
3565
.pdf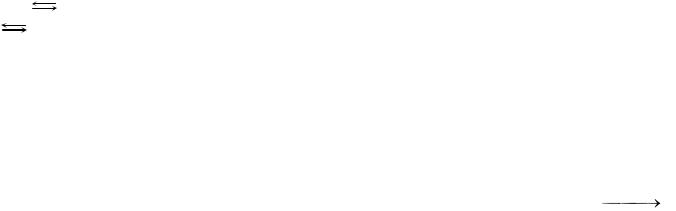
сталлами. |
|
|
противление пленок Ag2S увеличивается и они |
|
Серебряное покрытие на корпуса наносят галь- |
становятся электроизоляционными. Образование |
|||
ваническим способом только на участки под пайку |
сульфидных пленок при хранении или запрес- |
|||
кристаллов и разварку внутренних выводов. Серебря- |
совке в пластмассу может привести к полной по- |
|||
ные покрытия, полученные из обычных электролитов, |
тере паяемости серебра оловянно-свинцовыми |
|||
характеризуются малой твердостью и незначительной |
припоями. |
|
||
износостойкостью. Для улучшения этих параметров в |
При температуре 175 °С и выше проявляет- |
|||
электролит при серебрении вводят соли никеля или |
ся металлический характер проводимости. В си- |
|||
кобальта. В этом случае твердость покрытия повыша- |
лу этого контактная пара может удовлетвори- |
|||
ется в 1,5, а износостойкость – почти в 3 раза. |
тельно работать при повышенных температурах |
|||
Известно, что серебро обладает чрезвычайно вы- |
при наличии плотной и прочно сцепленной |
|||
сокой чувствительностью к окружающей воздушной |
сульфидной пленки с поверхностью покрытия. В |
|||
среде. На поверхности серебра появляются оксидные |
то же время следует помнить, что термообработ- |
|||
пленки толщиной 10 – 20 нм, серебряное покрытие |
ка серебряных гальванических покрытий при |
|||
темнеет. Ионы серебра вступают в реакции с другими |
температуре 400 °С приводит к их отслаиванию |
|||
ионами с образованием труднорастворимых соедине- |
от основы. |
|
||
ний, например сульфида серебра |
|
С точки зрения электропроводимости Ag2S |
||
Ag2O + H2O |
2AgOH; |
является полупроводником n-типа проводимо- |
||
AgОН |
Ag+ + ОН–; |
сти. Наивысшей проводимостью обладает Ag2S в |
||
2Ag+ + 2OH– + H2S → Ag2S ↓ + 2H2O. |
γ-модификации при температуре выше 178 °С. |
|||
Сульфид серебра может образовываться также и |
Из фазовой диаграммы системы Ag – S видно, |
|||
при непосредственном воздействии сероводорода на |
что при температуре выше 178 °С происходит |
|||
серебро. Известно, что Ag2S может существовать в |
изменение в структуре от α-Ag2S к γ-Ag2S. Этот |
|||
трех модификациях: α-модификации, устойчивой до |
переход сопровождается изменением внешнего |
|||
температуры 110 °С; β-модификации, устойчивой в |
вида потемневшего покрытия при нагреве. Воз- |
|||
интервале температур 90 – 175 °С; γ-модификации, |
можно и протекание реакции |
2Ag + SO2. |
||
образующейся при температурах, превышающих |
Ag2S + O2 |
|||
|
|
|
нагрев |
|
175°С. Проводимость сульфида серебра резко меня- |
Влияние сульфида серебра (потускневшее |
|||
ется с температурой, при температуре 26 °С она не- |
серебро) на выводных рамках с серебряным по- |
|||
значительна. |
|
|
крытием на процессы пайки кристаллов и при- |
|
При понижении температуры электрическое со- |
соединения выводов подробно рассмотрено в ра- |
|||
138 |
|
|
139 |
|
боте.
