
3565
.pdf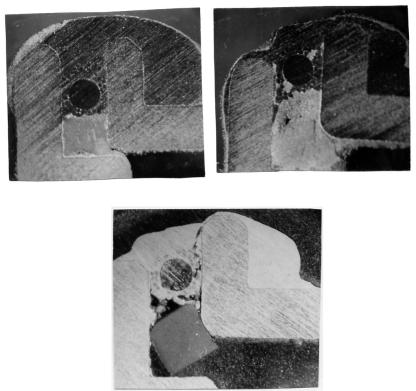
нений из сплава AМг, покрытого химическим никелем толщиной 9 мкм, а сверху белой бронзой (45 % меди и 55 % олова). Микроструктурный анализ паяных соединений корпусов микросборок показал, что качество адгезии покрытий никеля, меди и серебра хорошее. Разновысотность буртиков крышки и корпуса приводит при пайке паяльником к неравномерному прогреву соединяемых деталей, что вызывает плохое смачивание припоем отдельных участков крышки или корпуса. Некачественная сборка крышки с корпусом также приводит к неравномерному зазору по периметру корпуса, что существенно влияет на смачивание и капиллярное течение припоя при пайке.
а) |
б) |
в)
Рис. 7.3. Поперечное сечение паяных соединений корпусов микросборок с уплотнительными прокладками: а – качественное соединение; б и в – соединения с плохой пайкой
7.5. Герметизация ИЭТ пластмассой
Различают следующие технологические способы пластмассовой герметизации: компрессионное прессование; литьевое (трансферное) прессование; опрессовка с помощью жидких композиций; обволакивание и окунание; герметизация в полые пластмассовые корпуса; заливка во вспомогательные съемные формы; заливка в предварительно изготовленный корпус – капсулу.
7.5.1. Герметизация прессованием пластмасс
Метод герметизации основана на свойствах полимерных материалов расплавляться и течь под действием температуры и давления, заполняя при этом пустоты металлической фермы с изделиями. Используют два основных способа герметизации прессованием: компрессионное и литьевое (трансферное).
При компрессионном прессовании прессматериал помещаются непосредственно в прессформу, при литьевом – в загрузочную камеру.
Сущность компрессионного прессования состоит в том, что плавление герметизирующего
199
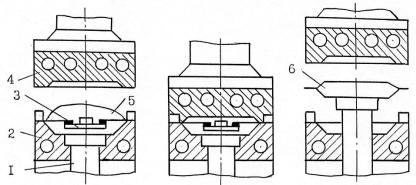
материала и заливка им полупроводниковых приборов и ИС осуществляется в пресс-форме с частичной полимеризацией (рис. 7.4).
При смыкании пресс-формы пресс-материал под действием теплоты и давления переходит в пластическое состояние и запоминает формирующую полость. По окончании выдержки опрессованые изделия вынимают из пресс-формы.
Компрессионное прессование применяют в том случае, когда пластмасса имеет температуру плавления не более 300 °С и низкое давление прессования, при котором не повреждаются металлическая арматура, кристалл (плата) и электродные выводы. С целью снижения вероятности повреждений кристаллы и электродные выводы защищают лаками, смолами или компаундами.
а) |
б) |
в) |
Рис. 7.4. Герметизация полупроводниковых приборов и ИМС пластмассовой компрессионными прессованием:
а – загрузка пластмассы и изделия; б – прессование; в
–выталкивание изделия; 1 – выталкиватель; 2, 4
–нижняя и верхняя части пресс-формы; 3 – кристалл; 5 – пресс-порошок (таблетка пластмассы); 6 – готовый прибор
7.5.2.Литьевое прессование
Этот способ является наиболее современным для создания бескорпусных оболочек. Он основан на использовании разъемных прессформ и пресс-порошков, получаемых из эпоксидных и кремнийорганических смол или их композиций. Металлическую ленту с кристаллами и выводами укладывают в пресс-форму, имеющую систему каналов (литников) и загрузочную камеру для прессматериала. Прессформу помещают между двумя плитами – нагревателями пресса, затем происходит смыкание двух половин пресс-формы и продавливание компаунд, перешедшего под воздействием давления и температуры в вязко-текучее состояние, через матричные отверстия в рабочую зону, в которой и происходит герметизация ленты с кристаллами (рис. 7.5).
