
книги из ГПНТБ / Григорьев Ю.П. Строительная механика летательных аппаратов дополнительные главы
.pdfВ обоих случаях напряжения меняются по линейному закону и объемы зоны действия наибольших напряжений будут не сильно отличаться по величине. Поэтому предел выносливости при кру чении оказывается примерно в два раза меньше предела вынос ливости при изгибе.
Сравнивая выносливость при изгибе и кручении, следует учи тывать наличие в первом случае растягивающих напряжений, действующих перпендикулярно плоскостям сдвига и способствую щих ускорению накопления усталостных повреждений.
Для большинства металлов с целью примерной оценки их выносливости при различных способах нагружения можно поль зоваться следующими экспериментальными зависимостями:
*уи = |
(1,5±0,5)аур, |
(3 4 2') |
тук = |
(0,58 + 0,12) зу р. |
|
Значительные колебания коэффициентов объясняются не только природой явлений, протекающих в металле при перемен ном нагружении, но и степенью точности определения пределов выносливости. Если обычная точность определения характери стик статической прочности, например, предела текучести, состав ляет 2—3%, то ошибки при определении предела выносливости не меньше 6% за счет большего разброса экспериментальных
точек.
Разрушение при повторном сжатии в принципе возможно, но требует в сотни раз большего числа циклов нагрузки, чем разру шение при растяжении равными по величине напряжениями. Этот факт доказывает влияние знака нормальных напряжений на ход процесса зарождения и раз вития усталостной трещины.
При равных касательных напряжениях наличие сжи мающих нормальных напря жений по плоскостям сдвига задерживает развитие уста
|
|
|
лостной трещины. |
|
|
|
|
|
На |
практике усталостное |
|
|
|
|
разрушение от сжатия встре- |
||
W3 |
to4 |
10s |
106 N чается |
крайне редко. |
При |
|
|
|
мер кривой усталости |
при |
|
|
Фиг. |
3.4.2 |
сжатии |
приведен |
на |
|
|
|
фиг. 3.4.2. |
|
Закон распределения напряжений в поперечном сечении стер жня влияет на развитие усталостного разрушения в значительно большей степени, чем при статическом разрушении. Эффект паде ния усталостной прочности с увеличением размеров детали (мас штабный фактор), по-видимому, связан с изменением градиента напряжений. Из фиг. 3.4.3 видно, что при равных максимальных
82
напряжениях omax уменьшение напряжений в образце большого диаметра идет медленнее, благодаря чему значительный объем материала подвергается действию больших напряжений. Вероят ность разрушения деталей возрастает с увеличением абсолютных размеров.
Точно также факт уменьшения эффективного коэффициента концентрации по сравнению с теоретическим может быть объяс нен сильным влиянием градиента напряжений, возникающим в месте концентрации. Благодаря быстрому уменьшению напря жений по мере удаления от поверхностных слоев, в неблагоприят ных условиях нагружения оказывается очень небольшой объем материала и накопление усталостных повреждений идет значи тельно медленнее, чем это можно было бы ожидать в случае, если бы напряжения большой величины распространялись на значи тельную часть сечения. В результате эффект концентрации напря жений оказывается не очень сильным.
Таким образом, влияние градиента напряжений приводит к уменьшению величины эффективного коэффициента концентра ции по сравнению с теоретическим.
3.5.ПОНЯТИЕ О МЕХАНИЗМЕ ВОЗНИКНОВЕНИЯ
ИРАЗВИТИЯ УСТАЛОСТНОГО РАЗРУШЕНИЯ
Под влиянием переменной нагрузки в материале происходят необратимые физико-химические процессы, приводящие к ослаб лению отдельных участков зерен и постепенному накоплению повреждений по мере увеличения числа циклов нагрузки. Внешне эти изменения проявляются в виде пластических деформаций, возникающих в отдельных наиболее слабых зернах и распростра няющихся затем на более широкие области.
