
Метод_практ_СДВЗ
.pdf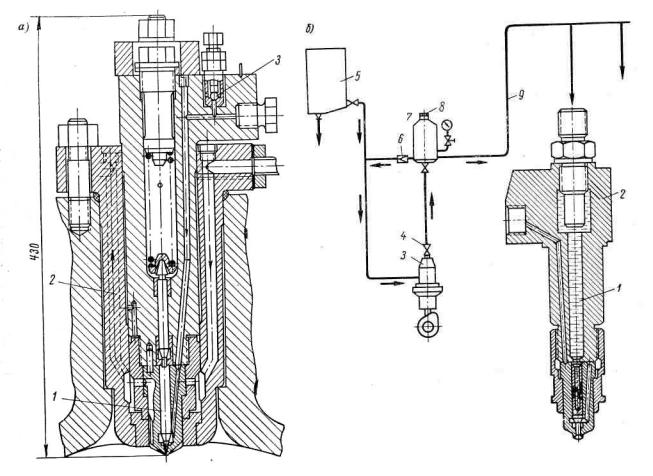
из-за повышенного износа и нарушения плотности цилиндрической части иглы и посадочного пояска нашли применение на судах у дизелей малой и средней мощности гидрозапорные форсунки, у которых игла закрывается под давлением жидкости.
Из схемы топливной системы с гидрозапорной форсункой (рис. 17, б) видно, что из корпуса 2 форсунки удалены все детали, которые действовали на иглу, а образовавшаяся полость 1 заполнена гидросмесью (топливо с маслом Д11) под давлением 180—200 /сГ/сл2. Пополнение утечек гидросмеси и поддержание постоянного давления осуществляется вспомогательной системой, состоящей из расходного бачка 5, одноплунжерного насоса 3, аккумулятора 7 и распределительного трубопровода 9 высокого давления. Кроме того, в системе предусмотрен перепускной клапан 6 с ручной регулировкой, предохранительный клапан 8 и обратный клапан 4. Испытания, проведенные на дизеле 64 25/34, показали, что вместе с топливом при работе дизеля сгорает в цилиндре частично и гидросмесь (около 0,3—0,4 кг1час); это вызывает соответствующее кажущееся снижение удельного расхода топлива (при 100%-ной нагрузке около 1—1,3 г1э. л. с. ч).
Рис. 17. Форсунка дизелей Зульцер типа TD56, МН42 и др. (а); схема гидрозапорной форсунки (б).
151
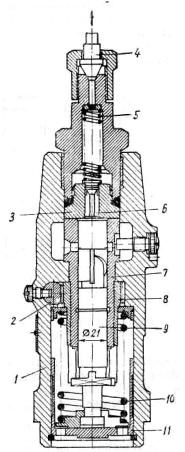
Результаты эксплуатации гидрозапорных форсунок подтвердили возможность значительного увеличения моторесурса распылителей (особенно при низком качестве их изготовления и при обводненном сернистом топливе). Эта система позволяет легко изменять давление гидросмеси, что равносильно увеличению предварительной затяжки (пружины иглы).
Наиболее ответственные прецизионные узлы топливной аппаратуры - плунжерные пары; нагнетательные клапаны насосов; распылители форсунок.
Типичная секция топливного насоса ВД с плунжером-золотником, имеющим механический привод, показана на рис. 18.
Секция насоса включает следующие основные элементы: корпус секции насоса /; прецизионную плунжерную пару, состоящую из плунжера 9 и его втулки 7; прецизионный нагнетательный клапан 6, его корпус 3 и пружину 5; поворотную зубчатую втулку 8 и регулировочную рейку 2; направляющий стакан 11 и пружину возврата плунжера 10; штуцер высокого давления 4 и другие детали.
