
- •ИННОВАЦИОННАЯ ОРГАНИЗАЦИОННАЯ КУЛЬТУРА КАК ФАКТОР ПОВЫШЕНИЯ ИННОВАЦИОННОЙ ВОСПРИИМЧИВОСТИ
- •ИНТЕГРАЦИЯ ПЕРИФЕРИЙНЫХ УСТРОЙСТВ В СЧПУ ДЛЯ ПОВЫШЕНИЯ ПРОИЗВОДИТЕЛЬНОСТИ
- •ИССЛЕДОВАНИЕ ПРОЦЕССОВ ТЕПЛОМАССООБМЕНА В РАЗНОТЕМПЕРАТУРНОМ КОНДЕНСАЦИОННОМ ФИЛЬТРЕ
- •КОММУТАЦИОННЫЙ АППАРАТ СЕНСОРНОГО (ЁМКОСТНОГО) УПРАВЛЕНИЯ С ФУНКЦИЕЙ РЕГУЛИРОВАНИЯ ПЕРЕМЕННОГО НАПРЯЖЕНИЯ НА НАГРУЗКЕ
- •КОМПЛЕКС МОДЕЛИРОВАНИЯ ИНФОРМАЦИОННЫХ ЭПИДЕМИЙ В БЕЗМАСШТАБНЫХ СЕТЯХ
- •МЕТОДИКА ИЗГОТОВЛЕНИЯ ТРЕХСЛОЙНЫХ СОТОВЫХ ПАНЕЛЕЙ
- •МНОГОМЕТОДНАЯ ПОДСИСТЕМА ПОДДЕРЖКИ ПРИНЯТИЯ РЕШЕНИЙ НА ОСНОВЕ ПАРАЛЛЕЛЬНЫХ ГЕНЕТИЧЕСКИХ АЛГОРИТМОВ
- •МОДЕЛИРОВАНИЕ СИСТЕМЫ ПОЖАРНОЙ БЕЗОПАСНОСТИ ТЕХНОЛОГИЧЕСКОЙ ЛИНИИ ТЭП-50 НА ОАО «ВОРОНЕЖСИНТЕЗКАУЧУК»
- •НАНОТЕХНОЛОГИИ ДЛЯ ПОВЫШЕНИЯ ИЗНОСОСТОЙКОСТИ РАБОЧИХ ПОВЕРХНОСТЕЙ ИЗДЕЛИЙ
- •ОБЕСПЕЧЕНИЕ КАЧЕСТВА НАУКОЕМКОЙ ПРОДУКЦИИ И ИННОВАЦИОННАЯ ДЕЯТЕЛЬНОСТЬ
- •ОПТИМИЗАЦИЯ ПРОИЗВОДСТВЕННОГО ПРОЦЕССА НА ОСНОВЕ ТЕХНОЛОГИЙ БЕРЕЖЛИВОГО ПРОИЗВОДСТВА
- •ОПТИМИЗАЦИЯ СОСТАВА КЕРАМИЧЕСКИХ ОБОЛОЧЕК ДЛЯ ЛИТЬЯ ПО ВЫПЛАВЛЯЕМЫМ МОДЕЛЯМ
- •ПЛАЗМЕННЫЕ РАКЕТНЫЕ ДВИГАТЕЛИ – РЕВОЛЮЦИЯ В КОСМИЧЕСКИХ ПОЛЕТАХ
- •ПОРТАТИВНОЕ ЦИФРОВОЕ УСТРОЙСТВО, ПРЕДНАЗНАЧЕННОЕ ДЛЯ ОТОБРАЖЕНИЯ ТЕКСТОВОЙ И ГРАФИЧЕСКОЙ ИНФОРМАЦИИ, ПРЕДСТАВЛЕННОЙ В ЭЛЕКТРОННОМ ВИДЕ
- •ПОСТРОЕНИЕ ПРОГНОСТИЧЕСКИХ МОДЕЛЕЙ РАСПРОСТРАНЕНИЯ НЕФТИ
- •ПРИМЕНЕНИЕ КЛАСТЕРНОГО АНАЛИЗА ДЛЯ ОБРАБОТКИ ОШИБОЧНЫХ СРАБАТЫВАНИЙ С УЧЁТОМ ПРИОРИТЕТОВ ПАРАМЕТРОВ
- •ПРИМЕНЕНИЕ ТЕХНОЛОГИЙ СЕМАНТИЧЕСКОЙ ПАУТИНЫ ДЛЯ ПРОЕКТИРОВАНИЯ ОНТОЛОГИЙ И СИСТЕМ УПРАВЛЕНИЯ СОДЕРЖИМЫМ НА ИХ ОСНОВЕ
- •ПРОГРАММНЫЙ КОМПЛЕКС «NETEPIDEMIC» ДЛЯ РИСК-АНАЛИЗА ПРОЦЕССОВ РАСПРОСТРАНЕНИЯ ДЕСТРУКТИВНОГО КОНТЕНТА В НЕОДНОРОДНЫХ СЕТЕВЫХ СТРУКТУРАХ
- •ПРОГРАММНЫЙ КОМПЛЕКС РИСК-АНАЛИЗА РАСПРЕДЕЛЕННЫХ ИНФОРМАЦИОННЫХ СИСТЕМ
- •РАЗВИТИЕ СПОСОБОВ ТОЧНОЙ ШТАМПОВКИ
- •РАЗРАБОТКА ГИБРИДНЫХ ФУНКЦИОНАЛЬНЫХ МАТЕРИАЛОВ НА ОСНОВЕ НИКЕЛЯ
- •РАЗРАБОТКА МОДЕЛЕЙ И АЛГОРИТМОВ ИНТЕЛЛЕКТУАЛЬНОГО АНАЛИЗА КЛИЕНТСКИХ СРЕД НА ОСНОВЕ НЕЧЁТКИХ НЕЙРОННЫХ СЕТЕЙ
