
- •ИННОВАЦИОННАЯ ОРГАНИЗАЦИОННАЯ КУЛЬТУРА КАК ФАКТОР ПОВЫШЕНИЯ ИННОВАЦИОННОЙ ВОСПРИИМЧИВОСТИ
- •ИНТЕГРАЦИЯ ПЕРИФЕРИЙНЫХ УСТРОЙСТВ В СЧПУ ДЛЯ ПОВЫШЕНИЯ ПРОИЗВОДИТЕЛЬНОСТИ
- •ИССЛЕДОВАНИЕ ПРОЦЕССОВ ТЕПЛОМАССООБМЕНА В РАЗНОТЕМПЕРАТУРНОМ КОНДЕНСАЦИОННОМ ФИЛЬТРЕ
- •КОММУТАЦИОННЫЙ АППАРАТ СЕНСОРНОГО (ЁМКОСТНОГО) УПРАВЛЕНИЯ С ФУНКЦИЕЙ РЕГУЛИРОВАНИЯ ПЕРЕМЕННОГО НАПРЯЖЕНИЯ НА НАГРУЗКЕ
- •КОМПЛЕКС МОДЕЛИРОВАНИЯ ИНФОРМАЦИОННЫХ ЭПИДЕМИЙ В БЕЗМАСШТАБНЫХ СЕТЯХ
- •МЕТОДИКА ИЗГОТОВЛЕНИЯ ТРЕХСЛОЙНЫХ СОТОВЫХ ПАНЕЛЕЙ
- •МНОГОМЕТОДНАЯ ПОДСИСТЕМА ПОДДЕРЖКИ ПРИНЯТИЯ РЕШЕНИЙ НА ОСНОВЕ ПАРАЛЛЕЛЬНЫХ ГЕНЕТИЧЕСКИХ АЛГОРИТМОВ
- •МОДЕЛИРОВАНИЕ СИСТЕМЫ ПОЖАРНОЙ БЕЗОПАСНОСТИ ТЕХНОЛОГИЧЕСКОЙ ЛИНИИ ТЭП-50 НА ОАО «ВОРОНЕЖСИНТЕЗКАУЧУК»
- •НАНОТЕХНОЛОГИИ ДЛЯ ПОВЫШЕНИЯ ИЗНОСОСТОЙКОСТИ РАБОЧИХ ПОВЕРХНОСТЕЙ ИЗДЕЛИЙ
- •ОБЕСПЕЧЕНИЕ КАЧЕСТВА НАУКОЕМКОЙ ПРОДУКЦИИ И ИННОВАЦИОННАЯ ДЕЯТЕЛЬНОСТЬ
- •ОПТИМИЗАЦИЯ ПРОИЗВОДСТВЕННОГО ПРОЦЕССА НА ОСНОВЕ ТЕХНОЛОГИЙ БЕРЕЖЛИВОГО ПРОИЗВОДСТВА
- •ОПТИМИЗАЦИЯ СОСТАВА КЕРАМИЧЕСКИХ ОБОЛОЧЕК ДЛЯ ЛИТЬЯ ПО ВЫПЛАВЛЯЕМЫМ МОДЕЛЯМ
- •ПЛАЗМЕННЫЕ РАКЕТНЫЕ ДВИГАТЕЛИ – РЕВОЛЮЦИЯ В КОСМИЧЕСКИХ ПОЛЕТАХ
- •ПОРТАТИВНОЕ ЦИФРОВОЕ УСТРОЙСТВО, ПРЕДНАЗНАЧЕННОЕ ДЛЯ ОТОБРАЖЕНИЯ ТЕКСТОВОЙ И ГРАФИЧЕСКОЙ ИНФОРМАЦИИ, ПРЕДСТАВЛЕННОЙ В ЭЛЕКТРОННОМ ВИДЕ
- •ПОСТРОЕНИЕ ПРОГНОСТИЧЕСКИХ МОДЕЛЕЙ РАСПРОСТРАНЕНИЯ НЕФТИ
- •ПРИМЕНЕНИЕ КЛАСТЕРНОГО АНАЛИЗА ДЛЯ ОБРАБОТКИ ОШИБОЧНЫХ СРАБАТЫВАНИЙ С УЧЁТОМ ПРИОРИТЕТОВ ПАРАМЕТРОВ
- •ПРИМЕНЕНИЕ ТЕХНОЛОГИЙ СЕМАНТИЧЕСКОЙ ПАУТИНЫ ДЛЯ ПРОЕКТИРОВАНИЯ ОНТОЛОГИЙ И СИСТЕМ УПРАВЛЕНИЯ СОДЕРЖИМЫМ НА ИХ ОСНОВЕ
- •ПРОГРАММНЫЙ КОМПЛЕКС «NETEPIDEMIC» ДЛЯ РИСК-АНАЛИЗА ПРОЦЕССОВ РАСПРОСТРАНЕНИЯ ДЕСТРУКТИВНОГО КОНТЕНТА В НЕОДНОРОДНЫХ СЕТЕВЫХ СТРУКТУРАХ
- •ПРОГРАММНЫЙ КОМПЛЕКС РИСК-АНАЛИЗА РАСПРЕДЕЛЕННЫХ ИНФОРМАЦИОННЫХ СИСТЕМ
- •РАЗВИТИЕ СПОСОБОВ ТОЧНОЙ ШТАМПОВКИ
