
- •ПЛАВКА ЧУГУНА В ВАГРАНКАХ
- •Содержание
- •1. Материалы, применяемые при плавке в вагранке
- •1.1 Огнеупорные матрериалы
- •1.2 Металлическая шихта
- •1.3 Ваграночное топливо
- •1.4 Флюсы
- •Вопросы для самоконтроля
- •2. Основное и вспомогательное оборудование ваграночного комплекса
- •2.1 Принцип работы вгранки
- •2.2 Устройство и основные узлы ваграночного комплекса
- •Вопросы для самоконтроля
- •3. Технологический процесс плавки чугуна в вагранке
- •3.1 Тепловые и металлургические процессы плавки
- •3.2.Технология плавки в коксовых вагранках
- •3.3 Расчет шихты
- •3.4 Экспресс-контроль чугуна по ходу плавки
- •Вопросы для самоконтроля
- •4. Расчет вагранки
- •4.1 Расчет материального и теплового баланса вагранки
- •4.2 Расчет размеров вагранки
- •Приложение 2
- •Приложение 3
- •Приложение 4
- •Приложение 5
- •Приложение 6
- •Приложение 7
- •Список литературы
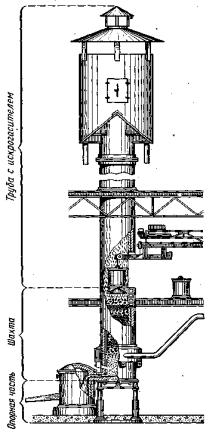
2. Основное и вспомогательное оборудование ваграночного комплекса
2.1 ПРИНЦИП РАБОТЫ ВГРАНКИ
Вагранка – шахтная плавильная печь непрерывного действия, в которой нагрев, плавление и перегрев капель расплавившегося металла осуществляются главным образом за счет теплоты, образующейся при сгорании твердого топлива.
Вагранка (рис. 2) состоит из следующих основных узлов: опорной части с механизмом открывания днища; шахты, оканчивающейся трубой с искрогасителем; фурменной коробки; механизма для загрузки шихты. Перед началом работы закрывают днища, набивают подину (лещадь) вагранки формовочным составом. Затем на нее загружают слой кокса, называемый холостой коло-шей, и разжигают его природным газом или дровами. Когда кокс разгорится, закрывают рабочее окно и на холостую колошу слоями загружают рабочие колоши, состоящие из металлических компонентов шихты, кокса и флюса. Загрузку ведут до заполнения шахты до завалочного окна, после чего через отверстия в шахте в нижней части, называемые фурмами, подают воздух, вызывающий интенсивное горение кокса.
Продукты горения кокса – ваграночные газы имеют высокую температуру; поднимаясь вверх по шахте, они нагревают шихту. По мере сгорания кокса рабочие колоши опускаются вниз, прогреваются восходящим потоком ваграноч-
Рис. 2 Общий вид вагранки ных газов. Металлические компоненты прогреваются до температуры плавления, плавятся на высоте 500 – 800.мм над фурмами и отдельными струйками и каплями, проходя
по раскаленной поверхности кокса, перегреваются и скапливаются в шахте вагранки ниже фурм (в горне) или стекают из вагранки в копильник для жидкого металла.
Кокс рабочих колош постоянно пополняет сгоревший кокс холостой колоши, так чтобы ее высота осталась постоянной. Флюсы, соединяясь с золой кокса, сплавившейся футеровкой лечи и посторонними предметами, поступающими с шихтой, образуют шлак, состоящий в основном из двойных и тройных соединений окислов SiO2, CaO, А12О3.
16
По мере расплавления металлической шихты, сгорания кокса, образования шлака и выпуска металла и шлака из вагранки – в шахту печи загружают новые колоши металла, кокса и флюсов.
