
книги / Металлы и сплавы. Анализ и исследование. Физико-аналитические методы исследования металлов и сплавов. Неметаллические включения
.pdf
ческого упрочнения. Схема оценки качества изго товленной металлопродукции должна содержать следующие этапы:
•выявление и классификацию технологиче ских дефектов макроскопического масштаба;
•исследование макро- и микроструктуры ме талла;
•обнаружение неметаллических включений, анализ их расположения на представительных пробах макро- и микростроения;
•классификацию включений с определением вида, механических свойств, химического состава
иструктуры;
•определение концентрации газов в металле (азота, кислорода);
•сопоставление полученных результатов и анализ технологических факторов;
•выработку рекомендаций по оптимизации технологии получения металла и обработки полу фабриката;
•проверку и уточнение выработанных реко
мендаций.
В зависимости от нормируемых параметров и технических условий на каждой ступени исследо вания определяется возможная причина образования технологического дефекта. В табл. 4.4 приведены некоторые отличительные признаки дефектов в прокате легированных сталей, идентификация ко торых затруднительна.
Встречаются и другие технологические дефек ты, связанные с наличием неметаллических вклю чений: волосовины, пузыри-вздутия и расслои (табл. 4.5).
Таблица 4.4
Характеристика дефектов в прокате легированных сталей, связанных с химическим составом и наличием неметаллических включений
Класс сталей |
Характерные признаки технологического дефекта |
Технологические |
||||
Внешний вид |
|
|
Химический |
|||
Макроструктура |
Микроструктура |
факторы |
||||
|
проката |
состав |
||||
|
|
|
|
|||
|
|
Раскатанные пузыри |
|
|
||
Все стали |
|
СХЗ С Э |
|
|
||
Продольные тон |
Вышедшие на |
Дефект заполнен |
Высокое содер |
Повышенное |
||
|
кие нарушения |
поверхность |
окалиной и не |
жание азота и |
содержание га |
|
|
сплошности, рас |
пузыри сопро |
металлическими |
водорода |
зов, в том числе |
|
|
положенные бес |
вождаются |
включениями, |
|
из-за попадания |
|
|
порядочно по пе |
подкорковой и |
расположен пер |
|
влаги |
|
|
риметру проката |
более глубокой |
пендикулярно к |
|
|
|
|
|
газовой порис |
поверхности |
|
|
|
|
|
тостью |
|
|
|
|
|
|
Раскатанные трещины |
|
|
||
|
|
б э а э |
|
|
||
Перлитные |
Протяженные де |
Раскрытые тре |
Вокруг трещин |
Содержание азо |
Перепад темпе |
|
стали с мелко |
фекты, ориентиро |
щины незначи |
неметаллические |
та и алюминия |
ратур в слитке, |
|
зернистой |
ванные вдоль на |
тельной (1-2 мм') |
включения от |
выше оптималь |
заниженные |
|
структурой в |
правления прокат |
глубины |
сутствуют |
ного |
температуры в |
|
литом состоя |
ки, расположены |
|
|
|
обжимном стане |
|
нии |
на образующих |
|
|
|
|
|
(С > 0,35 %) |
поверхностях |
|
|
|
|


данные о размерах, морфологии, распределении и пластической деформируемости частиц, видимых в окуляре светового микроскопа.
Неметаллические частицы в сталях могут иметь размеры от дисперсных и неразличимых в поле зрения светового микроскопа до крупных, обна руживаемых невооруженным глазом и имеющих протяженность в несколько десятков миллимет ров. Поэтому принято различать макровключения размером более 1 мм и микровключения величи ной менее 1 мм. Наиболее достоверным методом обнаружения макровключений или скоплений включений средних размеров, расположенных в слитках на различной высоте, является ультразву ковой контроль прокатанной или прокованной за готовки по всей длине. Метод позволяет обнару жить дефекты размером 1 мм и более.
Методы определения загрязненности металла макро- и микровключениями различны. Выбор метода оценки зависит от цели исследования. Так, для определения степени загрязненности включе ниями макроскопических размеров пользуются ГОСТ 3763, который предусматривает применение специальных методов испытаний: на «синий» из лом, ступенчатой машинной обработки и магнит ной дефектоскопии. В этом стандарте параметра ми, характеризующими наличие неметаллических частиц, являются общее количество и длина или ширина включений, которые не разделяются по структурным типам.
