
- •ПРЕДИСЛОВИЕ
- •ГЛАВА 1. ВЫСОКОТЕМПЕРАТУРНАЯ ФИКСАЦИЯ АЗОТА
- •ХОЛОДИЛЬНЫЕ ЦИКЛЫ
- •Холодильный цикл среднего давления с расширением воздуха в детандере (цикл Клода)
- •ФИЗИКО-ХИМИЧЕСКИЕ ОСНОВЫ ПРОЦЕССОВ КОНВЕРСИИ ПРИРОДНОГО ГАЗА
- •РАВНОВЕСИЕ РЕАКЦИЙ КОНВЕРСИИ МЕТАНА ВОДЯНЫМ ПАРОМ
- •КАТАЛИЗАТОРЫ КОНВЕРСИИ МЕТАНА
- •Кинетика конверсии метана
- •КОНВЕРСИЯ ОКСИДА УГЛЕРОДА (II)
- •КАТАЛИЗАТОРЫ КОНВЕРСИИ ОКСИДА УГЛЕРОДА (II)
- •КИНЕТИКА КОНВЕРСИИ ОКСИДА УГЛЕРОДА (II)
- •ТЕХНОЛОГИЧЕСКИЕ СХЕМЫ КОНВЕРСИИ ПРИРОДНОГО ГАЗА
- •ОСНОВНОЕ ТЕХНОЛОГИЧЕСКОЕ ОБОРУДОВАНИЕ ПРОЦЕССОВ КОНВЕРСИИ ПРИРОДНОГО ГАЗА
- •Очистка газов от диоксида углерода водными растворами аминоспиртов
- •Очистка газов от диоксида углерода водными растворами карбонатов щелочных металлов
- •ОЧИСТКА КОНВЕРТИРОВАННОГО ГАЗА ОТ ОКСИДА УГЛЕРОДА (II)
- •РАВНОВЕСИЕ РЕАКЦИИ СИНТЕЗА АММИАКА
- •КАТАЛИЗАТОРЫ СИНТЕЗА АММИАКА
- •КИНЕТИКА СИНТЕЗА АММИАКА
- •ВЫДЕЛЕНИЕ АММИАКА ИЗ ПРОРЕАГИРОВАВШЕЙ АЗОТОВОДОРОДНОЙ СМЕСИ
- •ТЕХНОЛОГИЧЕСКИЕ СХЕМЫ СИНТЕЗА АММИАКА
- •ТЕХНОЛОГИЧЕСКОЕ ОБОРУДОВАНИЕ БЛОКА СИНТЕЗА АММИАКА
- •Теплообменная аппаратура
- •Аппаратура для выделения жидкого аммиака
- •Пути совершенствования схем синтеза аммиака
- •ГЛАВА 6. ПРОИЗВОДСТВО АЗОТНОЙ КИСЛОТЫ
- •ОКИСЛЕНИЕ АММИАКА
- •ОКИСЛЕНИЕ ОКСИДА АЗОТА (II)
- •ТЕХНОЛОГИЧЕСКИЕ СХЕМЫ ПОЛУЧЕНИЯ АЗОТНОЙ КИСЛОТЫ
- •ПРОИЗВОДСТВО КОНЦЕНТРИРОВАННОЙ АЗОТНОЙ КИСЛОТЫ
- •Прямой синтез концентрированной азотной кислоты
- •ГЛАВА 7. ПРОИЗВОДСТВО АЗОТНЫХ УДОБРЕНИЙ
- •ПРОИЗВОДСТВО СУЛЬФАТА АММОНИЯ
- •ПРОИЗВОДСТВО НИТРАТА АММОНИЯ
- •ПРОИЗВОДСТВО КАРБАМИДА
- •ТЕХНОЛОГИЧЕСКИЕ СХЕМЫ СИНТЕЗА КАРБАМИДА
- •ЖИДКИЕ АЗОТНЫЕ УДОБРЕНИЯ
- •ЛИТЕРАТУРА
- •ОГЛАВЛЕНИЕ

114 |
Глава 5 |
поступает аммиак из конденсационной колонны. За счет дросселирования жидкого аммиака с высокого давления до давления 20 · 105 Па происходит выделение растворенных в жидком аммиаке газов Н2, N2, Аг, СН4. Эти газы, называемые танковыми, содержат около 16% NН3. Утилизация аммиака из танковых газов производится путем его конденсации в испарителе 12 на линии танковых газов при температуре от –20 до –25°С.
