15
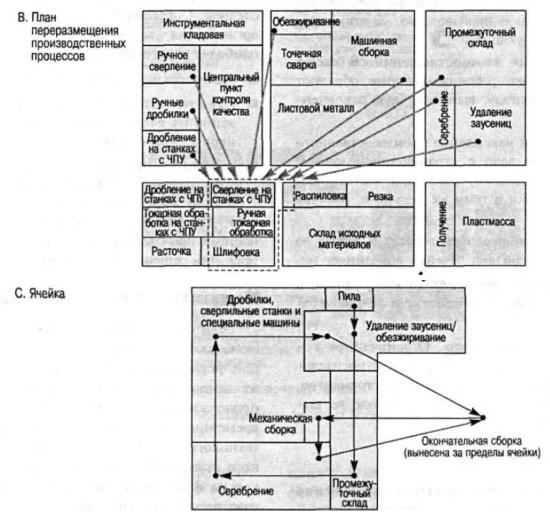
Рис. 4.16. Схема формирования производственных ячеек
На рис. 4.16 А показано исходное размещение, ориентированное на технологический процесс; на рис. 4.16 В показан план переразмещения технологических операций, основанный на общности этапов обработки компонентов изделия, объединенных в семейства; на рис. 4.16 С - размещение оборудования и операций в технологической ячейке, в которой выполняются все операции, за исключением последней.
4.3.4. Размещение оборудования по принципу обслуживания неподвижного объекта
Размещение оборудования по принципу обслуживания неподвижного объекта используется при относительно небольшом числе единиц выпускаемой продукции, но, как правило, крупногабаритной и сложной.
Разрабатывая размещение оборудования для производства неподвижного изделия, можно мысленно представить его в виде ступицы колеса с материалами и оборудованием, расположенными концентрически вокруг точки производства в порядке их использования и необходимости их перемещения. Например, в кораблестроении заклепки, использующиеся во всей конструк-
16
ции изделия, должны размещаться близко к корпусу или прямо в нем. Тяжелые части двигателя, подвозимые к корпусу только один раз, можно разместить на более далеком расстоянии, а подъемные краны, поскольку они постоянно используются, следует располагать рядом с корпусом.
Размещение оборудования и компонентов вокруг неподвижного объекта следует разрабатывать по принципу группирования материалов по их технологическому приоритету. Для организации производства неподвижного изделия необходимо установить очередность выполнения работ, которая определяется производственными стадиями.
4.4.Задача оптимизации внутренних перевозок в микрологистических системах
Внутренний транспорт (например, вилочные тележки или транспорте-
ры поддонов) играет особую роль в функционировании промышленного предприятия. Между цехами, ячейками складов и погрузочно-разгрузочными фронтами непрерывно перемещаются потоки материалов, комплектующих, полуфабрикатов и т.п., объемы которых в течение месяца могут составлять до нескольких десятков тысяч тонн. Этим определяется важность грамотной организации внутренних перевозок, скрывающей в значительные резервы экономии.
Корректные внутренние транспортные связи должны устанавливаться на этапе проектирования предприятия либо во время его модернизации (при изменении размещения производственных подразделений и складов).
Проектирование внутренних перевозок на предприятии - это сложный процесс, в котором выделяют техническую, организационную и экономическую составляющие. Оно должно быть объединено с проектированием предприятия как целого либо с его реструктуризацией (модернизацией).
Проектирование внутренних перевозок должно предваряться рядом предпроектных решений, важнейшими среди которых являются:
•расчет массы грузов, предназначенных для различных зон функционирования предприятия (на входе, в производственной сфере, в сбыте и т.д.);
•определение топологии размещения складов и производственных подразделений с расчетом длины маршрутов продвижения потоков;
•определение интенсивности потоковых процессов ( она может быть постоянной, переменной, случайной и определяться объемами и структурой производства или продаж);
•определение базового принципа транспортного обслуживания («вытягивание» или «проталкивание»). Например, либо склад сырья доставляет материалы на рабочие места, либо в роли организаторов снабжения производственной сферы выступают соответствующие структуры этой сферы;
•выбор централизованного или распределенного способа организации внутренних перевозок;
•выбор транспортных средств.
17
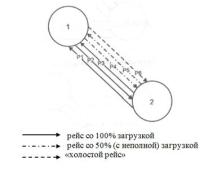
Внутренняя транспортировка подразделяется на непрерывную и дискретную. Непрерывная транспортировка характерна для отраслей с аппаратным характером технологического процесса (например, для химической или сахарной промышленности), этот выбор предопределяется технологией производства. В свою очередь, дискретная транспортировка чаще всего используется в упоминавшихся выше механосборочных отраслях; они характеризуются неравномерным поступлением и отпуском грузов.
