
- •ИННОВАЦИОННАЯ ОРГАНИЗАЦИОННАЯ КУЛЬТУРА КАК ФАКТОР ПОВЫШЕНИЯ ИННОВАЦИОННОЙ ВОСПРИИМЧИВОСТИ
- •ИНТЕГРАЦИЯ ПЕРИФЕРИЙНЫХ УСТРОЙСТВ В СЧПУ ДЛЯ ПОВЫШЕНИЯ ПРОИЗВОДИТЕЛЬНОСТИ
- •ИССЛЕДОВАНИЕ ПРОЦЕССОВ ТЕПЛОМАССООБМЕНА В РАЗНОТЕМПЕРАТУРНОМ КОНДЕНСАЦИОННОМ ФИЛЬТРЕ
- •КОММУТАЦИОННЫЙ АППАРАТ СЕНСОРНОГО (ЁМКОСТНОГО) УПРАВЛЕНИЯ С ФУНКЦИЕЙ РЕГУЛИРОВАНИЯ ПЕРЕМЕННОГО НАПРЯЖЕНИЯ НА НАГРУЗКЕ
- •КОМПЛЕКС МОДЕЛИРОВАНИЯ ИНФОРМАЦИОННЫХ ЭПИДЕМИЙ В БЕЗМАСШТАБНЫХ СЕТЯХ
- •МЕТОДИКА ИЗГОТОВЛЕНИЯ ТРЕХСЛОЙНЫХ СОТОВЫХ ПАНЕЛЕЙ
- •МНОГОМЕТОДНАЯ ПОДСИСТЕМА ПОДДЕРЖКИ ПРИНЯТИЯ РЕШЕНИЙ НА ОСНОВЕ ПАРАЛЛЕЛЬНЫХ ГЕНЕТИЧЕСКИХ АЛГОРИТМОВ
- •МОДЕЛИРОВАНИЕ СИСТЕМЫ ПОЖАРНОЙ БЕЗОПАСНОСТИ ТЕХНОЛОГИЧЕСКОЙ ЛИНИИ ТЭП-50 НА ОАО «ВОРОНЕЖСИНТЕЗКАУЧУК»
- •НАНОТЕХНОЛОГИИ ДЛЯ ПОВЫШЕНИЯ ИЗНОСОСТОЙКОСТИ РАБОЧИХ ПОВЕРХНОСТЕЙ ИЗДЕЛИЙ
- •ОБЕСПЕЧЕНИЕ КАЧЕСТВА НАУКОЕМКОЙ ПРОДУКЦИИ И ИННОВАЦИОННАЯ ДЕЯТЕЛЬНОСТЬ
- •ОПТИМИЗАЦИЯ ПРОИЗВОДСТВЕННОГО ПРОЦЕССА НА ОСНОВЕ ТЕХНОЛОГИЙ БЕРЕЖЛИВОГО ПРОИЗВОДСТВА
- •ОПТИМИЗАЦИЯ СОСТАВА КЕРАМИЧЕСКИХ ОБОЛОЧЕК ДЛЯ ЛИТЬЯ ПО ВЫПЛАВЛЯЕМЫМ МОДЕЛЯМ
- •ПЛАЗМЕННЫЕ РАКЕТНЫЕ ДВИГАТЕЛИ – РЕВОЛЮЦИЯ В КОСМИЧЕСКИХ ПОЛЕТАХ
- •ПОРТАТИВНОЕ ЦИФРОВОЕ УСТРОЙСТВО, ПРЕДНАЗНАЧЕННОЕ ДЛЯ ОТОБРАЖЕНИЯ ТЕКСТОВОЙ И ГРАФИЧЕСКОЙ ИНФОРМАЦИИ, ПРЕДСТАВЛЕННОЙ В ЭЛЕКТРОННОМ ВИДЕ
- •ПОСТРОЕНИЕ ПРОГНОСТИЧЕСКИХ МОДЕЛЕЙ РАСПРОСТРАНЕНИЯ НЕФТИ
- •ПРИМЕНЕНИЕ КЛАСТЕРНОГО АНАЛИЗА ДЛЯ ОБРАБОТКИ ОШИБОЧНЫХ СРАБАТЫВАНИЙ С УЧЁТОМ ПРИОРИТЕТОВ ПАРАМЕТРОВ
- •ПРИМЕНЕНИЕ ТЕХНОЛОГИЙ СЕМАНТИЧЕСКОЙ ПАУТИНЫ ДЛЯ ПРОЕКТИРОВАНИЯ ОНТОЛОГИЙ И СИСТЕМ УПРАВЛЕНИЯ СОДЕРЖИМЫМ НА ИХ ОСНОВЕ
- •ПРОГРАММНЫЙ КОМПЛЕКС «NETEPIDEMIC» ДЛЯ РИСК-АНАЛИЗА ПРОЦЕССОВ РАСПРОСТРАНЕНИЯ ДЕСТРУКТИВНОГО КОНТЕНТА В НЕОДНОРОДНЫХ СЕТЕВЫХ СТРУКТУРАХ
- •ПРОГРАММНЫЙ КОМПЛЕКС РИСК-АНАЛИЗА РАСПРЕДЕЛЕННЫХ ИНФОРМАЦИОННЫХ СИСТЕМ
- •РАЗВИТИЕ СПОСОБОВ ТОЧНОЙ ШТАМПОВКИ
- •РАЗРАБОТКА ГИБРИДНЫХ ФУНКЦИОНАЛЬНЫХ МАТЕРИАЛОВ НА ОСНОВЕ НИКЕЛЯ
- •РАЗРАБОТКА МОДЕЛЕЙ И АЛГОРИТМОВ ИНТЕЛЛЕКТУАЛЬНОГО АНАЛИЗА КЛИЕНТСКИХ СРЕД НА ОСНОВЕ НЕЧЁТКИХ НЕЙРОННЫХ СЕТЕЙ
- •РАЗРАБОТКА СИСТЕМЫ ПЛАНИРОВАНИЯ СЕТИ И ОБЕСПЕЧЕНИЯ ДОСТУПА К ВЫСОКОСКОРОСТНОМУ СОЕДИНЕНИЮ КОНЕЧНОГО ПОЛЬЗОВАТЕЛЯ
- •РАЗРАБОТКА ЭЛЕМЕНТОВ ГИБРИДНОЙ СИСТЕМЫ ЛОКАЛЬНОЙ ТЕРМОСТАБИЛИЗАЦИИ ЭЛЕКТРОННЫХ МОДУЛЕЙ НА ОСНОВЕ МИКРОКАНАЛЬНЫХ ТЕПЛООБМЕННИКОВ И ТЕРМОЭЛЕКТРИЧЕСКИХ ПРЕОБРАЗОВАТЕЛЕЙ
- •СИСТЕМА АВТОМАТИЗИРОВАННОГО ПЛАНИРОВАНИЯ, ОПТИМИЗАЦИИ И УЧЕТА ШИРОКОПОЛОСНОГО РАДИОДОСТУПА И ЦИФРОВОГО ТВ
- •СОВРЕМЕННЫЕ ТЕХНОЛОГИИ, ИСПОЛЬЗУЮЩИЕСЯ В ПРОИЗВОДСТВЕ РАКЕТНО-КОСМИЧЕСКОЙ ТЕХНИКИ
- •СТРУКТУРА ЗОНДА СКАНЕРА БЛИЖНЕГО ПОЛЯ
- •ТЕХНИЧЕСКАЯ СИСТЕМА ОБЕСПЕЧЕНИЯ ЭКОЛОГИЧЕСКОЙ БЕЗОПАСНОСТИ НА ТЕПЛОВЫХ ЭНЕРГЕТИЧЕСКИХ УСТАНОВКАХ
- •ТЕХНОЛОГИИ 3D-ПЕЧАТИ В РАКЕТОСТРОЕНИИ
- •УСТРОЙСТВА ДЛЯ ОБРАБОТКИ ЗВУКА МУЗЫКАЛЬНЫХ ИНСТРУМЕНТОВ В РЕЖИМЕ РЕАЛЬНОГО ВРЕМЕНИ
