
Метод_практ_СДВЗ
.pdf
В малооборотных двигателях одну или две канавки располагают в нижней части направляющей; у среднеоборотных — располагают одну или две канавки в нижней части направляющей и одну — непосредственно за последним уплотняющим кольцом. Наконец, у многооборотных дизелей, имеющих укороченную направляющую часть, располагают всего одну канавку над поршневым пальцем.
Для ускорения приработки чугунных направляющих поршня рекомендуется покрывать последнюю тонким слоем олова (6 = 0,01 мм). У мало- и среднеоборотных дизелей иногда в направляющую зачеканивают один или два бандажа (кольца) из свинцовистой или оловянистой бронзы.
5.В отъемных головках можно, как указывалось, выбирать оптимальные сорта материалов и для головки и для направляющей.
К такой конструкции относится, например, поршень четырехтактного тронкового дизеля с газотурбинным наддувом (рис. 12), у которого головка отлита из жаростойкой стали, а направляющая — из чугуна или алюминиевого сплава.
6.Поршневой палец в устарелых
конструкциях запрессовывали в гнезда и фиксировали один из концов болтом и, кроме того, шпонкой против проворачивания. При расширении от сильного нагрева запрессованный палец вызывает деформацию направляющей части поршня, что может вызвать заедание последнего.
Рис. 12. Поршень с направляющей |
Рис. 13. Поршень дизеля Д100 |
из Al-сплава и стальной головкой. |
с цилиндрической вставкой для |
|
крепления пальца. |
|
51 |
Всовременных конструкциях применяют в основном так называемые «плавающие» пальцы (см. гл. III), не фиксированные в опорных гнездах и имеющие возможность свободно проворачиваться вокруг оси пальца; продольное смещение пальца ограничивается либо заглушками, либо пружинными стопорными кольцами (см. рис. 11 и 15).
Рациональной конструкцией является крепление пальца в особом цилиндрическом проставив, установленном в поршне и прикрепленном к головке. В этом случае тронковая часть поршня не прорезается отверстиями для гнезд и при нагреве имеет равномерную деформацию. К такой конструкции относится, например, поршень дизеля Д100 (рис. 13), у которого палец имеет опорную поверхность во вставке, крепящейся к головке длинными шпильками.
Отвод тепла и его распределение у головок поршней
1.За время процесса сгорания - расширения к днищу поршня подводится тепло, интенсивность подвода которого зависит от температуры, плотности и степени завихрения заряда.
Наименее благоприятные условия подвода тепла - в дизелях с непосредственным распыливанием топлива, при котором отдельные зоны днища подвергаются местным перегревам. Наибольших значений удельный тепловой поток достигает у многооборотных 2-тактных дизелей с повышенными степенями наддува.
Взадачу конструктора входит выбор таких степеней наддува и распределения тепла в головке, которые полностью предохраняли бы головку поршня от возможности превышения максимально-допустимых температур для выбранного материала головки.
2. Наиболее простой способ отвода тепла (через поршневые кольца), применяемый у неохлаждаемых поршней, может быть использован только в тронковых дизелях с относительно невысокой цилиндровой мощностью Л^ц, например, при чугунных поршнях 4-тактных дизелей Л^ц sg 120 э. л. с, а у 2-тактных Neu, й£ 60 э. л. с. соответственно при поршнях из А1-сплавов в 4-тактных Nea ^ 250 э. л. с, а в 2-тактных Ыщ «s 125 э. л. с, где принято условно, что тепловая нагрузка поршня у 2-тактных дизелей вдвое выше, чем у 4-тактных (при одинаковых индикаторных давлениях).
Отвод тепла у неохлаждаемых поршней осуществляется от головки к охлаждающей цилиндровую втулку воде — через поршневые кольца (60—75%) и тронковую часть поршня (25—40%).
Для получения равномерного распределения теплового потока и максимального снижения температуры днища целесообразно увеличивать толщину днища примерно до 6=(0,12-^0,14)0, а также толщину переходных сечений от центра днища к боковым стенкам головки, например, за счет выбора большего радиуса закругления (см. рис. 5). Этот способ отвода тепла с успехом используется у чугунных и у алюминиевых поршней.
