
3565
.pdf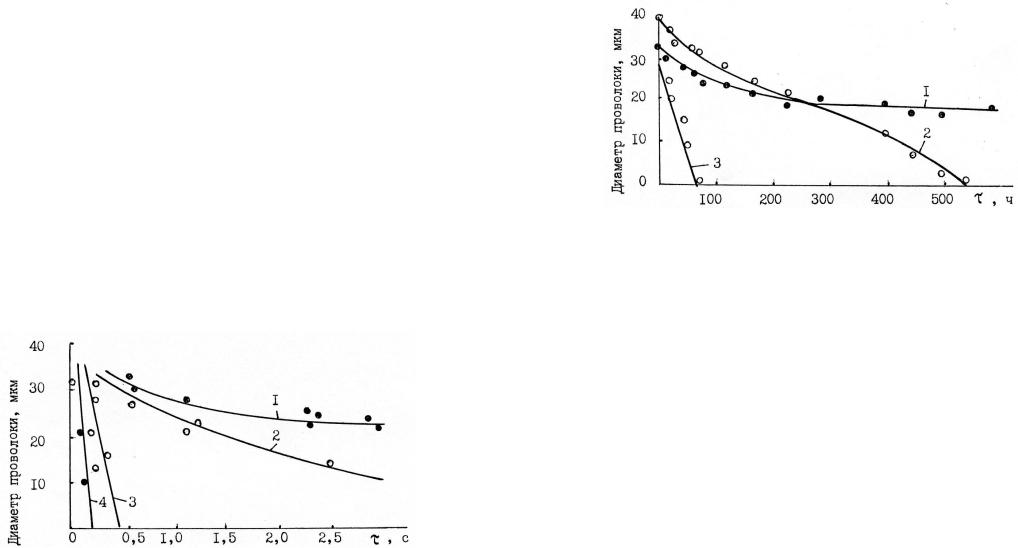
валось по шлифам поперечных сечений с точностью до 1 мкм. Установлена зависимость растворения золотой проволо-
ки при низкотемпературной пайке выводов ИС на печатные платы от температуры и времени пайки. Из рис. 4.14 видно, чем меньше температура расплава, тем меньше растворимость золотой проволоки в припое. В связи с этим, рекомендовано при монтаже ГИС золотой проволокой пайку проводить при температуре не выше 10 °С от температуры плавления припоя.
Экспериментальным путем установлена зависимость растворения золотой проволоки диаметром 40 мкм от времени выдержки в твердой фазе (температура 100 °С) низкотемпературных припоев (рис. 4.15). Полное растворение проволоки произошло через 60 ч испытаний в припое ПОСК50-18 и через 540 ч – в припое ПОИ50. Наименьшей растворимостью обладает золотая проволока в контакте с припоями на основе эвтектики олово-свинец: за 600 ч выдержки в припое ПСрОСЗ58 диаметр проволоки уменьшился до 18 мкм.
Рис. 4.14. Растворение золотой проволоки диаметром 40 мкм от времени выдержки в припое ПОС-61 при различных температурах расплава, °С: 1 – 190; 2 – 210; 3 – 230; 4 – 250
100
Рис. 4.15. Растворение золотой проволоки диаметром 40 мкм от времени выдержки при температуре 100 °С для различных припоев: 1 – ПСрОСЗ-58; 2 – ПОИ50; 3 – ПООК50-18
Для уменьшения растворения золотой проволоки как в жидкой, так и в твердой фазах припоя используют способ пайки сопротивлением, позволяющий гарантировать дозированное погружение в припой золотой проволоки при пайке.
4.3. Влияние свойств соединяемых элементов и их подготовки к монтажу на качество соединений
Трудоемкость технологических процессов сварки и пайки в производстве изделий электронной техники составляет 15 % от их общей трудоемкости изготовления. Для увеличения выхода годных изделий на операциях монтажа необходимо повысить качество инструмента и проволоки, а также улучшить состояние поверхности контактных площадок на кристалле и покрытий корпуса.
