
3565
.pdf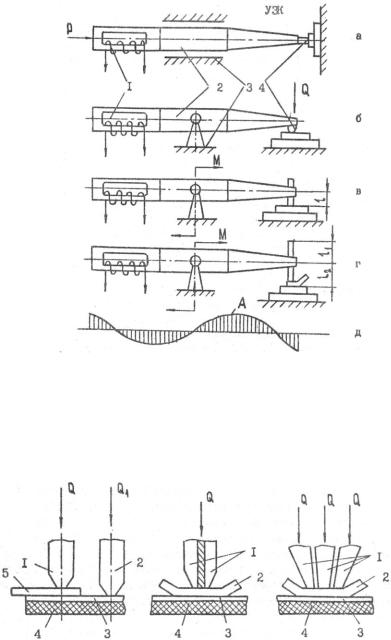
Рис. 3.6. Ультразвуковые колебательные системы для микросварки: 1 – преобразователь; 2 – волноводконцентратор; 3 – акустическая развязка; 4 – сварочный инструмент. А – амплитуда колебаний; Р – усилие сжатия; М – момент силы
а) |
б) |
в) |
47
Рис. 3.7. Схемы односторонней контактной сварки: а – односторонняя точечная сварка: 1 – электрод для сжатия свариваемых деталей и подвода тока к проволоке; 2 – электрод для подвода тока к шине печатной платы; 3 – контактная площадка или шина печатной платы; 4 – диэлектрическое основание печатной платы; 5 – привариваемая проволока или лента; б и в – односторонняя сварка соответственно сдвоенным электродом (с параллельными зазорами) и строенным электродом трехфазным (1 – электроды; 2 – привариваемый проводник; 3 – тонкая металлическая пленка; 4 – диэлектрическая подложка)
3.5. Пайка электродных выводов
Пайкой присоединяют электродные выводы мощных полупроводниковых приборов – транзисторов, выпрямителей, туннельных и СВЧ диодов, а также модулей. Пайку выполняют низкотемпературными припоями на основе олова, свинца и индия в печах непрерывного или периодического действия в атмосфере защитного газа или на воздухе. Пайку можно производить нагревом (прямым и косвенным) электрическим током или паяльником (электрическим, газовым). Перед пайкой детали необходимо тщательно очищать.
В производстве находит применение кассетная сборка мощных транзисторов в защитной
48
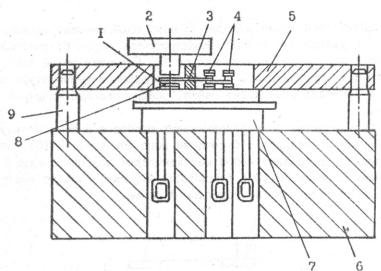
восстановительной среде (рис. 3.8). Применение пре- |
9 – направляющие |
цизионных кассет позволяет совместить операции |
|
пайки кристаллов на ножку корпуса, выводов к кри- |
3.6. Беспроволочные методы монтажа |
сталлу и траверсам, ликвидировать применение флю- |
|
са и, следовательно, последующей его отмывки, а |
К беспроволочным методам, позволяющим |
также исключить влияние оператора на качество из- |
исключать как проволочные соединения, так и |
готовления приборов. Кассета должна обеспечить |
ручную сборку, относятся монтаж перевернутого |
точную ориентацию кристалла относительно ножки |
кристалла (флип-чип) и кристалла с балочными |
прибора, выводов относительно контактных площа- |
выводами, а также с помощью паучковых выво- |
док и исключить их смещение в процессе пайки. Уси- |
дов. |
лие прижатия выводов к кристаллу и траверсам, а |
При монтаже методом перевернутого кри- |
также к ножке должно быть достаточным для полу- |
сталла в качестве выводов используют твердые |
чения надежного соединения. |
выступы в виде шариков из меди, покрытые лег- |
|
коплавким припоем (рис. 3.9). Необходимые со- |
|
единения на кристалле электрически связаны с |
|
шариками (контактными столбиками). Кристалл |
|
1 монтируется на ножку или плату 3 планарной |
|
стороной к точно расположенным участкам ме- |
