
- •ИННОВАЦИОННАЯ ОРГАНИЗАЦИОННАЯ КУЛЬТУРА КАК ФАКТОР ПОВЫШЕНИЯ ИННОВАЦИОННОЙ ВОСПРИИМЧИВОСТИ
- •ИНТЕГРАЦИЯ ПЕРИФЕРИЙНЫХ УСТРОЙСТВ В СЧПУ ДЛЯ ПОВЫШЕНИЯ ПРОИЗВОДИТЕЛЬНОСТИ
- •ИССЛЕДОВАНИЕ ПРОЦЕССОВ ТЕПЛОМАССООБМЕНА В РАЗНОТЕМПЕРАТУРНОМ КОНДЕНСАЦИОННОМ ФИЛЬТРЕ
- •КОММУТАЦИОННЫЙ АППАРАТ СЕНСОРНОГО (ЁМКОСТНОГО) УПРАВЛЕНИЯ С ФУНКЦИЕЙ РЕГУЛИРОВАНИЯ ПЕРЕМЕННОГО НАПРЯЖЕНИЯ НА НАГРУЗКЕ
- •КОМПЛЕКС МОДЕЛИРОВАНИЯ ИНФОРМАЦИОННЫХ ЭПИДЕМИЙ В БЕЗМАСШТАБНЫХ СЕТЯХ
- •МЕТОДИКА ИЗГОТОВЛЕНИЯ ТРЕХСЛОЙНЫХ СОТОВЫХ ПАНЕЛЕЙ
- •МНОГОМЕТОДНАЯ ПОДСИСТЕМА ПОДДЕРЖКИ ПРИНЯТИЯ РЕШЕНИЙ НА ОСНОВЕ ПАРАЛЛЕЛЬНЫХ ГЕНЕТИЧЕСКИХ АЛГОРИТМОВ
- •МОДЕЛИРОВАНИЕ СИСТЕМЫ ПОЖАРНОЙ БЕЗОПАСНОСТИ ТЕХНОЛОГИЧЕСКОЙ ЛИНИИ ТЭП-50 НА ОАО «ВОРОНЕЖСИНТЕЗКАУЧУК»
- •НАНОТЕХНОЛОГИИ ДЛЯ ПОВЫШЕНИЯ ИЗНОСОСТОЙКОСТИ РАБОЧИХ ПОВЕРХНОСТЕЙ ИЗДЕЛИЙ
- •ОБЕСПЕЧЕНИЕ КАЧЕСТВА НАУКОЕМКОЙ ПРОДУКЦИИ И ИННОВАЦИОННАЯ ДЕЯТЕЛЬНОСТЬ
- •ОПТИМИЗАЦИЯ ПРОИЗВОДСТВЕННОГО ПРОЦЕССА НА ОСНОВЕ ТЕХНОЛОГИЙ БЕРЕЖЛИВОГО ПРОИЗВОДСТВА
- •ОПТИМИЗАЦИЯ СОСТАВА КЕРАМИЧЕСКИХ ОБОЛОЧЕК ДЛЯ ЛИТЬЯ ПО ВЫПЛАВЛЯЕМЫМ МОДЕЛЯМ
- •ПЛАЗМЕННЫЕ РАКЕТНЫЕ ДВИГАТЕЛИ – РЕВОЛЮЦИЯ В КОСМИЧЕСКИХ ПОЛЕТАХ
- •ПОРТАТИВНОЕ ЦИФРОВОЕ УСТРОЙСТВО, ПРЕДНАЗНАЧЕННОЕ ДЛЯ ОТОБРАЖЕНИЯ ТЕКСТОВОЙ И ГРАФИЧЕСКОЙ ИНФОРМАЦИИ, ПРЕДСТАВЛЕННОЙ В ЭЛЕКТРОННОМ ВИДЕ
- •ПОСТРОЕНИЕ ПРОГНОСТИЧЕСКИХ МОДЕЛЕЙ РАСПРОСТРАНЕНИЯ НЕФТИ
- •ПРИМЕНЕНИЕ КЛАСТЕРНОГО АНАЛИЗА ДЛЯ ОБРАБОТКИ ОШИБОЧНЫХ СРАБАТЫВАНИЙ С УЧЁТОМ ПРИОРИТЕТОВ ПАРАМЕТРОВ
- •ПРИМЕНЕНИЕ ТЕХНОЛОГИЙ СЕМАНТИЧЕСКОЙ ПАУТИНЫ ДЛЯ ПРОЕКТИРОВАНИЯ ОНТОЛОГИЙ И СИСТЕМ УПРАВЛЕНИЯ СОДЕРЖИМЫМ НА ИХ ОСНОВЕ
- •ПРОГРАММНЫЙ КОМПЛЕКС «NETEPIDEMIC» ДЛЯ РИСК-АНАЛИЗА ПРОЦЕССОВ РАСПРОСТРАНЕНИЯ ДЕСТРУКТИВНОГО КОНТЕНТА В НЕОДНОРОДНЫХ СЕТЕВЫХ СТРУКТУРАХ
- •ПРОГРАММНЫЙ КОМПЛЕКС РИСК-АНАЛИЗА РАСПРЕДЕЛЕННЫХ ИНФОРМАЦИОННЫХ СИСТЕМ
- •РАЗВИТИЕ СПОСОБОВ ТОЧНОЙ ШТАМПОВКИ
- •РАЗРАБОТКА ГИБРИДНЫХ ФУНКЦИОНАЛЬНЫХ МАТЕРИАЛОВ НА ОСНОВЕ НИКЕЛЯ
- •РАЗРАБОТКА МОДЕЛЕЙ И АЛГОРИТМОВ ИНТЕЛЛЕКТУАЛЬНОГО АНАЛИЗА КЛИЕНТСКИХ СРЕД НА ОСНОВЕ НЕЧЁТКИХ НЕЙРОННЫХ СЕТЕЙ
- •РАЗРАБОТКА СИСТЕМЫ ПЛАНИРОВАНИЯ СЕТИ И ОБЕСПЕЧЕНИЯ ДОСТУПА К ВЫСОКОСКОРОСТНОМУ СОЕДИНЕНИЮ КОНЕЧНОГО ПОЛЬЗОВАТЕЛЯ
- •РАЗРАБОТКА ЭЛЕМЕНТОВ ГИБРИДНОЙ СИСТЕМЫ ЛОКАЛЬНОЙ ТЕРМОСТАБИЛИЗАЦИИ ЭЛЕКТРОННЫХ МОДУЛЕЙ НА ОСНОВЕ МИКРОКАНАЛЬНЫХ ТЕПЛООБМЕННИКОВ И ТЕРМОЭЛЕКТРИЧЕСКИХ ПРЕОБРАЗОВАТЕЛЕЙ
- •СИСТЕМА АВТОМАТИЗИРОВАННОГО ПЛАНИРОВАНИЯ, ОПТИМИЗАЦИИ И УЧЕТА ШИРОКОПОЛОСНОГО РАДИОДОСТУПА И ЦИФРОВОГО ТВ