Следует отметить, что сульфид серебра не всегда формируется в виде пленок. В некоторых случаях на серебряном покрытии вырастают тонкие копьевидные кристаллы длиной до 3 – 5 мм, способные приводить к короткому замыканию близлежащих цепей или их размыканию при пониженных температурах. Начало роста нитевидных кристаллов Ag2S происходит на границе раздела фаз Ag – Ag2S, его росту способствуют повышенная влажность и нагрев. Полагают, что рост кристаллов сульфида серебра происходит изза повышенной миграции ионов серебра к активным центрам и высокой подвижности их в присутствии влаги, адсорбируемой пленкой сульфида. Условия, в которых могут вырастать кристаллы сульфида серебра, не поддаются точному прогнозу. В силу этого, конструктор должен знать о вероятности их образования и учитывать это явление при проектировании ИЭТ, особенно при выборе покрытий под пайку или сварку. Знание этого явления позволит производить работоспособные и надежные ИЭТ.
Методами микрорентгеноспектрального анализа и сканирующей электронной микроскопии исследовано серебряное покрытие на печатных платах из фольгированного стеклотекстолита марки СФ. Исследования показали, что гальваническое покрытие имеет ровные и плотные участки размером 20 – 50 мкм, чередующиеся с участками неправильной формы, в которых сконцентрированы поры размером 0,5 – 1 мкм. Отмечено, что в порах серебряное покрытие имеет толщину менее 1 мкм.
Покрытия никелем и его сплавами. Покры-
тия корпусов ИЭТ никелем и его сплавами широко используются в электронной промышленности. Основным недостатком никелевых покрытии является низкая теплостойкость, поэтому их применяют только при низкотемпературном монтаже элементов или при пайке в защитной среде. Для повышения теплостойкости никелевые покрытия легируются тугоплавкими металлами Со, W, Mo, Re и В. Практическое применение в электронной промышленности нашли покрытия никеля, легированные до 1 % В. Легирование никеля бором существенно повышает температурную стабильность сплава даже при малой концентрации бора, а микротвердость и хрупкость покрытия уменьшают путем отжига.
Установлено, что паяемость покрытий никель – бор (с содержанием бора от 0,46 до 0,87 %) припоем ПОС61 со спиртоканифольным флюсом лучше, чем никелевых. Коэффициент растекания составляет от 1,03 до 1,10, что согласно ГОСТу 9.302-79 считается удовлетворительным. Это связано с тем, что легирование никелевых покрытий бором способствует уменьшению образования поверхностных оксидов никеля (NiO и Ni2O3), а оксидная пленка, образующаяся при окислении бора (В2О3), легко удаляется флюсом при температуре расплавленного припоя и не препятствует смачиванию покрытия.
Следует отметить, что при изготовлении некоторых полупроводниковых ИЭТ кристаллы к
140
корпусам припаиваются без флюса (в защитной среде). Поэтому паяемость покрытий никель – бор в данных средах может отличаться от паяемости с использованием флюсов.
Гальванические покрытия контактных поверхностей кристалла и корпуса при пайке ИЭТ должны обладать не только хорошей смачиваемостью, но и высокой коррозионной стойкостью. Этим требованиям в полной мере отвечают сплавы никеля с оловом и индием.
При осаждении сплава олово – никель необходимо строго соблюдать условия электроосаждения: температуру электролиза, соотношение концентраций компонентов электролита, плотность тока. Практическое значение получили фторидхлоридные электролиты, из которых получают блестящие покрытия с содержанием олова от 50 до 65 %. Основными компонентами электролита являются хлориды олова и никеля, фториды натрия и аммония. Недостатком электролита является то, что в присутствии фторида аммония покрытия осаждаются хрупкие, что значительно снижает их способность к пайке. Установлено, что введение во фторидхлоридный электролит органической добавки ОС-20 позволяет получать качественно другие покрытия из сплава никель – олово, не блестящие, а серебристо-белые. ОС-20 – это оксиэтилированный спирт неионогенного характера
RO(CH2CH2О)nCH2CH2OH,
где R – алкильный остаток, содержащий 16 – 18 атомов углерода; n = 19 – 24.