|
|
Рис 18. Типичная конструкция |
Плунжерные |
пары. Конструкции |
секции золотникового |
плунжерных пар зависят в основном от ти- |
топливного насоса |
|
па топливного насоса |
(клапанного или зо- |
|
лотникового). Наиболее простую конструкцию имеют плунжерные пары клапанных насосов (рис. 19, а) с гладким плунжером, имеющим уплотняющую поверхность по всей своей длине. Благодаря этому плунжерная пара имеет повышенную износостойкость и высокий срок службы (в сравнении с плунжером-золотником). Плунжерные пары с гладким
плунжером нашли преимущественное распространение в |
средне- |
и |
малооборотных судовых дизелях, имеющих повышенный моторесурс. |
|
|
Плунжерные пары топливных насосов с |
золотниковым |
распределением сложнее и имеют различные конструктивные выполнения (см. рис. 19). Наличие плунжера-золотника упрощает общую конструкцию насоса, так как уменьшается количество подвижных деталей. Для нагнетания топлива в них обычно используется около 1/3 хода плунжера, при котором последний имеет наибольшую среднюю скорость. Наличие распределительных кромок у плунжера-золотника дает возможность применять различные способы регулирования, а также изменять момент опережения впрыска при изменении числа оборотов и нагрузки дизеля.
Из приведенных на рис. 19 вариантов выполнения плунжерных пар можно установить следующие особенности их конструкции.
152
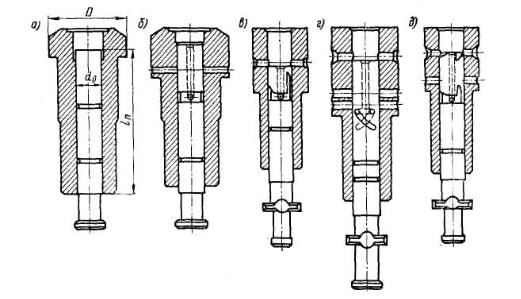
Плунжерная пара (19, б) предназначена для насосов клаланно - золотникового типа, у которых количественное регулирование и изменение момента начала впрыска осуществляется всасывающим клапаном, а отсечка (в конце нагнетательного хода) происходит в тот момент, когда кольцевая проточка на плунжере совпадает с двумя радиальными сверлениями во втулке.
Типичная плунжерная пара с регулировкой по концу подачи показана на рис. 19, в; особенностью ее конструкции является наличие двух симметрично расположенных регулировочных кромок, обеспечивающих уравновешивание боковых сил, действующих на плунжер.
Для увеличения моторесурса плунжерных пар вместо распределительного выреза на головке плунжера применяется осевой канал, соединенный верхними радиальными отверстиями со всасывающей полостью, а нижними - с отсечной полостью (рис. 19, г). Благодаря этому всасывающая полость отделяется от отсечной, что улучшает наполнение насоса и задерживает износ плунжерной пары. Для регулирования и отсечки на плунжере имеются две симметрично расположенные спиральные канавки; средний ряд отверстий во втулке служит для устранения возможности дополнительного впрыска (у многооборотных дизелей). На рис. 19, д показана плунжерная пара с четырьмя симметрично расположенными спиральными кромками, позволяющая осуществлять смешанное регулирование топлива по концу и по началу.
Рис. 19. Конструкции плунжерных пар топливных насосов:
а — клапанного; б — клапанно-золотникового; в, г, д — золотниковых.
В качестве материалов для изготовления плунжерных пар рекомендуются стали ХВГ (ГОСТ 5950—51) и ШХ15 (ГОСТ 801—60) с последующей термообработкой и двойным старением. Твердость сопрягающихся поверхностей готовых деталей должна быть не ниже HRC 58, а уплотнительных торцов не ниже HRC 55. Допускается изготовление
153
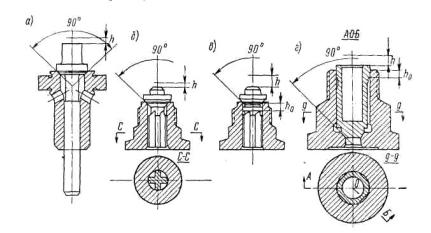
плунжерных пар из стали 25Х5М (а также стали 38ХМЮА и ЗОХЗВА) с последующим азотированием; твердость готовых деталей должна быть не ниже HV 820.
