
- •ПЛАВКА ЧУГУНА В ВАГРАНКАХ
- •Содержание
- •1. Материалы, применяемые при плавке в вагранке
- •1.1 Огнеупорные матрериалы
- •1.2 Металлическая шихта
- •1.3 Ваграночное топливо
- •1.4 Флюсы
- •Вопросы для самоконтроля
- •2. Основное и вспомогательное оборудование ваграночного комплекса
- •2.1 Принцип работы вгранки
- •2.2 Устройство и основные узлы ваграночного комплекса
- •Вопросы для самоконтроля
- •3. Технологический процесс плавки чугуна в вагранке
- •3.1 Тепловые и металлургические процессы плавки
- •3.2.Технология плавки в коксовых вагранках
- •3.3 Расчет шихты
- •3.4 Экспресс-контроль чугуна по ходу плавки
- •Вопросы для самоконтроля
- •4. Расчет вагранки
- •4.1 Расчет материального и теплового баланса вагранки
- •4.2 Расчет размеров вагранки
- •Приложение 2
- •Приложение 3
- •Приложение 4
- •Приложение 5
- •Приложение 6
- •Приложение 7
- •Список литературы
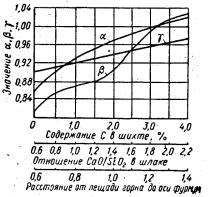
Количество шлака при кислом процессе составляет 5 – 8%, а при основном 8 – 10% от массы чугуна.
Легирующие элементы Сг, Ni, Cu, Ti, Mo и др., как правило, вводятся в
жидкий чугун, так как поставка природно-легированных доменных чугунов литейным цехам сократилась, а загрузка в вагранки высокопроцентных ферросплавов связана с их повышенным угаром и увеличением колебаний химсостава чугуна по этим элементам. Величина угара элементов зависит от условий плавки, конструкции вагранки, состава шихты и других факторов. Влияние этих факторов на содержание в чугуне основных элементов (%) выражается нижеприведенными уравнениями:
С = (1,3 + 0,00238 tМе + 0,027МnМе – 0,317SiMe – 0,33РМе – 0,36SМе) αβγ; (3.7)
Si = 0,24 + l,093Siш – 0,08CaCО3 – 0,064FeO; |
(3.8) |
Мn = – 0,013 + 0,852Мnш + 0,006CaCO3 – 0,002FeO; |
(3.9) |
S = – 0,088 + 1,349Sш – 0,018СаСОз + 0,003FeO; |
(3.10) |
(при непрерывном выпуске шлака); |
|
S = 0,051 + 0,444Sш – 0,008СаСОз + 0,003FeO |
(3.11) |
(при периодическом выпуске шлака), |
|
где МnМе, SiМe, РМе, SMe – содержание элементов в чугуне; Siш Мnш, Sш – содержание элементов в шихте; α, β, γ – коэффициенты, определяемые по рис.14. Ко-
эффициент α определяется в зависимости от содержания углерода; β – в зави-
симости от отношения CaO/SiO2 в шлаке; γ – в зависимости от расстояния от лещади горна до
|
оси фурм. |
|
Как видно из этих уравнений, стабильность со- |
|
става выплавляемого чугуна зависит от ста- |
|
бильности состава шихты и шлака, а также от |
|
температуры металла. Минимальные колебания |
|
состава чугуна обеспечиваются при примене- |
|
нии автоматических систем дозировки, ста- |
|
бильности химического состава шихты и под- |
|
держании постоянной tМе. В этом случае коле- |
Рис. 14 Вспомогательный график для |
бания химического состава в течение плавки не |
определения коэффициентов α, β и γ в фор- |
превышают значений: по С – 0,05%; по Si – |
муле (3.7) при расчете содержания углеро- |
0,15%; по Мn – 0,05%; по S – 0,02%; по Р – |
да в чугуне. |
|
|
0,1%. |
3.2.ТЕХНОЛОГИЯ ПЛАВКИ В КОКСОВЫХ ВАГРАНКАХ
Технология плавки должна обеспечивать получение нужного и стабильного состава чугуна и высокой температуры металла при заданной производительности. Выполняются эти требования за счет выбора соответствующего расхода
32
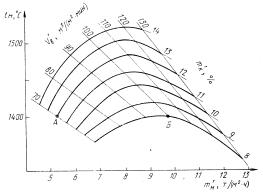
кокса и дутья (иногда и за счет изменения температуры подогрева дутья). Сложность управления процессом заключается в том, что изменение расходов кокса или воздуха изменяет одновременно как температуру металла, так и производительность вагранки. Поэтому для изменения только производительности или только температуры металла, как правило, необходимо изменять и расход кокса, но и расход дутья, как это видно из номограммы на рис. 15.