- •РАЗРАБОТКА ГИБРИДНЫХ ФУНКЦИОНАЛЬНЫХ МАТЕРИАЛОВ НА ОСНОВЕ НИКЕЛЯ
- •РАЗРАБОТКА МОДЕЛЕЙ И АЛГОРИТМОВ ИНТЕЛЛЕКТУАЛЬНОГО АНАЛИЗА КЛИЕНТСКИХ СРЕД НА ОСНОВЕ НЕЧЁТКИХ НЕЙРОННЫХ СЕТЕЙ
- •РАЗРАБОТКА СИСТЕМЫ ПЛАНИРОВАНИЯ СЕТИ И ОБЕСПЕЧЕНИЯ ДОСТУПА К ВЫСОКОСКОРОСТНОМУ СОЕДИНЕНИЮ КОНЕЧНОГО ПОЛЬЗОВАТЕЛЯ
- •РАЗРАБОТКА ЭЛЕМЕНТОВ ГИБРИДНОЙ СИСТЕМЫ ЛОКАЛЬНОЙ ТЕРМОСТАБИЛИЗАЦИИ ЭЛЕКТРОННЫХ МОДУЛЕЙ НА ОСНОВЕ МИКРОКАНАЛЬНЫХ ТЕПЛООБМЕННИКОВ И ТЕРМОЭЛЕКТРИЧЕСКИХ ПРЕОБРАЗОВАТЕЛЕЙ
- •СИСТЕМА АВТОМАТИЗИРОВАННОГО ПЛАНИРОВАНИЯ, ОПТИМИЗАЦИИ И УЧЕТА ШИРОКОПОЛОСНОГО РАДИОДОСТУПА И ЦИФРОВОГО ТВ
- •СОВРЕМЕННЫЕ ТЕХНОЛОГИИ, ИСПОЛЬЗУЮЩИЕСЯ В ПРОИЗВОДСТВЕ РАКЕТНО-КОСМИЧЕСКОЙ ТЕХНИКИ
- •СТРУКТУРА ЗОНДА СКАНЕРА БЛИЖНЕГО ПОЛЯ
- •ТЕХНИЧЕСКАЯ СИСТЕМА ОБЕСПЕЧЕНИЯ ЭКОЛОГИЧЕСКОЙ БЕЗОПАСНОСТИ НА ТЕПЛОВЫХ ЭНЕРГЕТИЧЕСКИХ УСТАНОВКАХ
- •ТЕХНОЛОГИИ 3D-ПЕЧАТИ В РАКЕТОСТРОЕНИИ
- •УСТРОЙСТВА ДЛЯ ОБРАБОТКИ ЗВУКА МУЗЫКАЛЬНЫХ ИНСТРУМЕНТОВ В РЕЖИМЕ РЕАЛЬНОГО ВРЕМЕНИ
- •ЭЛЕКТРИЧЕСКИЕ РАКЕТНЫЕ ДВИГАТЕЛИ – ДВИГАТЕЛИ БУДУЩЕГО
- •ЭНЕРГОСБЕРЕЖЕНИЕ В РАЗДЕЛИТЕЛЬНЫХ ОПЕРАЦИЯХ

УДК 681.2.084
СТРУКТУРА ЗОНДА СКАНЕРА БЛИЖНЕГО ПОЛЯ
Аспирант кафедры АВС Глотов В.В. Руководитель: д-р техн. наук, доцент М.А. Ромащенко
В статье представлены описания структур зондов ближнего электромагнитного поля
Зонды ближнего поля являются инструментами для пространственноколичественной оценки излучений от печатной платы. Зонды реагируют определенным образом на ближнее поле и могут быть подключены к анализатору спектра для отображения в частотной области. Идеальный зонд должен выбрать только один из трех ортогональных компонентов электрического или магнитного поля. Малая конструкция петли и стержень конструкции, как правило, используются для Н-полевых и Е-полевых зондов, так как они имеют максимальную направленность вдоль некоторой оси.