Наибольшие температуры у поверхности днищ поршней из А1-сплавов допускаются до 300—350° С, а для чугуна до 450—500° С; температура стенки под канавкой первого поршневого кольца во избежание его пригорания не
52
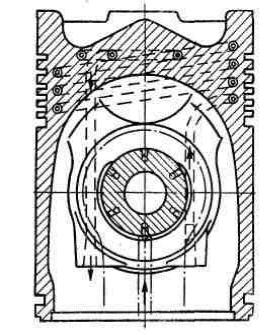
должна превышать 200—220° С.
Основной недостаток указанного выше способа отвода тепла - увеличение радиального перепада температур и возрастание веса поршня.
3. Наиболее эффективное средство снижения температуры головки поршня, как известно, - введение охлаждения головок, применяемое не только при больших D цилиндров, но и при относительно малых D (менее 200 мм), в связи со значительной форсировкой дизеля как по наддуву, так и по числу оборотов.
Доля тепла, отводимого в охлаждающую среду от головки поршня (в % от тепла, внесенного с топливом) составляет ориентировочно: при масляном охлаждении от 4 до 10% (65— 160 ккал1э. л. с. ч.) * и при водяном от 10 до 15% в зависимости от системы охлаждения (160—240 ккал/э. л. с. ч.).
Утронковых дизелей наибольшее распространение получило струйное охлаждение головки поршня через сверление в шатуне; реже (у дизелей с D
>300 мм) применяют телескопическую или шарнирную системы охлаждения, дающие возможность подводить к головке большие количества масла.
Укрейцкопфных дизелей применяют телескопическую систему охлаждения, вынесенную за пределы картера или размещенную внутри картера. Охлаждающую среду подводят к головке либо через шток, либо непосредственно к головке. Для предотвращения гидравлических ударов в систему телескопического охлаждения вводят воздушные колпаки.
Для снижения температуры поршней из Al-сплавов у форсированных
тронковых |
Дизелей |
(ре == 12 кГ/см2) |
Средней |
мощности |
применяют ряд |
зарекомендовавших себя конструктивных решений, как это показано ниже на типичных примерах.
Из рис. 14 поршня дизеля с D = 400 мм (ре = 14,5 кГ/см2) видно, что для охлаждения головки в наиболее нагретых зонах (у верхних поршневых колец) заливают в тело головки змеевик, через который циркулирует масло, поступающее по шатуну через поршневой палец; этот способ охлаждения дает возможность
снизить температуру головки у первого |
Рис. 14. Охлаждение маслом |
поршневого кольца на 40—60° С . |
головки поршня из Alсплава |
|
D = 400 посредством змеевика |
Аналогичную цель преследует поршень Al-Si-сплава многооборотного форсированного дизеля типа М. G. О. (рис. 15). На тело головки насаживается и приваривается к ней бандаж 3 с гнездами для поршневых колец; в образовавшуюся кольцевую полость 4 через канал 1 подается масло, которое и охлаждает зону расположения поршневых колец. Вытекающее масло через
53
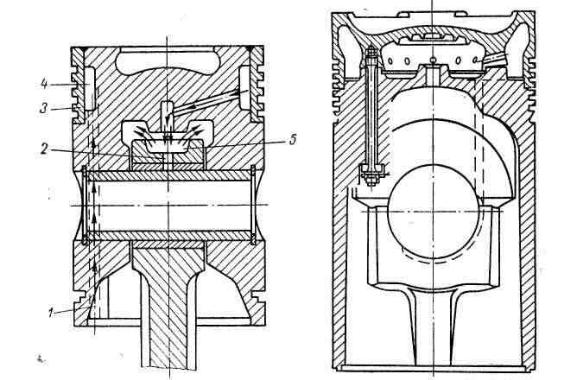
сверление 2 идет на смазку пальца; часть масла задерживается в выемке 5 и при движении поршня разбрызгивается и охлаждает днище поршня за счет «взбалтывания» масла. Верхнее поршневое кольцо обычно хромируют.
