
3565
.pdf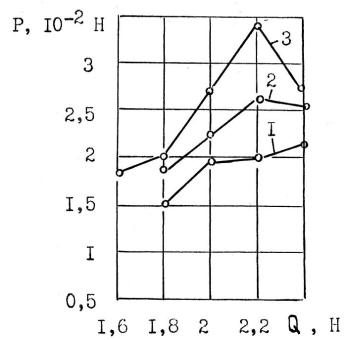
Рис. 4.24. Влияние усилия сжатия Q при термокомпрессионной сварке на прочность микросоединений алюминий - золото в зависимости от температуры: 1 – 300 °С; 2 – 325 °С; 3 – 350 °С
Применение ударной термокомпрессионной сварки позволяет повысить стабильность свойств соединений по сравнению с ультразвуковой сваркой и снизить брак в 2,8 раза.
Процесс групповой термокомпрессии падающим пуансоном обеспечивает хорошую воспроизводимость прочности соединений при сварке алюминиевых лепестковых выводов сечением 0,03 – 0,3 мм с коваровой золоченой рамкой толщиной 0,25 мм. Оптимальный режим сварки характеризуется следующими параметрами: температура нагрева рабочего стола 300 °С масса пуансона 7,4 кг; высота подъема пуансона относительно стола 0,6 мм.
4.4.2. Влияние технологических режимов на прочность микросоединений при ультразвуковой сварке
Основными параметрами микросварки являются: мощность ультразвукового преобразователя, амплитуда колебаний сварочного инструмента, усилие сжатия и время микросварки. С учетом малых толщин и размеров соединяемых элементов к основным параметрам следует отнести частоту колебаний микросварочного инструмента. При этом для конкретной сварочной установки частота является постоянной величиной, изменяемой только в узких пределах. При этом следует помнить, что одним из наиболее важных параметров является электрическая мощность, подводимая к преобразователю. Электрическая мощность определяет мощность, поглощаемую в зоне сварки (акустическая мощность), от которой зависит качество микросварного соединения. Акустическая мощность, передаваемая в зону сварки, составляет не более 20 – 30 % электрической мощности ультразвуковой колебательной системы.
Амплитуда колебаний в период микросварки дает большее представление об акустической мощности, чем электрическая мощность преобразователя. Поэтому увеличение амплитуды колебаний ведет к повышению акустической мощности в зоне сварки. Следует отметить, что амплитуда колебаний имеет оптимальное значение для каждого свариваемого материала определенной толщины.
На прочность микросоединений при ультразвуковой микросварке существенное влияние оказывает усилие сжатия, которое обусловливает возникновение тангенциальных напряжений в месте сварки. Оптимальное усилие сжатия увеличивается с увеличением толщины свариваемых элементов и размера сварного соединения и существенно зависит от подводимой мощности. Чем больше усилие сжатия, тем больше должна быть ампли-
120 |
121 |
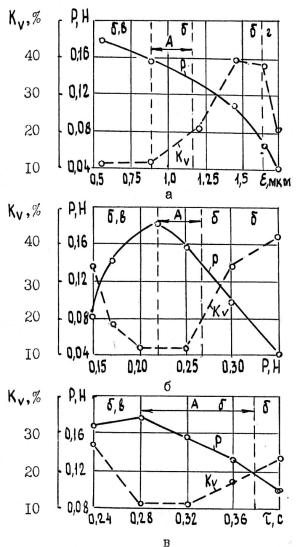
туда колебаний инструмента и необходимая электрическая мощность. Если усилие сжатия не обеспечивает необходимого сцепления между инструментом и верхней свариваемой деталью, то происходит проскальзывание инструмента по детали и сварного соединения не образуется. Усилие сжатия должно увеличиваться пропорционально амплитуде колебаний инструмента при соответствующем увеличении мощности колебательной системы.
Длительность сварки увеличивается с толщиной материала, твердостью и уменьшением электрической мощности. Существует экстремальный характер зависимости прочности микросварных соединений от времени сварки. Уменьшение прочности при длительном времени микросварки объясняется в большинстве случаев увеличением общей деформации и появлением трещин в зоне микросварки.