- •СОВРЕМЕННЫЕ ТЕХНОЛОГИИ, ИСПОЛЬЗУЮЩИЕСЯ В ПРОИЗВОДСТВЕ РАКЕТНО-КОСМИЧЕСКОЙ ТЕХНИКИ
- •СТРУКТУРА ЗОНДА СКАНЕРА БЛИЖНЕГО ПОЛЯ
- •ТЕХНИЧЕСКАЯ СИСТЕМА ОБЕСПЕЧЕНИЯ ЭКОЛОГИЧЕСКОЙ БЕЗОПАСНОСТИ НА ТЕПЛОВЫХ ЭНЕРГЕТИЧЕСКИХ УСТАНОВКАХ
- •ТЕХНОЛОГИИ 3D-ПЕЧАТИ В РАКЕТОСТРОЕНИИ
- •УСТРОЙСТВА ДЛЯ ОБРАБОТКИ ЗВУКА МУЗЫКАЛЬНЫХ ИНСТРУМЕНТОВ В РЕЖИМЕ РЕАЛЬНОГО ВРЕМЕНИ
- •ЭЛЕКТРИЧЕСКИЕ РАКЕТНЫЕ ДВИГАТЕЛИ – ДВИГАТЕЛИ БУДУЩЕГО
- •ЭНЕРГОСБЕРЕЖЕНИЕ В РАЗДЕЛИТЕЛЬНЫХ ОПЕРАЦИЯХ

УДК 621.9.04
ИНТЕГРАЦИЯ ПЕРИФЕРИЙНЫХ УСТРОЙСТВ В СЧПУ ДЛЯ ПОВЫШЕНИЯ ПРОИЗВОДИТЕЛЬНОСТИ
Аспирант кафедры АОМП Черных Д.М. Руководитель: д-р техн. наук, профессор В.В. Трофимов
В работе рассмотрена возможность интеграции различных периферийных устройств для повышения производительности фрезерной обработки. В частности разработана схема использования дополнительной поворотной оси для изменения схемы формообразования сложных криволинейных профилей и использование приспособления для адаптивного изменения жесткости зажима заготовок на базе систем с нулевой точкой
В современных условиях перед машиностроительными предприятиями ставят задачи повышения качества продукции и снижения издержек производства. При обработке деталей со сложными криволинейными поверхностями с повышенными требованиями к точностным характеристикам, в частности в авиакосмической отрасли, возникает ряд проблем, связанных с невозможностью обработки профиля без получения погрешностей формы. Это происходит из-за ограничений, накладываемых системами числового программного управления (СЧПУ) и несовершенством кинематики металлообрабатывающих станков. СЧПУ апроксимируют траекторию обработки последовательностью отрезков определенной длины, которая определяется возможностью интерполятора СЧПУ.
Отсутствие встроенной функции Look Ahead и малый размер буфера СЧПУнегативно сказывается на производительности обработки. При отработке каждого из отрезков рабочие органы станка вначале разгоняются до требуемой подачи, а затем замедляются для исключения зарезов. Назначение блока Look Ahead опережающего просмотра состоит в определении условного времени отработки кадра в циклах интерполятора для последующей коррекции контурной скорости и анализе в каждом кадре базовых параметров движения (вектора контурной скорости в начале и конце кадра, скорости