Дальнейшее развитие технологии и оборудования сборочных процессов связано с разработкой автоматического оборудования с электронными сканирующими устройствами и системами оптико-телевизионного контро-
101
ля. Уже созданы автоматы производительностью до 10 – 15 тыс. соединений в час и выше. Автоматизация процессов монтажа проволочных соединений предъявляет повышенные требования к механическим и физическим свойствам проволоки, определяемым ее составом.
На прочность и качество микросоединений существенное влияние оказывают поверхностные загрязнения проволоки и контактной площадки. Наличие оксидов металла или органических загрязнений действует как барьер, препятствующий осуществлению взаимодиффузии между проволокой и пленкой. Оксиды металлов обычно удаляются химическим травлением, а органические загрязнения перед термокомпрессионной сваркой рекомендуется удалять ультрафиолетовым облучением. Травление золотой проволоки и пленки перед сваркой в растворе (Н2О:HF·HNO3) с концентрацией (10:1:1) приводит к увеличению прочности соединений проволока – пленка. Кроме того, данный раствор не изменяет геометрических размеров проволоки и морфологии ее поверхности.
Поверхностные явления играют очень важную роль в обеспечении качества контактных соединений в производстве РЭА. Исследования с применением метода Ожеспектроскопии термокомпрессионных соединений показали, что причины появления пурпурной и черной чумы самым тесным образом связаны с чистотой и загрязнениями поверхности, к которой присоединяется проводник.
4.3.1. Прочность микросоединений, выполненных термокомпрессионной и ультразвуковой сваркой, в зависимости от механических свойств алюминиевой проволоки
В настоящее время в качестве материала перемычек между кристаллом и корпусом в большинстве случаев применяют алюминий и золото. Золото обладает уникальными физикомеханическими свойствами, однако его применение ограничено из-за металлургической «несовместимости» с алюминие-
выми пленками. Применение алюминиевой проволоки позволяет использовать при монтаже микросоединений термокомпрессионную и ультразвуковую сварки.
Проволоку микронных размеров получают методом волочения через алмазные фильтры или гидростатическим прессованием – гидроэкструзией. Для волочения проволоки из легированного кремнием алюминия в медной оболочке разработана прямоточная машина марки МВА-4/40. Основные технические характеристики машины следующие: скорость волочения до 200 м/мин, диаметр проволоки от 0,1 до 0,029 мм.
Наиболее важными механическими свойствами привариваемой проволоки являются прочность и относительное удлинение. Прочность – есть напряжение при разрушении, а относительное удлинение – процентная деформация при разрушении проволочного образца, подвергнутого испытанию натяжением при комнатной температуре. Эти свойства могут изменяться в довольно широких пределах для каждой партии и даже для отдельных катушек одной партии проволоки. Для стабилизации свойств проволоки микронных размеров ее подвергают отжигу перед монтажом. Целью отжига является снижение механической прочности и повышение пластичности проволоки.
Параметры механических свойств сварочной проволоки (прочность и удлинение) основываются, в основном, на данных, полученных в лабораторных условиях. Однако условия сборки на высокопроизводительной установке могут существенно отличаться от лабораторных. Поэтому сведения о механических свойствах проволоки постоянно изменяются, когда накапливаются экспериментальные данные с производственных участков. Это прагматическое приближение удовлетворительно для операции сборки стандартного прибора, но заведомо неэффективно, когда применяется новая проволока или из-
102 |
103 |
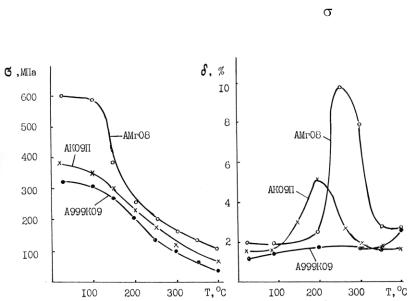
