
книги / Системы, технологии и организация услуг в автомобильном сервисе. Ч. 1
.pdf–системой и средствами связи (телефон, факс);
–оргтехникой (компьютеры, принтеры, модем, копировальный аппарат и т.д.);
–мебелью (столы, стулья, шкафы, полки);
–сейфом для хранения документов.
Бытовые помещения включают места отдыха и приема пищи, раздевалки, душевые, санитарные узлы и др.
В помещениях основного назначения выделяются зоны: разгрузки, приемки товаров по количеству и качеству, хранения, комплектования заказов для отправки, упаковки, погрузки. Эти зоны обычно связаны между собой проходами и проездами. Зона разгрузки примыкает к зоне приемки товаров по количеству и качеству. Зона хранения занимает основную часть площади склада. К зоне хранения примыкают зоны комплектования и упаковки запасных частей и материалов.
Для хранения тарных и штучных грузов (запасных частей) чаще всего применяются стеллажи. Сборно-разборные стеллажи собирают из унифицированных деталей и узлов, допускающих различные варианты компоновки.
Каркасные стеллажи состоят из металлической обрешетки, вертикальных стоек и горизонтальных балок. Перфорация в стойках позволяет переставлять горизонтальные балки и изменять высоту ячейки стеллажа.
«Проходные», «набивные» каркасные стеллажи или стеллажи «глубокого складирования» применяются для хранения товаров на поддонах в тех случаях, когда номенклатура запасных частей небольшая и по каждому наименованию большое количество поддонов. Грузовые полки выполнены из специального профиля с ловителем, позволяющим точно устанавливать поддоны с грузом. Грузовые полки крепятся к рамам и стойкам с помощью кронштейнов. Вверху рамы и стойки связываются с помощью связей и талрепов. Ширина секции или загрузочной ячейки определяется рас-
351
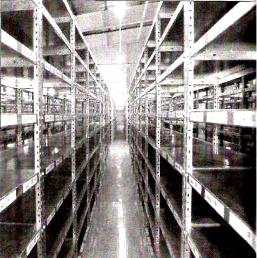
стоянием между рамами (стойками) и бывает обычно 1480 или 1380 мм.
На рис. 2.14 представлено планировочное решение склада автосервиса и вариант расстановки стеллажей для запасных частей автомобилей.
Рис. 2.14. Объемно-планировочное решение склада автосервиса и вариант расстановки стеллажей
Самыми распространенными из универсальных стеллажей являются полочные, называемые так из-за сплошных полок, укрепленных на рамах и балках. Рамы изготавливаются из специального профиля, имеющего перфорацию с шагом 50 или 75 мм, что позволяет регулировать расстояние между грузовыми полками. Высота рам зависит от высоты склада и достигает порой 38 м. Конструктивные размеры балок выбираются в зависимости от расчетной нагрузки.
Ширина рам выбирается в каждом конкретном случае в зависимости от габаритов товаров. Чаще применяются раз-
352
меры 550, 700, 900 мм. Длина балок выбирается в зависимости от веса запасных частей, которые будут храниться.
Стеллажи должны быть прочными, устойчивыми и крепиться между собой и к конструкции зданий. Проходы между стеллажами должны быть шириной не менее 1 м.
Стеллажи должны быть изготовлены в соответствии с требованиями ГОСТ 14757–81 «Стеллажи сборно-разбор- ные. Типы, основные параметры и размеры» (И-1-Х-87, И-2-VII-92) и ГОСТ 16140–77 «Стеллажи сборно-разборные.
Технические условия» (И-1-VI-84, И-2-VIII-89).
2.4.4. Технология складских работ
Логистические задачи
Моделирование процессов на складе для определения маршрутов товарных потоков, выбора стандартов документооборота, формирования организационно-штатной структуры и алгоритмов функционирования.
Определение по результатам моделирования содержания операций на каждом рабочем месте, составление технологических карт процессов и должностных инструкций и выбор оборудования для оснащения склада.
Формирование технологических маршрутов и технологических карт на выполнение технологических операций склада.
Разработка вариантных резервов и обходных технологий для различных вариантов исполнения складских операций.
Обеспечение фиксации затрат времени персонала и оборудования на комплектацию заказов, а также расчета времени готовности партии товара по заказу.
Организация контроля и планирования загрузки персонала и оборудования при исполнении текущих и планируемых операций.
353
Оптимизация процессов
Ускорение движения товарных потоков на складе определяется ускорением обработки товаров и документов на всех технологических этапах. Например, пути перемещения товаров стараются «выпрямить» в горизонтальном и в вертикальном направлении – это сокращает сроки перемещения.
В качестве средств оптимизации сроков технологических процессов на складах используют компьютерные системы, диспетчеризацию, технологические карты, сетевые графики, оперативное планирование, системы радиосвязи, внутригородское телевидение и другие средства оргтехники.