Ваграночные газы, закончившие теплообмен с шихтой (называемые колошниковыми), через трубу и искрогаситель выбрасываются в атмосферу. Однако они содержат значительное количество пыли и токсичных составляющих в виде угарного, сернистого и серного газов, поэтому перед выбросом в атмосферу должны проходить эффективную очистку. Кроме того, в них содержится значительное количество тепловой энергии (имеют температуру 250 – 500°С и содержат 10 – 25% СО, при дожигании которого выделяется большое количество теплоты). Эта тепловая энергия может быть использована для подогрева воздуха, идущего в вагранку.
В зависимости от источника теплоты, используемого для плавки, вагранки подразделяют на коксовые, газовые, коксогазовые и электрические. Наибольшее распространение получили коксовые вагранки (98%), а коксогазовые и газовые не нашли широкого применения (2%). Электрические (плазменные и индукционные) вагранки имеются лишь в опытных образцах.
Вагранки классифицируются по футеровке (кислые и основные), по теплотехническим особенностям (без подогрева и с подогревом дутья), по степени очистки газов (открытые, полузакрытые и закрытые). В открытых вагранках проводится только грубая очистка от крупных частиц пыли, в полузакрытых очищается только часть газов, а в закрытых эффективной очистке подвергаются все газы.
Открытые вагранки холодного дутья не могут быть рекомендованы к применению по экологическим соображением и в связи с низким КПД. Вагранки с частичной очисткой газов от пыли в мокрых искрогасителях (пылеосадителях) допускается применять диаметром до 1300 мм при условиях длительности непрерывной работы не более 7 часов и значительной удаленности от жилых помещений.
Вагранки с высокотемпературным подогревом дутья в выносном рекуператоре с использованием теплоты отходящих ваграночных газов и полной их очисткой рекомендуются для высокопроизводительных литейных цехов заводов индивидуального и мелкосерийного производств, а также цехов металлургических предприятий.
При крупносерийном и массовом производстве отливок должны применяться вагранки с высокотемпературным подогревом дутья с применением эффективных рекуператоров и полной очисткой ваграночных газов.
По условиям теплообмена между металлом, коксом и газами всю шахту вагранки можно условно разбить на четыре зоны (рис. 3).
Зона I – зона подогрева шихты; она простирается от завалочного окна вниз до того уровня, на котором температура поверхности кусков чугунной шихты достигает температуры плавления (1150 – 1200 °С). Размеры этой зоны не постоянны. Они зависят от многих факторов, в первую очередь от расхода кокса и воздуха и
17
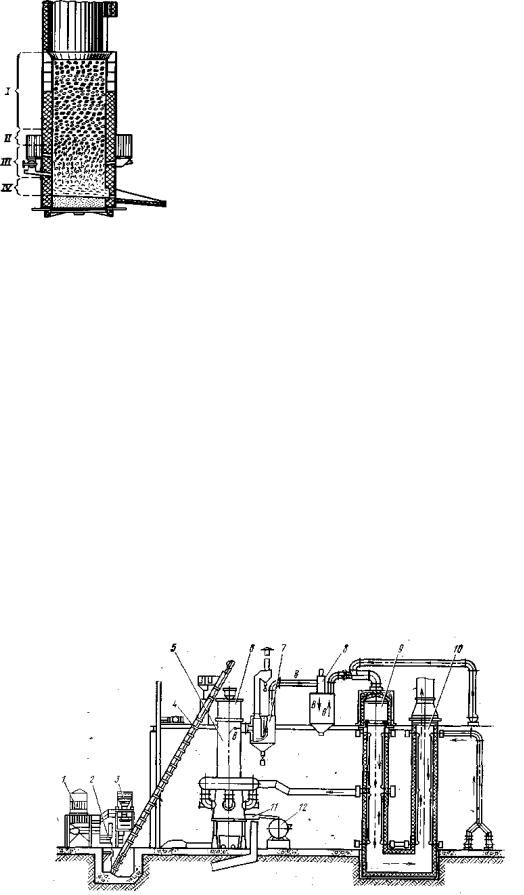
Рис.3 Зоны теплообмена
ввагранке:
І– зона подогрева; ІІ – зона плавления; ІІІ – зона перегрева; ІV – горн
размеров кусков шихты.
