
- •ПЛАВКА ЧУГУНА В ВАГРАНКАХ
- •Содержание
- •1. Материалы, применяемые при плавке в вагранке
- •1.1 Огнеупорные матрериалы
- •1.2 Металлическая шихта
- •1.3 Ваграночное топливо
- •1.4 Флюсы
- •Вопросы для самоконтроля
- •2. Основное и вспомогательное оборудование ваграночного комплекса
- •2.1 Принцип работы вгранки
- •2.2 Устройство и основные узлы ваграночного комплекса
- •Вопросы для самоконтроля
- •3. Технологический процесс плавки чугуна в вагранке
- •3.1 Тепловые и металлургические процессы плавки
- •3.2.Технология плавки в коксовых вагранках
- •3.3 Расчет шихты
- •3.4 Экспресс-контроль чугуна по ходу плавки
- •Вопросы для самоконтроля
- •4. Расчет вагранки
- •4.1 Расчет материального и теплового баланса вагранки
- •4.2 Расчет размеров вагранки
- •Приложение 2
- •Приложение 3
- •Приложение 4
- •Приложение 5
- •Приложение 6
- •Приложение 7
- •Список литературы
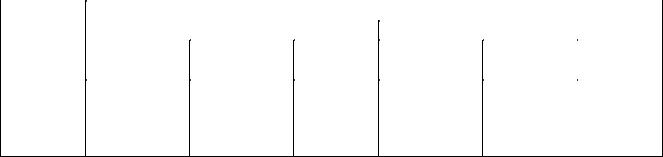
3.Технологический процесс плавки чугуна в вагранке
3.1ТЕПЛОВЫЕ И МЕТАЛЛУРГИЧЕСКИЕ ПРОЦЕССЫ ПЛАВКИ
Тепловые процессы при плавке в вагранке определяются горением топлива, теплообменом между топливом, продуктами его сгорания и шихтовыми материалами, а также химическим взаимодействием между металлическими компонентами, шлаком и газовой фазой. В качестве топлива в коксовых вагранках, кроме кокса, иногда используются различные виды коксобрикетов, термоантрацит и литейный антрацит. Основной горючей составляющей в них является углерод, горение которого может протекать по следующим реакциям:
С+О2 = СО2 +94060 кал |
(393800 Дж); |
(3.1) |
С + 0,5О2 = СО + 26420 |
кал (110600 Дж); |
(3.2) |
СО + 0,5О2 = СО2 + 67640 кал (283200 Дж); |
(3.3) |
|
СО2 + С = 2СО – 41220 кал (172600 Дж). |
(3.4) |
Содержание СО и СО2 в отходящих газах колеблется в широких пределах в зависимости от качества и расхода кокса, температуры, количества дутья и ряда других причин (табл. 3.1).
Таблица 3.1
Состав отходящих газов коксовой вагранки
Расход |
|
|
|
|
Состав отходящих газов, % |
|
|
||
|
при холодном дутье |
при горячем дутье |
|||||||
кокса, % |
СО |
|
CO2 |
|
CO2·100 |
СО |
CO2 |
CO2·100 |
|
|
|
|
СО + СО2 |
СО + СО2 |
|||||
|
|
|
|
|
|
|
|
||
8 |
– |
|
|
– |
|
– |
8,0 – 12,0 |
12,5 – 15,0 |
50 – 65 |
10 |
8,0 – 12,0 |
|
12,5 |
– 15,0 |
|
50 – 65 |
10,0 – 16,0 |
10,0 – 14,0 |
39 – 60 |
12 |
10,0 – 14,0 |
|
11,5 |
– 14,0 |
|
46 – 60 |
14,0 – 20,0 |
7,5 – 11,0 |
27 – 44 |
14 |
12,0 – 18,0 |
|
9,0 – 12,5 |
|
33 – 50 |
16,0 – 24,0 |
5,5 – 10,0 |
18 – 39 |
Основным продуктом реакций в кислородной зоне является СО2. В редукционной зоне преимущественно идет реакция (3.4). Высота кислородной зоны при холодном дутье равна 6 – 8 диаметрам кусков кокса, а при подогреве воздуха до 500 °С – 4 – 6 диаметрам. Изменение расхода дутья не оказывает заметного влияния на высоту зоны. Температурный режим иллюстрируется рис.11.
В связи с интенсивным отбором тепла от газов на плавление и перегрев чугуна реакция восстановления СО2 идет не полностью и практически прекращается при температуре газов около 1000°С в так называемой третьей, подготовительной зоне.
