
3565
.pdf1 |
2 |
3 |
4 |
ле |
между сварными соедине- |
|
|
|
ниями и смежной металли- |
|
|
|
зированной дорожкой или |
|
|
|
контактной площадкой |
|
|
|
меньше ширины металлизи- |
|
|
|
рованной дорожки в самом |
|
|
|
узком месте по чертежу; ме- |
|
|
|
нее ¾ площади сварного со- |
|
|
|
единения находится в преде- |
|
|
|
лах контактной площадки. |
|
|
2. |
Изделие бракуют, если: диа- |
То |
100 % |
Контроль |
метр шарикового контакта к |
же |
|
кристаллу менее двух диа- |
|
||
|
|
|
|
дефектов |
метров или в четыре раза |
|
|
сварного |
больше диаметра проволоч- |
|
|
ного вывода; имеются следы |
|
|
|
|
|
|
|
соедине- |
повторной сварки на одной и |
|
|
ния «ша- |
той же контактной площад- |
|
|
ке; центр сварного контакта |
|
|
|
|
|
|
|
риком» |
смещен к краю контактной |
|
|
|
площадки более чем на ½ |
|
|
|
диаметра проволочного вы- |
|
|
|
вода |
|
|
3. |
Изделие бракуют, если: раз- |
То |
100 % |
Контроль |
мер сварного соединения на |
же |
|
кристалле меньше 4/3 диа- |
|
||
|
|
|
|
дефектов |
метра или в три раза больше |
|
|
сварного |
диаметра проволочного вы- |
|
|
вода; имеются следы по- |
|
|
|
|
|
|
|
соедине- |
вторной сварки на одной и |
|
|
ния «кли- |
той же контактной площад- |
|
|
ке. |
|
|
|
|
|
|
|
ном» |
|
|
|
|
|
|
|
4. |
Изделие бракуют, если: |
В |
100 % |
Контроль |
сварное соединение не пол- |
изуаль- |
|
ностью расположено на вы- |
|
||
|
|
|
|
дефектов |
воде основания корпуса; |
но, |
|
|
размер сварного соединения |
|
|
сварных |
меньше 4/3 диаметра или |
микро- |
|
соедине- |
больше трех диаметров про- |
скоп |
|
волочного вывода. |
|
||
|
|
|
|
ний на |
|
МБС -1 |
|
выводах |
|
|
|
основания |
|
|
|
корпуса |
|
|
|
|
|
|
|
Окончание Таблицы 6.1
1 |
2 |
3 |
4 |
5. |
Изделие бракуют, если: |
В |
100 % |
Контроль |
стрела прогиба проволоки в |
изуаль- |
|
горизонтальной плоскости |
|
||
дефектов |
больше трех диаметров про- |
но, |
|
волочного вывода; имеются |
|
||
|
|
|
|
сварных |
неровности проволоки в ви- |
микро- |
|
соедине- |
де «сгиба» бороздок, умень- |
скоп |
|
шающие диаметр проволоки |
|
||
ний про- |
более чем на ¼, сужение |
МБС -1 |
|
проволоки из-за сильного |
|
||
|
|
|
|
волочных |
растяжения проволочного |
|
|
выводов с |
вывода более чем на ¼ диа- |
|
|
метра; «хвосты» сварных |
|
|
|
выводами |
соединений составляют бо- |
|
|
лее одного диаметра прово- |
|
|
|
|
|
|
|
основания |
лочного вывода на кристалле |
|
|
корпуса |
и более трех диаметров на |
|
|
выводе основания корпуса; |
|
|
|
|
расстояние между проволоч- |
|
|
|
ными выводами меньше трех |
|
|
|
диаметров проволоки и (или) |
|
|
|
½ расстояния между свар- |
|
|
|
ными соединениями на кри- |
|
|
|
сталле и на выводе основа- |
|
|
|
ния корпуса; проволочный |
|
|
|
вывод оборван; разводка |
|
|
|
проволочных выводов не |
|
|
|
соответствует ТД; прово- |
|
|
|
лочный вывод соединения |
|
|
|
«шариком» не перпендику- |
|
|
|
лярен поверхности кристал- |
|
|
|
ла |
|
|
|
6.Ко |
Разрушение соединения |
Ус |
Выбо- |
|
нтроль |
должно происходить не в |
тройст- |
бо- |
|
месте сварки, а по проволо- |
во для |
рочно |
||
|
||||
|
опреде- |
|||
прочности |
ке. Прочность сварного со- |
(три |
||
ления |
||||
|
единения должна быть не |
соеди |
||
сварного |
усилия |
|||
меньше: для золотой прово- |
еди- |
|||
|
отрыва |
|||
соедине- |
локи диаметром 0,05 мм – |
нения |
||
(граммо |
||||
|
0,05 Н; 0,04 мм – 0,05 Н; |
из |
||
ния |
мо- |
|||
0,03 мм – 0,04 Н, а для алю- |
метр), |
пар- |
||
|
||||
|
миниевой проволоки диа- |
микро- |
тии) |
|
|
метром 0,04 мм – 0,03 Н. |
скоп |
|
|
|
|
МБС-1, |
