
3625
.pdf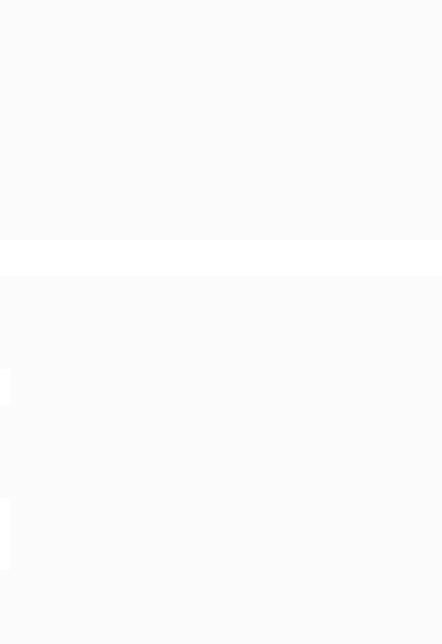
-обеспечивает оптимальный подвод импульсной высокочастотной энергии в зону электрохимической обработки;
-имеет широкий диапазон регулирования параметров обработки;
-обеспечивает прием и установку режимов работы и параметров выходных сигналов, задаваемых оператором станка, от ЧПУ станка;
-обеспечивает индикацию на мониторе ЧПУ тревожных и аварийных ситуаций;
-модульная конструкция;
-наличие двух контуров технологического тока, обеспечивающих одновременную двустороннюю электрохимическую обработку с возможностью раздельной работы контуров.
ГТТ ИП ЭХС с десятью силовыми блоками имеет следующие технические характеристики:
-в режиме постоянного тока:
-выходное напряжение с плавной регулировкой – 10-20 В;
-максимальный уровень тока нагрузки – 3000 А;
-в режиме импульсного тока формируются импульсы с характеристиками:
-амплитудное значение напряжения с плавной регулировкой
– 10-40 В;
-длительность импульсов напряжения – 0,3-3 мс;
-дискретность установки длительности импульсов – ± 0,1 мс;
-длительность паузы – 1-10 мс;
-дискретность установки длительности паузы – ± 0,1 мс;
-длительность фронтов импульсов – ± 0,1 мс;
-максимальное амплитудное значение тока нагрузки – 10000 А;
-формирование пачек из импульсов произвольной конфигурации:
- количество импульсов в пачке – 1-10; - длительность пауз в пачке – 1-10.
ГТТ ИП ЭХС обеспечивает прием и установку от ЧПУ задаваемых оператором станка режимов работы и параметров
71

выходных сигналов каждого из контуров, а также индикацию на мониторе ЧПУ следующих режимов и параметров работы контуров:
-режима работы (импульсный или постоянный ток, без/с выравниванием и т.п.);
-величины выходного напряжения (среднее значение);
-величины тока нагрузки (среднее значение);
-длительности импульса (в режиме импульсного тока);
-длительности паузы (в режиме импульсного тока);
-температуры токонагретых частей силовых блоков;
-наличие охлаждающей жидкости в системе охлаждения ГТТ ИП ЭХС.
ГТТ ИП ЭХС обеспечивает индикацию на мониторе ЧПУ о тревожных и аварийных ситуациях:
-отсутствие охлаждающей жидкости в системе охлаждения ГТТ ИП ЭХС,
-превышение предельно допустимой температуры токонагретых частей силовых блоков.
-не закрыты двери шкафа ГТТ ИП ЭХС.
Тревожные и аварийные ситуации сопровождаются звуковым сигналом с одновременным миганием лампочек сигнальной колонны и передачей на ЧПУ сообщения с указанием причины и времени возникновения тревожной и аварийной ситуации. Аварийные ситуации приводят к отключению силовой части соответствующего контура ГТТ ИП ЭХС (отсутствие напряжения на выходных клеммах).
Время установления рабочих режимов ГТТ ИП ЭХС не превышает 5 мин.
