
Метод_практ_СДВЗ
.pdf
Рис. 5. Коленчатый вал дизеля Доксфорд типа J с укороченными расстояниями между смежными опорами (цилиндрами).
Для обеспечения равномерного хода двигателя вспышки в рабочих цилиндрах должны чередоваться через одинаковые углы п. к. в. α; поэтому для двигателей:
четырехтактных ...... α =
двухтактных ……….α =
(i - число цилиндров).
Для равномерного нагружения вала и опорных подшипников вспышки у двух последовательно работающих цилиндров не должны происходить в смежных цилиндрах, а должны иметь место в цилиндрах, расположенных по возможности по разные стороны от центра тяжести вала.
Неравномерная заклинка колен применяется иногда как исключение для улучшения уравновешивания двигателя (например у 4-тактного 9-цилиндрового дизеля).
Окончательный выбор оптимальной схемы коленчатого вала делают после детального динамического расчета двигателя.
Основные размеры колена зависят в первую очередь от радиуса кривошипа R, диаметров шеек и расстояния между серединами двух смежных коренных подшипников lц; последние, соответствующие расстоянию между соседними цилиндрами, зависят в основном от конструктивного оформления и габаритных размеров рабочих цилиндров и крышек.
81
Расстояние между цилиндрами lц |
должно |
быть минимально- |
возможным, чтобы обеспечить наименьшую общую длину двигателя L. |
||
Применение легированных сталей |
вместо |
углеродистых при |
одинаковых запасах прочности приводит к уменьшению жесткости колена. В известных условиях при такой замене сорта стали жесткость вала может оказаться недостаточной.
Наименьшие значения lц применяются в 4-тактных легких многооборотных двигателях, а наибольшие - у 2-тактных мощных малооборотных.
Коренные шейки, как правило, выполняются все одинакового диаметра. Окружные скорости на поверхности шейки обычно не превосходят
10 м/сек.
Полые шейки уменьшают вес вала, позволяют контролировать
доброкачественность поковок вала и могут быть использованы |
для |
подвода смазки. |
|
Шатунные шейки выполняют обычно того же диаметра, |
что и |
коренные. Уменьшение dш (по сравнению с dk) практикуется для уменьшения масс вращающихся частей и для облегчения возможности выемки шатуна с поршнем через рабочий цилиндр, так как габаритные, размеры нижней головки шатуна зависят в первую очередь от dш.
Щекам колена придают различные конструктивные формы в зависимости от типа двигателя (рис. 6): прямоугольную - в основном в малооборотных двигателях; шестиили восьмигранную овальную (эллиптическую); круглую; фигурную (у составных валов). Наиболее простой, с точки зрения изготовления, является прямоугольная форма, а наиболее рациональной (в особенности для многооборотных двигателей) в отношении прочности, равномерного распределения напряжений и веса —
овальная.
Для уменьшения масс неуравновешенных частей колена у щек делают срезы (скосы, например на рис. 6, а) в местах, где материал вала не участвует в передаче усилий от коренной к щатунной шейке. Переход на меньшие расстояния между цилиндрами lц вызывает необходимость уменьшения толщины щек (чтобы не увеличивать удельные давления на шейку). Поэтому для сохранения необходимой прочности и жесткости увеличивают ширину щек, перейдя от прямоугольных щек к овальным и круглым.
Круглые щеки, помимо простоты изготовления и относительного уменьшения толщины, дают возможность использовать их.если это потребуется, в качестве опорных шеек коленчатого вала, сокращая таким образом общую длину двигателя (см. рис. 4).
В местах сопряжения с шейками на щеках колена, служащего упором для подшипника, делают иногда круговые полированные выступы.
При наличии перекрытия шеек (см. рис. 7, а) при больших отношениях dк/D и малых S/D колено становится жестче и толщина щеки h может быть снижена примерно до нижних рекомендуемых пределов.
82

4 |
14,0 |
14.0 |
Рис. 6. Шейки коленчатых валов:
а — конструктивные формы; б — влияние формы отвестий в шейках и размеров щек на пределы усталости при кручении кривошипа (τ-1 кГ/см2).
Переходные галтели между щеками и шейками колена должны выполняться с возможно большими радиусами закруглений r, так как коэффициент концентрации напряжений непосредственно зависит от
отношения (d— диаметр шейки).