Для осаждения паяемых блестящих электроли-
тических покрытий сплавом никель – олово в качестве блескообразователя применяются фторид аммония и многие другие органические добавки.
Исследования микроструктуры поверхности покрытий, полученных из электролитов с добавкой препарата ОС-20 при плотности тока 0,75 А/дм2 и различных температурах, показали следующие результаты. При температуре 40 °С получаются крупнокристаллические покрытия, в которых массовая доля олова составляет 99,8 % (по технологии электролиза – 65 %). Повышение температуры электролита до 65 – 80 ºС (без добавки препарата ОС-20 или при содержании его в электролите 5 г/л) приводило к увеличению массовой доли никеля в сплаве до 30 – 35 %. Получаемые покрытия приобретало мелкокристаллическую структуру и блеск.
Установлено влияние добавки ОС-20 на коррозионную стойкость сплавов никель – олово
иникель – индий. Исследовалось не только электрохимическое поведение покрытий из этих сплавов, нанесенных на бериллиевую основу, но
испособность этих покрытий к пайке. Для исследований влияния термообработки на качество облуживаемости использовались образцы из бериллиевой бронзы с покрытиями из никеля, сплавов никель – олово и никель – индий. Образцы выдерживали в термошкафу при 170 °С в течение 4 ч, при 150 °С – 7 ч и при 125 °С – 14 ч. Последующее облуживание припоем ПОС61 со спиртоканифольным флюсом показало для пер-
142
вых двух температур 100 %-ную облуживаемость с |
ния |
электрофизических и диэлектрических |
покрытием из сплавов никель – олово и никель – ин- |
свойств пленочных покрытий. |
|
дий и неудовлетворительную – для никелевых покры- |
В |
производстве полупроводниковых ИЭТ |
тий. Для температуры 125 °С установлена 100 %-ная |
для исследований пленочной металлизации ши- |
|
облуживаемость для покрытий никель – олово и ни- |
роко используется следующее оборудование: |
|
кель – индий и 20 %-ная для никелевого. Следует от- |
растровый электронный микроскоп типа IEM- |
|
метить, что покрытия из сплавов никель – олово и |
100СХ, растровый электронный микрозонд |
|
никель – индий сохраняют 100 %-ную паяемость по- |
РЭМП-6 и Оже-спектрометр типа 09ИОС-10-005. |
|
сле выдержки при комнатной температуре в течение 5 |
Загрязнения поверхности пленочной металлиза- |
|
лет. |
ции контролируются методами контактной раз- |
|
Результаты исследований показали, что покры- |
ности потенциалов и «мягкого» зонда. |
тия из сплавов никель – олово (30 – 50 % Ni) и никель
– индий (10 – 30 % In) можно использовать как припой для пайки на химический никель. Более качественный внешний вид покрытий, а также небольшое преимущество в коррозионной стойкости делает предпочтительным использование покрытия из сплава никель – индий.
Контроль качества покрытий. В технологии производства ИЭТ для контроля качества, структуры и свойств получаемых покрытий применяются различные методы. Например, внешний вид, состояние структуры поверхности и конфигурация пленочных элементов контролируются визуально с помощью оптических микроскопов. Наиболее качественен контроль при использовании электронных, в том числе растровых электронных микроскопов. Субструктура пленок контролируется методами электронографии и рентгенографии, а компонентный состав – с помощью химического или микрорентгеноспектрального анализов. При необходимости проводятся также измере-

5.2. Инструмент для сварки внутренних выводов
Сварочный инструмент является одним из основных элементов сварочного оборудования, от которого зависит получение качественных соединений СПП.
