
книги / Основы технологии машиностроения. Методы обработки заготовок и технологические процессы изготовления типовых деталей машин
.pdfкунды. Припуск под хонингование составляет на сторо- ну 0,002–0,005 мм. Станки для хонингования зубчатых колес во многом аналогичны станкам для шевингования.
Притирка (ляппинг-процесс) широко применяется для чистовой, окончательной отделки зубьев закаленных зубчатых колес.
Притирка получила большое распространение в тех отраслях машиностроения, где требуется изготовление зуб- чатых колес 4–7-й степени точности при шероховатости поверхности Ra = 0,04…0,63 мкм.
Процесс притирки заключается в том, что обрабаты- ваемое зубчатое колесо вращается в зацеплении с чугун- ными шестернями-притирами, смазываемыми пастой, со- стоящей из смеси мелкого абразивного порошка с маслом. Помимо этого обрабатываемое зубчатое колесо и притиры имеют в осевом направлении возвратно-поступательное движение друг относительно друга. Осевое движение уско- ряет процесс обработки и повышает ее точность. В боль- шинстве случаев движение в осевом направлении придает- ся притираемому зубчатому колесу.
Притирочные станки изготавливаются с параллель- ными (рис. 9.27, а) и перекрещивающимися (рис. 9.27, б) осями притиров.
Наибольшее распространение получили притирочные станки, работающие со скрещивающимися осями притиров, устанавливаемых под разными углами. Один из трех при- тиров часто устанавливают параллельно оси обрабатывае- мого зубчатого колеса. При таком расположении притиров зубчатое колесо работает, как в винтовой передаче, и путем дополнительного осевого перемещения притираемого зуб- чатого колеса притирка происходит равномерно по всей боковой поверхности зуба. Притираемое зубчатое колесо
221
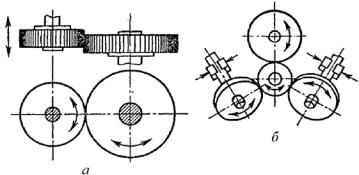
Рис. 9.27. Схемы притирки зубьев цилиндрических зубчатых колес: а – с параллельными осями притиров; б – со скрещивающимися осями притиров
получает вращение попеременно в обе стороны для равно- мерной притирки обеих сторон зуба, необходимое давление на боковой поверхности зубьев во время притирки создает- ся гидравлическими тормозами, действующими на шпин- дели притиров.
Притирка сглаживает неровности и шероховатости поверхности зубьев, придает эвольвентным поверхностям зубьев зеркальный блек, значительно уменьшает шум и уве- личивает плавность работы зубчатых колес. Притиркой можно исправить лишь незначительные погрешности фор- мы. При наличии значительных погрешностей формы зубча- тые колеса перед притиркой следует шлифовать, а затем притирать.
Приработка зубьев отличается от притирки тем, что притираются не зубчатое колесо с притиром, а два парных зубчатых колеса, изготовленных для совместной работы в собранной машине.
Приработка производится при помощи абразивного материала, который ускоряет взаимную приработку зубьев зубчатых колес и придает им гладкую поверхность.
222
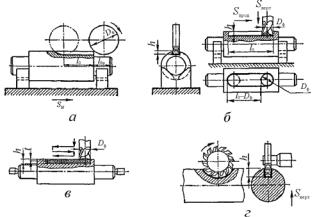
10. МЕТОДЫ ОБРАБОТКИ ШПОНОЧНЫХ ПАЗОВ И ШЛИЦЕВЫХ ПОВЕРХНОСТЕЙ
10.1. Обработка шпоночных пазов
Шпоночные пазы (канавки) на валах изготавливают- ся для призматических и сегментных шпонок. Шпоночные пазы для призматических шпонок могут быть закрытыми с двух сторон (глухие), закрытыми с одной стороны и сквозными.
Шпоночные пазы изготавливаются различными спо- собами в зависимости от конфигурации паза и вала, приме- няемого инструмента. Они выполняются на горизонтально- фрезерных либо вертикально-фрезерных станках общего назначения или на специальных станках.
