
книги / Металлы и сплавы. Анализ и исследование. Физико-аналитические методы исследования металлов и сплавов. Неметаллические включения
.pdf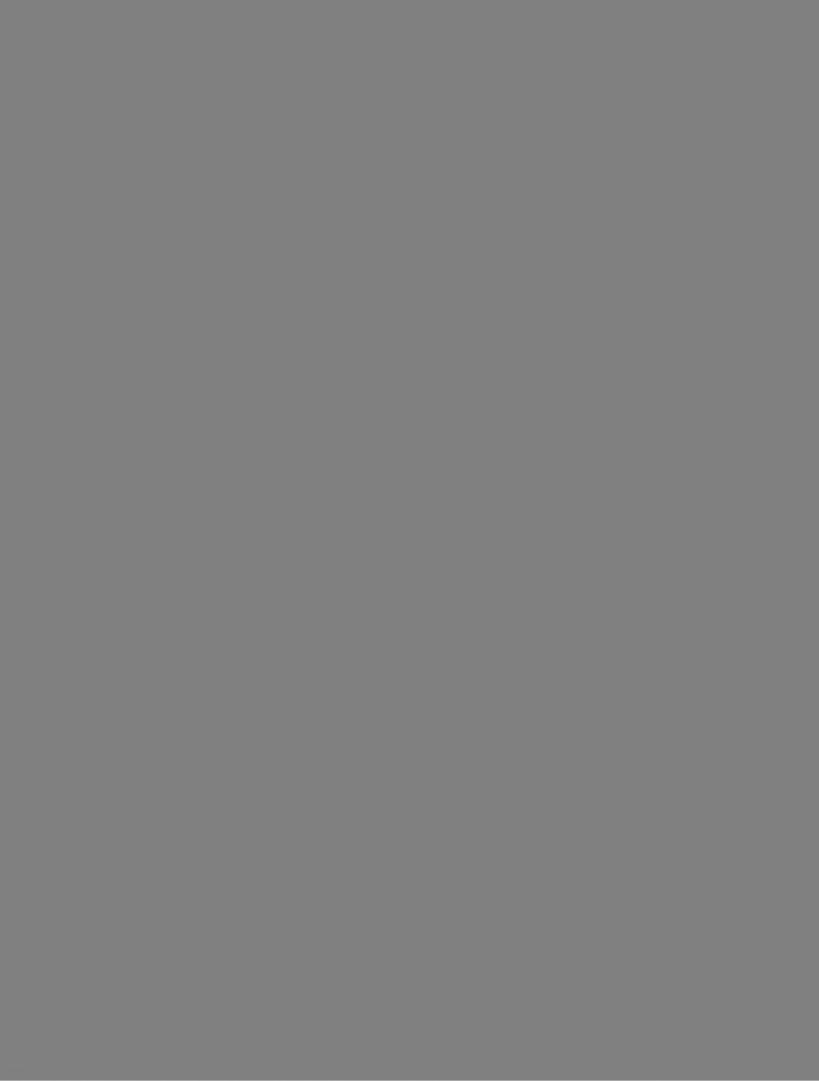
В этом случае энергии электронов достаточно, чтобы на флуоресцирующем экране микроскопа сформировать изображения картин дифракции пучка электронов в кристаллической решетке ме талла или микродифракции от локального участка фольги. Однако фольга не должна быть слишком тонкой, чтобы в процессе ее подготовки в струк туру материала не были внесены побочные иска
жения и артефакты.
Считается, что внутреннее строение фольги и массивного образца идентичны, если на длине свободного пробега подвижной дислокации не ме нее четырех раз встретится препятствие, способ ное вызвать ее поперечное скольжение. К другим условиям соответствия дислокационных структур в массивных заготовках и тонких фольгах, изго товленных из них, относят температуру. В процес се приготовления температура фольги должна быть ниже того значения, при котором формиро валось распределение дислокаций в исходной за готовке. Например, при изучении влияния терми ческой обработки на структуру, нагрев фольги может резко изменить кинетику образования вы делений, а также значительно снизить закалочные напряжения и деформации. Кроме того, в фольге совершенно недопустим наклеп металла, вызван ный неосторожным обращением, как на стадиях изготовления, так и исследования, например, при установке в столик держателя образцов.