При сварке широко применяются капилляры с боковым отверстием. При разработке инструмента с боковым отверстием для автоматических сварочных установок необходимо учитывать условие гарантированного совмещения проволоки с рабочим пазом инструмента и ограничения на ее свободную протяжку. Опытным путем найдены оптимальные соотношения между размерами рабочих элементов инструмента и диаметром привариваемой проволоки, на базе которых предложена конструкция инструмента для автоматической сварки.
Площадь физического контакта проволочных выводов с контактными площадками при сварке может быть увеличена за счет изменения формы торца инструмента. Установлено, что при УЗС инструментом с V-образным пазом на торце при одной и той же степени деформации алюминиевой проволоки усилие осадки будет больше, чем для инструмента с плоским торцом. Это приводит к активации контактных поверхностей и увеличению площади физического контакта в зоне проволока-пленка, а, следовательно, и к повышению прочности сварных соединений.
Рекомендуется проводить сварку при усилии нагружения инструмента при сварке (Fсв.) меньше оптимального сварочного давления (Fсв.опт). При сварочном давлении Fсв. > Fсв. опт. возможно снижение прочности соединения. При усилиях Fсв. Fсв. опт. получают
144
качественные соединения с деформацией алюминиевой проволоки 30 – 50 %. Эти режимы обеспечивают максимальную прочность сварных соединений при высокой производительности процесса монтажа.
Одним из основных показателей, характеризующих качество проволочного монтажа, является прочность проволочной перемычки на растяжение, которая зависит от площади зон взаимодействия материалов в сварном соединении и от состояния участка перехода проволоки из сварного соединения в вывод, т. е. от прочности «шейки» вывода. Поэтому при выборе режимов сварки необходимо определять оптимальную степень деформации проволоки, при которой не происходит чрезмерного ослабления «шейки». На прочность «шейки» большое влияние оказывают размеры и чистота поверхности капиллярного отверстия, через которое протягивают проволоку в процессе формирования перемычки, т. к. трение проволоки в отверстии сварочного инструмента может ослаблять прочность перемычки.
Известно, что максимальная сила трения возникает после сварки на кристалле в начальный момент перемещения инструмента на позицию сварки на траверсе или корпусе. Эта сила не разрушает сварное соединение, если создаваемое усилие при протягивании проволоки через капиллярное отверстие меньше заданного значения прочности «шейки» вывода. Зная минимальное
145
усилие отрыва для данного сечения проволоки, можно подобрать такое сечение капиллярного отверстия сварочного инструмента, в котором сила трения при протягивании проволоки не создает усилий отрыва больше допустимых значений. При этом прочность проволочной перемычки должна регистрироваться с помощью специальных датчиков.
Следует отметить, что перечисленные выше конструкции сварочных инструментов используются в установках для сборки маломощных полупроводниковых ИЭТ, в которых перемычка между кристаллом и траверсами корпуса формируется проволокой диаметром до 0,06 мм.
В СПП при УЗС выводов используется алюминиевая проволока диаметром 0,25 мм и более. Соединения должны иметь плавный переход сварного соединения в проволоку, «без шейки», так как повышенное напряженное состояние данного участка соединения приводит к увеличению электрического сопротивления контактов под токовой нагрузкой и, естественно, к снижению надежности СПП.
Для УЗС проволочных выводов в СПП разработана конструкция сварочного инструмента. Инструмент для УЗС (рис. 5.1) имеет рабочую площадку 1 с продольной канавкой 2, поперечное сечение которой имеет форму равнобочной трапеции с размерами в нижнем основании 1,0 d, в верхнем – 0,75 d и высотой 0,6 d, где d – диаметр привариваемой проволоки. При этом радиус закругления R1 на передней кромке рабочей площадки инструмента равен радиусу изгиба проволоки при сварке на корпусе, а радиус закругле-
ния R2 – соответствует радиусу изгиба проволоки при подаче ее через капиллярное отверстие в зону сварки на кристалле.
Ширина канавки на рабочей площадке инструмента в нижнем основании, равная диаметру привариваемой проволоки, обеспечивает центрирование проволоки относительно контактной площадки при сварке. Глубина канавки, равная 0,6 диаметра проволоки, ограничивает деформацию проволоки при сварке и практически исключает ее заклинивание в канавке инструмента после сварки.