- •ЭЛЕКТРИЧЕСКИЕ РАКЕТНЫЕ ДВИГАТЕЛИ – ДВИГАТЕЛИ БУДУЩЕГО
- •ЭНЕРГОСБЕРЕЖЕНИЕ В РАЗДЕЛИТЕЛЬНЫХ ОПЕРАЦИЯХ
УДК 681.2; 621.9.047
ПЛАЗМЕННЫЕ РАКЕТНЫЕ ДВИГАТЕЛИ – РЕВОЛЮЦИЯ В КОСМИЧЕСКИХ ПОЛЕТАХ
К.В. Гостева Руководитель: д-р техн. наук, доцент Е.В. Смоленцев
В работе рассмотрено устройство, принцип работы и применение плазменных ракетных двигателей
Введение
Плазменный двигатель— электрический ракетный двигатель, рабочее тело которого приобретает ускорение, находясь в состоянии плазмы.
Существует множество типов плазменных двигателей. В настоящее время наиболее широкое распространение — в качестве двигателей для поддержания точек стояния геостационарных спутников связи — получили стационарные плазменные двигатели, идея которых была предложена А. И. Морозовым в 1960-х гг. Первые лётные испытания состоялись в 1972 г.
1. История
История плазменных двигателей началась в 1950 году, когда выпускника физфака МГУ Алексея Морозова партком распределил преподавать механику и электротехнику в техникуме заводского поселка Людиново на юго-востоке Калужской области [1]. Причина проста: отец Морозова был репрессирован и никто не принимал во внимание ни его специализацию (квантовая теория поля), ни неоднократные просьбы его научного руководителя
–декана физфака Арсения Александровича Соколова – оставить его на кафедре. Преподавателей физики в те годы довольно часто просили выступать с лекциями об атомной энергии, и Морозов не стал исключением. В один из дней 1953 года он возвращался в Людиново с подобной лекции в деревне Черный поток. «Незадолго до этого я прочитал книжку Гудмана об основах ядерной энергетики. Там была схема ядерной ракеты – газ проходил сквозь активную зону и разогревался. Меня поразило, насколько неэффективна эта конструкция – с одной стороны, атомная энергия, а с другой – это ведь просто тепловая машина! – вспоминал Алексей Иванович. – И пока я шел 12 км по шпалам доЛюдиново, я вспомнил эксперименты с силой Ампера и катушкой Томсона, которые я показывал студентам в училище, и мне пришла в голову идея
–почему бы не раз-гонять рабочее тело магнитным полем?» Теоретические выкладки показывали, что это вполне возможно, и Морозов решил провести эксперимент. Изготовив из асбоцемента «кирпичик», он просверлил в нем крест-накрест два отверстия. В одно он с разных сторон вставил два угольных стержня от батареек, а сверху и снизу бруска расположил два полюса мощного электромагнита. В обычном состоянии плазма, образующаяся в процессе горения дуги, с легким шипением вылетала с
обеих сторон второго отверстия, но стоило включить электромагнит – и поток стал бить в одну сторону со страшным ревом.
