
книги / Основы технологии машиностроения. Методы обработки заготовок и технологические процессы изготовления типовых деталей машин
.pdf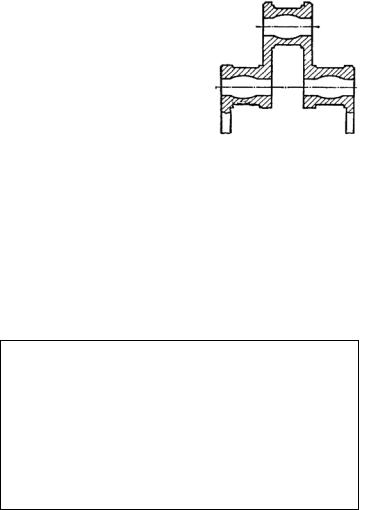
Заготовки судовых и тепло- возных валов, как правило, ли- тые пустотелые. Длина вала 4 м и более. Например, вал тепло- возного двигателя длиной около 4 м имеет 10 шатунных шеек диаметром 170 мм и 12 корен- ных шеек диаметром 204 мм.
Фрагмент конструкции такого Рис. 12.27. Фрагмент кон- |
||
вала показан на рис. 12.27. |
струкции коленчатого ва- |
|
ла двигателя тепловоза |
||
Материал вала – модифи- |
||
|
цированный чугун с содержанием углерода 2,2–2,4 %, ле- гированный молибденом, хромом, никелем. Заготовка ли- тая, пустотелая.
Кристаллизацию материала производят при верти- кальном положении заготовки.
Технические условия на изготовление коленчатого ва- ла тепловозного двигателя (по данным одного из заводов):
Допуск на обработку шеек по диаметру, |
|
|
не более............................................................................... |
0,02 |
мм |
Овальность и конусность шеек, не более........................ |
0,02 |
мм |
Допуск на радиус кривошипа, не более............................. |
0,1 |
мм |
Перекос осей шатунных шеек относительно |
|
|
коренных шеек, не более ......................................................... |
0,02 |
мм |
Биение коренных шеек по всей длине, |
|
|
не более............................................................................... |
0,03 |
мм |
Шероховатость поверхности шеек................ |
Ra = 0,32…0,63 мкм |
|
Припуски на обработку.................................... |
5–6 мм на сторону |
Технологические базы меняются в следующей после- довательности: черновые поверхности коренных шеек; цен- тровые отверстия; обточенные наружные поверхности ко- ренных шеек; специально расточенные в торцах конусные отверстия под конусные пробки. Шлифование осуществля- ется на конусных пробках.
331
Технологический маршрут обработки коленчатого вала тепловозного двигателя приведен в табл. 12.11.
|
|
Т а б л и ц а 1 2 . 1 1 |
||
|
Технологический маршрут обработки |
|||
коленчатого вала тепловозного двигателя |
||||
|
|
|
|
|
Номер |
Краткое содержание |
Оборудование |
Технологические |
|
операции |
операции |
базы |
||
|
||||
1 |
2 |
3 |
4 |
|
05 |
Фрезерование торцов |
Продольно- |
Коренные шейки |
|
|
фрезерный станок |
|||
10 |
Центрование |
Токарный станок |
Коренные шейки |
|
|
|
с люнетом |
|
|
|
Предварительная |
Двухсуппортный |
Центровые |
|
20 |
обточка коренных |
токарный станок |
||
отверстия |
||||
|
шеек |
с люнетом |
||
|
|
|||
|
Предварительная об- |
|
|
|
|
точка шатунных шеек |
|
|
|
30 |
(вал неподвижный, |
Специальный то- |
Коренные шейки |
|
|
шейки обтачивают |
карный станок |
|
|
|
вращающейся |
|
|
|
|
головкой) |
|
|
|
|
Термическая обработ- |
|
|
|
|
ка – высокий отпуск |
|
|
|
40 |
для снятия внутрен- |
— |
— |
|
|
них остаточных |
|
|
|
|
напряжений |
|
|
|
50 |
Гамма-дефектоскопия |
— |
— |
|
|
Чистовая обточка |
Двухсуппортный |
Центровые |
|
60 |
коренных шеек |
токарный станок |
||
отверстия |
||||
|
|
с люнетом |
||
|
|
|
||
|
Чистовая обточка ша- |
Специальный |
|
|
70 |
тунных шеек (анало- |
Коренные шейки |
||
токарный станок |
||||
|
гично операции 30) |
|
||
|
|
|
||
|
Растачивание конусов |
Токарный станок |
|
|
80 |
на концах вала под |
Коренные шейки |
||
|
конусные пробки |
с люнетом |
|
|
|
|
|
||
|
Статическая баланси- |
Специальный |
|
|
90 |
ровка перед шлифо- |
Коренные шейки |
||
стенд |
||||
|
ванием |
|
||
|
|
|
||
332 |
|
|
|

О к о н ч а н и е т а б л . 1 2 . 1 1
1 |
2 |
3 |
4 |
|
100 |
Снятие дисбаланса |
Продольно- |
Коренные шейки |
|
|
фрезерный станок |
|||
|
Шлифование корен- |
Специальный |
Коренные шейки |
|
110 |
ных шеек при уста- |
шлифовальный |
||
попеременно |
||||
|
новке вала в люнетах |
станок |
||
|
|
|||
|
Слесарная. Установка |
|
|
|
120 |
конусных центровых |
Слесарный верстак |
— |
|
|
пробок |
|
|
|
