
книги / Основы технологии машиностроения. Методы обработки заготовок и технологические процессы изготовления типовых деталей машин
.pdfНа первых операциях черновой базой служит наруж- ная поверхность прутка. Поскольку необходимо получить соосность опорных шеек, буртиков и винта, то при даль- нейшей обработке базой служат центровые отверстия.
Для устранения деформации винта при обработке под действием сил резания и силы тяжести применяют люнеты, то есть в качестве направляющей базы используют наруж- ную поверхность винта. Эта поверхность должна быть тща- тельно обработана на первых операциях.
Как правило, обработку ходовых винтов производят в следующей последовательности, применяя поименован- ное ниже оборудование:
–отрезают заготовку от прутка – в большинстве случа- ев на отрезном станке ленточными или дисковыми пилами;
–подрезают торцы и центрируют на токарных стан- ках в люнетах при длине винта свыше 1,5 м. При длине за- готовки до 1,5 м эту операцию можно выполнять на фре- зерно-центровальном станке;
–обрабатывают начерно наружную поверхность вин- та на токарном станке за две установки с люнетом (с пово- ротом винта на 180°). Припуск на последующую обработку оставляют в пределах 3,5–4 мм;
–после чернового точения применяют искусственное старение, чтобы снять внутренние напряжения в материале винта, вызванные правкой прутков и черновой обработкой. Например, режим старения для винта из стали У10А: на- грев до температуры 550 °С со скоростью 75 град/ч, вы- держка при этой температуре 7–8 часов и охлаждение с пе- чью со скоростью 75 град/ч. При обработке винт подвеши- вают вертикально;
– выполняют перецентровку центровых отверстий, в том же порядке и на тех же режимах, как описано выше; базируясь на центровых отверстиях, выполняют чистовую токарную обработку под шлифование, так как из-за дефор-
311
маций винта при черновой обработке изменяется положе- ние осей и повреждаются при термообработке центровые отверстия. Чистовую токарную обработку наружных по- верхностей винта выполняют с припуском под предвари- тельное шлифование 0,3–0,4 мм на сторону;
–шпоночные канавки обрабатывают на шпоночно- фрезерном станке при установке винта на призмы;
–шлифуют предварительно опорные шейки, буртики
иповерхности под резьбу за две установки;
–нарезают резьбу на прецизионных токарно- винторезных станках с низкими режимами резания (ско- рость резания 2–3 м/мин, поперечная подача 0,04–0,06 мм на проход). Припуск под получистовое шлифование 0,5– 0,6 мм на сторону;
–второй раз искусственно старят в том же порядке
ина тех же режимах, как описано выше;
–перецентровывают центровые отверстия в том же порядке и на тех же режимах, как описано выше;
–проводят получистовое шлифование профиля резь- бы на резьбошлифовальном станке с припуском на чисто- вое шлифование 0,2–0,3 мм на сторону;
–выполняют чистовое шлифование наружной по- верхности винта на круглошлифовальном станке в люнетах в пределах поля допуска на изготовление;
– делают чистовое шлифование профиля резьбы на резьбошлифовальном станке в пределах поля допуска на изготовление резьбы;
–осуществляют третью термическую обработку (ста- рение) в электропечи с нагревом до 160 ±10 ° С. Винт вы- держивают при этой температуре 36 ч. На все термообра- ботки партии винтов затрачивается порядка 80 ч;
–доводят резьбу чугунным притиром с использова- нием паст ГОИ;
–производят окончательный контроль ходового винта.
312
В табл. 12.7 приведен технологический маршрут об- работки прецизионного ходового винта (материал винта – сталь У10А). Менее точные винты обрабатывают по более простому маршруту.