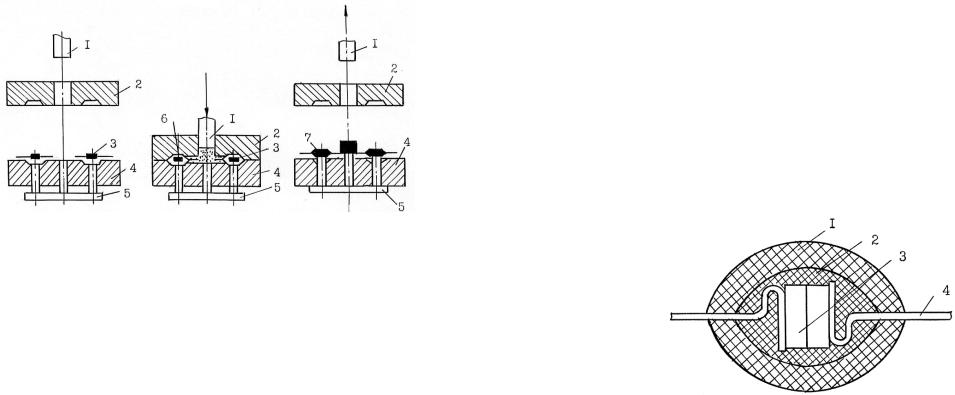
Рис. 7.5. Опрессовка полупроводниковых приборов и интегральных схем: 1 – шток; 2 – верхняя плита; 3 – кристалл с выводами; 4 – нижняя плита; 5 – выталкиватель; 6 – жидкая пластмасса; 7 – готовый прибор
7.6. Герметизация способами обволакивания и окунания
Обволакивание – наиболее простой способ, при котором каплю герметика наносят на вращающуюся сборку. При вращении сборки предотвращается стекание капли неотвержденного компаунда, поэтому корпуса получаются равномерной толщины сферической формы. Для обеспечения механической прочности и герметичности структуры, как правило, наносят несколько слоев герметизирующего материала с предварительным подсушиванием каждого слоя. На рис. 7.6 показан выпрямительный диод, загерметизированный способом обволакивания.
Окунание применяют для дополнительной герметизации полупроводниковой герметизации полупроводниковых приборов и ИС или в качестве основ-
201
ного метода герметизации бескорпусных изделий. Окунание может быть многократным. Процесс нанесения покрытий окунанием не требует сложного оборудования. Ванна с герметизирующим составом помещается на вибратор. Вследствие вибрации происходит изменение вязкости герметизирующего состава. Погружение изделий в состав и извлечение их с определенной скоростью позволяет получить достаточно толстый, не стекающий слой герметизирующего материла, который затем отверждается.
Рис. 7.6. Пластмассовая герметизация полупроводниковых приборов и ИМС обволакиванием: 1, 2 – верхний и защитный слой пластмассы; 3 – кристалл; 4 – выводы
Данный метод находит ограниченное применение. Форма загерметизированных изделий не регламентируется. Примеры изделий, загерметизированных методом окунания, приведены на рис. 7.7.
202
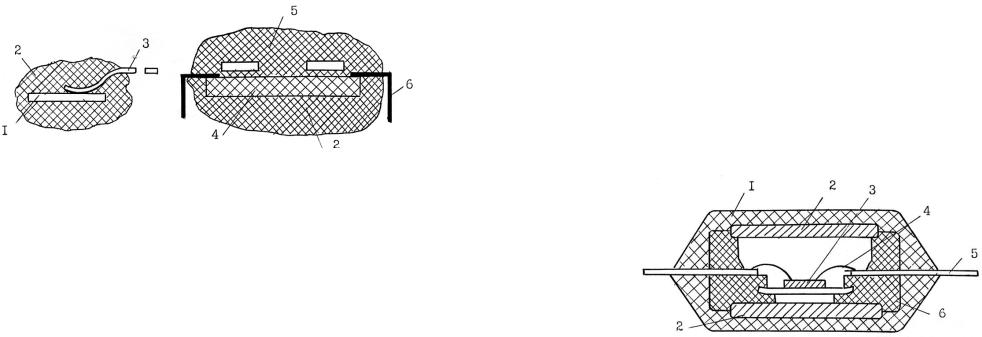
а) |
б) |
Рис. 7.7. Примеры изделий, |
загерметизирован- |
ных методом окунания: а – транзистора; б – микросхемы; 1 – кристалл; 2, 5 – герметизирующие материалы; 3, 6 – выводы; 4 – арматура микросхемы
Рассмотренные методы пластмассовой герметизации обволакиванием и окунанием характеризуются тем, что при них давление не прикладывается и в результате изделия не повреждаются. Жидкая пластмасса заполняет заданный объем, поэтому из нее можно изготовлять изделия любой формы. Для получения качественной герметизации необходимо использовать пластмассы с меньшим ТКЛР, чем ТКЛР кристаллов.