|
Шлифование шатун- |
Специальный |
|
|
130 |
ных шеек |
шлифовальный |
Центровые пробки |
|
|
|
станок |
|
|
|
Слесарная. |
|
|
|
140 |
Съем центровых |
Слесарный верстак |
— |
|
|
пробок |
|
|
|
|
Нарезание резьбы для |
|
|
|
|
заглушек в конусных |
Токарный станок |
|
|
150 |
отверстиях, ввинчи- |
Коренные шейки |
||
|
вание заглушек, под- |
с люнетом |
|
|
|
|
|
||
|
резка торцов вала |
|
|
|
160 |
Фрезерование |
Шпоночно- |
Коренные шейки |
|
шпоночных канавок |
фрезерный станок |
|||
170 |
Сверление отверстий |
Горизонтально- |
Коренные шейки |
|
во фланце по контуру |
расточной станок |
|||
|
Сверление отверстий |
Горизонтально- |
|
|
180 |
под маслопроводные |
Коренные шейки |
||
расточной станок |
||||
|
трубки |
|
|
|
190 |
Слесарные операции |
Слесарный верстак |
— |
|
200 |
Контроль |
Контрольный стол |
— |
12.4. Технологические процессы обработки зубчатых колес
Технологические процессы изготовления зубчатых колес должны обеспечивать получение деталей, соответст- вующих условиям эксплуатации и требованиям точности при наименьших трудозатратах.
Основными факторами, влияющими на выбор техно- логического процесса, являются:
– конструкция и размеры зубчатого колеса;
333
–вид заготовки и материал;
–вид и качество термической обработки;
–требования к точности и качеству механической обработки;
–объем производства.
Детали класса «втулка» имеют центральное отвер- стие, концентричное наружной цилиндрической, кониче- ской или глобоидальной поверхности. В одних случаях центральное отверстие является конструктивной базой ко- леса, в других – технологической базой.
В деталях класса «вал» базой в большинстве случаев являются центровые отверстия. При малой жесткости дета- ли или при ее большой длине за базу при формировании зуба принимают конструкторскую базу или в виде цилинд- рической шейки под подшипник, или специально создавае- мую для базирования шейку.
Каждый вид зубчатых колес имеет свои технологиче- ские особенности изготовления. Зубчатые колеса, принад- лежащие к тому или иному классу, могут иметь технологи- ческие процессы, несколько отличающиеся друг от друга по содержанию и последовательности выполнения ряда операций в зависимости от специализации производства. Так, например, методы изготовления зубчатых колес в авиационной промышленности существенно отличаются от методов, применяемых при производстве зубчатых колес аналогичных размеров в автомобильной промышленности. Технология производства турбинных передач значительно отличается от технологии изготовления таких же по разме- рам зубчатых передач для прокатных станов, и т.д.
Таким образом, условия работы и требования конст- рукции зубчатой передачи существенно влияют на содер- жание технологического процесса изготовления зубчатого колеса.
334
Вавиационных передачах зубчатые колеса при ми- нимальных размерах и минимальной массе должны переда- вать большие крутящие моменты и работать при высоких окружных скоростях, в то же время передача должна обес- печивать весьма высокую точность и надежность.
Данные требования заставляют конструкторов созда- вать эти передачи из высоколегированных сталей с приме- нением цементации и закалки, что усложняет технологиче- ский процесс изготовления зубчатого колеса, обуславливая необходимость введения операций шлифования (предвари- тельных и окончательных), большого количества операций промежуточного контроля и операций термообработки.
Вавтостроении, тракторостроении и станкостроении шлифованию зубьев подвергаются только некоторые наи- более ответственные пары зубчатых колес. Зато широкое применение находят такие процессы, как шевингование, притирка и т.д.
Зубчатые колеса общего машиностроения и подъем- но-транспортных машин имеют другую специфику изго- товления. Здесь преобладают колеса из улучшенных ста- лей, без последующей термообработки готовой детали. Технологический процесс при этом упрощается, однако требования к точности зубообрабатывающих станков и ин- струмента не снижаются.