Частота колебаний ультразвуковой микро сварочной установки выбирается с учетом физико-механических свойств и размеров соединяемых элементов. Соединение элементов полупроводниковых приборов и ИС целесообразно проводить на частотах свыше 20 кГц. Зависимость энергии ультразвуковых колебаний от амплитуды и частоты определяется по формуле
ε = ξ·f·η,
где ξ, f, η- соответственно амплитуда, частота и время микросварки. Из этого выражения видно, что сохранение необходимого для сварки уровня мощности можно компенсировать соответствующим повышением частоты или уменьшением амплитуды.
На рис. 4.25 показано влияние основных параметров ультразвуковой сварки (длительности η, усилия сжатия Q амплитуды колебаний сварочного инструмента εсв) на прочность Р и коэффициент вариации прочности Kv сварных соединений алюминиевой проволоки. А995Д диаметром 0,04 мм с алюминиевыми пленками толщиной 1 мкм, напыленными на окисленный кремний. Сварка проводилась на частоте 60 кГц инструментом с рабочим торцом шириной 90 мкм и поперечной канавкой.
Рис. 4.25. Зависимость прочности Р при испытании на отрыв и коэффициента вариации прочности Kv от параметров ультразвуковой сварки при соединении алюминиевой проволоки диаметром 40 мкм с пленкой алюминия δ = 1 мкм на окисленном кремнии. Режимы сварки: а –
122 |
123 |
мощность УЗ колебаний NЭ = 75·10–3 Вт; Р = 25·10–2 Н; б – NЭ = 75·10–3 Вт; η = 0,32 с; в – Р = 25·10–2 Н; η = 0,32 с
Контроль прочности соединений осуществлялся на отрыв проволоки под углом 90° к подложке. При испытаниях разрушение соединений происходит по проволоке вдали от зоны сварки (а), в месте наибольшей деформации проволоки (б), с отслаиванием проволоки от пленки (в) и с отрывом части соединения (г) принимая за оптимальные соединения со средней прочностью не ниже 0,12 Н (50 % прочности проволоки) при коэффициенте вариации Kv не более 20 % и при условии разрушения соединений только по виду (б), то из графиков можно установить зоны оптимальных режимов (А). Испытания данных соединений показали, что наиболее критичными параметрами для ультразвуковой сварки являются амплитуда колебаний и контактное усилие, а наименее критичным – длительность процесса.
Время микросварки и амплитуда колебаний инструмента (мощность генератора) подбираются, исходя из получения максимальной прочности соединений. При этом при испытаниях полученного соединения на механическую прочность разрушение соединений должно происходить по проволоке.
4.4.3. Сварка платиновой проволоки с пленкой платины
При монтаже внутренних соединений в специальных изделиях микроэлектроники используется платиновая проволока диаметром 0,03 – 0,05 мм. Уникальные физико-химические свойства – высокая коррозионная стойкость и каталитическая активность, стабильные электрические и термоэлектрические характеристики, высокие износоустойчивость и механические свойства при повышенных температурах – определяют традиционное применение платиновых металлов при изготовлении приборов и изделий специального назначения. Стабильность механических и электрических параметров обеспечиваются присоединением платиновой проволоки к контактным пло-
щадкам из платины. Так как платина имеет высокую температуру плавления, то оптимальным способом образования контактных микросоединений Рt – Pt является импульсная сварка «расщепленным» электродом.
Для получения максимальной механической прочности сварного соединения при импульсной сварке необходимо создать условия для обеспечения основных параметров процесса: сварочного напряжения, тока в электродах, усилия сжатия проволоки к пленочной металлизации и длительности сварочного импульса. Выбор оптимальных режимов монтажа микросоединений проводился на установке УСМ-1C с использованием сварочного электрода с рабочей частью из вольфрама. Деформация привариваемой проволоки (сварного контакта) определялась при помощи микроскопа МИМ-7 и фотографий сварных микросоединений, а механическая прочность контактов оценивалась на отрыв проволоки под углом 90° к подложке на установке УКПМ-1. Для исследования влияния параметров процесса сварки на механическую прочность микросоединений применялась платиновая проволока диаметром 0,05 мм, отожженная при различных температурах. Проволока присоединялась к платиновой пленке, которая напылялась на подложку из кварца на вакуумной установке с электронно-лучевым испарителем. Давление остаточной атмосферы в камере вакуумной установки при напылении пленок составляло 133·10–4 Па. Кварцевые пластинки при напылении подогревались до температуры 800 °С. После напыления пленок в течение 30 мин проводили отжиг образцов при той же температуре. Толщина пленок платины составляла 3 мкм. Для исследований качества микросоединений Pt – Рt на каждом режиме получали по 20 контактных соединений.
