
Метод_практ_СДВЗ
.pdf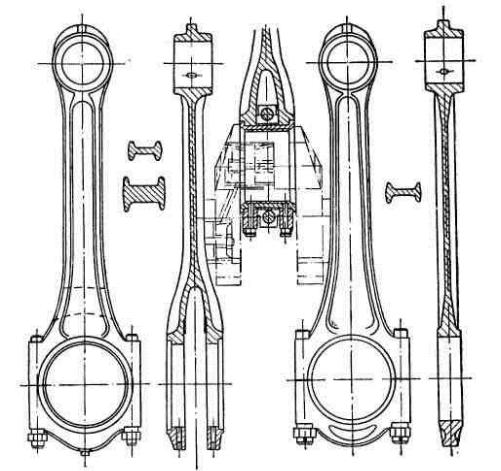
У головки с прицепным шатуном дизеля типа М601 головка имеет косой разъем относительно оси главного шатуна; крышка крепится коническими штифтами. Прицепной шатун имеет неразъемную нижнюю головку с бронзовой втулкой; соединение с главным шатуном осуществляется с помощью пальца, установленного в проушинах головки.
Рис. 11. Шатун V-образного дизеля с центральным расположением нижних головок.
Уцентральных шатунов (рис. 11) нижняя головка вильчатая; стальной вкладыш заливают антифрикционным сплавом по всей внутренней поверхности и по среднему поясу наружной поверхности (последняя охватывается нижней разъемной головкой внутреннего шатуна). Наконец, у
дизелей со смещенными осями цилиндров кривошипные шейки соседних цилиндров одинаковые и располагаются на одной и той же шейке коленчатого вала (рис. 12).
Основные недостатки указанных констукций следующие.
Уцентральных шатунов — тяжелые условия работы подшипника внутреннего шатуна, имеющего повышенное (вдвое) удельное давление, а также затрудненный тепло-отвод; недостаточная жесткость вилки внешнего шатуна. У смещенных шатунов — удлиненные шатунные шейки вала, усложненная конструкция и удлиненный двигатель в целом.
71
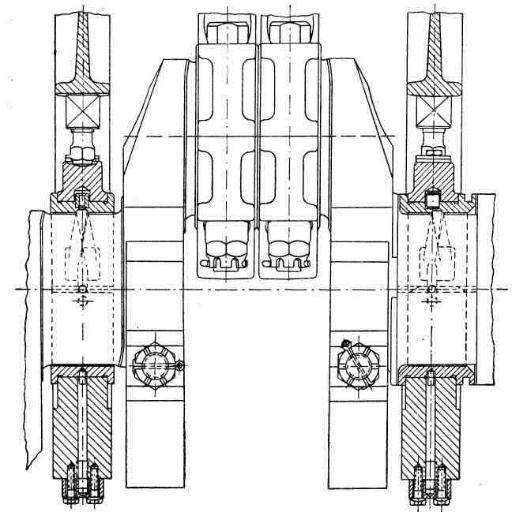
Рис. 12. Расположение нижних головок шатунов V-образных дизелей со смещенными осями цилиндров.
У прицепных шатунов — дополнительная нагрузка на главный шатун, различные усилия, действующие в главном и прицепном шатунах и, наконец, повышенное удельное давление на палец прицепного шатуна.
На практике наибольшее распространение получили конструкции с прицепным и смещенным шатунами.
Шатунный болт – одна из наиболее ответственных деталей
«движения», особенно у 4-тактных двигателей, у которых имеется знакопеременная нагрузка в подшипнике кривошипной головки. В 2-тактных двигателях (простого действия) знакопеременная нагрузка в болтах отсутствует, так как газовые силы обычно превосходят силы инерции деталей «движения».
Надежность работы шатунных болтов зависит в основном от их конструкции, качества изготовления, правильного монтажа и, наконец, качества материала.
Возникающие в эксплуатации обрывы болтов во время работы вызывают значительные разрушения деталей «движения», а иногда и остова двигателя.