Основными недостатками данных способов являются: трудность нанесения равномерного по толщине покрытия, длительность технологического цикла и сложность механизации процесса.
7.7. Герметизация в полые пластмассовые корпу-
са
Пластмассовый корпус состоит из основания с
203
выводами и крышки. Габариты корпуса, количество и расположение выводов зависят от конструктивных особенностей герметизируемого изделия. Полые пластмассовые корпуса применяют для герметизации МДП-структур, чувствительных к загрязнениям.
Герметизация корпусов (рис. 7.8) осуществляется приклеиванием крышки к основанию.
Рис. 7.8. Герметизация изделий в полых пластмас-
совых корпусах опрессовкой прямых выводов: 1, 6 –
эпоксидная и кремнийорганическая пластмассы; 2 –
крышка,
3 – кристалл; 4, 5 – электродный и ленточный выводы
При этом первоначально кремнийорганической пластмассой 6 опресовывают ленточные выводы 5 корпуса, получив таким образом целую конструкцию. После монтажа кристалла 3 и присоединения электродных выводов 4 к выводам 5 конструкцию сверху и снизу закрывают коваровыми крышками 2 и опресовывают эпоксидной пластмассой 1. Перед нанесением компаунда торцы блоковых сторон основания и край крыш-
204
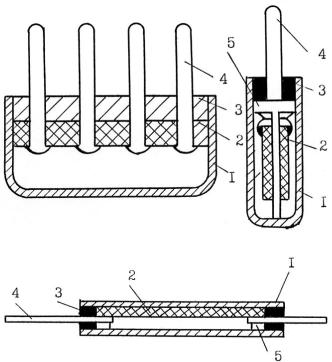
ки по периметру зачищают для получения шероховатой поверхности. После приклеивания крышки к основанию корпуса их плотно зажимают.
а) |
б) |
в)
Рис. 7.9. Примеры герметизации способом капсулирования: а – изделие со штыревыми выводами; б
– односторонний пенальный корпус; в – двусторонний; 1 – капсула; 2 – подложка; 3 – герметизирующий компаунд; 4 – вывод; 5 – прокладка
7.8. Герметизация способом капсулирования
205
Этот способ широко используется для герметизации элементной базы и блоков МЭУ. В зависимости от расположения выводов изделий существуют следующие схемы герметизации
(рис. 7.9).
При герметизации капсулированием изделие помещается в корпус (капсулу) выводами наружу. Свободный торец капсулы и выводы заливаются компаундом. При использовании металлических капсул (чаще всего анодированный алюминий) влагостойкость корпусов существенно возрастает, поэтому под капсулироваением иногда понимается герметизация в металлополимерные корпуса. Для этого вида герметизации изделий микроэлектроники наибольшее распространение получил жидкий компаунд ЭК-16"Б". Применяется также герметизация корпусов таблетками, изготовленными из порошкообразных компаундов. Герметизация порошкообразными компаундами в виде таблеток позволяет автоматизировать процесс сборки и герметизации изделий.
7.9. Контроль герметичности корпусов
Надежность полупроводниковый ИЭТ в процессе работы в аппаратуре и при хранении в значительной степени определяется герметичностью корпуса. Чтобы убедиться, что корпуса обладают требуемой герметичностью, их подвергают контролю.
Методы испытаний должны обладать высо-
206
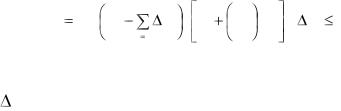
кой чувствительностью и в то же время быть экономичными. Применяемые в полупроводниковом производстве методы и средства контроля разделяют на три основные группы.
К первой группе относят компрессионнотермический (масляный), компрессионный, а также вакуумно-жидкостный методы, при которых утечку газа через неплотности или микроотверстия определяют созданием в контролируемом объекте избыточного давления.
