
книги / Основы технологии машиностроения. Методы обработки заготовок и технологические процессы изготовления типовых деталей машин
.pdfОсновными базами шпинделя являются его опорные шейки, но так как использовать их в качестве технологиче- ской базы в последующем не представляется возможным, то, пользуясь ими, вначале осуществляют подрезку (фрезе- рование) торцов и центрование (выполнение центровых отверстий). Поверхности центров служат в дальнейшем технологическими базами.
Технологическая схема обработки шпинделя токар- ного станка приведена в табл. 12.5.
Т а б л и ц а 1 2 . 5
Технологический маршрут обработки шпинделя токарного станка
Номер |
Краткое содержание |
Выбор баз |
Назначение операции |
|
операции |
операции |
|||
|
|
|||
1 |
2 |
3 |
4 |
|
|
Фрезерование (подрезка) |
Наружные |
Обеспечение точного |
|
|
торцов и центрование на |
поверхности |
расположения цен- |
|
05 |
фрезерно-центровальном |
необработан- |
тров, выбранных |
|
|
или токарном станке |
ных шеек |
в качестве технологи- |
|
|
|
|
ческой базы |
|
|
Черновое точение на- |
Поверхности |
Обеспечение концен- |
|
|
ружных поверхностей |
центров |
тричности наружной |
|
|
шеек до фланца |
|
поверхности шеек |
|
10 |
с предварительной его |
|
со стороны хвостовой |
|
подрезкой на токарно- |
|
части шпинделя |
||
|
|
|||
|
гидрокопировальном |
|
|
|
|
станке или на токарном |
|
|
|
|
станке с ЧПУ |
|
|
|
|
Чистовое точение на- |
Поверхности |
Обеспечение концен- |
|
|
ружных поверхностей |
центров |
тричности наружной |
|
|
шеек до фланца под |
|
поверхности шеек |
|
20 |
шлифование и прорезка |
|
со стороны хвостовой |
|
канавок на токарно- |
|
части шпинделя |
||
|
|
|||
|
гидрокопировальном |
|
|
|
|
станке или токарном |
|
|
|
|
станке с ЧПУ |
|
|
|
|
|
|
301 |
П р о д о л ж е н и е т а б л . 1 2 . 5
1 |
2 |
3 |
4 |
|
|
|
|
|
Чистовое точение на- |
Поверхности |
Обеспечение концен- |
|
ружной поверхности |
центров |
тричности наружной |
30 |
на токарно-гидрокопиро- |
|
поверхности шеек |
|
вальном станке или то- |
|
со стороны головной |
|
карном станке с ЧПУ |
|
части шпинделя |
|
|
|
|
|
Сверление осевого от- |
Наружные |
Обеспечение концен- |
|
верстия с одной стороны |
поверхности |
тричности наружных |
|
на длину более половины |
обработан- |
и внутренних поверх- |
|
длины шпинделя и с дру- |
ных шеек |
ностей |
|
гой стороны на проход |
|
|
|
на вертикально- |
|
|
40 |
сверлильном или на то- |
|
|
|
карном станке, либо |
|
|
|
сверление с одной сторо- |
|
|
|
ны на проход ружейным |
|
|
|
или артиллерийским |
|
|
|
сверлом на станке для |
|
|
|
глубокого сверления |
|
|
|
|
|
|
|
Зенкерование конусного |
Наружные |
Обеспечение концен- |
|
отверстия со стороны |
поверхности |
тричности наружных |
|
головной части шпинде- |
обработан- |
и внутренних поверх- |
50 |
ля (коническим зенке- |
ных шеек |
ностей |
|
ром) на вертикально- |
|
|
|
сверлильном или на |
|
|
|
токарном станке |
|
|
|
|
|
|
|
Растачивание переднего |
Наружные |
Подготовка техноло- |
|
и заднего конических |
поверхности |
гической базы для |
60 |
отверстий и подрезка |
обработан- |
отделочной обработки |
|
торцов на токарном |
ных шеек |
поверхностей |
|
станке |
|
|
|
|
|
|
|
Сверление отверстий |
Поверхность |
|
|
и нарезание резьбы |
конуса |