72
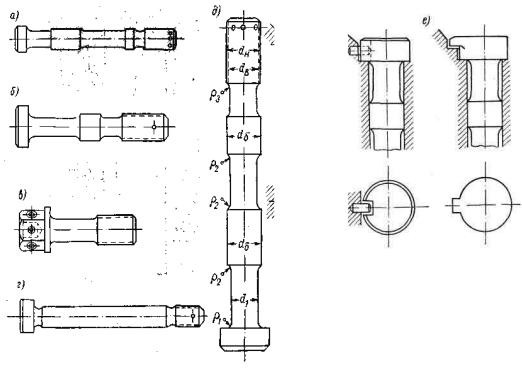
Обычное количество болтов — два; иногда с целью уменьшения габаритов кривошипной головки (например, для возможности выема поршня с шатуном через цилиндр) и по конструктивным соображениям вместо двух устанавливают четыре болта. Недостатком последней конструкции (по сравнению с конструкцией с двумя болтами) являются менее благоприятные условия для центрирования нижней половинки головки относительно верхней, а также для равномерного затяга всех четырех болтов.
Конструктивные формы шатунных болтов весьма разнообразны в зависимости от типа двигателя и его назначения (рис. 13). При конструировании болтов следует обращать особое внимание на необходимость повышения усталостной прочности болтов. Для этой цели рекомендуется площадь поперечного сечения болта делать равной 80—85% от площади сечения внутреннего диаметра резьбы; в связи с необходимостью повышения податливости болта надо по возможности увеличивать его длину. Переходы от головки и поясков к утолщенной части стержня и к резьбе должны быть плавные и иметь достаточные радиусы закруглений. Обычно место перехода от резьбы к стержню заменяют проточкой длиной не менее 0,5dн. Наибольшая концентрация напряжений возникает в резьбовом соединении; поэтому резьба должна быть мелкая, метрическая, с возможно большим радиусом закруглений у впадин, чисто обработанная, без каких-либо заусениц, забоин и др. Материал болтов должен иметь высокую усталостную прочность. Во избежание появления дополнительных изгибных напряжений у стержня вследствие перекашивания опорных поверхностей гайки и головки болта кривошипные головки шатуна должны быть жесткие.
Рис. 13. Шатунные болты:
а — д — конструкции болтов; е — фиксация болтов
73
Шатунные болты должны устанавливаться в калиброванные отверстия головки, расположенные возможно ближе к кривошипной шейке вала. Затягиваются болты корончатыми гайками, зафиксированными шплинтом. Правильная затяжка болта при монтаже имеет первостепенное значение; величина предварительной затяжки болтов устанавливается заводом и должна строго соблюдаться.
Перетяжка болтов и неравномерная их затяжка может привести к обрыву болтов. Допустимая величина удлинения болтов при затяге должна контролироваться специальной измерительной скобой. У крупных двигателей гайки болтов снабжаются нониусными делениями для регулирования величины затяга (см. например рис.6). От проворачивания болты предохраняют фиксирующим штифтом или выступом на головке (см. рис. 13,
е).
Материалы для изготовления деталей КШМ.
Материалы для изготовления поршней должны удовлетворять ряду требований, среди которых основные приведены ниже:
-хорошая теплопроводность металла λ, обеспечивающая необходимый отвод тепла от днища к поршневым кольцам (неохлаждаемые днища) или от днища в охлаждающую среду; в этом отношении Al-сплавы имеют значительные преимущества по сравнению с чугуном;
-малые значения коэффициента линейного расширения α, позволяющие при работе двигателя, и особенно при пуске, уменьшить рабочие зазоры между поршнем и втулкой. Среди А1-сплавов наибольшее удлинение при нагреве имеет старый сплав Y (A1-, Cu-группы), обладающий высокой прочностью и хорошей теплопроводностью; сплавы Al-Si-группы имеют меньший коэффициент удлинения и большую износостойкость, однако обладают меньшей теплопроводностью;
-высокая механическая прочность и жаростойкость материала головок поршней при повышенных температурах;
-хорошие антифрикционные свойства и износостойкость у материала направляющей части поршня; в этом отношении поршни из чугуна или А1-сплава примерно равноценны, однако у последних больше износ канавок под поршневые кольца;
-малый удельный вес у материалов для возможности снижения конструктивного веса поршня (многооборотные дизели); в этом отношении поршни из чугуна или стали значительно уступают таковым из Al-сплавов (в
2,5—3 раза).
В качестве материалов для поршней, удовлетворяющих поставленным выше требованиям, применяют чугун, сталь и алюминиевые сплавы.