Сущность метода испытаний на «синий» излом
состоит в определении общего количества и рас пределения неметаллических включений, видимых на поверхности продольного излома, нагретого до определенной температуры, и вызывающих синий цвет побежалости. Включения имеют вид белых строчек. Для проведения этого испытания от изде лия отрезают образец толщиной 10 мм. Способ вырезки может быть любой, но важно, чтобы об разец находился вне зоны возможного термиче ского влияния. Далее на одной из сторон в середине образца перпендикулярно его оси делается надрез, форма и глубина которого не регламентируются. Затем образец нагревается до температуры 750— 950 °С, при которой некоторое время выдержива ется, а затем остужается на воздухе до температу ры «синеломкости» (300-350 °С), при которой ис пытывается динамическим изгибом. Полученный излом осматривают невооруженным глазом или
спомощью увеличительного стекла (увеличение до х10). Обнаруженные включения сравниваются
сизображениями эталонных шкал, имеющихся в стандарте, или оцениваются подсчетом числа и измерением длин (толщин). Метод прост, но его недостаток заключается в том, что ферритные по лосы и карбидные строчечные включения могут быть приняты за неметаллические включения.
Метод ступенчатой машинной обработки
предполагает обнаружение и оценку количества неметаллических частиц, видимых на продольных поверхностях цилиндрического образца, подверг нутого последовательной механической обточке. Количество образцов и их расположение в полу фабрикатах (прутках и болванках) стандартом ГОСТ 3763 не регламентируются. Обычно обра зец, предназначенный для испытаний, содержит три уступа такой длины и диаметра, чтобы пло щадь поверхности всех уступов была одинаковой. После машинной обработки поверхность должна быть чистой и ровной без резко выраженного рельефа. Ее осматривают невооруженным глазом или с помощью увеличительного стекла (с увели чением до х10). Обнаруженные включения отме чают, подсчитывают и измеряют на каждом уступе. Недостаток машинной обработки состоит в том, что помимо неметаллических включений этим ме тодом могут быть выявлены трещины, расслои, усадочные раковины и другие макроскопические технологические дефекты.
Способ магнитной дефектоскопии применим для анализа только ферромагнитных сталей. Ме тод заключается в осмотре поверхности образца после ее обработки на станке и покрытия жидко стью, которая содержит суспензию ферромагнит ного порошка. При воздействии приложенного магнитного поля неметаллические включения, внося искажения в форму и параметры силовых линий, притягивают к себе частицы ферромагнит ного порошка и удерживают их. За счет этого про изводится визуальная индикация местоположения включений. Отбор, количество и расположение образцов требованиями стандарта не оговарива ются. Контролируемая поверхность шлифуется в направлении, перпендикулярном направлению прокатки, дабы избежать механического «вырыва ния» включений. Магнитная жидкость готовится из расчета 5—10 г магнитного порошка, состоящего из оксида железа с частицами размером 0,5-1 мкм,
на 1л воды с антикоррозионными добавками или керосина. Допускается использование и прозрач ного светлого минерального масла. Метод намаг ничивания предполагает прямое пропускание тока плотностью до 200 А/см2 через образец с после дующим нанесением магнитной жидкости. После этого просушенную поверхность рассматривают в лучах белого (с компонентой ультрафиолета) света. Для документации выявленных неметалли ческих включений используют липкую прозрач ную ленту, которую прижимают липкой стороной к месту расположения неметаллических включе ний и частиц порошка. Эту процедуру выполняют, не выключая ток, чтобы исключить изменения магнитного поля. Дальнейшая оценка чистоты ме талла по содержанию неметаллических включений производится аналогично методу ступенчатой машинной обработки.
Определение методами металлографии степени загрязненности сталей и сплавов микровключе ниями регламентировано стандартами* ГОСТ 1778 (для металлоконструкций) и ГОСТ 801 (для инст рументальных сталей). В этих стандартах имеются отличия (табл. 4.6). Например, в ГОСТ 1778 для оценок предусмотрены пятибалльные шкалы и два диапазона увеличений с двумя диаметрами (мм) поля зрения в каждом: 0,75—0,85 и 1,1-1,3 мм для х(90—110); 0,38-0,48 и 0,60-0,80 для х(170-210). Требования ГОСТ 801 предусматривают четырех балльную оценку только при одном увеличении и одном поле зрения: 1,1-1,3 мм при х(90-110).