К концу 1950-х успехи СССР в космосе вдохновили конструкторов замахнуться на несколько крупномасштабных космических проектов. Планировался даже полет к Марсу. 2 июля 1959 года прошло совещание сотрудников ИАЭ (Институт атомной энергии). Темой обсуждения была возможность построения двигателей для марсианского корабля. Была предложена системы со следующими характеристиками: тяга около 10 кгс, скорость истечения 100 км/спри мощности двигателя 10 МВт. Сотрудники ИАЭ предложили несколько проектов: плазменный импульсный двигатель (А.М. Андрианов), магнитно-плазменный аналог сопла Лаваля (А.И. Морозов) и двигатель на основе однощелевого источника ионов, практически такого же, какой применялся для электромагнитного разделения изотопов (Павел Матвеевич Морозов, однофамилец Алексея Ивановича).
Кстати, все эти проекты в том или ином виде позднее были реализованы. Плазменно-эрозионный (вариант импульсного) двигатель Андрианова значительно меньшей мощности был установлен на один из спутников и выведен в космос в 1964 году, а ионный двигатель П.М. Морозова под именем «Зефир» (тоже маломощный) стоял на том самом спутнике «Метеор-10». Эксперименты с магнитным аналогом сопла Лаваля с центральным телом (сами разработчики называли его «коаксиал») велись с 1960 года, но схема оказалась сложной, и построен он был лишь в 1980 году совместными усилиями ИАЭ, Харьковского физико-технического института, ТРИНИТИ и Института физики Белоруссии. Мощность этого монстра составила 10 ГВт.
Однако эти проекты не подходили для марсианской программы по одной простой причине: у конструкторов тогда не было источников питания подходящей мощности. Эта проблема актуальна и сейчас: максимум, на который можно рассчитывать, это десятки киловатт.
В 1957 году М.С. Иоффе и Е.Е. Юшманов начали исследования магнитной (так называемой пробочной) ловушки для плазмы. Для заполнения ее горячей плазмой (10 млн. градусов) они использовали ускорение ионов в скрещенных электрических и магнитных полях. Эта работа послужила фундаментом для создания ряда плазменных двигателей. В 1962 году Алексей Морозов предложил
78

свою конструкцию плазменного двигателя малой мощности, названного СПД (стационарный плазменный двигатель). Принципиально важной особенностью СПД было то, что величина магнитного поля нарастала к срезу канала двигателя – это обеспечивало создание в плазме объемного электрического поля. Вся идея двигателя была построена именно на существовании такого поля.
Группа А.И. Морозова начала заниматься СПД в 1962 году. Почти пять лет двигатель существовал в лабораторном варианте – в 1967-м модель еще была оснащена водяным охлаждением. Пора было приступать к летно-космическим испытаниям, но на этом этапе разработчики столкнулись с неожиданной проблемой. Конструкторы космических аппаратов категорически отказывались ставить на борт что-либо электрическое. Однако проблемы на этом не закончились. Но уже в февралеиюне 1972 г. были проведены первые включения и испытания, продемонстрировавшие работоспособность СПД в космосе и совместимость с КА на околоземных орбитах. Высота орбиты была поднята на 17 км.
В начале 1980-х «Факел» начинает серийно производить двигатели СПД-70 – потомки «Эолов». Первый спутник с этим двигателем, «Гейзер №1», был запущен в 1982-м, а в 1994-м новой моделью СПД-100 оснастили спутник связи «Галс-1». Хотя сообщение об успешном испытании плазменного двигателя «Эол» в 1974 году было совершенно открыто опубликовано в журнале «Космические исследования», зарубежные конструкторы считали СПД лишь интересной теоретической разработкой. Поэтому демонстрация представителям NASA и JPL в 1991 году работающих двигателей «Факела» и сообщение, что подобными оснащены серийные спутники, вызвала у них настоящий шок (американцы в основном пошли по пути разработки ионных двигателей). Неудивительно, что «Факел» сейчас считается в мире ведущим производителем электроракетных плазменных двигателей. «На каждом третьем российском спутнике стоит наш двигатель, а три из пяти крупнейших западных производителей космических аппаратов покупают у нас СПД, – рассказал директор и генеральный конструктор ОКБ «Факел» Вячеслав Михайлович Мурашко. – Ими, например, оснащены спутники
MBSat-1, Intelsat-X-02, Inmarsat-4F1». Посылая свой спутник SMART-1 к Луне, Европейское космическое агентство выбрало для него в качестве двигателей плазменные PPS-1350, совместную разработку французской компании SnecmaMoteurs, ОКБ «Факел» и МИРЭА [2].