Оперативное регулирование процессом обеспечивается только за счет изменения температуры или расхода дутья и содержания в нем кислорода. Изменение же расхода кокса влияет на ваграночный процесс с задержкой в 30
– 60 мин, т. е. после достижения измененной порцией кокса холостой колоши. В определенном интервале можно регулировать производительность ва-
Рис. 15 Сетчатая номограмма взаимосвязи параметров гранки только за счет изменения рас-
ваграночного процесса хода дутья. При этом температура металла сохраняется практически постоянной. Применение подогрева дутья, доменного профиля шахты вагранки и по-
дача 50% дутья через фурмы, расположенные на высоте 700 – 1000 мм от первого ряда, позволяет значительно увеличить диапазон допустимого изменения производительности вагранки только за счет изменения подачи дутья. В табл. 3.4 приводятся пределы изменения средней удельной производительности в различных конструкциях вагранок, при которых температура металла и расходы кокса сохраняются постоянными.
Необходимость изменять производительность вагранки возникает в первую очередь при серийном поточном производстве, где требуется синхронность производительности вагранки с металлоемкостью заформованных опок. Уменьшить колебания производительности вагранки можно за счет применения миксеров большой емкости, сглаживающих неравномерность потребления металла в течение смены и его химсостава.
Тепловой к.п.д. работы вагранок различен при нагреве шихты, плавлении ее и нагреве жидкого металла. В зоне нагрева шихты к.п.д. имеет наибольшее значение и составляет 50 – 60%, в зоне плавления 30 – 40%, а в зоне нагрева капель жидкого металла – всего 10 – 15%.
33
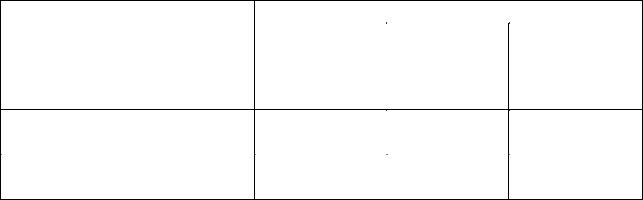
Таблица 3.4
Удельные производительности вагранок различных типов
|
|
Вагранки |
|
|
Показатели |
с цилиндриче- |
с доменным |
с вторичным |
|
ским профи- |
профилем и |
дутьем и пере- |
||
|
лем и холод- |
подогретым |
менной темпе- |
|
|
ным дутьем |
дутьем |
ратурой дутья |
|
Средняя удельная производи- |
7,0 – 7,5 |
8,0 – 8,5 |
7,0 |
|
тельность, т/(м2×ч) |
||||
|
|
|
||
Диапазоны изменения удель- |
± 15 |
±3 0 |
± 60 |
|
ных производительностей, % |
||||
|
|
|
Оптимальный режим работы вагранок – получение чугуна в интервале температур 1340 – 1400°С при холодном дутье и 1400 – 1450°С при подогретом дутье. Получение более высокой температуры металла в вагранке (до 1550°С) возможно, но требует высокотемпературного дутья и повышенного расхода кокса; поэтому экономичнее использовать для перегрева электрические индукционные и дуговые миксеры. Выплавка чугуна с более низкими температурами, хотя и позволяет снизить расход кокса, приводит к технологическим трудностям по обслуживанию вагранки из-за зашлаковывания фурм, настылей, опасности «закозления» вагранки при незапланированных простоях и др.