- •РАЗРАБОТКА СИСТЕМЫ ПЛАНИРОВАНИЯ СЕТИ И ОБЕСПЕЧЕНИЯ ДОСТУПА К ВЫСОКОСКОРОСТНОМУ СОЕДИНЕНИЮ КОНЕЧНОГО ПОЛЬЗОВАТЕЛЯ
- •РАЗРАБОТКА ЭЛЕМЕНТОВ ГИБРИДНОЙ СИСТЕМЫ ЛОКАЛЬНОЙ ТЕРМОСТАБИЛИЗАЦИИ ЭЛЕКТРОННЫХ МОДУЛЕЙ НА ОСНОВЕ МИКРОКАНАЛЬНЫХ ТЕПЛООБМЕННИКОВ И ТЕРМОЭЛЕКТРИЧЕСКИХ ПРЕОБРАЗОВАТЕЛЕЙ
- •СИСТЕМА АВТОМАТИЗИРОВАННОГО ПЛАНИРОВАНИЯ, ОПТИМИЗАЦИИ И УЧЕТА ШИРОКОПОЛОСНОГО РАДИОДОСТУПА И ЦИФРОВОГО ТВ
- •СОВРЕМЕННЫЕ ТЕХНОЛОГИИ, ИСПОЛЬЗУЮЩИЕСЯ В ПРОИЗВОДСТВЕ РАКЕТНО-КОСМИЧЕСКОЙ ТЕХНИКИ
- •СТРУКТУРА ЗОНДА СКАНЕРА БЛИЖНЕГО ПОЛЯ
- •ТЕХНИЧЕСКАЯ СИСТЕМА ОБЕСПЕЧЕНИЯ ЭКОЛОГИЧЕСКОЙ БЕЗОПАСНОСТИ НА ТЕПЛОВЫХ ЭНЕРГЕТИЧЕСКИХ УСТАНОВКАХ
- •ТЕХНОЛОГИИ 3D-ПЕЧАТИ В РАКЕТОСТРОЕНИИ
- •УСТРОЙСТВА ДЛЯ ОБРАБОТКИ ЗВУКА МУЗЫКАЛЬНЫХ ИНСТРУМЕНТОВ В РЕЖИМЕ РЕАЛЬНОГО ВРЕМЕНИ
- •ЭЛЕКТРИЧЕСКИЕ РАКЕТНЫЕ ДВИГАТЕЛИ – ДВИГАТЕЛИ БУДУЩЕГО
- •ЭНЕРГОСБЕРЕЖЕНИЕ В РАЗДЕЛИТЕЛЬНЫХ ОПЕРАЦИЯХ
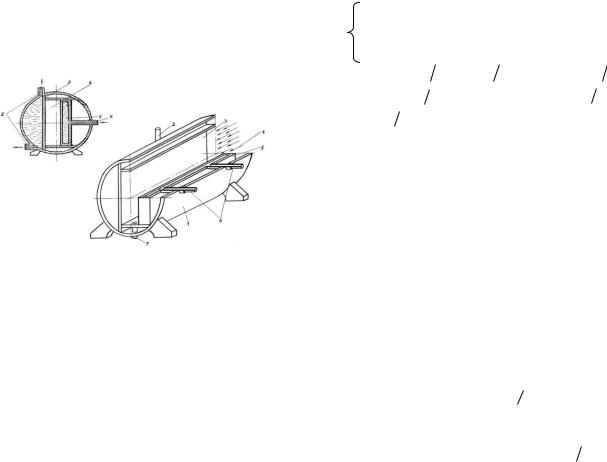
УДК 536.248.2
ИССЛЕДОВАНИЕ ПРОЦЕССОВ ТЕПЛОМАССООБМЕНА В РАЗНОТЕМПЕРАТУРНОМ КОНДЕНСАЦИОННОМ ФИЛЬТРЕ
Аспирант кафедры ТПТЭ Зварыкин И.И. Руководитель: канд. техн. наук, доцент П.А. Солженикин
В настоящей работе основное внимание уделено вопросам очистки газовых потоков от посторонних включений и разработке аппаратов для их более эффективной очистки. Рассматривается установка для очистки газовых потоков, главным узлом которой является разнотмепературный конденсационный фильтр
Разнотемпературный конденсационный фильтр имеет газовый тракт прямоугольного сечения, противоположные стенки которого имеют разную температуру (рис. 1).
Рис. 1 Разнотемпературный конденсационный фильтр 1–корпус; 2 – подвод и отвод горячей воды; 3 – горячая стенка; 4 – газовый поток в канале; 5 – полость холодной воды; 6 – трубопроводы холодной воды; 7 –слив конденсата.
При проведении термического анализа рассматривалась бинарная газовая смесь, которая поступает в плоский канал длиной H и шириной h со скоростью и температурой tвх, причем температура горячей th и холодной t0 стенок поддерживаются постоянными.