|
70 |
во фланце на вертикаль- |
отверстия |
— |
но-сверлильном или на |
|
||
|
|
|
|
|
радиально-сверлильном |
|
|
|
станке |
|
|
|
|
|
|
302 |
|
|
|
П р о д о л ж е н и е т а б л . 1 2 . 5
1 |
2 |
|
3 |
4 |
|
|
Термическая обработка: |
|
|
||
|
закалка поверхностей |
|
|
||
|
шеек, внутреннего |
|
|
||
80 |
и наружного конусов |
— |
— |
||
и торца фланца на уста- |
|||||
|
|
|
|||
|
новке ТВЧ. Твердость |
|
|
||
|
HRC 48–52. |
|
|
|
|
|
Низкотемпературный |
|
|
||
|
Предварительноеотпуск |
шли- |
Поверхность |
Обеспечение концен- |
|
|
фование наружных по- |
конуса |
тричности шеек |
||
90 |
верхностей шеек с при- |
отверстия |
с осью шпинделя |
||
|
пуском на круглошлифо- |
|
|
||
|
вальном станке |
|
|
|
|
|
Предварительное шли- |
Поверхности |
Обеспечение концен- |
||
|
фование наружного ко- |
зацентрован- |
тричности шеек |
||
|
нуса на пробках |
|
ных отвер- |
с осью шпинделя |
|
100 |
в центрах круглошлифо- |
стий пробок, |
|
||
|
вального станка |
|
вставленных |
|
|
|
|
|
в конусные |
|
|
|
|
|
отверстия |
|
|
|
Нарезание резьбы под |
Поверхности |
Обеспечение пра- |
||
|
гайки и подрезка торцов |
зацентрован- |
вильности располо- |
||
|
навернутых на шпиндель |
ных отвер- |
жения резьбы |
||
110 |
упорных гаек на токар- |
стий пробок, |
и канавок относи- |
||
|
но-винторезном станке |
вставленных |
тельно опорных шеек |
||
|
|
|
в конусные |
|
|
|
|
|
отверстия |
|
|
|
Фрезерование шлицев |
Поверхности |
Обеспечение пра- |
||
|
на шлицефрезерном |
зацентрован- |
вильности располо- |
||
|
станке |
|
ных отвер- |
жения шлицев отно- |
|
120 |
|
|
стий пробок, |
сительно опорных |
|
|
|
|
вставленных |
шеек |
|
|
|
|
в конусные |
|
|
|
|
|
отверстия |
|
|
|
Фрезерование шпоноч- |
Поверхности |
Обеспечение пра- |
||
|
ной канавки на шпоноч- |
зацентрован- |
вильности располо- |
||
|
но-фрезерном станке |
ных отвер- |
жения шпоночного |
||
130 |
|
|
стий пробок, |
паза относительно |
|
|
|
|
вставленных |
опорных шеек |
|
|
|
|
в конусные |
|
|
|
|
|
отверстия |
|
|
|
|
|
|
303 |
О к о н ч а н и е т а б л . 1 2 . 5
1 |
2 |
3 |
4 |
|
|
Сверление двух отвер- |
Поверхности |
Обеспечение пра- |
|
|
стий под стопор на вер- |
зацентрован- |
вильности располо- |
|
|
тикально-сверлильном |
ных отвер- |
жения стопоров отно- |
|
140 |
станке |
стий пробок, |
сительно опорных |
|
|
|
вставленных |
шеек |
|
|
|
в конусные |
|
|
|
|
отверстия |
|
|
|
Отделочное шлифование |
Поверхности |
Обеспечение концен- |
|
|
наружных поверхностей |
зацентрован- |
тричности шеек отно- |
|
|
шеек на круглошлифо- |
ных отвер- |
сительно оси шпин- |
|
150 |
вальном станке |
стий пробок, |
деля |
|
|
|
вставленных |
|
|
|
|
в конусные |
|
|
|
|
отверстия |
|
|
|
Чистовое шлифование |
Поверхности |
Обеспечение концен- |
|
|
наружного конуса |
зацентрован- |
тричности поверхно- |
|
|
на круглошлифовальном |
ных отвер- |
сти конуса относи- |
|
160 |
станке |
стий пробок, |
тельно оси шпинделя |
|
|
|
вставленных |
|
|
|
|
в конусные |
|
|
|
|
отверстия |
|
|
|
Отделочное шлифование |
Наружные |
Обеспечение концен- |
|
|
поверхности конуса |
поверхности |
тричности поверхно- |
|
170 |
под патрон и торца |
шеек |
сти конуса относи- |
|
|
фланца на круглошлифо- |
|
тельно оси шпинделя |
|
|
вальном станке |
|
|