Все H-зонды и Е-зонды построены с использованием полужестких коаксиальных кабелей, как показано на рисунках 1-3. Н-зонд содержит один виток, как показано на рисунке 1. Он изготовлен из 50 Ом полужесткого коаксиального кабеля и согнутого его в петлю, которая улавливает излучения поля перпендикулярно к отверстию контура. Внешний и внутренний проводник припаиваются к внешнему кабелю. Затем проводник разрезается в верхней точке петли. Три ортогональных компонент H поля, Hx, Hy, а Нz, измеряют путем вращения зонда, чтобы выровнять контур в нужное направление.
Рис.1. Н – зонд с петлевой структурой Е-зонд 1, как показано на рисунке 2,
предназначен для измерения вертикальной составляющей Ez предполагая, что тестирующее устройство находится в горизонтальной плоскости (плоскости ху). Он изготовлен из цельного куска кабеля 50 Ом из полужесткого коаксиального кабеля с коротким внутренним проводником, экспонированный на наконечнике, который служит в качестве несимметричной антенной, составляющую поля Е вдоль нее. Поскольку нет никакой дополнительной структуры петли для проводимости тока, устройство имеет высокое отторжение к полю Н.
Рис.2. Е – зонд со стержневой структурой Второй Е-зонд, как показано на рисунке 3,
предназначен для измерения тангенциальных компонент Ех и Еу. Это сбалансированный дипольный провод, состоящий из двух 50 Ом полужестких коаксиальных кабелей и 180º - ого гибридного ответвителя. Внешние проводники двух кабелей спаяны вместе и имеющие одинаковую длину внутренних проводников, подвергаются сгибанию на 90º с образованием дипольной проволоки. Оголенные дипольный провод подхватывает тангенциальную компоненту Е-поля.
Рис.3. Е- зонд с сбалансированным диполем Выходные сигналы двух кабелей
поступают на входные порты на 180º-ый гибридный ответвитель, чтобы сбалансировать реакцию зонда. Если разделение двух проводов значительно меньше, чем длина волны измеряемого поля, паразитные реакции двух кабелей можно считать идентичными. Тогда разностный сигнал на выходе 180º соответствует желаемому соединению с тангенциальной составляющей Е-поля.
Литература
1.Князев А. Д., Кечиев Л. Н.Конструирование радиоэлектронной и электронновычислительной аппаратуры с учетом электромагнитной совместимости. – М.:Радио и связь, 1989. – 224с.
2.http://emc-problem.net
136

УДК 622.271
ТЕХНИЧЕСКАЯ СИСТЕМА ОБЕСПЕЧЕНИЯ ЭКОЛОГИЧЕСКОЙ БЕЗОПАСНОСТИ НА ТЕПЛОВЫХ ЭНЕРГЕТИЧЕСКИХ УСТАНОВКАХ
Студент гр. ЗС-121 Завьялова А.Ю. Руководитель: канд. техн. наук, доцент А.В. Звягинцева
В работе рассматриваются вопросы разработки систем автоматизированного контроля параметров тепловых энергоустановок для обеспечения их безопасности. Применение данной системы сводит к минимуму вероятность принятия ошибочного решения в случае возникновения чрезвычайной ситуации.
Современные энергоустановки являются по- тенциально-опасными объектами, и к их системам жизнеобеспечения предъявляются очень жесткие требования, связанные с охраной окружающей среды. Перечислим основные требования, предъявляемые к современной системе обеспечения безопасности тепловых энергоустановок:
система должна позволять в реальном времени контролировать параметры безопасности энергоустановки;
все контролируемые параметры должны быть визуально представлены оператору на экране монитора;
система должна хранить историю изменения каждого из контролируемых параметров;
по запросу оператора система должна выдавать отчет о состоянии контролируемых параметров за указанный промежуток времени;
в случае угрозы возникновения чрезвычайной ситуации система должна информировать оператора об этом и предлагать оптимальный вариант решения проблемы;
в случае угрозы жизням людей система должна самостоятельно подавать команду эвакуации персонала из зоны риска.
Аппаратная часть системы отвечает за измерение контролируемых параметров энергоустановки, программная – за анализ результатов этих измерений. Шина данных обеспечивает передачу результатов измерения в ЭВМ и трансформацию их в вид, пригодный для программного анализа. Структурная схема программного обеспечения предлагаемой системы представлена на рис. 1.