Уравнение переноса теплоты:
t |
|
t |
|
t |
|
|
2t |
|
2t |
|
|||
|
|
|
u |
|
a |
|
|
|
|
|
|
||
|
|
|
|
2 |
|
2 |
|||||||
τ |
|
x |
|
y |
|
|
x |
|
y |
|
|||
|
|
|
|
|
|
|
|
||||||
|
|
h<<H ; |
|
u |
≈ 0 ; |
τ → ∞ , |
|||||||
|
|
|
|
|
|
|
|
|
|
|
|
|
|
где τ, x, y – текущие время и координаты; t – температура;
, u – компоненты скорости потока в направлении осей ox и oy соответственно;
а – температуропроводность бинарной смеси. Упрощенная постановка задачи:
|
|
|
t |
|
2t |
|
; |
|
|
(1) |
|
|
|
x a |
y 2 |
|
|
||||||
|
|
|
|
|
|||||||
t 0, y t |
вх |
; |
t x, h t |
h |
; |
t x,0 t |
0 |
. |
|||
|
|
|
|
|
|
|
|
Безразмерная форма записи:
T X ,Y |
|
|
1 2T X ,Y |
|
|
|
|
|
|||||||||||||||||||||||||||||
|
|
X |
|
|
|
Pe |
|
|
|
|
Y |
|
2 |
|
|
|
|
|
|
|
|
|
|
|
|||||||||||||
|
|
|
|
|
|
|
|
|
|
|
|
|
|
|
|
|
|
|
|
|
|
||||||||||||||||
T 0,Y |
0 ; |
|
T |
X ,1 ξ1 ; |
T X ,0 ξ 0 |
|
(2) |
||||||||||||||||||||||||||||||
где |
X x h ; |
Y y h ; |
ξ1 th tвх |
tвх |
; |
||||||||||||||||||||||||||||||||
ξ0 t0 tвх tвх ; T X ,Y t x, y tвх tвх ; |
|
||||||||||||||||||||||||||||||||||||
Pe h a . |
|
|
|
|
|
|
|
|
|
|
|
|
|
|
|
|
|
|
|
|
|
|
|
|
|
|
|
|
|||||||||
Решение системы (2): |
|
|
|
|
|
|
|
|
|
|
|||||||||||||||||||||||||||
|
|
|
|
|
|
T X , Y ξ1 Y ξ 0 1 Y |
|
(3) |
|||||||||||||||||||||||||||||
|
|
|
|
|
|
|
2 |
|
|
|
|
1 |
n |
|
|
|
|
|
1 sin Y π n |
|
|
||||||||||||||||
|
|
|
|
|
|
|
|
|
|
{ξ |
|
|
|||||||||||||||||||||||||
|
|
|
|
|
|
|
|
|
|
|
n |
|
|
|
|
||||||||||||||||||||||
|
|
|
|
|
|
|
π n 1 |
|
|
|
|
|
|
|
|
|
|
|
|
|
|
|
|
|
|
|
|
|
|
|
|||||||
ξ |
0 |
|
sin 1 Y π n } exp π 2 n 2 X / Pe |
|
|||||||||||||||||||||||||||||||||
|
|
|
|
|
|
|
|
|
|
|
|
|
|
|
|
|
|
|
|
|
|
|
|
|
|
|
|
|
|
|
|
|
|
|
|
|
|
|
|
|
|
Средняя температура: |
|
|
|
|
|||||||||||||||||||||||||||||
|
|
|
|
|
|
|
|
|
|
|
|
|
1 |
|
|
|
|
|
|
|
|
|
|
|
|
|
|
|
|
|
|
|
|
|
|
|
|
|
|
T |
X T X , Y dY ξ1 ξ0 |
|
|||||||||||||||||||||||||||||||||
|
|
|
|
|
|
|
|
|
|
|
|
|
0 |
|
|
|
|
|
|
|
|
|
|
|
|
|
|
|
|
|
|
|
|
|
|
|
(4) |
|
|
|
|
|
|
|
|
|
|
|
|
|
|
|
|
|
|
|
|
|
|
|
|
|
|
|
|
|
n |
|
|
|
|
|
|||
{ |
1 |
|
|
|
2 |
|
1 |
1 1 n |
|
||||||||||||||||||||||||||||
|
|
|
2 |
|
|||||||||||||||||||||||||||||||||
|
|
|
|
|
2 |
|
|
|
|
π |
n 1 |
|
|
|
n |
|
|
|
|
|
|
|
|
|
|
||||||||||||
|
|
|
|
|
|
|
exp π2n2 |
|
|
X Pe }. |
|
|
|
||||||||||||||||||||||||
Инженерная оценка: |
|
|
|
|
|
|
|
|
|
|
|||||||||||||||||||||||||||
|
|
|
|
|
|
|
|
|
|
|
|
|
|
|
|
|
|
|
1 |
|
|
|
|
|
4 |
|
|
2 |
|
|
|
||||||
|
|
|
|
|
|
|
|
|
|
|
|
|
|
|
|
|
|
|
|
|
|
|
|
|
|
|
|||||||||||
T X ξ |
1 |
|
ξ |
0 |
|
|
|
|
|
|
|
|
|
|
|
exp π |
|
X Pe |
(5) |
||||||||||||||||||
|
|
|
|
|
|
|
2 |
|
|
||||||||||||||||||||||||||||
|
|
|
|
|
|
|
|
|
|
|
|
|
|
|
|
|
|
|
|
|
|
|
π |
|
|
|
|
|
|
||||||||
|
|
|
|
|
|
|
|
|
|
|
|
|
|
|
|
|
|
|
2 |
|
|
|
|
|
|
|
|
|
|
||||||||
Погрешность при X = 0: |
|
|
|
|
|
||||||||||||||||||||||||||||||||
|
|
|
|
|
|
|
|
|
|
|
|
|
|
|
|
|
|
1 |
|
|
|
4 |
|
|
|
|
|
|
|
|
|||||||
|
|
|
|
|
|
|
|
|
|
|
|
|
|
|
|
|
|
|
|
|
|
|
|
|
|
|
|||||||||||
T 0 ξ |
1 |
ξ |
0 |
|
|
|
|
|
|
|
|
|
|
|
|
0,095 (9,5%). |
(6) |
||||||||||||||||||||
|
|
|
|
|
|
2 |
|
||||||||||||||||||||||||||||||
|
|
|
|
|
|
|
|
|
|
|
|
|
|
|
2 |
|
|
|
|
π |
|
|
|
|
|
|
|
||||||||||
|
|
|
|
|
|
|
|
|
|
|
|
|
|
|
|
|
|
|
|
|
|
|
|
|
|
|
|
|
Численный анализ полученного решения (3) в виде основных характеристик температурного поля приведен на рис. 2.