Существующие методы оценки загрязненности металла микровключениями предполагают срав нение изображений анализируемого шлифа на об разце с эталонными шкалами, приведенными в стандарте, или подсчет выявленных включений с последующим определением объемного и массо вого их количества. Например, контроль металла на загрязненность по методикам ГОСТ 1778 пред лагает четыре варианта:
• метод Ш — сравнение с эталонными шкала ми для испытания деформированного металла. Он наиболее распространен и имеет 14 вариантов (от Ш1 до Ш14), которые различаются по условиям наблюдения: увеличению светового микроскопа, диаметру выбранного поля зрения, способу оценки
За рубежом используются аналогичные нормативные
шлифов и критерию характеристики плавок. В осно ве всех вариантов лежит сравнение видимого в оку ляре изображения шлифа с эталонными шкалами;
•метод К — подсчет количества включений для испытания деформированного и литого металла;
•метод П — подсчет количества и содержания включений в объемных процентах, пригодный для литого и деформированного металла. Метод реко мендуется как исследовательский для сталей и
сплавов всех марок;
• метод Л — линейный подсчет включений для отливок. Стандартом рекомендуется его использо вать в исследовательских целях для оценки каче ства литья из углеродистой и легированной кон струкционной стали.
Выбор метода контроля и нормы допустимой загрязненности оговариваются как в стандартах, так и в технических условиях на металлопродукцию.
Металлографический метод выявления и клас сификации неметаллических включений наиболее прост и удобен. При решении многих материаловедческих задач, которые встречаются на практике, он позволяет достаточно надежно идентифициро вать включения без применения других методов.
Согласно ГОСТ 1778, для контроля на наличие неметаллических включений в плавке отбирают не менее 6 образцов от разных прутков (рис. 4.9). При диаметре или толщине прутков не более 120 мм вырезают образцы в поставляемом размере. При диаметре или толщине свыше 120 мм образцы отрезают после перековки темплетов на круг или квадрат размером 80-120 мм (рис. 4.10).
Неметаллические микровключения по методу Ш определяют только в деформированном метал ле с помощью образцов диаметром или толщиной не менее 6 мм на шлифах с продольным направле нием волокон. В образцах деформированного ме талла меньшего размера (менее 6 мм) загрязнен ность оценивают в промежуточном полуфабрикате, профиле или заготовке. После термической обра ботки с заготовки шлифованием удаляют припуск (> 0,5 мм) и приготавливают шлиф. Длину образ цов выбирают таким образом, чтобы площадь шлифа была 400 ± 50 мм2. Для прутков небольших диаметров (< 10 мм) допускается уменьшение пло щади шлифа, но не менее, чем до 200 мм Также допускается изготовление шлифов на двух взаимно перпендикулярных плоскостях образца. При этом каждая плоскость считается отдельным шлифом.
акты: ISO 4967, ASTM Е 45, ASTM 1122, JIS G 0555.
Таблица 4.6
Возможность классификации и критерии оценок загрязненности металла неметаллическими микровключениями по отечественным стандартам
Показатели |
г о с т |
ГОСТ |
|
1778 |
801 |
||
|
|||
Классификация по видам |
|
|
|
Оксиды кремния, марганца, алюми |
|
|
|
ния, которые образуются при рас |
|
|
|
кислении сталей: |
+ |
+ |
|
строчечные |
|||
точечные |
+ |
- |
|
недеформирующиеся (глобулярные) |
- |
+ |
|
Силикаты сложного состава: |
+ |
|
|
хрупкие |
- |
||
пластичные |
+ |
- |
|
недеформирующиеся |
+ |
- |
|
Сульфиды (Mn, Fe)S, которые при |
+ |
+ |
|
недостаточном количестве марганца |
|
|
|
образуют с FeO эвтектику. При на |
|
|
|
греве 1200 °С под горячую прокатку |
|
|
|
эвтектика плавится и вызывает раз |
|
|
|
рушение металла во время деформа |
|
|
|
ции (красноломкость) |
|
|
|
Нитриды и карбонитриды: |
+ |
|
|
строчечные |
- |
||
точечные |
+ |
- |
|
Нитриды алюминия |
+ |
- |
|
Критерии оценки |
+ |
|
|
Средний балл как среднее арифме |
+ |
||
тическое максимальных оценок каж |