Зона ІІ – зона плавления кусков металлической шихты. Продолжительность плавления 5 – 15 мин в зависимости от размеров кусков, состава материала и условий теплообмена. За это время куски успевают опуститься в холостую колошу на 300 – 500 мм, т.е. время плавления определяет размеры зоны плавления.
Зона ІІІ – зона перегрева жидкого чугуна, которая начинается с того места, где образуются капли чугуна и простирается до нижнего ряда фурм. Капли чугуна, стекая по кускам раскаленного кокса и омываясь потоком разогретых до высокой температуры газов, значительно перегреваются. Этому способствует и состав газовой атмосферы, так как в зоне фурм газы содержат свободный кислород, который частично окисляет примеси чугуна и за счет этого дополнительно его
перегревает.
Зона IV – горн вагранки; она находится в нижней части шихты между нижней кромкой нижнего ряда фурм и лещадью. В этой зоне кокс и продукты его горения имеют более низкую температуру из-за недостатка кислорода. Чугун, стекая по кускам кокса и располагаясь между ними (при отсутствии копильника), охлаждается и насыщается углеродом и серой, поэтому желательно, чтобы время пребывания чугуна в горне вагранки было минимальным.
2.2УСТРОЙСТВО И ОСНОВНЫЕ УЗЛЫ ВАГРАНОЧНОГО КОМПЛЕКСА
Внастоящее время конструкции вагранок существенно изменились, созданы сложные ваграночные комплексы. Один из них показан на рис. 4. Управление работой всего ваграночного комплекса осуществляют с центрального пульта.
Рис. 4. Схема установки ваграночного комплекса;
1 – бункерная эстакада; 2 – весовая тележка; 3 – установка для дозирования кокса; 4 – подъемник для шихты; 5 – вагранка; 6 – шлюзовая камера; 7 – пылеосадительная камера; 8 – эжекторный скруббер; 9 – камера дожигания; 10 – радиационный рекуператор; 11 – шлакоотделительный желоб; 12 – копильник
18
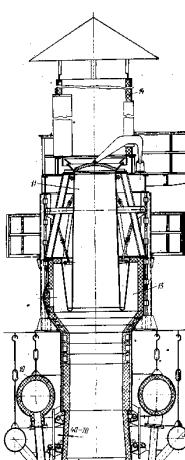
Конструкция вагранки. Основой ваграночного комплекса является вагранка (рис.5). Рассмотрим основные ее узлы.
Опорная часть воспринимает статическую нагрузку от всей вагранки и динамическую от загружаемой шихты. Она со-
|
стоит из фундаментной плиты 1, четырех ко- |
|
лонн 2, опорной рамы 3, подовой плиты 4, |
|
днища 5, механизма 6 открывания и закрыва- |
|
ния днища. Высота опорной части (1,5 – 4 м) |
|
должна быть достаточной для размещения |
|
перед вагранкой миксеров или ковшей для |
|
приема жидкого металла, а также для механи- |
|
зации уборки из-под вагранки отходов после |
|
плавки. Днище вагранки состоит из двух кры- |
|
шек (полуднищ), которые с помощью цапф |
|
подвешиваются на оси, проходящей через |
|
подшипники, закрепленные к подовой плите. |
|
Полуднища закрываются и открываются с по- |
|
мощью гидравлического, электромеханическо- |
|
го или пневматического привода. В закрытом |
|
положении полуднища надежно закрепляются |
|
с помощью клиньев или других запоров. |
|
Шахта вагранки имеет цилиндрический, |
|
конический или сложный («доменный») про- |
|
филь. Корпус шахты по всей высоте или толь- |
|
ко в нижней зоне может охлаждаться водой. |
Рис. 5. Общий вид вагранки: |
Водоохлаждаемая зона за исключением горна, |
1 – фундаментная плита; 2 – колонна; 3 – как правило, не имеет огнеупорной футеровки
опорная рама; 4 – подовая плита; 5 – дни- |
или футеруется только тонким слоем огнеу- |
ще; 6 – механизм открывания и закрывания |
порной массы толщиной 10 – 20 мм или кир- |
днища; 7 – горн вагранки; 8 – фурма; 9 – |
|
шахта вагранки с водяным охлаждением |
пичом «на плашку» – 40 – 70 мм. Неводоохла- |
корпуса шахты; 10 – фурменная коробка; |
ждаемая, как правило, цилиндрическая шахта |
11 – узел загрузки шихты; 12 – металло- |
|
приемник-шлакоотдели-тель для выпуска |
вагранки имеет огнеупорную футеровку тол- |
металла и шлака; 13 – устройство для отбо- |
щиной 180 – 350 мм. Из-за низкой стойкости |
ра ваграночных газов в газоочистку; 14 – |
футеровки длительность работы неводоохла- |
дымовая труба |
|
|
ждаемой вагранки до выбивки для текущего |
ремонта не превышает двух смен.