У выполненных |
судовых дизелей радиусы закруглений лежат в |
следующих пределах: |
|
малооборотные |
r = (0,07÷0,055) d |
многооборотные |
r = (0,07÷0,08) d |
Для более плавного перехода применяют галтели, описанные двумя (и более) радиусами, причем больший радиус должен примыкать к щеке. Иногда применяют эллиптические галтели (переход с постепенным уменьшением r
(рис. 7, б).
83
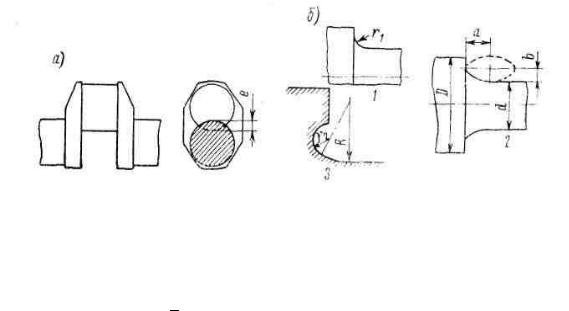
Рис. 7. Формы колен:
а - с перекрытием шеек; б - переходные галтели (1 - круговая, 2 - эллиптическая, 3 - с поднутрением).
При отношениях менее 0,1 значение коэффициента концентрации
напряжений достигает двух и более; при увеличенной длине переходного участка и плавном переходе концентрация напряжений может быть значительно уменьшена.
Шейки валов и их галтели должны быть тщательно обработаны и иметь полированную поверхность без каких-либо следов резца. Щеки целых валов должны быть чисто обработаны, а литые сплошные щеки составных колен — тщательно очищены.
Для облегчения веса коленчатого вала, как уже указывалось, изменяют форму колена, уменьшают расстояние lц, высверливают шейки, скосы на щеках и др.
В легких типах дизелей обычно высверливают как шатунные так и рамовые шейки; благодаря большому отношению шейки приобретают трубчатую форму (рис. 8, а). Ось сверления шатунной шейки иногда смещают к периферии колена (рис. 8, в), что снижает износ наиболее напряженной части шатунной шейки и повышает на 10-15% усталостную прочность колена. Форма внутреннего сверления шатунной шейки оказывает большое влияние на прочность колена. Наиболее рациональна бочкообразная форма полости, при которой уменьшается концентрация напряжений в месте перехода «бочки» в цилиндрическое сверление (рис. 8, б). Наиболее целесообразная конструктивная форма колена в отношении равномерного распределения напряжений и уменьшения концентрации напряжений может быть получена в литых чугунных коленчатых валах (рис. 9); помимо бочкообразной формы полости, в последних достигается оптимальная форма щек и без затруднений могут быть выполнены внутренние местные приливы для смазочных отверстий. Несмотря на более сложную форму чугунного литого коленчатого вала, он обходится значительно дешевле кованого стального.
Смазка шеек коленчатого вала - циркуляционная, под давлением. Масло подводится через штуцер к кольцевой канавке коренного подшипника, откуда оно попадает через сверление в шейке во внутреннюю ее полость.
84
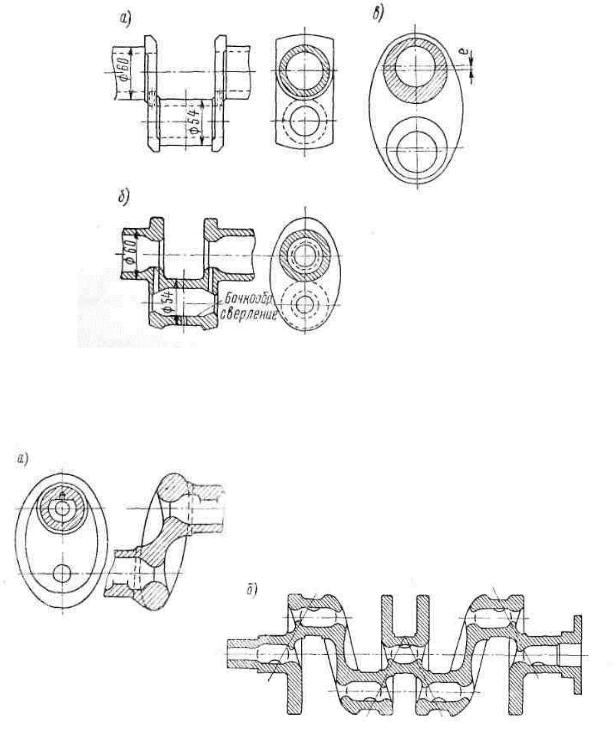
Рис. 8. Формы отверстий у шеек колен:
а — трубчатая; б—бочкообразная; в — с эксцентричным сверлением.