Азотирование плунжерных пар повышает их износостойкость и антикоррозионную стойкость, что особенно важно при использовании в эксплуатации топлив с повышенным содержанием серы.
Наконец, при наличии в деталях резьбовых отверстий можно использовать сталь 18Х2Н4ВА с цементацией рабочих поверхностей на глубину 1,0—1,5 мм и твердостью в пределах HRC 55—60.
К изготовлению и геометрической форме плунжера и втулки предъявляют ряд жестких требований технологического порядка, изложенных в специальных тех-условиях, ГОСТ. Среди них особенно важными являются требования, предъявляемые к плунжерной паре в сборе, — обеспечение свободного передвижения плунжера во втулке и возможно меньшая утечка топлива (либо полное ее отсутствие). Эти требования могут быть выполнены только при строгом соблюдении заданного диаметрального зазора, высокой точности изготовления и высокой чистоте рабочих поверхностей плунжерной пары.
Удовлетворяющая техническим условиям плунжерная пара является комплектом, в котором замена деталей не допускается. Отдельные плунжеры и втулки взаимозаменяемы только в пределах одной группы селекции.
Гарантийный срок службы плунжерных пар составляет около 2500 час. для многооборотных и около 4000 час. для остальных типов дизелей.
Нагнетательные клапаны. Основное назначение нагнетательного клапана - отключать трубопровод высокого давления и форсунку от рабочей полости насоса в процессе наполнения ее топливом. Клапан помещается непосредственно за надплунжерным объемом, снабжается цилиндрической пружиной, а иногда и ходо ограничителем.
Основные конструктивные выполнения нагнетательных клапанов показаны на рис. 21.
Рис. 21. Конструкции нагнетательных клапанов:
а - без разгрузочного пояска; б – золотникового насоса; в - то же с разгрузочным пояском; г - с утопленной пружиной и разгрузочным пояском.
Нагнетательному клапану иногда придается дополнительная функция изменения характеристики топливной системы (особенно для дизелей транспортного типа). В обычной конструкции (рис. 22, а) проходное сечение
154
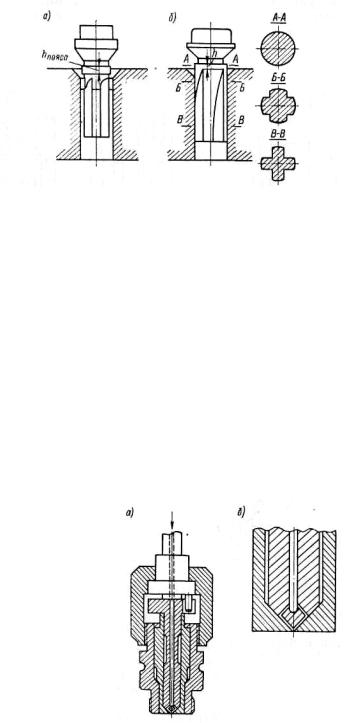
резко увеличивается после выхода отсасывающего пояска из направляющей. У измененной конструкции (рис. 22, б) поясок соединен с пазами на хвостовике клапана, имеющими постепенно уменьшающиеся сечения (А- А; Б—Б; В—В), что вызывает дросселирование топлива при его перетекании из насоса в трубопровод. G увеличением числа оборотов скорость перетекания возрастает, следовательно, в большей степени проявляется дросселирующий эффект, который выражается в большем подъеме клапана. При обратном движении клапана (после отсечки) трубопровод разгружается тем больше, чем выше поднимается клапан.
В качестве материалов для изготовления нагнетательных клапанов рекомендуются те же легированные стали, что и для плунжерных пар, а именно стали ХВГ и ШХ15 и, кроме того, сталь 18ХНВА с последующей цементацией или цианированием. Твердость готовых деталей должна быть для клапана не ниже HRC 56, а для направляющей HRC
60.