Т а б л и ц а 1 2 . 7
Технологический маршрут обработки ходового винта
Номер |
Краткое содержа- |
Применяемое |
Технологические |
|
операции |
ние операции |
оборудование |
базы |
|
1 |
2 |
3 |
4 |
|
05 |
Отрезание заго- |
Отрезной станок |
Наружная |
|
товки по длине |
|
поверхность |
||
|
|
|||
10 |
Подрезание |
Токарный станок |
Наружная |
|
торцов |
с люнетом |
поверхность |
||
|
||||
20 |
Центрование |
Токарный станок |
Наружная |
|
торцов |
с люнетом |
поверхность |
||
|
||||
|
Черновая токарная |
|
Центровые |
|
30 |
обработка наруж- |
Токарный станок |
отверстия. |
|
ных поверхностей |
с люнетом |
Наружная поверх- |
||
|
||||
|
за две установки |
|
ность |
|
|
1-я термическая |
|
|
|
40 |
обработка |
Электропечь |
— |
|
|
(старение) |
|
|
|
|
Перецентровка |
|
Наружная |
|
50 |
(за две установки) |
Токарный станок |
поверхность. |
|
и чистовое точение |
с люнетом |
Центровые |
||
|
||||
|
под шлифование |
|
отверстия |
|
|
Обработка шпо- |
|
Наружная |
|
|
ночных канавок |
Шпоночно-фрезерный |
||
60 |
поверхность. |
|||
(если они есть |
станок |
|||
|
Призмы |
|||
|
на чертеже) |
|
||
|
|
|
||
|
Предварительное |
|
Центровые |
|
|
шлифование |
|
||
|
Круглошлифовальный |
отверстия. |
||
70 |
наружной |
|||
станок с люнетами |
Наружная |
|||
|
поверхности |
|||
|
|
поверхность |
||
|
за две установки |
|
||
|
|
|
||
|
Предварительное |
Прецизионный токарно- |
Центровые |
|
80 |
нарезание резьбы |
винторезный станок |
отверстия. |
|
|
Наружная |
|||
|
|
с люнетами |
||
|
|
поверхность |
||
|
|
|
||
|
2-я термическая |
|
|
|
90* |
обработка |
Электропечь |
— |
|
|
(старение) |
|
|
|
|
|
|
313 |
О к о н ч а н и е т а б л . 1 2 . 7
1 |
2 |
3 |
4 |
|
|
Исправление |
Токарный станок |
Наружная |
|
100 |
центровых |
|||
с люнетом |
поверхность |
|||
|
отверстий |
|||
|
|
|
||
|
Получистовое |
|
Центровые |
|
110 |
шлифование |
Круглошлифовальный |
отверстия. |
|
наружной |
станок с люнетами |
Наружная |
||
|
||||
|
поверхности |
|
поверхность |
|
|
Получистовое |
Резьбошлифовальный |
Центровые |
|
120 |
шлифование про- |
|||
станок |
отверстия |
|||
|
филя резьбы |
|||
|
|
|
||
|
Чистовое шлифо- |
|
Центровые |
|
130 |
вание наружной |
Круглошлифовальный |
отверстия. |
|
поверхности |
станок с люнетами |
Наружная |
||
|
||||
|
|
|
поверхность |
|
|
Чистовое шлифо- |
Резьбошлифовальный |
Центровые |
|
140 |
вание профиля |
|||
станок |
отверстия |
|||
|
резьбы |
|||
|
|
|
||
|
3-я термическая |
|
|
|
150 |
обработка |
Электропечь |
— |
|
|
(старение) |
|
|
|
160 |
Доводка резьбы |
Токарный станок |
Центровые |
|
|
отверстия |
|||
|
|
|
||
170 |
Доводка опорных |
Токарный станок |
Центровые |
|
шеек |
отверстия |
|||
|
|
|||
180 |
Контроль винта |
— |
— |
* Примечание. При изготовлении ходовых винтов из стали ХВГ их подвергают упрочнению. Упрочнение винтов до твердости HRC 57–60 обеспечивается объемной закалкой в шахтной соля- ной ванне в вертикальном подвешенном положении при ступен- чатом нагреве: сначала нагревают до температуры 550–600 °С и выдерживают в течение одного часа, затем постепенно увели- чивают температуру до 840–850 °С.