Интерфейс
пользователя
Подсистема |
|
|
|
|
Подсистема |
|
|
СППР |
|
формирования |
|
ввода/вывода |
|
|
|
||
|
|
|
|
отчетов |
|
|
|
|
|
|
|
|
|
|
|
|
|
База данных
Рис. 1. Структура программной части системы Аппаратная часть системы состоит из ЭВМ и
подсистем мониторинга и оповещения. Подсистема мониторинга отвечает за измерение контролируе-
мых параметров и передачу результатов измерений в ЭВМ [1]. Подсистема ввода/вывода предназначена для приема данных от подсистемы мониторинга и преобразования их в вид.
Реализация подсистемы ввода/вывода данных зависит от интерфейса. Если для вывода сигнала на усилители подсистемы оповещения надежнее всего использовать линейный выход звуковой карты ЭВМ, то сигналы с датчиков подсистемы мониторинга могут поступать несколькими способами: по COM, LPT или USB интерфейсам.
Система поддержки принятия решений в разрабатываемой системе является центральным элементом системы [2]. В функции СППР входит: анализ данных, приходящих от датчиков подсистемы мониторинга; оповещение оператора о возникшей нештатной ситуации; выработка оптимального метода устранения неисправности; принятие решения о включении подсистемы оповещения персонала. Блок-схема алгоритма системы поддержки принятия решений представлена на рис. 2.
Как видно из этого рисунка, после включения системы начинается бесконечный цикл опроса датчиков подсистемы мониторинга. Первым этапом этого алгоритма является анализ неисправности – система определяет причину возникшей неисправности и ее возможные последствия. Если в результате возникшей неисправности риску подвергаются жизни рабочих – происходит включение системы оповещения персонала, начинается его эвакуация с территорий, подверженных опасности.
|
Начало |
|
|
|
Опрос датчиков |
|
Включение системы |
подсистемы мониторинга |
оповещения |
||
|
|
|
Запрос в БД о |
нет |
Наличие |
|
возможных путях |
|
неисправности |
|
устранения проблемы |
|
|
|
|
|
да |
|
Выбор оптимального |
|
Анализ неисправности |
|
пути устранения |
|
|
проблемы |
|
|
|
|
|
|
Угроза жизни |
да |
Вывод сообщения |
|
|
оператору |
|
|
|
|
|
|
нет |
|
|
|
Рис. 2. Алгоритм работы СППР |
137

После этого СППР, в соответствии с описанием возникшей неисправности, извлекает из базы данных способы ее устранения. В общем случае таких способов может быть несколько, каждый из них характеризуется набором параметров: скоростью устранения проблемы, надежностью, побочными эффектами и т.п.
После того, как сформирован список методов решения проблемы, он выводится на экран монитора оператора, при этом вариант с максимальной надежностью и минимальным риском для персонала отмечается как рекомендуемый системой поддержки принятия решений. После этого система, не дожидаясь действий оператора, переходит к следующему циклу опроса датчиков.
В случае возникновения нештатной ситуации это позволит установить ее причины, а в случае возникновения неисправности в одном из модулей программного обеспечения – не приведет к потере данных. Внешний вид главного окна программы, реализующей интерфейс пользователя разрабатываемой системы, в режиме контроля параметров приведен на рис. 3.
Как видно на рисунке 3. интерфейс пользователя позволяет оператору полностью контролировать ситуацию в котельной. Для всех котлов приведен полный список контролируемых параметров, для каждого из них есть возможность отобразить график изменения с течением времени (в приведенном на рисунке случае отображается график изменения давления в котле). В случае возникновения нештатной ситуации (в данном случае – отсутствия пламени в котле номер 3) оператору выдается сообщение, содержащее рекомендации по устранению неисправности. В этом же сообщении указывается необходимость эвакуации персонала. В случае возникновения угрозы здоровью персонала включается система оповещения, а оператору выдается сообщение.