|
|
|
|
МБС-2 |
|
Фотографии внешнего вида качественных микросоединений, а также дефектных контактов, характерных для конкретного прибора и вида монтажа, должны быть у каждого контрольного мастера. Качество микросоединений контролируемых приборов сравнивается с эталонными образцами. При контроле прочности микросоединений разрушению подвергаются не менее трех соединений из партии приборов. Если прочность соединения не удовлетворяет заданным требованиям, то всю партию приборов, как правило, бракуют.
6.3. Неразрушающие методы контроля качества микросварных соединений
В технологии производства ИЭТ одновременно с совершенствованием сборочного оборудования и оптимизацией технологических процессов монтажа развиваются методы и средства неразрушающего контроля качества микросоединений. К неразрушающим
методам прямой оценки качества микросоединений относятся:
–визуальный контроль под микроскопом;
–оценка электрических параметров контактного соединения: сопротивления, емкости, шума;
–ультразвуковое воздействие;
–контроль по тепловым параметрам;
–контроль по минимально заданному усилию на отрыв;
–обдув струей газа под давлением;
–рентгеновский контроль;
– электромагнитное воздействие. Заслуживает внимания контроль по тепло-
вым параметрам зоны соединения. Для определения тепловых полей, несущих информацию о качестве контролируемых соединений, применяют бесконтактный метод по инфракрасному излучению и контактный с помощью жидких кристаллов.
Наиболее широкое распространение в технологическом процессе сборки полупроводниковых приборов и микросборок получил неразрушающий метод прямого контроля качества микросоединений визуальным осмотром контактов под микроскопом. При выпуске особо надежных приборов применяют рентгеновский контроль просвечиванием приборов на пленку или с помощью рентгенотелевизионного микроскопа.
Электромагнитный метод применяется при отбраковочных испытаниях полупроводниковых
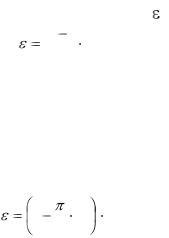
приборов. Для этого метода используются установки, управляемые ЭВМ.
6.3.1. Контроль геометрических размеров микросварных соединений (визуальный контроль)
Визуальный контроль качества микросварных соединений в настоящее время остается одним из основных методов 100 %-ного контроля сформированных микросварных соединений. В качестве основного критерия в данном случае используют величину и стабильность деформации присоединенной проволоки. Стабильность деформации проволоки после сварки считают показателем точности поддержания режимов и воспроизведения условий процесса сварки, т.е. стабильности прочности и других характеристик полученных сварных соединений.
Визуальный метод контроля предполагает, что внешний вид сварных соединений связан с их прочностью и зависит от деформации проволоки. При малой деформации прочность сварного соединения, как правило, незначительная. В этом случае при испытаниях прибора может произойти разрушение микросоединений по сварному шву. С увеличением деформации проволоки прочность соединений возрастает, но начинает снижаться прочность вывода за счет ослабления его сечения в месте наибольшей деформации. Поэтому оптимальная деформация определяется при достижении максимальной прочности соединений на отрыв и ее стабильности для всех контактов. Так, например, для микросоединений алюминиевой микро-
171
проволоки, полученных методом ультразвуковой сварки, оптимальной считается деформация 35 – 45 % от исходного диаметра вывода.
Деформация проволоки диаметром d может определяться по величине ее осадки :
d t |
100 %, |
|
d |
||
|
где t - толщина деформированного участка проволоки.