Сквозные и открытые с одной стороны шпоночные пазы изготавливаются фрезерованием дисковыми фрезами
(рис. 10.1, а).
Рис. 10.1. Методы фрезерования шпоночных пазов валов:
а– дисковой фрезой с продольной подачей; б – концевой фрезой
спродольной подачей; в – концевой фрезой с маятниковой подачей; г – дисковой фрезой с вертикальной подачей
223
Фрезерование паза осуществляется за один-два прохо- да. Этот способ наиболее производителен и обеспечивает достаточную точность ширины паза, но его применение ог- раничивается конфигурацией пазов: закрытые пазы с закруг- лениями на концах не могут выполняться этим способом. Такие пазы изготовляются концевыми фрезами с продоль- ной подачей за один или несколько проходов (рис. 10.1, б).
Фрезерование концевой фрезой за один проход про- изводится таким образом, что сначала фреза при верти- кальной подаче проходит на полную глубину канавки, по- том включается продольная подача, с которой шпоночный паз фрезеруется на полную длину. При этом способе требу- ется мощный станок, прочное крепление фрезы и обильное охлаждение эмульсией. Вследствие того, что фреза работа- ет в основном периферийной частью, диаметр которой уменьшается от переточки к переточке, по мере увеличения числа переточек точность обработки (по ширине паза) ухудшается.
Для получения точных по ширине пазов применяют- ся специальные шпоночно-фрезерные станки с «маятнико- вой подачей», работающие концевыми двуспиральными фрезами с лобовыми режущими кромками. При этом спо- собе фреза врезается на глубину 0,1–0,3 мм и фрезерует паз на всю длину, затем опять врезается на ту же глубину, как и в предыдущем случае, и фрезерует паз на всю длину, но в обратном направлении (рис. 10.1, в). Отсюда происходит название «маятниковая подача».
Этот метод является наиболее рациональным для из- готовления шпоночных пазов в серийном и массовом про- изводстве, так как точность изготовления паза обеспечива- ет взаимозаменяемость в шпоночном соединении. Кроме того, поскольку фреза работает лобовой частью, она будет
224
долговечнее, так как изнашивается лобовая, а не перифе- рийная часть фрезы. Недостатком этого способа является низкая производительность. Из этого следует, что метод маятниковой подачи надо применять при изготовлении па- зов, требующих взаимозаменяемости, а метод фрезерова- ния за один проход следует использовать в тех случаях, ко- гда допускается пригонка шпонок по пазу.
Шпоночные пазы под сегментные шпонки изготав- ливаются фрезерованием при помощи дисковых фрез (рис. 10.1, г). Сквозные шпоночные пазы валов можно об- рабатывать на строгальных станках (длинные пазы – на продольно-строгальных, а короткие пазы – на попереч- но-строгальных станках).
Шпоночные пазы в отверстиях втулок зубчатых колес, шкивов и других деталей, надевающихся на вал со шпонкой, обрабатываются в индивидуальном и мелкосерийном произ- водстве на долбежных станках, в крупносерийном и массо- вом производстве – на протяжных станках.
10.2. Обработка шлицевых поверхностей
Шлицевые соединения применяют для посадок с на- тягом или зазором деталей различного назначения (зубча- тых колес, втулок, шкивов и др.) на валу. По сравнению со шпоночными шлицевые соединения имеют ряд преиму- ществ: детали на шлицевых валах лучше центрируются и направляются при перемещении вдоль вала; напряжения смятия на гранях шлицев меньше, чем на поверхностях шпонок; прочность шлицевых валов при динамических на- грузках выше, чем валов со шпонками.
Наиболее распространены шлицевые соединения с прямоугольной прямобочной (рис. 10.2, а), эвольвентной (рис. 10.2, б) и треугольной (рис. 10.2, в) формой шлицев.