Радиусы закругления R1 на передней кромке рабочей площадки инструмента и R2 на задней кромке – позволяют формировать плавный переход от сварного соединения к недеформированному сечению проволоки, т. е. получать сварные соединения без «шейки». Радиус R1 зависит от формы перемычки проволоки между кристаллом и корпусом, а радиус R2 – от упругих свойств проволоки и угла наклона капиллярного отверстия инструмента.
Схема присоединения проволочных выводов в диодах Шоттки в корпусе ТО-220 представлена на рис. 5.2.
Использование разработанной конструкции инструмента для УЗС по сравнению с существующими конструкциями имеет следующие преимущества: обеспечивает напряженное состояние в проволоке в зоне сварки близкое к всестороннему сжатию; способствует минимальной
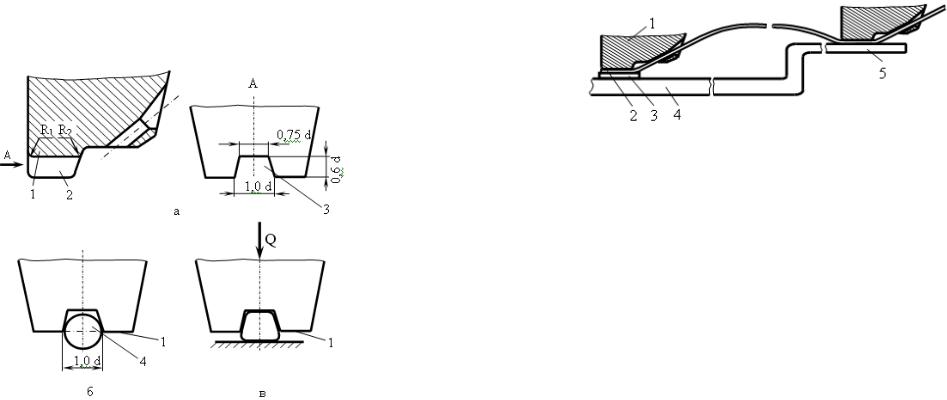
деформации привариваемой проволоки в зоне сварки; создает
Рис. 5.2. Схема формирования проволочной перемычки между кристаллом и корпусом диодов Шоттки: 1 – сварочный инструмент; 2 – привариваемая проволока; 3 – кристалл; 4 – корпус;
|
5 – траверса корпуса |
|
плавный переход от сварного соединения к не- |
|
деформированному сечению проволоки. |
|
Для соединений между кристаллом и тра- |
|
версами корпуса СПП, как было отмечено выше, |
|
целесообразно использовать проволоку диамет- |
|
ром 0,4 – 0,5 мм. Для УЗС проволоки данных |
|
размеров требуются повышенные мощность |
Рис. 5.1. Инструмент для УЗС проволочных вы- |
ультразвукового генератора и давление свароч- |
водов СПП: а – рабочий торец инструмента в разрезе; |
ного инструмента. Кроме того, использование |
б – положение проволоки в канавке инструмента пе- |
проволоки приводит к неравномерной прочности |
ред сваркой; в – положение проволоки в канавке ин- |
сварного соединения по площади взаимодейст- |
струмента после сварки: 1 – рабочая площадка; 2 – |
вия проволоки с контактной площадкой кристал- |
продольная канавка, 3 – поперечное сечение канавки; |
ла или корпуса. Наибольшая площадь контакти- |
4 – привариваемая проволока; Q – давление инстру- |
рования проволоки с пленкой характерна для |
мента при сварке |
центральной области проволоки. |
|
«Жесткие режимы» УЗС, особенно на кристалле, |
|
приводят к ухудшению электрических параметров СПП. |
|
Поэтому для обеспечения заданной мощности, подавае- |
|
мой на СПП между кристаллом и траверсами корпуса |
|