Закалка производится в масле, подогретом до 50 °С. После закалки предусмотрен отпуск.
Термическая обработка, закалка, отпуск (вместе с об- разцами-свидетелями) ходовых винтов производятся после предварительного нарезания резьбы на операции 90* (вме- сто операции старения ходового винта из стали У10А).
314
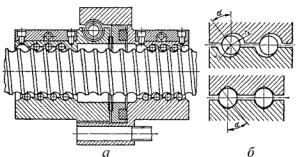
Предварительное шлифование профиля резьбы про- изводится многониточным шлифовальным кругом 44А (8-16)П М(1-2) (8-12)К. Окончательное шлифование про- филя резьбы производится на прецизионных резьбошифо- вальных станках типа 5Д822В однониточным шлифоваль- ным кругом Л12-Л25 СМ1-СМ2 8 К 100 %.
В настоящее время широко применяют передачи винт – гайка качения (ВГК), иногда называемые шарико- выми передачами. Эти передачи применяются в приводах подач точных станков: координатно-расточных, копиро- вальных и станков с программным управлением, в приво- дах для перемещения тяжелых узлов – траверз, стоек и т.п. На рис. 12.18 показана передача винт – гайка качения по ГОСТ 25329–82.
Рис. 12.18. Передача винт – гайка качения
Преимуществами передач ВГК по сравнению с обыч- ными винтовыми передачами являются:
–малый зазор в резьбе;
–возможность создания натяга, обеспечивающего осевую жесткость;
–высокий КПД передачи (до 0,95–0,98);
–постоянство силы трения при изменении скорости вращения и малая сила трения покоя.
315
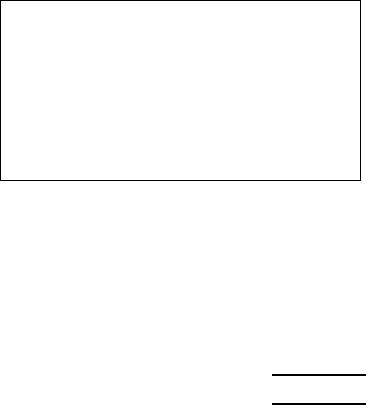
При изготовлении винта передачи ВГК длиной 1,5 м из стали ХВГ следует выдерживать следующие техниче- ские условия.
Точность регулирования натяга....................................... |
|
1–2 мкм |
Поверхностная твердость ............................................ |
|
HRC 60–63 |
Шероховатость поверхности резьбы ................ |
|
R a = 0,32…0,63 мкм |
Погрешность шага для винта класса 1 .................................... |
|
±3 мкм |
Накопленная погрешность шага, не более |
........................ 20 мкм |
|
Колебание величины рабочего диаметра |
|
|
резьбы, соответствующего точкам |
|
|
касания шариков на длине 1 м, не более............................... |
|
5–8 мкм |
Овальность, конусность, |
|
|
бочкообразность и другие |
|
|
погрешности формы, не выше................... |
0,01 мм на всей ее длине |
Общий припуск на обработку заготовки составляет от 10–15 до 12–20 мм на диаметр в зависимости от величи- ны диаметра и непрямолинейности заготовки.
Примерный технологический маршрут обработки для винта диаметром 50 мм, длиной 1650 мм из стали ХВГ при- веден в табл. 12.8.