Рациональную конструкцию имеет поршень судового дизеля МАH типа VV 40/54 (рис. 16) с высоким наддувом (ре = 18 кГ/см2). Головка поршня откована из жаростойкой стали вместе с поясом для трех верхних колец; пояс может расширяться книзу, что уменьшает деформацию колец при их нагреве. Головка крепится к направляющей из А1-сплава четырьмя длинными болтами (для увеличения их податливости). Благодаря наличию стального днища имеется возможность уменьшить диаметральный зазор между головкой и втулкой, а также уменьшить толщину стенок днища. Охлаждение последнего осуществляется «взбалтыванием» масла. Температура в зоне верхних колец не превышает 140° С; гнезда для колец могут быть закалены, что значительно уменьшает их износ (особенно важно при работе дизеля на тяжелых сортах топлива).
Рис. 15. Конструкция А1-поршня |
Рис. 16. Конструкция поршня |
дизеля типа MGO. |
дизеля МАН типа VV40/54. |
Для многооборотных форсированных транспортных дизелей значительный интерес представляет конструкция поршня малого диаметра (D
— 185 мм) дизеля Майбах (рис. 17, а) с цилиндровой мощностью 250 э. л. с. при 1900 об/мин, ре = = 11,7 кГ/см2 и ст = 14,4 м/сек.
Поршень состоит из тонкостенной головки из жаропрочной стали с тремя гнездами для колец; направляющая поршня чугунная или из Al-сплава имеет два маслосъемных кольца.
54
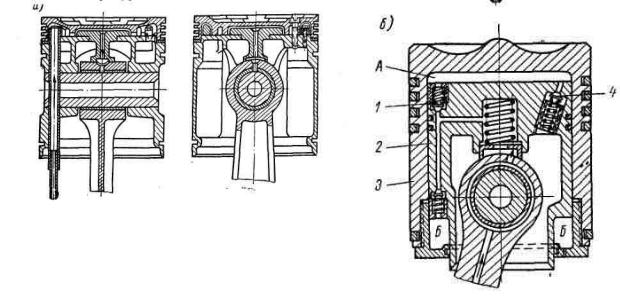
Рис. 17. Конструкции поршней форсированных дизелей:
а- типа Майбах с D = 185 мм; б - 4-тактного дизеля с
переменной степенью сжатия.
Охлаждающее масло подается по телескопическому устройству; давление масла регулируется в зависимости от числа оборотов для ускорения циркуляции масла между днищем и корпусом установлен вытеснитель. Температура днищ не превышает 400° С, а канавки верхнего кольца - 200° С.
Для 4-тактных дизелей с высоким наддувом разработана конструкция поршня (D = 226 мм), дающая возможность автоматически осуществлять переменную степень сжатия (е = 12÷8) в зависимости от нагрузки (рис. 17, б). Конструкция позволяет снижать рг при форсировке дизеля, улучшает экономичность на долевых режимах, а также пусковые качества.
Поршень состоит из наружного подвижного корпуса 3 и внутреннего 2, соединенного с пальцем и шатуном. Взаимное положение двух корпусов определяется количеством масла, заполняющего верхнюю А и нижнюю Б (кольцевую) полости.
Масло поступает в эти полости по шатуну и клапанам 1. При достижении наибольшего рz открывается клапан 4; часть масла при этом вытекает в картер и корпус перемещается вниз, a pz автоматически снижается. Чтобы стакан 3 находился в положении, при котором поддерживалась бы е, соответствующая выбранному (рг)тах, используется сила инерции стакана и масла в камере А, действующая в конце хода выпуска ив 1-ой части хода впуска. При ре до 22 кГ/см2, как показали испытания BICERA, удается ограничить рг в допустимых пределах.