225
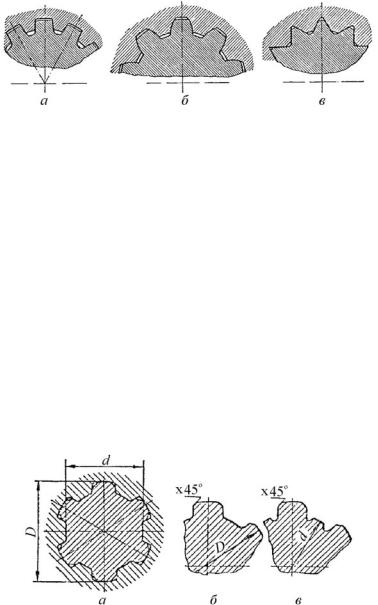
Рис. 10.2. Виды шлицевых соединений
В прямоугольных шлицевых соединениях применяют три способа центрирования (базирования) шлицевого вала
ивтулки:
–по боковым сторонам шлицев;
–по наружному диаметру шлицев;
–по внутреннему диаметру шлицев.
Центрирование по боковым сторонам шлицев при- меняется для соединений с наружным диаметром от 25 до 90 мм в тех случаях, когда точность центрирования втулки не имеет существенного значения и в то же время необходимо обеспечить достаточную прочность соедине- ния в эксплуатации.
В механизмах, где особое внимание уделяется кине- матической точности передач, например в механизмах ме- таллорежущих станков, автомобилей, тракторов и др., при- меняют центрирование по наружному (D) или внутреннему (d) диаметрам шлицев (рис. 10.3, а).
Рис. 10.3. Способы центрирования шлицевых соединений
226
Выбор наружного или внутреннего диаметра в каче- стве центрирующего определяется твердостью поверхно- стей шлицевых пазов и размерами соединения. Если шли- цевые пазы отверстия термически не обрабатываются или твердость их поверхности допускает калибрование протяж- кой после термообработки, то применяют центрирование по наружному диаметру. Если твердость поверхностей от- верстия не позволяет производить калибрование, то приме- няют центрирование по внутреннему диаметру.
Центрирование по внутреннему диаметру применяют также при обработке длинных валов, подвергающихся тер- мообработке, так как в этом случае возможно одновремен- ное шлифование боковых сторон зубьев (выступов) шлицев и внутреннего диаметра вала.
При центрировании по наружному диаметру на углах шлицевых выступов вала (рис. 10.3, б), а при центрирова- нии по внутреннему – в углах шлицевых пазов отверстия выполняются фаски и скругления.
При центрировании по внутреннему диаметру, а так- же при необходимости обеспечить контакт боковых сторон зубьев шлицевого вала и шлицевых пазов отверстия в углах впадин шлицевого вала делают канавки (рис. 10.3, в).
Шлицевые валы с прямоугольными зубьями обраба- тываются специальными профильными фрезами для каж- дого диаметра и числа зубьев.
Эвольвентные шлицевые соединения используют для передачи значительных крутящих моментов, а также в тех случаях, когда к точности центрирования сопрягаемых элементов предъявляются повышенные требования. Эти соединения обладают повышенной прочностью вследствие постепенного утолщения зубьев от вершины к основанию зуба, а также вследствие уменьшения концентрации напря- жений у основания. Кроме того, благодаря применению на этапе обработки шлицев червячной фрезы с прямолиней-
227
ными режущими кромками обеспечиваются более высокая точность обработки и меньшая шероховатость поверхности шлицев, исключающие в большинстве случаев последую- щее шлифование.
При эвольвентном профиле шлицев можно допускать отделочные виды обработки, применяемые при зубообра- ботке: шевингование, шлифование по методу обкатки и др.
Центрирование эвольвентных соединений обычно осу- ществляется по боковым (эвольвентным) сторонам шлицев.
Треугольные шлицевые соединения используют глав- ным образом для неподвижных соединений при небольших величинах крутящего момента (чтобы избежать прессовых посадок), а также для тонкостенных втулок. Центрирование при этом виде шлицевых соединений осуществляют по бо- ковым сторонам шлицев.
