
книги / Основы технологии машиностроения. Методы обработки заготовок и технологические процессы изготовления типовых деталей машин
.pdf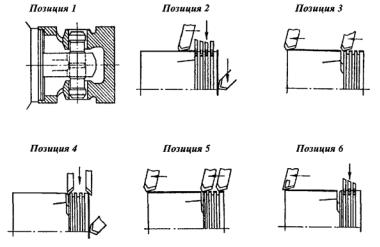
После получения вспомогательных технологических баз заготовка поршня поступает на обработку наружных поверхностей с установкой по вспомогательным техноло- гическим базам.
Предварительную и чистовую обработку наружной поверхности производят на многошпиндельных токарных полуавтоматах за одну установку. Наиболее распространен- ными видами многорезцовых станков для обработки порш- ней по наружным поверхностям являются шести- и восьми- шпиндельные полуавтоматы горизонтального и вертикаль- ного типов. На рис. 12.46 приведена схема обработки на- ружных поверхностей поршня на шестишпиндельном полу- автомате.
Рис. 12.46. Схема обработки наружных поверхностей поршня на шестишпиндельном многорезцовом полуавтомате
На позиции 1 заготовку поршня устанавливают пред- варительно расточенным внутренним пояском юбки на оп- равку и закрепляют на оправке пальцем, вставленным через отверстие поршня. Затем оправку пневматическим приво-
411
дом затягивают внутрь шпинделя станка и закрепляют за- готовку. На позиции 2 предварительно обрабатывают юбку, канавки под поршневые кольца и днище поршня. На пози- ции 3 производят получистовую обработку юбки двумя резцами. На позиции 4 снимают фаски и выполняют чисто- вую подрезку днища. На позиции 5 обтачивают начисто юбку и головку тремя резцами, установленными с посте- пенным уменьшением размера обработки по направлению к днищу. На позиции 6 производят отделочную обработку всех наружных поверхностей и канавок под поршневые кольца набором резцов. Юбка поршня обтачивается на ко- нус по конусной линейке. Овальные юбки обтачивают по специальному копиру. Предварительную обработку от- верстий под поршневой палец и канавок под стопорные кольца производят на двусторонних многопозиционных станках с многоместными приспособлениями барабанного типа, с базированием по пояску юбки, торцу и наружной по- верхности приливов бобышек или по установочным отвер- стиям (поршни с вырезанной юбкой). При обработке на этих станках на позиции 1 устанавливают, закрепляют и снимают заготовки, на позиции 2 производят зенкерование или пред- варительное растачивание со снятием фасок, на позиции 3 производят развертывание или чистовое растачивание обоих отверстий с одной стороны на проход, и на позиции 4 проре- зают канавки под стопорные кольца.
Чистовую обработку отверстия под поршневой палец осуществляют чистовым растачиванием на одно- или дву- сторонних горизонтально-расточных станках. В обоих слу- чаях расточная оправка (борштанга) обрабатывает за один проход отверстия в обеих бобышках, только во втором слу- чае предварительное растачивание производят одной из оп- равок, оснащенной двумя резцами, а окончательное – другой оправкой, расположенной с противоположной стороны
412
иоснащенной одним резцом. Шпиндели оправок вращаются с различными числами оборотов, а стол станка передвигает- ся с различной подачей.
При предварительной обработке удаляют припуск 0,2– 0,5 мм на диаметр, а при окончательной – 0,08…01 мм.
Наружную поверхность поршня окончательно обра- батывают шлифованием на копировально-шлифовальных полуавтоматах с базированием по вспомогательным базам
иприводом во вращение ложным пальцем. Цилиндриче- ские поршни с круглой юбкой шлифуют на бесцентрово- шлифовальных станках с продольной (сквозной) подачей, а ступенчатые или конусные – с радиальной (поперечной) подачей.