Поскольку оценить толщину деформированного участка трудно, то оценка деформации проволоки может быть выражена через ширину (диаметр) сварной точки:
1 |
|
|
d |
100 % , |
|
|
|
||
|
|
|
||
4 |
|
В |
|
где В - ширина (диаметр) деформированного участка проволоки (сварной точки).
При визуальном контроле микросварных соединений могут быть также обнаружены такие дефекты, как несоответствие места положения сварных соединений контактным площадкам прибора, разрушение поверхности полупроводникового кристалла, диэлектрических покрытий и металлических пленок, надрезы и надрывы проволоки и т. д.
6.3.2. Контроль по электрическим характеристикам контактов
Сварные соединения при пропускании через них электрического тока характеризуются рядом
172
электрических параметров: омическим сопротивлением, емкостью, спектром шума. Величина контактного электросопротивления сформированного микросварного соединения корректируется с прочностью и воспроизводимостью качества соединений, поэтому измерение электросопротивления или падения напряжений дает возможность контролировать качество микросварного соединения. Для повышения эффективности данного метода контролируют изменение падения электрического напряжения на контакте при приложении к нему калиброванной механической нагрузки отрыва натяжением вывода.
Следует отметить, что рассматриваемый метод трудно осуществим для контроля проволочного монтажа полупроводниковых приборов и интегральных схем, так как в этих цепях включено множество сопротивлений. Практически этот метод используется для сравнения качества соединений выводов, выполненных различными способами или в различных режимах. Исследования возможности контроля качества микросварных соединений по величине электрической емкости контакта не дают положительных результатов для полупроводниковых приборов.
Контроль сформированных соединений путем измерения спектра шума при пропускании через контакт постоянного электрического тока также не пригоден для определения качества изолированных контактов из-за сложных электрических цепей полупроводниковых приборов и интегральных схем. Шумовое напряжение контактов значительно меньше шумового напряжения всей цепи прибора, содержащего
кроме контактов p-n-переходы и резисторы.
6.3.3. Контроль качества ультразвуковым методом
Данный метод контроля качества сформированных микросварных соединений основан на свойстве электрического импеданса изменяться в зависимости от условий прохождения ультразвуковых колебаний в исследуемом микросварном соединении. Известны контактный и бесконтактный способы контроля данным методом.
Контактный способ осуществляется с помощью установки (рис. 6.1), оснащенной системой статического нагружения, в которой закреплен зонд-волновод. Система статического нагружения обеспечивает постоянство контактных усилий, а по изменению электрического импеданса пьезоэлемента, закрепленного на зондеволноводе, судят о качестве сварного соединения. После установки зонда-волновода на поверхность контролируемого микросварного соединения в волновую систему его включается сварное соединение. Поэтому качество сварного соединения при прохождении волны через систему зонд-соединение оказывает влияние на электрический импеданс пьезопреобразователя. Изменения электрического импеданса коррелируют с качеством сварных соединений, в результате чего устанавливается процент отраженной энергии при наличии непроваров и других де-
173
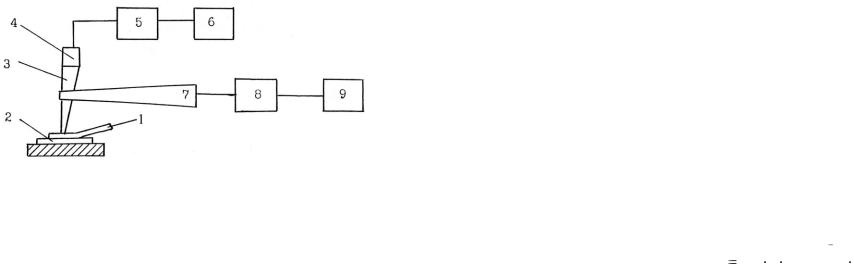
фектов между контактной площадкой и выводом, так как при идеальном сварном соединении ультразвуковая волна имеет минимальные потери.
Рис. 6.1. Схема установки контроля качества микросоединений ультразвуковым резонансным методом: 1 – алюминиевая проволока; 2 – пленочная металлизация (контактная площадка); 3 – зондволновод; 4 – пьезоэлемент; 5 – измеритель электрического импеданса; 6 – генератор; 7 – держатель зонда; 8 – система нагружения; 9 – индикатор нагружения
Таким образом, контактный способ является трудоемким и имеет низкую чувствительность для малых размеров контактных соединений, он может быть применен для выборочного контроля и исследований качества микросоединений.