Фрезерование шлицев валов небольших диаметров
(до 100 мм) осуществляют за один проход, больших диа- метров – за два прохода.
Черновое фрезерование шлицев, в особенности боль-
ших диаметров, иногда производится фрезами на горизон- тально-фрезерных станках, имеющих делительные меха- низмы (рис. 10.4).
На рис. 10.4, а показано фрезерование одной канавки шлицев дисковой шлицевой (фасонной) фрезой. Фрезеровать шлицы можно способом (см. рис. 10.4, б), позволяющим применять более дешевые фрезы, чем дисковые фасонные фрезы. Более производительным способом является одно- временное фрезерование двух шлицевых канавок двумя дисковыми фрезами специального профиля (рис. 10.4, в).
Чистовое фрезерование шлицев дисковыми фрезами производится только в случае отсутствия специального станка и инструмента, так как оно не дает достаточной для взаимозаменяемости точности по шагу и ширине шлицев.
228
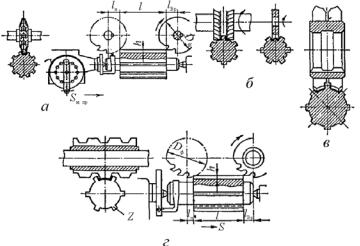
Рис. 10.4. Способы фрезерования шлицев валов: а – шлицевой дисковой фрезой; б – двумя фрезами; в – двумя дисковыми специальными фрезами; г – шлицевой червячной фрезой
Более точное фрезерование шлицев производится ме- тодом обкатки при помощи шлицевой червячной фрезы (рис. 10.4, г). Фреза, помимо вращательного движения, по- лучает продольное перемещение вдоль оси нарезаемого вала. Этот способ является наиболее точным и производи- тельным.
При центрировании втулки (или зубчатого колеса) по внутреннему диаметру шлицев вала как червячная, так и дисковая фреза должна иметь «усики», вырезающие ка- навки в основании шлица, чтобы не было заедания во внут- ренних углах.
Шлифование шлицев валов: при центрировании по наружному диаметру шлифуют только наружную ци- линдрическую поверхность на обычных круглошлифоваль- ных станках. Шлифование впадины (то есть по внутренне- му диаметру шлицев вала) и боковых сторон шлицев в этом случае не применяется.
229
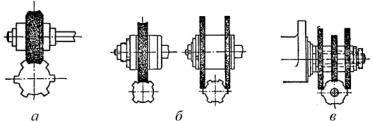
При центрировании шлицевых валов по внутреннему диаметру шлицев фрезерование последних дает точность по внутреннему диаметру до 0,05–0,06 мм, что не всегда достаточно для обеспечения точной посадки.
Если шлицевые валы после чернового фрезерования прошли термическую обработку в виде улучшения или за- калки, то после этого они не могут быть подвергнуты чисто- вому фрезерованию. В этом случае шлицевые валы необхо- димо шлифовать по поверхностям впадины (то есть по внут- реннему диаметру) и боковым сторонам шлицев. Наиболее производителен способ шлифования фасонным шлифоваль- ным кругом (рис. 10.5, а).
Рис. 10.5. Способы шлифования шлицев валов: а – фасонным шлифовальным кругом; б – в две операции: сначала одним,
азатем – двумя шлифовальными кругами;
в– тремя шлифовальными кругами
Однако при таком способе шлифования шлифоваль- ный круг изнашивается неравномерно ввиду неодинаковой толщины снимаемого слоя у боковых сторон и впадины вала. Для восстановления формы шлифовального круга требуется частая правка. Несмотря на этот недостаток, дан- ный способ широко распространен в машиностроении.
Шлифовать шлицы можно в две отдельные операции (рис. 10.5, б). На первой операции шлифуют только впади- ны по внутреннему диаметру, а на второй – только боковые стороны шлицев. После каждого продольного хода стола
230