Чугунные поршни отливают из марок СЧ24-44, СЧ28-48, СЧ32-52 и ВЧ45-0, характеризующихся высокой прочностью и износостойкостью, малым коэффициентом линейного расширения и дешевизной.
Пределы прочности серых чугунов с пластинчатым графитом мало изменяются до 400—450° С; выше этой температуры прочность значительно
74
снижается. При нагреве головки поршня свыше 400° С, под воздействием высокой температуры и окислительной среды, возникает так называемый «рост» чугуна, нередко сопровождающийся растрескиванием поверхности днища.
Замедление роста чугуна достигается модифицированием, а также легированием чугуна хромом и молибденом, что позволяет в некоторых случаях доводить температуру днища до 500—600° С. Наименьшей чувствительностью к росту чугуна обладают высоколегированные чугуны аустенитного класса.
Значительный интерес для изготовления головок поршней форсированных дизелей представляет применение модифицированных чугунов со сфероидальным графитом, у которых пределы прочности доходят до 50—60 кГ/мм2, а рост чугуна значительно меньше, чем у обычного серого чугуна.
Для направляющей поршня (тронка) рекомендуемые для днища структуры материалов мало подходят, так как эти материалы характеризуются относительно низкими антифрикционными свойствами. Поэтому целесообразно, где это возможно, отливать направляющую отдельно от головки или обеспечить изготовление целого поршня с различными свойствами для днища и направляющей.
Наряду с чугуном для изготовления поршней широкое распространение получили алюминиевые сплавы особенно для многооборотных дизелей), благодаря ряду их преимуществ по сравнению с чугунными, а именно:
-меньшему удельному весу (γ = 2,7÷2,8 г/см3), позволяющему снизить массу поршня и силы инерции, а следовательно, форсировать число оборотов двигателя;
-более высокой теплопроводности (λ=0,23÷0,40 кал/см· сек °С), дающей возможность у неохлаждаемых поршней снизить рабочую температуру днища на 100—150° С (по сравнению с чугунными поршнями);
-возможности замены охлаждаемых чугунных поршней неохлаждаемыми из Аl-сплавов;
-возможности изготовления заготовок поршней более эффективными способами (кокильное литье, прессование, ковка) с минимальными припусками.
К недостаткам А1-сплавов следует отнести:
-высокие коэффициенты линейного расширения, вынуждающие увеличивать зазоры между поршнем и втулкой;
-меньшие сопротивления износу по сравнению с чугунными;
-более низкие механические свойства (чем у чугуна), ухудшающиеся при нагреве;
-относительно высокая стоимость.
В двигателестроении применяют для поршней как литейные, так и деформируемые алюминиевые сплавы. Среди литейных жаропрочных сплавов чаще других применяют марки АЛ1, АЛ 10В, АЛЮ, В-300, В-14А
75
Химический состав литейных жаропрочных сплавов весьма разнообразен; основным содержанием сплавов является медь (3,3—8%) и магний (0,2—1,75%); кроме того, сплав АЛ1 содержит 1,75—2,2% никеля, сплав АЛ10В — 4,5—6,5% кремния и, наконец, сплавы АЛЮ, В-300 и В-14А
—марганец (от 0,15% до 1,0%).
К преимуществам, литейных жаропрочных сплавов относится и хорошая жидкотекучесть (3—4 балла), а также возможность изготовления сложных и вместе с тем плотных отливок. При отливке поршней в кокиль могут быть достигнуты более высокие механические качества и повышенная чистота поверхности. Литейные сплавы в зависимости от марки сплава могут применяться при рабочей температуре поршней от 175 до 350° С. Для повышения прочности, твердости и износостойкости литые поршни подвергаются термообработке (закалке и старению или только старению).
Среди деформируемых жаропрочных сплавов специального назначения наибольшее распространение для изготовления поршней нашли сплавы марок АК2, АК4, АК4-1, Д20, Д21 и др. Заготовки из этих сплавов в отличие от литейных могут быть получены прокаткой, прессованием и штампованием.
В термически обработанном виде деформируемые сплавы имеют более высокие механические свойства, чем литейные.