|
|
Отделочное шлифование |
Наружные |
Обеспечение концен- |
|
180 |
поверхности внутреннего |
поверхности |
тричности поверхно- |
|
конуса на внутришлифо- |
шеек |
сти конуса относи- |
||
|
||||
|
вальном станке |
|
тельно оси шпинделя |
|
190 |
Контроль шпинделя |
— |
— |
Черновую обработку осевого отверстия шпинделя обычно выполняют на специальных станках типа РТ-54 для глубокого сверления. Технологическими базами являются поверхности двух шеек шпинделя, одну из которых зажи- мают в патроне станка, а другую устанавливают в люнет. Осевые отверстия в зависимости от диаметра обрабатывают специальными сверлами (ружейными, пушечными, перо-
304
выми, кольцевыми) и резцовыми головками. Отверстия больших диаметров обрабатывают многорезцовыми рас- точными головками.
После выполнения черновых операций заготовку шпинделя направляют на термическую обработку (нормали- зацию и улучшение), способствующую перераспределению внутренних напряжений (после удаления слоя металла) и улучшению обрабатываемости заготовки. Термообработка завершается операцией правки на правильных станках.
После правки производят чистовую обработку осево- го отверстия на станках для глубокого сверления, так же, как при черновой обработке. Эта операция является очень ответственной, так как она должна обеспечить концентрич- ность и соосность наружных поверхностей с поверхностя- ми осевого отверстия, являющегося технологической базой при последующей обработке наружных поверхностей.
Чистовую обработку наружных поверхностей выпол- няют так же, как и черновую, на токарно-копировальных станках типа МР-24. Припуск, оставляемый для чистовой обработки, составляет 0,25–0,4 мм на сторону.
После чистовой обработки наружных и внутренних по- верхностей обрабатывают шлицы на горизонтальном шли- цефрезерном полуавтомате типа 5350Б червячной шлицевой фрезой. Шпоночные канавки обрабатывают торцовыми, дис- ковыми или концевыми фрезами на универсальных фрезер- ных станках или на специальных шпоночно-фрезерных полу- автоматах типа 692А. Точность углового расположения шпо- ночных канавок обеспечивают делительной головкой, если шпиндель устанавливают в центрах, или делительным дис- ком, надеваемым на шейку шпинделя и закрепляемым сто- порным болтом. Далее обрабатывают отверстия во фланце, а также нарезают резьбу. В качестве технологических баз при сверлении и нарезании резьбы используют основные базы шпинделя. То, что отклонение от соосности отверстий нахо-
305
дится в пределах допуска, достигается накладными приспо- соблениями, центрируемыми по конусу фланца.
В зависимости от марки стали полностью обработан- ную (начерно и начисто) заготовку шпинделя подвергают термической обработке. Наиболее распространенным спо- собом такой обработки является поверхностная закалка с применением нагрева токами высокой частоты (ТВЧ). При этом способе тепло образуется в поверхностном слое обрабатываемой заготовки, и температура основной массы металла вследствие кратковременности нагрева (0,5–20 с) не изменяется, что предохраняет заготовку от деформации и предотвращает образование окалины. Глубину закаленного слоя можно автоматически регулировать в пределах 1–5 мм. Твердость закаленного слоя HRC 48–52 постепенно снижа- ется от наружной поверхности заготовки к ее оси.