Методы интенсификации ваграночного процесса направлены либо на повышение температурного режима в вагранке, либо на перегрев жидкого металла на желобе, в горне или копильнике. Для повышения температуры металла применяется подогрев дутья, обогащение его кислородом, подача дутья через два ряда фурм, применение карбида кальция и подача части дутья через горн.
Подогрев дутья и обогащение его кислородом обеспечивают повышение температуры металла примерно на 15 – 25°С на каждые 100°С подогрева дутья или на 1% повышения содержания кислорода в дутье. Наиболее простым методом обогащения дутья кислородом является его подача в воздухопровод перед фурменной коробкой. Во многих случаях обогащение дутья кислородом применяют в начальный период плавки. В этом случае увеличение содержания кислорода на 2% повышает температуру первого выпуска чугуна на 70°С. По зарубежным данным в связи с ростом цен на чушковые чугуны и кокc, применение кислорода экономически оправдано при объеме выплавки чугуна более 15 т/сут.
Отвод части дутья через горн и стационарный копильник расширяет высокотемпературную кислородную зону и может привести к повышению температуры металла на 30 – 50 °С в вагранках малого диаметра. Положительные результаты при этом методе обеспечиваются только в случае правильного распре-
34
деления дутья, продуваемого через горн и шахту вагранки в отношении 20 – 25% и 75 – 80% и увеличения общего расхода дутья.
Карбиды кальция или кремния подаются в вагранку вместе с коксом рабочей топливной колоши в количестве 2% от металлозавалки. Благодаря высокой температуре плавления, карбид кальция плавится в кислородной зоне и сгорает, выделяя 5500 ккал/кг (23×106 Дж/кг) и повышая температуру в этой зоне. Присадка 2% карбида кальция повышает температуру металла на 40 – 50°С и приводит к снижению содержания серы в чугуне. Положительные результаты получаются только при применении литейного карбида кальция эвтектического состава с температурой плавления 1650 °С.
Для перегрева жидкого металла применяется также электроконтактный и электрошлаковый подогрев на желобе вагранки либо продувка кислородом жидкого металла в копильнике или на желобе. Однако эти методы не нашли широкого применения из-за сложности и небезопасности в обслуживании и могут считаться только временной мерой для периодического перегрева чугуна. Техника же ведения процесса плавки должна обеспечивать нормальную, безаварийную эксплуатацию вагранки. Поэтому предпочтительнее вагранки с подогревом дутья и очисткой ваграночных газов, хотя они требуют более жесткой регламентации всех приемов по подготовке и проведению плавки. Кроме того, арсенал приемов и возможностей ведения плавки в них значительно шире, чем в вагранках с холодным дутьем.
Ремонт и подготовка вагранки к плавке заключается в ремонте футеровки, металлоконструкций, механизмов и оборудования, обеспечивающего нормальную работу вагранки. Ниже рассматриваются периодичность и технология ремонта футеровки в вагранках с длительным и односуточным циклом работы.
Капитальный ремонт трубы вагранки выше завалочного окна производится не чаще одного раза в год. После удаления всей старой футеровки труба выкладывается шамотным кирпичом – клином ребровым и клином прямым марки ШБВ (ГОСТ 3272 – 71) – на ремонтной глине «на ребро» или «на ребро и плашку»; толщина футеровки 120 мм или 180 мм. Зазор между кирпичами – не более 2 – 3 мм.
Капитальный ремонт шахты вагранки выше зоны плавления до защитных кирпичей или загрузочного окна выполняется не чаще одного раза в квартал. При этом удаляется внутренний ряд футеровки. Нарушенные места наружного ряда кладки закладываются подтесанным кирпичом. Кладку выполняют шамотными кирпичами марки ШБВ (клин ребровый, прямой, трапециевидный) на жидком растворе ремонтной глины. Толщина шва – не более 1,5 мм. Продолжительность сушки на воздухе – не менее 24 часов после капитального ремонта розжиг вагранки требуется проводить на 0,5 – 1 часа дольше, чем после текущего ремонта, загрузив дополнительное количество кокса.