|
таллизации 4. Он с определенным усилием при- |
|
жимается к плате при температуре, несколько |
|
превышающей температуру плавления припоя. |
|
Припой расплавляется и стекает на контактные |
|
металлизированные площадки платы, образуя |
|
прочное соединение. |
Рис. 3.8. Схема сборки транзисторов в прецизионной кассете: 1 – кристалл; 2 – грузик; 3 – паз для ориентации вывода; 4 – навеска из припоя; 5 – трафарет; 6 – корпус кассеты; 7 – ножка транзистора; 8 – прокладка из припоя;
49
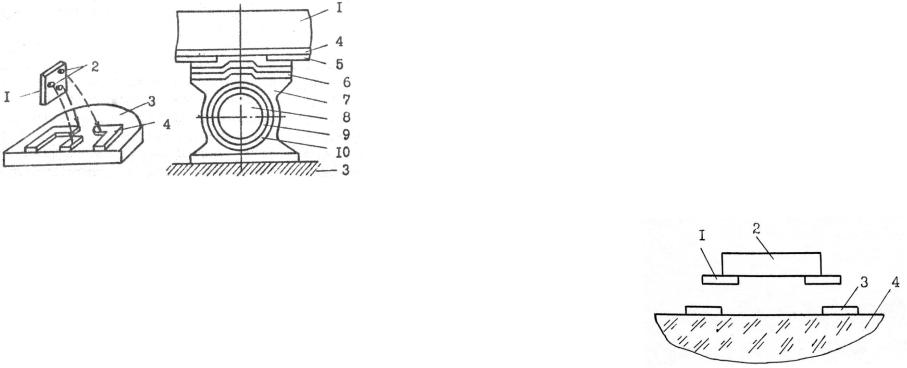
а) б)
Рис. 3.9. Монтаж перевернутого кристалла: а – с выступами; б – с шариками; 1 – кристалл; 2 – выступы; 3 – плата; 4 – алюминиевая металлизация; 5 – пленка
диоксида кремния; 6 – слои хрома; 7, 10 – припой; 8 – медный шарик; 9 – слой никеля
Контактные выступы на кристаллах могут быть изготовлены из припоя, а также гальваническим осаждением алюминия или золота. В случае получения выступов гальваническим осаждением кристаллы присоединяются термокомпрессионной или ультразвуковой сваркой.
В некоторых случаях в качестве выступов используют медные шарики (рис. 3.9, б). Для этого в кремниевом кристалле 1 на контактных площадках, покрытых пленкой 5, изготовляют окна, в которые осаждают слой хрома 6. Затем на этот слой наносят оловянистый припой 7 и укладывают медный никелированный шарик 8, который закрепляют оплавлением мягкого припоя 10. Совмещая такой выступ с контактной площадкой платы 3, при определенной
50
температуре и давлении на кристалл происходит пайка, обеспечивающая надежное соединение.
В производстве полупроводниковых приборов и ИС используют также монтаж кристаллов с балочными выводами (рис. 3.10). Балочные выводы представляют собой металлические полоски толщиной 10 – 40 мкм, шириной 50 –100, длиной 250 – 400 мкм, которые выступают за края кристалла подобно консольной балке.
Рис. 3.10. Монтаж кристаллов с балочными выводами: 1 – балочные выводы; 2 – кристалл; 3
– слой металлизации; 4 – плата
Кристалл 2 с балочными выводами 1 присоединяют к слою металлизации 3 на плате 4 термокомпрессионной или ультразвуковой сваркой. При монтаже кристаллов к плате приваривают только наружные части балок. Это предохраняет кристалл от разрушения и компенсирует напряжения, возникающие при сварке.
Развитие микроэлектроники привело к необходимости разработки и производства сверхбольших (СБИС) и сверхскоростных (ССИС) ин-
51
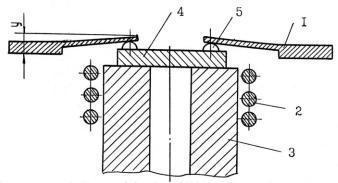
тегральных микросхем. Помимо роста степени интеграции, функциональной сложности, быстродействия и размеров кристалла резко возрастает число входных/выходных контактных площадок в данных схемах.
С увеличением числа выводов и размеров кристалла значительно увеличиваются габариты корпусов и длина межсоединений, а вследствие этого, значения сопротивлений, индуктивностей и емкостей.