Особенности конструирования и охлаждения поршней мощных
2-тактных дизелей с ГТН. В связи с развитием мощных судовых 2-тактных дизелей с газотурбинным наддувом, у которых диаметры цилиндра достигают D = 840 -Й050 мм, ре я» 8 -ч-Ю кГ/см2 и Neil — 2000^-4000 э. л. с, возникла трудная задача — снизить теплонапряженность двигателей, в первую очередь поршня. В связи с этим, ведущими заводами были произведены большие работы по переконструированию поршней и усовершенствованию системы
55
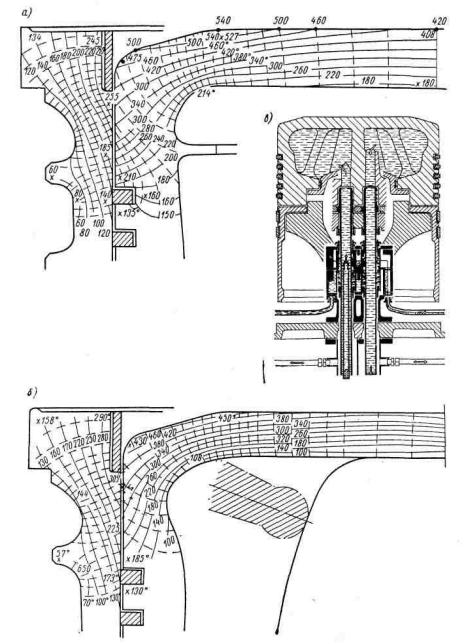
охлаждения с тем, чтобы обеспечить надежную работу поршневой группы в эксплуатации.
1. Сопоставление температурных полей головок поршней дизеля Зульцер типа RD76 при масляном или водяном их охлаждении показало, что при переходе на повышенные давления наддува (сверх ре = 8 ч-9 кГ/см2) возможности масляного охлаждения ограничены (рис. 18, а, б). Уже при ре 7 кГ/см2 наибольшая температура днища с огневой стороны достигает 500° С, а со стороны масляного охлаждения 200—220° С (предель ной для масла). У головки без ребер эта температура может быть снижена до 190—195° за счет интенсификации потока масла.
Рис. 18. Температурные поля днищ поршней и втулок дизеля типа RSAD 76 при охлаждении поршней:
а — маслом (ре= 7 кГ/см2); б — водой (ре= 10 кГ/смг); в — конструкция охлаждения головки водой.
56
Однако в эксплуатации при старении или загрязнении масла возможно появление нагара, что может привести к недопустимому повышению температуры днища у периферии (до 600° С и более). Поэтому для облегчения очистки днища от нагара в эксплуатации необходимо, чтобы внутренняя поверхность днища была гладкой, без каких-либо ребер, а турбулизацию потока масла следует осуществлять за счет специальных сопел на вытеснителе. Замеренный перепад температур в центре днища при полной нагрузке составляет 240° С, т. е. около 35° на 1 см толщины днища.
При введении водяного охлаждения поршней наступает радикальное улучшение условий охлаждения головки поршня (см. рис. 18, б). В этом случае днище поршня подкрепляется ребрами, что дает возможность утонить днище (примерно до 0,07D). При этой конструкции и повышенной степени наддува (ре = 10 кГ/см2 и А,н = 1,43) температуры с огневой и охлаждаемой стороны днища составляют соответственно: в центре днища 400 и 75° С (At = 325°, т. е. 60° на 1 см) и на периферии - 460 и 100° С. Для уменьшения возможности коррозии днище изготовляют из нержавеющих сортов стали, а охлаждающую пресную воду подвергают специальной обработке. Во избежание попадания воды в циркуляционную масляную систему разработана новая конструкция уплотнения телескопических труб (рис. 18, в), полностью исключающая возможность смешения масла с водой, так как возможные утечки воды из сальников, расположенных между поршнем и диафрагмой, отводятся в сливной бак.
2. Для снижения теплонапряженности головки мощных дизелей типа
780S и других фирма Фиат разработала модернизированную конструкцию поршня (рис. 19); слева на рис. 19 показана действующая конструкция поршня, а справа — модернизированная, отличающаяся в основном утонением днища и креплением последнего с проставком к фланцу штока длинными податливыми болтами (/б = 0.85D). Тонкостенная литая головка с ребрами из молибденовой стали опирается на жесткий проставок.
Толщина днища должна обеспечить получение минимальных суммарных напряжений (механических и тепловых) в днище; возможно низкую температуру на периферии днища; равномерное распределение поля температур по всей поверхности днища. Каналы для интенсификации масляного охлаждения имеют в зоне поршневых колец винтообразную форму, а под днищем — спиральную. Днище поршня покрывают (посредством металлизации) защитным слоем жаростойкого сплава.
Исследования теплового состояния головки при ре—7,6 кГ/см2 показывают (рис. 20, а), что средние температуры с огневой стороны не превышают 350° С, а с внутренней — 200° С (т. е. перепад А^ = 150°); под канавкой первого поршневого кольца они не превышают 150° С.
