
3625
.pdfзующих знаков и перпендикулярность их торцовых поверхностей к образующим.
Кроме пайки может быть применен токопроводящий эпоксидный клей, в состав которого кроме смолы, пластификатора и отвердителя входит графитовый наполнитель. Такое крепление обеспечивает удовлетворительное качество инструмента при небольшом числе знаков.
Аналогично получают инструменты при изготовлении знаков штамповкой, чаще с последующим соединением их из отдельных частей. Эти инструменты могут быть использованы как для мелкого, так и для глубокого маркирования.
Технологический процесс изготовления инструментов гравированием имеет свои особенности: глубину гравирования подбирают такой, чтобы она позволяла проводить периодическую зачистку знаков; рабочие части выполняют из меди, латуни, коррозионно-стойкой стали, которые обладают высокой пластичностью. Гравирование ведут на станках по шаблонам, имеющим наружный профиль, аналогичный профилю гравируемого знака. При единичном производстве используется слесарное гравирование по разметке. Информация может быть нанесена в виде углубления профиля знаков или же путем снятия металла вокруг них. В первом случае операция гравирования упрощается, но выпуклые знаки, которые сложнее получать, находят большое применение при электрохимическом маркировании.
В ряде случаев гравирование выполняют после нанесения изоляции с хорошей адгезией к металлу. Например, рекомендовано изготовлять рабочую часть инструмента из никеля, которую окисляют путем нагрева до 1450-1500 К в течение 2-3 ч с охлаждением на воздухе (по а.с. 529040 (СССР)). Образуется стойкое беспористое диэлектрическое покрытие толщиной 0,1-0,2 мм, по которому гравированием легко получить любые надписи и изображения. Тогда технологический процесс несколько изменится: нанесение изоляции на рабочую поверхность будет производиться на заготовке, а далее будет следо-
191
вать гравирование, которое выполняется вращающимся инструментом (при ширине штриха более 0,2 мм) или же методом строгания (при ширине штриха не менее 0,03-0,05 мм).
В зависимости от положения изоляции создают зазор между электродами. При нанесении изоляции в углубления знаков ее площадь незначительна, и создание зазора путем местных выпуклостей не практикуется.
После изготовления знаков контролируют их геометрические размеры, расположение знаков, качество изоляции и зазор (по контрольному маркированию, измерениями).
С применением гравированных знаков можно выполнять мелкое и глубокое маркирование.
Вырезкой (при малом количестве знаков) или вырубкой получают отдельные элементы, знаки или всю наносимую информацию, связанную перемычками, удерживающими части знаков от выпадания. Перемычки могут быть минимальной ширины, ограниченной возможностями штамповки (свыше 0,3 мм). После закрепления информации на рабочей части инструмента такие перемычки можно удалить.
При вырезке контроль качества знаков выполняют до закрепления их на рабочей части инструмента; в случае вырубки такой контроль совмещают с окончательным, а геометрические размеры не проверяют, так как они переносятся со штампа. Однако во всех случаях необходимо измерить удельное электрическое сопротивление между знаками и инструментом, которое должно быть не более (12-20) 10-8 Ом·м. Такие знаки используют в основном для глубокого маркирования.
При изготовлении инструментов для маркирования используют электрические и химические методы обработки.
Непрофилированным электродом можно получить как отдельные знаки, так и полный набор информации. Процесс можно вести на станках с программным управлением или же с обработкой профиля по шаблонам. Если используются электрохимические станки, то необходимо предусмотреть промывку и пассивацию деталей. Крепление знаков необходимо вы-
192
полнять, если использован проволочный электрод; при обработке концевой частью стержня знак получают непосредственно на рабочей части инструмента. Операции по доводке рабочей части, нанесению изоляции, созданию зазора и контролю такие же, как после изготовления знаков вырубкой. При выборе метода следует учесть, что при электроэрозионной обработке можно получить точность профиля в пределах 0,01 мм с острой кромкой, однако производительность здесь будет на 1-2 порядка ниже, чем при использовании электрохимического метода.
В случае прошивки или вскрытия профиля можно получить любой объемный знак, но при этом необходимо иметь инструмент с зеркальным отображением, который при электроэрозионной обработке изнашивается (до 20-40 % к объему снятого металла), поэтому такой метод применяется, если возникает необходимость в изготовлении значительного числа одинаковых инструментов для маркирования. Ширина штриха зависит от боковых зазоров, которые определяются режимом процесса удаления металла. Промывка и пассивация особенно необходимы после электрохимической обработки с применением электролитов. В случае вскрытия профиля лучом лазера эта операция необязательна, так как в ходе ее не возникает продуктов, влияющих на коррозионные свойства инструмента для маркирования.
Ультразвуковой метод прошивки может применяться при изготовлении инструментов из твердых сплавов и хрупких материалов.
Калибровка выполненных знаков включает устранение уклона стенки по глубине, создание наружной кромки. Полученный прошивкой и обработкой по контуру инструмент используется в основном для глубокого маркирования. Известен способ химического травления знаков, однако применение его ограничено из-за токсичности травильных растворов.