менения касаются выводной рамки или металлизации кристал- |
Алюминиевая проволока марки А999 диаметром |
||||||
ла. |
|
|
0,025 – 0,04 мм, легированная 1 % кремния, обладает |
||||
Неиспользованная проволока с течением времени может |
достаточной прочностью при некотором снижении элек- |
||||||
менять свои свойства. Это обусловлено релаксацией напряже- |
тропроводности по сравнению с чистым алюминием. Од- |
||||||
ний от холодной обработки, вводимых во время волочения. |
нако введение в алюминий легирующего элемента крем- |
||||||
Ослабление напряжений обычно вызывает увеличение удли- |
ния приводит к неоднородной двухфазной структуре |
||||||
нений, но если релаксация металла неоднородна, удлинение |
сплава. Предварительная закалка прутков из сплава алю- |
||||||
может уменьшаться. Чтобы свести к минимуму изменение |
миния с 1 % кремния позволяет получить структуру мик- |
||||||
свойств долго не использованной проволоки, обычно рекомен- |
ропроволоки с равномерным мелкодисперсным распре- |
||||||
дуется хранить ее при комнатной температуре и не более 6 ме- |
делением второй фазы. |
|
|||||
сяцев. |
|
|
Механические свойства проводников влияют не |
||||
Релаксация напряжения в проволоке может изменять |
только на прочность микросоединений, но и на надеж- |
||||||
прочность сварного микросоединения. Наибольшую деграда- |
ность контактов и полупроводниковых приборов в це- |
||||||
цию испытывает проволока, подвергнутая холодной обработ- |
лом. Прочность алюминиевой проволоки влияет на цело- |
||||||
ке, отожженная проволока изменяется |
в |
меньшей степе- |
стность оксида SiO2 под сварным контактом. Известно, |
||||
ни.Данные зависимости прочности на разрыв |
и относитель- |
что после ультразвуковой сварки изменяется сопротив- |
|||||
ного удлинения δ от температуры отжига для различных марок |
ление между проволочным выводом и подложкой, т. е. |
||||||
алюминиевой микропроволоки представлены на рис. 4.16. |
через пленку SiO2. В соединениях, в которых использо- |
||||||
|
|
|
валась проволока с прочностью на разрыв Рразр. = 0,3 – |
||||
|
|
|
0,37 Н, |
наблюдалось |
сопротивление |
утечки менее |
|
|
|
|
100 кОм, т. е. происходило нарушение пленки оксида. |
||||
|
|
|
Для соединений с проволокой Рразр. = 0,2 – 0,25 Н сопро- |
||||
|
|
|
тивление утечки составляло около 1 кОм. |
|
|||
|
|
|
Для исследования влияния физико-механических |
||||
|
|
|
свойств алюминиевых проводников на качество контак- |
||||
|
|
|
тов при термокомпрессионной сварке оценивалась проч- |
||||
|
|
|
ность соединений проводник – алюминиевая пленка. В |
||||
|
|
|
качестве выводов применялась алюминиевая проволока |
||||
|
|
|
диаметром 0,027 мм с различной прочностью на разрыв: |
||||
|
|
|
Ppaзр. = 0,16; 0,20; 0,24 Н. Различные механические свой- |
||||
|
|
|
ства алюминиевых проводников получены соответст- |
||||
а) |
б) |
вующей термообработкой. |
|
||||
Для оценки влияния химического состава провод- |
|||||||
Рис. 4.16. Зависимость прочности на разрыв (а) и относи- |
|||||||
ников |
на прочность |
микросоединений |
использовалась |
||||
тельного удлинения (б) от температуры отжига для различных |
марок алюминиевой микропроволоки. |
алюминиевая проволока диаметром 0,027 мм, легирован- |
|
ная 0,72 % Mg, 1 % Mg, 0,9 % Si и 0,5 % Сu. Толщина |
||
|
104 |
105 |
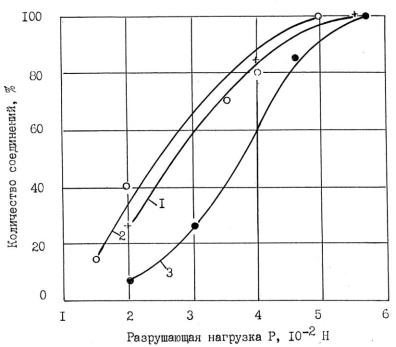
алюминиевых пленок составляла 1 – 1,2 мкм. Термокомпрессионная сварка выполнялась на установке НПВ-1A на оптимальных режимах: температура 350 ± 5 °С, усилие сжатия 1,1 Н и время 0,4 с. Микросоединения подвергались визуальному контролю под микроскопом. Прочность соединений измерялась путем отрыва проводников под углом 45° к подложке.