Клапаны в сборе проверяют на легкость перемещения клапана в седле и на герметичность.
Распылители. Наиболее ответственным прецизионным элементом форсунки является распылитель, служащий для осуществления эффективного процесса распыливания топлива.
Конструктивные особенности распылителей зависят от типа дизеля, топливоподающей аппаратуры и форсунки.
Ниже приведены типичные примеры распылителей, применяемых на судовых дизелях.
На рис. 23, а показана открытая форсунка-распылитель, у которой отсутствует какой-либо запорный орган, а нагнетательный трубопровод заканчивается либо обычными сопловыми отверстиями, либо перекрещивающимися каналами (рис. 23, б), образующими при впрыске плоский веер (например, у дизелей с ПДП).
Рис. 23. Открытая форсунка -распылитель.
155
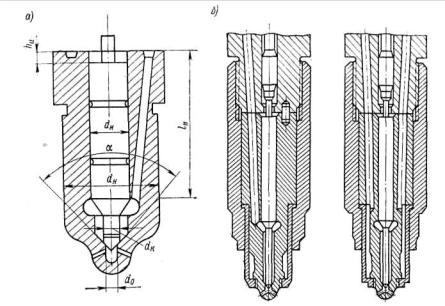
На рис. 24, а показан неохлаждаемый распылитель стандартного типа, у которого корпус распылителя составляет одно целое с направляющей иглы и сопловым наконечником. Видоизменением этой конструкции является удлиненный неохлаждаемый стандартный распылитель (рис. 24, б), характеризующийся удалением от сопла направляющей иглы с целью обеспечения более низкой температуры и меньшей деформации пары направ-
ляющая - игла.
Рис.24. Распылители стандартного типа:
а — нормальный; б — удлиненный
У закрытых форсунок дизелей средней и большой мощности сопловый наконечник делается съемным для удобства его быстрой замены, например в случае засорения сопловых отверстий (см. рис. 15).
Прецизионная пара игла - направляющая выполняется с минимальными зазорами; поэтому нагрев распылителя свыше определенной температуры может вызвать загорание сопловых отверстий и зависание иглы. В дизелях с диаметром цилиндра свыше 400 мм для снижения температуры соплового наконечника применяют циркуляционное охлаждение пресной водой, маслом или топливом (рис. 25). Наиболее эффективным является охлаждение распылителя водой, при помощи которой удается отвести до 2-6 ккал/э. л. с. ч; однако возможность коррозии охлаждаемых поверхностей вынуждает применять чаще всего масло или дизельное топливо.
В дизелях меньшей размерности (с D менее 400 мм) распылитель не охлаждают, но применяют ряд мероприятий для снижения температуры сопловых наконечников, рекомендуется: 1) обеспечить минимальный радиальный зазор, гарантирующий отсутствие касания между распылителем и крышкой (около 0,3—0,4 мм для малых и 0,5—1,0 мм для больших
двигателей); |
2) |
уменьшить по |
возможности |
нагреваемую |
лобовую |
поверхность |
|
распылителя; |
3) применять |
удлиненную конструкцию |
распылителей (см. рис. 24, б); 4) экранировать распылитель стальными колпачками и др.
Эти мероприятия дают возможность снизить температуру распылителей на величину до 50—75° С.
156

Рис. 25. Распылители с жидкостным охлаждением:
а — дизеля SD72; б — дизеля C-758S.
По типу запорных органов распылителей форсунки можно разделить на следующие группы (рис. 26):
-клапанные (схемы а и б), имеющие запорную иглу (клапан), нагруженную цилиндрической пружиной, и постоянное сечение сопловых отверстий (одного или нескольких);
-штифтовые (схемы в, г) с кольцевым сечением (вместо отверстий), имеющие либо постоянное, либо переменное сечение в зависимости от величины подъема иглы;
Рис. 26. Схемы запорных органов распылителей:
а, б — клапанные; в, г — штифтовые; д—с плоским седлом.