Диспетчеры обеспечивают оперативное регулирование всех операций – погрузочно-разгрузочных работ, оформления приемных и отгрузочных документов, выдачи и отправки товаров заказчикам.
Технологические карты – подробное описание последовательности и методов выполнения складских операций
иперечень документов, составляемых по ходу работы на основании соответствующих инструкций и нормативных документов. Они предназначены для эффективного использования средств труда и рабочей силы, исключения ошибок при выполнении операций. Их разрабатывают на отдельные этапы складской обработки (приемка, размещение, хранение, отбор товаров и т.д.) применительно к функциям отдельных специалистов или групп (бригад) специалистов – водителей подъемно-транспортных машин, отборщиков, упаковщиков
идругих складских работников.
Технологические процессы необходимо четко организовать, т.е. планировать сроки и объемы поступления и отпуска товаров, использования рабочего времени, складских площадей и средств.
Графики работы погрузочно-разгрузочных механизмов, графики прибытия покупателей для получения товаров, графики работы экспедиции и т.д. помогают планировать за-
354
грузку людей и выполнение операций в течение определенных периодов.
Сетевое планирование при помощи сетевых моделей
играфиков, представляющих собой графическое последовательное изображение операций с расчетными параметрами
исроками исполнения, помогает увязать темпы исполнения многих операций для получения в желаемый срок необходимого результата – например, отбора и упаковки крупной партии товаров для загрузки целого состава и морского судна.
Сроки движения товаров и документооборота пропор-
циональны количеству номенклатурных позиций запаса и количеству учетных операций между различными структурными единицами, которые необходимы для прослеживания движения товаров и оформления необходимой документации.
Скорость движения товаров может быть увеличена и за счет предварительных заказов клиентов на товары.
2.4.5.Определение номенклатуры
иобъемов хранения агрегатов, узлов и деталей на складах различного уровня
Очевидно, что хранить все выпускаемые в качестве запасных частей детали у дилера и, тем более на АТП, не рационально. Это приведет к значительному увеличению запасов, росту складских площадей и, самое главное, к неэффективному использованию запасов – большая их часть останется лежать «мертвым грузом». С другой стороны, поскольку выход деталей из строя носит случайный характер, теоретически в любой момент может понадобиться любая из запасных частей.
Изучение отечественного и зарубежного опыта организации МТО показало, что решается эта сложная задача путем применения складской формы продвижения продукции от изготовителей к потребителям, заключающейся в централи-
355

зации различных по номенклатуре и объему запасов на складах различных уровней.
По мере необходимости детали нужной номенклатуры со склада высшего уровня передаются на склад низшего уровня, поддерживая тем самым необходимый для удовлетворения спроса запас на каждом из них.
Определение номенклатуры запасных частей и объемов хранения на складах разного уровня осуществляется различными методами. В основу наиболее распространенного положено деление всей номенклатуры запасных частей для каждой модели автомобиля по частоте спроса на группы А, В
и С (рис. 2.15).
Рис. 2.15. Взаимосвязь номенклатуры N и стоимости SΣ запасных частей (график АВС)
Первая группа (детали высокого спроса) включает около 20 % общей номенклатуры запасных частей. Ими удовлетворяется около 85 % заказов потребителей, а стоимость составляет 65 % стоимости всей потребляемой номенклатуры. Именно эти детали чаще всего выходят из строя, и путем за-
356

мены их у дилеров, на СТО и АТП устраняют большую часть неисправностей и отказов.
Вторая группа (детали среднего спроса) включает около 20 % общей номенклатуры, но ими удовлетворяется только 10 % спроса на запасные части, а стоимость составляет около
10 %.
Третья группа (детали редкого спроса) включает более 60 % общей номенклатуры. Ими удовлетворяется 5 % спроса на запасные части, стоимость составляет около 5 %.
Потребность в деталях, относящихся к той или иной группе, определяют путем анализа продаж за предыдущие периоды и перераспределяют их с учетом текущей информации о спросе и движении запасных частей в системе.
Для определения объема хранения каждой детали и момента заказа очередной партии применяются сложные эко- номико-математические расчеты. С их помощью определяют размер заказа и количество заказов в году, при которых суммарные затраты на закупку и хранение одной детали минимальны (рис. 2.16).
Рис. 2.16. Определение оптимального размера и момента заказа запасных частей: 1 – затраты на закупку, 2 – на хранение, 3 – суммарные
357

Если одновременно заказать всю годовую потребность в деталях, то затраты на закупку (подготовка заказа, получение и доставка, контроль и др.) будут на единицу заказа минимальными, связанные с хранением, – максимальными. Например, при годовой потребности в 300 деталей и единовременном их заказе запас в течение года будет изменяться от максимального, равного 300, до минимального, равного нулю. При этом расходы на хранение будут определяться средним по году уровнем запаса, равным 150 деталям.