|
|
|
дого образца |
+ |
|
|
Средний и максимальный баллы и |
|
||
количество образцов с баллом выше |
|
|
|
максимального, процент от общего |
|
|
|
количества образцов |
+ |
|
|
Средний и максимальный баллы и |
|
||
количество образцов с максималь |
|
|
|
ным баллом |
+ |
|
|
Количество полей зрения с баллом 2 |
|
||
и более раздельно по кислородным, |
|
|
|
сульфидным и нитридным включе |
|
|
|
ниям, отнесенным к площади 10 см2 |
|
|
|
Пр имсчанне. Знак «+» свидетельствует о |
наличии, |
а знак «-» — об отсутствии соответствующего вида включе ний или критерия оценки в требованиях стандарта
Рис. 4.9. Отбор образцов для контроля на неметаллические включения (для метода Ш): а — из круглого и квадратного профиля диаметром или толщиной до 40 мм;
б — из круглого и квадратного профиля диаметром или толщиной свыше 40, но менее 80 мм;
в — из круглого и квадратного профиля диаметром или толщиной свыше 80 до 120 мм включительно; 1— плоскость реза; 2 — плоскость шлифа
5-я зона Т |
] |
|
5-я зона |
■ |
4-я зона |
■ |
N. |
4-я зона |
■ |
3-я зона |
■ |
\ |
3-я зона |
■ |
2-я зона |
1 |
\ |
2-я зона |
1 |
1-я зона |
1 |
1 |
1-я зона |
1 |
б
Рис. 4.10. Схема определения неметаллических включений металлографическим методом (П)
на прокате круглого (а) и прямоугольного (б) профилей. Черным цветом показана площадь, приходящаяся
на поля зрения, подвергаемые анализу
В методе К применяют шлифы с продольным направлением волокна, а в методе П предусматри вается определение загрязненности металла на шлифах с поперечным направлением волокон. Пе ред просмотром шлиф расчерчивают от края до центра на пять равных зон. В каждой зоне поля зрения выбирают вдоль прямых линий, перпенди кулярных к оси слитка или проката, с учетом ис пользованного оптического увеличения микроско па (табл. 4.7).
Независимо от метода обработки изображений и оценки качества металла, этапы выявления и классификации неметаллических включений пред полагают высокое качество подготовленного шли фа. Он не должен иметь рисок, царапин и других механических дефектов.
Поверхность шлифа должна быть плоской без «завалов» на краях. Для улучшения условий под готовки анализируемой поверхности применяют предварительную термическую обработку образ цов, повышающую твердость металла и устра няющую выкрашивание включений на стадии подготовки пробы.
Неметаллические включения размером более 1мкм на образцах литых и деформированных ста лей изучают на нетравленых шлифах. С целью об наружения и классификации включений с помо щью металлографических микроскопов использу ют светлопольное и темнопольное освещение объекта, а также поляризованный свет.
Метод качественного анализа позволяет полу чить достаточно полную характеристику вида и возможных свойств неметаллических включений.
Определяемыми показателями являются цвет, прозрачность, размеры и форма, степень анизо тропии, микротвердость и деформируемость, взаимодействие с определенными химическими реактивами. Например, в методе светлого поля при небольших (до х200) увеличениях определяют общую картину расположения неметаллических частиц, а при увеличениях х400 и выше — мель чайшие подробности строения отдельных включе ний, их окраску, отражательную способность. В режиме темного поля исследуют мелкие (раз
Характеристики деформируемости объектов определяют по отношению протяженности отдельных частиц или групп включений (строчек) к их поперечному сечению в продоль ной плоскости (в направлении прокатки).
мером до 10 мкм) неметаллические включения, рельеф их поверхностей и собственную* внутрен нюю окраску. Применение поляризованного света позволяет определить прозрачность и анизотроп ность частиц. Кроме того, с помощью замеров микротвердости (прибор ПМТ-3) можно устано вить отличия для включений малых размеров. При воздействии химических реактивов некоторые не металлические включения вытравливаются или растворяются, оставляя пустоты, окрашиваются, изменяют цвет или остаются неизменными (табл. 4.8).