Вагранка с доменным профилем шахты (с небольшой, конусностью водоохлаждаемого корпуса 9, с вдвинутыми водоохлаждаемыми медными фурмами 8, утолщенной футеровкой горна 7 (см. рис. 5) рассчитана на длительную эксплуатацию без выбивки для специального ремонта футеровки. Доменный профиль способствует равномерному распределению газов по сечению шахты, повышению температуры выплавляемого чугуна и стабильности металлургиче-
19
ских процессов, протекающих во время плавки. Внутренний диаметр шахты определяет производительность вагранки.
Фурменный пояс. Воздух в вагранку подается в фурменную коробку, которая распределяет его между фурмами одного или двух рядов. Фурменная коробка 10 с водоохлаждаемой фурмой 8 состоит из собственно фурмы, патрубка поворотного шибера и соединительных труб. Патрубок фурмы имеет откидную крышку со смотровым окном из огнестойкого стекла. Окно служит для наблюдения за процессом плавки и открывается при прекращении подачи воздуха и при розжиге вагранки. У вагранок с обычным циклом работы фурмы не имеют водяного охлаждения, но также оборудованы откидными смотровыми окнами.
Устройства для выпуска металла и шлака – летки, переходные каналы, сифонные металлоприемники или компрессионные шлакоотделители. Летка для металла служит для периодического выпуска чугуна из вагранки или стационарного копильника. Она представляет собой отверстие диаметром ~30 мм, высверленное в огнеупорном кирпиче. После каждого выпуска металла отверстие забивают «притычкой» из; жирной глины. Шлаковая летка в вагранке без копильника выполняется диаметром 50 – 100 мм (из-за большей, чем у чугуна, вязкости шлака) в огнеупорном кирпиче и располагается ниже фурм на 80 – 100 мм, чтобы шлак нe попадал в фурмы. Для выполнения леток выбирают наиболее качественный кирпич.
Переходные каналы (обычно сечением 115 х 70 мм) между вагранкой и стационарным копильником выкладывают огнеупорным кирпичом марки ШАВ, так как они работают в тяжелых условиях воздействия высоких температур чугуна и шлака.
Сифонные металлоприемники применяют для непрерывной выдачи металла из шахты вагранки в поворотные копильники. Такое устройство позволяет исключить тяжелую и опасную» операцию по открыванию и закрыванию летки. Конструкция сифонного металлоприемника-шлакоотделителя показана на рис. 6, а. Металл и шлак поступают по переходному каналу 1 в металлоприемник 2. Освобожденный от шлака металл проходит под перегородкой, поднимается и стекает по переднему желобу 3. Высоту подъема металла перед желобом рассчитывают так, чтобы предотвратить выбивание газов через переходной канал и избежать подъема шлака в горне до уровня фурм. Вагранки длительного действия оборудуют компрессионными шлакоотделителями (рис. 6, б), являющимися разновидностью сифонных металлоприемников. Применение такого шлакоотделителя позволяет снизить разъедание футеровки горна шлаками, так как шлак в нем не накапливается, а стекает в металлоприемник. Оснащение вагранки двумя такими шлакоотделителями, работающими попеременно через неделю, продлевает работу вагранки без выбивки и текущего ремонта до 3 – 8 недель.