27
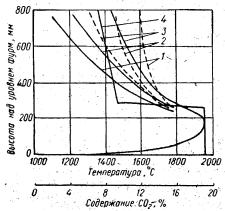
В соответствии с теплотехническими процессами вся шахта вагранки может быть разделена на зоны: нагрева шихты до температуры плавления; плавления; перегрева жидкого металла; охлаждения металла (горн). Как показали исследования, температура металла находится в прямой зависимости от высоты расположения h зоны плавления и при подогреве дутья, например до 450 °С, рассчитывается по
Рис. 11 Изменение температуры (—) и содержа- |
уравнению |
(3.5) |
|
ния CO2 ( – – –) в газах по высоте вагранки (тем- |
tМе = 1380 + 0,215 (h – 200), |
||
пература дутья 450°С): |
которое справедливо для h = 200 ÷ 600 мм, |
||
1 |
– расход кокса 10%; 2 – расход кокса 14%; |
||
3 |
– слой горящего кокса без металлозавалки; |
причем h зависит от условий теплообмена |
|
4 |
– температура поверхности горящего кокса |
в зоне нагрева и интенсивности снижения |
|
|
|
температуры газов в нижней |
части ва- |
гранки главным образом за счет реакции восстановления СО2.
Из факторов, влияющих на температуру металла (tМе) при плавке в вагранке, основными являются: количество и температура подогрева дутья, степень обогащения его кислородом, расход и качество кокса, количество стального скрапа в шихте, угар элементов и др. Например, подогрев дутья на каждые 100°С или обогащение его кислородом на 1% повышает температуру в кислородной зоне
на 70 – 75°С, а tМе на
15 – 25°С. Увеличение расхода кокса с 8 – 10% до 12 – 14% повышает tМе на 60
– 100°. Дальнейшее увеличение расхода кокса оказывает заметное влияние на tМе только тогда, когда из-за недостаточного объема шахты вагранки, крупногабаритной шихты или чрезмерного форсирования дутья нагрев шихты до температуры плавления происходит в условиях незавершенного теплообмена. При увеличение расхода дутья уровень начала расплавления поднимается, а уровень его окончания – снижается; максимальный нагрев чугуна обеспечивается в кислородной зоне, поэтому полное расплавление шихты должно заканчиваться на возможно более высоком уровне, во всяком случае выше границы между редукционной и кислородной зонами. Такое расположение зоны плавления уменьшает угар элементов, получающий наибольшее развитие в кислородной зоне. Однако при этом нужно учитывать, что угар 1% Si повышает tМе на 220°, а угар 1% Mn – на 65°.
Оптимальный удельный расход воздуха, обеспечивающий максимальную высоту среднего уровня зоны плавления и, соответственно, максимальную тем-
пературу металла, зависит от приведенной толщины кусков шихты
28
æ |
|
|
|
Объем куска |
ö |
|
ç |
R |
пр |
= 4 |
|
÷ |
: |
|
||||||
ç |
|
|
|
÷ |
|
|
è |
|
|
|
Площадь поверхности .куска ø |
|
Rпр. мм. |
100 |
150 |
200 |
250 |
300 |
Удельный расход воз- |
140–150 |
130–140 |
120–130 |
100–110 |
90–100 |
духа в зоне плавления, |
нм3/(м2·мин)
Для того чтобы уменьшить высоту зоны плавления и сохранить преимущества от высокого удельного расхода дутья, полезно применять вагранки с доменным профилем шахты. При таком профиле зона плавления находится в наиболее широкой части шахты – в распаре, а зона горения – в наиболее узкой части – в горновой, и поэтому высота зоны плавления при иных равных условиях будет минимальной.
Металлургические процессы заключаются в диссоциации известняка, образовании шлака, угаре элементов и других окислительно-восстановительных реакциях между газовой фазой, шихтой и шлаком.