Текущий ремонт шахты вагранки в плавильном поясе производят после каждой выбивки вагранки. При этом сначала удаляют шлак, прогоревшие кирпичи и настыли, но сохраняют ошлакованную поверхность шахты. Новую фу-
35
теровку выполняют кирпичом марки ШАВ, набивным футеровочным составом или торкретной массой. Толщина футеровки в вагранках без водяного охлаждения 180 – 250 мм, в водоохлаждаемых – 65 – 120 мм. Вагранки с длительным циклом работы либо вовсе не имеют футеровки, либо обмазываются ремонтной глиной толщиной 8 – 20 мм, либо выкладываются «на плашку» лещадкой или кирпичом «клин ребровой».
Текущий ремонт зон фурм и горна вагранки выполняется после каждой выбивки. При ежедневной выбивке вагранок после одной или двух смен работы они футеруются слоем толщиной 180 – 500 мм так же, как и плавильный пояс. При работе без выбивки в течение недели и более, горн выкладывается высокоглиноземистым кирпичом (муллитокорундовым) класса ВГО – 72 от подины до уровня фурм. Зона фурм при доменном профиле набивается шамотной массой или выкладывается кирпичом марки ШАВ. Вся зона может набиваться графитовой массой.
Текущий ремонт переходного канала, сифонного шлакоотделителя и летки производят после каждой выбивки. При холодном дутье для такого ремонта используют наиболее качественный кирпич марки ШАВ с толщиной шва не более 1,5 мм, при длительном цикле работы – высокоглиноземистый кирпич, блоки ДВ-5, ДВ-6 (ГОСТ10381 – 84), выкладываемые на высокоглиноземистом мертеле марки ВТ-1.
В качестве набивных масс для ремонта футеровки применяются: шамотная масса (24% глины, 36% песка, 40% шамота); углеродистая масса (коксик молотый 70%, мертель высокоглиноземистый 20%, пек каменноугольный 10%); масса на основе кремнезема (песок 92 – 94%; мертель 6 – 8%), наносимая шприцмашиной (фирма SAS, Франция); ремонтная глина (глина огнеупорная 35%, песок 65%). Кроме того, во всех случаях добавляется вода в количестве 6 – 15%.
Подготовка вагранки к плавке заключается в проверке исправности всех узлов и систем, обеспечивающих ее эксплуатацию. Особое внимание при этом нужно обращать на прочность крепления и исправность днища вагранки, фурм, устройств для набора, взвешивания и загрузки шихты. В вагранках с очисткой газов, подогревом дутья и использованием природного газа необходимо проверять плотность фланцевых соединений смотровых люков, задвижек, шиберов, предохранительных и взрывных клапанов в системе газоочистки и трубопроводах природного газа, воды и воздуха. При подготовке вагранки закрытого типа к плавке необходимо проверять исправность всех систем дистанционного и автоматического управления, приборов КИП и работу звуковой и световой аварийной сигнализации.
Работа вагранки. Перед началом работы в вагранку через загрузочное окно загружают кокс. Получаемый столб кокса называют холостой колошей. Розжиг кокса холостой колоши в открытых вагранках происходит за счет естественной тяги трубы. Загрузка кокса проводится частями в 2 – 3 приема. Разжигают холостую колошу чаще всего природным газом, а в случае его отсутствия
– дровами. После загрузки первой порции кокса (35 – 50%) в отверстие рабоче-
36
го окна вставляется предварительно зажженная переносная горелка для природного газа (типа ИГК-2 – 10). После того, как кокс у рабочего окна разгорелся, горелки поочередно переставляют в фурмы, следя за равномерностью розжига холостой колоши по сечению. После розжига первой порции загружают последующие части холостой колоши. Розжиг завершается продувкой холостой колоши и замером ее высоты. Уровень холостой колоши должен быть на 1200 – 1500 мм выше фурм независимо от диаметра вагранки и применяемого давления дутья. Розжиг продолжается 3 – 4 часа.