На рис. 4.17 представлены зависимости прочности микросоединений от механических свойств алюминиевой проволоки. Как видно из рисунка, механические свойства проволоки практически не влияют на прочность микросоединений. Это можно объяснить тем, что при термокомпрессионной сварке происходит дополнительный отжиг проволоки. Разброс по прочности микросоединений объясняется нестабильностью геометрических размеров сечений проволоки.
Прочность микросоединений зависит от химического состава материалов выводов (рис. 4.18). Некоторое увеличение прочности достигается при сварке проволокой, легированной
магнием и кремнием.
Рис. 4.17. Интегральное распределение прочности соединений Al – Al, выполненных термокомпрессионной сваркой, проволокой с различной прочностью: 1 – Рразр. = 0,16 Н; 2 – Рразр. = 0,20 Н; 3 – Рразр. = 0,24 Н
Воспроизводимость прочности микросоединений в зависимости от химического состава алюминиевой проволоки недостаточно высокая, В значительной степени это связано с технологическими режимами сборочных операций.
Качество соединений алюминиевая проволока – пленка, выполненных ультразвуковой сваркой, также зависит от свойств проволоки. Для исследования зависимости прочности соединения от содержания кремния в алюминии проволока приваривалась к пленке на следующих режимах: мощность ультразвукового преобразователя 0,6 – 0,7 Вт, давление сварочного инструмента 0,3
– 0,4 Н, время сварки 0,1 – 0,2 с. Максимальная проч-
106 |
107 |
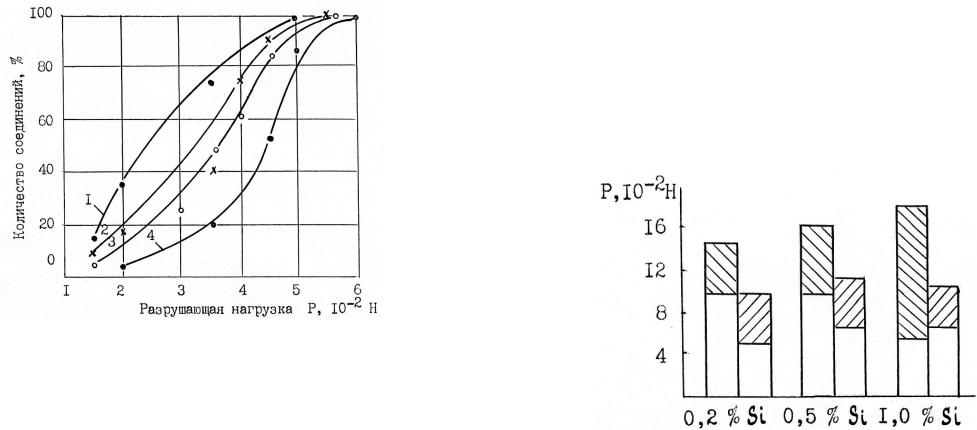
ность с наименьшим разбросом ее показателей достигается при ультразвуковой сварке алюминиевой проволоки диаметром 0,04 мм, легированной 0,5 и 0,8 % кремния (рис. 4.19).
Рис. 4.18. Интегральное распределение прочности соединений Al – Al, выполненных термокомпрессионной сваркой, проволокой с различным содержанием легирующих веществ: 1
– Al (0,5 % Сu); 2 – А1 (0,72 % Mg); 3 – Al (0,9 % 56 Si); 4 – Al (1,0 % Mg)
4.3.2. Влияние химической обработки алюминиевой проволоки перед сваркой на качество соединений
При решении вопроса о надежности микросоединений в ИЭТ, наряду с отработкой режимов монтажа, следует учитывать и такой фактор, как подготовка соединяемых элементов к сварке или пайке. К сожалению, вопросам влияния очистки проволоки и пленочной металлизации перед операцией при-
соединения выводов на надежность микросоединений уделяется недостаточное внимание.
