
Основы проектирования электронных средств Материалы к Экз ОПЭС-2014 РК-01-02 / Назаров_Конструирование_РЭС
.pdfИз приведенных в табл. 10.1 металлических покрытий наибольшей температурной стабильностью обладает хромовое (тускнеет при 500°С); золотое покрытие не взаимодействует с кислотными, щелочными и сернистыми соединениями, но очень мягкое и легкое, подвергается износу и истиранию. В ряде случаев защитное покрытие делают многослойным, например: слой меди, толщиной 6...10 мкм (высокая адгезия к стали), слой никеля толщиной 3...6 мкм (высокая твердость), слой хрома толщиной 0,5 мкм (антифрикционность).
Пленочные покрытия образуют на поверхности материала тонкий и непрерывный слой лака. Они защищают материалы от проникновения в его поры влаги, увеличивают прочность изоляции. При пропитке или покрытии деталей используют изоляционные лаки УР-231, СБ-1С; перхлорвиниловые эмали ХВ-125; пентафталевые эмали ПФ-115, МФ-28, ПФ-223; эпоксидные эмали Э-5, Э-11; нитроцеллюлозные эмали НЦ-11; ЭМ-508, НЦ-25; кремнийорганические эмали ЭМ-9, ЭМК-2, ЭМКО-81 и компаунды МБК, ЭЗК, ФК-20, УТ-31. Пленочному покрытию изоляционными лаками и эмалями подвергаются многие функциональные узлы печатного монтажа, микросхемы и микросборки. Пропитке также подвергаются детали, изготовляемые из гигроскопичных, пористых или волокнистых материалов, а также различные моточные изделия.
Применяемые лаки, эмали, компаунды, эпоксидные смолы разрабатывались, в первую очередь, для защиты от коррозии, создания лакокрасочных и декоративных покрытий, а также для пропитки, заливки, склеивания и т.д. К недостаткам органических полимерных материалов относится ухудшение электрических и механических свойств при длительном воздействии повышенных температур и их резком изменении.
В настоящее время применяются комбинированные пассивационнозащитные покрытия из тонкой пленки неорганического диэлектрика и органического полимерного покрытия. Назначение тонкой пленки диэлектрика, например слоя Si О 2, — нейтрализовать активные центры и в
определенной мере стабилизировать свойства поверхности. Относительно толстый слой полимерного покрытия предотвращает механическое повреждение пленки неорганического диэлектрика, защищает его поверхность от воздействия внешней атмосферы.
В качестве пропиточных, заливочных и обволакивающих материалов широкое распространение получили компаунды на основе эпоксидных смол ЭД-5 и ЭД-6. Компаунды ЭПК-1 и ЭПК-4 применяют для пропитки, компаунды ЭЗК-1, ЭЗК-4, ..., ЭЗК-12, ЭК-20 — для заливки деталей и узлов.
Пенополиуретан ЖК-2 применяют, когда требуется обеспечить теплоизоляцию изделий при сохранении малой массы. Его достоинством является высокая адгезия к большинству материалов.
361
Широкое распространение получили пластичные компаунды и герметики ВГП-2П, ВГО-1, СКТН-1, виксинты У-1-18, У-2-28, К-18, ПК68.
Недостатком этих компаундов и герметиков на каучуковой основе является их недостаточная адгезионная способность к металлам и различным материалам.
10.4. Герметизация корпусов микросхем и РЭС
Корпусная герметизация обычно предусматривает окончательную защиту от климатических и радиационных воздействий, оговоренных в ТУ на изделме. Корпуса изготавливаются на основе не сорбирующих влагу неорганических материалов (металла, стекла, керамики). Проходная арматура (выводы, теплоотводы), а также герметизация мест соединения отдельных деталей в них должны быть вакуумно-плотными, поэтому подобные корпуса относятся к категории вакуумно-плотных. Для интегральных схем корпуса подразделяются на металлические, металлостеклянные, стеклянные, металлокерамические и керамические.
Плоские корпуса ИС выполняют в двух основных конструктивных вариантах: со штыревыми и планарными выводами, расположенными обычно по противоположным сторонам корпуса.