Из испарителя танковые газы и сконденсировавшийся аммиак поступают в сепаратор 15, где жидкий аммиак отделяется
иподается в сборник 13. Для поддержания в циркуляционном газе содержания инертов в пределах 14–18% производят постоянный отбор части газа после первичной конденсации. Количество продувочных газов зависит от содержания инертных при-
месей в свежем газе, давления в системе синтеза, активности катализатора и колеблется в пределах 3–8 тыс. м3. Аммиак из продувочных газов выделяется при температуре (–25)–(–30)°С в конденсационной колонне 10 и испарителе 11. Смесь танковых
ипродувочных газов после выделения аммиака используют как топливный газ, для чего она направляется на сжигание в блок риформинга метана.
ТЕХНОЛОГИЧЕСКОЕ ОБОРУДОВАНИЕ БЛОКА СИНТЕЗА АММИАКА
В состав блока синтеза аммиака входит реакционная аппаратура (колонна синтеза), теплообменники, предназначенные для охлаждения прореагировавшей азотоводородной смеси с целью конденсации аммиака и нагревания циркуляционного газа до температуры зажигания катализатора, и сепараторы, предназначенные для отделения жидкого аммиака от непрореагировавшей азотоводородной смеси.
Колонна синтеза аммиака. Наиболее сложным и ответственным аппаратом в блоке синтеза аммиака является колонна синтеза. Она работает в очень жестких условиях – высокие давления (25– 35 МПа), высокие температуры (450–550°С) и агрессивная среда (наличие водорода). При высоких температурах водород может диффундировать внутрь стали и вызывать ее обезуглероживание, что может привести к уменьшению прочности стали и разрушению корпуса. Для того чтобы избежать этих явлений, необходимо

Синтез аммиака |
115 |
защитить корпус колонны синтеза от воздействия высоких температур. С этой целью внутри корпуса концентрически к нему располагается насадка, изготовленная из высоколегированной стали. Внутри насадки располагается встроенный теплообменник, предназначенный для нагревания циркуляционного газа до температуры зажигания катализатора, и катализаторная корзина, в которую загружается катализатор. Для защиты корпуса колонны синтеза от воздействия высоких температур циркуляционный газ из выносного газового теплообменника, имеющий температуру ~190–200°С, подается в колонну синтеза и движется по зазору между корпусом колонны синтеза и корпусом насадки к встроенному теплообменнику, где нагревается за счет тепла прореагировавшей смеси до температуры зажигания катализатора и подается на катализатор, где происходит реакция синтеза аммиака. Поэтому при разработке конструкции катализаторной корзины большое внимание уделяют обеспечению необходимого температурного режима в зоне катализатора. Оптимальная температура синтеза аммиака непостоянна и изменяется по мере протекания реакции. В начале процесса, когда концентрация аммиака в газовой смеси невелика, процесс выгоднее вести при высоких температурах, а по мере протекания реакции температуру необходимо снижать по линии оптимальных температур. Эту задачу можно решить только за счет отвода теплоты реакции синтеза путем охлаждения газовой смеси. В промышленных условиях отвод тепла из зоны катализа осуществляют по-разному, применяя различные конструкции насадок. Наибольшее применение в промышленности получили колонны с трубчатой или полочной насадкой. В колоннах с трубчатой насадкой катализатор загружают в один слой, а для отвода тепла в слое катализатора располагают теплоотводящие трубки, через них проходит холодный циркуляционный газ, который нагревается до температуры зажигания катализатора и подается на катализатор. В этом случае отвод тепла осуществляется непрерывно. В колоннах с полочной насадкой катализатор располагают на нескольких полках, а отвод тепла осуществляют дискретно путем охлаждения газовой смеси после каждого слоя катализатора.
В современных крупнотоннажных агрегатах синтеза аммиака наибольшее применение получили колонны с полочной насадкой. С целью большего приближения температурного режима к оптимальному используются колонны синтеза с четырьмя полками.