по дополнительным координатным осям, пути в основной системе координат, радиуса кривизны траектории движения)[1]. В результате своей работы блок Look Ahead анализирует траекторию и позволяет плавно изменять скорость подачи в процессе резания. Даже при наличии данной функции при малом размере буфера наблюдаетсяснижение производительности из-за ограниченного количества кадров УП, анализируемых СЧПУ.
Использование дополнительной поворотной оси приводит к значительному расширению технологических возможностей станка. Также появляется возможность изменить схему формообразования. Дополнительная поворотная ось C позволяет обрабатывать криволинейные профили посредством согласования
перемещения рабочих органов по осям X, Y, Z и оси C.
Реализация данного согласования ложится на СЧПУ станка и микроконтроллер, управляющий поворотной осью. Для генерирования управляющей программы используется постпроцессор. Он представляет собой отдельный или интегрированный в систему Computer-Aided Manufacturing (CAM) программный модуль,
основной задачей которого является преобразование разработанной траектории перемещения инструмента относительно заготовки
вУП для конкретного станка с ЧПУ, основываясь на особенностях его кинематики.Постпроцессор, основываясь на информации о положении, траектории инструмента, режимах резания и других технологических параметрах, обрабатывает данные и формирует управляющую программу для определенного станка. В данном случае к трем координатам, две из которых могут управляться одновременно, добавляется координата, отвечающая за поворот стола.. При использовании дополнительной поворотной оси круговая интерполяция заменяется на линейную в плоскости обработки и поворот заготовки на определенный угол[2].Для обработки криволинейных поверхностей используется линейная интерполяция
вплоскости обработки XZ и поворотная ось C. При расфрезеровывании отверстий, радиус которых не превышает диаметр инструмента и их ось совпадает с осью вращения стола, инструмент совершает движение по винтовой линии (рис. 1).
а) б)
Рис. 1. Траектория фрезы при обработке отверстия
В таблице представлены фрагменты УП для стандартной обработки (время обработки составило
26
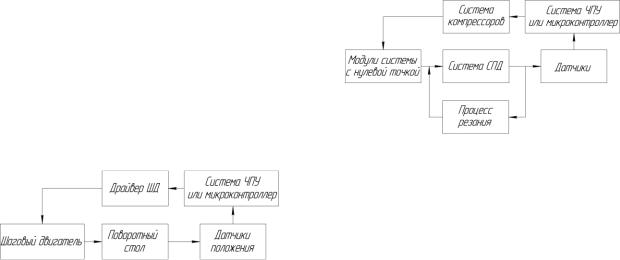
76 с) и обработки с использованием поворотного стола (время обработки составило 33 с).