20
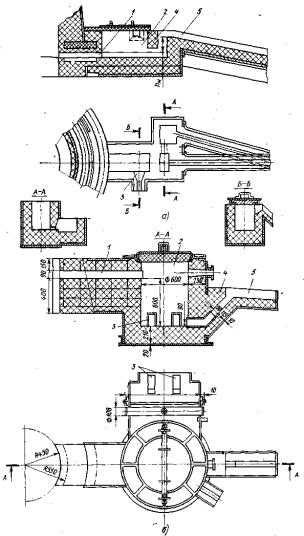
|
Узел загрузки шихты и |
|||||
|
удаления |
ваграночных |
га- |
|||
|
зов располагается в верх- |
|||||
|
ней части шахты вагранки. |
|||||
|
Если ваграночные газы от- |
|||||
|
бираются в систему газо- |
|||||
|
очистки ниже узла загруз- |
|||||
|
ки шихты, как это показа- |
|||||
|
но на рис. 6, то узел за- |
|||||
|
грузки |
шихты |
должен |
|||
|
обеспечить |
полный отбор |
||||
|
газов, не допускать выби- |
|||||
|
вание токсичных ваграноч- |
|||||
|
ных газов. Из печи в атмо- |
|||||
|
сферу цеха |
при загрузке |
||||
|
шихты и исключать воз- |
|||||
|
можность |
проникновения |
||||
|
воздуха в систему газо- |
|||||
|
очистки во избежание об- |
|||||
|
разования |
взрывоопасной |
||||
|
смеси. |
|
|
|
|
|
|
Ваграночные |
газы |
||||
|
становятся |
взрывоопасны- |
||||
|
ми при |
концентрации |
в |
|||
|
них от 5 до 10% кислорода |
|||||
|
и наличии 12 – 72% окиси |
|||||
Рис. 6 Сифонный (а) и компрессионный (б) металлоприемник-шлако- |
углерода СО. |
|
|
|||
С повышением темпе- |
||||||
отделитель: |
||||||
1 – переходной канал; 2 – металлоприемник; 3 – желоб для шлака; 4 – |
ратуры газов взрывоопас- |
|||||
перегородка для шлака; 5 – желоб для металла |
ность газов увеличивается |
|||||
|
и при 600 °С происходит |
самовоспламенение при любых концентрациях СО и О2. Скорость распространения взрывной волны равна примерно 1 м/с. Поэтому скорость движения газов через газоочистительную систему должна быть всегда больше 1 м/с. Для исключения подсоса воздуха в системе не должно быть разряжения. Конструктивно это решается применением шлюзовой камеры с двумя попеременно открываемыми крышками (рис. 7) или устройством дополнительной шахты над узлом отбора газов высотой 3,5 – 4 м до загрузочного окна (см. рис. 5). Сопротивление столба шихтовых материалов, расположенных над узлом отбора газов, и поддержание давления в узле отбора газов ±10 мм вод. ст. препятствуют выбиванию газов в цех или подсосу воздуха в систему газоочистки. При этом уровень загрузки шихты должен строго контролироваться уровнемером, автоматически подающим команду на загрузку вагранки при опускании столба шихты в
21

печи. В конце плавки, после последней завалки, когда слой шихты снижается, вагранку закрывают специальными крышками, препятствующими проникновению в вагранку атмосферного воздуха.