Герметизация обеспечивает вакуумно-плотное соединение выводов корпуса с его основанием или стенкой, изолирование выводов от металлических частей корпуса и собственно герметизацию корпуса, которая производится после сборки и монтажа изделия и состоит обычно в создании вакуумно-плотного шва.
В керамических корпусах герметизация выводов осуществляется стеклоэмалью или стеклоприпоем. Узел «вывод — тело корпуса» (гермоввод) является критичным у всех корпусов, так как механические нагрузки на выводы при монтаже корпусов могут привести к потере герметичности узла. Некоторые конструкции герметичных выводов представлены на рис. 10.1. Видно, что оптимальной является конструкция керамического корпуса, внешние выводы которого устанавливаются вне герметизированного объема (рис. 10.1,а).
Герметизация стеклянных и керамических (рис. 10.1, б) корпусов производится металлизацией узлов корпуса по месту соприкосновения с последующей пайкой. Широкое распространение получила герметизация стеклянных корпусов бесфлюсовой пайкой низкотемпературными припоями. Существует герметизация керамических корпусов с помощью приклейки крышки корпуса к рамке органическими полимерными клеями.
Герметизация металлостеклянных корпусов обычно осуществляется сваркой плавлением, контактной сваркой, иногда пайкой мягкими
362

\
Рис.10.1.Конструкциигерметичныхвыводовкорпусов:
а, б — керамические; в, г — металлостеклянные; / — припаянная крышка (ковар); 2 —слой металла; 3 — керамическое кольцо;
4 — вывод (ковар); 5 — основание (керамика); б — крышка (керамика); 7 — слой металла или клеевой шов; 8 — крышка (нержавеющая сталь, ковар);
9 —изолятор (стекло); 10 — основание (ковар); // — кольцо (ковар)
припоями. Примеры конструкций стеклянных корпусов
приведены |
на |
рис. 10.1, в, |
г. |
Высокий уровень герметичности корпусов допускает повышение надежности изделий за счет заполнения внутреннего объема корпусов разными материалами. Так, часто корпуса заполняют инертными газами (например, аргоном) для исключения из объема влаги и предотвращения окислительных процессов, жидкими веществами или вазелинами;часто внутри корпуса помещают геттеры для регулирования влажности среды в корпусе.
Герметизация вывода корпуса блока осуществляется путем спая ковара со стеклом. В блоках могут быть использованы гермовводы, представляющие либо одиночный металлостеклянный вывод (рис. 10.2), либо групповую колодку выводов, впаянную в корпус блока (рис. 10.3).
Рис. 10.2. Конструкция одиночного ме- |
Рис. 10.3. Вариант установки |
таллостеклянногогермоввода: |
гермопереходниковвкорпус |
1 — оболочка из ковара; 2 — проволока |
блока: / — корпус; 2 — про- |
из ковара; 3 — стеклянный изолятор |
волока из ковара; 3 —припой |
|
ПОС-61; 4 — оболочка из ко- |
|
вара |
|
363 |

Герметизация корпусов РЭС может быть выполнена сваркой, пайкой или с помощью эластичных уплотнений. Первые два способа герметизации используются в случае жестких требований к герметичности блоков, состоящих из негерметизированных ячеек. Высокую технологичность имеет вакуумно-плотная герметизация корпусов блоков пая-
ным швом по всему периметру корпуса (см. разд. 3). |
|
|
||||
|
При разъемном способе герметиза- |
|||||
|
ции в паз кожуха или корпуса изделия |
|||||
|
укладывается прокладка, которая при |
|||||
|
поджатии уплотняет стык между кожу- |
|||||
|
хом и корпусом (рис. 10.4). Уплотни- |
|||||
|
тельная прокладка, равномерно поджи- |
|||||
|
маясь по всей поверхности крепежными |
|||||
|
винтами, осуществляет герметизацию, |
|||||
|
находясь в сжатом состоянии и заполняя |
|||||
|
все сечения паза. Утечка газов через уп- |
|||||
Рис. 10.4. Герметизация блока |
лотнение |
при |
сжатии |
прокладки на |
||
уплотнительнойпрокладкой: |
25...30% от ее первоначальной высоты |
|||||
/ — корпус; 2 — кожух; |
происходит |
только |
за |
счет |
диффузии. |
|
3 — прокладка |
Большие усилия |
при |
сжатии |
не рекомен- |
||
|
дуются, поскольку из-за интенсивного старения прокладка быстро выходит из строя.