Фольгу как представительную статистическую пробу массивного металлического полуфабриката изготавливают, используя операции механической резки и шлифования, электрохимического утоне ния и полирования, а также ионного травления. Внешние размеры фольги определяются посадоч ным диаметром предметного столика в держателе микроскопа. Как правило, его диаметр равен 3 мм.
Из массивных заготовок необходимые образцы можно готовить двумя способами:
1.С помощью фрезерных или электроискровых станков вырезают пластинку произвольной формы
иразмеров, из которой в дальнейшем выкраивают участки нужной толщины для получения фольг.
2.На токарном станке производят заготовку диаметром 3-4 мм, от которой электроискровым
или другим способом отрезают пластинки в форме дисков.
При резке и токарной обработке все механиче ские усилия, способные деформировать пробу,
должны быть сведены к минимуму. Толщина дис ка должна включать слой механически наклепан ного металла, который при последующих опера циях будет удален. К настоящему времени в лабо раторной практике все чаще находит применение способ отрезки дисков заданной толщины с помо щью тонких алмазных кругов. Регулируемое число оборотов и прижимное усилие инструмента а также точное (до 0,1 мм) позиционирование ал мазного круга обеспечивают высококачественное отрезание заготовки с поверхностью реза, допус кающей переход к электрохимическому полирова нию, минуя механическую полировку. В зависи мости от вида металлического материала в подго товительном цикле рекомендуются следующие толщины заготовок фольг:
•для алюминия и его сплавов 0,7-0,8 мм;
•магния и его сплавов 1,0-1,2 мм;
•титана и его сплавов 0,3-0,4 мм;
•сплавов на основе железа 0,2-0,3 мм. Предварительное утонение пластин или дисков,
подготовленных из алюминия, магния и сплавов на их основе, реализуется методами химического утонения, шлифования й электролитической поли ровки. Сплавы на основе титана и железа обраба тывают шлифованием и электролитическим поли рованием.
Химическое утонение пластин и дисков, выре занных из полуфабрикатов алюминиевых мате риалов, производят в 40% водном растворе едкого натра или в концентрированной плавиковой ки слоте плотностью 112 кг/м3 Пластинки и диски, подготовленные из магния и сплавов на его осно ве, утоняют в концентрированной азотной кислоте. С целью предохранения краев заготовок от раство рения их защищают перхлорвиниловым лаком. Алюминиевые образцы утоняют до 0,25-0,3 мм, а магниевые — до 0,1-0,15 мм. Рельеф поверхно сти, возникший в результате химического утоне ния, удаляют шлифованием.
Шлифование образцов выполняют вручную с помощью двух гладких пластин, обернутых шли фовальной бумагой. Процедуру начинают на гру бой шкурке (№ 10 по ГОСТ 6465), а заканчивают на тонкой шлифовальной бумаге (М 28). Шлифо вание прекращают по достижении толщины, мм: 0,01-0,02 — для образцов алюминия, 0,02-0,025 — для сплавов магния и 0,012-0,015 —для материа лов на основе титана и железа. После шлифования
подготовленные заготовки фолы на 1-2 мин по мещают в ванну химического утонения, после чего промывают в воде и высушивают с помощью фильтровальной бумаги.
Этап электролитической полировки обычно совпадает со стадией окончательного утонения фольги. Лабораторная практика показывает, что состав электролита и режим полировки выбраны правильно, если через 2-5 мин после начала опе рации на поверхности образца не возникают рас травы и оксидные пленки, а блестящая поверх ность фольги не содержит следов грубого полос чатого рельефа. При этом образующийся вязкий полирующий слой хорошо смывается без подтравливания фаз, присутствующих в сплаве. После проведения подготовительных операций фольга, пригодная для просмотра в просвечивающем элек тронном микроскопе, имеет толщину менее 0,2 мкм (200 нм).
Электролитическое полирование осуществляют
всосуде с двойными стенками, которые позволя ют поддерживать в растворе необходимую темпе ратуру (рис. 3.3.18). В крышке сосуда крепится пинцет с захватом образца и электроды.
Электрополирование — процесс анодного рас творения металлов, сопровождающийся выравни ванием поверхности. Наклепанный поверхност ный слой, который образуется при механической обработке, удаляется только этим способом.