формируют по 2 или 3 перемычки из проволоки диамет- |
147
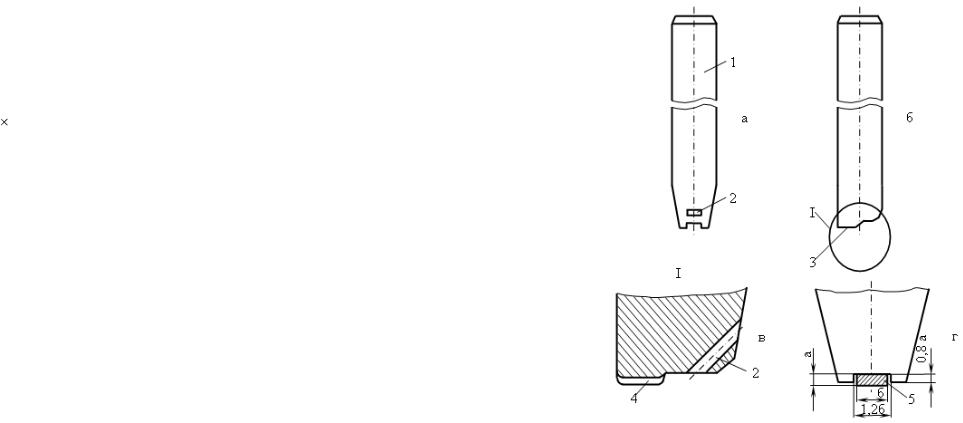
ром 0,25 мм. Данная технология приводит к повышению себестоимости выпускаемых СПП.
Анализ способов и технологии монтажа внутренних соединений в СПП показал, что целесообразно использовать ленточные выводы вместо проволочных. Например, проволока диаметром 0,4 мм соответствует ленте с поперечным сечением
0,2 0,6 мм.
В связи с вышеизложенным, разработана конструкция инструмента для сварки ленточных выводов к контактным площадкам СПП. Инструмент для сварки (рис. 5.3) представляет собой цилиндрический стержень 1 с боковым отверстием 2 прямоугольной формы, на конусном торце которого имеется рабочая площадка 3 с продольной канавкой 4 высотой до 0,8 а и шириной до 1,2 б, где “а” – толщина, а “б” – ширина привариваемого вывода.
Ширина канавки на рабочей площадке инструмента, составляющая до 1,2 ширины привариваемого вывода, обеспечивает центрирование вывода относительной контактной площадки при сварке.
Рис. 5.3. Инструмент для сварки ленточных выводов СПП: а – вид со стороны подачи ленточного вывода; б – вид сбоку; в – рабочая площадка в разрезе; г – положение ленты в канавке инструмента перед сваркой: 1 – корпус инструмента; 2 – боковое отверстие; 3 – рабочая площадка; 4 – продольная канавка; 5 – привариваемая лента
Высота канавки, составляющая до 0,8 толщины вывода, обеспечивает необходимую де-
148 |
149 |
формацию вывода при сварке и исключает контактирование выступов инструмента с контактной площадкой.
Боковое отверстие для подачи привариваемого вывода, выполненное в виде прямоугольника обеспечивает перемещение вывода в зону сварки.
Инструмент работает следующим образом. Привариваемая лента толщиной “а” и шириной
“б” пропускается через боковое отверстие 2 инструмента таким образом, при котором конец ее располагается в пазу 4 рабочей площадки 3 и совмещается с контактной площадкой на кристалле. После сварки на кристалле инструмент перемещается вверх к сварке на корпусе.
При этом вывод протаскивается через боковое отверстие 2, деформируясь и образуя петлю. При небольшом превышении размеров отверстия 2 относительно размеров вывода происходит надрыв сварного соединения на кристалле. При значительном превышении надрывы исключаются, но ухудшается точность совмещения вывода относительно рабочей площадки инструмента и контактной площадкой на траверсе корпуса.