Для сохранения высокой прочности при нагреве А1-сплавы имеют сложный фазовый состав. Как видно из табл. 3, сплав АК2 имеет меньшую жаропрочность, чем сплавы АК4 и АК4-1. Преимущества сплава АК4-1 (по сравнению с АК2 и АК4) сказываются только при температурах выше 150° С. До 300° С свойства сплава Д21 выше, чем у Д20 и АК4-1, а свыше 300° С — наилучшие свойства имеет сплав Д20 [9].
С увеличением температуры механические качества сплавов снижаются.
Широко применяются (особенно для форсированных дизелей) алюми-
ниевые сплавы с высоким содержанием кремния:
эвтектические с содержанием Si до 12—14% и сверхэвтектические с содержанием Si до 20—24%.
Примерное содержание остальных компонентов у обоих сплавов составляет: Си— 0,8-1,5%; Ni — 0,8-1,3%; Mg —0,8-1,3%; Fe — 0,7%; Mn— 0,2%; Zn — 0,2%; остальное — Al.
Важными преимуществами этих сплавов, по сравнению с АК4 и АК2,
являются повышенная жаростойкость и низкие коэффициенты линейного расширения α, благодаря чему имеется возможность уменьшать зазоры между головкой поршня и втулкой, а также увеличивать износостойкость поршневых канавок при повышенных температурах. Для сокращения периода приработки направляющую часть поршня лудят легкоплавкими металлами, например, оловом; толщина слоя покрытия для поршней с D < 150 мм составляет 5— 10 мк.
Среди еще сравнительно редко применяемых материалов для поршней многооборотных двигателей следует отметить возможность изготовления их
76
(или только их головок) из жаропрочных сталей, обеспечивающих получение прочной и легкой конструкции.
Защитные покрытия для днища поршня. Для предупреждения появления тепловых трещин на днищах поршней дизелей, имеющих высокую форсировку рабочего процесса, последнее время применяют различные
теплоизоляционные покрытия.
Анодирование, т.е. превращение алюминиевой поверхности днища поршня в окись алюминия, дает сравнительно небольшое повышение сопротивления возникновению тепловых трещин вследствие слишком тонкого защитного слоя (0,01—0,02 мм).
Лучшие результаты дает спекание слоя А1-порошка толщиной около 10 мм с днищем поршня при высоком давлении и температуре (несколько ниже температуры плавления); применение этого способа, однако, значительно повышает стоимость поршня.
Наиболее перспективным является применение керамического жаростойкого покрытия с низкой теплопроводностью толщиной —0,1—0,2 мм, наносимого на днище поршня плазменным способом специальным устройством, в камеру которого подается смесь кислорода, ацетилена и порошкообразного жаропрочного материала.
Покрытие обладает большой твердостью и плотностью, надежно защищает днище от появления трещин и снижает температуру поршня (на 20—80° С). Испытания Дженерал Моторс показали, кроме того, что после длительного времени покрытие не нарушается, нагарообразование и износы поршня снижаются, улучшаются рабочий процесс сгорания и пусковые качества дизеля и, наконец, облегчается возможность работы на топливах с более низкими цетановыми числами.
К материалу поршневых колец, работающих в весьма тяжелых условиях (особенно верхние два кольца), предъявляются следующие
основные требования:
-высокая износостойкость в условиях граничного трения;
-высокая механическая прочность при повышенных рабочих температурах;
-высокие антифрикционные свойства пары поршневое кольцовтулка;
-быстрая прирабатываемость к поверхности цилиндровой
втулки.
77
Практичне заняття № 4. Колінчасті вали. Призначення. Особливості конструкції. Матеріали, які застосовуються при
виготовленні. Особливості конструкціїкшм крейцкопфних двигунів. Штоки, крейцкопфи. Призначення. Особливості конструкції
Коленчатый вал состоит из коренных и шатунньых шеек, щек и соединительных фланцев (рис. 1, а, б, 2). В зависимости от количества колен, размеров шеек, длины и веса валы изготовляют целыми (рис. 3) или составными из двух или более частей, соединяемых жесткими фланцами. Колена (кривошипы), в свою очередь, изготовляют целыми (рис. З, а), полусоставными (рис. З, б) и составными (рис. З, в). Последние две конструкции применяли до последнего времени в основном у малооборотных судових дизелей с радиусом кривошипа R свыше 450 мм; однако в настоящее время для удешевления валов применяют составные колена и при меньших R.