Проволока, подлежащая сварке, должна быть гладкой и чистой. При УЗС поверхностные пленки и загрязнения интенсивно вытесняются из зоны сварки, но не полностью. Поэтому проволоку необходимо очищать от смазки, отпечатков пальцев, водяных капель, монооксида кремния и других включений, загрязняющих контактные площадки кристалла и корпуса при сборке, тем самым, ослабляя сварное соединение. Кроме того, нарушается свободная подача проволоки через отверстие микросварочного инструмента.
Рис. 4.19. Зависимость прочности сварных соединений на отрыв проволоки диаметром 0,04 мм под углом 90° к подложке от содержания кремния в алюминии:
– соединение Al – Al
– соединение Al – Аu.
Обычно в полупроводниковой промышленности используется способ «мокрой» химической очистки, заключающийся в частичном стравливании металлической
108
поверхности или растворении неорганических загрязнений. Для исследований влияния видов химической очистки
алюминиевой проволоки перед термокомпрессионной сваркой на качество сварных соединений Al – Au использовались следующие способы обработки:
–кипячение в изопропиловом спирте в течение 4 минут с последующей сушкой в вакууме (давление 0,14 Па) при температуре 70 °С в течение 10 мин;
–трехкратная обработка в ацетоне по 2 мин с последую-
щей сушкой в вакууме (давление 0,14 Па) при температуре 40 °С в течение 10 мин;
–обработка в течение 2 мин и дважды по 20 с в растворе триэтаноламина (ТЭА) (0,6 мл/л) с последующей сушкой после каждой операции при температуре 70 °С в течение часа;
–обработка в растворе триэтаноламина (0,6 мл/л); бензойнокислого натрия (0,2 г/л) в течение 2 мин с последующей сушкой при температуре 70 °С в течение часа.
Данные реагенты были выбраны потому, что они снимают примеси с поверхности проволоки, не подтравливая ее.
Сравнительная оценка влияния обработки проволоки перед сваркой проводилась ускоренными испытаниями соединений А1 – Аu на коррозионную стойкость. Для проведения коррозионных испытаний были изготовлены образцы, представляющие собой позолоченную коваровую ножку транзистора KT312, траверсы которой термокомпрессионной сваркой соединены алюминиевой проволокой, легированной 0,8 % Мg. Диаметр проволоки составлял 0,027 мм. Соединения формировались на установке НПВ-1A на режимах: давление инструмента 2,2 Н, температура 350 °С, время 0,4 с.
Исследования соединений Аl – Аu проводились в конденсате промышленной атмосферы (моль/л): 0,01·NaCl +
0,001·Na2SO4 + 0,001·N2SО3. Эффективность очистки проволоки оценивали по времени полного разрушения контакта.
Перед сваркой на проволоке, обработанной различными химическими веществами, снимались кривые потенциал – время (θ-η) со статическим градиентом потенциала 0,2 В. Ре-
109
жим снятия θ-η – кривых со статическим потенциалом 0,2 В давал возможность проводить ускоренные коррозионные испытания, так как этому интервалу потенциалов соответствует область активного растворения алюминия. Для сравнения были проведены аналогичные исследования на необработанной проволоке той же партии и плавки. Скорость разрушения микропроволоки обусловлена, как правило, ее структурной неоднородностью, а коррозия, несмотря на наличие химической обработки, носит язвенный характер. Алюминиевая проволока при наличии в ней магния подвергается равномерному коррозионному разрушению. Для того, чтобы замедлить развитие коррозионного процесса, необходимо снизить скорость анодной, либо катодной реакции. Применяемые для обработки вещества являются ингибиторами катодного типа. Следовательно, их ингибирующий эффект будет проявляться в том случае, если они достаточно прочно адсорбируются на поверхности защищаемого металла. Из всех исследованных химических веществ лишь триэтаноламин обладает ярко выраженной склонностью к хемосорбции, поэтому он и обладает более высокими защитными свойствами.
Результаты испытаний показали, что контактная коррозия сварных микросоединений имеет минимальную скорость в случае обработки алюминиевой проволоки раствором триэтаноламина, а также раствором триэтаноламина с бензойнокислым натрием (рис. 4.20).