Рис. 9. Чугунные литые коленчатые валы:
а—щека; б — 4-коленчатый вал.
В шатунный подшипник масло канализируется посредством
(рис. 10, а) осевых и радиальных сверлений (1); диагональных сверлений (2); латунных трубок, развальцованных по концам (3). В первых двухслучаях отверстия в шейках должны быть закрыты по концам заглушками, представляющими собой стальные или силуминовые фланцы, стянутые одним болтом (4), или глухие штампованные крышки с кольцевым затвором (5).
Выходы радиальных сверлений на рабочую поверхность шейки для уменьшения концентрации напряжений должны быть снабжены закруглениями (см. рис. 10, б), а само сверление полировано. Так как эпюра касательных напряжений от крутящего момента по сечению шатунной шейки
85
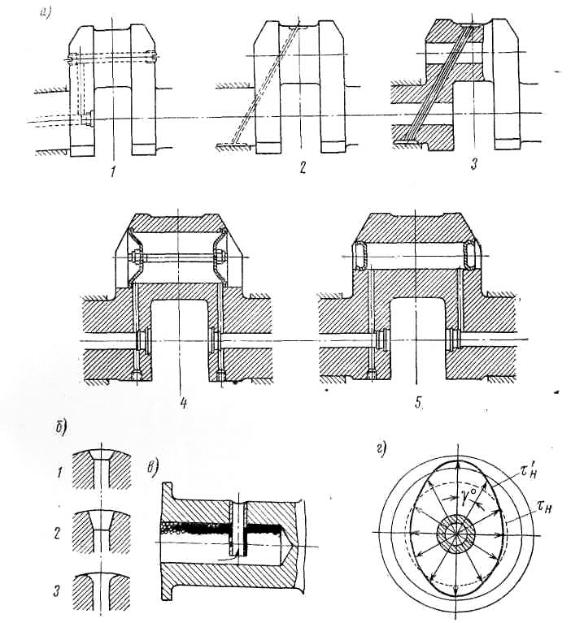
имеет овальную форму с большей осью в плоскости колена (рис. 10, г), то смазочное отверстие целесообразно располагать в плоскости минимальных напряжений, т. е. под углом 90 или 270° к плоскости колена, что повышает предел усталости вала.
У многооборотных двигателей для предотвращения попадания загрязненного масла на поверхность шейки применяют так называемые сепараторы (рис. 10, е), т. е. медные трубки, завальцованные в смазочное отверстие.
Рис. 10. Смазка шеек коленчатого вала:
а — схемы конструктивного оформления (1—5); б — смазочные отверстия (/, 2, 3 — выходы на поверхность шейки); в — сепаратор; г — эпюра
касательных напряжений.
86
На рис. 11 приведена система смазки колена дизеля 84VT2BF-180 dk = 680 мм и lц = 1540 мм; давление масла 1,8 атм; температура - на входе 40-50° С и на выходе 50-60° С; направление движения масла (см. →),
Противовесы на коленчатых валах применяются с целью уравновешивания неуравновешенных сил и моментов сил инерции деталей «движения», уменьшения удельных давлений на коренные подшипники за счет уравновешивания действующих центробежных сил от неуравновешенных частей колена; уравновешивания «внутренних моментов», нагружающих остов двигателя. Вследствие отсутствия места для размещения больших противовесов последние могут лишь частично (на 70—80%) уравновешивать центробежные силы колен. Недостатком применения противовесов является повышение момента инерции приведенных масс колена, что снижает частоту собственных колебаний системы вала.
Конструкции противовесов весьма разнообразны (рис. 12). В
многооборотных двигателях противовесы иногда отковывают вместе со щеками или приваривают к щекам. В остальных типах двигателей противовесы крепят к щекам с помощью болтов, причем для разгрузки последних применяют шпонки, работающие на срез, зубчатые соединения и другие устройства; для уменьшения массы противовеса его центр тяжести стремятся располагать возможно дальше от оси коленчатого вала.
