
книги / Основы технологии машиностроения. Методы обработки заготовок и технологические процессы изготовления типовых деталей машин
.pdfваний (щелочей). Анодное растворение сопровождается образованием на обрабатываемой поверхности пассирую- щей пленки (гидрата окиси металла). Эта пленка из-за пло- хой проводимости электрического тока замедляет протека- ние процесса, а в ряде случаев полностью останавливает электрохимическое растворение металла. Для нормального протекания анодного растворения пассирующую пленку необходимо удалять.
При алмазном хонинговании и полировании продук- ты гидролиза удаляются с поверхности заготовки механи- ческим путем – абразивными зернами. Например, при элек- трохимической размерной обработке пера лопатки продук- ты анодного растворения удаляются потоком электролита.
Принцип электрохимической обработки в проточном электролите заключается в том, что обрабатываемая заго- товка устанавливается относительно электродов с зазором, через который с большой скоростью прокачивается элек- тролит. При этом деталь является анодом, а электрод- инструмент – катодом. При прохождении электрического тока по цепи катод-инструмент – анод-заготовка заготовка под действием электрического тока растворяется, прини- мая форму электрода-инструмента. Продукты анодного растворения непрерывно удаляются с поверхности анода- заготовки потоком прокачиваемого электролита и осаж- даются в баке отстойника в виде шлама. Электроды- инструменты при электрохимической обработке практиче- ски не изнашиваются, сохраняя свою первоначальную форму, и служат в качестве токопроводящих элементов. В зависимости от геометрических и электрохимических па- раметров межэлектродный зазор изменяется от 0,3 до 0,5 мм. Для регулирования процесса электрохимического растворе- ния требуется поддерживать гидравлические, механические и электрические параметры режима обработки. К гидравли- ческим режимам относят скорость потока электролита в за-
251
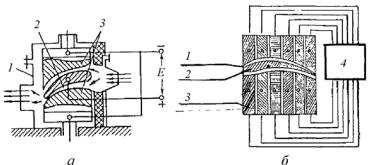
зоре между электродами. Постоянство скорости потока элек- тролита при изменении зазора обеспечивается изменением давления электролита в трубопроводах. К механическим ре- жимам относят поперечную подачу, обеспечивающую по- стоянный зазор между электродами. К электрическим режи- мам относят стабилизацию напряжения и плотности тока. При выборе электролита необходимо учитывать электропро- водность, безопасность в работе и стоимость.
Электролиты не должны содержать вредных веществ и поражать металлические части станка коррозией. С уче- том этих требований рекомендуется применять для сталей водные растворы поваренной соли NaCl, для титановых сплавов – раствор азотнокислого натрия NaNO3, для жаро- прочных сталей – раствор сернокислого натрия NaSO4. Концентрация растворов колеблется от 10 до 15 % (наи- лучшая – 12 %), плотность электрического тока 20–30 А/см2, скорость потока электролита 20–30 м/мин, температура электролита 20–30 °С.
На рис. 11.8 приведены схемы обработки пера лопат- ки авиационного газотурбинного двигателя (ГТД).
Рис. 11.8. Схемы электрохимической обработки пера: а – лопатки авиационного газотурбинного двигателя: 1 – рабочая камера, 2 – деталь, 3 – электрод-инструмент; б – крупногабаритной лопатки секционными электродами: 1 – межэлектродный зазор,
2 – лопатка, 3 – секции инструмента, 4 – блок коммуникации
252
Пропорционально величине зазора изменяется съем металла на отдельных участках профиля пера обрабаты- ваемых лопаток. Следовательно, на выступающих участках профиля пера лопатки съем металла будет протекать более интенсивно, с течением времени произойдет выравнивание зазора, и съем металла будет равномерным по всей поверх- ности лопатки. Для ускорения процесса выравнивания ме- жэлектродного зазора рекомендуется применять электроли- ты, насыщенные воздухом. При пропускании газированно- го электролита через межэлектродный зазор воздушные пузырьки будут концентрироваться в зонах, имеющих мак- симальный зазор, то есть в зонах, имеющих минимальное сопротивление. При этих условиях концентрация воздуха в электролите будет неравномерна. В зонах с увеличенной концентрацией воздуха процесс электрохимического рас- творения будет замедляться, и наоборот, в зонах с мини- мальным межэлектродным зазором (на выступах) съем металла будет протекать более интенсивно. При этих ус- ловиях за более короткий промежуток времени выравни- вается неравномерность снимаемого припуска за счет бо- лее интенсивного удаления неровностей профиля лопатки.