Фрагмент УП при обработке с |
Фрагмент УП при обработке с |
|
использованием двух |
использованием поворотного |
|
одновременно управляемых |
стола |
|
|
осей |
|
… |
|
… |
N060 Z-2.3008 |
N080 G1 X-31.0515 Z-.5355 |
|
N070 G1 X-20.3395 Y17.5933 |
C325.321 F250. M08 |
|
Z-2.3806 F250 |
N090 X-31.4353 Z-.5565 |
|
N080 X-21.3161 Y18.5988 Z- |
C325.114 |
|
2.5032 |
|
N100 X-32.6727 Z-.6214 |
… |
|
C325.167 |
N2870 |
X-28.5 Y11. |
… |
N2880 |
Z-1. |
N420 X-35.1177 Z-3. C331.976 |
N2890 |
G0 Z7.4992 |
N430 G0 Z7.4992 |
N2900 M02 |
N440 M02 |
При разработке прототипа, схема управления которымпредставлена на рис. 2, управление поворотным столом осуществлялось при помощи микроконтроллера ATmega328. К нему подключается драйвер шагового двигателя (ШД), назначением которого является преобразование команд контроллера шагового двигателя в импульсы, подаваемые на обмотки ШД и их усиление. Т.к. ШД представляет собой синхронный бесщёточный электродвигатель с несколькими обмотками, то ток, подаваемый в одну из обмоток статора, вызывает фиксацию ротора. Последовательная активация обмоток двигателя вызывает дискретные угловые перемещения ротора. Для контроля положения поворотного стола используются датчики углового поворота.
Рис. 2. Схема управления дополнительной поворотной осью представлена
Передача данных на микроконтроллер осуществляется через виртуальныйCOM порт. Такой режим управления позволяет подключать дополнительные программируемые периферийные устройства.
Причиной снижения производительности и неудовлетворительного качества обработанных поверхностей часто становится вибрация главных механизмов станка, при которой изменяется траектория движения режущего инструмента, следствием чего является увеличение глубины микронеровностей, характеризующих шероховатость поверхности.
Возникающие вибрации со значительными амплитудами колебаний обусловлены резонансом между собственными частотами обрабатываемой детали и составляющими частотного спектра силы
резания, определяемыми импульсным воздействием зубьев в ее режущей части на деталь.
[3]
Исключить возможность возникновения резонансных вибраций возможно за счет изменения собственной частоты колебаний системы стол- приспособление-деталь (СПД). За счет уменьшения типоразмера используемых модулей системы с нулевой точкой и дифференциации системы управления ихсостояние,возможно изменение жесткости системы СПД. Схема устройства для изменения собственных частот системы СПД представлена на рис. 3. Изменение состояния модулей осуществляется при помощи компрессора с системой регулируемых клапанов. Управляться они будут посредством СЧПУ или микроконтроллера, который будет получать и обрабатывать данные о процессе резания при помощи совокупности датчиков, установленных на рабочих органах металлообрабатывающего оборудования, образующих информационноизмерительную систему.
Рис. 3. Схема управления процессом резания
Возможность изменять жесткость зажима приспособления в автоматическом режиме посредством СЧПУ позволяет не только повысить качество поверхности обработанной детали, но и сократить время ее механической обработки за счет использования ранее недоступных, более высоких частот вращения шпинделя. Также снижение вибрации в процессе обработки благоприятно сказывается на стойкости инструмента и сроке службы рабочих органов станка. Внедрение систем с нулевой точкой уменьшает вспомогательное время обработки за счет снижения времени переустановки заготовок, а также за счет возможности базирования и установки заготовки в приспособление вне станка.Использование дополнительной управляемой поворотной оси позволяет повысить производительность обработки за счет сокращения времени отработки УП и повысить точность обработки за счет изменения схемы формообразования.
Литература
1.Сосонкин В.Л., Мартинов Г.М. Системы числового программного управления: Учеб. пособие. - М.: Логос, 2005. - 296 с.
2.Родин П.Р. Основы формообразования поверхностей резанием. – М.:Вища школа, 1977. -192 с.