Т а б л и ц а 1 2 . 8
Технологический маршрут обработки ходового винта передачи ВГК
Номер |
Краткое содержа- |
Применяемое |
Технологические |
|
операции |
ние операции |
оборудование |
базы |
|
1 |
2 |
3 |
4 |
|
05 |
Отрезание |
Отрезной станок |
Наружная |
|
заготовки по длине |
поверхность |
|||
|
|
|||
10 |
Подрезание |
Токарный станок |
Наружная |
|
торцов |
с люнетом |
поверхность |
||
|
||||
20 |
Центрование |
Токарный станок |
Наружная |
|
торцов |
с люнетом |
поверхность |
||
|
||||
|
Черновая токарная |
|
|
|
30 |
обработка наруж- |
Токарный станок |
Центровые |
|
ных поверхностей |
с люнетом |
отверстия |
||
|
||||
|
за две установки |
|
|
|
316 |
|
|
|
О к о н ч а н и е т а б л . 1 2 . 8
1 |
2 |
3 |
4 |
|
|
Нарезание резьбы |
Прецизионный |
Центровые |
|
40 |
твердосплавным |
токарно-винторезный |
||
отверстия |
||||
|
резцом ВК6М |
станок с люнетом |
||
|
|
|||
|
Термическая: |
|
|
|
50 |
закалка до твердо- |
Шахтная печь |
— |
|
|
сти HRC 60–63 |
|
|
|
|
Предварительное |
|
|
|
60 |
шлифование на- |
Круглошлифовальный |
Центровые |
|
ружного диаметра |
станок |
отверстия |
||
|
||||
|
резьбы и шеек |
|
|
|
|
Окончательное |
|
|
|
70 |
шлифование на- |
Круглошлифовальный |
Центровые |
|
ружного диаметра |
станок |
отверстия |
||
|
||||
|
резьбы и шеек |
|
|
|
|
Окончательное |
Резьбошлифовальный |
Центровые |
|
80 |
шлифование про- |
|||
станок |
отверстия |
|||
|
филя резьбы |
|||
|
|
|
12.3.3. Технологические процессы обработки коленчатых валов
Коленчатые валы входят в число наиболее ответст- венных деталей двигателей внутреннего сгорания. По кон- струкции коленчатые валы делят на цельные и составные. Цельные коленчатые валы применяют в автомобильных, тракторных и авиационных двигателях, в средних стацио- нарных и передвижных двигателях внутреннего сгорания, компрессорах, эксцентриковых прессах.
На рис. 12.19 показаны коленчатые валы автомо- бильных и тракторных двигателей.
Составные коленчатые валы применяют в крупных судовых и стационарных двигателях внутреннего сгорания. Их изготавливают в незначительных количествах в услови- ях, как правило, единичного производства.
317

Рис. 12.19. Коленчатые валы автомобильных и тракторных двигателей: а – малолитражного автомобиля; б – грузового автомобиля; в – трактора малой мощности;
г – трактора средней мощности
Коленчатые валы двигателей обычно имеют несколь- ко (2–8) опорных коренных шеек и до 8 шатунных шеек. Ко- ленчатые валы изготовляют с противовесами или без них. Кривошипы валов располагают под углом 120 или 180°, ре- же – под углом 90°. Размеры коленчатых валов автомобиль- ных и тракторных двигателей: длина вала 500–1500 мм; диаметр коренных шеек 50–100 мм, их длина 30–100 мм; диаметр шатунных шеек 45–95 мм, их длина 45–95 мм; ра- диус кривошипа 35–110 мм, диаметр фланца 110–200 мм.
Основные технологические задачи при обработке ко- ленчатых валов сводятся к тому, чтобы получить соосные коренные шейки высокой точности, точные шатунные шейки, расположенные под соответствующими углами од- на относительно другой и на одинаковом расстоянии от оси коренных шеек, а также достичь хорошей уравновешенно- сти всего коленчатого вала при вращении вокруг оси ко- ренных шеек.
Основные технические условия на изготовление ко- ленчатых валов автомобильных и тракторных двигателей приведены в табл. 12.9.
