
3625
.pdf
ских схемах обработки: к ним относятся приспособления закрытого типа, контейнеры для обработки пера лопаток и др.
Рис. 3.1. Обработка с интенсивной прокачкой электролита через МЭП
Обработка с подачей инертного газа в электролит (рис. 3.3) была впервые предложена в Японии фирмой «Мицубиси Электрик Корпорейшен» и реализована на станках типа МС20V, MC-50V. При такой схеме в электролит перед входом в МЭП подается инертный газ с давлением Р, численное значение которого на 105 Па выше, чем давление электролита. В данном случае устраняется «струйность» и выравнивается скорость движения электролита по сечению, т.к. газожидкостная смесь обладает более упругими свойствами и низкой вязкостью, чем электролит. Эти свойства газожидкостной смеси особенно важны при обработке сложнофасонных поверхностей.
Для устранения влияния отрицательных свойств отработанного электролита (шлам, высокая температура электролита, газонаполнение) применяют обратную схему подачи жидкости (рис. 3.4). Эта схема приемлема для обработки длинномерных деталей.
141
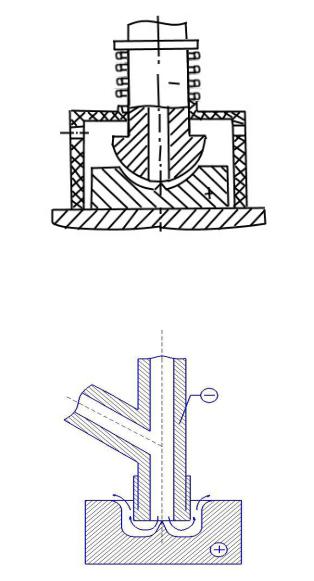
Рис. 3.2. Обработка в приспособлениях закрытого типа
Рис. 3.3. Обработка с подачей инертного газа в электролит
142

При изготовлении некоторых деталей, например профиля пера лопаток или гравюр штампов, приходится обработку выполнять при боковой подаче электролита (рис. 3.5). Эта категория приспособлений относится к схемам закрытого типа.
Рис. 3.4. Обратная схема подачи жидкости
Рис. 3.5. Обработка при боковой подаче электролита
143
При электрохимической размерной обработке надо рассматривать две группы камер.
К первой группе относятся камеры универсального назначения. Они являются частью станка и не играют никакой роли в формировании струи электролита в МЭП. Обычно такая камера выполняется со своим столом, установленным на дне камеры. В крышке выполнено отверстие для движения штока шпинделя станка, а на боковых стенках или на донышке имеются отверстия для подвода и вывода электролита. Предусмотрен также люк для установки заготовки.
Ко второй группе относятся камеры, работающие с повышенным давлением, обеспечивающим необходимый гидродинамический режим в МЭП. Эти камеры должны удовлетворять следующим требованиям:
-выдерживать значительные давления электролита при незначительной деформации;
-быть герметичными;
-не подвергаться коррозии от воздействия электролитов;
-быть удобными в эксплуатации и технологичными в изготовлении.
3.1.2.Выбор токоподводов
Ток от источника питания к механической части станка передают по гибким или жестким шинам. Используемые электрические проводники, кабели или шины должны иметь сечения, соответствующие силе передаваемого тока. Так, например, при силе тока до 100 А можно использовать отдельные провода большого сечения или их наборы. Если сила тока не превышает 1000-1200 А, то применяют наборы гибких медных оплеток или пакеты медной фольги. При силе тока до 20000 А используют шины в виде полос из меди, алюминия и их сплавов. Иногда токоподводы делают охлаждаемыми (воздухом или водой).
Площадь сечения токоподвода Sт находят из условия прохождения по нему технологического тока Iт с предельной
144

плотностью JN |
|
ST = IT / JN. |
(3.2) |
Для медных токоподводов без охлаждения |
JN = 1-2 |
А/мм2, для алюминиевых – JN = 0,8-1,5 А/мм2. При охлаждении водой JN = 3-6 А/мм2 и JN = 2-3 А/мм2 соответственно для медных и алюминиевых проводов.
На станках для ЭХО токоведущие шины или кабели из луженой меди соединяют генератор с двумя точками внутри станины (точка А и В, рис. 3.6), одна из которых соединена с положительным полюсом (анод), а другая с отрицательным (катод). Эти проводники не должны находиться в коррозионноопасной среде. Из точек А и В отходят другие проводники, соединяющие внутреннюю часть рабочей камеры, стол и электрододержатель.
Рис. 3.6. Токоведущие шины или кабели на станках для ЭХО
Обычно отрицательный полюс источника тока не изолируется от корпуса станка, благодаря чему станок во время работы защищен от электрохимической коррозии. Во многих современных конструкциях станков стол выполняется из гранита, базальта и других материалов, а положительный полюс источника питания присоединяется непосредственно к деталям или приспособлению. Для этого кабели положительного полюса должны быть гибкими и удобно монтироваться.
145