Форма поперечного сечения прокладки может быть различной. Наиболее распространены прокладки сечений, показанные на рис. 10.5, а, б,
в,
так как они просты в изготовлении и выдерживают широкий диапазон давлений. Гребенчатая прокладка (рис. 10.5, г) используется в аппаратуре с большим сроком службы.
Рис. 10.5. Формы сечений уплотнительных прокладок
В качестве материала прокладбк используется резина, обладающая высокой эластичностью, податливостью и способностью затекать в мельчайшие углубления и неровности. Для уплотнительных прокладок можно применять следующие марки резины: ИРП-1267, ИРП-1338, ИРП-1354. Перед сборкой прокладка смазывается тонким слоем масла ЦИАТИМ-221.
364
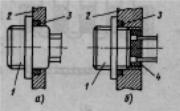
Ширина фланца определяется по формуле bФЛ = 2δст + 2,6dкв,
где δст — толщина стенки корпуса; d к в — диаметр крепежного винта.
Площадь сечения прокладки 5 вычисляется из выражения
Sпр = (1,1...1,2)Sп )
где S п — площадь сечения паза.
При расчете герметизации определяется усилие обжатия прокладки, на основе которого вычисляются усилие затягивания и количество крепежных винтов.
Герметизация внешних электрических связей РЭС осуществляется с помощью металлостеклянных гермовводов, впаиваемых в стенку блока, опайкой соединителей (например, высокочастотных) по периметру, полимерной герметизацией низкочастотных соединителей. Электрические соединители герметизируются уста-
новкой на прокладки (рис. 10.6, а), залив- |
Рис. 10.6. Герметизация соеди- |
|
кой компаундами (рис 10.6, б). |
|
нителя спомощью уплотнитель- |
|
ной прокладки (а), уплотни- |
|
Надо отметить, что уплотнительными |
компаундом (б): 1 — соедини- |
|
прокладками, устанавливаемыми в круп- |
тельной прокладки и заливки |
|
тель; 2 — корпус; 3 — проклад- |
||
ных приборных корпусах, трудно |
обеспе- |
ка; 4 — компаунд |
чить абсолютную герметичность. |
Однако |
|
они в достаточной мере предохраняют внутреннюю полость прибора от влажного воздуха или воды, обеспечивая более благоприятные условия работы изделий во влажной среде, особенно если при этом в приборах используют средства осушения. Наиболее эффективным способом осушки внутренней полости изделия в период эксплуатации является использование влагопоглотителей. Широкое применение получил силикагель, который в размельченном виде помещают в патроны, футляры или мешочки, устанавливаемые внутри изделия. Осушительный патрон предусматривает замену силикагеля при полном насыщении его влагой. Контроль за влагонасыщением силикагелем производится по изменению его цвета. Для этого силикагель окрашивают 3%-м водным раствором хлористого кобальта, тогда при полном насыщении влагой он принимает розовый цвет, а после просушки — синий.
Капсулирование широко используется для герметизации элементной базы и функциональных ячеек РЭС. В зависимости от особенно-
365

стей конструкции изделий, в частности расположения выводов, существуют два вида корпусов с использованием металлической капсулы:
свертикальным расположением выводов (рис. 10.7, а) — в этом случае поверхность изделия контактирует с герметизирующим компаундом;
свыводами в одной плоскости с подложкой (рис. 10.7, б, в) — в этом случае герметизирующий материал не контактирует с поверхностью изделия.