Если размер заказа сократить в 10 раз (до 30 деталей), то расходы на хранение будут определяться новым средним уровнем запаса, равным 15 деталям, т.е. сократятся, а затраты на закупку увеличатся (вместо одного – 10 заказов).
Оптимальный размер заказа Q по критерию минимизации совокупных затрат на хранение запаса и повторение заказа рассчитывается по формуле Вильсона:
Q = 2AS / C,
где А – затраты на закупку единицы заказа, руб.; S – годовой расход данной детали, шт.; С – затраты на хранение единицы заказа, руб.
Сеть сбыта строится таким образом, чтобы гарантировать получение клиентами деталей, относящихся к группе А, в течение суток, а к группам В и С – через 2–3 суток после поступления заказа. Для этого объемы хранения деталей во всех звеньях сети регулируются так, чтобы на складах дилеров хранились 1–2-месячные запасы деталей высокого спроса, а на региональных – 2–3-месячные запасы деталей высокого и среднего спроса.
Контрольные вопросы
1. Каковы основные функции складского хозяйства предприятия?
358
2.Дайте классификацию складов и их характеристику.
3.Порядок хранения изделий и материалов на складах автосервисного предприятия.
4.Объемно-планировочные решения складских помещений.
5.Конструктивные решения складов.
6.Укажите типы стеллажей, применяемые на складах предприятий.
7.В чем заключается оптимизация процессов складских
работ?
8.Как определяется номенклатура и объемы хранения запасных частей на складах?
2.5.Нормирование и определение потребности
в ресурсах в автотранспортных организациях
2.5.1. Нормы расхода запасных частей
Назначение и виды норм. Потребность в запасных частях для ТО и ремонта проявляется в процессе эксплуатации
иопределяется:
–надежностью изделия;
–уровнем технической эксплуатации;
–условиями эксплуатации. Потребность в запасных частях:
–диктует спрос на них;
–определяет размер запасов на предприятиях, объем
ипериодичность заказов;
– определяет финансовые затраты на приобретение и содержание запасных частей, которые, например, при ТР достигают 40 %.
Потребность в запасных частях оформляется в виде норм расхода. Виды норм:
– финансовые – средние удельные затраты на запасные части, расходуемые на эксплуатацию, в том числе по видам ТО и ремонта (ТО-1, ТО-2, ТР), руб/1000 км; применяются
359

для парка автомобилей при планировании расходов; определяются обобщением опыта, данными по фактическим расходам, аналитическими расчетами;
–номенклатурные (Н) – устанавливают средний рас-
ход конкретной детали в штуках на п автомобилей в год
(в России п = 100), содержатся в каталогах заводов-изготови- телей, номенклатурных тетрадях, у дистрибьюторов; включают от 400 до 800 наименований деталей;
–индивидуальные – разрабатываются для конкретного АТП, фирмы, маршрута, учитывают специфику эксплуатации.
Методы определения норм. В основе расчета всех форм – данные по надежности и условиям эксплуатации автомобилей.
Аналитический (точный) – использование данных по ведущей функции потока отказов или замен Ω(t).
Из рис. 2.17 следует, что за t, HI = Ωt(t)100;
за ∆t = t2 −t1, |
HI = |
Ω(t2 ) −Ω(t1 ) |
100. |
|
|
|
||
t2 |
−t1 |
|
|
|
||||
|
|
|
|
|
|
|||
Пример. Ω(t |
= 10) = |
15 деталей: t = |
10 лет. HI = |
|||||
|
|
|
= (15·100)/10 |
|
= 150, т.е. |
|||
|
|
|
|
150 деталей на 100 автомо- |
||||
|
|
|
|
билей в год. |
|
|
|
|
|
|
|
|
|
|
|
||
|
|
|
|
|
Приближенная оценка |
|||
|
|
|
|
|
||||
|
|
|
|
по ресурсу до 1-й замены |
||||
|
|
|
|
детали: |
|
Lг |
100, |
|
|
|
|
|
|
HII = |
|
||
|
|
|
|
|
|
|||
|
|
|
|
|
|
|
||
|
|
|
|
|
|
η L |
||
|
|
|
|
|
|
|
1 |
|
|
|
|
|
где Lг – средний годовой |
||||
|
|
|
|
|||||
Рис. 2.17. Определение нормы |
|
пробег автомобиля; L1 – ре- |
||||||
по Ω(t) |
|
|
|
сурс до 1-й замены детали; |
||||
|
|
|
η – коэффициент восстанов- |
|||||
|
|
|
|
ления ресурса.
360