Что же ожидает нас в ближайшем будущем? Дальний космос требует двигателей с мас-
штабами 10-100 кВт или даже МВт. Подобные разработки уже есть – в 1976 году в ИАЭ сделали двигатель мощностью в 30 кВт, да и «Факел» в конце 1980-х разработал СПД-290 мощностью 25 кВт для космического буксира «Геркулес». В любом случае теория таких двигателей построена, поэтому в рам-
79
ках классической схемы СПД вполне реально довести мощность до 300 кВт. А вот дальше, возможно, придется перейти к другим конструкциям. Например, к двухлинзовому ускорителю на водороде, разработанному в ИАЭ в конце 1970-х. Эта машина имела мощность 5 МВт и скорость истечения 1000 км/с. В любом случае на межпланетных кораблях будут стоять плазменные двигатели.
С 1995 года СПД используется в системах коррекции серии связных геостационарных КА (космических аппаратов) типа «Галс», «Экспресс», «Экспресс-А», Экспресс-АМ, Sesat разработки НПО прикладной механики, а с 2003 года — в составе зарубежных геостационарных спутников типа
Inmarsat, Intelsat-X, IPSTAR-II, Telstar-8 для решения задач приведения в «рабочую точку», стабилизации положения в этой точке, изменения «рабочей точки» в случае необходимости и увода с неё по окончании эксплуатации.
К январю 2012 года на запущенных в космос аппаратах было установлено в общей сложности
352двигателя СПД.
2.Принцип работы
Нейтральный газ ксенон подается через металлический кольцевой анод с отверстиями в двустенную (кольцевую) керамическую газоразрядную камеру, на выходе которой установлен полый газоразрядный (работающий также на ксеноне) катодкомпенсатор для эмиссии электронов (рис. 1).
Рис.1. Структура В керамической газоразрядной камере внут-
ренний и наружный полюса электромагнита создают радиальное магнитное поле в несколько сотен Гаусс, нарастающее вдоль камеры и быстро спадающее за её пределами. Если между анодом и като- дом-компенсатором приложить постоянное напряжение в несколько сотен Вольт, то в газоразрядном

канале зажигается разряд и ксенон ионизируется, создавая плазму. Тяжёлые ионы ксенона ускоряются электрическим полем вдоль канала, почти не отклоняясь слабым магнитным полем, и набирают энергию несколько меньшую, чем приложенное напряжение.
Электроны же, напротив, не могут свободно перемещаться вдоль канала, поскольку их ларморовский радиус очень мал. Впрочем, из-за коллективных процессов в плазме электроны всё же составляют небольшую часть разрядного тока. Основной же ток разряда переносят ионы ксенона. Поток ускоренных ионов, вылетающих из газоразрядной камеры, создаёт реактивную тягу двигателя. Вместе с ионами из плазменного двигателя уходит равный им по величине поток электронов из като- да-компенсатора.
Источник питания
Главным показателем эффективности плазменных двигателей [речь обо всей двигательной установке, включая генератор] является отношение веса к мощности, число килограмм необходимых для генерации киловатта электроэнергии. Панели солнечных батарей имеют массу около 20 килограмм на каждый генерируемый им киловатт. Лучшие ядерные реакторы, сконструированные для космических полетов, имеют удельную массу в 45 килограмм.
Пентагон и компания Боинг разрабатывают следующее поколение солнечных батарей с целью достижения отношения веса к мощности в 7 килограмм на ватт, согласно Агентству перспективного планирования научно-исследовательских работ Министерства обороны США [DARPA,
DefenseAdvancedResearchProjectsAgency]. Инжене-
ры предсказывают, что ядерные энергоустановки достигнут эффективности в несколько килограммов на один киловатт в течение двух ближайших десятилетий.
3. VASIMR
Электромагнитный ускоритель с изменяемым удельным импульсом (англ.
VariableSpecificImpulseMagnetoplasmaRocket; VASIMR) — электромагнитный плазменный ускоритель, предназначенный для реактивного ускорения космического аппарата. Реактивный двигатель использует радиоволны для ионизации рабочего тела с последующим разгоном полученной плазмы с помощью электромагнитного поля для получения тяги [2].
Метод нагрева плазмы, используемый в VASIMR, был разработан в результате исследований в области термоядерного синтеза. Цель разработки VASIMR — заполнить разрыв между высокоэффективными реактивными системами малой тяги с высоким удельным импульсом и низкоэффективными системами большой тяги с низким удельным импульсом. VASIMR способен работать в режимах, близких к системам большой тяги и малой.
80
Концепция двигателя предложена астронавтом и учёным Франклином Чанг-Диазом из КостаРики в 1979 году и продолжает развиваться в настоящее время.
3.1 Основной проект
VASIMR (рис. 2), иногда рассматриваемый как электротепловой плазменный ускоритель (ЭПУ), использует радиоволны для ионизации и нагрева рабочего тела и электромагнитные поля для ускорения плазмы для получения ускорения.
Рис. 1.
Этот тип двигателя можно рассматривать как вариацию безэлектродного плазменного ускорителя, отличающегося в способе ускорения плазмы. Оба типа двигателя не имеют никаких электродов. Основное преимущество такого проекта в исключении проблемы эрозии электродов. Более того, так как все части VASIMR защищены магнитным полем и не приходят в прямой контакт с плазмой, потенциальная продолжительность эксплуатации двигателя, построенного по такому проекту, гораздо выше ионного двигателя.