Начальную фазу подготовки усталостного разрушения можно разбить на четыре стадии:
6* |
83 |

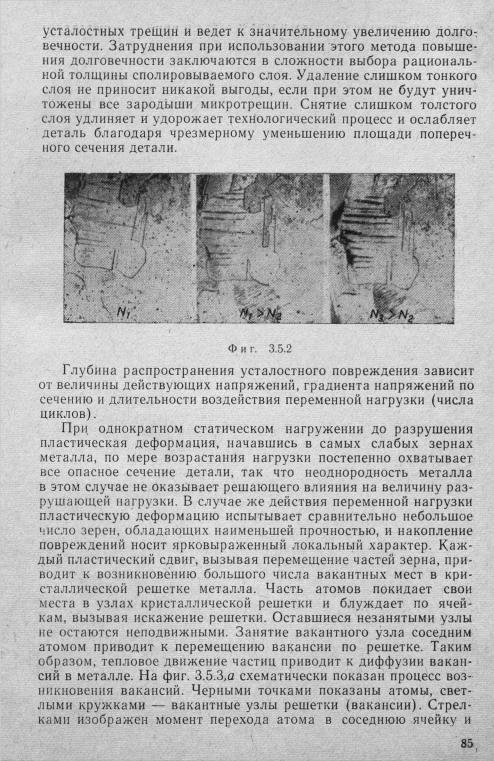
появления вакансии. Кристаллическая решетка условно показана неискаженной. В действительности вокруг атомов, внедрившихся в соседние ячейки, решетка будет несколько расширена, а вокруг вакансий несколько сужена. На фиг. 3.5.3,6 показан процесс диф фузии и скапливания вакансий (стрелками показан переход соседних атомов в вакантные узлы). Скопление вакансий на фиг. 3.5.3,6 ограничено волнистой линией.
Каждый цикл переменной нагрузки приводит к появлению новых вакансий. Часть из них занимается случайными атомами, блуждающими по решетке. Остальные, скапливаясь вместе в ре зультате диффузии, образуют сначала микроскопические полости (пустоты), а затем сливаются в мельчайшие трещины. Разумеется эти трещины образуются вблизи мест интенсивного образования вакансий, т. е. внутри полос скольжения. Хаотичность располо жения зародышей трещин объясняется случайным характером процесса появления и накапливания вакансий.
Влияние скорости нагружения и температуры на усталостную прочность металлов может быть объяснено с точки зрения вакансионного механизма накопления усталостных повреждений. Для скопления вакансий в микропоры необходим определенный про межуток времени, длительность которого определяется скоростью
диффузии несовершенств (вакансий, |
блуждающих |
атомов) |
в атомной решетке. Скорость диффузии |
определяется |
составом |
металла, микроструктурой и температурой. Повышение темпера туры ускоряет движение частиц и увеличивает вероятность объ единения вакансий, возникших при пластической деформации.
Чем меньше скорость нагружения (частота цикла), тем боль ше времени для протекания процесса образования усталостных повреждений, тем меньшее число циклов требуется для разруше ния детали.
Объединение несовершенств решетки, скапливание их в ко лонии, внешне проявляется в виде релаксации напряжений, так
8G
как при этом уменьшается суммарная внутренняя энергия дефор мированного тела. Самопроизвольные перемещения частиц, их диффузия внутри тела, согласно законам термодинамики всегда ведут к уменьшению энергии системы. Релаксация напряжений происходит на протяжении всего процесса нагружения, как при увеличении, так и при уменьшении усилий. Однако с достаточной интенсивностью она будет идти только при наличии большого числа вакантных мест, т. е. при условии возникновения повтор ных местных пластических деформаций.
При медленных (статических) повторных нагрузках напряже ния, созданные пластической деформацией материала, успевают прорелаксировать почти полностью, а это означает, что большин ство вакансий объединяются в микропоры. В силу медленного изменения нагрузки процесс идет без существенного повышения температуры, так что скорость диффузии внутри металла опреде ляется температурой окружающей среды.
Увеличение скорости нагружения приводит к постепенному росту числа циклов, потребных для накопления повреждений, вызывающих усталостное разрушение. Каждый цикл с увеличе нием частоты нагружения дает все меньшую и меньшую долю повреждения. Времени для полного объединения вакансий не хватает.
Однако рост скорости испытания приводит к повышению тем пературы образца и увеличению скорости диффузии. Этот фак тор, ускоряющий процесс объединения вакансий, частично гасит
эффект |
уменьшения времени, приходящегося на один Цикл, и |
||||||
в конце |
концов приводит |
к тому, что дальнейшее увеличение |
|||||
частоты |
перестает |
влиять |
на величину |
Предела |
выносливости |
||
материала. Поэтому при испыта |
|
|
|||||
нии на |
средних частотах от 10 до |
|
|
||||
50 гц кривые усталости для одно |
|
|
|||||
го и того же материала практиче |
|
|
|||||
ски совпадают. |
|
|
|
|
|
||
По мере увеличения |
перепада |
|
|
||||
температуры |
образца |
и |
внеш |
|
|
||
ней среды возрастает теплоотда |
Фиг. |
3.5.4 |
|||||
ча в воздух |
через |
поверхность |
|
|
|||
образца |
и рост, температуры образца с увеличением частоты |
||||||
начинает замедляться. |
Увеличение частоты испытания свыше |
||||||
50 гц ведет к медленному |
возрастанию |
предела |
выносливости |
||||
(фиг. 3.5.4). |
|
|
|
|
|
|
Замедленный из-за повышенной теплоотдачи нагрев образца больше не в состоянии компенсировать продолжающееся сокра щение времени протекания каждого цикла нагружения.