В зависимости от размещения пунктов приемки и выдачи применяют одну из трех систем организации внутренних перевозок: Маятниковую, лучевую или кольцевую.
Маятниковую систему организуют в случае, если перевозка грузов между двумя пунктами направлена, как правило, только в одну сторону (обратный пробег чаще всего оказывается «холостым»).
Лучевая система связывает один пункт отправки (или получения) с несколькими пунктами получения (или отправки) и - так же, как и при маятниковой системе - характеризуется, как правило, «холостым» обратным пробегом.
Кольцевая система применяется для поддержания транспортных связей между несколькими пунктами, если эти пункты расположены вдоль непрерывной линии, а грузы последовательно доставляются в одном и том же направлении от первого до последнего пункта.
Пример [Скворонек и др.] :
В таблице ниже приведены данные о программе суточных внутренних перевозок между подразделениями на территории предприятия. Необходимо определить рациональный маршрут объезда этих пунктов, если известно, что для перевозки используются электрокары г/п 2 т.
Таблица 4.1 Программа суточных внутренних перевозок между подразделениями в т.:
Подразделения: |
1 |
2 |
3 |
1 |
0 |
3 |
3 |
2 |
5 |
0 |
3 |
3 |
4 |
4 |
0 |
При использовании маятниковой системы перевозок для решения задачи потребовалось бы 16 рейсов – рис. 4.17.
Рис. 17. Исходная маятниковая схема организации перевозок
18
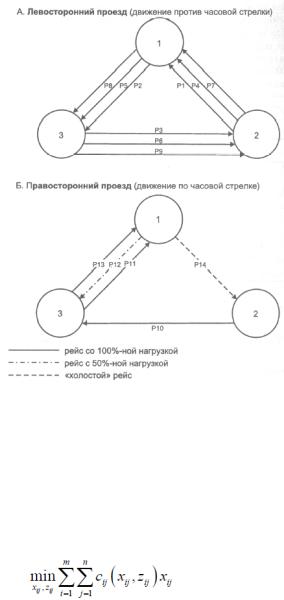
Например, для перевозки грузов между пунктами 2 и 1 будут необходимы 6 рейсов: 3 со 100 %-ной загрузкой, 2 с 50%-ной и один «холостой» пробег. Для организации перевозок между пунктами 2 и 3 потребуются 4 рейса (в том числе один с 50%-ной загрузкой), а между пунктами 1 и 3 - 6 рейсов (3 со 100%-ной 1, один с 50%-ной и два «холостых»). В результате имеем:
•9 рейсов со 100%-ной загрузкой;
•4 рейса с 50%-ной загрузкой;
•3 рейса с «холостым» пробегом.
Переход к кольцевой системе перевозок позволяет сократить количество рейсов до 14 – см. рис. 4.18.
Рис.4.18. Предложенная кольцевая схема организации перевозок
На практике используются специальные математические модели и программные средства для решения задачи оптимизации внутрипроизводственной транспортировки.
Математическая формулировка задачи оптимизации транспортной производственной системой может быть представлена следующим образом [Якубовская]:
, |
(4.4) |
где xij – количество ресурса, транспортируемого из пункта i в пункт j; zij – номер группы ТС, осуществляющих транспортировку из i в j;
cij – стоимость транспортировки единицы ресурса из i в j.
19

n |
m |
|
|
|
xij |
ai , г деi 1 m; xij |
bj , г де j 1 n; ai |
bj |
(4.5) |
j 1 |
i 1 |
i |
j |
|
D ={dкl} к, l =1…N – количество вершин в графе транспортной сети D;
dкl = dкl (xij , zij ) – стоимость транспортировки ресурсов xij группой zij из пункта k в пункт l транспортной сети
(4.6)
Pij ={i= кij (0)→lij (0) =кij (1) → кij (nij ) →lij (nij ) = j};
Tz = {tz1,…,tnzz }– z-ая группа ТС.
(4.7)
где g – ресурсоемкость.
(4.8)
Сначала решается подзадача определения оптимальных путей перемещения ресурсов, затем строится матрица затрат на транспортировку. На матрице затрат решается транспортная задача. Полученное решение транспортной задачи используется для формирования матрицы цен назначений. Наконец, на матрице цен назначений решается задача о назначениях. Решение задачи о назначениях является решением задачи оптимального оперативного управления ТПС. Это решение указывает, какая группа ТС должна осуществить заданную транспортировку. Таким образом, постановка задачи оптимизации ТПС сводится к ее декомпозиции, оптимизации отдельных задач и системы в целом – рис. 4.19.
Рис. 4.19. Структура задачи об оптимизации технологической транспортной системы
20