157
- клапанно-сопловые, сочетающие наличие клапана, образующего переменное дросселирующее сечение с сопловыми распыливающими отверстиями постоянного сечения (используются в основном в насос-форсунках). В дизелях с неразделенными камерами сгорания применяют в основном клапанные распылители многодырчатого типа.
Штифтовые распылители, а также клапанные, имеющие одно сопловое отверстие, применяют в сравнительно маломощных дизелях с разделенными камерами сгорания. Штифтовой распылитель с цилиндрическим штифтом (в) имеет постоянную площадь истечения и образует сосредоточенный факел с малым углом конуса (до 4°). Штифтовой распылитель с коническим штифтом (г) имеет переменную площадь истечения и позволяет осуществлять конус факела от 4 до 30°. Однодырчатые распылители с плоским седлом (д) применяются сравнительно редко.
Требования к материалам основных деталей распылителя.
Игла и корпус (направляющая) распылителя работают на смятие и истирание в условиях высоких давлений (до 1000 кГ/см2), высоких скоростей протекания топлива (до 200 м/сек) при температурах до 200—250° С. Напряжения смятия опорного пояска иглы доходят до 2500 кГ/см2. Корпус распылителя испытывает при работе ударные воздействия иглы и топлива. Зазоры между направляющей и иглой должны быть выдержаны минимальные (около 2—3 мк).
Таким образом, сорта стали для изготовления распылителей должны обеспечивать получение высокой твердости и износостойкости, сохранение геометрической формы при эксплуатации и хранении, способность работать в условиях повышенных давлений и температур.
Наиболее подходящими для изготовления корпуса распылителя являются стали 18Х2Н4ВА (заменители - стали 15ХНГ2ВА и 15Х2Г2СВА) и ХВГ.
Сортовой прокат стали 18Х2Н4ВА после предварительной термообработки поступает для изготовления корпусов распылителей. Для получения высокой твердости и износостойкости корпуса подвергают цементации на глубину 0,4—1,0 мм,- обеспечивающую твердость рабочих поверхностей до HRC 56—60. Для получения стабильных размеров и геометрической формы корпуса вводят дополнительную обработку холодом и старением.
Заготовки подвергают предварительной термообработке. Окончательная термообработка корпуса распылителя состоит в закалке и низком отпуске с последующим длительным старением.
Игла распылителя изготовляется из быстрорежущей стали Р18 следующего химического состава:
Для игол из стали Р18 (заменителя стали Р9 и ХВГ) применяют стандартный режим термообработки - ступенчатый нагрев под закалку с последующим охлаждением в масле. Закаленные детали подвергают 2- или 3-кратному отпуску. Твердость должна быть в пределах HRC 60—63.
158

Основные требования, предъявляемые к распылителям в сборе:
- пара игла с корпусом - должна быть единым комплектом (т. е. замена одной из деталей не допускается);
-полная герметичность иглы при закрытом ее положении;
-достаточная плотность между иглой и ее направляющей, ограничивающая величину допустимой утечки топлива;
- плавное перемещение иглы в направляющей; - ограничение подъема иглы в заданных пределах.
К геометрической форме деталей распылителя предъявляется ряд жестких требований, оговоренных в технических условиях на изготовление.
Перечисленные выше основные требования к распылителям в сборе контролируются (после обкатки) на особых стендах на герметичность, плотность и плавность перемещения иглы.
Кулачные шайбы. Кулачные шайбы небольших многооборотных дизелей транспортного типа изготовляют за одно целое с распределительным валом; поэтому опережение впрыска, одинаковое для всех цилиндров, может быть изменено только путем углового поворота вала.
У насосов блочного типа с самостоятельным кулачковым валиком регулирование угла опережения осуществляется посредством муфты сцепления вручную или автоматически.