Повышение температуры внешней среды Т2 > приводит к снижению выносливости материала при всех частотах v нагруз ки (пунктирная линия на фиг. 3.5.4).
87
Справедливость приведенных выше рассуждений доказывает ся путем испытания на выносливость при различных условиях теплоотвода. Ухудшение теплоотвода всегда приводит к падению предела выносливости. В то же время искусственное охлаждение образца во время испытания значительно замедляет развитие усталостного разрушения.
Влияние масштабного фактора (уменьшение предела вынос ливости с увеличением диаметра детали) частично объясняется неизбежным повышением скорости диффузии вакансий в массив ных деталях. При одинаковых максимальных напряжениях и оди наковых режимах усталостного испытания нагрев массивного образца будет сильнее, так как накапливаемая тепловая энергия пропорциональна объему, а количество отводимого тепла про порционально площади поверхности образца.
3.6.МЕТОДЫ ИССЛЕДОВАНИЯ ПОВРЕЖДАЕМОСТИ ПРИ ДЕЙСТВИИ ПЕРЕМЕННЫХ НАГРУЗОК
Под действием переменных нагрузок происходит постепенное необратимое изменение механических свойств материала и накоп ление мельчайших повреждений, приводящих к разрушению детали.
Кривые выносливости строятся по результатам эксперимен тов, при которых испытываемые образцы или детали доводятся до полного разрушения и определяется суммарное число циклов нагрузки, потребное для разрушения при данном уровне макси мальных напряжений. В эту сумму входит как количество цик лов, идущее на подготовку образования усталостной трещины, так и количество циклов, вызывающее рост макроскопической трещины вплоть до момента поломки.
Появление трещины, обнаруживаемое каким-либо методом дефектоскопии, говорит о необратимом повреждении детали, уменьшающем ее несущую способность. Такая деталь непригодна для дальнейшей эксплуатации.
Поэтому, если конструктор для определения прочности дета лей по разрушающим нагрузкам использует кривые выносливо сти, то для инженера-эксплуатационника больший интерес пред ставляют условные кривые п о в р е ж д а е м о с т и , показываю щие момент возникновения в детали трещин недопустимо боль шой величины. Кривые повреждаемости могут использоваться для оценки времени, потребного для полного разрушения детали,
вкоторой обнаружена зародышевая трещина (время доломки детали). Это минимальное время, которое можно гарантировать
вкачестве дополнительного срока службы детали, выработавшей установленный ресурс, но не имеющей заметных повреждений,
которые могли бы быть обнаружены более совершенными мето дами дефектоскопии.
Условная кривая повреждаемости 1 (фиг. 3.6.1) по характеру напоминает кривую выносливости 2 для данного материала, но
88
лежит левее последней. Разумеется положение кривой 1 целиком зависит от чувствительности метода дефектоскопии, с помощью которого определялся момент появления усталостного поврежде ния. Чем чувствительнее метод дефектоскопии, тем раньше обна руживается повреждение и тем левее располагается соответст вующая кривая повреждаемости.
Для каждого металла существует своя предельная кривая повреждаемости, которая соответствует настолько малым уста лостным повреждениям, что они не оказывают влияния на вели чину долговечности образца при его дальнейшем испытании при более высоких нагрузках (пунктирная кривая 3 на фиг. 3.6.1).
Построение предельной кривой повреждаемости требует боль шого количества образцов и длительного времени испытания. Сначала строится обычная кривая выносливости. Другие образ цы из той же партии подвергают предварительному действию переменной нагрузки при различных уровнях наибольших напря жений цикла от8Х, а затем строят вторичную кривую выносливости, 0
определяя остаточную |
долговеч |
ность предварительно |
нагружен |
ных образцов. |
повреж |
Предельная кривая |
|
даемости представляет |
большой |
теоретический интерес, но на практике имеет ограниченное при
менение. |
|
( |
|
Большой практический |
инте |
||
рес |
представляют |
условные |
|
кривые |
повреждаемости |
1 |
(фиг. 3.6.1). Для их построения применяют метод красок, маг нитный метод, метод ультразвуковой дефектоскопии и метод вихревых токов. Методы обнаружения трещин перечислены в по рядке возрастания их чувствительности. Последний метод еще находится в стадии разработки.