АРМ – Режим контроля параметров
Файл Режим Установки Вид Справка
Котел 1
Контролируемый параметр |
|
Значение |
|
||||
Температура газа на входе |
|
|
30 |
|
|
||
Давление газа на входе |
|
|
1,5 |
|
|
||
Расход газа на входе |
|
|
24 |
|
|
||
Давление воздуха на входе |
|
|
1,02 |
|
|
||
Давление воды на входе |
|
|
0,7 |
|
|
||
Температура продуктов сгорания |
|
115 |
|
|
|||
Давление в котле |
|
|
1,54 |
|
|
||
Расход воды |
|
|
902 |
|
|
||
Давление воды на выходе |
|
|
2,3 |
|
|
||
Температура воды на выходе |
|
|
107 |
|
|
||
|
Отображать график |
|
|
|
|
|
|
|
|
|
|
|
|
|
|
|
Давление в котле |
|
|
|
|
|
|
|
|
|
|
|
|
|
|
|
|
|
|
|
|||
P |
Выбрать параметр |
|
|||||
2 |
|
|
|
|
|
|
|
1 |
|
|
|
|
|
|
|
|
|
|
|
|
t |
||
14:12 14:13 14:14 |
14:15 |
14:16 |
|
Котел 2
Контролируемый параметр |
Значение |
Температура газа на входе |
31 |
Давление газа на входе |
1,5 |
Расход газа на входе |
22 |
Давление воздуха на входе |
1,03 |
Давление воды на входе |
0,7 |
Температура продуктов сгорания |
113 |
Давление в котле |
1,58 |
Расход воды |
860 |
Давление воды на выходе |
2,1 |
Температура воды на выходе |
104 |
Отображать график
Котел 3
Контролируемый параметр |
Значение |
Температура газа на входе |
30 |
Давление газа на входе |
1,5 |
Расход газа на входе |
0 |
Давление воздуха на входе |
1,02 |
Давление воды на входе |
0,7 |
Температура продуктов сгорания |
21 |
Давление в котле |
1 |
Расход воды |
0 |
Давление воды на выходе |
0 |
Температура воды на выходе |
0 |
Пламя отсутствует!
Рекомендации по устранению:
-проверить подачу газа;
-прочистить форсунку.
Эвакуация персонала: не требуется
Параметры котлов: авария на котле 3 Загазованность в помещении котельной: отсутствует |
Котлы: 3 из 3 |
Рис. 3. Главное окно программы в режиме контроля параметров
Как видно из этого рисунка, интерфейс пользователя позволяет оператору полностью контро-
лировать ситуацию в котельной. Для всех котлов приведен полный список контролируемых параметров, для каждого из них есть возможность отобразить график изменения с течением времени (в приведенном на рисунке случае отображается график изменения давления в котле). В случае возникновения нештатной ситуации (в данном случае – отсутствия пламени в котле номер 3) оператору выдается сообщение, содержащее рекомендации по устранению неисправности. В этом же сообщении указывается необходимость эвакуации персонала.
При необходимости формирования отчета по результатам контроля параметров безопасности появляется диалоговое окно в котором оператор выбирает номер котла, для параметров которого формируется отчет, параметры, в него включаемые, и формат выходных данных. Программа позволяет формировать отчеты в стандартных форматах: HTML, PDF, MS Word, Open Office XML. Также указывается отчетный период, данные за который включаются в отчет.
Разработанная система обладает следующими преимуществами [1, 2]:
Отображение в реальном времени текущего состояния рабочих параметров котлов;
Выдача аварийных и предупредительных сообщений при достижении контролируемыми параметрами опасных значений технологических уставок;
Хранение и ввод технологических установок;
Учет времени работы каждого котла;
Формирование текущих (оперативных) и «исторических» (долговременных) архивов контролируемых параметров;
Формирование журнала событий;
Расчет количества выработанного тепла по каждому котлу в отдельности и всей энергоустановке в целом.
Таким образом, применение предлагаемой системы обеспечения безопасности позволит существенно снизить риск возникновения чрезвычайных ситуаций на тепловых энергоустановках. Наличие в ней разветвленной системы датчиков позволяет выявить возникающие проблемы на ранних стадиях, а алгоритм работы СППР предоставляет оператору не только информацию о возникновении нештатной ситуации, но и ее вероятную причину, а также рекомендуемый оптимальный способ ее устранения.
Литература 1. Белинов С.В., Зайцев А.А. Современные
информационные технологии. - М.: Инфра-М,
2003.- 450 с.
2. Каpатыгин С.Н. Базы данных: простейшие средства обработки информации; системы управления базами данных. - М.: ABF, 2002.- 370 с.
138
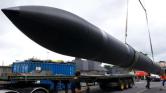
УДК 681.2; 621.9.047
ТЕХНОЛОГИИ 3D-ПЕЧАТИ В РАКЕТОСТРОЕНИИ
Гришина Е.Н.