Малооборотные судовые дизели средней и большой мощности имеют отдельные кулачные шайбы, конструкция которых позволяет замену шайб в экс- ] плуатации без разборки распределительного вала и регулирование опережения впрыска (индивидуальное для каждого цилиндра); ниже показаны типичные примеры таких шайб.
Из рис. 36, а видно, что перестановка опережения впрыска достигается за счет регулирования взаимного торцового зацепления двух шайб (переднего и заднего хода), свободно сидящих на \ втулке; последняя насажена на вал на шпонке и имеет, как и шайбы, на внутренней стороне бурта торцовые зубцы. Обе шайбы прижимаются к бурту особой гайкой.
Рис. 36.
Регулирование
опережения кулачных шайб посредством:
а — торцового зацепления шайб; б — болтов.
На рис. 36, б показано, что шайбы выполнены из двух частей, | причем бугель закреплен на валу шпонкой, а кулак притягивается к бугелю двумя болтами. Регулировка достигается за счет 1 передвижки кулака в пределах предусмотренных зазоров; для лучшей самоцентровки при передвижке
159
болты снабжены шаровыми опорами.
В качестве материалов для кулачных шайб применяются стали 12ХНЗА и 15Х с цементацией рабочей поверхности на глубину до 1,5—2,0 мм; твердость поверхности должна быть в пределах HRC 58—62. Шайбы, состоящие из двух половин, обрабатываются совместно и образуют единый комплект, в котором замена отдельных деталей не производится.
Топливные фильтры; топливоподкачивающие насосы
Топливные фильтры служат для очистки топлива от механических примесей, засоряющих систему, и подразделяются на три типа:
-фильтры грубой (предварительной) очистки, устанавливаемые перед топливоподкачивающим насосом низкого давления (НД);
-фильтры тонкой очистки, устанавливаемые на пути от насоса НД к насосу ВД;
-щелевые фильтры ВД, устанавливаемые в непосредственной близости к форсунке или в самом корпусе форсунки.
В фильтрах тонкой очистки топливо очищают от механических примесей посредством пропускания через специальные фильтрующие материалы и через узкие щели, образованные сеткой, набором пластин и т. д.
Вкачестве фильтрующих материалов применяют бумагу, хлопчатобумажную пряжу, концы, фетр, особые поглощающие массы.
Качество очистки топлива оказывает огромное влияние на надежную и бесперебойную работу топливного насоса и форсунки. При работе с неисправными или засоренными фильтрами топливо, загрязненное мелкими твердыми частицами и волокнами, вызывает быстрый износ и заедание плунжерных пар, засорение и загорание сопловых отверстий. Поэтому в эксплуатации необходимо тщательно следить за состоянием фильтров и своевременно производить их чистку, промывку, смену
Конструкции фильтров и их фильтрующих элементов (патронов) чрезвычайно разнообразны. Общие требования, предъявляемые к фильтрам,
— наибольшая эффективность их действия при минимальных габаритах, надежность работы и простота обслуживания и смены патронов в эксплуатации. На дизелях малой и средней размерности фильтры обычно устанавливают на самом двигателе. Иногда, как, например, на крупных судовых дизелях, они нередко являются отдельными автономными агрегатами судовой силовой установки. Фильтры судовых дизелей обычно выполняют сдвоенными, чтобы обеспечить текущую очистку фильтра без остановки двигателя. Сопротивления в новых фильтрах не должны превышать 0,1—0,2 кГ/см2 и контролируются по перепаду давлений до и после фильтра.
На рис. 37, а показан сдвоенный фильтр грубой очистки, применяемый на дизелях Д50 и Д100. Он состоит из двух металлических элементов - наружного 2 и внутреннего 1 гофрированых стаканов, на которых навита латунная лента, имеющая с одной стороны выступы, расположенные на равных расстояниях. В навитом состоянии лента образует щель величиной в 0,07 мм. Для переключения фильтров в корпусе предусмотрена коническая пробка 3, служащая в качестве трехходового крана.
160