27
УДК 622.357.7
ИССЛЕДОВАНИЕ ВОЗДЕЙСТВИЯ СОСТАВА ПРИРОДНОЙ ВОДЫ НА КОРРОЗИОННУЮ СТОЙКОСТЬ МАГИСТРАЛЬНЫХ ТРУБОПРОВОДОВ
Аспирант кафедры ПЭБЖД Тенькаева А.С. Руководитель: д-р техн. наук, профессор Н.В. Мозговой
Проведены гравиметрические исследования коррозионной стойкости трубной стали магистральных трубопроводов Изучено влияние природы среды, в которой могут эксплуатироваться магистральные трубопроводы
На территории России ежегодно происходит более 20 тысяч официально зарегистрированных аварий, сопровождающихся значительными разливами нефти. Объемы среднего разлива нефти и нефтепродуктов колеблются от 3 до 20 м3. В результате, значительные территории суши, обширные морские и океанские акватории загрязняются нефтяными углеводородами. Из анализа литературных данных следует, что проблема повышения безопасности на нефтепроводах остается актуальной [1, 2]. Нефтегазоносный комплекс представляет объекты повышенного экологического риска, который возникает в результате аварий на техногенных объектах. Анализ статистики аварий трубопроводов по причинам (табл. 1) свидетельствует о доминирующей роли коррозии, что переносит главный фактор экологического риска и возможного ущерба на период эксплуатации.
Таблица 1 Причины и частота аварий на трубопроводах
|
Частота |
Частота |
Причина |
аварий |
аварий |
аварии |
промыслов |
магистральны |
|
ых |
х |
|
трубопрово |
трубопроводо |
|
дов, % |
в, % |
|
|
|
Дефекты труб |
0,5-1,5 |
2-5 |
(заводской |
|
|
брак) |
|
|
|
|
|
Дефекты труб |
0,5-1,0 |
6-8 |
(строительны |
|
|
й брак) |
|
|
|
|
|
Дефекты |
2-3 |
12-15 |
сварки |
|
|
|
|
|
Коррозия |
91-95 |
70-80 |
|
|
|
Нарушение |
1-3 |
2-5 |
правил |
|
|
эксплуатации |
|
|
|
|
|
Авторы ряда работ оценивают вклад различных причин следующим образом [1,2].:
1.Причины потерь нефти: 39 % - нарушения при строительстве и изготовлении деталей нефтепроводов; 34 % - внешняя коррозия; 27% - внешние воздействия.
2.Причины потерь нефти: 30 % - аварии из-за заводских дефектов; 48-52 % - коррозия; 20-30% - внешнее воздействие.
3.Аварии происходят из-за: 64 % - разрушение труб; 27% - повреждение оборудования насосных станций; 9% - аварии по вине сторонних организаций и стихии.
4.Причины отказа промысловых нефтепроводов: 91 % - внутренняя коррозия; 3,9 % - внешняя коррозия; 2,8 % - строительные дефекты; 0,8 % - нарушение правил эксплуатации; 1,5 % - прочее.
5.Причины аварий на магистральных нефтепроводах: 70-80 % - внешняя коррозия; 10-15 % - брак в строительно-монтажных работах (в
основном при сварке); 10-15 % - механические повреждения; 2-5 % - заводской брак в трубах и запорной арматуре; 2-5 % - эксплуатационные причины.
Общее состояние трубопроводов можно характеризовать как критическое и требующее принятия радикальных решений, так как с позиций современных экологических требований и норм эксплуатация аварийных нефтегазовых объектов становится невозможной.
Цель работы – продолжение исследования коррозионной стойкости трубной стали магистральных трубопроводов в модельных растворах имитирующим различные коррозионные среды, в которых эксплуатируются магистральные трубопроводы [1, 2].
Методика эксперимента
Для проведения коррозионных испытаний
изготовляли образцы из стали с поверхностью 10 см2 и помещали их в коррозионные среды (модельные растворы). Продолжительность испытаний до 100 часов. Потерю массы стального образца определяли гравиметрическим методом с
точностью взвешивания до 10 4 г.
Результаты и их обсуждение
Для проведения коррозионных испытаний трубной стали были приготовлены модельные растворы, имитирующие коррозионную среду по соответствующим участкам пролегания трубопровода. В табл. 2 представлены различные коррозионные среды, в которых находятся участки трубопровода.