Поэтому, методы сборки многовыводных СБИС в металлокерамические (пластмассовые) корпуса с помощью термокомпрессионной или ультразвуковой сварки проволочных выводов имеют ряд принципиальных ограничений дальнейшего развития.
Одним из последних достижений в области сборки ИС является метод паучкового крепления выводов. В производстве наибольшее распространение получили следующие схемы присоединения паучковых выводов к кристаллу: ультразвуковая групповая сварка, микропайка с косвенным подогревом без инструмента (рис. 3.11) и термоимпульсная микропайка
(рис. 3.12).
Рис. 3.11. Схема микропайки с косвенным подогревом: 1 – рамка с выводами; 2 – нагреватель; 3 – присоска; 4 – кристалл; 5 – контакт шариковый
При ультразвуковой групповой сварке кристалл удерживается в ориентированном положении вакуумной присоской, совмещение выводов с контактными площадками кристалла производится при помощи оптической системы, сварка осуществляется контурным инструментом за счет ультразвуковых колебаний.
При микропайке с косвенным подогревом после совмещения паучковых выводов 1 с шариковыми контактами 5 кристалла 4 вакуумная присоска 3 перемещается вверх, деформируя выводы на величину "У". За счет упругой деформации выводов возникающая сила стремится прижать их к шариковым контактам на кристалле. Включая нагревательный элемент 2, в местах соприкосновения выводов можно достичь температуры расплавления припоя. После остывания в местах контакта образуется спай.
При проектировании оборудования по данной схеме необходимо знать оптимальную деформацию паучковых выводов, которые должны создавать достаточное усилие на шариковые выводы в процессе микропайки.
52
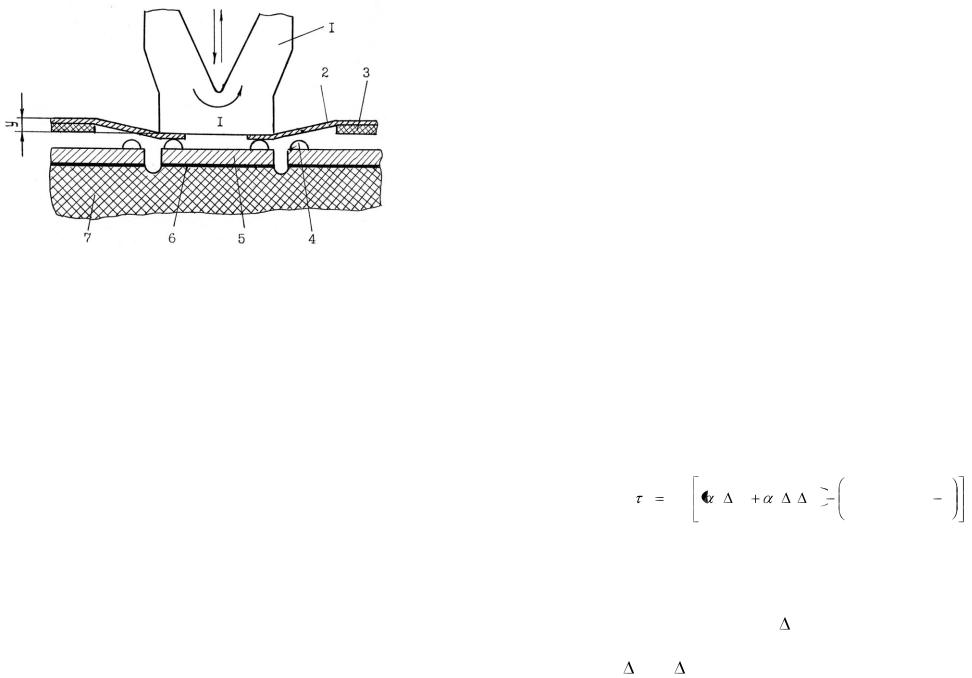
Рис. 3.12. Схема термоимпульсной микропайки: 1 – инструмент; 2 – паучковый вывод; 3 – диэлектрическая пленка; 4 – шариковый контакт; 5 – кристалл; 6 – клей; 7 – подложка
При термоимпульсной микропайке паучковые выводы 2 (рис. 3.12), закрепленные на диэлектрической пленке 3, совмещаются с шариковыми контактами4 на кристалле 5. Инструмент 1 опускается, прижимая паучковые выводы к шариковым контактам. Через инструмент пропускается импульс тока. Тепло передается в места контакта, нагревая их до температуры пайки. Слой клеящего вещества 6, удерживающий кристаллы на подложке 7 в ориентированном положении, расплавляется, и при поднятии инструмента кристалл, припаянный к паучковым выводам, отрывается от подложки за счет силы, вызванной предварительной упругой деформацией паучковых выводов. Силы сцепления кристалла с клеящим веще-
53
ством и подложкой должны быть меньше этой силы.