32

а) |
б) |
в) г)
Рис. 2. Основные характеристики температурного поля: а – профили температур при Pe = 10, ξ0 = 1, ξ1 = 2 и
различных X: 1 – 0,5; 2 – 1; 3 – 1,5; 4 – 2,0; 5 – 6; б -
профили температур при Pe = 10, ξ 0 = 0, ξ1 = 1 и
различных X: 1 – 0,5; 2 – 1; 3 – 1,5; 4 – 4; в - профили температур при Pe = 10, ξ 0 = -1, ξ1 = 1 и различных X: 1
– 0,1; 2 – 0,5; 3 – 2; г - изменение средней по сечению канала температуры по его длине для Pe = 10: 1 - ξ 0 = 1,
ξ1 = 2; 2 - ξ 0 = 0, ξ1 = 1.
Синтезирована кинетическая модель зародышеобразования, роста и осаждения капель жидкости в рабочей камере при движении потока в пространстве их размеров:
f x, , f x, ,
f x, ,
x 2
h k f x, , (7) f x, ,0 0 ; f 0, , 0 ; f x, s , I
(8)
Решение (7) с условиями (8) в относительных переменных:
X , L, l A 1 L LS l X A 1Bk L LS (9)
|
L |
|
|
exp A 1 |
L2 K * L dL |
||
|
L |
S |
|
|
|
|
Полученная математическая модель (7) – (9) в совокупности с решением (5) образует сопряженную систему уравнений, учитывающую одновременно возникновение центров конденсации, роста капель и их осаждение в потоке бинарной смеси в камере. Она позволяет определить количественно потоки конденсата на стенки камеры и на выходе из неё.
Массы осевших аэрозольных частиц
H
Mо 0,5h3kv к 4nТ I 1H X , функ dX (10)
0
и вынесенных частиц за относительное время функционирования фильтра функ
функ
M в 0,5kv к 4 I 1Uhk 1 cв H , d (11)
0
где , |
c |
– относительная толщина частиц на |
|||
|
в |
|
|
|
|
стенках |
|
и |
их |
масса |
при |
X = H соответственно. |
|
|
|
Сравнение экспериментальных результатов при проведении опытов на разнотемпературном
конденсационном фильтре |
и теоретических |
|
данных, |
полученных |
использованием |
предложенной математической модели, показало удовлетворительную сходимость.
Осуществлено решение и анализ уравнений модели.
Безразмерные переменные:
L * ; |
k * h ; |
X x h ; |
|
||||||||||
Ф X , L, f x, , I ; |
|
K * L L 2k k * ; |
(12) |
||||||||||
A h *k * ; |
B k * |
|
|||||||||||
|
|
|
|
|
|
|
k |
|
|
|
|
|
|
Реперная переменная: |
|
|
|
|
|
||||||||
|
|
kT |
|
17 |
|
108 |
|
2 7 |
(13) |
||||
* |
|
|
|
|
|
|
|||||||
|
3k |
|
|
|
|
|
|
||||||
|
|
|
g k |
|
|
||||||||
Концентрация насыщения для воды: |
|
||||||||||||
c T |
|
0,289 |
|
|
|
|
|
5116,12 |
|
||||
|
|
|
|
exp |
20,342 |
|
|
|
(14) |
||||
|
|
|
|
|
|
||||||||
|
|
|
T |
|
|
|
|
|
|
|
T |
|
Результаты расчетов по (9) графически представлены на рис. 3, характеризующем динамику функции распределения капель аэрозоля на выходе, которые показывают, что с увеличением A , т. е. чем больше скорость роста капель, тем они крупнее, то же самое имеет место, если меньше Bk, т. е. чем меньше линейная скорость взвеси.
а)
б)
в)
33

УДК. 621.396.969.11
ИССЛЕДОВАНИЕ ТОЧНОСТИ ОПРЕДЕЛЕНИЯ КООРДИНАТ РАЗНОСТНО - ДАЛЬНОМЕРНЫМ МЕТОДОМ
Магистрант группы РТм-151 Хрипунов Е.Г. Руководитель: д-р техн. наук, профессор А.Б. Токарев
Строится математическая модель канала связи с многолучевым распространением применительно к разностнодальномерной системе (РДС). Исследуется влияние амплитуды отраженных лучей на смещение максимума взаимнокорреляционной функции (ВКФ), если время их задержки значительно отличается от истинного значения, а так же если находится в пределах основного пика ВКФ. На основе статистических методов оценивания минимизируется погрешность определения координат
Разностно-дальномерный метод использует измерения разностей моментов прихода сигнала в несколько пунктов наблюдения, находящихся на некоторых расстояниях друг от друга[1]. Разность моментов прихода этих сигналов в разнесенные пункты определяется по положению максимума их ВКФ
(1)
где
(2)
Модель канала связи с многолучевым распространением, для наглядности, представим ее на рисунке 1.
(3)
где s(t) – сигнал, поступающий в канал связи, K – оператор, показывающий влияние среды распространения на сигнал s(t), (t) – аддитивный шум, N – количество формирующихся лучей в канале связи.
Результаты влияния амплитуды одного и двух отраженных лучей на смещение максимума ВКФ с задержкой значительно отличающейся от tз (истинной задержки) приведены на рис. 2 и 3.