Технологический процесс фотохимического изготовле-
ния знаков позволяет наносить информацию непосредственно с чертежа, что исключает ее искажение при многократном по-
193
вторении, необходимость многократного возобновления покрытий и др. Процесс аналогичен фотографированию на поверхность инструмента с удалением эмульсии на участках, которые должны быть обработаны, и закреплением ее на выступающих частях инструмента.
Полученные заготовки обрабатывают на электрохимических станках с неподвижными электродами, при этом получают минимальные размеры перемычек от 0,2 мм и выше при глубине знака до 0,6 мм. После электрохимической обработки защитный сдой удаляют обычно путем тонкой зачистки абразивным инструментом.
Изготовление трафаретов. Мелкое и глубокое марки-
рование можно выполнять с использованием трафаретов, которые представляют собой плоские или объемные поверхности с просечками в местах нанесения информации. Форма и размеры просечек повторяют знаки, требуемые для маркирования.
Трафареты могут быть выполнены из диэлектрических материалов или металлов (рис. 3.40). В практике маркирования чаще используются диэлектрические трафареты, хотя они и обладают малой механической прочностью. Прочность трафарета должна составлять не менее 50 % прочности цельной пластины той же толщины. Поэтому при изготовлении информации между элементами знаков предусматривают перемычки. С той же целью трафарет наносят клеем, гальваническим или механическим методом, напылением на поверхность детали или инструмента.
Диэлектрические трафареты выполняют из полиэтилена, специальной бумаги, гетинакса, органического стекла, винипласта, лавсановой пленки и других материалов с толщиной рабочей части 0,1-0,5 мм. Опыт показал, что для плоских трафаретов наиболее подходящей является лавсановая пленка толщиной 0,2 мм. Объемные трафареты (например, для нанесения информации на головку винта) выполняют методом точения или объемного формообразования из органического стекла, винипласта с толщиной рабочей части 0,3-0,8 мм.
194

Рис. 3.40. Трафареты, применяемые для маркирования
Металлические трафареты могут быть выполнены с меньшей толщиной, чем диэлектрические, однако они сами требуют защиты от растворения. Практически могут применяться трафареты из титанового сплава, пассивированные в готовом виде при малой плотности тока в среде зашламленного электролита (по а.с. 310772 (СССР)), трафареты из коррозион- но-стойкой стали, покрытые керамическими эмалями, которые дают слой толщиной 0,03-0,05 мм, стойкий к механическому разрушению. Недостатком этого покрытия является высокая (до 1450 К) температура термообработки, что вызывает коробление деталей. Для разовых работ используют металлические трафареты без покрытия.
Независимо от материала, трафареты наносят на рабочую поверхность инструмента, детали или помещают в зазор на время маркирования, прижимая к аноду, катоду или перемещая в режиме вибрации между электродами (по а.с. 537782
195
(СССР)). Трафареты могут быть выполнены гравированием, горячим прессованием, в виде профиля, нанесенного фотохимическим методом.
При гравировании знаков плоскую или объемную заготовку обрабатывают концевой фрезой с углом заточки 8-10° и частотой вращения от 5 до 20 тыс. об/мин. На режущую поверхность инструмента наносят слой дисульфида молибдена. Если трафарет выполняют из диэлектрика, то для повышения механической прочности его наклеивают на подложку. Наименьшая высота знаков, которые можно получить гравированием – 2,5-3 мм. Можно также нанести диэлектрическое покрытие на поверхности инструмента или детали, например, путем окисления слоя никеля при высокой температуре, а затем выполнять гравированием требуемую информацию.
При горячем прессовании листовой заготовки требуемые знаки выполняют пуансоном с нанесенной на рабочую поверхность информацией в специальном приспособлении с нагревателем. После охлаждения с приспособлением рабочие поверхности обрабатывают (устраняют наплывы материала, выпуклости, устанавливают в рамку и др.). Процесс прессования позволяет получать знаки при минимальных механических силах, однако трудоемок и требует дорогостоящей оснастки.
Перспективны методы получения трафаретов путем серии разрядов по контуру индексов и, особенно, печатанием на обычных машинках, в результате чего можно получить надписи с высотой знака 1,5-2,0 мм без перемычек .При закреплении диэлектрического покрытия на аноде или катоде необходимо учитывать специфические требования, вытекающие из условий процесса электрохимического маркирования.
196
Вопросы для самоконтроля
1.Особенности проектирования оснастки для электрохимической размерной обработки (ЭХРО).
2.Конструкция и проектирование рабочих камер для ЭХО.
3.Расчет и изготовление каналов для прокачки электролита при ЭХО.
4.Расчет гидравлических трактов при ЭХО.
5.Примеры проектирования гидравлических трактов для ЭХО.
6.Выбор и расчет токоподводов при ЭХО.
7.Обеспечение условий контакта в местах подвода тока.