При проектировании оборудования по одной из рассмотренных схем присоединения необходимо рассчитывать оптимальные упругие деформации паучковых выводов и усилия, обусловленные этими деформациями. Знание этих величин позволит правильно выбирать материал и конструкцию паучковых выводов.
При групповом монтаже паучковых выводов к шариковым контактам кристаллов ИС из-за различных коэффициентов термического расширения выводов, кристалла и подложки в собранном узле возникают значительные термомеханические напряжения. Их величина зависит от соединяемых материалов, геометрических размеров и температуры процесса микропайки. Компенсировать термомеханические напряжения можно путем создания предварительных упругих деформаций паучковых выводов.
Для определения напряжения сдвига в направлении длины выводов получено выражение
|
Еh |
|
l |
T |
|
х T |
l 2 |
arcsin |
2 у |
l , |
х |
|
1 |
2 |
|
|
|||||
2rl |
|
1 |
|
2 у |
|
l |
|
|||
|
|
|
|
|
|
|
|
где у – величина прогиба паучкового вывода, мм; h – паучкового вывода в месте микропайки, мм; l
– длина паучкового вывода от защемления до центра шарикового контакта, мм; r – радиус шарикового контакта, мм; х - расстояние от центра шарикового контакта до центра кристалла ИС, мм; Т1 и Т2 – разность температур паучкового
54
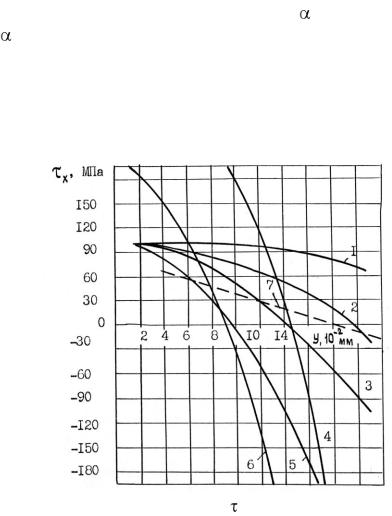
вывода и кристалла при микропайке и окружающей
средой, ºС; 1 и 2 – коэффициенты термического расширения материалов паучкового вывода и кристалла соответствен-
но, 1/ºС;
Е – модуль упругости материала паучкового вывода, кг/мм2.
Рис. 3.13. Зависимость х от прогиба y: 1 – при h = 0,02 мм и l = 3 мм; 2 – при h = 0,02 мм и l = 2 мм;
3 – при h = 0,02 мм и l = 1,5 мм; 4 – при h = 0,08 мм и l
= 1,5 мм; 5 – при h = 0,02 мм и l = 1 мм; 6 – при h = 0,04 мм и l
= 1 мм; 7 – кривая, разграничивающая области упругих и пластических деформаций для кривых 1, 2, 3 и 5
при h = 0,02 мм
Напряжения сдвига в зависимости от прогиба, длины и толщины выводов приведены на рис. 3.13. Для практического использования расчетов следует ввести ограничения по максимально возможным упругим деформациям. Пунктирная линия (рис. 3.13) разграничивает области упругих и пластических деформаций для толщины вывода h = 0,02 мм. При длине паучкового вывода в 1 мм (рис. 3.13) снизить термомеханические напряжения до нуля за счет упругих деформаций не удается. Поэтому по кривым зависимости целесообразно определять оптимальную длину паучкового вывода.
Используя данную методику определения оптимальных размеров паучковых выводов, получаем надежные микросоединения при групповом монтаже ИС.
3.7. Лучевые методы сварки и пайки
Технологические операции в производстве приборов микроэлектроники, осуществляемые с помощью лазеров, основаны на поглощении лазерного излучения веществом, т. е. на тепловом воздействии света на непрозрачные среды. Световой поток лазерного излучения, направленный на поверхность обрабатываемого материала частично отражается от нее, а частично проходит в глубь тела. Излучение, проникающее в глубь ме-
55

талла, практически полностью поглощается свободными электронами проводимости в приповерхностном слое толщиной 0,1 – 1,0 мкм.