В некоторых конструкциях вагранок отбор газов на газоочистку производится выше узла загрузки шихты. В этой случае стараются максимально уменьшить размеры загрузочного окна. Если это невозможно, то следует открывать окно только на момент загрузки шихты. Чем больше загрузочное окно, тем больше через него подсасывается воздуха и тем большее количество газов приходится пропускать через систему газоочистки, при этом увеличиваются стоимость сооружения и эксплуатационные расходы. Кроме того, при разбавлении ваграночных газов
большим количеством воздуха затруднено дожигание СО, содержащегося в ваграночных газах. Размеры загрузочного окна вагранки могут быть различны в зависимости от способа загрузки шихты. Они максимальны при, центральной бадьевой загрузке с помощью наклонного подъемника, шарнирного крана или монорельсовой тележки и минимальны при загрузке с помощью вибрационных питателей.
Верхняя часть шахты под загрузочным окном выполняется в виде защитной воронки из чугунных кирпичей, предохраняющих футеровку шахты от ударов кусков шихты при загрузке.
Рис. 8 Стационарный копильник для жидкого чугуна
Конструкция и размеры дымовой трубы должны обеспечить надежное удаление из цеха всех ваграночных газов, способствовать вентиляции колошниковой площадки вагра-ночного отделения и не допускать выбивания ваграночных газов.
Копильники для жидкого чугуна служат для накопления металла, усреднения его химического состава и периодической выд ачи на участок заливки форм. По конструкции копильники поразделяются на стационарные и поворотные. Стационарные копильники применяют в цехах крупного и тяжелого литья, где выдача металла на заливку
22
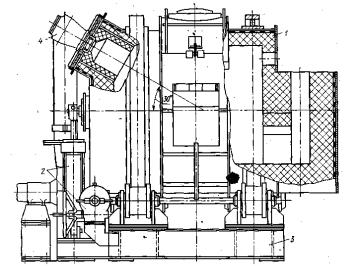
осуществляется не чаще 3 – 4 раз в час. Стационарный копильник (рис. 8) состоит из футерованного корпуса 1, передней дверцы 2 с леткой и желобом для жидкого чугуна, смотрового окна 3, крышки 4, шлаковой летки 5. Преимущества стационарных копильников: небольшие потери температуры металла, возможность снижения содержания в чугуне углерода и серы за счет снижения высоты горна вагранки, высокая стойкость футеровки горна вагранки (ее работа с «сухим горном»).
|
|
Недостатком |
стационарного |
|||||
|
копильника |
является |
применение |
|||||
|
тяжелой и опасной ручной опера- |
|||||||
|
ции открывания и закрывания ме- |
|||||||
|
таллической |
и шлаковой |
леток. |
|||||
|
Поэтому в механизированных це- |
|||||||
|
хах мелкого и среднего литья при- |
|||||||
|
меняют |
поворотные копильники- |
||||||
|
миксеры, |
оборудованные в |
целях |
|||||
|
поддержания постоянной темпера- |
|||||||
|
туры чугуна устройствами для га- |
|||||||
|
зового или индукционного обогре- |
|||||||
|
ва металла. На рис.9 показан пово- |
|||||||
|
ротный копильник с газовым обо- |
|||||||
Рис. 9. Поворотный копильник |
гревом. Он состоит из футерован- |
|||||||
ного корпуса |
1, механизма поворо- |
|||||||
1 – футерованный корпус; 2 – механизм поворота копиль- |
||||||||
ника; 3 – опорная конструкция; 4 – газовая горелка |
та |
копильника |
2, |
опорной |
конструкции 3, газовой горелки 4.
Система очистки ваграночных газов от пыли. Простейшими уловителями пыли из ваграночных газов являются сухие цилиндрические и камерные искрогасители, устанавливаемые на трубах вагранок. Оседание пыли в этих аппаратах происходит за счет снижения скорости газовых потоков и многократных резких поворотов потока на 90 и 180°. В таких пылеуловителях осаждается только 40% ваграночной пыли, наиболее крупной. Более эффективны мокрые пылеуловители, когда в искрогаситель подается мелкораспыленный поток воды, промывающий газы. Однако и в этом случае осаждается не более 85% пыли; остаточная запыленность составляет 0,3 – 0,6 г/м3. Как сухие, так и мокрые искрогасители устанавливают на открытых вагранках, где движение газов через пылеуловитель осуществляется за счет естественной тяги трубы.