Скорость разрушения контактов после обработки проволоки в изопропиловом спирте и ацетоне мало отличается от необработанных образцов. Следовательно, для повышения физико-химической устойчивости контактов алюминий – золото целесообразно обрабатывать проволоку перед термокомпрессионной сваркой в растворах, содержащих триэтаноламин. Такая обработка не только повышает коррозионную стойкость контактов, но и спо-
111
110
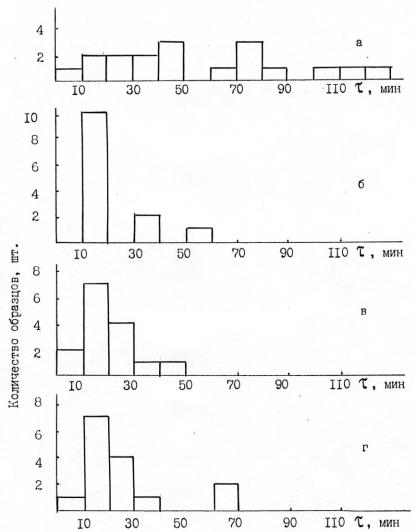
собствует получению наиболее стабильных результатов по прочности сварных соединений.
Рис. 4.20. Гистограмма кинетики разрушения контактов алюминий – золото в зависимости от видов химической обработки перед сваркой проволоки AМг08: а – раствор ТЭА с бензоинокислым натрием; б – без обработки; в – изопропиловыи спирт; г – ацетон
4.4. Зависимость качества микросоединений от технологических режимов микросварки
Одним из основных критериев качества микросоединений является их прочность, которая зависит от соединяемых материалов, методов соединения, конструктивных особенностей оборудования, формы и материала сварочного инструмента. При микросварке давлением проволочных выводов прочность микросоединений зависит от величины деформации проволоки. Величина деформации проволоки является обобщенной характеристикой режимов сборочных процессов: температуры, давления и времени сварки. При малой деформации прочность сварного соединения, как правило, незначительная. В этом случае при испытаниях прибора может произойти разрушение микросоединения по сварному шву. С увеличением деформации проволоки прочность соединения возрастает, но начинает снижаться прочность вывода за счет ослабления его сечения в месте наибольшей деформации. Оптимальная деформация проволоки определяется по достижению максимальной прочности на отрыв и ее стабильности для всех соединений. Для микросварных соединений алюминиевой микропроволоки, полученных методом ультразвуковой сварки, оптимальной считается деформация на 35 – 45 % больше исходного диаметра вывода, а при термокомпрессионной сварке ширина деформированной части проволоки в месте контакта не должна превышать трех диаметров проволочного вывода.
Для контроля прочности микросоединений в настоящее время существуют автоматы микросварки, предусматривающие автоматический контроль проволочных перемычек с последующей отбраковкой изделий, не вы-
112
державших испытание. Данные установки могут работать автономно или в составе линии сборки приборов.
Методы контроля сформированных микросварных соединений не могут быть использованы для оперативной корректировки параметров режима сварки, т. е. управления процессом микросварки. В настоящее время актуальным направлением разработок в области микросварки является создание систем активного контроля процесса формирования микросварных соединений и управления процессом микросварки. При этом очень важным является выбор исходных параметров, которые отображают состояние элементов в процессе формирования неразъемного соединения.
Различают следующие методы контроля формирования соединений и управления процессом микросварки: по электрическим характеристикам контакта; по деформации присоединяемой проволоки; по электрическим характеристикам ультразвуковой колебательной системы. Для организации процесса управления необходимо иметь информацию о результатах управления, устройство для анализа полученной информации и выработки решения, а также исполнительное устройство, осуществляющее управление сварочной системой.
При выборе метода управления процессом микросварки необходимо учитывать применимость его к конкретному способу сварки и конструкции изделия. Основным недостатком методов управления процессом микросварки является зависимость критерия качества микросварных соединений от свойств соединяемых элементов, подготовки свариваемых поверхностей и величины силы сцепления сварочного инструмента с присоединяемым выводом.
Одной из актуальных проблем управления качеством в электронной промышленности считается проблема снижения трудоемкости операции визуального контроля. Данная операция имеет весьма низкую эффективность, так как количественная оценка результатов затруднена из-за сложности описания процесса восприятия и переработки зрительной информации, а также неизбежности субъективного подхода к оценке
113
качества продукции со стороны контролера. Поэтому используются автоматы, заменяющие визуальный контроль на машинный. Работа данных автоматов состоит в фотографировании телевизионной камерой участков сварных соединений, сканировании изображения для получения последовательных электрических сигналов, преобразования последних в двоичные сигналы, которые оцениваются управляющим процессором мини-ЭВМ.