Продолжительность рабочего цикла обработки од- ной лопатки электрохимическим методом составляет 15– 20 мин.
Точность профиля пера лопатки ГТД из стали ЭИ 435 после электрохимической обработки колеблется в преде-
лах 0,1–0,2 мм.
При обработке деталей относительно небольших раз- меров электроды-инструменты изготавливаются из мини- мально возможного количества электродов (см. рис. 11.8, а). При электрохимической обработке крупногабаритных дета- лей, например лопаток водяных и паровых турбин, предло-
253
женная схема обработки не может быть реализована из-за чрезмерно большой площади электродов. При этих условиях очень сложно обеспечить требуемую плотность электриче- ского тока. Поэтому обработку крупногабаритных загото- вок осуществляют по принципу бегущей волны движущим- ся электрическим полем. Для этой цели электроды изготав- ливаются в виде отдельных секций, изолированных друг от друга (см. рис. 11.8, б). На каждую секцию подаются крат- ковременные импульсы за счет выборочной коммутации. В первую очередь подключаются те секции, которые имеют минимальный межэлектродный зазор. Удаление припуска заготовки осуществляется по программе. Предварительный обмер колебаний припуска на заготовке определяет оче- редность коммутации секций с целью выравнивания неров- ностей. После выравнивания неровностей обработка осу- ществляется с помощью бегущей волны.
Электрохимический метод применяется также для обработки отверстий в деталях из твердых сплавов. В ка- честве электрода-инструмента используются трубки, изго- товленные из титановых сплавов или нержавеющих ста- лей, на наружной поверхности которых нанесено изоля- ционное многослойное покрытие. Изоляционное покрытие электродов осуществляется с помощью лаков или эмалей, которые не разрушаются под воздействием применяемых электролитов.
Электроабразивная обработка осуществляется токо-
проводящим шлифовальным кругом, который является ин- струментом-электродом. Зазор между заготовкой и шлифо- вальным кругом-катодом равен высоте наиболее выступаю- щих и связки шлифовальных (абразивных) зерен. В этот за- зор подается электролит. Продукты анодного распада удаляются абразивными зернами шлифовального круга, вы-
254
ступающими из связки. Электроабразивная обработка при- меняется при плоском и круглом шлифовании твердых спла- вов, быстрорежущих, конструкционных и жаропрочных ста- лей и сплавов, при обработке профильных пазов, шлицевых поверхностей, заточке режущих инструментов. Процесс протекает при значительно меньшей теплонапряженности по сравнению с обычным шлифованием.
В качестве режущего инструмента применяются абра- зивные и алмазные круги на токопроводящих связках М1, М5, СЭШ-1, СЭШ-2, основными компонентами которых являются медь, цинк, алюминий. При электроабразивном шлифовании жаропрочных и конструкционных сталей при- меняют белый электрокорунд, для титановых сплавов – кар- бид кремния зеленый. В качестве токопроводящих электро- литов, обеспечивающих требуемое качество поверхности, точность и производительность, а также не вызывающих коррозию на незащищенных частях оборудования, приме- няются растворы нейтральных солей с добавками ингибито- ров для придания им антикоррозийных свойств. В качестве ингибиторов используют двухромовокислый калий или три- этаноломин.