Руководитель: д-р техн. наук, доцент О.Н. Кириллов
В работе рассмотрено внедрение инновационных способов прототипирования, таких как 3D-печать в ракетостроении, печать деталей ракетного двигателя на 3D-принтере,ракетные двигатели «Резерфорд», «SuperDraco», отечественные 3D-технологии и их роль в производстве деталей для авиакосмических двигателей
Введение
В настоящее время во многих направлениях высокотехнологичного производства человечество начинает упираться в потолок технических возможностей традиционных методов обработки материалов. Внедрение инновационных способов прототипирования и производства, таких как 3Dпечать, позволяет перешагнуть эти барьеры и реализовать самые смелые идеи конструкторов и ученых. Применение трехмерной печати все больше влияет на ускорение внедрений прорывных идей в дизайне, машиностроении и, конечно, ракетостроении. [1]
Основные части ракеты, построенные с использованием технологии 3D-печати, прошли еще один этап огневых испытаний НАСА, укрепляя доверие к новой технологии производства. Две ракетные форсунки, сделанные при помощи 3Dпринтера, во время испытаний вели себя аналогично деталям, произведенным традиционным способом. Детали подвергались температурам до 3316 градусов Цельсия под экстремальным давлением.
Данные исследования помогают НАСА оценить потенциал технологии 3D-печати, которая может сделать исследования космоса дешевле и эффективнее.
Форсунки, напечатанные на 3D-принтере, подверглись серии из 11 испытаний с общим временем горения в 46 секунд. Детали успешно прошли испытания и остались в отличном состоянии. Однако, на производство традиционных форсунок требуется 10 000 долларов и 6 месяцев работы, в то время как напечатанная версия обходится в 5 000 долларов и несколько недель работы. Сам процесс печати занял около 40 часов, еще пару недель понадобилось на полировку и осмотр детали.
По всей видимости, НАСА видит большие перспективы в технологии 3D-печати. Уже сейчас, агентство сотрудничает с калифорнийской фирмой "MadeinSpace" и планирует отправить 3D-принтер на Международную космическую станцию. [2]
1. RocketLab Electron
История компании RocketLab уходит корнями
в 2007 год, когда Питер Бек |
основал небольшую |
аэрокосмическую фирму в |
Окленде, Новая |
Зеландия, как центр передовых космических программ.
В 2009 году они запустили суборбитальную метеорологическую ракету Вtea–1 («космос» на Маори) — она имела 6 метров в длину и весила 60 кг, и имела возможность выводить 2 кг полезной нагрузки на высоту до 120 км. И вот сейчас RocketLab представляет углекомпозитную ракету– носитель Electron с первыми в мире напечатанными на 3d–принтере двигателями Rutherford, снабженные электроприводом топливных насосов и работающими на крайне необычном высокоплотном монотопливе. [3]
1.1. Ракета–носитель «Электрон»
Двухступенчатая ракета легкого класса Electron высотой 18 метров, способна доставить до 400 кг на низкую околоземную орбиту или до 110 кг полезной нагрузки на гелиосинхронную (до 500 км) за $4,9 млн, была презентована в июле 2014 года. В конструкции ракеты чрезвычайно широко применяются самые современные углеволоконные композитные материалы, в том числе и для головного абляционного покрытия.
На первой ступени установлены 9 двигателей Rutherford, на второй — один переработанный Rutherford для более эффективной работы в вакууме, отличающийся только формой сопла, основная конструкция — идентична, для обеспечения высокой скорости процесса производства.
Ракета располагает самой современной авионикой, а также, находящейся на стадии разработки, парашютной системой спасения. [3]
2 марта 2015 года произошла погрузка РН «Электрон» на трейлер для транспортировки. (Рис.1)
Рис.1. Погрузка РН «Электрон» на трейлер для транспортировки 2 марта 2015 г
139
1.2 Двигатель «Резерфорд»
Названный в честь великого британского физика новозеландского происхождения Эрнеста Резерфорда, революционный ракетный двигатель
Rutherford |
представляет |
собой |
керосино– |
кислородный |
гибридный |
двигатель с |
|
регенеративным охлаждением. |
|
|
|
Подавляющее большинство |
компонентов |
(камеры сгорания, форсунки, турбонасосы и клапаны подачи горючего) изготовлены на 3d– принтере, а именно, — методом электронно– лучевой плавки (EBM), весьма схожей с более известным методом выборочного лазерного спекания (SLS), но производящий спекание или плавку металлических порошков с помощью электронных пучков вместо лазеров.
Тяга «Резерфорда» — 20,5 кН у земли, удельный импульс — 327 с.
Двигатель интересен еще и тем, что подача топлива и окислителя осуществляется с помощью вентильного электрического турбонасоса мощностью 37 кВт с питанием от литий– полимерных аккумуляторов. При этом размер каждого электродвигателя «не больше банки газировки, это весьма нетривиальная вещь, — изготовить электродвигатель такой удельной мощности», — отмечает Бек.
