
книги / Основы технологии машиностроения. Методы обработки заготовок и технологические процессы изготовления типовых деталей машин
.pdfвой позиции устанавливают заготовку в приспособление и обрабатывают отверстия корпуса коробки скоростей (см. рис. 12.14, а), при этом одновременно на второй по- зиции обрабатывают отверстия другой (ранее установлен- ной) заготовки (см. рис. 12.14, б). По окончании рабочего хода силовые головки возвращаются в исходное положе- ние и происходит поворот стола станка на 180°, при этом заготовка с первой позиции перемещается на вторую по- зицию, а обработанная на второй позиции заготовка воз- вращается на первую позицию. Обработанную заготовку, находящуюся на первой позиции, снимают, и вместо нее устанавливают новую заготовку.
Т а б л и ц а 1 2 . 3
Технологический маршрут обработки коробки скоростей токарного станка в крупносерийном производстве
Номер |
Краткое содержание операции |
|
операции |
||
|
||
|
|
|
1 |
2 |
|
|
|
|
05 |
Предварительное шлифование верхней плоскости |
|
на плоскошлифовальном станке |
||
|
||
|
|
|
10 |
Промывание отливки корпуса коробки скоростей |
|
в моечном агрегате |
||
|
||
|
|
|
|
Сверление и нарезание резьбы во всех отверстиях |
|
20 |
с верхней стороны и развертывание двух технологи- |
|
|
ческих отверстий |
|
|
|
|
|
Предварительное и окончательное фрезерование |
|
30 |
торцов на 4-шпиндельном продольно-фрезерном |
|
|
станке |
|
|
|
|
|
Предварительное и окончательное фрезерование |
|
40 |
нижних платиков и зеркала на восьмишпиндельном |
|
|
продольно-фрезерном станке |
|
|
|
|
|
291 |
|
О к о н ч а н и е т а б л . 1 2 . 3 |
|
|
|
|
1 |
2 |
|
|
|
|
50 |
Окончательное шлифование верхней плоскости |
|
на плоскошлифовальном станке |
||
|
||
|
|
|
60 |
Черновое растачивание всех отверстий продольных |
|
осей с двух сторон на агрегатном станке |
||
|
||
|
|
|
70 |
Чистовое растачивание всех отверстий продольных |
|
осей с двух сторон на агрегатном станке |
||
|
||
|
|
|
80 |
Предварительное и окончательное растачивание от- |
|
верстий под шпиндель на алмазно-расточном станке |
||
|
||
|
|
|
|
Сверление и растачивание отверстий с переднего |
|
90 |
и заднего торцов и с передней стороны |
|
|
на агрегатном станке |
|
|
|
|
100 |
Сверление, зенкерование и развертывание отверстий |
|
с передней и задней сторон на агрегатном станке |
||
|
||
|
|
|
|
Нарезание резьбы во всех отверстиях, расположен- |
|
110 |
ных на переднем и заднем торцах и с передней сто- |
|
|
роны на резьбонарезном станке |
|
|
|
|
120 |
Сверление и нарезание резьбы в отверстиях с нижней |
|
стороны на радиально-сверлильном станке |
||
|
||
|
|
|
130 |
Хонингование отверстий под шпиндель на верти- |
|
кально-хонинговальном станке |
||
|
||
|
|
|
|
Окончательное шлифование нижней плоскости |
|
140 |
и вертикального платика на плоскошлифовальном |
|
|
станке |
|
|
|
|
150 |
Промывание корпуса в моечном растворе |
|
|
|
292
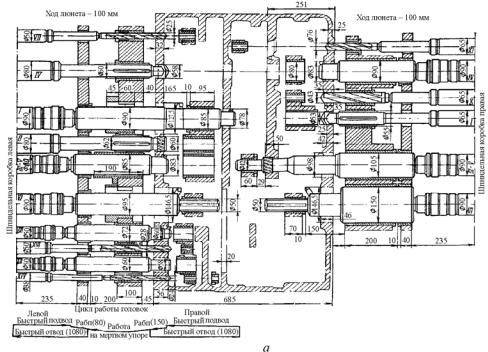
293
Рис. 12.14. Схемы обработки отверстий в корпусе коробки скоростей: первая позиция
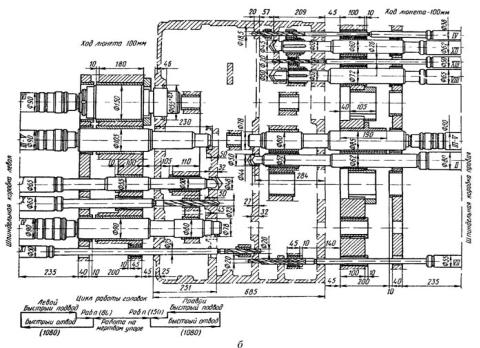
294
Рис. 12.14. Окончание
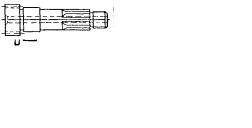
12.3.Технологические процессы обработки валов
Вконструкциях машин и механизмов основными де- талями для передачи вращательного движения и крутящего момента являются валы. В процессе работы валы испыты- вают сложные деформации: кручение, изгиб, растяжение
исжатие. Поэтому валы должны быть достаточно жестки- ми. Валы очень разнообразны по форме и размерам, однако по технологическим признакам можно выделить две разно- видности: гладкие и ступенчатые валы. Наиболее простую геометрическую форму имеют прямые гладкие валы посто- янного диаметра, но их применение весьма ограниченно. Наиболее распространены ступенчатые валы, основными технологическими параметрами которых являются: общая длина вала, количество ступеней, неравномерность их пе- репада по диаметрам, диаметр наибольшей ступени, нали- чие шлицев и их форма. В табл. 12.4 приведены разновид- ности сплошных и полых ступенчатых валов.