Электроабразивное шлифование твердых сплавов осуществляется на следующих режимах: скорость круга 15–30 м/с, напряжение 15–20 В, плотность тока 1–7 А/см2.
При этом обеспечивается точность 6–8-го квалитета и шероховатость поверхности Ra = 0, 32…1,25 мкм.
Метод обработки лучом (лазерная обработка) осно-
ван на использовании электромагнитных колебаний свето- вого диапазона, получаемых с помощью квантово-оптичес- ких генераторов (лазеров).
Этими электромагнитными колебаниями можно управлять, их можно фокусировать в очень тонкие пучки,
255
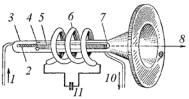
измеряемые единицами угловых минут (менее 30 угловых минут), с высокой когерентностью, то есть с колебаниями в излучаемом свете практически одной фазы и частоты.
Направленный когерентный световой луч обладает огромной световой и тепловой энергией.
На рис. 11.9 приведена схема классического лазера. Стержень 5, представляющий собой рубин с зеркально по- серебренным торцом 4 и полупрозрачно посеребренным торцом 7, укреплен пружиной 2 в держателе 9, оканчиваю- щемся стеклянной трубкой 3. Охлаждение трубки происхо- дит при пропускании газа по каналам 1 и 10. Световой им- пульс лампы-вспышки 6 от источника импульсного пита- ния 11 возбуждает атомы хрома в рубиновом стержне 5.
После прекращения импульса возбужденные атомы возвращаются к ис- ходному уровню, освобо- ждая энергию в виде излу-
чения в видимой или ин- Рис. 11.9. Схема лазера фракрасной части спектра.
Это излучение проявляет- ся в форме светового луча 8, имеющего большую удель- ную мощность и обладающего способностью нагревать заданную точку обрабатываемой поверхности до высоких температур.
Этот метод обработки применяют для получения от- верстий малых диаметров, резки материалов, в том числе материалов с высокой твердостью (алмазов, платины, ру- бинов и др.) по заданному контуру, прорезки пазов и т.п.
Ультразвуковая обработка применяется для изго-
товления деталей из хрупких материалов (стекла, керамики, фарфора, твердых сплавов). Метод основан на использова-
256
нии ультразвуковых колебаний инструмента, осуществляе- мых с помощью магнитострикционных вибраторов. Магни- тострикционный эффект основан на способности некото- рых материалов изменять свои геометрические размеры в магнитном поле. Такими свойствами обладает никель. Магнитострикционные вибраторы позволяют получить частоты колебаний 20–30 кГц. Для получения этих колеба- ний используют пьезоэлектрический эффект, основанный на способности некоторых материалов изменять свои гео- метрические размеры под воздействием электрического поля. Это свойство наиболее выражено у кристаллов кварца и титанита бария.
При наличии ультразвуковых колебаний в жидких средах возникает кавитация – образование в жидкости не- больших кавитационных пузырьков. Эти пузырьки неус- тойчивы. При их разрушении возникают силы, сопровож- дающиеся гидравлическим ударом. Если вблизи этих пу- зырьков будет находиться твердое тело, то под действием гидравлического удара оно будет подвергнуто разрушению. На поверхности образуются мелкие раковины.
Если в зону обработки непрерывно подавать абразив- ную суспензию из мельчайших частиц алмазной пыли, кар- бида бора или карбида кремния, то под воздействием высокочастотных колебаний инструмента- магнитостриктора 3 (рис. 11.10) абразивные частицы с большой скоростью будут ударяться об обрабатываемую поверхность, разрушая ее. На резонансной частоте амплитуда колебаний магнитострикционных вибраторов составляетДля повышения5–10 мкм. эффективности ультразвуковой об- работки необходимо, чтобы торец инструмента вибрировал с амплитудой 0,03–0,1 мм.