3.2. Применения
VASIMR не подходит для подъема полезной нагрузки с поверхности планеты (например Земли) на околопланетную орбиту из-за его низкого соотношения тяги к массе и может быть использован только в невесомости (например для старта корабля с околопланетной орбиты). Он может быть использован в качестве последней ступени, сокращая потребность в топливе для транспортировки в космосе, или в качестве разгонного блока. Ожидается, что двигатель должен выполнять эти операции за доли стоимости от стоимости аналогов на основе технологий химического реактивного движения:
•компенсация торможения в верхней атмосфере Земли (подъем орбиты) для орбитальных станций;
•обеспечение доставки грузов на лунную
орбиту;
•заправка топливом в космосе;
•восстановление ресурсов в космосе;
•космические транспортировки со сверхвысокими скоростями для дальних исследовательских программ.
Другие применения VASIMR (например, транспортировка людей к Марсу) требуют наличия
источников очень высоких энергий с небольшой массой, таких как, например, ядерные энергоблоки.
4. Полет к Марсу
Едва ли не основная сложность в организации пилотируемой миссии на Марс — ее продолжительность. Текущие технологии потребуют полгода на путешествие только в одну сторону — и этот срок порождает массу дополнительных проблем, от трудностей с жизнеобеспечением до защиты от длительного воздействия радиации.
Однако плазменный двигатель нового поколения может сократить время, которое требуется для полета к Марсу, всего до 39 дней, по сравнению с шестью месяцами, которые необходимы традиционным ракетам. Предполагается, что 200мегаваттный двигатель класса VASIMR сможет осуществить эту миссию [3].
Традиционные реактивные двигатели ракет создают тягу за счет экзотермической химической реакции между компонентами топлива. Львиная его доля уходит на преодоление земного притяжения и вывода аппарата на орбиту.
В отличие от них, плазменные ракетные двигатели (ПРД) используют в качестве создающего тягу рабочего тела заряженную плазму, то есть полностью ионизированный газ.
Современное состояние техники не позволяет создать такие двигатели, способные преодолеть
81
силу тяжести, однако в работе на орбите они могут оказаться незаменимыми. Во-первых, топлива им требуется на порядки меньше, чем обычным ракетам. Во-вторых, работают они очень долго. Разгоняясь понемногу, зато постоянно, они позволяют кораблям, на которых установлены, довольно быстро обгонять своих традиционных собратьев.
Двигатель VASIMR представляет собой куда более совершенную систему. Работает над ним компания AdAstra, которая была основана в 2005 г. физиком и бывшим астронавтом Франклином Чен-
Диазом (FranklinChang-Diaz).
Заключение
Как следует из приведенных данных, стационарные плазменные двигатели успешно освоены в космической технике, иесть еще направления, по которым они могут развиваться и расширять область своихприменений.
Литература
1.Журнал «Наука и жизнь», 1999, статья «Космический электровоз», Доктор физикоматематических наук А. Морозов.
2.https://ru.wikipedia.org
3.Публикации NewScientistSpace, LisaGrossman: «Плазменный мотор: 40 дней до Марса».
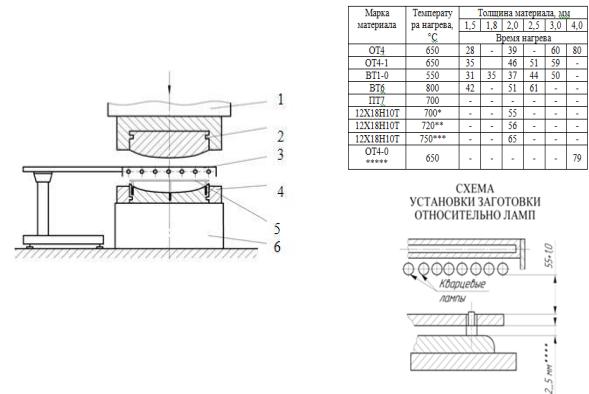
УДК 614.87
ПОВЫШЕНИЕ КАЧЕСТВА ШТАМПОВОЙ ОСНАСТКИ ПРИ ИЗГОТОВЛЕНИИ
ДЕТАЛЕЙ САМОЛЁТА
Студент группы УКм-151 Сидельникова Ю. А. Руководитель: д-р техн. наук, профессор В.И. Максименков
Рассмотрен процесс формообразования деталей кабины самолёта с предварительным нагревом заготовки. Выявлены браковочные признаки, возникающие при формообразовании деталей с нагревом. Разработан способ повышения стойкости штамповой оснастки методом борирования, обеспечивающий повышение твёрдости до 2000HV и стойкости штамповой оснастки в 4 – 10 раз.