|
|
Т а б л и ц а 1 2 . 4 |
|
|
Виды ступенчатых валов |
||
Конструктивные |
Сплошные валы |
Полые валы |
|
без центрального |
с центральным |
||
разновидности |
|||
отверстия |
отверстием |
||
|
|||
Гладкие валы без |
|
|
|
шлицев и зубчатых |
|
|
|
венцов |
|
|
|
|
|
|
|
Шлицевые валы |
|
|
|
|
|
|
|
Валы с зубчатым |
|
|
|
венцом |
|
|
|
|
|
|
Жесткость конструкции вала определяется геометри- ческой формой (отношением длины вала к его диаметру). Увеличить жесткость вала за счет уменьшения его длины не всегда возможно.
295
Наиболее технологичными являются валы с возрас- тающим или убывающим диаметром ступеней. Участки вала, имеющие один и тот же номинальный размер, но раз- ные допуски, должны быть разделены канавками, четко разграничивающими обрабатываемые поверхности и необ- рабатываемые. При этом желательно, чтобы обрабатывае- мые участки вала имели равные или кратные длины, а пе- репады ступеней были по возможности наименьшими. Конструкция вала должна допускать обработку ступеней на проход и обеспечить удобный подход и выход режущего инструмента.
Валы изготовляют из сталей, обладающих высокой прочностью, малой чувствительностью к концентрации напряжений, хорошей обрабатываемостью и способно- стью подвергаться термической обработке, например, из сталей 35, 40, 45, 40Г, 50Г и др. В ряде случаев валы изготавливают из серых чугунов, например, из чугу- нов СЧ 15, СЧ 20 и др.
Валы с небольшим количеством ступеней и неболь- шими перепадами диаметров изготавливают из штучных заготовок, отрезанных от стального горячекатаного или холоднокатаного прутка. Стальные валы, имеющие более сложную конфигурацию и с большим числом ступеней или со ступенями, значительно отличающимися по диа- метрам – из заготовок, получаемых ковкой, штамповкой, поперечным прокатом или ротационным обжатием. Для изготовления валов сложной конфигурации, например ко- ленчатых валов, используют стальные или чугунные ли- тые заготовки.
Выбор рациональной заготовки должен быть обосно- ван технико-экономическими расчетами.
В массовом и крупносерийном производствах валы изготавливают из заготовок, обеспечивающих эффективное
296
использование материала (коэффициент использования ма- териала более 0,65) и значительное сокращение трудоемко- сти механической обработки. Штучную заготовку из прут- ка заменяют штамповкой, если коэффициент использова- ния материала повышается не менее чем на 5 %. Заготовка, полученная ротационным обжатием, наиболее близка по конфигурации и размерам к готовой детали (коэффициент использования материала составляет 0,85–0,95).
Заготовки небольших ступенчатых валов диаметром до 25 мм изготовляют сочетанием холодной высадки и экс- трюдинг-процесса, а именно: из штучной заготовки за не- сколько переходов высаживают ступенчатую часть, имею- щую диаметр, больший, чем исходная заготовка, а затем вытягивают ту часть, диаметр которой меньше размера ис- ходной прутковой заготовки.
Механической обработке поверхностей вала предше- ствует образование единой базы для установки обрабаты- ваемой заготовки на всех операциях. Основными базами вала являются торцовые поверхности и центровые отвер- стия. От точности выполнения основных баз зависит точ- ность исполнения последующих операций.
Основной технологической задачей, решаемой в про- цессе механической обработки ступенчатых валов, является обеспечение расположения осей всех обрабатываемых сту- пеней вала на одной геометрической линии в целях умень- шения радиального биения.
Одной из сложных разновидностей ступенчатого ва- ла, где к указанным выше требованиям прибавляется необ- ходимость обеспечить расположение осей всех наружных поверхностей ступеней вала и ступенчатых участков цен- трального осевого отверстия на одной геометрической оси, являются шпиндели металлорежущих станков.