Ко второй группе относятся радиоактивный и масс-спектрометрический методы, при которых непосредственно определяют герметичность контролируемых изделий или помещают их вакуумную камеру, регистрируя изменение предварительно созданного в них разрежения, происходящего из-за проникновения пробного газа.
Третья группа включает в себя бомбовый, ацетоновый и влажностный методы проверки герметичности. Эти методы основаны на изменении (ухудшении) электрических параметров ИЭТ при попадании жидкости в их корпуса. При бомбовом методе готовые полупроводниковые приборы подвергают опрессовке в жидкой среде, которая, проникает внутрь негерметичного корпуса, резко ухудшает их электрические параметры. При ацетоновом методе, являющемся разновидностью бомбового, вместо опрессовки ограничиваются выдержкой приборов в ацетоне при атмосферном давлении. При влажностном методе приборы определенное время выдерживают в условиях повышенной влажности. Влага, приникая сквозь неплотности корпусов (если они имеются), ухудшает параметры приборов.
Одним из вариантов ускоренных испытаний ка-
чества герметизации металлопленочных резисторов с помощью эпоксидных смол является воздействие на изделия электрического напряжения. Согласно этому методу на поверхность герметизирующего покрытия из эпоксидной смолы наносится слой металла и между ним и резистивным слоем включается напряжением 100 В. Резисторы на 10 суток помещают в камеру с влажностью 95 – 98 % и температурой 25 – 75 °С. После окончания испытаний определяется изменение сопротивления каждого резистора, обусловленного электрохимической коррозией резистивного слоя. Испытания проводятся с большой партией резисторов, а критерием оценки служит показатель, вычисляемый по формуле
H 100 N |
R / N |
10 F 2 , R 1 , |
|
|
N |
|
|
|
i |
N |
i |
|
i 1 |
|
где N – число испытываемых резисторов; F – число резисторов с отключением сопротивления Ri > 0,4 %. При этом такие резисторы призна-
ются непригодным.
Наиболее чувствительным является радиоактивный метод. Приборы, подлежащие испытанию, герметизируются в атмосфере сжатого радиоактивного газа (например, Kr 85). При испытании с помощью счетчиков регистрируется интенсивность гамма-излучения газа, вытекающего из корпуса. Этот метод используется только в экстремальном производстве (отработка конструкции корпуса или технологии герметизации).
Масс-спектрометрический метод основан на обнаружении гелиевым течеискателем гелия, предварительно введенного в корпус прибора. Технология испытаний заключается в следую-
207
щем: герметизированный корпус помещается в камере, в которую вводится газ под требуемым давлением. Если в корпусе или соединительном шве имеются неплотности, гелий проникает внутрь корпуса. После этого исследуемый корпус помещается в другую камеру, соединенную с массспектрографом, который фиксирует обратную утечку гелия из корпуса в камеру.
Контроль качества герметизации может быть и разрушающим. При разрушающем контроле изделие после испытаний вскрывают и проверяют визуально.
Кроме исследований на отсутствие неплотностей и на воздействие влаги, влияние которых на параметры изделий наиболее сильно, существуют и другие методы испытаний. К ним относятся следующие испытания: в соляном тумане, при низкой и высокой температуре, при пониженном атмосферном давлении, на устойчивость к солнечной радиации и термоударам, к воздействию песка и пыли.
Качество герметизации проверяют непосредственно после изготовления ИЭТ или после различных воздействий на них. Технология контроля изделий на герметичность оговаривается специальными инструкциями.
Следует отметить, что наиболее простым методом контроля герметичности корпусов полупроводниковых ИЭТ является компрессионно-термический метод. Он основан на повышении давления газа в замкнутом объеме корпуса, погруженного в нагретое масло, и регистрации пузырьков газа, выходящих через неплотности в нем. При компрессионном методе регистрируют также пузырьки газа, выходящие через неплотности ножек (спай стекла с металлом), погруженных в жидкость, при давлении на их конструктивные элементы, равном 1,1 – 1,3 МПа.