Отделочную обработку наружных поверхностей порш- ня шлифованием, несмотря на ее простоту, высокую произ- водительность и экономичность, в последнее время все чаще заменяют тонким (алмазным) копирным обтачиванием. Этот способ обработки, обеспечивая почти ту же точность и чис- тоту обработанной поверхности, обладает рядом преиму- ществ: устраняет вероятность попадания и внедрения частиц абразива в рабочую поверхность поршня, что возможно при шлифовании, и обеспечивает значительно меньшее радиаль- ное усилие резца, чем шлифовальный круг.
Для тонкого обтачивания используют многошпин- дельные быстроходные прецизионные станки и режущий инструмент, оснащенный доведенными твердосплавными пластинами, или алмазные резцы. Обработку ведут в два прохода: сначала резцом с твердым сплавом, а затем алмаз- ным резцом.
Отверстия для смазки сверлят в канавках маслосъем- ных колец, в специальных маслосъемных канавках и в бо- бышках отверстия под палец. Заготовки поршней при свер- лении устанавливают по тем же вспомогательным техноло- гическим базам – пояску на юбке поршня и ее торцу с уг-
413
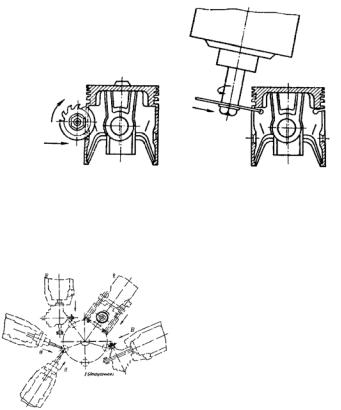
ловой ориентацией поршня по отверстию под палец или по двум установочным отверстиям для заготовок поршней
свырезанной юбкой.
Умногих алюминиевых поршней в юбке фрезеруют прорези, расположенные перпендикулярно или наклонно к образующей юбки поршня. На рис. 12.47 показана схема фрезерования прорезей в юбке поршня, а на рис. 12.48 – схема сверления вспомогательных отверстий и фрезерова- ния прорезей на пятипозиционном агрегатном станке.
Рис. 12.47. Схема фрезерования прорезей в юбке поршня
На I позиции устанавливают и снимают заготовку; на II позиции сверлят отверстия в юбке для выхода фрезы при разрезании юбки; на III позиции выполняют фрезерование
|
одной |
наклонной |
прорези; |
|
|
на IV позиции – фрезерование |
|||
|
одной горизонтальной прорези |
|||
|
в кольцевой канавке; на V по- |
|||
|
зиции – фрезерование второй |
|||
|
наклонной прорези. |
|
||
|
Заключительной опера- |
|||
Рис. 12.48. Схема обработки |
цией обработки поршней яв- |
|||
ляется |
подгонка их |
по весу |
||
прорезей и вспомогательных |
отверстий
414
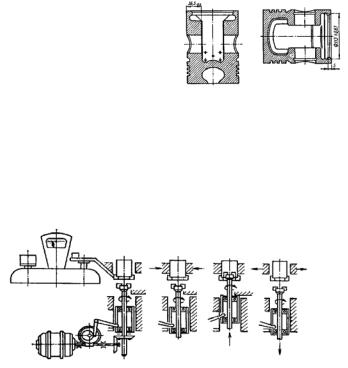
и сортировка на группы по диаметрам юбки. Подгонка поршней по массе связана с удалением излишнего металла режущим инструментом путем растачивания юбки поршня или (реже) подрезания внутренних бобышек для поршнево- го пальца.
На рис. 12.49 жирными линиями показаны места под- гонки поршня по массе.
Подгонку поршня по ве- су ведут на специальных стан- ках, снабженных весовым уст- ройством, управляющим пода- чей шпинделя с резцовой оп-
равкой. При удалении излишка металла подача шпинделя автоматически выключается, и резание прекращается.
На рис. 12.50 показана принципиальная схема работы полуавтомата для подгонки поршня по массе.