В закрытых вагранках розжиг можно производить так же, как и в открытых, или же за счет принудительной тяги через систему газоочистки. В последнем случае появляется возможность в определенных пределах регулировать интенсивность розжига холостой колоши, создавая то или иное разрежение под колошником вагранки. В период розжига за счет принудительной тяги должны быть приняты все меры против образования взрывоопасной смеси газов с воздухом в системе газоочистки. В различных конструкциях эти меры обеспечиваются за счет надежной герметизации загрузочного отверстия или установки запальника для дожигания образовавшейся смеси на входе в систему газоочистки. При принудительной тяге вся холостая колоша загружается в вагранку полностью до начала розжига. Период розжига может быть сокращен до 1,5 – 2 часов. Продувка холостой колоши и замер ее высоты, как правило, не проводятся.
На подготовленную таким образом холостую колошу загружают первую металлическую колошу, на нее первую рабочую коксовую колошу. Далее вагранку загружают поочередно металлическими и коксовыми колошами вплоть до загрузочного окна вагранки. В каждую металлическую колошу добавляют флюс (известняк) для образования необходимого химического состава ваграночного шлака. В процессе ведения плавки ошлаковываются зола кокса, футеровка, пригар с литников.
Масса металлической колоши принимается равной 1/10 – 1/12 часовой производительности вагранки, а масса рабочей топливной (коксовой) колоши – 8 – 14% от массы металлической. Загрузка первого столба шихты зачастую проводится с соблюдением следующих особенностей: в первых четырех-пяти колошах доля металлозавалки уменьшается на 20%, доля стального лома увеличивается в 1,5 – 2 раза, чтобы уменьшить пригар углерода; исключается применение для этих колош массивных кусков лома (боя изложниц). В пятую колошу загружается удвоенная порция топлива. Перед пуском дутья закрывают летки для металла и шлака или (при наличии сифонного металлоприемника-шлакоотдели- теля) переходный канал. Металлическая летка закрывается притычной глиной с бруском, изготовленным по размеру летки из боя стержней. Шлаковая летка заделывается горелой и наполнительной формовочной смесью. Переходный канал шлакоотделителя забивается на всю длину гарью или сухим кварцевым песком, а сверху притрамбовывается формовочной смесью. Расчет шихты производится с учетом угара элементов, указанного выше.
37
Дутье в вагранку подается сразу же после окончания завалки первого столба шихты. Если по каким-либо причинам пуск дутья задерживается, нужно принять меры к замедлению горения кокса холостой колоши. В вагранках с принудительной тягой для этого уменьшают разрежение на колошнике; в открытых вагранках закрывают гляделки на нескольких фурмах. Закрывать гляделки всех фурм до пуска дутья в вагранку категорически воспрещается из-за возможности образования взрывоопасной смеси в фурменной коробке и в воздухопроводе. В вагранках с дожиганием газов, производимым в специальных камерах или топках, перед пуском дутья необходимо убедиться в том, что приняты необходимые меры для устойчивого горения ваграночных газов (включены запальники, созданы необходимые разрежение и температура в камере дожигания). Давление дутья вначале рекомендуется устанавливать в размере 40 – 50% от оптимального.
При подаче дутья в вагранку воздух поступает через фурмы в холостую коксовую колошу. Начинается интенсивный процесс горения кокса с выделением большого количества теплоты. Первая металлическая колоша, расположенная непосредственно на раскаленном коксе, начинает плавиться. Капли и струйки жидкого металла стекают между кусками кокса к подине. Сюда же стекает и образующийся в процессе плавки шлак. Через соединительную летку металл и шлак поступают в копильник. Когда уровень шлака достигнет необходимой высоты, открывают шлаковую летку и шлак выпускают из копильника. Затем выпускают расплав чугуна через металлическую летку.
При правильном ведении розжига первые капли металла появляются у фурм через 15 – 20 мин; после этого давление дутья увеличивют до оптимального. Первый выпуск металла производят в зависимости от конструкции вагранки, емкости горна или копильника через 15 – 40 мин после появления первых капель у фурм. При выпуске первого металла через сифонный шлакоотделитель необходимо кратковременно уменьшать давление дутья в вагранке во избежание выброса металла из металлоприемника давлением газов.
К моменту полного расплавления первой металлической колоши уровень холостой коксовой колоши понижается. Для получения чугуна с постоянной температурой и постоянным химическим составом высота рабочей топливной колоши должна быть равна высоте, на которую уменьшилась холостая колоша. Тогда каждая последующая металлическая колоша плавится на одной и той же высоте. При этом движение колош происходит непрерывно.