Тема |
разработки |
повышение |
качества |
Формообразование детали из сплава ОТ4-1 |
||||
штамповой оснастки при изготовлении деталей |
осуществляется с базированием заготовки на |
|||||||
самолёта. |
|
|
|
|
матрице. При этом на заготовке выполняются |
|||
Цель |
работы: |
рассмотреть |
схему |
отверстия, в которые входят направляющие |
||||
формообразования заготовки, а так же время |
элементы, установленные на матрице. |
|
||||||
нагрева заготовок после испытаний; определить |
Перед |
процессом |
формообразования |
|||||
стойкости штампа; выявить браковочные признаки, |
осуществляется тарировка установки. При этом |
|||||||
возникающие при штамповке; выбрать техпроцесс |
определяются |
высота |
расположения |
|||||
повышения стойкости штампов – борирование; |
нагревательных ламп относительно заготовки, |
|||||||
провести |
экспериментальные исследования на |
время и температура нагрева заготовки. |
|
|||||
образцах. |
|
|
|
|
После |
процесса |
формообразования |
|
В конструкции кабины самолёта используются |
осуществлялся контроль наличия окалины на |
|||||||
листовые материалы из титановых сплавов и |
поверхности |
испытываемых |
материалов. |
|||||
нержавеющих сталей. Учитывая, что толщина |
Результаты испытаний различных |
материалов |
||||||
заготовок равна 4 мм, деформировать такие |
приведены в табл.1. |
|
|
|||||
заготовки в холодном состоянии не представляется |
|
|
|
|
||||
возможным. |
|
|
|
|
|
|
Таблица 1 |
|
Разработана |
установка |
УНКЛ-18, |
Время нагрева заготовок с использованием УНКЛ – |
|||||
обеспечивающая |
предварительный |
нагрев |
18 |
|
|
|
заготовок перед формообразованием .
Установка использовалась в составе с молотом МЛ–3. Схема процесса формообразования представлена на рис. 1.
Рис. 1. Схема процесса формообразования заготовки:
1 – стессель; 2 – пуансон; 3 – установка для нагрева заготовок;
4 – матрица; 5 – заготовка; 6 – шабот
82
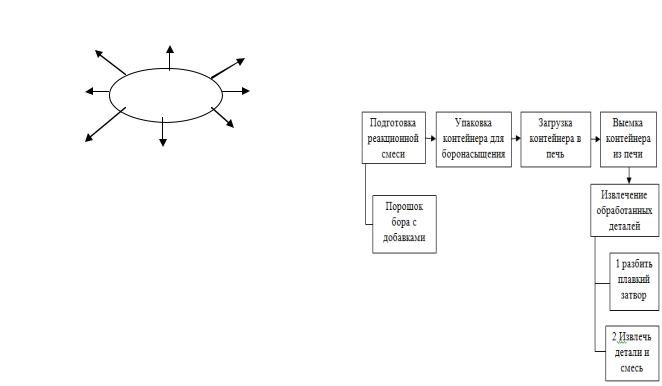
В процессе формообразования заготовки определяли температуру нагрева матрицы. Максимальная температура нагрева соответствовала 300 . Эта величина может изменяться с учётом геометрии штампа.
Учитывая характер ударной нагрузки в процессе формообразования, выбран материал штампа 5ХНМ – инструментальная сталь. Режимы термообработки: закалка 850oC с охлаждением в масле и последующий отпуск при 460 – 520oC. На выбор материала штампа оказывает влияние его стоимость, а так же условия эксплуатации.
Относительная стойкость данного материала приведена в табл. 2.
Таблица 2 Относительная стойкость молотовых штампов
|
Материал штампа |
|
5ХНМ |
|
||
|
|
|
|
|
||
|
Относительная стойкость в % |
|
90 |
|
||
|
|
|
|
|||
|
Стойкость штампов зависит от следующих |
|||||
факторов (рис. 2). |
|
|
|
|||
|
от |
от условий |
|
|
|
|
относительной |
|
от вида и |
||||
эксплуатации штампа |
|
|||||
|
толщины |
|
качества |
|||
|
|
|
||||
материала |
|
|
материала |
|||
конструкции |
Стойкость |
|
от |
|||
штампа и типа |
штампа |
температуры |
||||
производимой |
|
нагрева |
||||
|
|
|||||
операции |
|
|
||||
|
|
|
|
|||
|
от |
от термообработки |
||||
|
|
рабочих деталей |
||||
геометрических |
от вида |
|||||
|
|
|
||||
|
|
штампа |
||||
|
форм детали |
оборудования |
|
|||
|
|
|
|
Рис. 2. Стойкость штампа
Проведён конструктивно – технологический анализ процесса штамповки, который позволил выявить дефекты оказывающие влияние на качество штампуемых деталей. Главные из них трещины, недоформовка поверхности, наводораживание и др., что во многом определяется состоянием штамповой оснастки. Возникающие браковочные признаки:
-Низкая стойкость;
-Появление сколов поверхности матрицы и пуансона;
-Появление сетки трещин;
-Образование окалины;
-Высокий износ;
-Возникновение дефектов в микроструктуре слоя.
Сцелью устранения браковочных признаков рассмотрены методы повышения качества штампов методами химико-термической обработки (ХТО). Следует выделить наиболее распространенные – это цементация, нитроцементация, азотирование и борирование.