Зубчатые колеса изготавливают из конструкционных сталей, серого чугуна, бронзы и синтетических материалов.
Вавтотракторостроении зубчатые колеса изготавли- вают из хромо-марганцовистых сталей 18ХГТ, 30ХГТ, хромомолибденовой стали 30ХМ. Сталь 18ХГТ благодаря наличию титана обладает повышенной прокаливаемостью, прочностью и меньшей чувствительностью к перегреву. Эта сталь отличается высокой способностью сопротивлять- ся смятию. Сталь 30ХГТ содержит несколько больше угле- рода, чем сталь 18ХГТ, и широко применяется для сильно
335
нагруженных зубчатых колес с модулем свыше 5 мм. Она обладает в термически обработанном состоянии высокими показателями прочности сердцевины в сечении зубьев.
Зубчатые колеса металлорежущих станков изготав- ливают из углеродистых сталей 45 и 50, а также из легиро- ванных хромистых сталей 40Х. Реже применяют легиро- ванные стали 18ХГТ, 30ХГТ, 12ХН3А и др.
Для изготовления зубчатых колес получили распро- странение малолегированные борсодержащие стали 20ХГР и 25ХГР. Введение небольших количеств бора (0,002–0,005 %) значительно увеличивает прокаливаемость, прочностные характеристики и вязкость. После химико-термической об- работки (цементации, закалки и низкого отпуска) твердость составляет HRC 58–62.
Зубчатые колеса, изготовленные из синтетических материалов (текстолита, нейлона, капрона и др.), могут ра- ботать при высоких скоростях (до 40–50 м/с). Колеса из синтетических материалов обеспечивают бесшумность, плавность передачи и гашение вибрации.
Для изготовления зубчатых колес, как правило, необ- ходимы заготовки, по форме и размерам приближающиеся к форме и размерам готовой детали.
Качество заготовки влияет на технологический мар- шрут механической обработки и ее трудоемкость. Конфи- гурация зубчатого колеса, его материал и объем выпуска предопределяют способ получения заготовки.
Заготовками для стальных зубчатых колес являются штамповки, поковки и прокат. Цилиндрические зубчатые колеса диаметром до 50 мм и плоские колеса без ступицы диаметром до 65 мм целесообразно изготовлять из горяче- катаного или холоднотянутого проката или из штучной за- готовки, отрезанной от прутка. Прутковые заготовки обра- батывают на токарных и револьверных станках и много- шпиндельных автоматах (крупносерийное и массовое про-
336
изводство), где производится предварительная черновая обработка с отрезкой штучных заготовок.
Цилиндрические колеса с наружным диаметром бо- лее 50 мм обычно изготавливают из штамповок, получае- мых на кривошипных ковочно-штамповочных прессах, мо- лотах, горизонтально-ковочных машинах.
Для штамповки заготовок на прессе припуски под механическую обработку устанавливают на 30–40 % меньше, чем при штамповке на молоте, особенно по раз- мерам, перпендикулярным к плоскости разъема штампа. Коэффициент использования металла в заготовках, полу- чаемых штамповкой на ковочно-штамповочных прессах, составляет 0,65–0,75.
Заготовки для зубчатых колес получают также горячей высадкой на горизонтально-ковочных машинах из прутка. Для ряда конфигураций и размеров зубчатых колес заготов- ки, откованные на горизонтально-ковочной машине, имеют более высокий коэффициент использования металла, чем заготовки, отштампованные на кривошипных прессах. На горизонтально-ковочной машине штамповкой произво- дят не только образование наружной формы заготовки, но и сквозную прошивку центрального отверстия. При штам- повке на молоте или прессе прошивка отверстия выносится в отдельную операцию. Коэффициент использования метал- ла в заготовках, полученных на горизонтально-ковочных машинах, достигает 0,65–0,75.
Кованые или штампованные заготовки подвергают термообработке (нормализации или отжигу) для снятия ос- таточных напряжений и улучшения их обрабатываемости. После термообработки заготовки очищают от окалины дробеструйной обработкой или травлением с последующим промыванием в горячей воде, а затем контролируют твер- дость, основные размеры, шероховатость поверхности.
337
12.4.1. Технологические процессы обработки цилиндрических зубчатых колес
Для выполнения требуемых эксплуатационных ка- честв в передачах с цилиндрическими зубчатыми колесами при их изготовлении должно быть обеспечено: достижение соответствующей кинематической точности, плавности за- цепления, необходимой величины и постоянства боковых и радиальных зазоров в передаче, а также соответствующая шероховатость поверхности зубьев. Кинематическая точ- ность зубчатых колес зависит от точности станка и инстру- мента, а также от точности базирования заготовки в про- цессе зубонарезания.