Рис. 12.50. Принципиальная схема работы полуавтомата для подгонки поршня по массе
Поршень, помещенный на весовое устройство, в за- висимости от своей массы устанавливается на определен- ной высоте и фиксируется в этом положении призмами. Расположенный снизу шпиндель с расточной головкой (зенкером) совершает автоматический цикл подъема на по-
415
стоянную высоту и снимает металл с нижней части юбки. Чем тяжелее поршень, тем ниже он опустится и тем боль- шее количество металла будет удалено при подрезании, благодаря чему колебание массы различных поршней огра- ничивается малыми пределами.
В некоторых устройствах подгонка поршня по массе производится путем фрезерования нижней части бобышек под поршневой палец по аналогичной схеме.
Точность подгонки по массе составляет ±2 грам- ма, производительность полуавтомата порядка 320 порш- ней в час.
После подгонки по массе поршни подвергают аноди- рованию. Это создает на поверхности твердую оксидную пленку, которая увеличивает срок службы поршня.
Контроль поршней заключается в проверке размеров и формы юбки, отверстия под поршневой палец, канавок под поршневые кольца и др. Контроль и сортировку на группы по диаметру юбки и отверстия под палец осуще- ствляется на специальных контрольных установках с одно- временным клеймением. Сортировка поршней на группы по диаметрам юбки преследует цель подбора поршней и цилиндров (гильз), находящихся по размерности в преде- лах определенного поля допуска.
Рассортированные на 4–5 групп поршни, как и ци- линдры блоков (гильзы), маркируют номером размерной группы, а затем при сборке комплектуют по этому призна- ку (селективная сборка).
Сортировочный допуск дает возможность обеспечить зазор между поршнем и цилиндром в пределах, который практически может быть достигнут при точности обработ- ки заготовок этих сопрягаемых деталей по 4–5-му квалите- ту точности.
416
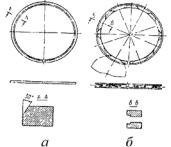
12.7.3. Технологические процессы обработки поршневых колец
Поршневые кольца предназначены для уплотнения зазора между стенками цилиндра (гильзы) и поршнем – это необходимо, чтобы предотвратить проникновение га- зов из камеры сгорания в картер (компрессионные кольца) и смазочного масла из картера в камеру сгорания (масло- съемные кольца). Например, в двигателях тракторов на поршень устанавливаются обычно 2–3 компрессионных и 1–2 маслосъемных кольца. Кроме того, поршневые коль- ца предохраняют поршень от перегревания, отводя тепло- ту, возникшую в результате трения, от поршня к охлаж- даемым стенкам цилиндров двигателя.
Поршневые кольца должны плотно и с равномерным распределением удельного давления прилегать к стенкам цилиндра по всей окружности. Для этого поршневые кольца выполняют с наружным диаметром в свободном состоянии больше, чем диаметр цилиндра (гильзы), делают прорези, выбирают соответствующий материал, обладающий высо- кой прочностью и упругостью, антифрикционными свойст- вами, теплопроводностью, износостойкостью, способностью выдерживать высокие температуры и др. На рис. 12.51 приведены виды поршневых колец и их профили в ради- альном сечении.
Компрессионные кольца (см. рис. 12.51, а) имеют в ра- диальном сечении прямо- угольную форму, на внешней образующей которой делают фаску под углом 30°. Эти кольца работают в условиях высоких температур и полу-
417
сухого трения, особенно кольцо, расположенное у камеры сгорания. Верхнее компрессорное кольцо, работающее в наиболее тяжелых условиях, подвергается пористому хромированию с последующим лужением слоем олова толщиной 0,005–0,01 мм. Толщина хромового покры-
тия 0,1–0,2 мм, глубина пор 0,04–0,06 мм.
Маслосъемные кольца (см. рис. 12.51, б) более разно- образны по конструкции, однако их назначение (отвод из- лишков масла) и расположение на поршне не требует при- дания им особых газоуплотняющих и теплоотводящих свойств. Наиболее распространенной конструкцией этих колец являются кольца с радиальными углублениями по торцовой поверхности, предназначенными для перепус- ка масла во внутреннюю полость поршня.