Выходные концы коленчатого вала используют для размещения различных вспомогательных устройств. На конце вала со стороны отбора мощности обычно устанавливают маховик, валоповоротное устройство, привод механизма газораспределения (вблизи узла крутильных колебаний), приводы газотурбонагнетателей и др. На свободном конце вала устанавливают шестерни привода масляного и водяного насосов, дополнительные колена для привода продувочного насоса или пускового компрессора, демпферы крутильных колебаний и др. У рыболовных судов для привода в действие промысловых механизмов производится частичный отбор мощности со свободного конца вала.
Маховик устанавливают либо на утолщенной наружной части вала, либо на фланцевом соединении коленчатого вала с гребным.
Маховая масса маховика определяется заданной степенью неравномерности вращения (для главных двигателей δ =1/30÷1/40), а наибольший диаметр маховика ограничивается опорными судовыми продольными балками под фундаментную раму дизеля. Обычно для главных судовых двигателей маховые массы самого двигателя обеспечивают требуемую δ, поэтому маховик не требуется, а вместо него устанавливают зубчатый диск валопо-воротного устройства.
Выходы коленчатого вала из картера должны быть тщательно уплотнены во избежание утечки масла; для этой цели применяют особые маслосбрасывающие кольца в комбинации с лабиринтным или сальниковым уплотнением, маслосгонную резьбу (при малых диаметрах вала) и другие уплотняющие устройства.
87
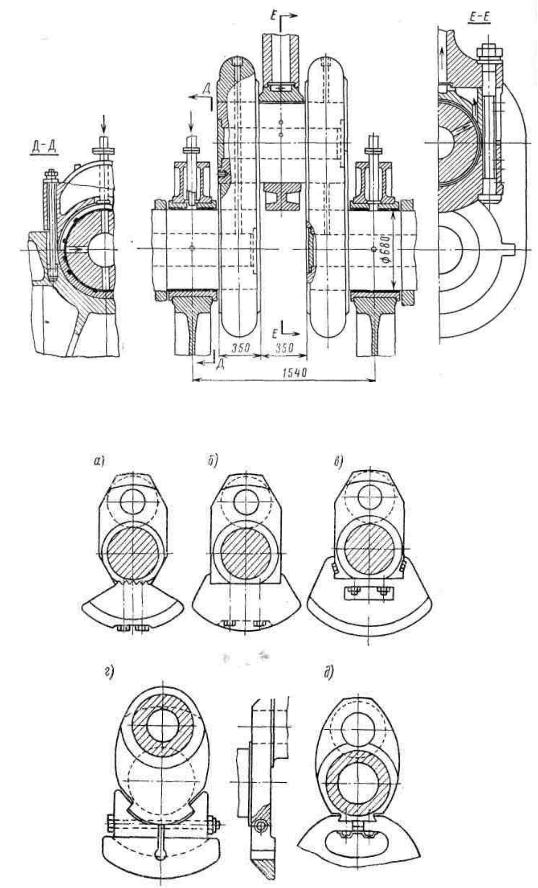
Рис. 11. Схема смазки колена дизеля типа 84VT2BF-180 с dk = 680 мм.
Рис. 12. Конструкции противовесов и их крепления (а-д).
88
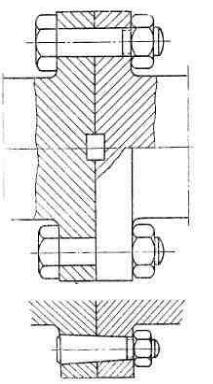
Для свободного теплового расширения вала относительно фундаментной рамы или картера должна быть предусмотрена возможность его осевого перемещения. В случае жесткого соединения коленчатого и гребного валов упорный судовой подшипник промежуточного вала служит одновременно и упорным подшипником для двигателя. Часто судовой упорный подшипник встраивают непосредственно в фундаментную раму двигателя, что избавляет от необходимости делать особые подкрепления на линии промежуточного вала. Торцовый зазор в упорном подшипнике составляет около 0,20÷0,05 мм в зависимости от размеров вала и конструкции подшипника.