На данный момент RocketLab завершила огневые испытания Rutherford, показавшие высокую стабильность работы двигателя, и занимается научно–исследовательской работой в области дальнейшего усовершенствования характеристик. [3]
Руководство компании говорит, что 3D-печать позволяет изготовлять сложные и легкие конструкции из таких материалов, как титан и другие сплавы. Это способствует уменьшению времени сборки от нескольких месяцев до нескольких дней и увеличению доступности компонентов.
RocketLab является не первой аэрокосмической компанией, применившей в своем производстве технологию трехмерной печати. Airbus уже использует в своих самолетах A350 детали, произведенные тем же методом. Однако, по словам Бека, RocketLab первой широко применила 3D-печать для изготовления космического аппарата.
Коммерческие запуски Electron планируется начать в 2016 году. [4]
2. Ракетный двигатель SpaceX «SuperDraco»
Компания SpaceX в настоящий момент занимается модифицированием своей космической капсулы Dragon и объявила об успешном окончании одного из первых испытаний нового ракетного двигателя SuperDraco. Новые двигатели призваны заменить ракетные двигатели Draco, ныне использующиеся компанией SpaceX для пространственной ориентации их космических
140
кораблей. Помимо этого, двигатели SuperDracoбудут использоваться также в качестве системы аварийного спасения при запусках кораблей Dragon, а также для посадки капсулы на Землю, а возможно, и на другие планеты.
Одним из самых заметных отличий новых ракетных двигателей SuperDraco от большинства других подобных систем является то, что его камера сгорания создана на основе 3D-печати, при использовании метода прямого лазерного спекания металла, где сложные металлические структуры создаются при использовании специальной лазерной установки, которая в буквальном смысле «выпекает» слой за слоем из металлической пыли готовую деталь. Сама же камера сгорания с регенеративным охлаждением производится из инконеля, жаростойкого хромоникелевого сплава, характеризующегося высокой прочностью. Такой сплав также используется, например, при постройке двигателей Merlin, используемых в ракетах Falcon 9.
В качестве топлива такие двигатели используют смесь из некриогенных жидкостей: монометил-гидразин в качестве самого топлива и азотныйтетроксид в качестве окислителя. Похожий состав используется и в двигателях Draco. Смесь самовоспламеняемая, то есть при контакте составных компонентов друг с другом они воспламеняются. Благодаря этому, у ракетных двигателей SuperDraco имеется возможность повторных перезапусков. При этом новые двигатели построены с расчетом быстрого зажигания. От запуска до полной подачи топлива требуется всего 100 миллисекунд. Но самым важным отличием ракетных двигателей SuperDraco является то, что они 200 раз мощнее двигателей Draco, развивающих тягу в 16 400 lb.
Основной задачей ракетных двигателей SuperDraco является обеспечение пространственной ориентации капсулы Dragon на орбите, а также во время ее обратного вхождения в атмосферу. Кроме того, они используются для системы аварийного покидания на старте. В отличие от предыдущих пилотируемых космических капсул, использовавшихся в США в 1960-х и 1970-х годах прошлого века, следующая версия капсулы Dragon не будет использовать специальную страховочную систему, которая позволила бы в любой момент убрать капсулу прочь при неудачном старте. Сама капсула Dragon, используя все восемь двигателей, способна за пять секунд в буквальном смысле отлететь от взлетной зоны, развив при этом тягу в 120 000 lb. Помимо этого, наличие восьми двигателей повышает уровень эффективности всей системы в случае, когда один или несколько двигателей могут выйти из строя.
Но самой амбициозной идеей за созданием нового ракетного двигателя SuperDraco является то, что, капсула Dragon разработана с возможностью мягкой посадки своими собственными силами.

SpaceX даже рассматривает возможность использования ракетных двигателей SuperDraco в качестве посадочных двигателей для будущего беспилотного корабля RedDragon, задачей которого будет посадка на Марс. [5]
3. Печать деталей ракетного двигателя на 3D-принтере
В НАСА при помощи технологий 3D-печати построили деталь ракетного двигателя из жаростойкого материала, представленный на рис. 2. Вкладыш для камеры сгорания напечатан из медного сплава GRCo-84, разработанного в НАСА, методом спекания металлического порошка лазером (SLS).
Рис. 2
Процесс печати занял более 10 суток, финальная деталь состоит из 8255 спеченных между собой слоев.
"Медь очень хорошо проводит тепло, – объясняет Зак Джонс, материаловед, руководивший 3D-печатью детали. – Именно поэтому этот металл
– идеальный материал для вкладыша камеры сгорания, равно как и других деталей. Но в то же время эти свойства меди осложняют 3D-печать, т.к. лазеру сложно расплавить медный порошок".