257
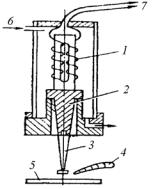
Для достижения этой цели применяют усилители колеба- ний (концентраторы). Конический стержень (концентратор) 3 изго- тавливается из высокопрочного металла, обладающего хорошими антифрикционными свойствами и износостойкостью к разрушаю- щему воздействию абразива.
Производительность про- цесса зависит от свойств обраба- тываемого материала, амплиту- ды и частоты колебаний инстру- мента, зернистости абразивного материала.
На машиностроительных заводах ультразвуковой метод применяется для обработки от- верстий в заготовках из закален- ных сталей, жаропрочных и ти- тановых сплавов, карбида вольф- рама и молибдена, стекла, графи-
та, керамики и т.п. Точность обработки зависит от величины абразивных частиц, она может быть получена в пределах
0,005–0,04 мм.
Ультразвуковая обработка достаточно часто приме- няется в сочетании с электроискровой обработкой. Предва- рительная обработка производится электроискровым мето- дом, чистовая – ультразвуковым.
258
12. ТЕХНОЛОГИЧЕСКИЕ ПРОЦЕССЫ ОБРАБОТКИ ТИПОВЫХ ДЕТАЛЕЙ МАШИН
Ввиду большого разнообразия форм и размеров дета- лей машин, наличия на заводах различного оборудования, разной степени подготовки персонала разработка технологи- ческих процессов, пригодных для любого машинострои- тельного завода, даже в пределах одного класса типичных деталей, является неосуществимой задачей. Типовые техно- логические процессы могут служить лишь основой для раз- работки конкретных технологических процессов. По этим же причинам для каждого класса деталей требуется разра- ботка своего типового технологического процесса.
Однако существует ряд общих условий, о которых говорилось выше и которые предопределяют технологиче- ский маршрут обработки деталей всех типов. Это конст- рукция деталей, требования к точности обработки, приме- нение технологических средств повышения износоустой- чивости и надежности деталей машин, соблюдение прин- ципа единства базы, необходимость обрабатывать с одной установки возможно большее количество поверхностей за- готовки и выявлять брак на первых операциях.
12.1. Технологические процессы обработки станин станков
Станина металлорежущего станка является основной
иответственной деталью, ее часто называют базовой дета- лью станка. Станина соединяет все узлы (механизмы) и де- тали. Именно относительно станины ориентируются и пе- ремещаются подвижные узлы (механизмы) станка. Для большинства станин характерным является наличие двух
иболее прямолинейных поверхностей. Наличие точно об-
259
работанных отверстий нетипично для станин. У них име- ются, главным образом, крепежные отверстия. Станины, как правило, относятся к деталям, с большими габаритны- ми размерами, с точными направляющими поверхностями, деформирующимися при обработке и эксплуатации.
В зависимости от служебного назначения станины подразделяют на шесть групп:
–с горизонтальными направляющими и несколькими тумбами (станины токарных, револьверных и других по- добных станков);
–с горизонтальными направляющими и несколькими тумбами, но с отлитыми за одно целое со станиной корпу- сом передней бабки;
–с горизонтальными направляющими, устанавливае- мые непосредственно своим основанием на пол или фунда- мент без тумб (станины горизонтально-расточных, про- дольно-строгальных, продольно-фрезерных и т.п. станков);
–с вертикальными направляющими и перпендику- лярно к ним расположенными отверстиями под опоры шпинделя (станины долбежных станков);
–с вертикальными направляющими, но без шпин- дельных отверстий (станины вертикально-сверлильных станков);
–станины в виде цилиндрической вертикальной ко- лонны с плоским основанием, расположенным перпенди- кулярно к оси цилиндра (станины радиально-сверлильных станков).
Точность работы станка в значительной степени оп- ределяется точностью направляющих станины и их износо- стойкостью.
Отклонение от прямолинейности и параллельности направляющих станин станков нормальной точности до-
260