В вагранке горячие газы, образующиеся при горении кокса, поднимаются, а материалы опускаются (принцип противотока). Вследствие этого происходит интенсивная теплопередача между газами и материалами, загружаемыми в вагранку. Металлическая колоша, опускаясь по шахте, постепенно нагревается до температуры плавления и плавится.
Горячие газы при движении вверх, встречаясь со все более холодными металлическими колошами, охлаждаются. Использование теплоты отходящих газов повышает КПД вагранки.
38
Основные показатели работы вагранки:
–температура выплавленного чугуна tM, єC;
–удельный расход кокса m′K , %;
–удельный расход воздуха VB′ , M3/(M2·мин);
–удельная производительность по жидкому металлу m'M, т/(M2·ч).
Температуру чугуна замеряют при выходе его из вагранки. Расход кокса считают на 100 кг металлозавалки. Расход воздуха в M3/мин и производительность вагранки т/ч пересчитывают на 1 M2 поперечного сечения вагранки в свету.
Взаимосвязь основных показателей работы вагранки, полученная В. Паттерсоном, представлена на рис. 15. Исследования проведены на вагранке с внутренним диаметром шахты вагранки 700 мм, полезной высотой 4900 мм при работе на холодном дутье. Значения удельного расхода кокса, приведенные на диаграмме, соответствуют удельному расходу углерода кокса без учета золы и других примесей, что облегчает применение полученных данных при работе на различных видах кокса.
По рис. 15 можно выбрать наиболее оптимальный режим работы. Например, если вагранка работает в режиме, соответствующем точке А: tM = 14000C; m′K = 12 %; VB′ = 70 M3/(M2·мин); m'M = 5,3 т/(м2·ч), то увеличив только удельный рас-
ход воздуха до 100 M3/(M2·мин), можно снизить расход кокса на 33% (m′K = 8 % ), сохранив температуру чугуна 14000C и увеличив удельную производительность
вагранки до 10 т/(M2·ч) (точка Б).
Управление работой вагранки в период плавки заключается также в обеспечении своевременного выпуска чугуна и шлака, нормальной работы всех механизмов и приборов, в изменении при необходимости режима плавки, в кратковременных остановках вагранки и устранении неполадок в ее работе. Если заранее известно о необходимости остановки вагранки, то за 30 – 40 мин до этого необходимо загружать удвоенную топливную колошу. При непредвиденных остановках более чем на 15 – 20 мин удвоенную колошу нужно загружать сразу же после пуска вагранки. Время простоев вагранки не должно превышать 10 мин в первый час работы, 30 мин – во второй и третий часы работы, не более 1
– 1,5 часов во все последующее время работы.
Период окончания плавки начинается с прекращения загрузки шихты. По мере проплавления столба шихты следует снижать давление дутья в фурменной коробке, сохраняя постоянным его расход при уменьшающемся сопротивлении столба шихты. В вагранке закрытого типа уменьшают расход дутья с таким расчетом, чтобы температура газов на колошнике до полного проплавления шихты не превышала 700 – 800°С. В вагранке с горячим дутьем после прекращения подачи дутья в вагранку его нужно пропускать через рекуператор для охлаждения теплообменников еще в течение 30 – 40 мин. Перед выбивкой вагранки следует выпустить весь металл и шлак из нее и сифонного устройства, убедиться в отсутствии воды и влажного грунта под вагранкой. Разгерметизация вагранки и
39
выключение запальника в камере дожигания закрытых вагранок производятся только после полной выбивки вагранки.
Специальные требования техники безопасности при ремонте и плавке заключаются в следующем. Работы внутри шахты вагранки, в рекуператоре и других узлах должны проводиться только после их проветривания и охлаждения до 30°С и в присутстви второго рабочего. Перед выполнением этих работ необходимо убедиться в узлах угарного газа. Рабочий, находящийся внутри узла, должен постоянно поддерживать связь с рабочим, находящимся снаружи. Удаление прогоревшей футеровки начинают сверху, новую фтеровку выполняют в обратном порядке – снизу вверх.