Бесконтактный способ осуществляется с помощью электромагнитоакустических датчиков, которые располагают над зоной контролируемого микросварного соединения. Датчики состоят из стержней и катушек, излучающие торцы находятся над контролируемым соединением. На электромагнитоакустиче-
ские датчики подают радиоимпульсы, усиливаемые электромагнитом, расположенным над датчиком. Импульсы возбуждают в соединяемых деталях ультразвуковые колебания, которые в свою очередь наводят ЭДС в катушках датчиков. Величина последней зависит от качества микросварного соединения. Наведенная ЭДС поступает на вход приемного устройства, где происходит ее усиление. При пропускании ЭДС через амплитудный селектор анализируется величина сигнала, определяющая качество соединения. Величина напряжения, снимаемого с электромагнитоакустического датчика, при изменении качества микросварного соединения определяется по формуле
|
3h |
|
S |
|
E 2,6 I n2 B 2 e R |
|
, |
||
|
|
|||
|
|
|
Z S |
где I – ток, возбуждаемый в катушке датчика; n – число витков катушки; B – индукция магнитного поля; h – зазор между датчиком и микросварным соединением; R – средний радиус катушки датчика; S – площадь зоны сварки; ZS – входной импеданс сварного соединения.
Данный способ является достаточно сложным, а получаемые результаты зависят не только от состояния сварного шва, но и от площади зоны сварки, что трудно коррелируется с качеством микросварных соединений.
6.3.4. Контроль по тепловым параметрам зоны
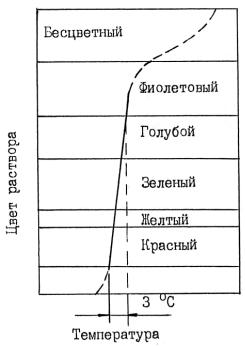
соединения
Микросоединения ИЭТ при прохождении по ним электрического тока нагреваются. Температура нагрева зависит от величины сопротивления, на которую влияет качество соединения проволоки с пленочной металлизацией. Поэтому знание реальной картины теплового поля в контактах позволяет судить о качестве микросоединений.
Наиболее распространенным способом контроля качества по тепловым параметрам зоны соединения является визуализация тепловых полей. Современные методы визуализации тепловых изображений можно подразделить на два класса: а) одновременное наблюдение теплового изображения всех соединяемых элементов; б) последовательное наблюдение теплового изображения всех соединяемых элементов. К первому классу относится, например, жидкокристаллический метод, использующий свойства холестерических жидкокристаллических соединений, окраска которых чувствительна к температуре и может обратимо изменяться вследствие эффектов дифракции и интерференции света в тонких пленках. Контроль температуры осуществляется по градуированным кривым, отражающим связь цвета с температурой. Характерное изменение цвета жидкокристаллического вещества в интервале 3 оС показано на рис. 6.2.
175
Рис. 6.2. Изменение цвета жидкокристаллического вещества в зависимости от температуры
Ко второму классу относятся методы визуализации, использующие развертку (сканирование) электронным или оптическим лучом и интерференционной голографии. Широкое распространение в технике контроля находят оптикомеханические сканирующие пирометры. Они характеризуются наличием оптико-механической сканирующей системы, осуществляющей при помощи подвижных или вращающихся элементов развертку изображения поля относительно приемника излучения.
Следует отметить, что методы контроля микросоединений по тепловым параметрам яв-
176

ляются весьма сложными и трудоемкими. Они могут применяться в лабораторных исследованиях микросварных контактов, полученных различными способами монтажа.
6.3.5. Использование тепловизоров для контроля тепловых полей
Одним из способов неразрушающего контроля является анализ температурного поля аппаратуры. Достаточно полную информацию о распределении температур по исследуемой поверхности дают тепловизоры. Оптическая система тепловизора представляет собой линзовый объектив, который формирует оптическое изображение объекта по его инфракрасному излучению (ИК) и фокусирует тепловой поток на поверхность приемника излучения. Приемник излучения преобразует падающий на его поверхность лучистый поток в электрический сигнал, который после усиления попадает в блок индикации. Приемник охлаждается жидким азотом в целях снижения шумов и влияния температуры окружающей среды на результаты измерений. Видимое изображение теплового рельефа градиента температур получают на экране электронно-лучевой трубки блока индикации. Рабочий диапазон длин волн приемной камеры тепловизора 2,0 – 5 мкм. Техническая характеристика тепловизоров приведена в табл. 6.2.