Зависимость прочности Р микросоединений от температуры отжига проволоки представлена на рис. 4.26. Анализ контактов при определении прочности микросо-
124 |
125 |
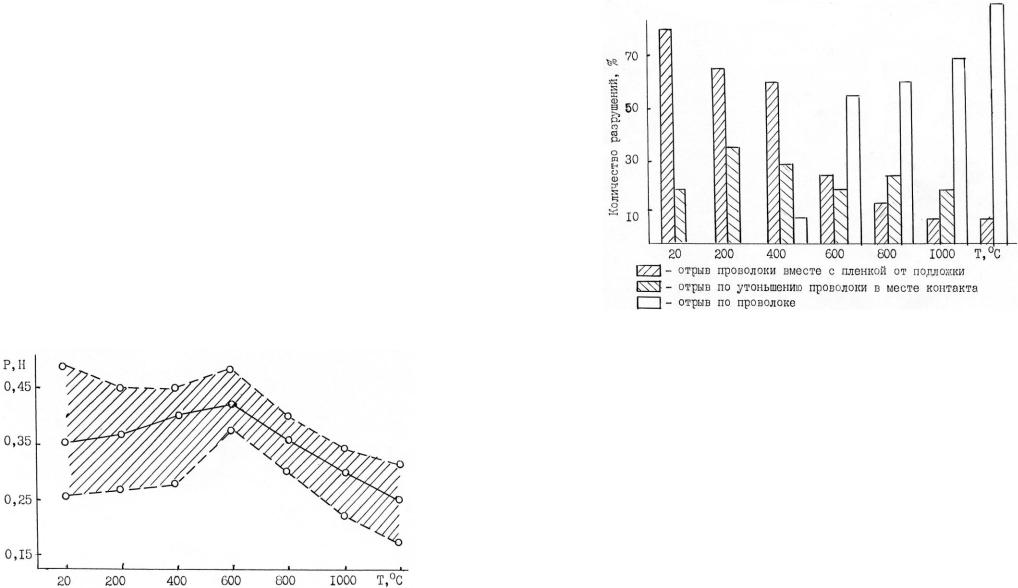
единений на отрыв выявил следующие виды разрушений (рис. 4.27): отрыв платиновой проволоки вместе с пленкой от подложки; отрыв по утоньшению проволоки в месте контакта; отрыв по проволоке.
Характер разрушений связан с физико-механическими свойствами платиновой проволоки. Как видно на рис. 4.26, максимальная прочность микросварных соединений наблюдается при сварке с использованием платиновой проволоки, отожженной при температуре около 600 °С, Неотожженная проволока и проволока с температурой отжига 200 и 400 °С достаточно жесткая, что приводит при сварке к нарушению адгезии платиновой пленки. Основным видом разрушений микросварных контактов, разваренных такой проволокой, является отрыв проволоки вместе с пленкой от подложки. При увеличении температуры отжига платиновой проволоки до 1000 и 1200 °С прочность микросоединений снижается, т. к. уменьшается механическая прочность самой проволоки. Разрушение микросварных соединений происходит по проволоке.
Рис. 4.26. Зависимость прочности Р микросоединений платиновая проволока – пленка платины от температуры отжига проволоки
Рис. 4.27. Гистограмма распределения видов разрушений микросоединений платиновая проволока – пленка платины в зависимости от температуры отжига проволоки
Для установления влияния давления сварочного электрода и напряжения, подаваемого на электрод (рис. 4.28, 4.29), на каждом режиме разваривалось по 20 образцов. Время сварки во всех случаях составляло 0,1 с. Наибольшая механическая прочность микросварных соединений Pt – Pt достигается при усилии сжатия электрода 16 МПа и напряжения 500 мВ. Дальнейшее увеличение усилия сжатия сварочного электрода нарушает адгезию платиновой пленки с подложкой. Повышение подачи напряжения на сварочный электрод приводит к прожогу металлизации и увеличению омического сопротивления контактов.