К числу ответственных операций относится отделка наружных поверхностей шпинделя. Эту операцию выпол- няют на шлифовальных станках типа 3161Т и обычно подразделяют на предварительную и окончательную. Ме- жду этими операциями шпиндели подвергают естествен- ному старению путем вылеживания в течение 2–12 часов, а шпиндели высокоточных станков иногда подвергают искусственному старению. Шпиндели шлифуют на круг- лошлифовальных станках с применением мелкозернистых кругов. Для обеспечения соосности и концентричности наружных и внутренних поверхностей используют по- верхности осевого отверстия шпинделя. Кроме шлифова- ния, поверхности шеек шпинделя, которые работают в опорах скольжения, подвергают суперфинишированию.
После отделки шеек шпинделя приступают к отделоч- ной обработке осевого отверстия на внутришлифовальном станке, используя в качестве технологической базы поверх- ности передней опорной шейки, устанавливаемой в люнете,
306
ишейки противоположного конца шпинделя, зажимаемой в самоцентрирующемся трехкулачковом патроне.
Завершающей операцией обработки шпинделя явля- ется балансировка. Шпиндели быстроходных станков вы- сокой точности, особо высокой точности и прецизионных станков балансируют в собранном виде. Погрешности изго- товления и монтажа шпиндельного узла, а также различная плотность металла деталей, входящих в шпиндельный узел, приводят к неуравновешенности, что может вызвать появ- ление вибраций при эксплуатации. Вибрации снижают стойкость режущего инструмента, ухудшают качество об- рабатываемых поверхностей и увеличивают износ опор подшипников и шеек шпинделя.
Неуравновешенность может быть статической, когда центр тяжести шпиндельного узла не совпадает с осью вращения (она вызывает возникновение центробежной си- лы) и динамической, когда действие неуравновешенных масс вызывает появление пары сил и центробежных мо- ментов, не равных нулю. Для устранения неуравновешен- ности шпиндельный узел необходимо балансировать в соб- ранном виде. В соответствии с двумя видами неуравнове- шенности существует два вида балансировок – статическая
идинамическая.
Статическую балансировку применяют для деталей, у которых отношение длины к диаметру менее единицы (маховики, диски, зубчатые колеса).
У шпинделей металлорежущих станков отношение длины к диаметру во много раз более единицы. В связи с тем, что на шпинделе станка монтируют целый ряд деталей (зубчатые колеса, гайки, подшипники, фланцы и т.д.), для шпиндельного узла в сборе характерны оба вида неуравно- вешенности. Поэтому шпиндельный узел в сборе подверга- ют динамической балансировке, которая устраняет их.
307
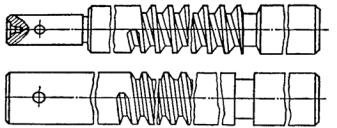
Динамическую балансировку производят на специ- альных балансировочных станках. Допускаемый дисбаланс от 10 до 50 г см (в зависимости от размера шпиндельного узла и числа оборотов).
12.3.2. Технологические процессы обработки ходовых винтов
Ходовые винты станков служат для преобразования вращательного движения винта в поступательное переме- щение (с помощью сопряженной с ним гайки) различных узлов станка (суппортов, кареток, фартуков, столов и др.) с заданной точностью.
На рис. 12.17 показан внешний вид ходовых винтов металлорежущих станков.
Рис. 12.17. Ходовые винты металлорежущих станков
Ходовые винты металлорежущих станков имеют дли- ну, более чем в 30 раз превышающую диаметр, и глубокие винтовые канавки на большей части тела винта. Жесткость этих ходовых винтов очень мала, поэтому необходимы спе- циальные приемы их обработки, транспортировки и хране- ния. Эти приемы могут служить примером изготовления не- жестких деталей со сложной многократной обработкой.
Основной технологической задачей при изготовле- нии ходовых винтов металлорежущих станков является получение точной резьбы, соосной с опорными шейками и буртиками.