318
Т а б л и ц а 1 2 . 9
Основные технические условия на изготовление коленчатых валов
Показатель |
Автомобильные |
Тракторные |
|
двигатели |
двигатели |
||
|
|||
Точность диаметра шеек |
5–7-й квалитет |
8-й квалитет |
|
Шероховатость |
Ra ≤ 0,16 мкм |
Ra ≤ 0,32 мкм |
|
поверхности шеек |
|||
|
|
||
Отклонение |
0,006–0,01 мм |
Не более 0,015 мм |
|
от круглости шеек |
|||
|
|
||
Отклонение |
0,01 мм на длине шейки |
0,03 мм |
|
от цилиндричности шеек |
на длине100 мм |
||
|
|||
Огранка шеек |
0,004–0,008 мм |
0,005–0,01 мм |
|
Отклонение от параллель- |
|
0,02–0,03 мм |
|
ности осей шатунных |
0,01 мм на длине шейки |
||
на длине 100 мм |
|||
и коренных шеек |
|
|
|
Допуск на расстояние |
|
|
|
между осями коренных |
0,08–0,15 мм |
0,1–0,2 мм |
|
и шатунных шеек |
|||
|
|
||
(радиус кривошипа) |
|
|
|
Твердость поверхности |
HRC 52–62 |
HRC 50–60 |
|
закаленных шеек |
|||
|
|
||
Точность динамической |
Не более 15 г см |
30–40 г см |
|
балансировки |
|||
|
|
Материалы коленчатых валов автомобильных и трак- торных двигателей должны обладать хорошими механиче- скими и пластическими свойствами, высокими износо- устойчивостью и циклической выносливостью. Коленчатые валы автомобильных и тракторных двигателей изготавли- вают из углеродистых и легированных сталей или из высо- копрочных чугунов, модифицированных магнием, никелем или молибденом. Литые валы обычно полые, имеют не- сколько увеличенные диаметры коренных и шатунных ше- ек, большую толщину щек и большие радиусы галтелей. Литые коленчатые валы имеют меньшую прочность при изгибе, чем кованые валы. Внутренние полости литых ва- лов обычно бочкообразные, благодаря чему уменьшается
319
неравномерность толщины тела вала в разных сечениях
иповышается качество отливки. Масса литых коленчатых валов на 10–15 % меньше, чем штампованных заготовок.
Большинство коленчатых валов изготавливают из ста- лей 45, 45Х, 45Г2, 50Г. Коленчатые валы судовых дизелей
иавиационных двигателей, работающие в условиях высо- ких нагрузок, изготавливают из хромоникелевых сталей 18ХНМА, 18ХНВА и 40ХНМА.
Заготовки малых и средних коленчатых валов, вы- полняемых из сталей, штампуют. Заготовки для стальных коленчатых валов крупных двигателей (например, судовых дизелей) получают свободной ковкой под молотом. Заго- товки литых валов из чугуна получают в основном двумя методами: отливкой в земляные и в оболочковые формы. При отливке в земляные формы используют сырые и сухие формы, изготовленные из смеси земли с жидким стеклом, которые затем просушивают и продувают углекислым га- зом. Иногда применяют отливки в оболочковые формы. Заготовки коленчатых валов, отлитые в оболочковые фор- мы, имеют высокую точность (8–10-й квалитет) и шероховатость
поверхности (Rz ≤ 40 мкм), повышенную плотность и хоро- шие эксплуатационные качества. При этом в 10–15 раз со- кращается расход формовочной смеси. Оболочковые формы заливают при горизонтальном или вертикальном положении вала. Затем заготовки коленчатых валов подвергают терми- ческой обработке (отжигу и нормализации), при которой снимаются внутренние напряжения в металле и уменьшается твердость (НВ 175–255), что облегчает обработку заготовок на металлорежущих станках. Чугунные заготовки коленча- тых валов правят в горячем состоянии.
Припуски на обработку из-за сложности конфигура- ции коленчатых валов значительно больше, чем для сту- пенчатых валов.
320