Рис. 1. Модель канала связи с многолучевым распространением
Для математического описания механизма многолучевого распространения сигналов в средах, где физические свойства изменяются случайным образом, воспользуемся следующей моделью многолучевого канала связи [2]
Рис. 2. ВКФ при наличии одного отраженного луча (Луч 4) с амплитудой равной 90% от амплитуды прямого луча (Луч 1) и временем задержки равным 3tз.
Рис. 3. ВКФ при наличии двух отраженных лучей с амплитудой равной 60% от амплитуды прямого луча и временем задержки равным 3tз
Таким образом, присутствие двух таких лучей, задержка которых обеспечивает перекрытие пиков их составляющих ВКФ, при достижении амплитуды 60% от прямого луча, смещает
34

максимум ВКФ в положение, равное времени их задержки (3tз в данном случае).
Результаты влияния одного отраженного луча на смещение максимума с задержкой, находящейся в пределах основного пика ВКФ, а так же идеальная ВКФ, для сравнения, приведены на рис. 4-7.
Рис. 4. Идеальная ВКФ
Рис. 5. ВКФ для одного отраженного луча с амплитудой 50% от основного и tз=8,8 мкс
По рис. 5 видно, что если время задержки отраженного луча попадет в отмеченную первую зону, то есть пик его составляющей полностью окажется под основным пиком ВКФ, то отклонение от истинного максимума будет минимальным, а уровень значительно вырастет над побочными составляющими.
Рис. 7. ВКФ для одного отраженного луча с амплитудой 80% от основного и tз=9,6 мкс
При попадании в третью область (рисунок 7), истинный максимум начинает уменьшаться, а второстепенный, находящийся от него по другую сторону от пика, начинает наоборот увеличиваться и при достижении амплитуды отраженного луча 80% от прямого луча он становится абсолютным. Погрешность в данном случае возрастает в разы.
В реальных условиях, при определении координат ИРИ, мы получаем множество пересечений линий положения. Поэтому для минимизации данной погрешности используют статистические методы оценивания. В результате применения итерационного метода наименьших квадратов, поправки в котором вычисляются на основе выражения
(4)
получили следующие результаты (рисунок 8).
Рис. 6. ВКФ для одного отраженного луча с амплитудой 60% от основного и tз=9,3 мкс
Если время задержки отраженного луча попадет в отмеченную вторую зону, как показано на рисунке 6, то есть пик его составляющей только на половину перекрывается основным пиком ВКФ, то отклонение от истинного максимума будет большим, чем в первом случае, а уровень начет снижаться с увеличением амплитуды отраженного луча.
Рис. 8. Расчет поправок к начальным приближениям Литература
1.Черняк В.С. Многопозиционная радиолокация/ В.С. Черняк/.- М.: Радио и связь 1993. – 416 с.
2.Иванов А. П. Имитатор многолучевого канала связи / А. П. Иванов // Труды международного симпозиума «Надежность и качество».: М. –
2011. – том 1. – с. 1 – 6.
35

УДК 621.791.72
К ВОПРОСУ СВАРКИ ТИТАНОВЫХ СПЛАВОВ ГИБРИДНЫМ СПОСОБОМ С ИСПОЛЬЗОВАНИЕМ ИЗЛУЧЕНИЯ ND:YAG - ЛАЗЕРА И ДУГИ С
НЕПЛАВЯЩИМСЯ ЭЛЕКТРОДОМ
Студент 4-го курса гр. СП-121 Илья О.Л.
В данной статье описывается исследование возможности выполнения лазерно-дуговой сварки соединений титановых сплавов, таких как низколегированный титановый сплав ВТ6 и высокопрочный Т110, а также оценка механических свойств полученных сварных соединений
В настоящее время титановые сплавы применяются при производстве ответственных конструкций в авиакосмической и химической промышленности, в судостроении. Из них изготавливают такие ответственные изделия, как баллоны высокого давления, элементы шасси, стрингерные панели для самолетов, элементы ракетной техники, емкости для химических реакторов и вытяжных систем, некоторые корпусные изделия . Заложенные в эти изделия конструкторские решения требуют применения сварных соединений. На практике более 90 % всех соединений выполняется аргонодуговой и электронно-лучевой сваркой.Однако эти методы сварки имеют и свои недостатки, такие как малую плотность энергии в дуговой плазме при дуговой сварке, или высокую стоимость и малые габариты большинства доступных вакуумных камер при электронно-лучевой сварке.
Впоследнее время расширяется применение лазерной сварки, имеющей такие преимущества как высокую плотность энергии в лазерном луче, высокую производительность и прецизионность обработки. Среди недостатков процесса лазерной сварки, прежде всего, можно отметить значительную себестоимость оборудования. В этом случае одним из путей снижения этого показателя в случае применения может являться частичная замена лазерной мощности дуговой при лазерной сварке.
Поэтому целью данной работы является исследование возможности выполнения лазернодуговой сварки соединений титановых сплавов таких как низколегированный титановый сплав ВТ6
ивысокопрочный Т110 и оценка механических свойств полученных сварных соединений.
Впроцессе работы изучались: технологическая схема процесса и особенности процесса лазернодуговой сварки титана и сплавов на его основе; выполнялось сравнение проплавляющей способности процесса лазерной и лазерно-дуговой сварки титана; определялись механические характеристики полученных сварных соединений титановых сплавов и изучалась их микроструктура.
Источником излучения служил Nd:YAG-лазер модели DY 044 мощностью до 4,4 кВт с длиной волны 1,06 мкм, а источником сварочного тока –
источник питания для автоматической сварки вольфрамовым электродом ВДУ-601 У3. Следует отметить, что в настоящее время известны исследования направленные на изучение процесса лазерно-дуговой сварки титана с применением MIGсварки, авторами был выбран вариант с применением TIG-сварки. Этот вариант позволяет выполнять сварку в широких диапазонах режимов, причем как с применением присадочного металла, так и без него.