Выполнение бокового отверстия в форме прямоугольника с заданными размерами улучшает прохождение привариваемой ленты через отверстие, исключает надрывы сварного соединения при подъеме инструмента вверх после образования сварного соединения на кристалле и повышает точность подачи вывода под рабочую площадку инструмента к месту сварки на корпусе.
150
При сварке на кристалле или корпусе инструмент, имеющий продольную канавку на рабочей площадке высотой до 0,8 а и шириной до 1,2 б, где “а” – толщина, а “б” – ширина привариваемого вывода, обеспечивает центрирование вывода относительно контактной площадки и минимальную его деформацию, а также исключает контактирование выступов инструмента с контактной площадкой при сварке.
Сварка инструментом с продольной канавкой на рабочей площадке обеспечивает равномерную прочность сварного соединения по всей площади взаимодействия ленточного вывода с контактной площадкой кристалла или корпуса.
Таким образом, использование предлагаемого инструмента для сварки по сравнению с существующими конструкциями имеет следующие преимущества: возможность сварки ленточных выводов; способствует минимальной деформации привариваемого вывода в зоне сварки; получение равномерной прочности сварных соединений по всей площади взаимодействия вывода с контактной площадкой кристалла или корпуса; исключает контактирование выступов инструмента с контактной площадкой при сварке.
Следует отметить, что использование данной конструкции инструмента для сварки ленточных выводов возможно на установке, которая обеспечивает получение качественных сварных соединений, особенно на кристаллах СПП. Для
151
этой цели необходимо использование специального способа сварки, позволяющего разрушать и удалять оксидные пленки с соединяемых поверхностей, а также обеспечивать необходимую пластичность материалов в зоне сварного соединения.
5.3.Соединение полупроводниковых кристаллов
соснованиями корпусов методом пайки
В производстве полупроводниковых ИЭТ на многих сборочных операциях широко используется пайка. На такие операции пайки, как монтаж кристаллов, присоединение внутренних выводов, герметизация, приходится более 25 % общей трудоемкости сборочных операций.
Качество пайки во многом зависит от места расположения припоя. При традиционном расположении прокладки припоя непосредственно под кристаллом в процессе пайки оксидные пленки и загрязнения на поверхности прокладки при расплавлении остаются в зоне шва, что ухудшает смачиваемость припоем поверхности кристалла и корпуса, нарушает сплошность шва, а это в свою очередь приводит к ухудшению его теплопроводности и снижению надежности ИЭТ.
Для улучшения смачивания припоем паяемой поверхности кристалла и основания корпуса широко используют капиллярный эффект заполнения зазора припоем в процессе пайки кристалла. Перед пайкой в непосредственном касании одной из боковых граней кристалла располагается навеска припоя в виде ша-
рика. Детали фиксируются относительно корпуса специальной кассетой, помещаемой в конвейерную водородную печь. Здесь при температуре (390 ± 20) °С происходит расплавление припоя, который благодаря капиллярным силам заполняет микрозазор между коллекторной стороной кристалла и основанием корпуса, смачивает эти поверхности, и при кристаллизации образуется паяный шов. Характерной особенностью этого процесса является то, что оксидные пленки и загрязнения остаются за пределами паяного шва – в месте первоначального расположения навески припоя.
Пайка кристаллов мощных транзисторов на мягкий припой более предпочтительна, нежели эвтектическая контактно-реактивная, так как в жестких эвтектических швах, особенно в случае пайки кристаллов больших размеров, могут возникать внутренние напряжения, приводящие к разрушению кристалла. В паяных соединениях кристаллов, образованных мягкими припоями, внутренние напряжения частично релаксируются и разрушения кристаллов даже при циклических испытаниях не наблюдаются.
Таким образом, при соединении кристаллов с основаниями корпусов наиболее широко применяется пайка, так как она обеспечивает металлургическую связь, а главное, электрический контакт, который с увеличением площади спая повышает надежность механического контакта и электрические характеристики полупроводнико-