При изготовлении зубчатого колеса к технологиче- скому процессу предъявляют определенные требования, от которых зависит качество готовых зубчатых колес.
К основным требованиям относятся:
–обеспечение концентричности цилиндрической по- садочной поверхности и наружных поверхностей;
–обеспечение перпендикулярности посадочной по- верхности и по крайней мере одного базового торца, а в зуб- чатых колесах, нарезаемых пакетом, – двух базовых торцов. При этом должна быть обеспечена перпендикулярность по- садочной поверхности и конструктивного опорного торца.
Отклонение от концентричности базовой и конструк- тивной посадочных поверхностей и поверхности выступов приводит к неравномерности зацепления, а для зубчатых ко- лес, у которых толщина зуба задается для измерения зубоме- ром, – к невозможности точного замера толщины зубьев.
Отклонение от перпендикулярности посадочной по- верхности и базового торца, как и отклонение от парал- лельности торцов, приведет к искривлению оправки, на ко-
торую устанавливается для нарезания зубчатое колесо, а само зубчатое колесо будет иметь погрешности, которые
338
выразятся в радиальном биении зубчатого венца и в иска- жении формы и положения пятна контакта.
Требования к базовым поверхностям заготовок дей- ствующими ГОСТ и ГОСТ Р не установлены, но они могут устанавливаться отраслевыми или заводскими норматив- ными документами.
Для обеспечения заданной точности готовых зубча- тых колес у заготовок нормируют следующие параметры:
–у насадных зубчатых колес – размеры и форма от- верстия (у валиков шестерен – опорные шейки);
–наружный диаметр заготовки;
–радиальное биение наружной поверхности заготовок;
–торцовое биение базового торца заготовки (торца, по которому заготовка базируется на станке при зубона- резании).
Отверстия в заготовке являются технологической базой при нарезании зубчатого колеса, а в готовом зубчатом коле- се – основной, измерительной и монтажной базами, то есть отверстие определяет точность обработки при зубонарезании
иточность измерения при контроле зубчатого колеса.
Таким образом, на заготовках зубчатых колес 3–5-й степени точности диаметры базовых отверстий следует вы- полнять не грубее 7-го квалитета точности, 6–7-й степеней точности – не грубее 8–9-го квалитета, а для колес 8-й сте- пени точности и ниже – не грубее 9–10-го квалитета.
Шероховатость поверхности базового отверстия зуб- чатого колеса 4–5-й степени точности следует выдерживать Ra = 0,32…0,63 мкм, зубчатых колес 6–7-й степени точно- сти – Ra = 0,63…1,25 мкм и зубчатых колес 8–10-й степени точности – Ra = 1,25…2,5 мкм.
Отклонения по наружному диаметру заготовки зуб- чатого колеса сами по себе не влияют на точность зубчатой передачи. Но так как наружная поверхность часто исполь- зуется как измерительная база при измерении на готовом
339
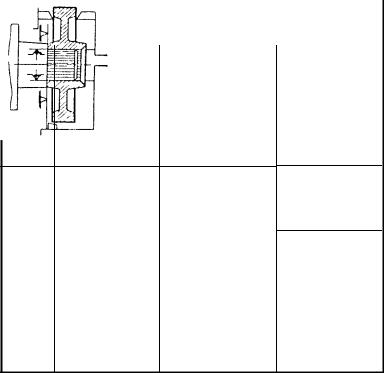
зубчатом колесе ряда параметров, а также как установочная база при базировании на зуборезном станке, то следует ог- раничить отклонения по наружному диаметру допусками в зависимости от использования наружной поверхности.
Технологические маршруты обработки зубчатых ко- лес класса «втулка» и класса «вал» существенно различа- ются. Это различие не зависит от конструктивных особен- ностей зубчатого колеса, а также от типов производства.
Технологический маршрут изготовления зубчатого колеса класса «втулка» приведен в табл. 12.12.
Т а б л и ц а 1 2 . 1 2
Технологический маршрут изготовления зубчатого колеса класса « втулка» в крупносерийном производстве
Номер |
Краткое содержание |
Эскиз |
Оборудование |
|
операции |
операции |
|||
|
|
|||
1 |
2 |
3 |
4 |
|
|
Сверление цен- |
|
Вертикально- |
|
|
трального отвер- |
|
сверлильный ста- |
|
|
стия, зенкерование |
|
нок, например, |
|
05 |
торца, снятие |
|
модели 2А150 |
|
фаски |
|
|
||
|
|
|
|
Протягивание кру- |
Протяжной станок, |
10 |
гового и шпоноч- |
например, модели |
ного отверстия |
7Б720 |
|
|
|
|
|
Предварительная |
Многорезцовый |
|
токарная |
токарный станок, |
|
обработка |
например, модели |
|
|
1720 |
20 |
|
|
340