Вполусоставных коленах шатунные шейки отковывают заодно со щеками, а в последние запрессовывают отдельно изготовленные коренные шейки; в составных коленах как коренные, так и шатунные шейки запрессовывают в щеки (кованые или стального литья). Запрессовку шеек осуществляют при небольшом нагреве (до 200—250° С) и при натяге в 1/800— 1/1000, обеспечивающем плотность соединения без постановки каких-либо фиксирующих шпонок или штифтов (рис. 4).
Всудових дизелях между двумя смежными коренными подшипниками, как правило, помещают только одно колено, чтобы обеспечить наибольшую его жесткость и прочность; исключением являются судовые дизели старой конструкции типа Доксфорд с ПДП, валы которых имеют по три колена на один цилиндр между смежньши опорами. В новой конструкции типа J, для уменьшения расстояния между цилиндрами наружные щеки двух бокових колен служат в качестве опорних коренных подшипников вала (рис. 5). В относительно маломощных и высокооборотных двигателях (например, автотракторного типа) помещают иногда 2, 3 и 4 колена между смежными опорами. В случае использования в многоцилиндровых двигателях роликових опорних подшипников целесообразно применять составные колена и устанавливать роликовые
обойми непосредственно на щеках колен, что дает возможность сократить расстояние между цилиндрами.
Взаимное расположение колен зависит в первую очередь от тактности двигателя и числа его цилиндров.
Выбор оптимального расположения колен преследует цель получить наибольшую равномерность крутящего момента; наиболее полное уравновешивание двигателя; равномерное нагружение вала (по его длине); при газотурбинном наддуве двигателя — возможность оптимального использования энергии выхлопных газов; наименьшие дополнительные напряжения от крутильных колебаний и др.
78
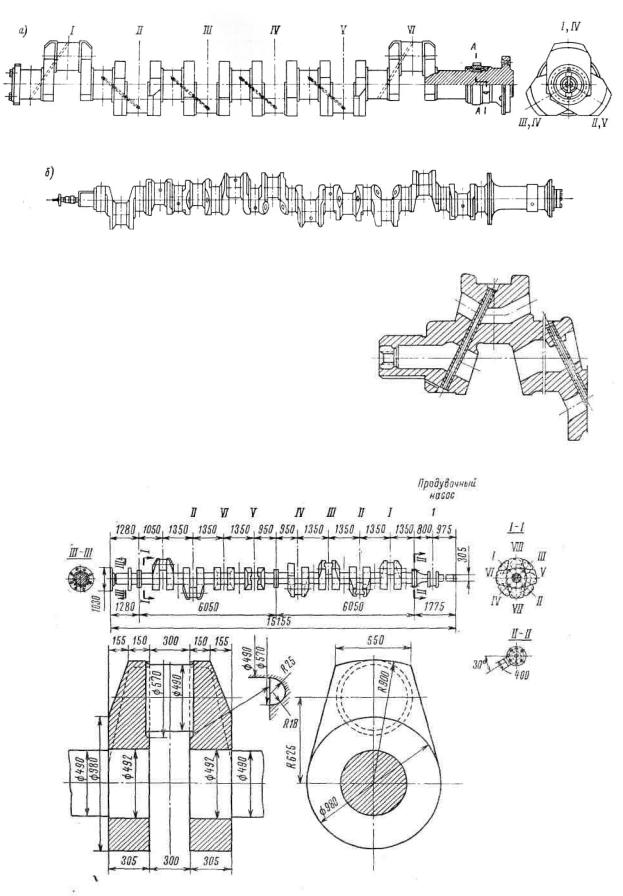
Рис. 1. Коленчатые валы:
а—стальной 4-тактного дизеля 6ч 36/45 мощностью 900 э. л. с. при 375 об/мин; б — чугунный 2-такт-ного дизеля 2Д100 мощностью 2000 э. л. с. при 850 об/мин.
Рис. 2. Коленчатый вал 2-тактного дизеля 8SD72 мощностью
5500 э. л. с. при 125 об/мин.
79

Рис. 3. Конструктивные схемы коленчатых валов:
а — цельные; б — полусоставные; в — составные.
Рис 4. Конструкции колен мощных дизелей:
а, б — Бурмейстер и Вайн; в — Зульцер; г — МАН.
80