Такое сочетание лазера и TIG-сварки позволяет увеличить проплавляющую способность процесса лазерно-дуговой сварки, а также допускает несложное введение присадочной проволоки в зону сварки.
Для реализации этой схемы была разработана гибридная сварочная головка, сочетающая в себе под вод сфокусированного линзой с фокусным расстоянием F = 300 мм лазерного излучения 1 и вольфрамового электрода 2 диаметром 5 мм.
Увеличение глубины провара, достигалось за счет того, что первой по ходу сварки расположена дуга неплавящегося электрода, что обеспечивало увеличение поглощаемого металлом лазерного излучения, т.к. расплавленный электрической дугой металл имеет лучшую поглощательную способность, чем холодный.
В качестве образцов использовали титановые сплавы ВТ-6 и Т110 толщиной δ = 13 мм. Проведенные экспериментальные исследования позволили установить, что лазерно-дуговым способом можно проваривать титановые сплавы
36

толщиной 12 мм на скорости 22—24 м/ч при мощности излучения 4,4 кВт, сварочном токе 400 А и напряжении 12—14 В. Поперечные макрошлифы сварных швов титановых сплавов ВТ6 и Т110 приведены на рис. 1 и рис.
2.
Рис. 1. Поперечный макрошлиф наплавки на титановом сплаве ВТ6 толщиной 13 мм: а – лазерно-дуговая сварка, б – лазерная сварка
Глубина проплавления при выполнении лазерно-дуговой сварки титанового сплава ВТ6 увеличилась по сравнению с лазерной сваркой в 3 раза при увеличении погонной энергии в 2 раза. При сварке титанового сплава Т110 глубина проплавления увеличилась в 2 раза.
Рис. 2. Поперечный макрошлиф наплавки на титановом сплаве Т110 толщиной 13 мм: а – лазерно-
дуговая сварка, б – лазерная сварка
Анализ механических свойств полученных сварных соединений, показал, что более высокие значения ударной вязкости и имеют сварные соединения, выполненные лазерно-дуговой сваркой. При этом сварные соединения сплава ВТ6, выполненные с применением как одного лишь лазера так и лазерно-дуговой сваркой имеют удовлетворительные показатели ударной вязкости металла шва, которые меньше несколько хуже аналогичных показателей для основного.
Рис. 3. Микроструктура металла шва и ЗТВ сварных соединений сплава ВТ6: а, б – выполненных лазерной
сваркой; в, г – выполненных лазерно-дуговой сваркой; а, в
– металл шва; б, г – ЗТВ околошовная зона
Анализ механических свойств полученных сварных соединений высокопрочного титанового сплава Т110 показал, что сварные соединения сплава Т110 выполненные с применением одного лишь лазера имеют неудовлетворительные показатели ударной вязкость металла шва, и самые низкие значения ударной вязкости в ЗТВ. Разрушение хрупкое. Металл шва и ЗТВ имеет малую ластичность и высокую прочность.
Для определения причин понижения свойств сварных соединений высокопрочного титанового сплава Т110 выполненных лазерной сваркой, по сравнению с выполненного лазерно-дуговой сваркой были проведены детальные исследования структуры сварных соединений.
Данные спектрального анализа и сканирующей электронной микроскопии, позволили сделать вывод, что при сварке образцов из сплавов ВТ6 и Т110 на выбранных режимах снижение содержания легирующих элементов в сварных швах находилось
впределах марочных стандартов.
Вметалле шва сварных соединений титанового сплава ВТ6 выполненных лазерной сваркой формируются преимущественно вытянутые
внаправлении теплоотвода первичные β-зерна характерные для титановых α + β-сплавов мартенситного типа (рис. 3, а). Внутризереную структуру после лазерной сварки составляет метастабильная мартенситная грубоигольчатая α′- фаза. ЗТВ при лазерной сварке этого сплава имеет строение, несколько отличающееся от строения ЗТВ после сварки плавлением сплава ВТ6 другими способами.
Как правило, в ЗТВ сварных соединений титановых сплавов различают три характерных участка: участок крупного зерна, (от температуры плавления до температур интенсивного роста β- зерен около 1300 °С); участок полной перекристаллизации, от температур интенсивного роста β-зерен до температур конца α → β- превращения 890 °С; участок неполной перекристаллизации; нагреваются до температур начала α → β-превращения 890 °С. Исследования выполненных сварных соединений показали, что в случае лазерной сварки сплава ВТ6 по указанному выше режиму в ЗТВ отсутствует участок крупного зерна.
Вучастке полной перекристаллизации, так же как и в шве, преобладает мартенситная α′-фаза (более мелкоигольчатая, чем в металле шва). Участок полной перекристаллизации имеет минимальную ширину, составляющую 0,5—1 зерно (рис. 3, б).В металле шва соединений титанового сплава ВТ6 выполненных лазерно-дуговой сваркой формируются так же, как и при лазерной сварке, вытянутые в направлении теплоотвода первичные β- зерна по всей высоте шва (рис. 3, в).
Внутризеренную |
структуру |
составляет |
37
грубоигольчатая α′-фаза, подобно тому как это происходило при лазерной сварке сплава ВТ6.
ВЗТВ сварного соединения, выполненного лазерно-дуговой сваркой, в отличие от ЗТВ сварного соединения, выполненного лазерной сваркой, присутствуют все три участка ЗТВ, описанные выше и характерные для других способов сварки плавлением. Внутризеренная структура околошовной зоны состоит из игольчатой метастабильной α′-фазы (рис. 3, г).