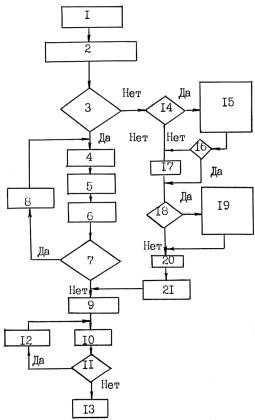
8. Поверхностный монтаж компонентов
8.1. Особенности поверхностного монтажа
Термин «технология поверхностного монтажа» является общим обозначением нового направления в области электроники, включающего и технику корпусирования компонентов. Для поверхностного монтажа используются компоненты, в основном, намного меньших размеров, чем традиционные эквиваленты, монтируемые в отверстия. Такие компоненты непосредственно закрепляются на верхней (или нижней) стороне коммутационной платы (КП) при совмещении их выводов или внешних контактов с контактными площадками.
Технология поверхностного монтажа способствовала появлению множества новых портативных потребительских изделий: видеокамеры высокого разрешения, переносимые телефоны, калькуляторы, малогабаритные компьютеры и т. д.
Этот метод сборки компонентов характеризуется следующими особенностями: более высокой плотностью монтажа на единицу площади коммутационной платы, что дает снижение массогабаритных показателей при том же уровне функциональных возможностей; увеличение числа выводов корпуса
расположение и реализации монтажноментов плат. Следует технологического составлять от 0,025 – имеют ширину и будущем потредорожек и
.
в производство РЭА монтажа.
, с одной или с двух изготовителей, используюодносторонним мон-
монтаж навесных комповерхность платы, и в быть три подхода: с набор компонентов обоих типов, а с дру- ; компоненты обоих
и, следовательно, повышение функциональных возможностей |
Третий – смешанно-разнесенный, когда с одной |
||||
на единицу поверхности коммутационной платы. |
стороны платы монтируются только компоненты для |
||||
Наряду с преимуществами конструкции, разработанной |
ТПМК, а с другой – только в сквозные отверстия. |
|
|||
на базе технологии поверхностного монтажа компонентов |
Технология |
поверхностного |
монтажа позволяет |
||
(ТПМК), существует сложный комплекс проблем, возникаю- |
широко использовать гибкие автоматизированные сбо- |
||||
щих на этапе производства. Основными из них являются: со- |
рочно-монтажные линии, достоинство которых – прежде |
||||
гласование по ТКР платы и монтируемых на ней навесных |
всего, |
в оперативной переналадке |
(не более |
чем за |
|
компонентов; обеспечение теплоотвода при повышенной рас- |
5 мин.) технологического процесса на любой вариант его |
||||
сеиваемой мощности; оптимизация геометрии элементов ком- |
реализации из трех (рис. 8.1). |
|
|
||
мутации с учетом специфики ТПМК, а также свойств, приме- |
Рис. 8.1. Алгоритм реализации технологического |
||||
няемых припойных, защитных и клеевых материалов. |
процесса сборки и монтажа навесных компонентов на |
||||
В процессе проектирования КП важно правильно вы- |
поверхность платы с учетом первых двух его вариантов: |
||||
|
|
|
|
|
|
|
1 |
– |
очистка |
КП; |
|
208 |
210 |
|
209 |
|
|
2 – входной контроль навесных компонентов; 3 – все ли компоненты монтируются на поверхность; 4 – нанесение припойной пасты; 5 – установка навесных компонентов; 6 – пайка оп-
лавлением |
|
дозированного |
припоя; |
||
7 |
– |
будет |
ли |
монтаж |
двухсторонним; |
8 – переворот КП; 9 – очистка платы после пайки; 10 – контроль качества смонтированной платы; 11 – имеются ли дефекты на смонтированной плате; 12 – регенерация платы (ремонт); 13 – приемосдаточные испытания и последующие операции; 14 – будет ли вестись монтаж на верхнюю поверхность; 15 – нанесение припойной пасты, установка компонентов, пайка расплавлением дозированного припоя; 16 – разнесен ли смешанный монтаж; 17 – установка навесных компонентов в отверстия платы; 18 – будет ли вестись монтаж на нижнюю поверхность платы; 19 – переворот КП, нанесение клея, установка компонентов для ТПМК, отверждение клея; 20 – установка компонентов в отверстия; 21 – пайка волной припоя
Многие методы микроконтактирования в ТПМК для обеспечения, в первую очередь, электрического соединения навесных компонентов с контактными площадками реализуются с использованием различных способов пайки. Для пайки на коммутационных платах компонентов в ТПМК обычно применяется расплавление дозированного припоя. Для обеспечения качественных микросоединений необходимо тщательное изучение физико-химических процессов, протекающих при пайке. В производстве обычно выбирают наиболее приемлемые методы и режимы пайки, а также соответствующее оборудование после предварительных экспериментальных исследований. Эксперименты являются неотъемлемой частью процесса совершенствование конструкции изделия с учетом особенностей пайки.