Проникновение излучения Е(х) в материалы
описывается уравнением
Е(х) = Е0(1 – R)e–αх
где E0 – энергия, падающая на поверхность; R – коэффициент отражения поверхности; α – коэффициент поглощения.
Для обеспечения эффективного плавления металла длительность лазерного импульса должна соответствовать тепловой постоянной времени для данно-
го металла, приближенно определяемой по формуле
η = δ2/4α,
где = /(c ) – коэффициент температуропроводимости.
Значения , для тонких образцов ( |
0,1 – |
0,2 мм) сопоставимы с длительностью импульсов лазеров в режиме свободной генерации, составляющей порядка нескольких миллисекунд. В следствие этого лазерная сварка металлов наиболее эффективна для данных толщин.
Оптимальные режимы лазерной обработки позволяют в полной мере использовать основные достоинства процесса – высокую степень концентрации энергии и
максимальную эффективность ее использования.
В настоящее время применение лазеров в технологии приборов микроэлектроники связаны со следующими операциями: сварка, сверление, резка, скрайбирование, подгонка радиоэлементов, отжиг,
56
перекристаллизация, осаждение слоев и другие. Серийно выпускаемые лазеры используются в таких сверхточных операциях, как программирование логических матриц, лазерная литография, восстановление ИЭТ.
3.7.1. Сварка лазерным излучением
Лазерное излучение обеспечивает высокую концентрацию энергии, значительно превосходящую другие источники энергии, используемые для сварки. Процесс лазерной сварки осуществляется на воздух либо в среде защитных газов: Ar, He, CO2 и др. С помощью лазеров хорошо свариваются сплавы на основе титана и никеля. Благодаря устойчивости никелевых сплавов к окислению сварка проводится при минимальной подаче инертного защитного газа.
Точечная сварка, проводимая неподвижным импульсным лазером, является эффективным способом присоединения проводов к электрическим контактам, сваривания термопар и соединения разнородных металлов и сплавов. Для сварки ИЭТ широко используются отечественные сварочные установки «Латус-31», «Квант-
30», «Квант-41», «Квант-18» и др.
Лазерная сварочная установка «Латус-31» с компактным конвективным лазером на углекислом газе выходной мощностью 1,5 кВт предназначена для точечной шовной сварки металлов с толщиной кромок 0,2 – 1,0 мм в защитной газо-
57
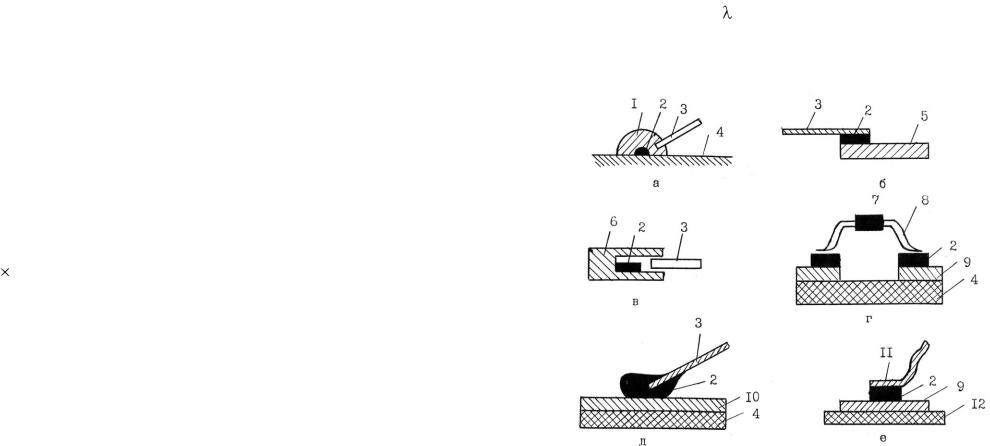
вой среде.
На установке «Квант-30» возможна прецизионная микросварка элементов ИС, полупроводниковых и других миниатюрных изделий.