126 |
127 |
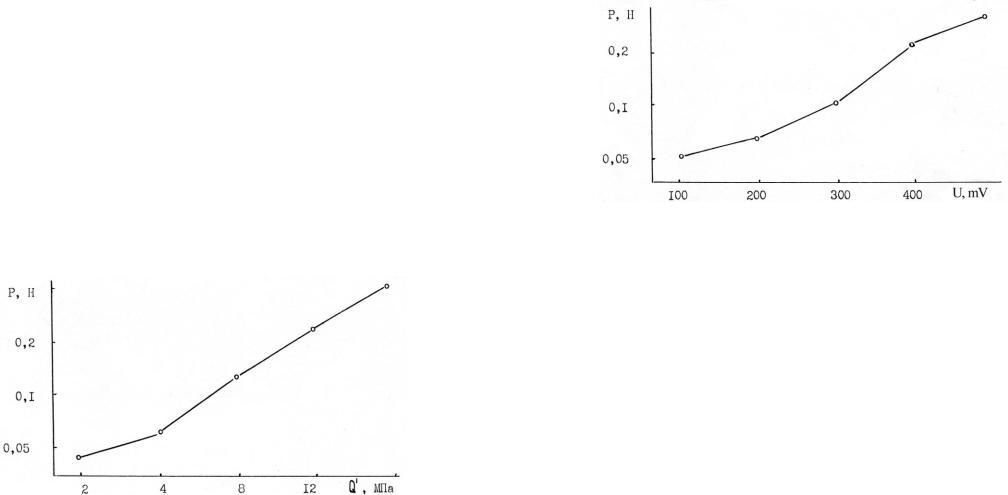
4.5. Номограмма для выбора режимов термокомпрессионной сварки и оценки качества микросоединений
В технологии производства ИЭТ для оптимизации режимов микросварки широко применяются методы планирования экспериментов и экспериментальный. При экспериментальном методе изменяется какой-либо параметр, а остальные, выбранные интуитивно, остаются неизменными. По результатам экспериментальных данных строятся номограммы, по которым осуществляется выбор оптимальных режимов монтажа микросоединений. Однако применение существующих номограмм на практике не дает полного анализа качества сформированных сварных соединений, т.к. не учитывает деформацию привариваемой проволоки и характер разрушения микросоединений при контроле их прочности.
Рис. 4.28. Влияние давления на сварочный электрод Q´, при сварке на прочность микросоединений проволока – пленка (при напряжении на электроде 460 мВ)
Для устранения вышеуказанных недостатков разработана номограмма процесса монтажа микросварных соединений, ко-
128
торая позволяет выбирать не только оптимальные режимы сварки, но и оценивать качество микросоединений, полученных на данных режимах.
Рис. 4.29. Зависимость прочности Ротр. микросоединений проволока – пленка от напряжения, подаваемого на сварочный электрод (при давлении на сварочный электрод 12 МПа)
На рис. 4.30 представлена номограмма процесса ТКС алюминиевой проволоки диаметром 0,027 мм к ва- куумно-осажденным пленкам алюминия толщиной 1,0 – 1,2 мкм на кристаллах и гальваническим пленкам золота толщиной 4 мкм на траверсах корпусов ИЭТ.
Испытания на прочность проводились путем разрушения микросоединений под углом 90° к поверхности подложки. При этом наблюдались следующие виды разрушений: обрыв по утоньшению проволоки в месте сварки, частичное или полное отслаивание проволоки от пленок. Определялись не только усилия отрыва проволоки от пленок алюминия и золота, но и деформация проволоки при сварке.