57
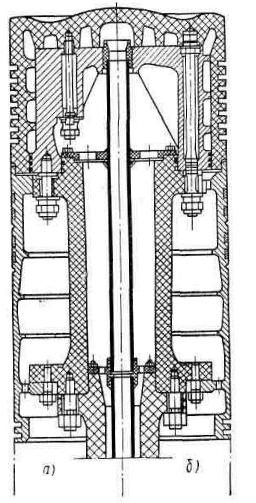
Повышение температуры головки при дальнейшей форсировке дизеля по наддуву показано на рис. 20, б; из последнего следует, например, что при ре = 10 кГ/см2 температуры в точках 1, 2 и 3 достигают соответственно 430, 250 и 175° С. Наконец, из рис. 20,в виден характер изменения температур на периферии огневой стороны днища (точка 1) при изменении нагрузки по винтовой характеристике и изменении
чисел оборотов от |
115 до 130 (—), |
а также при |
постоянной мощ- |
ности 2100 (-.-.-.- ) э. л. с. и изменении оборотов (в тех же пределах).
Рис. 19. Конструкции поршня 780S Фиат:
а —более ранняя; б — действующая
Поршневые кольца и их конструирование
Поршневые кольца подразделяются на уплотнительные и маслосъемные. Уплотнительные кольца служат для предотвращения прорыва газов из камеры сгорания в картер для отвода части тепла от головки в охлаждающую воду. Маслосъемные кольца защищают камеру сгорания от попадания в нее излишков масла с зеркала цилиндра.
Уплотнительные кольца работают в очень тяжелых условиях, в особенности первое кольцо. Кольца совершают возвратно-поступательное движение, сильно нагреваются от соприкосновения с горячими газами и нагретой стенкой цилиндра, а также от трения. В связи с высокой температурой первого кольца трудно обеспечить надлежащую смазку кольца, особенно при положении поршня в в. м. т.
Основными дефектами в работе колец в эксплуатации являются; пригорание колец, пропуски газов, потеря упругости и повышенные износы.
Уплотняющее действие колец достигается за счет прижатия колец к зеркалу цилиндра, а также лабиринтного их действия. Прижатие колец ко втулке происходит благодаря собственной упругости колец и давлению газов, проникающих через зазоры в заколечные полости канавок.
Лабиринтное действие колец возникает вследствие перетекания газов через систему над- и заколечных полостей. Из-за незначительного расхода
58
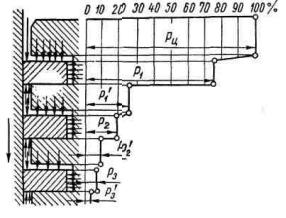
(около 0,5% от Vs) и скорости газа падение давления в системе полостей происходит по ступеням (в соответствии с количеством колец). Из схемы уплотнения колец (рис. 21) видно, что наибольшее давление р, примерно равное давлению в цилиндре, будет у первого кольца. По мере расширения газа и перетекания его в следующие заколечные полости давление падает до давления окружающей среды. Основными условиями для сохранения уплотняющей способности колец являются: правильное сопряжение колец по наружной их поверхности с зеркалом цилиндра; отсутствие перекоса колец вследствие тепловой деформации головки; отсутствие неравномерного износа
втулки (и |
колец) и др. |
|
|
Качество |
газоуплотнения |
|
|
мало зависит от количества колец. |
|
||
При нормальной приработке в много- |
|
||
оборотных |
двигателях газоуплотне- |
|
|
ние может быть обеспечено двумя |
|
||
кольцами (например, в карбюра- |
|
||
торных двигателях). Большее количе- |
|
||
ство колец (до трех у многооборотных |
|
||
дизелей и до шести у малооборотных) |
|
||
необходимы в основном для лучшего |
|
||
теплоотвода от головки, для сохра- |
|
||
нения герметичности уплотнения в |
Рис. 21. Схема уплотнительного |
||
случае пригорания одного или двух |
действия поршневых колец. |
верхних колец и, наконец, для уменьшения утечек заряда при запусках двигателей.