Перед началом ремонтных работ необходимо убедиться в плотности закрытия задвижек, шиберов и затворов на трубопроводах воздуха, ваграночногои природного газа. В период розжига вагранки, завалки первого столба шихты и после прекращения подачи дутья запрещается находиться против открытых фурм. При прекращении подачи дутья фурмы должны быть открыты, закрываются они не рань-ше чем через 30 – 40 с после возобновления подачи дутья. Прекращать подачу дутья следует шибером, расположенным на трубопроводе как можно ближе к фурменной коробке. В вагранках с сифонными шлако-отделителями запрещается наращивать металлические и шлаковые порги в процессе плавки. В вагранках с герметичной загрузкой шихты запрещается какие-либо работы, связанные с нарушением герметичности в системе газоочистки, до полной остановки вагранки и устройств (дымососов, эжекторов), обеспечивающих разрежение в системе газоочистки. Аварийные работы на колошнике и у системы газоочистки разрешается проводить только в противогазе и в присутствии второго рабочего или мастера.
Целесообразно оснащение вагранок системой автоматического управления процессом плавки и контроля. Наличие устройств для подогрева дутья, очистки газов, водяного охлаждения, набора и массоизмерения шихты, выдачи металла, уборки отходов очень затрудняет обслуживание ваграночной установки при необходимости визуального наблюдения за работой всех систем и узлов вагранки и местного управления отдельными приводами и снижает надежность ее работы. Поэтому снабжение системой КИП и центральным пультом управления превращается из желательного элемента культуры производства в непременное условие безаварийной работы вагранки. В этом случае решаются три основных задачи:
∙управление тепловым режимом ваграночного процесса; ∙управление процессом дозирования шихтовых материалов;
∙управление электроприводами, локальными системами регулирования и контроль за параметрами процесса, обеспечивающими нормальный безаварийный режим работы установки.
Управление тепловым режимом ваграночного процесса заключается либо в поддержании заданных значений режимных параметров, таких, как расходы кокса и воздуха, температура подогрева дутья и др., либо в регулировании
40
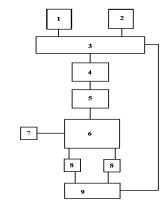
производительности или температуры металла по одному из параметров режима плавки, либо, наконец, в поддержании в заданных пределах всех целевых переменных, таких, как производительность печи, температура металла, состав его и минимальная стоимость производства за счет отработки в счетно-решаю- щем устройстве оптимальных значений режимных параметров и автоматического их поддержания.
Поддержание с пульта заданных с пультов управления или шкафов КИП параметров режима плавки осуществляется автономными локальными системами регулирования с помощью стандартных электронных регулирующих приборов с датчиками. Регулирование производительности вагранки и температуры металла по одному или двум параметрам режима плавки (например, по расходу и температуре дутья) осуществляется с помощью одноили двухканального оптимизатора. Примерами таких систем являются одноконтурный, экстремальный регулятор или двух контурный и двухканальный регулятор конструкции ИПЛ АН Украины.
Управление ваграночным процессом, обеспечивающее заданные значения всех целевых переменных, осуществляется с помощью специальных УВМ для автоматизации технологических процессов (АСУ ТП). Схема управления ваграночным процессом с помощью такой системы представлена на рис. 16. В счет- но-решающее устройство машины вводятся заданные целевые параметры и программа с данными по конструкции установки. Счетно-решающее устройство вырабатывает управляющие параметры ваграночного процесса и передает их для выполнения соответствующим автономным системам регулирования.
Одновременно счетно-ре- шающее устройство вырабатывает промежуточные переменные, служащие для контроля процесса плавки. Фактически достигнутые целевые и промежуточные параметры сопоставляются с заданными, и в случае рассогласования счетно-ре- шающее устройство вводит необходимые коррективы в управляющие команды.
Система управления процессами дозирования шихтовых материалов обеспечивает точность состава
колош и заданное соотношение металл-кокс и металл-флюсы. Добиться точного соответствия массы каждой составляющей шихты в колоше заданной дозе с помощью механизированных дозирующих установок не представляется воз-
41