28
Таблица 2 Характеристика модельных растворов, имитирующих различные коррозионные среды, в
которых эксплуатируется трубопровод
Коррозио |
pH |
Состав водной вытяжки, в мг |
|||||
нная |
|
на 100 г среды |
|
|
|
||
среда |
|
Na+K |
Ca |
|
Mg |
Cl |
SO |
|
|
|
|
|
|
|
2 |
|
|
|
|
|
|
|
4 |
Торфяная |
2,6 |
2,91 |
10, |
|
2,9 |
0,1 |
56,7 |
вода |
|
|
9 |
|
|
|
|
Болотная |
5,5 |
4,3 |
9,8 |
|
1,9 |
0,2 |
22,4 |
вода |
|
|
|
|
|
|
|
Речная |
6.5 |
8,1 |
3,3 |
|
0,8 |
0.4 |
16,7 |
вода |
|
|
|
|
6 |
|
|
Грунтово |
7,1 |
6,5 |
2,3 |
|
0,3 |
21, |
0,26 |
-песчаная |
|
|
|
|
4 |
3 |
|
вода |
|
|
|
|
|
|
|
Из табл. 2. видно, что наиболее агрессивной средой является торф, водная вытяжка которого имеет весьма кислую среду (pH = 2,6), а менее агрессивной является водная вытяжка болота. Для сравнения коррозионные испытания, проводимые также в 3 % - ном растворе NaCl, имитирующем морскую воду.
В табл. 3 представлены результаты гравиметрических исследований коррозионной стойкости трубной стали, в различных средах имитирующих возможные типы почвы пролегания магистрального трубопровода. Из данных таблицы следует, что с большей скоростью окисляется сталь в 3 % растворе NaCl, что очевидно, можно объяснить активирующим действием хлорид – ионов, разрушающих оксидную пленку на поверхности стали. Из природных сред с наибольшей скоростью происходит растворение стали в водной вытяжке торфа, что, обусловлено повышенной кислотностью данной среды, способствующей разрушению поверхности оксидной пленки на стали. В остальных средах скорость растворения заметно меньше, что можно объяснить их более низкой минерализацией и
пониженным содержанием H (нейтральная среда).
Процесс коррозии стали, во всех растворах протекает с кислородной деполяризацией по схеме:
А (-): Fe – 2e = Fe 2
К (+): O 2 + 2H 2 O + 4e = 4OH .
Для защиты стали от коррозии используют протекторы-металлы, чаще всего используют Mg, Al, Zn, которые при контакте с железом являются анодом в образующемся гальваническом элементе, заметно снижают скорость растворения основного металла. Защитное действие Mg-протектора достаточно эффективно в солевой среде, но при этом в менее агрессивной грунтово-песчаной воде Mg-протектор защищает в большей степени (рН = 7,1) Определенным недостатком Mg-протектора является то, что в процессе работы коррозионной пары А(-) Mg |NaCl, H2O| Fe К(+), он как более
активный металл коррозирует с водородной
деполяризацией:
A(-): Mg-2e- = Mg2+
K(+): 2H2O + 2e = H2 + 2OH ֿ .
В процессе работы этого коррозионного элемента выделяющийся газообразный водород, может снижать безопасность эксплуатации магистральных трубопроводов.