8.Выбор материалов для электрода-инструмента.
9.Проектирование электрододержателей.
10.Конструкция приспособлений для прошивки отверстий.
11.Методы защиты от коротких замыканий при выходе инструмента из отверстия.
12.Расчет формы электрода-инструмента для прошивки отверстий.
13.Конструкция ЭИ для прошивки отверстий.
14.Расчет ЭИ для обработки фасонных полостей.
15.Проектирование ЭИ для изготовления фасонных полостей.
16.Проектирование рабочей части приспособлений для снятия заусенцев.
17.Конструкция рабочей части приспособления для групповой прошивки отверстий.
18.Выбор базовых элементов для приспособлений.
19.Проектирование рабочего тракта для подачи электролита при перфорации отверстий.
20.Технико-экономические преимущества применения ЭХО для прошивки отверстий.
21.Область использования ЭХО в машиностроении.
22.Место диэлектрических покрытий на электродах.
23.Приспособления для удаления заусенцев в глубоких каналах.
197

4. ТЕХНОЛОГИЧЕСКАЯ ОСНАСТКА ДЛЯ УЛЬТРАЗВУКОВОЙ РАЗМЕРНОЙ ОБРАБОТКИ
4.1. Дополнительный инструмент
Колебательные системы ультразвуковых станков используются в технологических процессах размерной обработки хрупких материалов, для интенсификации операций резания при лезвийной и абразивной обработке, для ультразвукового упрочнения, удаления заусенцев, полирования деталей.
При размерной обработке обрабатывающим инструментом является абразив, подаваемый в рабочую зону в виде суспензии (смесь зерен и жидкости), а дополнительным инструментом (далее просто инструментом) служит твердый носитель формы углубления (отверстия, полости и др.).
Схема ультразвукового прошивания отверстий приведена на рис. 4.1.
Рис. 4.1. Схема ультразвукового прошивания отверстий
На рис. 4.1 инструменту 1 сообщают колебания с амплитудой 2Ак в направлении заготовки 2 с осевой подачей Vп и силой прижима Fст. Возможно также (для круглых отверстий) вращение инструмента 1 (или заготовки 2) со скоростью Vи. Подача суспензии выполняется через центральное отверстие инструмента.
198
В хрупких материалах возможно получение сквозных и глухих отверстий диаметром (d) до 20 мм и глубиной до 400 мм.
Для чистовых и отделочных операций применяют инструменты со свободным и связанным абразивом (бруски, диски и др.).
На рис. 4.2 показаны конструкции инструментов для ультразвуковой обработки (УЗО).
Инструменты (рис. 4.2) содержат корпус (1 или 5) абразивный инструмент (2, 4 или 6). Они соединены с концентратором 3, который тоже может быть дополнительным инструментом.
На рис. 4.2,а приведен инструмент для сверления или прошивки, работающий со свободным абразивом или со связанным абразивным слоем.
Для схемы шлифования применяют инструмент (рис. 4.2,б), имеющий кольцо с алмазным или абразивным слоем (4), или работающий с абразивной суспензией. Инструмент имеет вращение с частотой до 45 с-1.
Инструмент на рис 4.2,в имеет геометрию хона (5) с брусками 6, перемещаемыми во время обработки в радиальном направлении.
На рис. 4.2,г показан инструмент для доводки круглых участков деталей с последовательным перемещением его вдоль зоны обработки. Аналогичный инструмент (рис. 4.2,д) приведен для локальной доводки и полирования местных частей, например шпоночных пазов, где инструмент устанавливается в станок цилиндрическим хвостовиком 7.
Конструкция головки для УЗО отверстий с наложением тока приведена на рис. 4.3.
На рис. 4.3 головка соединена со шпинделем 1 сверлильного станка через пиноль 2. Она содержит корпус 3, шпиндель 4, коллектор 5 с токосъемными кольцами, щетки 6, подшипник 7, колебательную систему 8, штуцер для подвода жидкости 9, уплотнение 10 и корпус 11со шпинделем 12, имеющим на конце
199
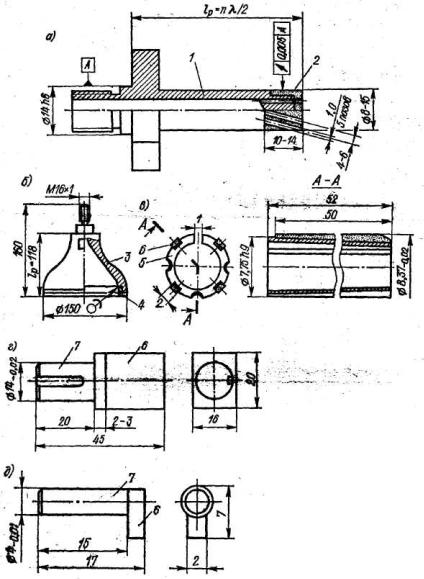
абразивное кольцо.
Рис. 4.2. Конструкции инструментов для ультразвуковой обработки
200