Представлены характеристики изменения твёрдости при различных видах химико – термической обработки (табл. 3).
|
|
|
Таблица 3 |
|
Сравнительные показатели твёрдости |
|
|
||
|
Процесс |
Твёрдость (HV) |
|
|
|
Борирование |
1800 |
– 2000 |
|
|
Цементация |
500 |
– 700 |
|
|
Азотирование |
300 |
– 350 |
|
|
Нитроцементация |
570 |
– 690 |
|
Учитывая техническую оснащенность предприятия и условий экологии, а так же оценку эффективности процесса, был выбран процесс борирования, т.е. насыщение поверхности матрицы и пуансона бором (табл. 4).
|
|
|
Таблица 4 |
Метод борирования |
|
|
|
Метод |
Режим борирования |
Глубина |
|
борирован |
|
|
слоя, мм |
Температ |
Продолжит |
||
ия |
ура, С |
ельность |
|
В |
900 |
|
|
порошко- |
|
0,15 – |
|
|
4 часа |
||
образной |
|
0,20 |
|
1000 |
|
||
смеси |
|
|
|
|
|
|
Этот процесс поможет уменьшить браковочные признаки и улучшить стойкость штампа. Процесс борирования осуществляется по схеме (рис. 3).
Рис. 3. Схема технологического процесса борирования
Весь этот процесс осуществляется в устройстве для борирования, которое состоит из карбида бора, матрицы, пуансона, асбеста, песка и все это покрывается ангидридом бора (плавкий затвор) (рис. 4). Это устройство после установки детали помещают в печь.
83
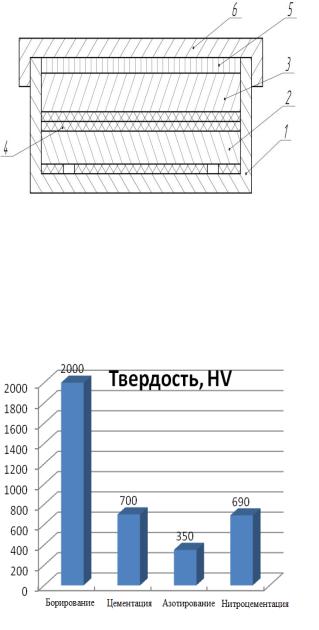
Рис. 4. Устройство для борирования - контейнер
1 – карбид бора, 2 – матрица, 3 – пуансон, 4
– асбест, 5 – песок, 6 – ангидрид бора
После процесса борирования проводилась оценка твёрдости матрицы и пуансона. Сравнительные характеристики приведены на рис.
5.
Рис. 5. Сравнительные характеристики твёрдости оснастки
Выявлено, что максимальная твёрдость получается при борировании. Проведённые испытания оснастки показали, что повышение твёрдости штамповой оснастки улучшили качество поверхности деталей. Определялась стойкость образцов, которые обрабатывались по технологии изготовления штампа.
Оценка стойкости осуществлялась с помощью идентора - конуса, которым наносились удары по образцу, и выявилась глубина следа идентора. При борировании - 0,08 мм, а при азотировании – 0,15мм. Результаты представлены в табл. 5.
|
|
Таблица 5 |
Оценка стойкости |
|
|
Метод |
Глубина |
Глубина |
обработки |
упрочнения |
следа |
|
|
идентора при |
84
|
|
ударе |
Борирование |
0,15 |
0,08 |
Азотирование |
0,2 |
0,15 |
Внедрение процесса позволяет снизить трудоёмкость изготовления штамповой оснастки в 4 раза, обеспечив повышение стойкости в 4 – 10 раз, при этом улучшается качество поверхности деталей.
В результате работы:
1Проведён анализ процессов химикотермической обработки и выбран процесс борирования деталей штампов;
2Разработана установка, обеспечивающая предварительный нагрев заготовок перед формообразованием;
3Разработана технология борирования;
4Предложена конструкция устройства для осуществления борирования;
5Внедрение процесса позволяет снизить трудоёмкость изготовления штампов в 4 раза, обеспечив повышение их стойкости в 4 – 10 раз.
УДК 621.455
ПОВЫШЕНИЕ ЭНЕРГЕТИЧЕСКОЙ ЭФФЕКТИВНОСТИ ЦЕНТРОБЕЖНЫХ НАСОСОВ
Аспирант кафедры НГОиТ Галдин Д.Н. Руководитель: д-р техн. наук, профессор А.В. Кретинин
Применение пакета конечно-элементного анализа ANSYS для математического моделирования гидродинамических процессов в проточной части центробежного насоса для получения оптимизированной геометрии проточной части, обеспечивающей максимальное энергетическое совершенство насоса
Задача оптимизации проточной части является задачей многокритериальной условной оптимизации, при этом возможна следующая постановка задачи, при которой ограничениями являются кавитационный запас и конструктивные параметры, а критериями оптимизации являются гидравлический КПД насоса и радиальная сила на ротор.
При этом считается, что основными элементами проточной части являются подвод, рабочее колесо, отвод насоса и в ряде случаев лопаточный направляющий аппарат. Варьируемыми параметрами для отдельных элементов проточной части могут быть назначены следующие факторы. Для рабочего колеса: количество лопастей, угол установки лопасти на входе на покрывном диске, угол установки лопасти на выходе, запас прочности вала насоса, отношение диаметра ступицы к диаметру вала, отношение толщины лопасти к выходному диаметру колеса, втулочный угол профиля лопасти, угол между выходной кромкой лопасти и осевым направлением. Для лопаточного направляющего аппарата (НА): число лопастей, угол установки лопасти на входе, угол установки лопасти на выходе, толщина лопастей, наружный диаметр НА, внутренний диаметр НА, ширина НА. Для отвода насоса: ширина входа в отвод, радиус входа в отвод, диффузорность обводного канала, коэффициент расширения обводного канала, угол установки "языка" отвода, пропускная способность спиральной части.