Установка «Квант-41» предназначена для шовной сварки со скоростью 0,5 м/мин при глубине проплавления 0,5 мм и 1 м/мин при 0,2 – 0,3 мм, а «Квант-18» – с проплавлением 1,5 – 2 мм (по ковару).
Для герметизации особо трудносвариваемых алюминиевых корпусов микроэлектронных приборов также можно применять установки лазерной сварки. При глубине проплавления 1,02 мм скорость сварки составляет 5,08 мм/мин. Таким образом, алюминиевый корпус размером 76,2 76,2 мм сваривается в течение 36 с.
3.7.2. Лазерная пайка
Лазерная пайка имеет следующие особенности:
–высокую скорость нагрева обрабатываемых де-
талей;
–точное дозирование энергии;
–нагрев труднодоступных участков обрабатываемых деталей;
–пайку в изолированном объеме и строго контролируемой среде;
–совмещение процессов пайки с другими технологическими процессами (очисткой поверхности изменением ее химического состава и др.);
–возможность автоматизации пайки.
Схемы вариантов пайки ИЭТ приведены на
рис. 3.14.
Для данных разновидностей пайки длина волны излучения = 1,06 мкм. Мощность и параметры излучения подбираются опытным путем, исходя из заданного качества паяных соединений.
Рис. 3.14. Примеры пайки лазерным излучением:
а – электрического проводника к поверхности; б
– электродный фольги к выводу электролитического конденсатора; в – соединение «трубка – лента»; г – резистора к контактным площадкам; д – электрического проводника к тонкопленочной системе; е – вывода ИМС к проводнику;
58
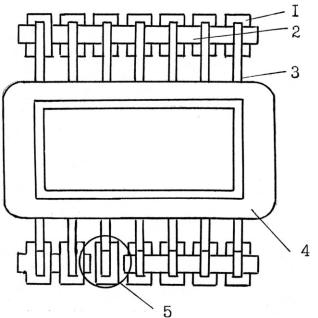
1 – флюс; 2 – припой; 3 – проводник; 4 – подложка; 5
– вывод конденсатора; 6 – трубка; 7 – резистор; 8 – вывод резистора; 9 – контактная площадка; 10 – пленка; 11 – вывод ИМС; 12 – печатная плата
Луч лазера может использоваться для пайки электрорадиоэлементов на печатные платы. Схема такого монтажа представлена на рис. 3.15. Микросхема 4 в корпусе планарными выводами 3 устанавливается на контактные площадки из стеклотекстолита. Предварительно выводы 3 микросхемы облуживают, отформовывают и опрессовывают припоем 2. При необходимости на места паек наносят дозированное количество флюса. Диаметр луча лазера 5 на плате устанавливают равным размеру контактной площадки. Под действием энергии излучения происходит разогрев и расплавление припоя с образованием в процессе кристаллизации паянного соединения. Непрерывное перемещение печатной платы со скоростью 8 мм/с обеспечивает производительность процесса монтажа 400 – 440 паек/мин
59
Рис. 3.15. Схема пайки микросхемы в корпусе на печатную плату лазером: 1 – контактные площадки; 2 – припой; 3 – выводы микросхемы; 4 – микросхема; 5 – луч лазера
3.7.3. Сварка и пайка энергией лучей оптического диапазона
Наиболее удобным излучателем для технологических целей являются дуговые неоновые лампы сверхвысокого давления. Дуговая неоновая лампа представляет собой шаровой баллон из оптически прозрачного кварца с помещенными в него двумя вольфрамовыми электродами. Излучение неоновой лампы фокусируется на изделие с помощью эллипсоидного отражателя. Для уве-
60
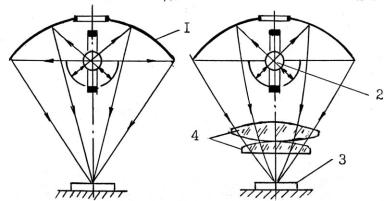
личения плотности энергии в пятне нагрева используется дополнительная линзовая оптика (рис. 3.16). Ввиду сравнительно низкой эффективности данного способа нагрева целесообразно его использовать для сварки и пайки материалов малых толщин.
а) б)
Рис. 3.16. Оптические схемы установок для сварки лучистой энергией: а – моноэллипсоидная система; б – то же, с двухлинзовым конденсатором; 1 – отражатель; 2 – лампа; 3 – изделие; 4 – конденсатор
61