Повысить эффективность мокрых пылеуловителей открытых вагранок можно увеличением высоты дымовой трубы и применением эжекторной тяги, как это показано на рис. 10. Такой пылеуловитель устанавливают на трубу вагранки. Он состоит из металлического корпуса 1, водоохлаждаемого зонта 2, в который вода подается через опорные трубы 3, а вытекает через верхнее отверстие 4. Газы из трубы 7 вагранки проходят по кольцевым зазорам 8, промываются водой, подаваемой через форсунки 9 и стекающей с крышки 10 зонта. Движение
23

газов через пылеуловитель осуществляется за счет разряжения, создаваемого эжектором 6, через который от специального вентилятора продувается в трубу пылеуловителя 5 воздух с высокой скоростью. В такой установке выброс пыли в атмосферу снижается до 1 кг на 1 т выплавляемого чугуна.
Рис. 10. Мокрый пылеуловитель с эжекторной тягой:
1 – корпус; 2 – водоохлаждаемый зонт; 3
– водоохлаждаемые опорные трубы; 4 – выпускное отверстие; 5 – труба пылеуловителя; 6 – воздушный эжектор; 7 – труба вагранки; 8 – кольцевые зазоры для прохода газов; 9 – водяные форсунки; 10 – крышка зонта
Однако высокоэффективную очистку ваграночных газов от пыли могут обеспечить только многоступенчатые системы, которыми оснащены вагранки закрытого типа, т.е. такие конструкции вагранок, в которых закрыт свободный выход газов в атмосферу и их перемещение через систему газоочистки и аппараты утилизации теплоты осуществляется различными тягодувными средствами.
Вмногоступенчатых газоочистках (см. рис.
4)предварительная очистка газов осуществляется сухим или мокрым способом в инерционных
пылеосадителях или в циклонах и скрубберах различной конструкции. Тонкая (окончательная) очистка возможна в тканевых фильтрах, в электростатических пылеуловителях, в аппаратах типа дезинтегратора, в эжекционных скрубберах и в скоростных пылеуловителях с трубами Вентури.
Принцип работы скоростных пылеуловителей с трубами Вентури заключается в подаче потока воды со скоростью 180 – 200 м/с в поток газа. За счет большой разности скоростей потоков происходит хорошее перемешивание газов с каплями воды и осаждение мельчайших частиц пыли на каплях воды (коагуляция пыли), после чего пыль хорошо улавливается с помощью
обычных инерционных пылеуловителей типа прямоточных скрубберов или циклонов. При перепаде давлений в трубе Вентури более 1500 мм вод. ст. (147 гПа) КПД пылеуловителя достигает 98 – 99%, а выброс пыли снижается до 0,1 кг на 1 т выплавляемого чугуна
Всистеме газоочистки с дезинтегратором коагуляция пыли осуществляется
врезультате механического перемешивания газов с водой, подаваемой через вал ротора дезинтегратора. Газы поступают предварительно охлажденными и
очищенными от крупных частиц в мокром скруббере башенного типа. Укрупненная в дезинтеграторе пыль осаждается в каплеосадителе. Дезинтегратор является одновременно коагулятором пыли и газодувной машиной, обеспечивающей перемещение газов через систему газоочистки.
В системе газоочистки с эжекторным скруббером коагуляция частиц пыли и перемещение газов через газоочистку осуществляется с помощью форсунки, выбрасывающей струю воды с высокой скоростью в смесительную камеру в направлении перемещения ваграночных газов. Струя воды эжектирует поток газов, и за счет большой разности скоростей воды и газа происходит их переме-
24
шивание и осаждение частиц пыли из газового потока на каплях воды. Капли воды осаждаются в инерционном каплеосадителе.
25