1.3.3. Расчет генераторов для ЭХО
Для правильного выбора промышленного источника питания необходимо учитывать потребность в реверсировании, рассчитать максимальную силу выходного тока. При изготовлении деталей из различных сплавов напряжение источника
72

берут по наибольшему граничному значению для всех материалов. При определении силы тока I на выходе источника питания расчет следует выполнять для детали, обработка которой потребует наибольшего тока:
I IT ,
3
где IT – сила тока, необходимая для анодного растворения обрабатываемой поверхности заготовки;
3 – коэффициент загрузки источника питания при режиме длительной работы (для источников питания типа ИПП
3=0,65…0,7; для типа ВАК 3=0,8…0,98).
Расчет силы тока для осуществления процесса ЭХО выполняется по формуле:
IТ |
jF |
Vрасч |
F , |
(1.1) |
|
||||
|
|
|
|
где Vрасч – расчетная скорость съема металла с заготовки; F – площадь рабочей части электрода-инструмента; j – плотность тока на аноде;
– плотность материала анода;
– электрохимический эквивалент обрабатываемого сплава;
– выход по току.
При обработке по схеме с неподвижными электродами требуемая сила тока со временем меняется. Расчет IT (формула 1.1) ведут по скорости съема в начальный момент времени, когда межэлектродный зазор равен S0
Vрасч=ηα (U-∆U)/γS0, |
(1.2) |
где – удельная электропроводность электролита; U – напряжение на электродах;
∆U – потери напряжения.
73
Для схем прошивания (с периодическим сближением электродов), точения и протягивания силу тока IT находят по скорости съема при минимальном зазоре Smin:
Vрасч=ηα (U-∆U)/γSmin. |
(1.3) |
При схеме шлифования металлическим инструментом силу тока IT рассчитывают по формуле
IT= (U-∆U)F/Smin. |
(1.4) |
В формуле (1.4) при расчете площади рабочей части электрода-инструмента следует учесть нерабочие участки (щели, отверстия, площадки, покрытые диэлектриком, и др.):
F=F0-F1, (1.5)
где F0 – общая площадь рабочей части электрода-инструмента; F1 – площадь нерабочих участков.
Расчет общей площади F0 для схемы разрезания выполняют для момента прохождения инструментом максимального размера поперечного сечения, например диаметра заготовки. Для шлифования площадь F0 находят в зависимости от диаметра, ширины инструмента и глубины обработки путем графического построения в масштабе 50:1 или 100:1.
По известным напряжению и силе тока источника питания можно найти потребляемую им мощность
P |
IU |
, |
(1.6) |
|
|||
n |
|
|
|
|
n |
|
где n – КПД источника питания.
74
1.3.4. Выбор токоподводов
При ЭХО ток от источника питания к механической части станка передают по гибким или жестким шинам. При силе тока до 100 А можно использовать отдельные провода большого сечения или их наборы. Если сила тока не превышает 10001200 А, то применяют наборы гибких медных оплеток или пакеты медной фольги. При большей силе тока используют шины в виде полос из меди, алюминия или других сплавов. Иногда токоподводы делают охлаждаемыми (воздухом или водой).
Площадь сечения токоподвода FT находят из условия прохождения по нему тока с предельной плотностью Jn:
F |
|
IT |
. |
(1.7) |
|
||||
T |
|
j |
|
|
|
|
n |
|
|
Для медных токоподводов без охлаждения |
jn = 1-2 |
А/мм2, для алюминиевых jn = 0,8-1,5 А/мм2. При охлаждении водой jn = 3-6 А/мм2 и jn = 2-3 А/мм2, соответственно для медных и алюминиевых проводов. Для надежной передачи тока следует правильно выбрать силу прижима и размеры контактных площадок. От этого будут зависеть потери напряжения, которые при нормальных условиях эксплуатации не должны превышать (0,03-0,05) UL (где U – номинальное напряжение, В; L – длина токоведущих шин, м) и потери мощности, которые составляют (0,1-1) PL (где P – мощность установки, кВт; L – длина проводов, м). Для снижения потерь напряжения и мощности необходимо обеспечить плотность прижима в контактных соединениях для меди (6-10) МПа, для алюминия 25 МПа.
Площади контакта Fk в местах соединений рассчитыва-
ют по формуле |
|
|
|
F |
IT |
, |
(1.8) |
|
|||
k |
j |
|
|
|
k |
|
|
75 |
|
|
|
где jk – предельная плотность тока через контакт (без охлаждения – jk 1 А/мм2, с охлаждением – jk 8 А/мм2).