Данная деталь работает в условиях сильных перепадов температур: в камеру сгорания подаются сверххолодные компоненты ракетного топлива, которые сгорают с выделением большого количества тепла.
Крис Сингер, директор технического управления Космического центра им. Маршалла, объясняет подробнее: "Температура внутри камеры сгорания достигает 2700°С, поэтому нам нужно защитить вкладыш от плавления, обдувая его газами, охлажденными менее чем до 100 градусов выше абсолютного нуля. Для циркуляции газа внутри стенок вкладыша сделано более 200 тонких каналов. Именно создание этих каналов сложной конфигурации и представляло основную сложность для наших экспертов в аддитивном производстве".
Производство медного вкладыша – это первый шаг в рамках проекта НАСА по снижению стоимости ракетных двигателей. Готовый вкладыш инженеры отошлют в исследовательский центр НАСА в Ленгли, где на него нанесут покрытие из никелевого суперсплава. [6]
141
4. Отечественные 3D-технологии и их роль в производстве деталей для
авиакосмических двигателей
Применении аддитивных технологий в аэрокосмической сфере принадлежит команде молодых ученых из Самары и Санкт-Петербурга. Они объявили о разработке нового 3D-принтера, способного печатать тугоплавкими и жаростойкими металлами. Новую установку планируют использовать с целью создания крупных узлов и деталей для авиакосмических двигателей.
Молодые ученые хотят создать аналог
ElеctronBeаmАdditiveMаnufacturing, то есть одновременно подводить и энергию, и материал для построения. С этой целью команда СГАУ активно занимается разработкой уникального сопла, с помощью которого и будет осуществляться подача материала. Такая технология намного эффективнее обычного наплавления металла.
Сегодня подобный подход мало кем используется. Только американская компания Sciaky применяет EBAM-технологию. (Аббревиатура «EBAM» означает «Аддитивное производство с использование электронных пучков».)
Если все сложится успешно, то мы сможем составить этому производителю неплохую конкуренцию. Хотя заявленная технология не может называться клоном ЕВАМ, так как специальный канал будет осуществлять подачу порошка, а оптическая система будет контролировать его распределение. [7]
Заключение
Таким образом, 3D-печать имеют большое значение для ракетостроения, так как экономит деньги, а главное время, необходимое на постройку
исборку космической техники.
ВНАСА полагают, что 3D-печать может совершить в космонавтике настоящую революцию, ведь помимо экономии на производстве космической техники, появилась возможность наладить производство в космосе. В настоящее время НАСА вместе с компанией MadeinSpace разрабатывает для МКС 3D-принтер, на котором можно будет напечатать любые инструменты. Также в НАСА изучают возможность печати пищи в длительных космических полетах. Эксперты полагают, что в будущем исследование космоса будет опираться на 3D-печать, которая позволяет производить непосредственно на месте все необходимое для отдыха и работы: от чайной ложки, до бетонного купола-укрытия.
Литература 1. Применение аддитивных технологий при
проектировании и прототипировании узлов и блоков для ракетно-космических систем. — Электронный документ
— Режим доступа:
http://www.nanonewsnet.ru/news/2014/primenenie- additivnykh-tekhnologii-pri-proektirovanii-prototipirovanii- uzlov-blokov-dlya-r
2. Технология 3D-печати в строительстве ракет. — Электронный документ — Режим доступа: http://www.lassy.ru/news/331-tehnologiya-3d-pechati-v- stroitelstve-raket.html
3.RocketLab Electron. — Электронный документ — Режим доступа: https://cosmos.dirty.ru/rocket-lab-electron- 722155/
4.Rocketlab представила первый 3d-напечатанный батарейный двигатель для ракеты-носителя — Электронный документ — Режим доступа: http://hi- news.ru/technology/rocket-lab-predstavila-pervyj-3d- napechatannyj-batarejnyj-dvigatel-dlya-rakety-nositelya.html
5.Spacex провела первые испытания нового ракетного двигателя Superdraco. — Электронный документ — Режим доступа: http://hi- news.ru/technology/spacex-provela-pervye-ispytaniya- novogo-raketnogo-dvigatelya-superdraco.html
6. Печать деталей ракетного двигателя на 3Dпринтере.— Электронный документ — Режим доступа: http://innogest.ru/m?na=11467
7.Как аддитивные технологии помогают в ракетостроении и авиакосмической отрасли? — Электронный документ — Режим доступа:http://make- 3d.ru/news/kak-additivnye-texnologii-pomogayut-v- raketostroenii-i-aviakosmicheskoj-otrasli/
142