Расчетный блок состоит из отдельных расчетных модулей. В модуле Geometry 1 создается параметризованная модель направляющего аппарата отвода, расчетная сетка для которого сроится в мо-
дуле Mesh 1. Модули Excel, Geometry 2 и Mesh 2
формируют параметризованную сеточную модель отвода. В отдельном модуле Vista CPD используется инструмент Vista Design для формирования меридионального сечения лопаточного колеса. Далее эти данные передаются в модуль BladeGen, где с помощью Blade Design проектируется лопастная система с лопатками двойной кривизны. Затем эти данные передаются в модуль TurboGrid, где с помощью инструментов Turbo mesh создается расчет-
ная сетка. Далее сеточная модель колеса передается для моделирования в модуль CFX. Кроме того, готовые геометрии направляющего аппарата и отвода также загружаются в модуль СFX, а именно, в CFX Pre. С помощью инструмента CFX Pre формируются граничные условия (на входе, выходе, стенках, интерфейсы), параметры моделирования (модель турбулентности, зависимости плотности, вязкости, давление насыщенных паров и пр.) и передаются в решатель CFX. В решателе задаются параметры алгоритма решения сеточных уравнений и запускается процесс решения. После сходимости системы сеточных уравнений результаты передаются в CFX Post, где обрабатываются и выводятся в качестве выходных критериев оптимизации.
Наиболее важным этапом реализации методики оптимизации является построение параметрических моделей проточной части с использованием инструментария ANSYS. Средствами встроенного редактора геометрии Design Modeler были созданы параметризованные модели элементов насоса с изменяемыми параметрами, указанными выше. Отличительной особенностью модели двузавиткового отвода является использование среды Microsoft Office Excel, что позволяет иметь удобный интерфейс, который к тому же может быть переадаптирован в случае незначительных изменений концепции построения.
Вербальная постановка тестовой задачи оптимизации состоит в следующем: подобрать значения следующих геометрических параметров, определяющих профиль лопатки рабочего колеса: запаса прочности вала насоса Ks, отношение диаметра ступицы к диаметру вала , углы установки лопасти на входе и выходе (β1s – угол установки лопасти на входе на покрывном диске, и β2 – угол установки лопасти на выходе), отношение толщины лопасти к выходному диаметру колеса такие, что гидравлический КПД насоса стремится к максимальному значению, а радиальная сила на ротор, приводящая к вибрациям насоса, стремится к минимальному значению). При этом кавитационный запас насоса является ограничением, и будет вычисляться для наилучшего варианта лопасти. По ряду факторов
85
осуществлялся одномерный оптимизационный по- |
3. Проведение многокритериальной оптимиза- |
иск. |
ции для отдельных элементов проточной части (ра- |
Реализация разработанной методики осу- |
бочее колесо, отвод) и насосов в целом. Формиро- |
ществляется методами комбинаторной и парамет- |
вание Парето-оптимальных множеств решения. |
рической оптимизации и содержит ряд связанных |
Проектирование проточной части насосов с учетом |
проблем. |
результатов решения задач оптимизации. |
1. Разработка параметризованных 3D-моделей |
Литература |
элементов проточной части: колесо, отвод, направ- |
1. Валюхов С.Г., Булыгин Ю.А., Кретинин А.В. |
ляющий аппарат. Разработка параметризованной |
Численное моделирование гидродинамических |
модели всей проточной части НА. Разработка рас- |
процессов в проточной части магистрального |
четных моделей в среде ANSYS. Разработка файла |
нефтяного насоса // Разработка, производство и |
сценария моделирования, с использованием кото- |
эксплуатация турбо-, электронасосных агрегатов и |
рого можно одной командой запустить проектиро- |
систем на их основе: Труды VI Международной |
вание, создать расчетную модель и выполнить рас- |
научно-технической конференции «СИНТ’11». – |
чет с выводом результатов расчета во внешний |
Воронеж: ИПЦ «Научная книга», 2011. – С.61-65 |
файл. Разработка программы-переходника, которая |
2. Валюхов С.Г., Кретинин А.В. Математическое |
задает в служебный файл ANSYS параметры гео- |
моделирование гидродинамических процессов в |
метрии, затем запускает ANSYS на проектирование |
проточной части центробежного насоса с использо- |
и расчет, и далее считывает из служебного файла |
ванием нейросетевых алгоритмов / Насосы. Турби- |
результаты расчета и записывает их во внешний |
ны. Системы. 2011, № 1. С. 53-60. |
файл результатов. Т.е., расчетчик во внешнем фай- |
3. Кретинин А.В., Галдин Д.Н., Шматов Д.П. Неде- |
ле задает необходимые параметры, далее запускает |
терминированное моделирование гидродинамиче- |
программу-переходник и далее весь расчет и про- |
ских процессов с использованием модуля ANSYS |
ектирование ANSYS проводит автоматически без |
DESIGNXPLORER / Вестник ВГТУ 2015, т.11 №5 |
вмешательства оператора. |
С. 37-41 |
2. Формирование набора формализованных |
|
постановок задач оптимизации: набора варьируе- |
|
мых параметров, набора критериев, диапазонов |
|
изменения параметров, ограничений. |
|
86