Анодом служит образец, закрепленный в захва те пинцета. Образцы в форме пластинок полиру ют, удерживая за край. Заготовки в форме дисков желательно укреплять в предварительно изготов ленных оправках. Во время полирования проба полностью погружается в электролит. Обработку ведут до толщины 0,05-0,1 мм. Катод выполняется
вформе пластин или кольца. Электролит может охлаждаться проточной водой, твердой углекисло той (сухим льдом) (до -40 °С) или парами азота (до -70 °С), пары которого подаются к стенкам через теплоизолированный канал. Низкотемпера турная полировка рекомендуется для титана и сплавов на его основе.
Реактивы, которые применяются для электро полирования, отличаются большим разнообразием (табл. 3.3.1). Обычно электролит состоит из слабо реакционных составных частей, которые не воз действуют на материал образца в отсутствие элек трического поля. Большое распространение полу
чили растворы, содержащие метанол и разные концентрации азотной или хлорной кислот. Во избежание окисления поверхности фолы в элек тролите нежелательно наличие воды, что заставля ет прибегать к ее выпариванию из хлорной кисло ты (НСЮ4). Эта кислота взрывоопасна, поэтому в лабораторной практике применяется в разбав ленном виде и при определенных концентрациях. Выпаривание (как и другие операции, связанные с электрополировкой) следует производить в вы тяжном шкафу с соблюдением правил безопасно сти при работе с химическими веществами. Кон центрация хлорной кислоты при плотности 1500— 1600 г/см3 и температуре не выше 90 °С обеспечи вает хорошее качество полируемой поверхности. Поскольку режим электрополирования может ме няться для сплава одного химического состава в зависимости от его обработки, конструкция уста новки должна предусматривать возможность лег кого регулирования электрических и температур ных параметров.
Рис. 3.3.18. Схема варианта конструкции сосуда
для электролитического полирования металлических образцов:
1— образец, который удерживается пинцетом;
2— пинцет; 3— катод;
4— крышка для крепления электродов;
5— сосуд с двойными стенками для поддержания нужного теплового режима реакции; 6— электролит. Размеры приведены в миллиметрах
Таблица 3.3.1
Электролиты и режимы электрополировки для приготовления металлических фольг
Состав электролита в мл или масс. %, соли в г (плотность, 103 кг/м3, и «химическое» качество)
28 хлорной кислоты (1,505),
77 уксусной кислоты (ледяной)
20 хлорной кислоты (1,505),
80 этанола (ректификата)
(из разных литературных источников)
Металлы и сплавы
А1—Си; Al; А1—Мп; А—Zn; сплавы Д20; АМц
Al—Mg; А1—Си—Mg; Al— Си—Mg—Мп; А1—Си—Mg— Zr; сплавы Д16; АМгб; AMrl 1
Al—Mg—Si; Al—Zn—Mg; Al—Zn—Mg—Си; сплавы АМЦ; B95
|
Режим полирования |
||
Напряже |
Плотность |
Температура, °С |
|
тока, |
|||
ние, В |
(материал катода) |
||
А/см2 |
|||
|
|
0,04 |
5-12 |
|
(алюминий) |
||
|
||
0,03 |
|
|
|
<6 |
|
10-20 |
(алюминий) |
|
|
||
0,02 |
|