Фиксация вала в случае соединения коленчатого вала с промежуточным валом при помощи эластичной муфты производится в одном из коренных подшипников (чаще всего кормовом), который в этом случае превращается в опорно-упорный подшипник. Удлинение вала составляет около 0,5÷0,6 мм на каждый 1 м длины и 50° С. Обычно у всех подшипников устанавливают в направлении расширения вала одинаковые зазоры, исходя из максимального зазора δ, требуемого для подшипника, наиболее удаленного от упорного.
Коленчатые валы судовых двигателей с кормовой стороны заканчиваются соединительными фланцами (рис. 13), откованными заодно с валом или насаженным на вал путем горячей посадки. Фланцы снабжаются центрирующими заточками, в которые при сборке валов вставляются шайбы. После того как линия валов проверена и фланцы жестко соединены между собой цилиндрическими болтами под развертку, центрирующие шайбы должны быть удалены, что дает возможность разбирать отдельные части валопровода без осевой передвижки вала.
Рис 13. Соединительный фланец коленчатого вала.
Конструктивное оформление коленчатых валов должно быть связано правильным выбором материала вала и способом
его изготовления. Принимая во внимание, что вал является наиболее сложной, напряженной и ответственной деталью двигателя, работающей на усталость, необходимо выбирать материалы с высокими прочностными показателями.
Коленчатые валы изготовляют тремя способами - ковкой,
штамповкой и отливкой. Валы крупных двигателей изготовляют путем свободной ковки и последующей вырезки отдельных колен при механической обработке. Стальное литье применяют для щек крупных составных валов, а
89
также для небольших цельнолитых валов. За последнее время получили широкое распространение чугунные литые валы для дизелей как малой, так и средней мощности.
Из углеродистой качественной стали (ГОСТ 1050—60) изготовляют коленчатые валы мало- и среднеоборотных дизелей; из легированных сталей - валы многооборотных и форсированных дизелей. Широкое распространение валов из углеродистых сталей объясняется их дешевизной, простотой термообработки и высокими пластическими свойствами. Чаще всего применяют для валов следующие марки качественной углеродистой стали -
35, 40, 45, 50, 35Г, 45Г, 50Г и др.
Высокопрочная легированная сталь для деталей «движения» может быть термообработана на сталь с мартенситовой структурой, получаемой после закалки и низкого отпуска, или на сталь с сорбитной структурой, получаемой после закалки и высокого, отпуска. Применение для коленчатых валов сталей мартенситного класса значительно облегчает их термическую обработку.
Сталь 18Х2Н4ВА дорога, трудно обрабатывается, не технологична; ее рекомендуют заменять сталями 40ХНВА или сталями 15ХНГ2ВА и 15Х2Г2СВА и др. При циклических нагрузках сталь 40ХНВА практически равноценна низкоотпущенной стали 18Х2Н4ВА; однако τ-1 улучшенной стали 35ХНВ на 25—35% выше τ-1 стали 18Х2Н4ВА после закалки и низкого отпуска. Хромомарганцововольфрамовые стали мартенситного класса дополнительно легированы: 15ХНГ2ВА никелем, а 15Х2Г2СВА кремнием. После закалки и низкого отпуска эти стали имеют те же механические свойства что и 18Х2Н4ВА, т. е. являются полноценными заменителями этой стали.
Вследствие большого ассортимента сталей различного назначения у коленчатых валов при их изготовлении из различных сортов стали могут быть получены одинаковые механические свойства. Поэтому в дизелестроении иногда задают для коленчатого вала не марку материала, а нужную категорию прочности, т. е. характеристику совокупности механических свойств материала, определяемых по пределу текучести. По заданной категории прочности металлургический завод, в зависимости от размеров вала и сечений поковки, рекомендует соответствующую марку стали.
Для получения категорий прочности поковок КТ-35 и КТ-40 в валах средней величины можно рекомендовать стали 40, 45 и 50, а для остальных более высокой прочности могут быть рекомендованы легированные стали, например, 40ХН, 35ХН (ОХМ), ЗЗХНЗМА и др.
Последнее время коленчатые валы все чаще изготовляются из чугунных отливок со сфероидальным (шаровидным) графитом. Получение отливок из чугуна с шаровидным графитом обеспечивается обработкой расплавленного чугуна присадками магния или другими специальными присадками.
В соответствии с ГОСТ 7293—54 существует два класса чугунов с шаровидным графитом: перлитный класс и ферритный класс.
90