Основным недостатком автоматизированного визуального контроля является относительность критерия «оптимальная деформация», так как деформация проволоки еще не означает правильный выбор параметров режима сварки. Это связано с разбросом по диаметру микропроволоки, изменением поверхности пленочной металлизации на кристалле и корпусе у разных приборов одной и той же партии. Метод визуального контроля микросварных соединений рекомендуется проводить параллельно с другими методами.
Разработанные системы управления процессом микросварки и активного контроля качества эффективны при соблюдении оптимальных режимов микросварки. При выборе метода управления процессом микросварки необходимо учитывать применимость его к конкретному способу сварки и конструкции изделия. Например, для ультразвуковой микросварки на автоматическом оборудовании для любой конструкции прибора можно рекомендовать управление процессом микросварки по изменению амплитуды колебаний сварочного инструмента или по изменению электрических параметров цепи ультразвукового преобразователя. Последующий автоматический контроль каждой сформированной перемычки осуществляется калиброванной нагрузкой, а затем проводится заключительный контроль внешнего вида сварных соединений с помощью машинного зрения. При таком системном построении контроля возможно получение микросварных соединений с гарантированной стабиль-
114
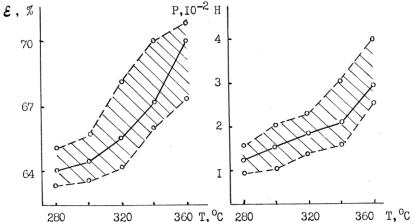
ностью качества соединений. Метод контроля сформированных микросоединений выбирается в зависимости от предъявляемых требований по прочности и конструкции ИЭТ.
4.4.1. Влияние технологических режимов на прочность микросоединений при термокомпрессионной сварке
Для оценки влияния на прочность микросоединений технологических режимов проводились исследования по выбору оптимальных усилий сжатия и температуры термокомпрессионной сварки алюминиевой проволоки с пленками алюминия и золота. Время сварки (0,2 – 1,0 с) практически не влияет на прочность микросоединений. Рассматривались не только усилия отрыва проводников от пленок алюминия и золота, но и изменение величины деформации. В качестве материала вывода применялся алюминиевый проводник марки А999К09 диаметром 0,027 мм. Исследования прочности микросоединений проводились на пластинах, покрытых слоем алюминия и золота, а также на приборах типа KT312. Сварка выполнялась на установке НПВ-1A. Режимы термокомпрессионной сварки изменялись в следующих пределах: усилия сжатия от 0,5 до 1,5 Н на кристалле и от 1,6 до 2,4 Н на траверсе, температура сварки от 260 до 360 °С, время сварки во всех случаях 0,4 с.
Испытания на прочность проводились путем разрушения микросоединений под углом 90° к поверхности подложки. При этом наблюдались в основном два вида разрушений: обрыв по утонению проволоки в месте контакта; частичное или полное отслаивание проволоки от пленок. Первый вид разрушений имеет место при температуре сварки 340 – 360 °С. При температуре сварки 280 – 320 °С в основном наблюдались разрушения с отслаиванием проводника. В этом случае на поверхности пленок алюминия видны характерные линии сдвига и зоны объемного взаимодействия проводника с пленкой золота.
Деформация и усилия отрыва алюминиевой проволоки с пленками Al и Аu, изменяются в зависимости от температуры сварки. Можно выделить две характерные зоны: первая 280 –
115
320 °С и вторая 320 – 360 °С. В первой зоне прочность соединений Al – Al (рис. 4.21, б) при усилии сжатия Q = 1 H и А1 – Аu (рис. 4.22, б) при усилии сжатия Q = 2 Н изменяется незначительно и колеблется в пределах 0,01 – 0,02 Н. Во второй зоне наблюдается значительное увеличение прочности до 0,03 – 0,05 Н.