Содержание влаги в шихте невелико (1,5 – 2,5% – в известняке, 3 – 6% – в коксе) и испарение ее происходит в самом верхнем слое шахты ва-
гранки. В этой же зоне происходит выделение из кокса летучих веществ, составляющих обычно не более 1% от массы кокса. Интенсивное разложение известняка происходит при t = 900÷ 1000°С, когда упругость его диссоциации, увеличивающаяся с подъемом температуры, превышает парциальное давление CO2. В этих условиях образующаяся при разложении известняка CO2 легко удаляется из его внутренних пор, увеличивая реакционную поверхность и ускоряя тем самым процесс диссоциации. Известняк подается в вагранки для образования жидкотекучего шлака из посторонних продуктов, поступающих вместе с шихтой, из сплавившейся футеровки, золы кокса, продуктов окисления шихты. Состав шлака определяет его основные свойства: температуру плавления, вязкость и основность. Наиболее тугоплавкими являются окислы SiO2 (tпл = 1625°С), СаО (tпл = 2370°С), Al2O3 (tпл = 2060°С). Образование двойных и тройных соединений этих окислов, особенно эвтектического состава, понижает tпл шлака (например, эвтектика, состоящая из 62% SiO2, 14,75% Al2O3 и 23,75% СаО, имеет tпл = 1155°С).
Состав и свойства ваграночного шлака оказывают большое влияние на характер плавки и свойства полученного металла. Шлак в вагранке образуется в результате угара элементов чугуна (1 – 2% массы металла, из них кремний угарает на 10 – 20%, марганец на 10 – 30%, железо на 0,25 – 1,5%), оплавления футеровки (0,4 – 3%), прилипания к шихте песка и формовочной смеси (2%), образования золы топлива (1 – 2%), ввода флюсов в целях понижения вязкости шлаков (2,5 – 4%), флюсы полностью переходят в шлак. Таким образом, шлака образуется 6 – 8% массы жидкого чугуна. Средний состав шлака для кислого процесса следующий, %: 40 – 60 кремнезема, 20 – 35 извести; 2 – 20 глинозема; 1 – 5 маг-
29

незии; 0,5 – 10 закиси железа; 1 – 5 закиси марганца; 0,1 – 0,5 оксидов фосфора; 0,05 – 0,03 серы; 0,2 – 0,3 чугуна в виде запутавшихся капель.
Три составляющие – кремнезем, оксид кальция и глинозем – дают 80 – 90% всей массы шлака. Их соотношение определяет температуру плавления шлака и его жидкотекучесть. Шлак должен иметь высокую жидкотекучесть, обеспечивающую его легкое отделение от чугуна, стекание по стенкам шахты без образования настылей, дополнительное поглощение серы из чугуна и легкость удаления через шлаковую летку. Вязкость шлака снижается, а жидкотекучесть повышается при замене части СаО на MgO с повышением содержания в шлаке FeO и МnО. Однако повышенное количество FeO и МnО свидетельствует о холодном ходе плавки и повышенной окисленности чугуна Шлак становится темным, почти черным, вместо зеленого. Оксиды FeO и МnО сильно разрушают футеровку печи.
Для получения шлака с наибольшей жидкотекучестью рекомендуется, чтобы отношение кремнезема к глинозему в нем было 6 – 8, а отношение оксида кальция к оксиду магния 2. Хорошо понижает вязкость ишака плавиковый шпат CaF2, который ускоряет реакции обмена между шлаком и чугуном, увеличивает растворимость серы в шлаке. Однако плавиковый шпат сильно разъедает футеровку печи и дорого стоит.
Состав шлака надо подбирать таким образом, чтобы он меньше взаимодействовал с основными составляющими футеровки печи, последняя для уменьшения разрушения должна быть по возможности менее пористой. Для шамотной футеровки желательно иметь шлак по составу, близкий шамоту, %: 40 – 48 SiO2; 10 – 15 А12О3; 25 – 30 СаО; до 8 FeO; 5 – 8 МnО; 3 – 5 MgO. Для вагранки, футерованной основными материалами, желательно иметь шлак следующего состава, %: 25 – 30 SiО2; 40 – 50 СаО; 2 – 20 А1203; 1 – 5 MgO; 0,5 – 3 FeO; 1 – 3 МnО; 0,5 – 1,0 P2O5; 0,5 – 1,08 S.