По формуле (1.8), кроме соединений шин, рассчитывают условия закрепления деталей в базовых элементах механической части станка. Эффективно использование тонких металлических прокладок в местах токоподводов путем их плотного обжатия обеими поверхностями (заготовки и токоподвода).
1.3.5. Системы подачи электролита
Если процесс ЭХО протекает в течение нескольких секунд, например, при маркировании деталей по схеме с неподвижными электродами, то электролит не успевает загрязниться продуктами обработки. В этих условиях электролит не прокачивают. При времени процесса до 8-10 с для перемещений электролита могут быть использованы ультразвуковые или низкочастотные вибрации электродов, а также влажные ленты, перемещаемые через межэлектродный зазор. Если обрабатывают детали, предназначенные для перемещения газов или жидкостей (крыльчатки компрессоров, насосов, шнеков и др.), то электролит можно перемещать за счет вращения самой заготовки. Жидкость протекает по зазору между электродами со скоростью, регулируемой частотой вращения заготовки. В остальных случаях используют насосы (табл. 1.19).
Наиболее широко применяются центробежные насосы, выполняемые из нержавеющей стали. Они не боятся загрязнения перекачиваемой жидкости и надежны в работе. Для подбора промышленного насоса необходимо знать его напор и подачу.
1.3.6. Ванны для комплектования станков
Ванны служат для хранения и приготовления электролита, промывки, консервации и пассивации деталей. Форма и размеры ванн для хранения электролита обусловлены необхо-
76
димостью размещения в них деталей, качественного отстоя продуктов обработки, периодического их удаления, стабилизации температуры жидкости. В ваннах устанавливают теплообменники для подогрева и охлаждения электролита.
|
Характеристики насосов |
Таблица 1.19 |
||
|
|
|||
|
|
|
|
|
Тип, |
Произво- |
На- |
Потреб |
Габариты, |
модель |
дитель- |
пор, |
ляемая |
мм |
|
ность |
м |
|
|
|
м3/час |
|
мощ- |
|
|
|
|
ность, |
|
|
|
|
квт |
|
|
|
|
|
|
ПА-45 |
2,5 |
20 |
0,8 |
940х960х1350 |
|
|
|
|
|
1,5Х-6Е-1 |
5,4-12 |
20 |
4,5 |
405х490х940 |
(коррозионно- |
|
|
|
|
стойкий) |
|
|
|
|
|
|
|
|
|
ЭКН-10/1-11 |
10 |
90 |
6,0 |
390х485х910 |
|
|
|
|
|
2Х6Е-1 |
12-29 |
35 |
7,5 |
485х540х1196 |
(коррозионно- |
|
|
|
|
стойкий) |
|
|
|
|
|
|
|
|
|
3МС-10 |
34 |
69 |
11 |
Сведения |
|
|
|
|
не приводятся |
|
|
92 |
15 |
|
|
|
|
||
|
|
|
|
|
4МС10 |
60 |
66 |
20 |
|
|
|
|
|
|
|
|
99 |
25 |
|
|
|
|
|
|
77
Продолжение табл. 1.19
3КМ6 |
45 |
54 |
17 |
|
ЭПЖН-3 |
50 |
80 |
35 |
|
5МС10 |
105 |
98 |
50 |
|
|
|
147 |
75 |
|
ЗХ-6К-1 |
90 |
85 |
55 |
1755х755х410 |
(коррозионно- |
|
|
|
|
стойкий) |
|
|
|
|
4Х12К-1 |
90 |
335 |
22 |
1400х560х330 |
(коррозионно- |
|
|
|
|
стойкий) |
|
|
|
|
Ванны обычно изготавливают из нержавеющей стали или химически стойких диэлектриков. Они могут иметь одну или несколько секций. Для удобства транспортировки и монтажа ванны вместимостью до 1,5 м3 обычно делают односекционными, более вместительные – двухсекционными. При большом числе станков электролит хранят в бетонных емкостях или в бассейнах.