Как указывалось, первое верхнее поршневое кольцо работает в тяжелых условиях: а) подвергается действию высокой температуры; б) отводит наибольшее количество тепла от поршня; в) прижимается к втулке в в. м. т. с давлением, примерно равным наибольшему давлению сгорания. В зоне первого кольца (при положении поршня около в. м. т.) наибольшим будет износ втулки, а из поршневых колец больше всего изнашивается первое кольцо. Для улучшения условий работы верхнего кольца применяют пористое хромиро-
вание двух верхних колец; уменьшают заколечное пространство; снижают температуру канавки до 200—220° С; применяют специальную конструкцию колец (например, трапецеидальные); применяют эффективные присадки к маслу (при повышенных температурах) и др.
Работа трения колец составляет около 40—50% от всей работы трения двигателя, что объясняется тем, что два верхних кольца часто работают в условиях полусухого трения.
Поэтому при конструировании необходимо обратить особое внимание на обеспечение надежной работы колец.
Для предохранения колец от загорания их не следует фиксировать на поршнях в 4-тактных двигателях, что дает возможность кольцам во время работы перемещаться в своих канавках. Для предупреждения «сбивания» всех замков колец в одну линию целесообразно давать косым прорезям замков
59
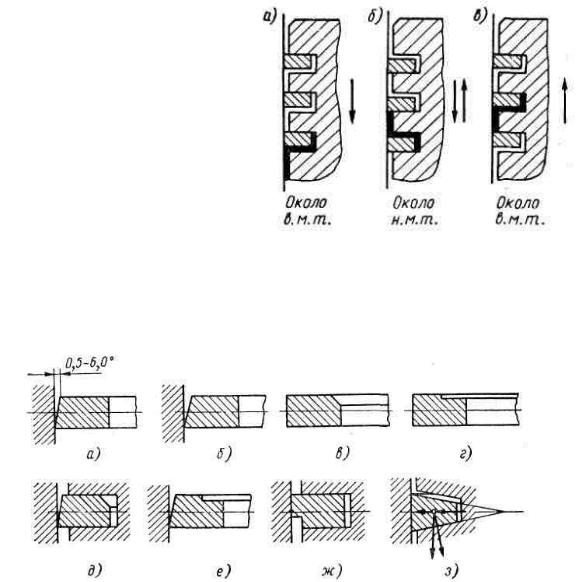
последовательно уклоны в разные стороны. Кольца 2-тактных дизелей часто фиксируют, учитывая наличие окон на зеркале цилиндра.
В малооборотных дизелях устанавливают от 1 до 3 маслосъемных колец в конце направляющей поршня. У многооборотных дизелей маслосъемное кольцо (одно) часто размещают непосредственно над поршневым пальцем.
Излишки масла на зеркале цилиндра, подлежащие удалению, образуются за счет: а) заброса циркуляционного масла на внутреннюю поверхность рабочего цилиндра (втронковых двигателях); б) так называемого «насосного» действия уплотнительных колец.
Насосное действие колец |
|
||||
состоит в «перекачке» масла, |
|
||||
находящегося |
на |
зеркале |
|
||
цилиндра, |
вследствие прижатия |
|
|||
уплотнительных |
колец |
попере- |
|
||
менно то к верхней, то к нижней |
|
||||
стенке канавки (рис. 22). |
|
||||
Для |
удаления |
масла с |
|
||
зеркала цилиндра кольца должны |
|
||||
быть |
снабжены |
режущей |
|
||
кромкой, плотно прилегающей к |
|
||||
цилиндру. Для удаления масла, |
|
||||
скапливающегося под кольцами, |
Рис. 22. Схема насосного действия |
||||
должны |
быть |
предусмотрены |
поршневых колец. |
«башмаки» (прорези) или сверления в самих кольцах, а также радиальные отверстия в стенке направляющей поршня.
Рис. 23. Конструкции уплотнительных колец.
Конструкции уплотнительных колец весьма разнообразны (рис. 23).
Поперечные сечения колец применяются: прямоугольные симметричные, с конусным передним срезом (а, б), клинообразные (трапециевидные) (з), скручивающиеся с несимметричным сечением (в, г). Кольца с конусным срезом со скосом около 1—2° и цилиндрической ленточной выточкой с
60