297
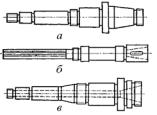
12.3.1. Технологические процессы обработки шпинделей станков
Шпиндель – одна из наиболее ответственных дета- лей металлорежущего станка. Шпиндель современного металлорежущего станка занимает особое место в кинема- тической цепи станка, так как от него зависит не только передача вращательного движения обрабатываемой заго- товки, но и качество обработки. Он вращается на опорных шейках, являющихся его основными базами, следователь- но, от стабильности положения вращающегося в опорах шпинделя зависит качество обработки.
Шпиндели работают на опорах качения и опорах скольжения. В первом случае к шпинделям предъявляют требования жесткости и прочности, а во втором, кроме то- го, и износостойкости.
По конструктивной форме шпиндели можно разде- лить на три вида, показанные на рис. 12.15:
– шпиндели без осевого отверстия (см. рис. 12.15, а), применяемые в шлифовальных станках;
– шпиндели с несквозным отверстием (см. рис. 12.15, б), применяемые в сверлильных станках и многошпиндельных сверлильных головках;
– шпиндели со сквозным отверстием (см. рис. 12.15, в), имеющие наибольшее примене- ние на станках токарной группы, фрезерных, резьбофрезерных, резьбошлифовальных и других.
Шпиндели изготавливают обычно из углеродистой ста-
298
ли 45, хромистой 20Х и 40Х, хромоникелевой 40ХН, 12ХН2,12ХН3 и реже – из сталей других марок.
Углеродистую сталь применяют главным образом для шпинделей токарных, токарно-револьверных, свер- лильных и фрезерных станков. Хромистую и хромоникеле- вую сталь применяют для шпинделей автоматов и шлифо- вальных станков. Для изготовления пустотелых шпинделей некоторых тяжелых станков используют серый чугун СЧ 15
иСЧ 20 или модифицированный чугун и в редких случа- ях – стальное литье. Сталь 35ХЮА применяют для изго- товления шпинделей тяжелых расточных и крупных круг- лошлифовальных станков (с азотированием опорных шеек).
Заготовку для шпинделей выбирают в зависимости от размера программы и конфигурации. Если шпиндель имеет фланец, диаметр которого значительно больше диаметра опорных шеек, то необходимо брать поковку, полученную свободной ковкой при единичном и мелкосерийном произ- водстве, и штамповку с горячей высадкой на горизонталь- но-ковочной машине или ковкой на ротационно-ковочной машине при крупносерийном производстве.
Если фланца у шпинделя нет или если диаметр флан- ца мало отличается от диаметра шеек, то заготовку следует брать из проката. В качестве заготовки для тонкостенных шпинделей без фланцев (шпиндели токарных автоматов
иполуавтоматов) целесообразно применять трубы соответствующих диаметров.
Требования точности, предъявляемые к металлоре- жущим станкам, предопределяют требования точности из- готовления шпинделей этих станков. По точности шпинде- ли можно разделить на три группы:
–для станков нормальной точности;
–станков повышенной и высокой точности;
–станков особо высокой точности и прецизионных станков.
299
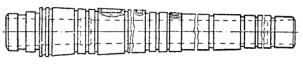
Отклонение формы (от круглости и от цилиндрично- сти) опорных шеек шпинделя для станков нормальной точ- ности не должны превышать 50 % допуска на диаметраль-
ные размеры оперных шеек. Для |
станков повышенной |
и высокой точности эти величины |
не должны превы- |
шать 25 %, а для прецизионных станков – 5…10 % от до- пуска на диаметр опорных шеек. Опорные шейки шпинде- лей современных прецизионных станков имеют отклонение от круглости не выше 0,3–0,5 мкм, отклонение от цилинд- ричности не выше 0,25–0,5 мкм на длине 300 мм при до- пуске на диаметр шеек 1,5–3 мкм.
Радиальное биение конусного отверстия шпинделя от- носительно подшипниковых (опорных) шеек не должно пре- вышать для станков нормальной точности 5…10 мкм, для станков повышенной и высокой точности – 3…5 мкм, а для прецизионных станков – 1…3 мкм. Торцовое биение опор- ных фланцев относительно оси вращения не должно превы- шать 6–8 мкм для станков нормальной точности, 3–6 мкм – для станков повышенной и высокой точности и 1–3 мкм – для станков особо высокой точности и прецизионных станков.
Шероховатость |
поверхности |
опорных |
шеек |
Ra = 0,4…0,8 мкм для |
станков нормальной точности, |
Ra = 0,1…0,2 мкм для станков повышенной и высокой точ- ности и Ra = 0,05…0,1 мкм для станков особо высокой точности и прецизионных станков.
Наиболее сложным является изготовление шпинделей со сквозным отверстием, например, шпиндель токарного станка. На рис. 12.16 показан общий вид такого шпинделя.
Рис. 12.16. Общий вид шпинделя токарного станка
300