Таблица 3 Результаты коррозионных испытаний трубной стали в различных коррозионных средах (100 часов)
Корроз |
|
Масс |
Масса |
Потеря |
Скорос |
|
|||
ионная |
|
а |
|
образца |
массы |
ть |
|
|
|
среда |
|
|
образ |
после |
образца |
корроз |
|
||
|
|
|
ца |
до |
испыта |
, ∆ m, г |
ии, |
|
|
|
|
|
испы |
ния |
|
Vкорр |
|
||
|
|
|
таний |
(m2), г |
|
мг/см2∙ |
|
||
|
|
|
(m1), |
|
|
час |
|
|
|
|
|
|
г |
|
|
|
|
|
|
Торфян |
|
8,803 |
8,7938 |
0,0093 |
0,0241 |
|
|||
ая вода |
|
1 |
|
|
|
|
|
|
|
Болотн |
|
9,134 |
9,1284 |
0,0064 |
0,0123 |
|
|||
ая вода |
|
8 |
|
|
|
|
|
|
|
Речная |
|
10,04 |
10,0412 |
0,0033 |
0,0093 |
|
|||
вода |
|
|
45 |
|
|
|
|
|
|
Грунто |
|
9,596 |
9,5934 |
0,0028 |
0,0065 |
|
|||
во- |
|
|
2 |
|
|
|
|
|
|
песчана |
|
|
|
|
|
|
|
|
|
я вода |
|
|
|
|
|
|
|
|
|
3 |
% |
|
9,708 |
9,6980 |
0,0106 |
0,036 |
|
||
раствор |
|
6 |
|
|
|
|
|
|
|
NaCl |
|
|
|
|
|
|
|
|
|
|
|
По |
результатам |
исследований |
можно |
||||
сделать выводы: |
|
|
|
|
|
||||
|
1.В |
процессе |
исследований |
было |
|||||
установлено, что торфяные |
воды являются более |
коррозионно-агрессивными в сравнении с другими водами. Это обусловлено тем, что водная вытяжка торфа имеет, кислую среду (рН = 2,6), чем остальные исследуемые среды.
2.Скорость коррозии трубной стали в солевой коррозионной среде, имитация морского климата, больше, чем в других исследуемых средах (торфяная, болотная, речная и грунтово-песчаная воды).
Таким образом, можно заключить, что для защиты магистральных трубопроводов от внешней коррозии необходимо учитывать географические пространственные особенности территории, через которую пролегает участок трассы трубопровода для повышения безопасности их эксплуатации.
Литература 1. Смирнова В.В., Мартынюк В.Ф.
Прусенко Б.Е. и др. Анализ причин аварийности, мероприятий по предупреждению опасностей и ликвидации последствий аварий на объектах нефтегазодобычи, на нефтепроводах. Безопасность жизнедеятельности, №7, 2007. С. 33-39.
29

УДК 621.396.24
ИССЛЕДОВАНИЕ И АНАЛИЗ РЕШЕНИЙ ДЛЯ ПОВЫШЕНИЯ УРОВНЯ
ВЫСОКОЧАСТОТНОГО СИГНАЛА
Студент гр. РТм-151 Курганский А.Е. Руководитель: д-р техн. наук, доцент А.В. Останков
Предложена совокупность простых решений по оптимизации работы устройства передачи данных, включая антеннофидерный тракт, при приеме высокочастотных сигналов, отличающаяся оригинальным сочетанием, повлекшим снижение стоимости устройства
Антенна типа «волновой канал» [1,2], представленная на рис.1 и рассчитанная с помощью программы MathCad, имеет следующий список параметров:
количество элементов антенны – 5 шт;
количество директоров – 3 шт;
расстояние между директорами (d) (включая активный вибратор) – 2.9 см;
расстояние между рефлектором и активным вибратором (r)– 5.9 см;
длина директора (D) – 5.6 см;
длина рефлектора (R) – 8.8 см;
длина активного вибратора (A) – 6.1 см;
длина всей антенны (стрелы) (S) – 14.7 см;
диаметр трубки элемента антенны (алюминий, железо или медь) – 3.5 мм;
КНД
10; КЗД равен 0.169;
входное сопротивление антенны – 73 Ом.
Длина волны принимаемого сигнала – 14.7 см, частота f – 2045 МГц – средняя частота 3G диапазона.
Рис. 1. Вибраторная антенна типа волновой канал
Диаграмма направленности (ДН) в горизонтальной плоскости данной антенны приведена на рис.2. В вертикальной плоскости вид ДН аналогичен, при условии расположения в 2,5 – 3,5 см (см. рис.1 (h)) под антенной металлической пластины или решетки с величиной ячейки не более
0,1 (14,7 мм) c длиной (a) и шириной (b) 15 и10 см,
30
перекрывающей площадку антенны, с целью повышения множителя земли (антенна в таком случае сможет лучше принимать/передавать).