Таблица 6.2
Техническая характеристика тепловизоров
177
Параметр |
ИФ- |
БТ-1 |
АГА-750 |
|
10ТВ |
(Швеция) |
|||
|
|
|||
Диапазон регистри- |
От + |
От + |
От – 20 |
|
руемых температур, |
30 |
30 |
до + 900 |
|
°С |
до + |
до + |
|
|
|
200 |
200 |
|
|
Чувствительность, |
0,5 |
0,4 |
0,2 |
|
°С |
|
|
|
|
Поле обзора, градусы |
10 5 |
4,5 |
20 20 |
|
|
|
4,5 |
|
|
Число кадров в 1 с |
12,5 |
16 |
25 |
|
Мгновенный угол |
|
|
|
|
зрения, мрад |
3 |
4 |
3 |
|
Число строк |
75 |
100 |
280 |
|
Рабочая температура |
|
|
|
|
приемника излуче- |
|
|
|
|
ния, °С |
– 196 |
– 196 |
– 196 |
Примечание. Питание – сеть переменного тока; напряжение 220 В; частота 50 Гц.
Получаемые с помощью сканирующих ИК радиометров теплограммы позволяют проводить как качественный, так и количественный анализ тепловых полей аппаратуры. При качественном анализе все входящие в данный блок элементы разбиваются на группы, имеющие приблизительно одинаковый коэффициент излучения. Затем исследуется тепловое поле элементов каждой группы. Тепловой режим оценивается по яркости изображения элементов на экране про-
178
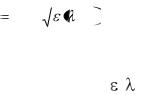
смотрового устройства или на теплограмме.
Для поиска неисправностей, возникающих в аппаратуре в процессе эксплуатации и испытаний, выявление скрытых дефектов в элементах и контроля технологических процессов изготовления блоков может быть использован метод образцовых теплограмм. Поиск изменений в тепловом режиме элементов РЭА данным способом осуществляется следующим образом. Предварительно с заранее обследованного образца исследуемого блока снимается теплограмма, которая в дальнейшем служит образцом, затем снимается теплограмма исследуемого блока. Сравнивая изображение теплового поля исследуемого блока с теплограммой образца, выявляются аномами в тепловом режиме, по которым можно определить причины их вызвавшие (неправильный монтаж элементов, изменение величины питающих напряжений, нагрузки, наличие дефектов в элементах и др.). Способ сравнения теплограмм дает возможность выбрать оптимальный вариант конструкции и способ крепления различных элементов схемы. Это особенно важно на стадии проектирования и отработки прибора.
Проведение качественного анализа существенно упрощается при цветном изображении тепловых полей. При цветном изображении теплового поля значительно увеличивается разрешающая способность человеческого глаза. Цветное изображение позволяет более детально исследовать тепловое поле блока РЭА.
Измерение температуры с помощью сканирующих ИК радиометров используется и для количест-
венного анализа ИЭТ. Для этих целей в приборе должно быть устройство, позволяющее получать изотермические линии, а температура измеряется по изотермам. Имея градуировочную кривую и семейство кривых, связывающих расчетную и истинную температуры, определяют расчетную температуру (Трас). Она равна истинной при условии, что излучательная способность объекта и опорного источника излучения, по которому снимается градуировочная кривая, равны. Чтобы исключить ошибку в измерении температуры, экспериментальным путем определяется связь между расчетной и истинной температурами для поверхностей, имеющих такой же коэффициент излучения, как и истинный объект. Между расчетной и истинной температурами частот существует линейная зависимость.
Измерение температуры ИК радиометрами заключается в регистрации энергетической (радиационной) температуры, величина которой определяется истинной температурой и коэффициентом излучения исследуемого объекта. В этом случае температура определяется по формуле
|
|
|
T Tэн / |
,Т , |
где Т – истинная температура исследуемого объекта; Тэн – энергетическая температура; ( , Т) - коэф-
фициент излучения поверхности исследуемого объекта.