При построении номограммы для выбора режимов ТКС, удобной в практическом применении, установлена зависимость качества микросоединений от степени де-
129
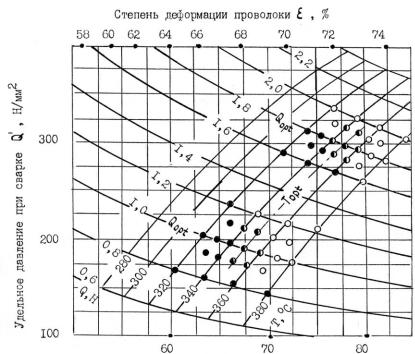
формации проволоки, сжимающего усилия при сварке, и температуры.
Рис. 4.30. Номограмма для выбора режимов ТКС и оценки качества микросоединений: – отслоение;
– обрыв проволоки в зоне сварки;
– смешанный характер разрушения
Степень деформации проволоки ε заданного диаметра d оценивалась по ширине сварной тючки B по известной методике. Удельное давление инструмента Q´ в конце процесса деформирования (отношение усилия сжатия Q к площади контактирования SК) при длине торца инструмента L определяется по формуле
Q´ = Q/SК = Q/BL
По оси абсцисс откладывались значения B от 50 до 85 мкм и вычисленные деформации ε (соответственно от 57 до 75 %). Задаваясь усилиями Q от 0,6 до 2,2 Н с интервалом 0,2 Н и определив деформацию B, на ось ординат наносились
130
полученные значения удельных давлений Q´. Температура ТКС изменялась в интервале от 280 до 380 °С. Длина торца сварочного инструмента L во всех случаях составляла 80 мкм.
Установлено, что наиболее критичным параметром при термокомпрессионной микросварке является температура, а изменение давления при постоянной температуре допустимо в более широких пределах. Следовательно, эти факторы необходимо учитывать при разработке оборудования для ТКС проволочных выводов в полупроводниковых приборах и ИС.
Разработанная номограмма процесса монтажа микро соединений ИЭТ позволяет выбирать не только оптимальные режимы сборочных процессов, но и анализировать качество микросоединений в широком интервале исследуемых параметров.
131

5. Сборка силовых полупроводниковых приборов
Возросший уровень цен на энергоносители и резкое увеличение энергоемкости внутреннего валового продукта активизировали разработку и производство изделий силовой энергосберегающей бытовой и промышленной аппаратуры.
Силовые полупроводниковые приборы в составе модулей обеспечивают коммутацию токов свыше 1000 А и напряжений до 5,5 кВ, при этом размеры чипов достигают площади 2,6 см2
(16 мм 16 мм).
Все это предъявляет повышенные требования к технологии производства, особенно к монтажносборочным операциям в силовых полупроводниковых приборах (СПП).
Известно, что надежность полупроводниковых ИЭТ в значительной степени зависит от качества контактных соединений. Одной из наиболее распространенных причин отказов изделий радиоэлектронной аппаратуры является нарушение соединений кристалла с корпусом и проволоки с контактными площадками кристалла и корпуса. В тоже время сборочные операции являются наиболее трудоемкими. Например, из общей стоимости изготовления интегральных схем на монтажносборочные работы приходится около 65 % затрат. Поэтому вопросы совершенствования технологии сборки остаются в центре внимания разработчиков и изготовителей полупроводниковых изделий микроэлектроники.
Качество и надежность любого изделия закладываются при конструировании, обеспечиваются технологическим процессом изготовления и должны сохраняться при эксплуатации.
Одним из методов контроля правильности выбора конструкции или технологического процесса изготовления полупроводниковых изделий является определение теплового сопротивления приборов. Перегрев кристалла изменяет электрические характеристики прибора и снижает его надежность.
132
Тепловой расчет температуры перегрева кристаллов проводят на этапе проектирования изделий. Требования к тепловому режиму необходимо учитывать при выборе материалов корпуса и подложки, а также конструкции изделий.
При решении вопроса о надежности соединений наряду с выбором оптимальных способов и режимов присоединения кристалла к основанию корпуса и внутренних выводов к кристаллу и траверсам корпуса, необходимо учитывать качество металлизации контактных площадок, присоединяемой проволоки, материала и конструкции сварочного инструмента.