Рис. 10.7. Примеры герметизации способом капсулирования: а — изделие со штыревыми выводами; б — односторонний пенальный корпус; в — двухсторонний; 1 — капсула; 2 — подложка; 3 — герметизирующий компаунд; 4 — вывод; 5 — прокладка
Наиболее широкое распространение получили корпуса первого вида [60], где надежная герметизация изделий определяется герметичностью узлов «вывод — компаунд (подложка)» и «капсула — компаунд», а также адгезией компаунда к поверхности платы. При герметизации капсулированием изделие помещается в корпус (капсулу) выводами наружу. Свободный торец капсулы и выводы заливаются компаундом. Для герметизации изделий микроэлектроники в металлополимерные корпуса наибольшее распространение получил жидкий компаунд ЭК-16. Однако он недостаточно пригоден для организации автоматизированного производства малогабаритных изделий. Это объясняется трудностью дозировки больших порций компаунда, низкой жизнеспособностью компаунда. Эффективнее применять порошкообразные компаунды. В этом случае появляется возможность осуществлять предварительную дозировку компаунда путем изготовления из него калиброванных по массе и размерам таблеток. Герметизация порошкообразными компаундами в виде таблеток позволяет автоматизировать процесс сборки и герметизации изделий.
366

ПРИЛОЖЕНИЯ
Таблица П.1
Формулы расчета осевых моментов инерции простейших сечений
367

|
Физические параметры некоторых |
|
Таблица |
||||||
|
|
П.2 |
|||||||
|
материалов |
|
|
|
|
|
|
||
|
|
|
|
|
|
|
|
||
|
|
|
|
|
Параметры материала |
||||
Материал |
Плотнос |
|
Модуль |
|
Коэффиц |
|
Предел |
|
Коэффици- |
|
|
|
|
||||||
|
|
и- |
|
прочнос |
|
ент |
|||
|
ть 3 |
|
упругост |
|
ент |
|
ти |
|
демпфи- |
|
|
и |
|
Пуассона |
|
при |
|
||
|
р, г/см |
|
Е 10"', Па |
|
|
изгибе |
|
рования |
|
|
|
|
|
Е |
|
а -КГ6, |
|
So |
|
1 |
2 |
|
3 |
|
4 |
|
5 |
|
6 |
Сплавы |
|
|
|
|
|
|
|
|
|
алюмини |
2,8 |
|
71 |
|
|
|
410 |
|
0,05...0,013 |
я: |
|
|
0,29 |
|
|
||||
щ, |
2,76 |
|
71 |
|
|
520 |
|
|
|
2,85 |
|
71 |
|
0,29 |
|
560 |
|
|
|
Д16, |
2,73 |
|
71 |
|
0,29 |
|
520 |
|
|
В95, |
2,65 |
|
71 |
|
0,29 |
|
180 |
|
0,004...0,00 |
АМц, |
2,65 |
|
72 |
|
0,29 |
|
200 |
|
|
АЛ2, |
2,71 |
|
69,6 |
|
|
|
58 |
|
|
АЛ9, |
|
|
|
|
|
|
|
|
|
АД1 |
|
|
|
|
|
|
|
|
85 |
Сплавы |
4,4...4,9 |
|
105 |
|
0,25...0,3 |
|
950 |
|
|
титана: |
|
|
|
|
3 |
|
|
|
|
ВТ 1-0, ВТЗ |
|
|
|
|
|
|
|
|
|
Сплавы |
1,48 |
|
45 |
|
|
|
180 |
|
0,0063...0,0 |
магниевые: |
|
|
|
|
|
||||
МА18, |
1,8 |
|
46 |
|
|
|
280 |
|
125 |
МА2-1 |
|
|
|
|
|
|
|
|
|
29НК (ковар) |
8,35 |
|
145 |
|
|
|
480 |
|
|
Сталь 20, Сталь |
7,82 |
|
200 |
|
0,25 |
|
420...61 |
|
|
ЗОХГСА |
7,85 |
|
198 |
|
0,36 |
|
1080 |
|
|
Бронза |
8,27 |
|
75...141 |