10 хлорной кислоты (1,505),
90 уксусной кислоты (1,049)
22 хлорной кислоты (1,505),
78 уксусного ангидрида (1,08)
40 уксусной кислоты (1,049),
30 ортофосфорной кислоты (1,71),
20 азотной кислоты (1,34),
10 воды (дистиллированной)
10 хлорной кислоты (1,505),
90 уксусной кислоты (1,049)
100 хлорной кислоты (1,58-1,60),
400 уксусного ангидрида (1,08)
340 серной кислоты (1,84),
70 фтористоводородной (плавиковой) кислоты (1,12), 30 воды (дистиллированной)
20 хлорной кислоты (1,505)
80 этанола
10 хлорной кислоты (1,505),
90 уксусной кислоты (1,049)
40 уксусной кислоты (1,049),
30 ортофосфорной кислоты (1,71),
20 азотной кислоты (1,34),
10 воды (дистиллированной)
22 хлорной кислоты (1,505),
73 уксусной кислоты (1,08),
5 воды (дистиллированной)
Al, Al—Мп, сплав АМЦ |
|
5-12 |
|
(алюминий) |
|
|
|
|
|
|
0,04 |
Al |
|
< 10 |
|
(алюминий) |
|
|
|
|
|
|
<20 |
Al |
60 |
(платиновая |
|
|
проволока) |
|
|
4-5 |
Mg, Mg—Mn—Cl;
Mg—Nd—Mn; Mg—Li—Al;
сплавы MA8; MAI 1
Ti; Ti—Al—Mo—Cr; Ti—Al—
Mo—V; Ti—Al—Mo—Zr;
сплавы BT1-1; ВТЗ-1; ВТ14;
ВТ15; ВТ 18; BT22
Ti; Ti—Al—Mo—Cr; Ti—Al—
Mo—V; Ti—Al—Mo—Zr;
сплавы BT1-1; ВТЗ-1; ВТ 14;
BT15; BT18; BT22
Сплавы на основе алюминия
<10 10-15 (нержавеющая
сталь)
20-30
60-70 0,3 (алюминий, титан)
20
20-30 0,1 (алюминий, титан)
Алюминий; двойные сплавы |
4-5 |
|
|
|
алюминия с медью, кремнием, |
0,3 |
-3 |
||
никелем и магнием |
|
|
|
|
Алюминий; многокомпонент |
|
|
|
|
ные сплавы алюминия с маг |
10-20 |
0,4 |
5-12 |
|
нием и кремнием, цинком |
|
|
|
|
Алюминий; многокомпонент |
|
|
|
|
ные сплавы алюминия с ме |
6-10 |
4-5 |
20 |
|
дью и магнием |
|
|
|
|
Алюминий; сплавы на основе |
10-20 |
0,4 |
10 |
|
алюминия |
||||
|
|
|
Состав электролита в мл или масс. %, соли в г (плотность, 103 кг/м3,
и «химическое» качество)
49 азотной кислоты (концентрированной), 49 метанола, 2 соляной кислоты
95 ортофосфорной кислоты,
5 серной кислоты,
12,5 г хромового ангидрида на 1 л раствора
20 хлорной кислоты,
80 этанола
10 хлорной кислоты,
10 воды,
70 этанола,
10 глицерина
62 ортофосфорной кислоты,
24 воды,
14 серной кислоты,
160 г хромового ангидрида на 1л раствора
Предварительный состав: 10 азотной кислоты, 90 воды;
Промежуточный состав: 80 этанола, 20 хлорной кислоты;
Окончательный состав: 70 этанола, 10 хлорной кислоты
(концентрированной), 20 глицерина
617 мл ортофосфорной кислоты,
134 мл серной кислоты
240 мл воды,
156 г хромового ангидрида
20 мл хлорной кислоты (1,25)
800 мл этилового спирта
100 мл азотной кислоты,
100 мл метанола,
4 мл соляной кислоты
1г хлорной кислоты, 9 г уксусной кислоты (ледяной)
Металлы и сплавы |
Напряже |
|
ние, В |
Сплавы на основе алюминия
Алюминий; двойные сплавы алюминия с медью, многоком понентные сплавы алюминия
с медью и магнием
10
Алюминий; сплавы на основе алюминия
Сплавы на основе алюминия |
15-20 |
Алюминий; сплавы на основе
2-3
алюминия
Сплавы на основе алюминия |
9-12 |
Алюминий; сплавы на основе алюминия.