В обеих конструкциях колец для предохранения их от заклинивания при расширении от нагрева (для компен- сации теплового расширения) в прорези (замке кольца) пре- дусматривают зазор 0,2–0,6 мм.
Для изготовления поршневых колец применяют вы- сококачественные перлитные чугуны, легированные хро- мом, молибденом, вольфрамом или ванадием, а также мо- дифицированный чугун. Наряду с чугунными поршневыми кольцами в некоторых конструкциях двигателей применя- ют стальные маслосъемные кольца, а также металлокера- мические поршневые кольца.
Стальные кольца изготавливают из стальной поли- рованной ленты толщиной от 0,5 до 0,76 мм и шириной от 2,92 до 4,75 мм. После навивки ленты по спирали и от- резания участков спирали, соответствующих размерам заготовки поршневого кольца, производят термообработку (термофиксацию) заготовок посредством их нагрева до температуры 215 °С в течение получаса. Недостатком
418
этих поршневых колец является то, что они теряют упру- гость при высоких температурах.
Металлокерамические поршневые кольца изготавли- вают из антифрикционных пористых железографитовых сплавов прессованием порошковой смеси с последующим спеканием. Полученные таким методом поршневые кольца обладают высокой износостойкостью, но недостаточной упругостью.
Отливки чугунных поршневых колец получают в ви- де индивидуальных отливок или маслот (трубчатых отли- вок на несколько колец). Литье заготовок чугунных порш- невых колец в виде маслот является наиболее простым спо- собом получения заготовок, но при этом способе возможна неравномерность структуры, твердости и толщины колец. Поэтому в современном производстве поршневых колец маслоты применяют крайне редко.
Индивидуальные заготовки поршневых колец отли- вают стопочным методом, то есть расположением несколь- ких опок (12–18) со стопкой из 6–8 поршневых колец в ка- ждой опоке с единой литниковой системой и питателями. После заливки, охлаждения и выбивки опок стопочная от- ливка имеет вид стержня с расположенными в вертикаль- ном направлении по его периметру отливками индивиду- альных заготовок поршневых колец.
Применение индивидуальных отливок наряду с обес- печением плотной мелкозернистой структуры металла и равномерной твердости заготовки снижает трудоемкость механической обработки, так как отход металла в стружку в 2–3 раза меньше, чем при изготовлении поршневых ко- лец из маслот.
Технические требования к механической обработке поршневых колец сводятся к следующему.
419
Точность обработки по высоте кольца выдерживают в пределах 7–8-го квалитета, шероховатость поверхности
торцов Ra ≤ 1,25 мкм. Допуск на ширину прорези в замке в сжатом состоянии кольца 0,1–0,2 мм. Отклонение от па- раллельности торцовых поверхностей допускается в преде- лах допуска на высоту кольца. Радиальная разностенность не более 0,1 мм. Шероховатость внешней боковой поверхно-
сти кольца Ra ≤ 2,5 мкм.
Технические требования предусматривают проверку кольца на коробление, на прилегание к зеркалу цилиндра и на упругость. Коробление торцовых поверхностей не должно превышать 0,05–0,07 мм. Контроль осуществ- ляется следующим образом. Две плоские полированные плиты устанавливаются параллельно друг другу на рас- стоянии, равном сумме наибольшей предельной высоты кольца и допуска на коробление. Годное кольцо должно под собственным весом провалиться между плитами.
Прилегание кольца к зеркалу цилиндра проверяется путем установки его в отверстие кольцевого калибра диа- метром, равным наибольшему предельному размеру гиль- зы. Местный радиальный зазор (просвет) между испыты- ваемым кольцом и калибром не должен превышать 0,02 мм на отдельных участках. Для поршневых колец не- которых двигателей зазор (просвет) при таком контроле не допускается.
Упругость поршневого кольца проверяется сжатием его силой, направленной перпендикулярно диаметральной линии, проходящей через замок, до получения в замке зазо- ра, соответствующего зазору кольца в цилиндре. Это уси- лие обычно находится в пределах 20–80 Н.
420