|
0,31 |
|
200... |
|
|
Латунь |
8,5 |
|
106...110 |
|
0,41 |
|
320.. |
|
0,03...0,06 |
Ситалл СТ50-1 |
2,65 |
|
180 |
|
0,26 |
|
176 |
|
|
Керамика 22ХС |
3,86 |
|
255 |
|
0,26 |
|
85 |
|
|
Брокерит-9 |
2,83 |
|
320 |
|
|
|
100 |
|
|
Поликор |
3,98 |
|
392 |
|
0,26 |
|
200 |
|
|
Фторопласт-4 |
2,25 |
|
0,47...0,85 |
|
22 |
|
|
|
0,02...0, |
Стеклотекстол |
|
|
|
|
|
|
|
|
|
ит: |
1,85 |
|
30,2 |
|
0,22 |
|
75 |
|
1 |
СФ, |
|
|
|
|
0,02...0, |
||||
СТЭФ |
2,47 |
|
32 |
|
0,279 |
|
75 |
|
1 |
Гетинакс |
1,4 |
|
|
|
11. ..14 |
|
|
|
0,03...0,08 |
368
Таблица П.З Коэффициенты теплопроводности наиболее часто применяемых материалов
|
Наименованиематериала |
X , Вт/(м К) |
|
|
|
1, Алюминиевые сплавы |
160...180 |
|
2. Брокеритовая керамика |
180...200 |
|
3. Воздух |
0,025 |
|
|
|
|
4. Германий |
52...5S |
|
|
|
|
5. Гетинакс |
0,15...1,18 |
|
б. Кремний |
120...130 |
|
7. Ковар Н29К18 |
21 |
|
8. Керамика 22ХС |
18...20 |
|
9. Латунь |
100...200 |
|
10. |
Магниевые сплавы |
120...127 |
11. Медь |
380...390 |
|
|
|
|
12. Олово |
64 |
|
13. Пенопласт |
0,04...0,06 |
|
|
|
|
14. Резина |
0,11-0,16 |
|
15. |
Ситалл СТ - 50 - 1 |
1,1. ..1,6 |
16. |
Стекло кварцевое |
1,4.. .1,5 |
|
|
|
17. |
Сталь конструкционная |
45...50 |
18. |
Слюда |
0,43.. .0,6 |
19. Стеклотекстолит |
ОД7...1.18 |
|
20. Титановые сплавы |
14.. .16 |
|
21. Клеи и компаунды |
0.15..ДЗ |
|
22. Поликор |
25...38 |
|
|
|
|
369
Степень черноты различных поверхностей |
Таблица П.4 |
|
|
||
|
|
|
Материал и состояние поверхности |
Температура, ° С |
Степень черноты |
|
|
|
Алюминий (полированная пластина) |
200...600 |
0,04...0,0б |
|
|
|
Алюминий (сильно окислен) |
35...500 |
0,2...0,31 |
|
|
|
Силуминовое литье (в песчаной форме) |
100...500 |
0,33...0,31 |
|
|
|
Силуминовое литье (в кокильной форме) |
100...500 |
0,16...0,23 |
|
|
|
Дюралюминий Д16 |
50...350 |
0,37...0,41 |
|
|
|
Сталь полированная |
100 |
0,066 |
Сталь листовая холоднокатаная |
93 |
0,075...0,085 |
Сталь листовая сильно окисленная |
25 |
0,8...0,82 |
Латунь прокатанная |
22 |
0,06 |
Латунь тусклая |
50...350 |
Of,22 |
|
|
|
Латунь хромированная полированная |
100 |
0,075 |
Медь шабренная до блеска |
22 |
0,072 |
Медь (пластина после нагрева до 600° С) |
200 |
0,57 |
Олово, луженое кровельное железо |
100 |
0,07...0,08 |
Цинк, оцинкованное железо |
25 |
0,23...0,27 |
Краски эмалевые, лаки различных цветов |
20... 100 |
0,92 |
|
|
|
Краски матовые различных цветов |
100 |
0,92...0,96 |
Лак черный матовый |
40... 100 |
0,96...0,98 |
|
|
|
Муар серый, черный |
20 |
0.86...0.9 |
Краска защитно-зеленая |
20 |
0,9 |
Краска бронзовая |
100 |
0,51 |
Краска алюминиевая |
100 |
0,28 |
Алюминиевая фольга |
100 |
0,09 |
|
|
|
370