Сплав Т110, относится к титановым α + β- сплавам мартенситного типа, коэффициент стабильности β-фазы в сплаве Т110 составляет около 0,6. В металле сварных соединений титанового сплава Т110, выполненном лазернодуговой сваркой, четко прослеживается дендритная структура (рис. 4, а). В металле шва фиксируются метастабильные β- и α′/α′′-фазы. В зернах шва фиксируется субструктура (рис. 4, а). В металле шва сплава Т110, выполненном лазерной сваркой после травления шлифа образовались многочисленные ямки травления, которые вытравливаются в местах выхода на поверхность скоплений дислокаций (рис. 4, г).Это может быть косвенным свидетельством напряженного состояния сварного соединения.
ВЗТВ сварного соединения сплава Т110, выполненного лазерной сваркой участок крупного зерна – отсутствует (рис. 4, б), как и в случае лазерной сварки сплава ВТ6. В зоне полного полиморфного превращения, после быстрого охлаждения фиксировалась метастабильная структура, состоящая из матричной β-фазы и дисперсных частиц мартенситной α′/α′′-фазы. Большинство зерен в околошовной зоне имеют субструктуру, в участках ЗТВ с неполной перекристаллизацией, примыкающих к ОМ, субструктура отсутствует.
При лазерно-дуговой сварке сплава Т110 в металле шва образуются преимущественно вытянутые в направлении теплоотвода β-зерна. Внутризеренная структура состоит так же, как и после лазерной сварки, из метастабильных β- и α′/α′′-фаз. При лазерно-дуговой сварке сплава Т110 участок крупного зерна присутствует. В отличие от сварного соединения сплава Т110, выполненного лазерной сваркой, ни в шве, ни в ЗТВ сварного
соединения, |
|
выполненного |
лазерно-дуговой |
сваркой, |
не |
наблюдалось |
субструктуры, |
микроструктура была более однородной и равномерной, ямки травления не появлялись, что по видимому связано с более низким уровнем
сварочных напряжений. |
|
Изложенные результаты |
позволили сделать |
следующие |
выводы: |
1.Установлено, что применение предложенной схемы лазерно-дуговой сварки при мощности лазерного луча 4,4 кВт и величине сварочного тока
400А обеспечивает примерно двукратное увеличение глубины провара по сравнению с результатами одной лишь лазерной сварки, выполненной на режиме с аналогичными параметрами.
2.Предел прочности сварных соединений титановых сплавов ВТ6 и Т110 (в состоянии после сварки), выполненных лазерно-дуговой сваркой,
несколько больше (на 2—4 %) значений предела прочности основного металла при удовлетворительной пластичности и ударной вязкости.
3.Наличие зоны крупного зерна в ЗТВ и отсутствие субструктуры в металле соединений, выполненных лазерно-дуговой сваркой, по мнению авторов, повышает их ударную вязкость по сравнению с соединениями, выполненными лазерной сваркой, в ЗТВ которых отсутствует зона крупного зерна.
38

УДК 621.791.72
КВОПРОСУ ЭЛЕКТРОННО-ЛУЧЕВОЙ СВАРКИ ВЫСОКОПРОЧНЫХ СТАЛЕЙ
СБРОНЗОЙ
Студент 4-го курса гр. СП-121 Киктев Д.А.
В данной статье пойдет речь об использовании динамического позиционирования электронного пучка электроннолучевой сварки высокопрочных сталей с бронзой, описание проблемы и пути ее решения, которые волнуют специалистов в этой области уже не первое десятилетие, а также, описание технологии получения качественных сварных соединений при ЭЛС высокопрочной стали 09Х16Н4Б с бронзой БрХ-08
При изготовлении ответственных изделий в машиностроении, судостроении, аэрокосмической и других отраслях промышленности возникает необходимость получения неразъемных соединений высокопрочных сталей с медью и ее сплавами. Однако плохая свариваемость сталей с медными сплавами при использовании дуговых способов сварки, связанная в первую очередь с низкой взаимной растворимостью меди и железа, различиями в структуре и теплофизических свойствах соединяемых металлов, ограничивает возможности конструирования сварных изделий.
При сваривании меди со сталью возникает ряд проблем, которые следует учитывать. Эти проблемы в свою очередь возникают из-за особенностей физико-химического поведения меди, также ее взаимодействие с кислородом. Все эти факторы являются затруднительными для получения качественного сварного соединения. Также низкая температура плавления меди, поглощения ею газов и разность коэффициентов теплопроводности отрицательно сказываются на качестве получаемого соединения.
Но если учесть все особенности металла и выбрать наиболее подходящую сварку к тому или иному виду соединений, вполне возможно получить качественное соединение с высокими производственными характеристиками. Медь, а также медные сплавы с содержанием бронзы и латуни прекрасно свариваются со стальными деталями всеми известными видами сварки. Но учитывая характеристики металлов свариваемых между собой, немного смещают сварную дугу со стыка, уводя ее в сторону от меди или ее сплавов.
При наплавлении меди на сталь с использованием флюсов в среде защитных газов получается надежное сварное соединение, обладающее удовлетворительной пластичностью. Также получаемое покрытие получается достаточно равномерным при действии на него статической нагрузки.
Такие комбинации как никель с бронзой лучше всего сваривать через буферные слои. Никелевый электрод следует применять для наплавки плакирующего слоя на бронзовую кромку.
Студент 4-го курса гр. СП-121 Д.А. Киктев
Наплавить нужную толщину никелевым электродом достаточно проблематично, поэтому первый слой наплавляется никелевым электродом, а последующие – Монелевым. Использование только Монелевого электрода для наплавки плакирующего слоя может привести к образованию трещин [1].