5.1. Покрытия контактных поверхностей кристаллов и корпусов полупроводниковых ИЭТ
К покрытиям контактных поверхностей кристаллов и корпусов для пайки ИЭТ предъявляются следующие требования: они должны обеспечивать хорошую паяемость (не менее 95 % площади кристалла), а также сохранять способность к пайке при заданном сроке хранения, обеспечивать антикоррозионную защиту, не подвергаться иглообразованию при хранении и разрушению при различных температурах.
В данной главе проанализированы покрытия, которые наиболее широко применяются на контактных поверхностях кристаллов и корпусов для пайки ИЭТ и могут быть использованы в производстве СПП.
Золотое покрытие. Гальванические покрытия ИЭТ из чистого золота (99,9 %) обладают комплексом положительных свойств: высокой
133
электропроводностью, низким контактным сопротивлением, хорошей смачиваемостью припоями, высокой коррозионной стойкостью, способностью к диффузионной сварке и др. Однако золотые покрытия имеют существенные недостатки: значительную пористость в покрытиях (особенно в тонких слоях); ослабление соединений при пайке вследствие растворения покрытий в припое; диффузию подслоя меди в покрытие. С целью устранения этих недостатков и снижения себестоимости производства ИЭТ золотые покрытия заменяются сплавами, имеющими свойства золота.
В электронной промышленности используются следующие сплавы на основе золота: золото – никель, золото – кобальт, золото – серебро, золото – медь, золото – кадмий. Из данных сплавов наиболее подробно исследованы сплавы золото – никель и золото – кобальт.
Наиболее перспективным сплавом является золото – кадмий, который имеет высокую износостойкость, паяемость, низкое контактное сопротивление, незначительно изменяется при старении. Наиболее важным преимуществом данного сплава по сравнению с другими является его способность выдерживать повышенные температуры в течение 1000 ч без изменения контактного сопротивления.
Адгезионная прочность золотых покрытий с никель – бор основой зависит от термообработки. При химической металлизации золотом ИЭТ с нанесенным покрытием из сплава никель – бор для увеличения адгезии золота с основой целесообразно прово-
134
дить термообработку при температуре 500 ± 20
°С.
Для улучшения паяемости корпуса ИС покрывают предварительно пленками химического или электрохимического никеля, а затем золотом (соответственно 6 – 9 и 2 – 6 км).
Увеличение среднего размера зерна, количества пор и концентрации примесей в никелевом покрытии приводят к снижению смачиваемости золотого покрытия припоем при пайке кристаллов и уменьшению площади физического контакта при ультразвуковой сварке проволочных выводов.
В связи с дефицитом драгметаллов проводятся мероприятия, направленные на сокращение использования золота, но при этом обязательным условием является сохранение качества и надежности приборов. Работы в направлении экономии золота можно разделить на три группы:
–минимизацию толщины гальванических покрытий путем совершенствования электролиза;
–применение способов локального или локально дифференцированного покрытия, позволяющих получать необходимую толщину золота только на функциональных участках корпусов;
–замену золотого покрытия другими недефицитными металлами.
Первый метод позволяет получить лишь незначительный эффект, так как толщина золотого покрытия уже минимизирована в большей части
135
конструкций ИЭТ. Второй метод также широко реализуется во многих приборах, поэтому основное внимание исследователей должно быть направлено на полную замену золота в конструкциях приборов. Тем более, что приборы с золотым покрытием обладают пониженной радиационной стойкостью.
Оловянное покрытие. В производстве некоторых типов полупроводниковых ИЭТ применяются оловянные покрытия, так как олово обладает химической устойчивостью и инертностью, а также высокой способностью к пайке. В то же время следует отметить, что при воздействии низкой температуры возможно превращение β-олова, кристаллизующегося в тетрагональной системе и имеющего плотность 7,29 г/см3,
вα-олово, имеющее кубическую решетку с плотностью 5,77 г/см3. Данное превращение сопровождается изменением объема и переходом контактного металла
впорошкообразное состояние, которое называют «оловянной чумой». Кроме того, при хранении деталей и изделий, покрытых оловом, способность к пайке существенно снижается, что вызывает определенные трудности при сборке изделий на поточных линиях. Особо важно отметить, что даже белая модификация олова после двухлетнего хранения на 60 % теряет прочность спая. Покрытия из чистого олова обладают склонностью к образованию на поверхности нитевидных кристаллов (усов), что ограничивает их применение для сборки полупроводниковых ИЭТ.