Для поверхностного монтажа компонентов на КП применяются следующие методы: пайка волной припоя, пайка расплавлением дозированного припоя в парогазовой среде при нагреве излучением, пайка методом контактного нагрева и с использованием электропроводящих клеев.
В настоящее время метод пайки волной припоя оказался эффективным, в основном, при реализации смешанных вариантов сборки и монтажа изделий. Пайка расплавлением дозированного припоя в парогазовой фазе уступает место пайке с инфракрасным нагревом, лазерная же пайка пока не получила распространения.
Реализация ТПМК с применением эластичных электропроводящих клеев дает некоторое преимущество в сравнении с методами, использующими припои. Так, клеи лучше выдерживают механические напряжения, более пластичны. Основной недостаток данного метода – недостаточная прочность спая компонента с контактной площадкой платы.
8.2. Пайка волной припоя (ПВП)
Этот метод в настоящее время достаточно хорошо освоен в ТПМК. На практике было установлено, что качество паяных соединений в значительной степени определяется геометрическими размерами волны, скоростью и другими ее характеристиками. Следует иметь ввиду, что по мере увеличения плотности монтажа возрастает и вероятность возникновения перемычек между проводниками при пайке, так называемое шунтирование элементов. Для предотвращения этого сразу после ПВП, когда припой еще находится в расплавленном состоянии, применяют специальный дешунтирующий «нож» (рис. 8.2), направляющий струю горячего воздуха (или другого газа) в месте пайки. Такой «нож» (а иногда и несколько) служит также и для очистки после пайки.
212
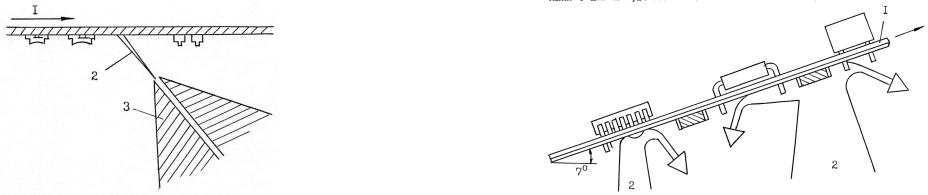
Рис. 8.2. Специальный дешунтирующий нож, используемый для очистки смонтированных плат от излишков припоя после ПВП: 1 – направление движения КП; 2 – струя горячего воздуха; 3 – дешунтирующий нож
В настоящее время разработано оборудование и приспособления (в частности, сопла) для ПВП, которые позволяют получать управляемую высокоскоростную (90 см/с) волну припоя. Пайка на таком оборудовании не оставляет перемычек между проводниками, расположенными с шагом 0,15 мм и более.
Первая волна формируется турбулентной и узкой, она исходит из сопла под большим давлением (рис. 8.3). На этом этапе обеспечивается полное смачивание и оплавление всех контактных точек на плате. Турбулентность и высокое давление потока припоя способствуют получению качественных соединений, исключая формирование полостей с лазообразными продуктами разложения флюса. Однако, турбулентная волна все же образует перемычки припоя, которые разрушаются второй, более пологой, с меньшей скоростью истечения. Вторая волна удаляет излишки припоя и устраняет перемычки, а также завершает формирование галтелей.
Рис. 8.3. Схематическое представление процесса пайки двойной волной припоя
Каждая волна формируется с помощью специальной щели и магнитного поля, направленного вертикально относительно поверхности припоя, поэтому амплитуда волны, а следовательно, и высота пайки регулируются автоматически. Наклон конвейерной ленты с платами под углом 7 – 10° обеспечивает лучшее смачивание припоем паяемых участков. Рекомендуемый температурновременной режим всего процесса микроконтактирования представлен на рис. 8.4.
Пайку двойной волной припоя наиболее целесообразно применять для одного типа КП: с традиционными компонентами на лицевой стороне и монтируемыми на поверхность простыми компонентами (чипами и транзисторами) на обратной. Некоторые компоненты для ТПМ (даже пассивные) могут быть повреждены при погружении в припой во время пайки.