К преимуществам ЭЛС можно отнести:
1.Высокая концентрация ввода теплоты в изделие, которая выделяется не только на поверхности изделия, но и на некоторой глубине в объеме основного металла. Фокусировкой электронного луча можно получить пятно нагрева диаметром 0,0002-5 мм, что позволяет за один проход сваривать металлы толщиной от десятых долей миллиметра до 200 мм. В результате можно получить швы, в которых соотношение глубины провара к ширине до 20:1 и более. Появляется возможность сварки тугоплавких металлов (вольфрама, тантала и др.), керамики и т.д. Уменьшение протяженности зоны термического влияния снижает вероятность рекристаллизации основного металла в этой зоне.
2.Малое количество вводимой теплоты. Как правило, для получения равной глубины проплавления при электронно-лучевой сварке требуется вводить теплоты в 4 ... 5 раз меньше, чем при дуговой. В результате рез ко снижаются коробления изделия.
3.Отсутствие насыщения расплавленного и нагретого металла газами. Наоборот, в целом ряде случаев наблюдается дегазация металла шва и повышение его пластических свойств. В результате достигается высокое качество сварных соединений на химически активных металлах и сплавах, таких как ниобий, цирконий, титан, молибден и др. Хорошее качество электронно-лучевой сварки достигается также на низкоуглеродистых, коррозионно-стойких сталях, меди и медных, никелевых, алюминиевых сплавах [2].
Исследована возможность получения бездефектных сварных швов при электроннолучевой сварке высокопрочной стали с бронзой с использованием динамического позиционирования электронного пучка, обеспечивающего возможность ввода теплоты в свариваемые заготовки в
39
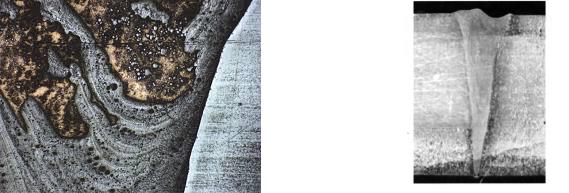
нескольких участках, расположенных на некотором расстоянии друг от друга.
В настоящее время широкое применение находит электронно-лучевая сварка (ЭЛС), позволяющая получить швы с высокими значениями отношения глубины сварного шва к его ширине, обеспечить минимальные размеры зоны термического влияния (ЗТВ) и высокие механические характеристики сварных соединений. Этот способ сварки является весьма эффективным при решении задачи получения качественных сварных швов при сварке сталей с медными сплавами и, в частности, с бронзами. Однако в случае, когда одна из деталей в таком биметаллическом сварном соединении изготовлена из высокопрочной легированной стали, возникают трудности формирования бездефектных сварных швов с требуемыми характеристиками.
Цель работы — разработка технологии, обеспечивающей получение качественных сварных соединений при ЭЛС высокопрочной стали 09Х16Н4Б с бронзой БрХ-08.
В существующих технологиях ЭЛС высокопрочных сталей с бронзой обязательным является предварительный подогрев расфокусированным электронным пучком сварного стыка со стороны детали из бронзы и при отсутствии осцилляции электронного пучка последующий сварочный проход осуществляется со смещением электронного пучка со стыка в сторону детали из бронзы. Данная технология не обеспечивает высокой воспроизводимости качества сварных соединений, так как даже незначительные технологические отклонения параметров приводят к возникновению трещин в сварных соединениях.
Рис. 1. Дефекты в сварном соединении стали 09X16Н4Б с бронзой БрХ-08
Наиболее вероятной причиной возникновения трещин в сварных швах является возникновение растягивающих напряжений в процессе непрерывного охлаждения при температурах ниже температуры начала мартенситного превращения стали (около 360 °С). Для снижения таких напряжений при сварке традиционно применяют предварительный подогрев свариваемого стыка до 200—250 °С. Кроме того, образование трещин может быть связано с «расклинивающим» действием расплава бронзы при его проникновении
в микронадрывы в стали по границам зерен с одновременным действием термических напряжений растяжения (эффект Ребиндера) [3].
Для оценки возможности предварительного подогрева стыка до указанных температур провели численное моделирование управления отклонением пучка, отклоняющие катушки электронной пушки подключались к специально разработанным широкополосным усилителям тока с верхней границей полосы пропускания 200 кГц. На входы этих усилителей через цифроаналоговый интерфейс подавались сигналы с компьютерной системы, которая работала под управлением разработанной программы, обеспечивающей заданные пространственно-временные характеристики теплового воздействия на свариваемые заготовки.
Для контроля и воспроизведения параметров фокусировки электронного пучка использовали разработанный авторами метод, основанный на регистрации высокочастотной составляющей тока несамостоятельного разряда в плазме. Этот разряд возбуждается в плазме, формируемой в зоне воздействия на металл мощного концентрированного электронного пучка, с помощью коллектора электронов, который устанавливается над зоной сварки и имеет положительный потенциал 20—30 В относительно свариваемого изделия. В процессе экспериментов из спектра тока несамостоятельного разряда в плазме выделяли составляющую с частотой 10—20 кГц и по экстремальным значениям ее амплитуды устанавливали «острую» фокусировку электронного пучка, обеспечивающую максимальную глубину проплавления для заданных ускоряющего напряжения и тока пучка.
Рис. 2. Макрошлиф поперечного сечения сварного соединения бронзы БрХ-08 со сталью
09X16Н4Б
При проведении экспериментальных работ выполняли сварочные проходы по кольцевому стыку диаметром 120 и толщиной 8 мм, составленному из бронзы БрХ-08 и стали 09Х16Н4Б. В стыке применяли соединение «в замок», при этом заготовка, обеспечивающая подкладку под стыком, была изготовлена из стали. Мощность электронного пучка в экспериментах составляла 4 кВт.
40