10-20
Последовательная обработка в каждом из растворов
Алюминий; двойные сплавы |
|
|
на основе алюминия (магна |
9-12 |
|
лии) |
|
|
Алюминий; сплавы на основе |
1-2 |
|
алюминия: А1—Си, А1—Ag, |
||
Al—Zn, Al—Mg |
|
|
Алюминий; сплавы на основе |
10-15 |
|
алюминия |
||
|
||
Алюминий; сплавы на основе |
|
|
алюминия: А1—Zn —Mg, |
18-20 |
|
Al—Zn, Al—Mg, Al—Cu—Mn |
|
Продолжение табл. 3.3.1
Режим полирования
Плотность
тока,
Температура, °С
А/см2
(материал катода)
-(15-20)
10
-30
-20
70
0,2
-(10-20)
70
(свинец)
До 35 (алюминий)
5 20
0,2
До 30 (алюминий)
Состав электролита в мл или масс. %, соли в г (плотность, 103 кг/м3, и «химическое» качество)
28 хлорной кислоты (1,505),
72 уксусной кислоты (1,040)
33 азотной кислоты,
67 метанола
40 азотной кислоты,
50 ортофосфорной кислоты,
10 соляной кислоты
133 мл уксусной кислоты,
7 мл воды
25 г хромового ангидрида
133 мл уксусной кислоты,
7 мл воды,
25 г хромового ангидрида
860 мл ортофосфорной кислоты,
50 мл серной кислоты,
100 г хромового ангидрида
5 мл хлорной кислоты,
95 мл уксусной кислоты,
2 г хромового ангидрида, 1г хлористого никеля
60 ортофосфорной кислоты,
40 серной кислоты
57 серной кислоты,
43 воды
20 мл хлорной кислоты( 1,48-1,54)
80 мл уксусной кислоты (ледяной)
795 мл уксусного ангидрида,
250 мл 57% хлорной кислоты
93 мл хлорной кислоты (1,58),
398 мл уксусного ангидрида,
24 мл воды
170 мл серной кислоты,
36 мл плавиковой кислоты,
16 мл воды
40 серной кислоты (1,84),
60 ортофосфорной кислоты (1,3)
Металлы и сплавы
Сплавы на основе алюминия
Алюминий; двойные сплавы алюминия с медью, марган цем, цинком и магнием
Сплавы на основе меди
Медь; двойной сплав меди с цинком
Медь; сплавы на медной основе
Медь; двойные сплавы меди с серебром, золотом
Сплавы на основе никечя
|
Продолжение табл. 3.3.1 |
||
|
Режим полирования |
||
Напряже |
Плотность |
Температура, °С |
|
тока, |
|||
ние, В |
(материал катода) |
||
А/см2 |
|||
|
|
||
10-20 |
0,4 |
5-12 |
|
4-8 |
0,5-0,6 |
-30 |
|
7-10 |
0,2-0,3 |
20 |
Двойной сплав никеля с мар |
7-10 |
0,2-0,3 |
20 |
|
ганцем |
||||
|
|
|
||
Никель; многокомпонентные |
|
|
|
|
сплавы никеля с хромом и же |
6-8 |
2-4 |
20-40 |
|
лезом |
|
|
|
|
Никель; сплавы на основе |
5-6 |
0,2 |
10 |
|
никеля |
||||
|
|
|
||
|
2,5 |
1,5 |
60 |
|
Сплавы на основе никеля |
10 |
0,2 |
20 |
|
|
5 |
2-3 |
До 30 |
|
Сплавы на основе титана |
|
|
|
|
Титан и сплавы на его основе |
60 |
|
35 |
|
Сплавы на основе a-Ti |
60-70 |
0,2 |
Не более 30 |
|
|
|
|
||
Сплавы на основе P-Ti |
20-30 |
|
До 30 |
|
Сплавы на основе железа |
|
|
|
|
Стали переходного класса |
10 |
2,5-3,0 |
40-60 |
Состав электролита в мл или масс. %, соли в г (плотность, 103 кг/м3,
и «химическое» качество)
400 мл ортофосфорной кислоты,
100 мл серной кислоты,
75 г хромового ангидрида,
25 мл воды
65 ортофосфорной кислоты,
15 серной кислоты,
6 хромового ангидрида,
14 воды
5 хлорной кислоты,
95 уксусной кислоты
10 хлорной кислоты,
90 уксусной кислоты
20 хлорной кислоты,
80 уксусной кислоты
20 хлорной кислоты,
80 метанола
860 мл ортофосфорной кислоты,
100 г хромового ангидрида
60 ортофосфорной кислоты,
40 серной кислоты
100 г хромового ангидрида,
250 мл ортофосфорной кислоты,
100 мл воды
|
|
Окончание табл. 3.3.1 |
||
|
|
Режим полирования |
||
Металлы и сплавы |
Напряже |
Плотность |
Температура, °С |
|
тока, |
||||
|
ние, В |
(материал катода) |
||
|
А/см2 |
|||
|
|
|
||
Сплавы на основе железа |
|
|
|
|
Стали переходного класса |
|
2-3 |
30-60 |
|
|
10 |
|
|
|
Мартенситно-стареющие |
|
0,3-0,5 |
40-60 |
|
стали |
|
|||
|
|
|
||
Железо и сплавы железа с ни |
35-40 |
0,5-0,7 |
До Ю |
|
келем, нержавеющие стали |
||||
|
|
|
||
Среднеуглеродистые стали |
|
0,1 |
-15 |
|
(промывка в метаноле) |
|
|||
12 |
|
|
||
Железо, сплавы железа |
|
|
||
|
0,6 |
|
||
с хромом |
|
|
||
|
|
До ю |
||