Наиболее целесообразно в антикоррозионном отношении применять кабели в изолирующей оплётке, которая должна герметизировать провод от электролита. Способ герметизации кабелей показан на рис. 3.7.
Рис. 3.7. Герметизация кабеля:
1 – провод; 2 – изоляция; 3 – наконечник; 4 – заливка диэлектриком
Наибольшие трудности вызывают переходные контакты, устанавливаемые непосредственно к оснастке и расположенные между оснасткой и деталью. Контакт должен обеспечивать наименьшие величины переходных сопротивлений, особенно при большой силе технологического тока. Примеры контактирования детали и ЭИ с токоподводами приведены на рис. 3.8.
Рис. 3.8. Место контактирования детали и ЭИ с токоподводами
146
Для надёжной передачи тока следует правильно выбрать силу прижима и размеры контактных площадок. От этого будут зависеть потери напряжения, которые при нормальных условиях эксплуатации не должны превышать (0,03-0,05) UL, где U - нормальное напряжение, В; L - длина токоведущих шин. Для снижения потерь напряжения и мощности необходимо обеспечить плотность прижима в контактных соединениях для меди (60-100) 105 Па, для алюминия – 250 105 Па. Площадь контакта в местах соединений рассчитывают по формуле
Sк IT / jk , |
(3.3) |
где jk - предельная плотность тока через контакт (без охлаждения jk 1А/мм2 , c охлаждением jk 8А/мм2 ).
По формуле (3.2) рассчитывают также условия закрепления деталей в базовых элементах приспособления. Эффективно также использование тонких металлических прокладок в местах контакта токоподводов путем их плотного обжатия обеими поверхностями (заготовки и токоподвода). На рис. 3.9 показан способ подвода тока к заготовке 2 и столу 3 станка через мягкую (например, из свинца) контактную вставку 4, которая поднимается к заготовке 2, противостоящий электродуинструменту 1, посредством силы F, создаваемой каким-либо упругим элементом.
На рис. 3.10 показан способ подвода тока к заготовке 3 и столу 1 станка посредством вставки 2 из токопроводящего материала, который прижимается к заготовке 3 посредством пружины. В случаях, когда конфигурация детали не позволяет осуществить токопередачу через стол, кабели токоподводов прикрепляют непосредственно к детали. Если подводится ток большой силы, то его необходимо передавать на деталь не только через стол станка, но и через дополнительные токоподводы в оснастке.
При конструировании ЭИ следует учитывать, что кар-
147

маны и распределительные пазы значительно уменьшают сечение металла электрода, через которые проходит ток. Кроме того, могут быть потери подводимой энергии в стыках формообразующей части ЭИ с распределительными жгутами. Поэтому контактную поверхность в местах стыков ЭИ нужно рассчитывать из условия пропускания тока плотностью 1,8-2 А/мм2.
Рис. 3.9. Подвод тока к заготовке 2 и столу 3 станка через мягкую контактную вставку
Рис. 3.10. Токоподвод от стойки станка к цилиндрической детали при помощи жгутов
148
Для хорошего контактирования отдельных элементов оснастки, стола, инструмента и заготовки необходимо соблюдать следующие условия:
-на поверхности заготовки не должно быть загрязнений (масляных пятен, окисных пленок, окалины);
-шероховатость контактирующих поверхностей должна быть не выше 0,63 мкм;
-отклонение от плоскостности не хуже 7-8 степени точности;
-необходимо обеспечить возможность использования больших прижимающих сил;
-следует максимально увеличить площадь контакта;
-по возможности применять прокладки из мягких материалов, обладающих большой электропроводностью;
-токоподводы следует располагать как можно ближе к месту обработки.
3.1.3.Конструкции типовых приспособлений
Схемы ЭXРO разнообразны, так же разнообразны конструкции приспособлений.
При обработке заготовок по схемам поступательного перемещения электрода-инструмента (ЭИ) и неподвижной заготовки (прошивка), вращении заготовки и поступательного перемещения ЭИ (типа токарной операции), вращении ЭИ и поступательном перемещении заготовки и других схемах шпиндельный узел, камера выполняют определенные функции, обеспечивающие процесс ЭХРО. Конструкции оснастки при одноместных приспособлениях для этих схем достаточно просты и они рассмотрены ранее.
Оригинальная конструкция оснастки получается при обработке деталей в стационарных условиях, т.е. при неподвижной заготовке и ЭИ, По данной схеме выполняются операции электрохимической зачистки заусенцев, клеймения, перфорации, образования карманов, полостей и другие работы, связанные со снятием небольшого припуска (от 0,1 до 2 мм). В процессе обработки по мере растворения металла межэлектродный
149

зазор увеличивается по параболическому закону, плотность тока и скорость движения электролита уменьшаются, поэтому при снятии больших припусков ухудшается точность и качество обработки.
С целью унификации конструкций приспособлений в мелкосерийном производстве применяют групповые приспособления со сменными вставками (наладками). На рис. 3.11 показана конструкция шестиместного приспособления, которая может быть применена для выполнения всех вышеперечисленных операций с соответствующими сменными вставками.
Посадочные поверхности у сменных вставок должны иметь постоянные размеры, которые определяются внутренним диаметром втулки 2 и размером отверстия d на плите 1 группового приспособления. Отрицательный полюс постоянного тока к электродам подводится через плиту, а положительный – к обрабатываемым деталям через прижим 3 приспособления. Одновременно можно обрабатывать 3 или 6 деталей.
Рис. 3.11. Шестиместное приспособление со сменными вставками (начало)
150