Рис. 2. Диаграмма направленности в полярных координатах
Согласование 4-х антенн, необходимое для увеличения общего производится следующим образом: стрелы директорных антенн располагаются
ввершинах квадрата со стороной (А) равной 15 см. К каждой из антенн подключается фидер с волновым сопротивлением 75 Ом. Все куски кабелей строго одинаковой длины. Конец каждого куска фидера рекомендуется обжать четвертьволновым стаканом, уменьшающим потери
впространство, и припаять к стакану оплетку; каждый из стаканов спаять вместе, как показано на рис.5. Длина каждого четвертьволнового стакана
равна . В качестве основного фидера рекомендуется использование коаксиального кабеля с волновым сопротивлением 50 Ом, так как модемы и различные ВЧ усилители имеют такое же входное сопротивление. Для согласования 4-х антенн с основным фидером используется четвертьволновый трансформатор. Необходимость в трансформаторе обусловлена подключением 4-х (антенных) фидеров к 1-му (основному). Технология изготовления
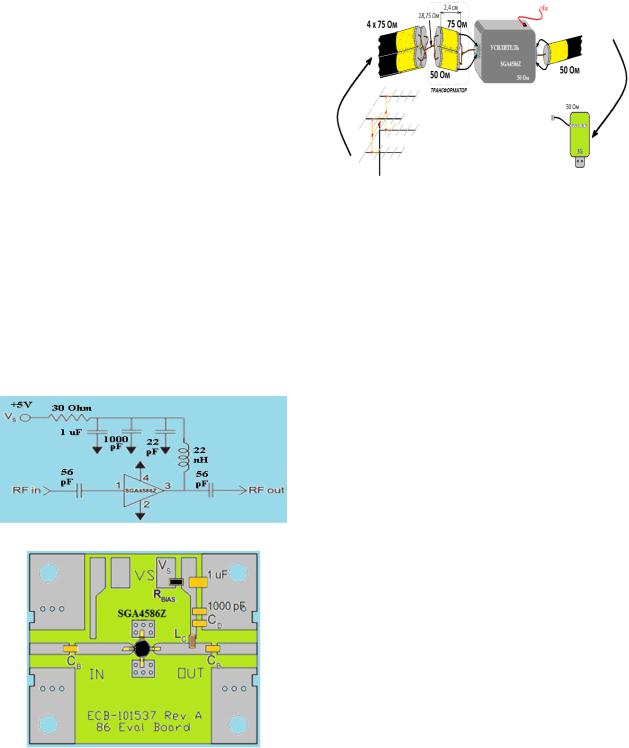
трансформатора сопротивлений приведена в [2]. Основные расчетные соотношения при изготовлении трансформаторов: (1), (2) (3).
Путем подбора разных комбинаций кусков 50омных и 75-омных фидеров, с помощью формулы (2), составляется трансформатор с наиболее близким к волновым сопротивлением.
Длина трансформатора с учетом укорочения длины волны в кабеле, по сравнению с длиной волны в пространстве, вычисляется по (3).
В представленном антенно-фидерном тракте используется трансформатор из 2-х кусков 50омного и 75-омного кабелей, длиною в 2.4 см. Для компенсации потерь в фидере целесообразно использовать высокочастотный операционный усилитель (ВЧ ОУ). Рассмотрим ВЧ ОУ SGA4586Z [3], схема которого представлена на рис.3:
коэффициент усиления не менее 17 дБ (на частотах от 1920 – 2170 МГц);
входное сопротивление – 50 Ом;
однополярное питание: (напряжение устройства
3,6 В);
максимальный ток потребления не более 90 мА;
относительно малая цена (в районе 3$ США).
Рис. 5. Активный согласованный антенно-фидерный тракт
Сигнал на входе основного 50-омного кабеля антенно-фидерного тракта (рис. 5) будет обладать усилением порядка 25 дБ.
Литература 1.Воскресенский Д.И. Антенны и
устройства СВЧ. Расчет и проектирование антенных решеток и их излучающих элементов. – М.: Советское радио, 1972. – 320 с.
2.Харченко К.П. УКВ антенны. – М.:
ДОСААФ, 1969. – 176 с.
3. Справочные данные на операционный усилитель SGA4586Z . – Электрон. Дан. – Режим доступа:http://www.rfmd.com/store/downloads/dl/file/i d/29515/ sga4586z
Рис. 3. Схема усилителя на SGA4586Z
Рис. 4. Вид печатной платы усилителя
Следует помнить, что получившуюся плату необходимо поместить в металлический (экранирующий) корпус для исключения влияния сторонних излучений.
В итоге, схема всего антенно-фидерного тракта, построение которого описано в данной статье, примет вид, как на рис.5.
31