Железо, нержавеющие стали |
|
|
||
(допускается замена метанола |
50-80 |
2,0 |
|
|
на этанол) |
|
|
|
|
Сплавы железа с никелем, |
|
|
|
|
хромом и молибденом, |
15 |
0,3 |
До 20 |
|
нержавеющие стали |
|
|
|
|
Нержавеющие стали |
10 |
1,5-3,5 |
До 30 |
|
Сплавы железа с марганцем |
6 |
1,0 |
30 |
Условия электрополирования, свойства элек тролита, а также анодные и катодные процессы достаточно полно характеризуются вольтамперной кривой в координатах «плотность тока (7)—напря жение (V)» на клеммах электролитической ячейки (рис. 3.3.19).
При повышении температуры электролита рас тет химическая активность и проводимость рас твора, а также скорость растворения материала анода. Однако возрастающее при этом выделение газов и ухудшение условий образования поли рующего слоя вблизи поверхности пробы ведут к ухудшению качества полируемой поверхности. Для реализации процесса электрохимического по
лирования необходим источник постоянного тока силой до 20 А при напряжении на регулируемых выходных клеммах 0-30 В. Заметное влияние на результат электрополировки оказывают размеры и форма электродов. Например, если катод значи тельно превышает размеры анода (фольги), то происходит разъедание краев анода (рис. 3.3.20).
Если исследуемый материал имеет чрезвычайно неоднородную (гетерогенную) структуру, то при менение химической или электрохимической об работки может привести к интенсивному локали зованному растраву. В таких случаях может быть рекомендовано применение резки с помощью ал мазных дисков с последующим ионным травлением.
УТ
Рис. 3.3.19. Вольтамперная кривая типичного электрохимического процесса. аЬ—участок травления; Ьс— переходная область; cd—зона «плато», в пределах которой осуществляется
полировка; de— область ускорения реакции с выделением газов. Лучшее качество поверхности фольги обеспечивается в зоне «плато» вблизи точки d
Поскольку для большинства распространенных металлических материалов окончательная обра ботка фолы производится электролитическим процессом (табл. 3.3.2), то к настоящему времени разработаны универсальные приборы, предназна ченные для приготовления фольг из металличе ских заготовок в форме дисков. В таких приборах, как правило, все три операции (предварительное химическое утонение, электрополирование и фи нишное утонение) выполняются последовательно путем вариации режимов и замены электролита. Все стадии обработки контролируются, а этап окончательного утонения фольги автоматизиро ван. С учетом управляемости процесса электропо лирования, воспроизводимости опытов и произво дительности в получении фольг нужной толщины и качества наибольшее распространение получил метод струйной обработки поверхности. Основу прибора определяет конструкция электрохимиче ской ячейки (рис. 3.3.21), в которой создаются условия для получения потоков электролита, на правленных на поверхность заготовки, а также приспособлений для контроля процесса.
Держатель /, в котором закреплен образец 2 в форме диска, помещен в реакционный объем 3. В его стенках с помощью уплотнений 4 установ лены сопла 5 специальной конструкции, которые посредством внешнего насоса б формируют пото ки электролита, направляемые на обрабатываемую поверхность. При финишном полировании фольги используются сопла диаметром 1,0-1,5 мм, вы полняющие роль катода. По окончании обработки
Рис. 3.3.20. Влияние плотности тока и формы катода на качество электрополировки фольги в форме диска: недостаточная плотность тока и маленький катод (слева); чрезмерная плотность тока и большой катод (справа); оптимальное соотношение размеров электродов
при удачном выборе режима полировки (в центре)
образец извлекают из держателя, промывают и тщательно высушивают. Затем его помещают в вакуумируемый эксикатор или непосредственно в колонну микроскопа для наблюдения или иссле дования.