Бассейны удобны тем, что в них методом отстаивания электролит очищается от продуктов обработки, имеет стабильный состав, температуру. Бассейны чистят не чаще одного раза в год. Открытые бассейны занимают большую площадь, велика длина трубопроводов, трудно регулировать состав и температуру жидкости. Нагрев и охлаждение больших емкостей требует дополнительных затрат энергии, занимают много времени, а зимой бассейны замерзают. Поэтому для хранения больших масс электролита чаще используют бетонные емкости, расположенные в закрытых помещениях. Если число станков не превышает 10-12 шт., то используют индивидуальные ванны.
Максимальная сила тока, необходимая для обработки деталей, связана с объемом ванны W соотношением
I |
T |
|
W |
, |
(1.9) |
|
|||||
|
|
|
|
||
|
|
78 |
|
|
|
где – удельный объем ванны, м3/А. В зависимости от объема ванны удельный объем имеет следующие значения: (0,5-0,6) 10-2 – для объема ванны 1 м3; (0,3-0,35) 10-3
– для объема ванны 1-2,5 м3; 0,3 10-3 – для объема ван-
ны > 2,5 м3.
1.3.7.Агрегаты очистки электролита от продуктов обработки
Впроцессе ЭХО в электролите происходит накопление продуктов обработки. При малых межэлектродных зазорах в загрязненном электролите между электродом-инструментом и деталью происходит пробой промежутка и короткое замыкание. В случае нормального протекания процесса ЭХО допустимая массовая концентрация твердых продуктов обработки в электролите зависит от размера зазора. Так, для межэлектрод-
ных зазоров (мм) 0,05; 0,2; 0,3; 0,5 допустимая концентрация продуктов обработки (кг/м3) составляет 0,5; 3; 6; 10, соответственно.
Очистка электролита может выполняться несколькими
способами. Наиболее часто применяют отстой. Однако для ванн объемом W > 0,4-0,5 м3 отстой занимает слишком много времени и его используют в комбинации с другими способами: центрифугированием, очисткой пресс-фильтрами и вакуумными фильтрами, электрофлотацией или осаждением продуктов обработки с помощью коагуляторов.
Для отдельных станков и небольших участков (до 3-4 станков) используют центрифугирование (табл. 1.20).
79
|
Характеристики центрифуг |
Таблица 1.20 |
|||
|
|
||||
|
|
|
|
|
|
Тип |
Опти- |
Эффек- |
Потре |
Пре- |
Габариты |
|
мальная |
тив- |
бляе- |
дель- |
|
|
произ- |
ность |
мая |
ный |
|
|
води- |
очист- |
мощ- |
техно- |
|
|
тель- |
ки, |
ность, |
лочи- |
|
|
ность, |
% |
кВт |
ческий |
|
|
м3/час |
|
|
ток |
|
|
|
|
|
ИП, |
|
|
|
|
|
А |
|
ОМД- |
0,8-1,0 |
80-90 |
4,5 |
до |
108х1240 |
802Н-1 |
|
|
|
5000 |
х1630 |
НОГШ- |
0,8-1,0 |
70-80 |
5,5 |
до |
730х1085 |
202К-3 |
|
|
|
5000 |
х1700 |
НОГШ- |
1,8-2,0 |
80-90 |
7,5 |
до |
715х1095 |
352К-1 |
|
|
|
15000 |
х1550 |
Центрифуги должны быть оснащены устройством для автоматической выгрузки отходов. Серийно выпускают отстойные центрифуги периодического действия типа ОМД, ОТН, шнековые центрифуги непрерывного действия типа НОГШ. Они обеспечивают очистку электролита с концентрацией продуктов обработки до 3 кг/м3.
Если на участке работает более 5 станков, то целесообразно применять вакуумный фильтр. Вакуумные фильтры надежны в работе, позволяют получить отходы, пригодные для дальнейшей переработки: гидроксиды металлов, содержащиеся в продуктах обработки, успешно используются в качестве сырья для порошковой металлургии. Применение вакуумных фильтров позволяет создавать автоматические системы очистки электролита. Загрязненность электролита после очистки в таких устройствах не превышает 0,5 кг твердого вещества в 1 м3 жидкости.
80