Количественный анализ измерения темпера-
туры проводят также сканирующим ИК радиометром, позволяющим осуществлять выбор строки и при этом сигналы, поступающие с приемника лучистой энергии, можно просмотреть на экране осциллографа. При этом оценка температуры осуществляется с учетом масштаба температур по осциллограмме строки. Амплитуды сигналов на экране осциллографа будут пропорциональны интегральной плотности излучения каждого элемента. Сравнивая амплитуды сигналов от исследуемых объектов с амплитудой сигнала от контрольного излучателя, можно вычислить истинную температуру.
Применяя ИК радиометры для исследования тепловых полей, необходимо учитывать ряд факторов, которые могут существенно повлиять на результаты измерений. Это связано с различной излучательной способностью исследуемых объектов, воздействием фонового излучения и различиями коэффициента излучения на разных участках поверхности исследуемого объекта. Прием и преобразование ИК излучения исследуемых объектов наиболее эффективны только при наличии прямой их видимости. Поэтому исследование температурных полей приборов обычно ведут только при снятых кожухах, что часто не дает возможности оценить очень важные характеристики приборов.
6.4. Контроль прочности микросоединений
Одним из основных критериев качества сформированных микросварных соединений является их
прочность. Контроль прочности микросварных соединений проводится испытанием на сдвиг и отрыв. Для алюминиевой проволоки диаметром менее 0,1 мм и золотой менее 0,06 мм испытание на сдвиг является не эффективным, так как разрушение происходит, как правило, по проволоке при самых различных режимах сварки. Характер разрушения зависит от многих факторов, основными из которых являются: полнота взаимодействия соединяемых материалов на контактных поверхностях; величина пластической деформации в зоне контакта; форма сварной точки, которая зависит от рабочего профиля инструмента (пуансона), деформирующего привариваемую проволоку; адгезия пленки контактной площадки с подложкой, которая может изменяться при воздействии сварочного импульса; пластичность привариваемой проволоки и уровень механических напряжений, возникающих в проволоке и подложке.
Методы контроля прочности сформированных микросварных соединений основаны на приложении механической силы к выводу или перемычке, соединяющей две сварные точки. При этом известны различные способы приложения силы: механическое натяжение, обдув струей газа, воздействие линейных ускорений, центробежная сила, электромагнитный метод. Рассмотрим подробнее каждый из перечисленных методов.
180
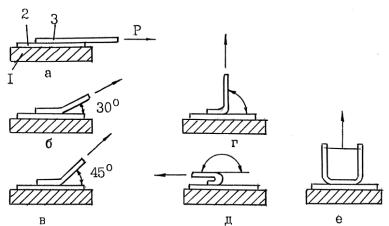
6.4.1. Контроль механическим натяжением проволоки
Данный метод является одним из наиболее распространенных методов контроля качества сформированных микросоединений. Для его реализации требуется простое технологическое оборудование, кроме того, применение метода позволяет получить количественные оценки прочности соединений. Суть метода состоит в том, что к проволочному выводу или перемычке прикладывается возрастающее механическое усилие до тех пор, пока не будет достигнуто заданное усилие натяжения или пока не произойдет разрушение соединения или проволочного вывода. В первом случае испытание является неразрушающим для контроля установленной прочности проволочных перемычек. Во втором случае проводится так называемое разрушающее испытание, при этом прилагаемое усилие называется разрушающим усилием и считывается мерой качества проволочных соединений.
На рис. 6.3 приведены возможные схемы испытания сварных соединений на прочность механическим натяжением проволоки.
181
Рис. 6.3. Схемы испытаний прочности микросоединений при натяжении: а – испытания на
сдвиг: |
1 |
– |
подложка; |
2 – контактная |
|
пленочная |
металлизация; |
3 – присоединенная проволока; б – д – испытания на отрыв под углом 30°, 45°, 90° и 180° соответственно; е – симметричная нагрузка по всей площади контакта
Испытание на сдвиг (рис. 6.3, а), как указывалось выше, не дает объективной оценки прочности микросоединений, так как разрушение происходит, как правило, по проволоке. При испытании на отрыв под углом 90 °С к контактной площадке (рис. 6.3, г) полнее характеризуется прочность микросоединений. Однако при испытании по данной схеме разрушение происходит по узким полоскам соединения, длина которых равна ширине деформированной проволоки. Поэтому этот вид испытаний не дает полного представления о действительной прочности соедине-
182