На стадии финишного утонения фольги очень важен критический момент появления первого от верстия. С целью его своевременного обнаруже ния в конструкцию прибора вводят вспомогатель ные приспособления, например светочувствитель ные фотодиоды и светопроводящие линии (све товоды). Световоды размещаются внутри сопел. В процессе обработки образца утоняемая поверх ность фольги освещается внешним источником света через один из световодов. У другого свето вода помещен фотодиод, который фиксирует мо мент появления света, прошедшего сквозь отвер стие в фольге. Как только в фольге появляется первое отверстие, процесс полировки немедленно прекращают.
Для получения на фольге высококачественной поверхности необходимо выбирать такие условия полирования, при которых распределение прохо дящего тока было бы равномерным, а форма кра теров — мест наибольшего локального утонения — характеризовалась плоским дном. Форма кратеров определяется геометрией (размерами и диамет ром) и расположением (расстоянием до образца) используемых сопел, а также конфигурацией дер жателя заготовки фольги (рис. 3.3.22). Эти пара метры определяют основные конструктивные осо бенности прибора.

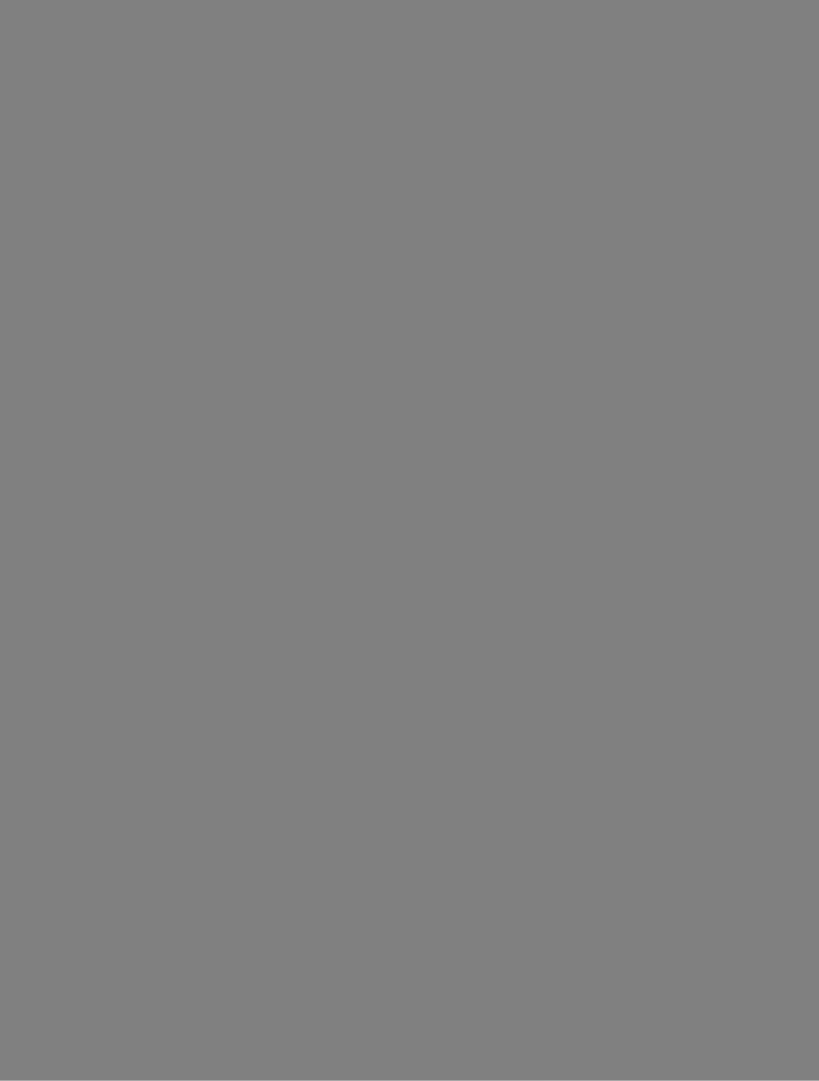