308
Ходовые винты в зависимости от степени точности перемещения, которую они обеспечивают, делятся на пять классов: 0, 1, 2, 3, 4.
Вметаллорежущих станках в основном применяют ходовые винты 0–3-го классов точности. Ходовые винты класса точности 0–1 применяют в прецизионных резьбо- шлифовальных, координатно-расточных станках и точных приборах. Винты класса точности 2 – в токарно-затыловоч- ных, прецизионных токарно-винторезных станках и дели- тельных механизмах зубообрабатывающих станков. Винты класса точности 3 применяют в токарно-винторезных, резь- бофрезерных и других станках нормальной точности. Винты 4-го класса точности применяют для прочих станков, ис- пользуемых для предварительной обработки заготовок.
Профиль резьбы ходовых винтов может быть прямо- угольным, полукруглым, трапецеидальным и треугольным. Винты с трапецеидальным профилем позволяют с помо- щью разрезной гайки регулировать осевые зазоры.
Втабл. 12.6 приведены основные технические усло- вия на изготовление ходовых винтов.
Т а б л и ц а 1 2 . 6
Технические условия изготовления ходовых винтов
|
|
|
Допускаемое |
Допускаемая |
|
|
|
Накопленная |
овальность |
|
|
Класс |
|
отклонение |
сечения |
|
|
Допускаемая |
ошибка |
половины |
Шероховатость |
||
точ- |
ошибка ша- |
в шаге на |
угла профиля |
по среднему |
поверхности |
ности |
га, мкм |
всей длине |
резьбы, мин |
диаметру |
по Ra, мкм |
винта |
резьбы, мкм |
||||
|
|
винта, мкм |
(шаг |
(при длине |
|
|
|
|
6–10 мм) |
|
|
|
|
|
винта 1–2 м) |
|
|
|
|
|
|
|
|
0 |
±2 |
8 |
10 |
40 |
0,08– 0,16 |
1 |
±3 |
20 |
12 |
60 |
0,16–0,32 |
2 |
±6 |
40 |
18 |
100 |
0,63–1,25 |
3 |
±12 |
80 |
25 |
150 |
1,25–2,5 |
4 |
±25 |
150 |
— |
250 |
1,25–2,5 |
309
Наружный диаметр ходовых винтов классов 0, 1, 2 выполняют по посадке h6; класса 3 – по посадке h7; клас- са 4 – по посадке h8. Шероховатость поверхности опорных шеек Ra = 0,32…0,63 мкм.
Основные трудности при изготовлении ходовых вин- тов связаны с особенностью их формы. Эти особенности формы винтов способствуют появлению деформаций при обработке. Деформации появляются из-за недостаточной жесткости винта при приложении сил резания, из-за внут- ренних напряжений в металле при нарезании резьбы, из-за изменения температуры при обработке. Деформации можно уменьшить правильным подбором металла и термообработ- кой, созданием простых, технологичных конструкций вин- тов, уменьшением колебаний температуры в производствен- ных помещениях, транспортировкой и хранением в верти- кальном положении.
Для закаливаемых и шлифуемых ходовых винтов классов точности 0 и 1 применяют стали У10А, ХВГ и 65Г; для термически необрабатываемых винтов – калиброван- ную горячекатаную сталь А40Г.
Заготовки получают из прутков сортового материала, разрезанных на куски, соответствующие длине винта. Прут- ки горячекатаной стали до разрезания на куски правят на правильном станке и обтачивают на бесцентрово-токар- ном станке. Прутки из калиброванного материала до разре- зания не обрабатывают.
Припуски на обработку назначают в зависимости от размера диаметра винта с учетом возможных деформа- ций при черновой обработке и необходимости перецен- тровки. В среднем для винтов диаметром 40–50 мм дается припуск 5–7 мм на сторону, для винтов диаметром свы- ше 50 мм – 6…8 мм на сторону. По сортаменту прутково- го материала соответствующей марки подбирают бли- жайший по размеру диаметр прутка.
310