а) б)
Рис. 4.21. Изменение величины деформации (а) алюминиевой проволоки диаметром 0,027 мм и прочности микросоединений (б) от температуры термокомпрессионной сварки при усилии сжатия 1,0 Н
Деформация алюминиевой проволоки ε после термокомпрессионной сварки определялась по формуле
ε = (1 – π/4 – d/B)·100 %,
где d – исходный диаметр алюминиевой проволоки; B – ширина сварной точки (деформированной проволоки).
Усилия сжатия, при которых достигается наибольшая прочность микросоединений, составляют 2 – 2,2 Н для соединения Al – Au и 1 – 1,2 Н для соединения Al – Al при температуре сварки 350 °С. При меньших усилиях сжатия разрушение микросоединений сопровождается в
117
116
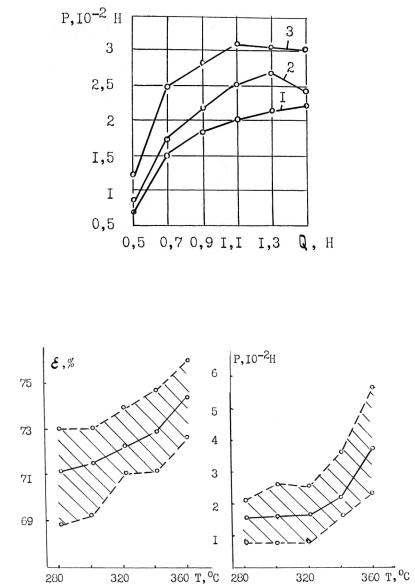
основном отслаиванием выводов от пленок. Усилия сжатия (1,3 – 1,5 Н на кристалле и 2,3 – 2,5 Н на траверсе) приводят к увеличению деформации проволоки. Разрушения при этих режимах наблюдаются в виде отрыва по утонению проволоки в месте контакта.
Исследования формы и размеров сварных соединений показывают, что величина деформации проводника изменяется незначительно при изменении температуры и усилии сжатия при сварке. Так, для соединения Al – Al при температуре сварки 350 °С и усилии сжатия 0,5 Н ширина сварной точки со-
ставляет 50 – 54 мкм (ε = 58 – 61 %)
и 63 – 71 мкм (ε = 67 – 70 %) при усилии сжатия 1,1 Н. Соответственно при той же температуре сварки для соединения Al
– Au ширина сварной точки составляет 68 – 74 мкм (ε = 68 – 72 %) при усилий сжатия 1,6 Н и 75 – 88 мкм (ε = 72 – 76 %) при усилии сжатия 2,4 Н (рис. 4.23, а).
Усилие сжатия является величиной фиксированной, т. е. не изменяющейся в процессе сварки, поэтому на рис. 4.21, б и 4.23, б приведены только средние арифметические значения прочности без учета разброса из-за геометрической нестабильности сечений проволоки. Колебание температуры сварки в пределах ± 5 °С от оптимальной (350 °С) несущественно влияет на изменение величины деформации проволоки и прочности микросоединений в сравнении с отклонениями геометрических размеров исходного диаметра проволоки. Так, в соединениях Al – Al (рис. 4.21, а) при оптимальной температуре величина деформации (средние арифметические значения ε ) изменяется от 68 до 69,2 % в то время как разброс из-за геометрической не стабильности сечения проводника диаметром 0,027 мм составляет 66,9 – 70,2 %. Аналогично изменяется и прочность микросоединений. При этом в первом случае разброс составляет 0,023 – 0,027 Н и 0,021 – 0,035 Н – во втором.
Одним из возможных способов высокопроизводительной сварки алюминиевых лепестковых выводов толщиной 30 – 40 мкм и шириной 100 – 150 мкм с полупроводниковым кристаллом является ударная термокомпрессионная микросварка.
118
Рис. 4.22. Влияние усилия сжатия Q, при термокомпрессионной сварке на прочность микросоединений алюминий – алюминий в зависимости от температуры: 1 – 300 °С; 2 – 325 °С; 3 – 350 °С
а) б)
Рис. 4.23. Изменение величины деформации (а) алюминиевой проволоки диаметром 0,027 мм и прочности микросоединений (б) от температуры термокомпрессионной сварки при усилии сжатия 2,0 Н
119