Таблица 4.7
Выбор полей зрения в зонах шлифа при оценке загрязненности металла по методу П (ГОСТ 1778)
|
Минимальное количество |
Общее |
||||
Увеличение |
|
полей зрения по зонам |
количество |
|||
|
|
|
|
|
полей зрения |
|
|
1 |
2 |
3 |
4 |
5 |
|
|
на шлифе |
|||||
|
|
|
|
|
|
|
хЗООи х400 |
5 |
15 |
25 |
35 |
45 |
125 |
х500 и хбОО |
15 |
45 |
75 |
105 |
135 |
375 |
Расположение включений может быть равно мерным и неравномерным, в виде отдельных обо собленных зерен, групп или цепочек. Важной ха рактеристикой является местоположение частиц по отношению к общей структуре металла, напри мер на границах или внутри зерен. Расположение включений оказывает влияние на механические свойства металлов и сплавов, поскольку при пла стической деформации вблизи частиц возникают высокие локальные напряжения. С этой точки зре ния наиболее опасными являются протяженные недеформируемые выделения строчечного вида — нитриды и карбонитриды (рис. 4.11).
В зависимости от химического состава и осо бенностей взаимодействия между атомами кри сталлическая решетка включений может принад лежать той или иной кристаллографической форме, которая позволяет идентифицировать выделение с помощью дифракционных методов анализа
Включения могут иметь собственный цвет, который строго постоянен для данного вида и не меняется в зависимо сти от качества полировки шлифа и условий наблюдения в микроскопе.
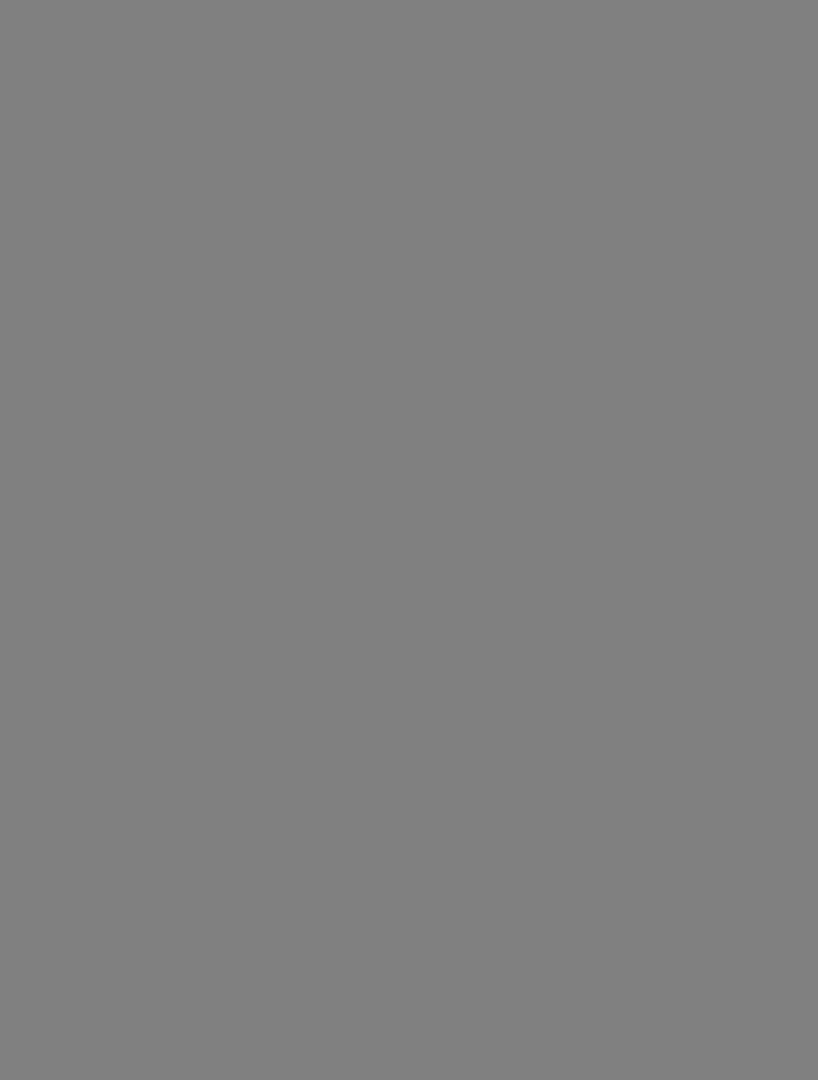