Характерные составы шлаков приведены в табл. 3.2
Процесс
Кислый
Основной
|
Составы ваграночных шлаков |
|
Таблица 3.2 |
|||||||
|
|
|
|
|
||||||
|
|
|
|
O |
|
|
|
|
Основность |
|
|
|
Мольная доля составных частей , % |
|
|
|
|||||
|
|
|
|
3 |
|
|
|
|
|
|
SiO |
CaO |
Al |
MgO |
FeO+Fe |
MnO |
|
P |
S |
|
|
|
СаО+MgO |
|
||||||||
|
|
3 |
|
2 |
|
|
5 |
|
|
|
2 |
|
O |
|
|
|
|
O |
|
|
|
|
|
2 |
|
|
|
|
2 |
|
|
|
|
|
|
|
|
|
|
|
|
|
|
|
|
|
|
|
|
|
|
|
2 |
|
|
|
|
|
|
|
|
|
|
SiO |
|
40–60 |
20–35 |
5–20 |
1–5 |
1–10 |
1–5 |
|
0,1–0,5 |
0,05–0,3 |
0,4–0,9 |
|
25–35 |
40–50 |
5–20 |
1–5 |
0,5–0,3 |
1–3 |
|
0,5–1,0 |
0,5–1,0 |
1,2–2,0 |
30
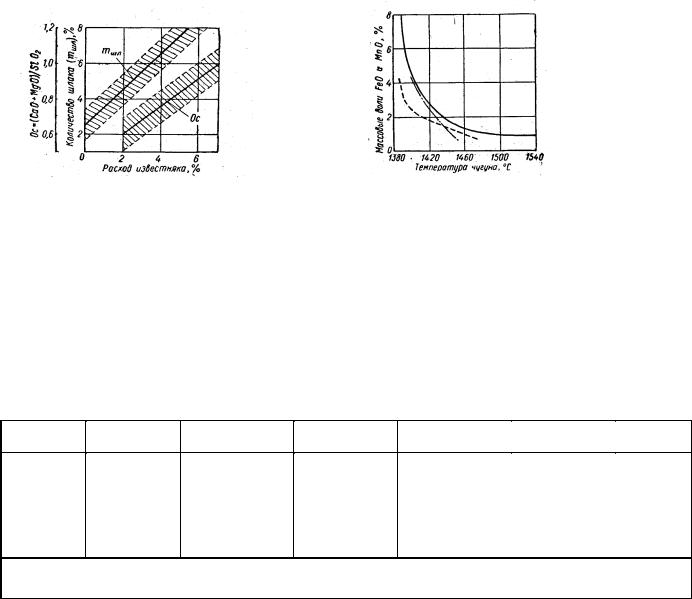
Наиболее подвижными являются шлаки состава: 45 – 50% СаО; 35 – 40% SiO2; 10 – 15% Al2O3. Уменьшение содержания СаО до 35% незначительно сказывается на вязкости шлака, а увеличение его содержания свыше 50% приводит к резкому ее повышению; окислы FеО, MnO, MgO в обычных концентрациях, наоборот, значительно снижают вязкость шлака, чему также способствует присадка в качестве флюса, кроме известняка, плавикового шпата. Количество и основность шлака определяются, главным образом, расходом известняка (рис. 12). В футерованной вагранке масса шлака может быть определена по уравнению:
mшл = 0,942 + 1,016СаСО3 + О,336МеОшл + АК/100, |
(3.6) |
где МеОшл – содержание окислов Fe и Мn в шлаке, %; А – содержание золы в коксе. %; К – расход кокса, %;
Рис. 12 Влияние расхода известняка на количество образующегося в вагранке шлака (mшл) и его основность (Ос).
Рис. 13 Влияние температуры чугуна на содержание в шлаке FeO и МnО ( –— – FеО; — — — МnО при содержании Мn в металле <0,7%; —·—·–МnО при содержании Мn в металле >0,7%).
С повышением tМе массовая доля FeO и МnО в шлаке резко снижается (рис. 13). Количество шлака, его основность и содержание в нем FeO и МnО наряду с расходом кокса, температурным и шлаковым режимом плавки оказывают большое влияние на угар элементов (табл. 3.3).
Таблица 3.3
Угар элементов при плавке в коксовой вагранке, %.
Дутье |
Процесс |
|
С |
Si |
Мn |
|
S |
P |
|
|
|
|
|
|
|
|
|
Холодное |
Кислый |
(+10) |
÷ (+50) |
(–10) ÷ (–25) |
(–10) ÷ (–30) |
(+40) |
÷ (+100) |
0 |
Горячее |
» |
(+20) |
÷ (+300) |
(–10) ÷ (+20) |
(–10) ÷ (–20) |
(+10) |
÷ (+50) |
0 |
» |
Основной |
(+30) |
÷ (+360) |
(–15) ÷ (–20) |
(–5) ÷ (–15) |
(–20) ÷ (–50) |
(0) ÷ (–10) |
|
|
|
|
|
|
|
|
|
|
Примечание.
Знак "–" – угар; "+" – пригар.
31