Сцелью устранения недостатков, присущих оловянным покрытиям, проводят электрохимическое легирование олова другими металлами (никелем, вис-
мутом, цинком, кобальтом, сурьмой и др.). Эти сплавы лишены недостатков, которыми обладает чистое олово, а кроме того, имеют определенные преимущества: сохраняется паяемость, повышенная коррозионная стойкость и другие специальные свойства.
Олово и его сплавы осаждаются в виде блестящих электролитических покрытий только в том случае, если в раствор при электролизе вводят специальные поверхностно-активные или коллоидные добавки, называемые блескообразующими. Органические соединения, добавляемые в электролиты, повышают катодную поляризацию, сближают потенциалы осаждаемых металлов, улучшают мелкокристалличность покрытия, его паяемость, увеличивают блеск и рассеивающую способность, повышают качество покрытия и стабильность работы электролита.
Покрытие сплавом олово – свинец. Сплавы олово – свинец, в отличие от чистого олова, сохраняют способность к пайке более длительное время. Данные покрытия не образуют при хранении нитевидных кристаллов, наблюдаемых на оловянных покрытиях.
Покрытия сплавом олово – свинец получают электрохимическим или горячим способом. Сплавы, осаждаемые электрохимическим способом, характеризуются химической неустойчивостью кристаллитов свинца и олова в неоплавленных покрытиях в течение длительного времени. Поэтому, если возможно по конструктивным со-
136
ображениям, то применяют горячий способ нанесения покрытия (из расплавленного припоя) вместо электрохимического. Горячий способ является экономически более выгодным и, кроме этого, обеспечивает самое высокое качество паяных соединений.
Гальваническое покрытие сплавом олово – свинец (на печатных платах из фольгированного диэлектрика) имеет значительную шероховатость и пористость. В поверхностном слое такого покрытия содержится преимущественно олово. Однако при оплавлении покрытия ИК излучением с использованием флюса ФКТ происходит его уплотнение и уменьшение шероховатости, при этом состав поверхностного слоя выравнивается и приближается к эвтектическому (63 % олова и 37 % свинца). Следует отметить, что после оплавления с использованием флюса ФКТ изменяется профиль покрытия, оно стягивается к середине печатных элементов и становится тоньше на краях. А использование при оплавлении флюса ВФ130 приводит к отсутствию стягивания покрытия к середине печатных элементов, и покрытие имеет одинаковую толщину на всей площади контактной площадки.
Одной из основных причин плохой паяемости покрытия олово – свинец является наличие более 0,1 г/л примеси меди в электролите. Для устранения данного дефекта необходимо рассмотреть электролит при плотности тока 0,3 – 0,4 А/дм2.
Олово – висмутовое покрытие. Покрытие спла-
вом олово – висмут характеризуется хорошей адгезией к меди и ее сплавам, легкой паяемостью и сохра-
нением способности к пайке в течение длительного времени. При электролизе возможно получение покрытия темно-серого цвета, которое характеризуется плохой паяемостью. Основной причиной данного дефекта, как и в покрытии олово – свинец, является наличие примесей меди в электролите.
Добавка висмута (0,3 – 3,8 %) предотвращает переход белой модификации олова в серую, существенно уменьшает образование нитевидных кристаллов на поверхности покрытия. Однако получение сплава олово – висмут сопряжено с определенными трудностями, связанными с нестабильностью электролита, так как соли висмута, входящие в состав электролита, подвергаются гидролизу. Результатом этого является разложение электролита, что требует частой его смены. Следует также отметить, что соли висмута являются дефицитными, а металлический висмут токсичен. Кроме того, такие покрытия теряют паяемость после 12 мес. хранения и не паяются с применением канифольных флюсов.
Серебряное покрытие. В полупроводнико-
вой микроэлектронике серебрение используется для создания функциональных покрытий с высокой электропроводностью и стабильной величиной переходного сопротивления в местах контактов. В некоторых изделиях серебро используется в качестве конечного покрытия коллекторной стороны кристалла. В этом случае осуществляется напыление пленки на пластины с кри-