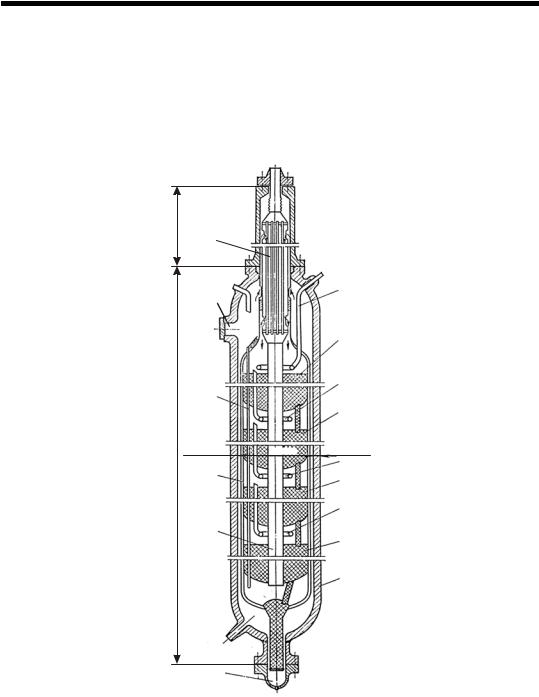
116 |
Глава 5 |
Охлаждение газовой смеси после каждого слоя катализатора осуществляется путем ввода холодного байпасного газа в количествах, необходимых для заданного снижения температуры. Конструкция четырехполочной колонны синтеза аксиального типа представлена на рис. 20.
6600
22 300
6
5
4
24 000
3
2
1
7
8
9
10
250
11
12
13
14
15
Рис. 20. Четырехполочная колонна синтеза аммиака:
1 – люк для выгрузки катализатора; 2 – центральная труба; 3 – корпус катализаторной коробки; 4 – термопарный чехол; 5 – загрузочный люк; 6 – теплообменник; 7 – ввод байпасного газа на первую полку;
8 – I катализаторный слой; 9 – ввод байпасного газа на вторую полку; 10 – II катализаторный слой; 11 – ввод байпасного газа на третью полку; 12 – III катализаторный слой; 13 – ввод байпасного газа на четвертую полку; 14 – IV катализаторный слой; 15 – корпус колонны

Синтез аммиака |
117 |
Основной поток газа поступает в колонну снизу, проходит по кольцевой щели между корпусом колонны и кожухом насадки и поступает в межтрубное пространство теплообменника. Здесь синтез-газ нагревается теплом конвертированного газа, выходящего из катализаторной коробки, до 410–440°С и затем последовательно проходит четыре полки катализатора, между которыми подается холодный байпасный газ. Пройдя четвертый слой катализатора, азотоводородная смесь при 500–515°С поднимается по центральной трубе, проходит по трубкам теплообменника, охлаждаясь при этом до 320–350°С, и выходит из колонны. При пуске колонны катализатор разогревают при помощи выносного газового подогревателя. Техническая характеристика четырехполочной колонны синтеза аммиака агрегата мощностью 1360 т/сут приведена ниже:
–давление – 31,5 МПа;
–рабочая температура – 300–520°С;
–диаметр (внутренний) – 2400 мм;
–высота – 32 м;
–толщина стенки – 250 мм;
–объем катализатора по полкам I–IV соответственно – 7; 8,4; 12,8; 14,7 м3;
–параметры встроенного теплообменника:
а) диаметр поковки (внутренний) – 1000 мм; б) высота – 6 м; в) размер трубок – 12×1,5 мм;
г) число трубок – 1920.
Температурный режим работы колонны по полкам представлен на рис. 21. На этом же рисунке показана концентрация аммиака в газовой смеси на входе и выходе в каждом слое.
При загрузке катализатора в колонну синтеза необходимо решить противоречие, связанное с выбором размера зерен катализатора. Крупнозернистый катализатор при его применении не может быть полностью использован, так как внутренняя часть зерен катализатора практически не работает.