Обнаружение трещин с помощью метода красок производит ся следующим образом. На обезжиренную поверхность образца наносится слой жидкой красной краски, легко проникающей в трещины. Затем этот слой тщательно удаляется с поверхности и заменяется тонким слоем более густой белой краски. Красная краска, заполнившая трещины, диффундирует сквозь слой белой краски и на поверхности отчетливо проступают очертания тре щины.
Магнитный метод применим только к образцам и деталям из ферромагнитных материалов. Для обнаружения трещины обра зец намагничивают с помощью сильного постоянного магнита, а район предполагаемого появления трещины поливают эмульсией из мелких железных опилок, смешанных с керосином и трансфор маторным маслом. Опилки притягиваются к местам сгущения
89
магнитных силовых линий вблизи поверхностных трещин и выяв ляют их очертания.
Для обнаружения поверхностных трещин с помощью ультра звукового дефектоскопа применяется специальная головка, обес печивающая излучение остронаправленного пучка ультразвуко
вых волн. Схематически ход луча показан на фиг. 3.6.2. Дойдя до торцевой поверхности 1-го образца ультразвуковая волна отра жается от нее и возвращается через головку 2 в дефектоскоп,
Ф и г. 3.G.3
вызывая появление на экране осциллографа концевого импульса.
Если контакт между головкой излучателя |
и образцом отсутст |
||
вует, |
то на экране будет виден только |
начальный |
импульс |
|
(фиг. 3.6.3,а). Расстояние меж |
||
|
ду начальным и конечным им |
||
|
пульсами (фиг. 3.6.3,6) пропор |
||
|
ционально длине пробега луча, |
||
|
т. е. расстоянию между точкой |
||
|
контакта головки с поверхно |
||
|
стью и торцом образца. |
||
|
При |
появлении поверхност |
|
|
ной трещины часть ультразву |
||
|
кового пучка отразится от воз |
||
3.6.4) |
никшего препятствия (фиг. |
||
и даст на экране промежуточный импульс (фиг. |
3.6.3,в'), |
положение которого мажду начальным и концевым импульсами соответствует месту расположения трещины на образце.
90
Ультразвуковой метод позволяет обнаруживать поверхности ные трещины в самом начале их зарождения, когда метод кра сок и даже магнитный метод не дают никаких результатов. На оборот, все трещины, обнаруживаемые методом красок и магнит ным методом, надежно выявляются и с помощью направленной поверхностной ультразвуковой волны.
На фиг. 3.6.5 показаны в полулогарифмической системе коор динат участки кривых повреждаемости и разрушения в зоне огра ниченной долговечности для дуралюмина Д16Т. Кривая повреж-
О,кг/см
2500
2250
2000
1750 |
|
|
1500 |
5,5 |
6,0 IgN |
5,0 |
||
Ф л г. |
3.6.5 |
|
даемости 1 получена с помощью ультразвука, кривая 2 — мето дом красок. Кривая 3 соответствует разрушению от усталости. По расстоянию между этими кривыми можно судить о количестве
циклов, |
необходимом |
для |
_________________________ |
|||||||||
долом,ки образца |
на данном |
rj, % ---- :____J.,.. |
J |
,, |
!..°. |
|||||||
уровне |
напряжений. Относя |
|
. |
О |
----------- г°— |
|||||||
|
|
о |
1 |
|||||||||
|
|
0 |
||||||||||
число |
циклов доломки |
(от- |
7 J --------------------------- ------------ |
|||||||||
резок АВ на фиг. |
|
3.6.5) |
к |
|
|
|
|
|
||||
количеству |
циклов, |
при |
ко |
|
|
|
|
|
||||
тором |
|
появляется |
первая |
50 |
|
X |
|
1 " |
||||
трещина, |
обнаруживаемая |
___ (___ ^ |
“_________ 2_ |
|||||||||
данным методом (точка А), |
|
|
|
X |
___ ;;. |
|||||||
_________________ * |
||||||||||||
получим |
кривую |
изменения |
^ |
|
|
|
|
|||||
относительной |
|
остаточной |
0 ------- ------- --------------- ------- |
|||||||||
долговечности |
|
материала |
||||||||||
в зависимости |
от |
величины |
!500 |
2000 |
|
2500 о,кг/с»^ |
||||||
максимального |
напряжения |
|
фиг |
366 |
|
цикда.
Как видно из фиг. 3.6.6, относительное число циклов доломки для дуралюмина Д16Т практически не зависит от уровня напря жений. Применение ультразвуковой дефектоскопии (кривая 1 фиг. 3.6.6) гарантирует примерно 90% остаточной долговечности
91