Применение мелкозернистого катализатора позволяет почти полностью использовать его активность, однако гидравлическое сопротивление слоя катализатора резко возрастает. Чтобы сгладить эти противоречия в крупнотоннажных агрегатах, проводят дифференцированную загрузку катализатора – на первый и второй
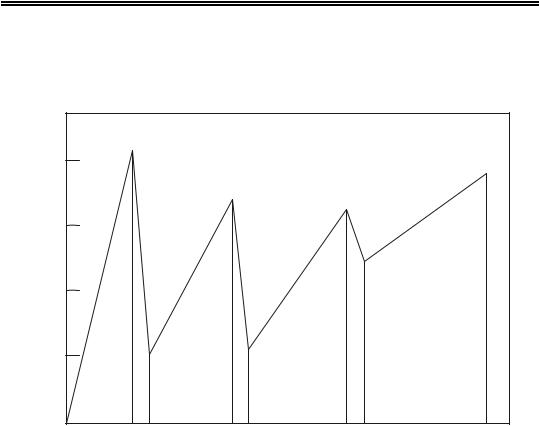
118 |
|
|
Глава 5 |
|
слои загружают катализатор с размером зерен 5–7 мм, на третий |
||||
слой – катализатор с размером зерен 7–10 мм, а на четвертый – |
||||
смесь с размером зерен 7–10 мм и 10–15 мм в разных объемах. |
||||
t, C |
|
|
|
|
|
|
522 |
|
515 |
520 |
|
9,21% |
|
|
|
|
15,25% |
||
|
|
|
507 |
|
|
|
|
505 |
|
|
|
|
11,58% |
|
|
|
|
13,68% |
|
500 |
|
|
|
|
|
|
|
|
|
|
|
|
|
488 |
480 |
|
|
|
13,13% |
|
I |
II |
III |
IV |
460 |
|
460 |
460 |
|
|
|
10,43% |
|
|
|
|
8,16% |
|
|
|
|
|
|
|
440 |
7,1 м3 |
8,4 м3 |
12,8 м3 |
14,7 м3 |
|
V |
= 43 м3 |
V |
|
|
|
|||
|
|
кат |
|
кат |
|
Рис. 21. Температурный режим четырехполочной |
|||
|
|
колонны синтеза аммиака |
Однако кардинальным решением проблемы уменьшения гидравлического сопротивления слоя катализатора является применение радиальных колонн синтеза аммиака. Одна из возможных конструкций такой колонны представлена на рис. 22.
В этой колонне холодный циркуляционный газ из выносного теплообменника с температурой ~200°С поступает в верхнюю часть колонны и движется вниз по зазору между корпусом колонны синтеза и корпусом насадки.
Затем газ поступает в межтрубное пространство встроенного теплообменника, нагревается до температуры зажигания катализатора и затем по центральной трубе направляется в катализаторную корзину, разделенную на два слоя. В верхнем слое центральная труба перфорирована. Наружный корпус катализаторной корзины также перфорирован. Поэтому в верхнем слое катализатора газ движется перпендикулярно оси колонны от центральной трубы к наружному корпусу.
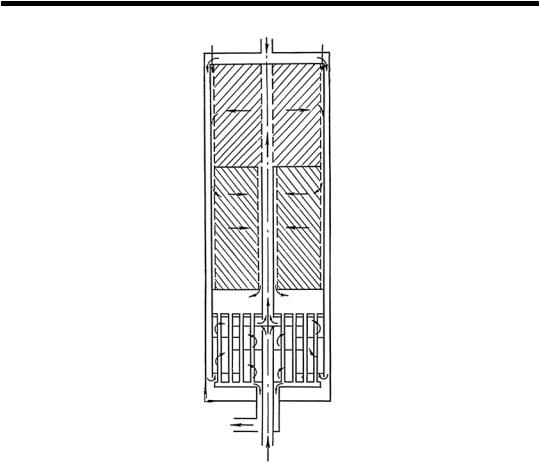
Синтез аммиака |
119 |
ХБ Газ ХБ
Газ
Рис. 22. Схема двухполочной радиальной колонны
В нижнем слое направление движения газа изменяется на противоположное. При этом для понижения температуры после первого слоя катализатора добавляют холодный байпасный газ. Пройдя через оба слоя катализатора, газовая смесь поступает в трубное пространство встроенного теплообменника, где нагревает циркуляционный газ, охлаждается до температуры 300–338°С и направляется на выделение аммиака. Основным преимуществом радиальных колонн синтеза перед аксиальными является уменьшение гидравлического сопротивления катализатора, так как толщина слоя катализатора не превышает 1 м. Это позволяет загружать в колонну синтеза мелкозернистый катализатор с размером зерен 1–3 мм и полностью использовать его активность, благодаря чему уменьшается давление синтеза аммиака, увеличиваются объемная скорость и удельная производительность катализатора. Поэтому радиальные колонны синтеза получают все большее применение.